Value Analysis in Six Sigma. What is it, How Does it Work, and How to Do it?
Organizations struggle with identifying true value-adding activities in their processes.
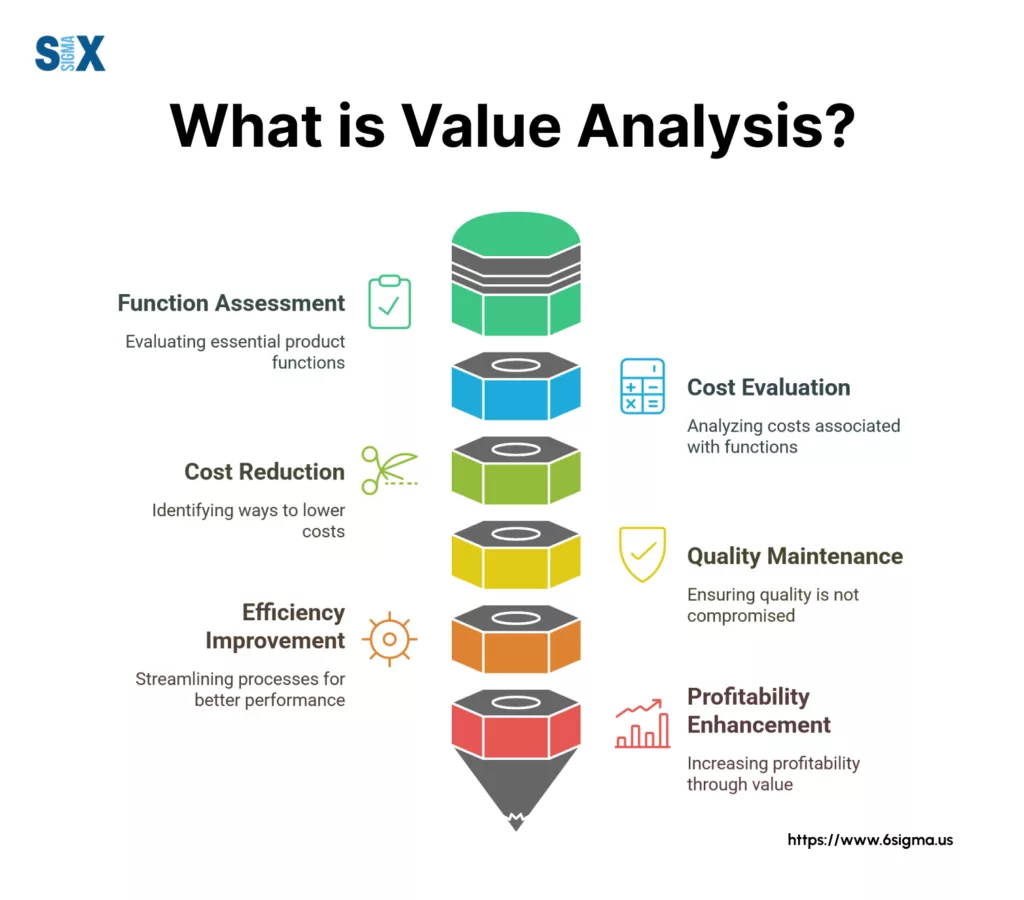
Value analysis is a proven approach that enables organizations to analyze how their various activities add value to the overall output.
This article will equip you with:
- How to differentiate between value-added and non-value-added activities using proven Six Sigma methodologies
- The critical role of Value Analysis in the DMAIC framework
- Practical techniques for implementing Value Analysis across different industries
- Common pitfalls to avoid and best practices
Value Analysis’s ability to bridge the gap between theoretical process improvement and practical business results makes it particularly powerful.
