Cost of Quality: A Comprehensive Guide to Driving Profitability
Quality has taken on new significance in today’s competitive business landscape – it is now a strategic necessity that can determine an organization’s very survival.
This is where the concept of “Cost Of Quality” (COQ) proves valuable as a systematic means for understanding, calculating and optimizing the financial impacts of attaining and sustaining product or service excellence.
Unlike more narrow views of quality mainly focusing on defect detection and remediation, COQ takes a comprehensive outlook.
It acknowledges that true quality is most powerfully achieved through proactive prevention of issues before they arise.
Key highlights
- A clear definition and overview of what is cost of quality, emphasizing its significance in today’s competitive market.
- A detailed breakdown of the components of the cost of quality, including the cost of good quality (prevention and appraisal costs) and the cost of poor quality (internal and external failure costs).
- Proven formulas and methodologies for accurately calculating and tracking quality costs within an organization.
- Insights into implementing robust quality management systems and tools, such as Six Sigma certification programs, Lean Manufacturing, Statistical Process Control (SPC), and Root Cause Analysis (RCA).
- Strategies for continuous improvement initiatives, including quality training programs, supplier quality management, and compliance with industry standards and regulations.
- Case studies and examples from various industries illustrate the tangible benefits of optimizing the cost of quality.
- An exploration of the long-term advantages of quality leadership, including improved profitability, enhanced brand reputation, customer satisfaction, and competitive advantage.
What is the Cost of Quality?
Where customers have an abundance of choices, quality is no longer a mere consideration – it’s a strategic imperative that can make or break a company’s bottom line, reputation, and long-term viability.
The “Cost of Quality” (COQ) concept is a comprehensive methodology that enables organizations to understand, quantify, and optimize the costs associated with achieving and maintaining product or service quality.
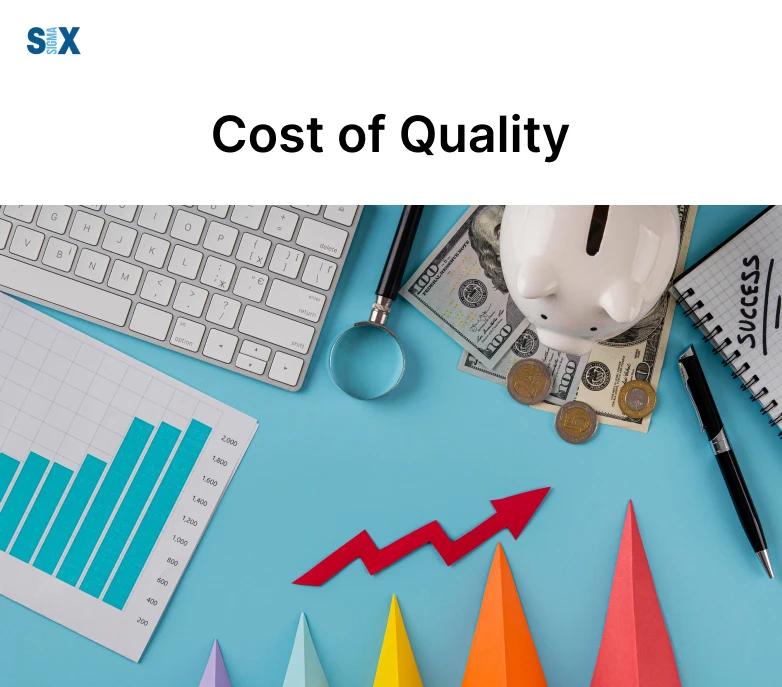
It recognizes that quality isn’t just about detecting and remedying defects; it’s about proactively preventing them from occurring in the first place.
Cost of quality is a holistic approach that encompasses all quality-related costs, from preventive measures to failure remediation.
By accurately measuring and analyzing these costs, companies can identify areas for improvement, allocate resources effectively, and ultimately drive profitability while enhancing customer satisfaction and brand reputation.
In an increasingly globalized and customer-centric business environment, the importance of cost of quality cannot be overstated.
Companies that fail to prioritize quality often find themselves at a significant disadvantage, facing mounting costs associated with defects, rework, warranties, and potential loss of market share.
Conversely, organizations that embrace quality as a strategic imperative and actively work to optimize their cost of quality can reap substantial rewards, including improved profitability, enhanced brand equity, and a competitive edge over their peers.
Understanding the Components of Cost of Quality
To effectively manage and optimize the cost of quality, it’s crucial to understand its key components. The cost of quality can be broadly categorized into two overarching categories: the cost of good quality and the cost of poor quality.
Cost of Good Quality
The cost of good quality represents an organization’s investments to prevent quality issues and ensure that its products or services meet the highest standards. This category encompasses two primary subcategories:
Prevention Costs: These are the costs associated with proactive measures aimed at reducing or eliminating defects before they occur.
Prevention costs may include activities such as quality planning, process improvement initiatives, employee training programs, and the establishment of robust quality management systems.
Appraisal Costs: Appraisal costs are incurred through activities designed to evaluate and verify the quality of products or services.
These costs may include product inspections, quality audits, supplier evaluations, and the implementation of process controls and monitoring systems.
By investing in prevention and appraisal activities, organizations can significantly reduce the likelihood of quality issues, thereby minimizing the potentially much higher costs associated with poor quality.
Cost of Poor Quality
The cost of poor quality, on the other hand, encompasses the costs incurred as a result of defects, nonconformities, or failures in products or services. This category can be further divided into two subcategories:
Internal Failure Costs: These are the costs associated with defects or nonconformities that are detected before the product or service reaches the customer.
Internal failure costs may include expenses related to scrap, rework, downtime, and the resources required for failure analysis and remediation.
External Failure Costs: External failure costs arise when defects or nonconformities are not detected until after the product or service has been delivered to the customer.
These costs can be substantial, encompassing expenses related to warranty claims, product returns, customer complaints, potential recalls, and the long-term impact on brand reputation and customer loyalty.
By understanding and effectively managing both the cost of good quality and the cost of poor quality, organizations can make informed decisions about resource allocation, process improvements, and strategic initiatives to enhance overall quality and drive profitability.
Calculating the Cost of Quality
While the concept of cost of quality may seem straightforward, accurately quantifying and tracking these costs can be a complex endeavor.
Fortunately, there are well-established formulas and methodologies that organizations can employ to gain valuable insights into their quality-related expenses.
The fundamental formula for calculating the cost of quality is as follows:
Cost of Quality (COQ) = Cost of Good Quality (COGQ) + Cost of Poor Quality (COPQ)
This formula can be further expanded to account for the individual components within each category:
COQ = (Prevention Costs + Appraisal Costs) + (Internal Failure Costs + External Failure Costs)
To effectively track and analyze quality costs, organizations must establish robust data collection and monitoring systems.
This may involve implementing specialized software or leveraging existing enterprise resource planning (ERP) systems to capture relevant data points, such as scrap rates, rework hours, warranty claims, and inspection results.
In addition to the quantitative financial data, organizations should also establish and track relevant quality metrics and key performance indicators (KPIs).
These may include measures such as defect rates, customer satisfaction scores, on-time delivery rates, and process capability indices.
By combining financial data with quality metrics, organizations can gain a comprehensive understanding of the true cost of quality and identify areas for targeted improvement efforts.
Managing and Reducing Cost of Quality
Once an organization has a firm grasp on its cost of quality, the next step is to implement strategies and initiatives to effectively manage and reduce these costs.
This typically involves a two-pronged approach: leveraging quality management systems and tools and fostering a culture of continuous improvement.
Quality Management Systems and Tools
Over the years, various quality management frameworks and methodologies have been developed to help organizations enhance their quality processes and reduce defects.