Lean Six Sigma — Foundation for Value Analysis
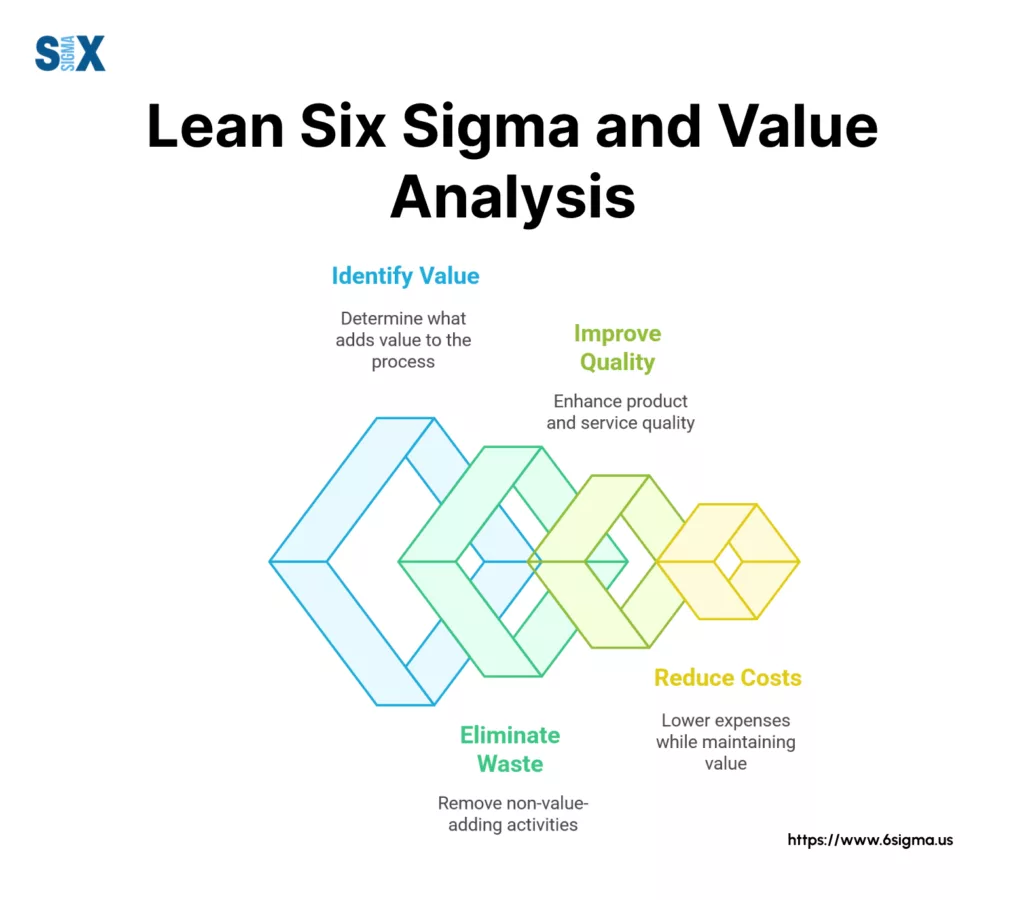
Lean Six Sigma is the mix of:
- Six Sigma: Focus on variation and defect reduction via statistical analysis.
- Lean principles: Focus on waste elimination and flow maximization.
This combination provides a robust framework for sustainable improvement.
DMAIC is an important methodology in Lean Six Sigma:
- Define: The Define phase establishes the project scope and objectives
- Measure: Measure quantifies current performance
- Analyze: Analyze identifies root causes; Improve implements solutions
- Control: Control ensures sustained results
Value Analysis is key during the Analyze and Improve phases, where we identify value-adding activities and eliminate waste.
Eight fundamental wastes are also addressed with the combination of Lean principles and DMAIC. These are: Inventory, Transportation, Overproduction, Motion, Waiting, Over-processing, Defects, and Skills underutilization.
Value Analysis with Lean Six Sigma helps to identify and maximize value-adding activities. It creates a powerful approach to process improvement that addresses both efficiency and effectiveness.
What is Value Analysis in Six Sigma?
Value Analysis in Six Sigma helps evaluate every step in a process. It examines individual process contributions and ties them to customer value. Unlike traditional methods, it focuses on understanding value from the customer’s perspective.
Six Sigma goes beyond simple cost considerations. It defines value as any activity that meets three critical criteria:
- it must transform the product or service,
- be done correctly the first time, and
- be something the customer is willing to pay for.
Value Analysis differs from other Six Sigma tools in its focus on the customer’s perspective combined with quantitative analysis. It helps understand and optimize the entire value stream.
Ready to become a Value Analysis expert?