Some of the most widely adopted and effective systems and tools include:
Six Sigma, a methodology often mastered through structured Six Sigma certification programs, is a data-driven approach that focuses on identifying and eliminating defects through statistical analysis and project management techniques like DMAIC.
Six Sigma methodologies, such as Define, Measure, Analyze, Improve, and Control (DMAIC) and Design for Six Sigma (DFSS), have proven highly effective in driving quality improvements across various industries.
Lean Manufacturing: A systematic approach that emphasizes the elimination of waste and the creation of value-added processes.
Lean principles, such as just-in-time production, continuous flow, and kaizen (continuous improvement), can help organizations streamline their operations, reduce inefficiencies, and enhance quality.
Statistical Process Control (SPC): A set of techniques used to monitor and control process performance over time.
SPC tools, such as control charts and process capability studies, enable organizations to identify and address process variations proactively, reducing the likelihood of defects and quality issues.
Root Cause Analysis (RCA), a skill often validated through root cause analysis training, is a structured approach to identifying underlying causes of quality issues.
RCA methodologies, such as the 5 Whys and Ishikawa (fishbone) diagrams, can help organizations implement effective and sustainable solutions to quality challenges.
Process Controls and Monitoring: Implementing robust process controls and monitoring systems can help organizations detect and address quality issues in real time, minimizing the impact of defects and reducing the overall cost of quality.
Continuous Improvement Initiatives
In addition to leveraging quality management systems and tools, fostering a culture of continuous improvement is crucial for sustainable quality optimization.
This involves empowering employees at all levels to identify opportunities for enhancement and actively participate in quality improvement efforts. Key continuous improvement initiatives may include:
Quality Training Programs: Investing in comprehensive quality training programs can help organizations build a workforce that is skilled and knowledgeable in quality principles and practices.
This not only enhances individual performance but also contributes to a shared understanding of quality goals and objectives.
Supplier Quality Management: As supply chains become increasingly complex and globalized, effective supplier quality management is essential.
This may involve establishing clear quality standards, conducting regular supplier audits and evaluations, and fostering collaborative relationships to drive continuous improvement throughout the supply chain.
Compliance with Standards and Regulations: Adherence to industry-specific quality standards and regulatory requirements is not only a legal necessity but also a key factor in ensuring consistent quality and minimizing the risk of costly non-compliance issues.
By implementing a holistic approach that combines quality management systems, continuous improvement initiatives, and a strong quality-focused culture, organizations can effectively manage and reduce their cost of quality, positioning themselves for long-term success.
Benefits of Optimizing Cost of Quality
The benefits of optimizing cost of quality extend far beyond mere financial considerations.
While cost savings and improved profitability are certainly compelling drivers, organizations that prioritize quality excellence can reap a multitude of advantages that contribute to sustained growth and market leadership.
Improved Profitability and Bottom-Line Impact
By reducing the costs associated with poor quality, such as scrap, rework, warranty claims, and customer returns, organizations can realize substantial cost savings and enhance their overall profitability.
These savings can then be reinvested into further quality improvement initiatives, creating a virtuous cycle of continuous enhancement.
Enhanced Brand Reputation and Customer Satisfaction
Today a company’s reputation is one of its most valuable assets.
By consistently delivering high-quality products or services, organizations can build a strong brand reputation that fosters customer loyalty and trust.
Satisfied customers are not only more likely to remain loyal but also to recommend the brand to others, driving sustained growth and market share.
Competitive Advantage through Quality Leadership
In many industries, quality has become a key differentiator and a source of competitive advantage.
By positioning themselves as quality leaders, organizations can differentiate themselves from their competitors, attract and retain top talent, and command premium pricing for their products or services.
Improved Operational Efficiency
Optimizing cost of quality often goes hand-in-hand with streamlining processes, reducing waste, and enhancing operational efficiency.