Our Green Belt Certification program will equip you with the DMAIC methodology and statistical tools needed to lead successful process improvement projects. Learn how to identify waste, implement solutions, and achieve measurable results!
Benefits of Conducting Value Analysis in Six Sigma
Organizations conducting thorough Value Analysis achieve remarkable improvements in their operations.
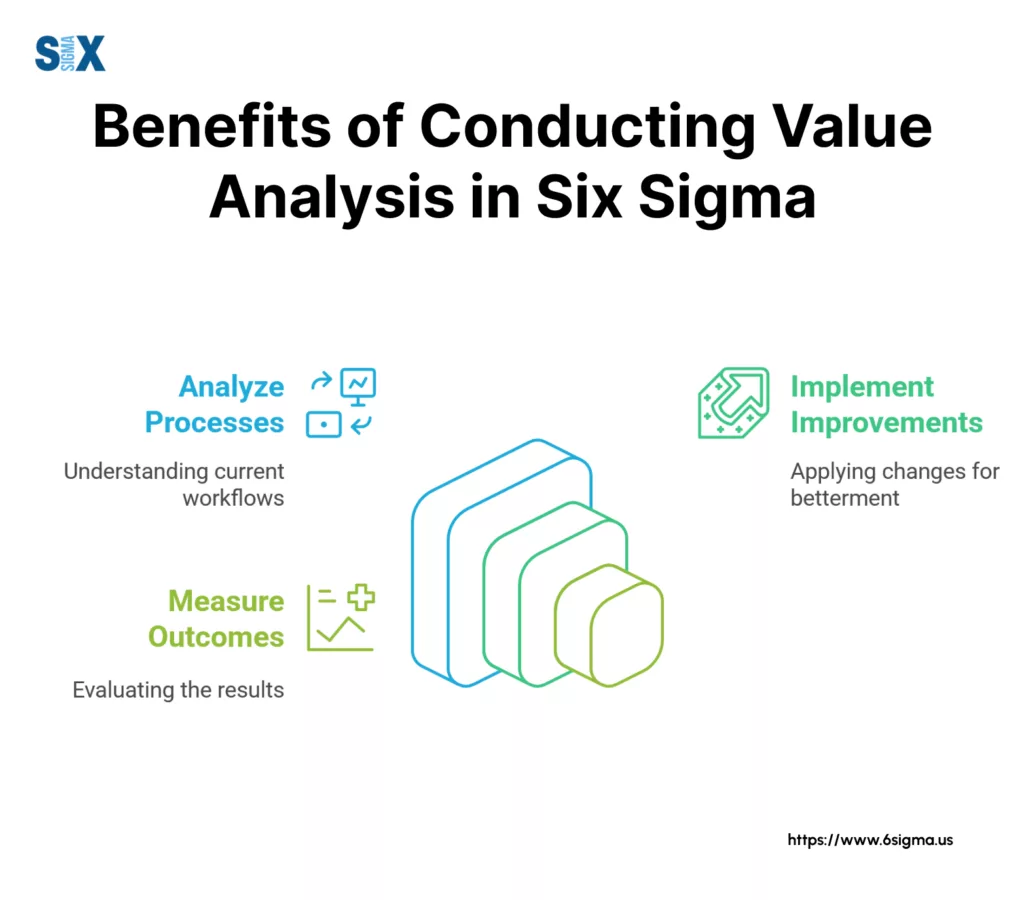
First and foremost, Value Analysis excels at identifying and eliminating waste. During a project with an electronics manufacturer, our Value Analysis revealed that 65% of their quality control steps were redundant.
By streamlining these processes, we reduced operational costs by 30% while maintaining product quality standards. This systematic approach to waste identification has proven invaluable across industries, from manufacturing to healthcare.
Process efficiency improvements are another significant benefit of Value Analysis in Six Sigma. While working with a product development team, we used Value Analysis to streamline their design review process.
The results were striking – a 40% reduction in cycle time and a 25% decrease in resource utilization. What’s particularly noteworthy is that these improvements didn’t come at the expense of quality; instead, they enhanced it.