By eliminating defects and non-value-added activities, organizations can improve throughput, reduce lead times, and increase overall productivity, contributing to a leaner and more agile business model.
Regulatory Compliance and Risk Mitigation
In regulated industries, such as healthcare, pharmaceuticals, and aerospace, adherence to quality standards and regulatory requirements is essential.
By prioritizing quality excellence, organizations can mitigate the risks associated with non-compliance, including fines, legal liabilities, and potential reputational damage.
Fostering a Culture of Continuous Improvement
Effective cost of quality management requires a mindset of continuous improvement and a relentless pursuit of excellence.
By embedding quality principles and practices into the organizational culture, companies can cultivate an environment that encourages innovation, problem-solving, and a shared commitment to delivering superior value to customers.
Cost of Quality in Examples
The transformative power of optimizing cost of quality is best illustrated through some examples and case studies from various industries.
These success stories not only highlight the tangible financial benefits but also showcase the broader impact on organizational performance, customer satisfaction, and market competitiveness.
Automotive Manufacturing
A leading automotive manufacturer implemented a comprehensive Six Sigma initiative to address quality issues and reduce costs associated with defects and rework.
By leveraging DMAIC methodologies, root cause analysis, and robust process controls, the company achieved significant reductions in defect rates, warranty claims, and scrap levels.
Over three years, the company reported cost savings of over $100 million, attributable to improved quality and operational efficiencies.
Additionally, customer satisfaction scores and brand loyalty metrics saw substantial improvements, contributing to increased market share and competitive advantage
Electronics Manufacturing
An electronics manufacturing company recognized the need to enhance its quality management practices to meet increasing customer demands and regulatory requirements.
By implementing a robust quality management system (QMS) based on ISO 9001 standards and leveraging statistical process control (SPC) tools, the company was able to significantly reduce defect rates and improve process capabilities.
This not only resulted in cost savings through reduced scrap and rework but also enabled the company to achieve compliance with stringent industry regulations, mitigating potential risks and liabilities.
Healthcare Services
A large healthcare provider embarked on a Lean Six Sigma initiative to address quality issues and operational inefficiencies in its patient care processes.
By applying Lean principles and DMAIC methodologies, the organization streamlined workflows eliminated non-value-added activities, and reduced defects in processes such as medication administration and patient handoffs.
The result was a significant improvement in patient satisfaction scores, reduced readmission rates, and substantial cost savings through improved operational efficiency and reduced errors and rework.
These examples underscore the far-reaching impacts of optimizing the cost of quality, from tangible financial benefits to enhanced customer satisfaction, regulatory compliance, and competitive positioning.
By embracing quality as a strategic imperative and implementing robust quality management practices, organizations across various industries can unlock the full potential of their operations and position themselves for sustained success.
Conclusion
Quality has rightfully taken on strategic prominence that can determine an enterprise’s destiny in today’s demanding business atmosphere.
Throughout this comprehensive guide, we have explored the fundamental aspects of cost of quality methodology.
This includes expenses of achieving strong quality like prevention and evaluation costs as well as penalties of weak quality such as internal and external failure costs.
We have delved into evidenced formulas and techniques for accurately determining and monitoring quality costs. Such financial visibility enables targeted areas for refinement and resource optimization within organizations.
Moreover, we examined various quality administration systems and instruments.
For instance, Six Sigma, Lean Manufacturing, Statistical Process Control and Root Cause Analysis – powerful frameworks granting enterprises means for lowering defects, streamlining processes and developing a culture of steady enhancement.
The proven cost-benefits of quality demonstrate its designation as an investment rather than mere business function.
I hope illuminating COQ’s strategic insights inspires optimizing your domain’s excellence methodically and profitably.
SixSigma.us offers both Live Virtual classes as well as Online Self-Paced training. Most option includes access to the same great Master Black Belt instructors that teach our World Class in-person sessions. Sign-up today!
Virtual Classroom Training Programs Self-Paced Online Training Programs