Customer satisfaction enhancement is perhaps the most crucial benefit. We implemented Value Analysis in customer service operations. By identifying and optimizing value-adding activities, we achieved a 45% improvement in customer satisfaction scores. The key was focusing on activities that customers truly valued rather than those we assumed were important.
Cost reduction and resource optimization naturally follow effective Value Analysis implementation. Through proper application of Value Analysis organizations can consistently achieve 15-25% cost savings.
As someone with a statistical background, I appreciate how Value Analysis provides quantifiable metrics for process improvement. During my work with government institutions, we used Value Analysis data to justify process changes and demonstrate ROI, making it easier to gain stakeholder buy-in for improvement initiatives.
Types of Activities in Value Analysis
Three distinct types of activities in Value Analysis are crucial for successful process improvement.
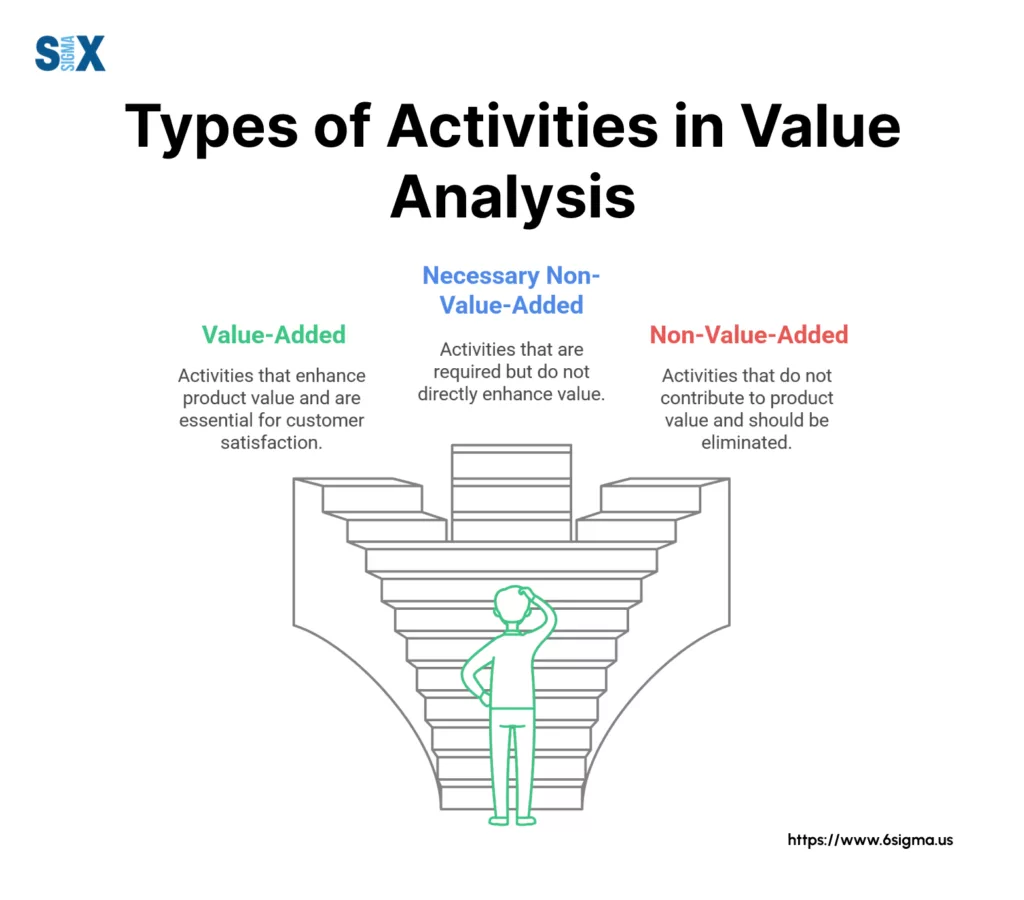
Value-Added Activities
Value-added activities typically constitute only about 5% of all process steps. These are activities that directly contribute to what customers are willing to pay for. Value-added activities are those that meet three critical criteria:
- they must physically transform the product or service,
- be done correctly the first time, and
- create something the customer values.
For example, in a manufacturing setting, the actual application of a coating to a product was value-added, while in a service environment, the direct resolution of a customer’s technical issue represented true value-added work.
Necessary Non-Value-Added Activities
Necessary Non-Value-Added Activities, which usually make up about 35% of process steps, are those that don’t directly add value but can’t be eliminated due to current constraints. Activities like regulatory documentation as necessary non-value-added work.
Although patients don’t directly value these activities, they’re essential for compliance and risk management. Quality inspections, while not directly adding value, were necessary to maintain product standards.
Non-Value-Added Activities
The most eye-opening category for many organizations is Non-Value-Added Activities, or waste, which typically accounts for 60% of process steps.
At a consumer electronics manufacturer, we found excessive movement of materials between workstations, redundant data entry, and unnecessary approvals that added no value to the final product. These activities consume resources without contributing to customer satisfaction or product quality.
What’s particularly interesting is how these percentages remain relatively consistent across industries. Whether I’m working with manufacturing plants or service operations, the initial distribution of activities typically follows this 5-35-60 pattern. The key to successful Value Analysis lies in recognizing these distinctions and systematically addressing each category appropriately.
Turn your Value Analysis insights into actionable data.
Minitab Essentials provides the statistical tools you need to quantify process improvements and validate your analysis. Don’t let valuable data go to waste – master the software that Six Sigma professionals rely on for accurate process improvement measurements.
Steps to Conduct Value Analysis in Six Sigma
A systematic approach to conducting Value Analysis can consistently deliver results.
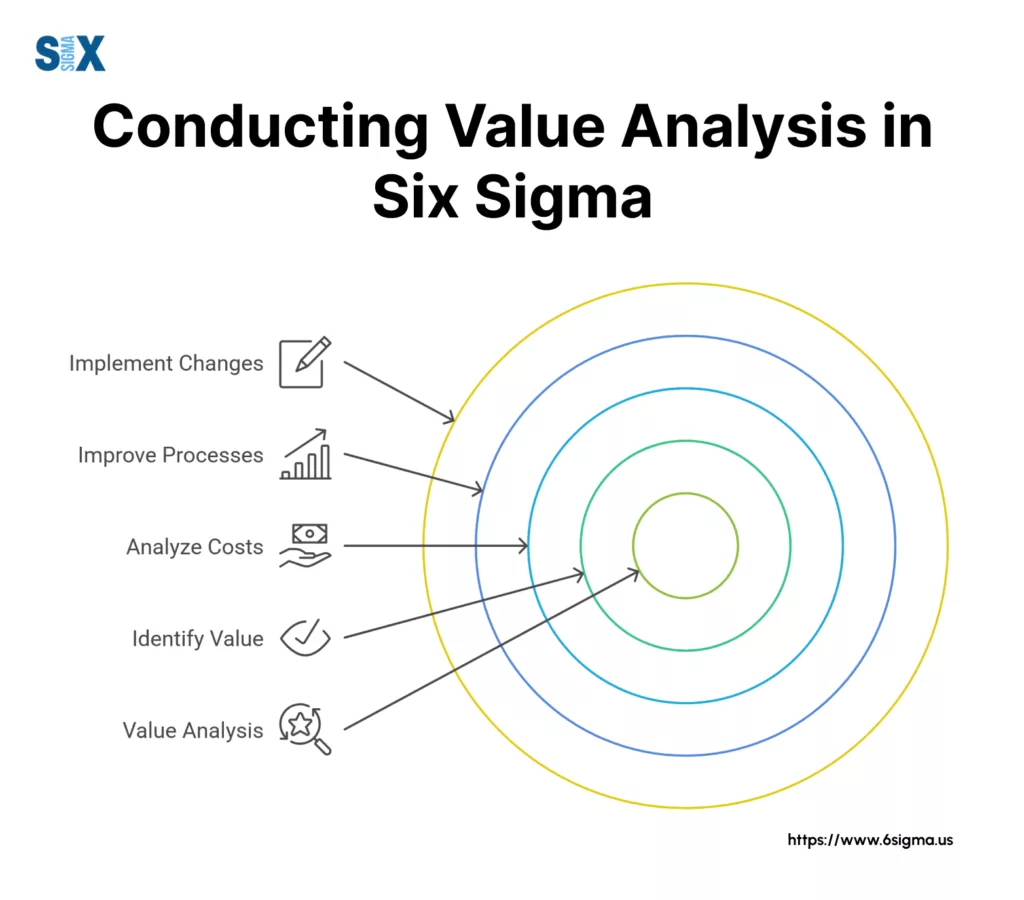
The foundation of effective Value Analysis begins with comprehensive process mapping and documentation. I always recommend using cross-functional process maps (swim lane diagrams) to capture both the process flow and organizational interactions. This approach proves particularly valuable to identify several hidden handoffs that create delays.
Once you have a detailed process map, the next critical step is identifying and categorizing activities. Involving front-line workers in this phase is crucial. Assemble teams of operators, supervisors, and engineers to categorize each process step. This collaborative approach not only improved accuracy but also facilitated buy-in for subsequent improvements.
Applying the Value Analysis Filter is perhaps the most crucial step.
- First, evaluate each activity from the customer’s perspective – would they pay for it?
- Second, assess the process outcome – does it transform the product or service?
- Finally, consider compliance and regulatory requirements – is it legally necessary?
Quantifying time and resources for each activity comes next. Implement a detailed time study program that reveals activities that consume far more resources than estimated. I recommend using a combination of direct observation, historical data, and statistical sampling to ensure accurate measurements.
The analysis phase involves identifying improvement opportunities based on the collected data. Develop a prioritization matrix that considers both the potential impact and the ease of implementation. This approach helps achieve quick wins while building momentum for more complex improvements.
Developing and implementing improvement strategies requires careful planning. Successful implementation depends on three key factors:
- clear communication,
- adequate training, and
- strong leadership support.
Finally, monitoring and controlling changes ensures sustained improvement.
Value Analysis Tools and Techniques
The effectiveness of Value Analysis largely depends on selecting and utilizing the right tools for each specific situation.
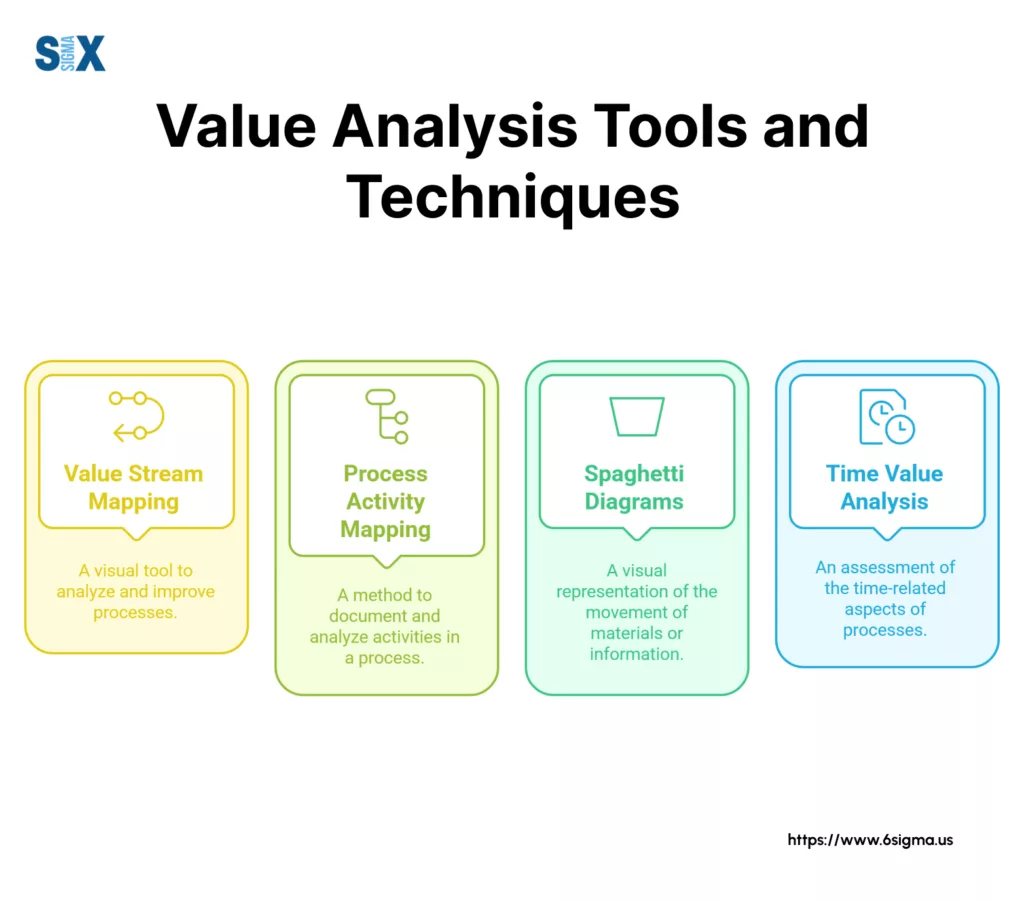
Value Stream Mapping
Value Stream Mapping stands out as the cornerstone tool for comprehensive Value Analysis. While working with a semiconductor division, we used VSM to visualize their entire production process, from raw material receipt to finished product delivery.
This powerful visualization tool helped us identify that 70% of their total lead time was actually spent in non-value-adding activities. The key to successful VSM implementation lies in capturing both material and information flows.
Process Activity Mapping
Process Activity Mapping provides a detailed examination of each step in the value stream. During my work with a healthcare division, we utilized this technique to break down complex medical equipment maintenance procedures.
By documenting each activity’s purpose, duration, and distance traveled, we identified opportunities to reduce maintenance time by 35%. This tool’s effectiveness is its ability to highlight redundancies and unnecessary movement patterns.
Spaghetti Diagrams
Spaghetti Diagrams have proven invaluable for analyzing physical movement within processes. We used these diagrams to track operator movements during product assembly. The resulting visual representation was eye-opening – operators were walking nearly three miles per shift due to poor layout design.
By reorganizing the workspace based on this analysis, we reduced movement by 60% and improved productivity significantly.
Time Value Analysis
Time Value Analysis focuses on the temporal aspect of processes. During a project, we mapped the time spent on each activity against its value contribution. This analysis revealed that high-value activities often represented less than 10% of total process time – a revelation that drove significant process redesign efforts.
In recent years, I’ve increasingly incorporated digital tools and software for Value Analysis. Modern solutions like EngineRoom and Minitab’s Value Stream Mapper have transformed how we collect and analyze data.
However, I always emphasize to my workshop participants that these tools should complement, not replace, fundamental analysis techniques.
Master the foundations of Value Analysis!
Our Lean Fundamentals course teaches you practical methodologies to reduce cycle times and improve productivity. Learn how to create robust Value Stream Maps and implement the 5S principles.
Integrating Value Analysis with Other Six Sigma Tools
Value Analysis becomes exponentially more powerful when integrated with other Six Sigma tools.
The integration of Value Analysis with Root Cause Analysis has proven particularly powerful. While working with a manufacturing division, we combined these approaches to not only identify non-value-adding activities but also understand their underlying causes.
This integrated approach reduces process variations by 40% and helps eliminate recurring issues. I’ve found that using the 5 Whys technique alongside Value Analysis helps teams dig deeper into why certain activities exist in the first place.
Combining Value Analysis with 5S has been another game-changer in my experience. During a project at a production facility, we used Value Analysis to identify wasteful activities while simultaneously implementing 5S principles.
This combination helped us create standardized workflows that eliminated non-value-adding steps while maintaining an organized, efficient workspace. The results were impressive – a 35% improvement in productivity and a 50% reduction in motion waste.
Value Analysis in Kaizen events has become a standard practice in my consulting work. We incorporated Value Analysis into rapid improvement workshops, which allowed teams to quickly identify and eliminate waste while maintaining focus on customer value.
This integrated approach typically yields results 30% faster than traditional Kaizen events alone. The key is to use Value Analysis as a lens through which to view all improvement opportunities during the event.
The synergy between Value Analysis and Failure Mode and Effects Analysis (FMEA) has been particularly noteworthy. While consulting with a healthcare division, we used this combination to not only identify non-value-adding activities but also assess their potential impact on product quality and reliability.
This integrated approach helped us prioritize improvement efforts more effectively, focusing on activities that both added value and reduced risk.
Industry-Specific Applications of Value Analysis
Value Analysis can be adapted to meet unique sector-specific challenges.
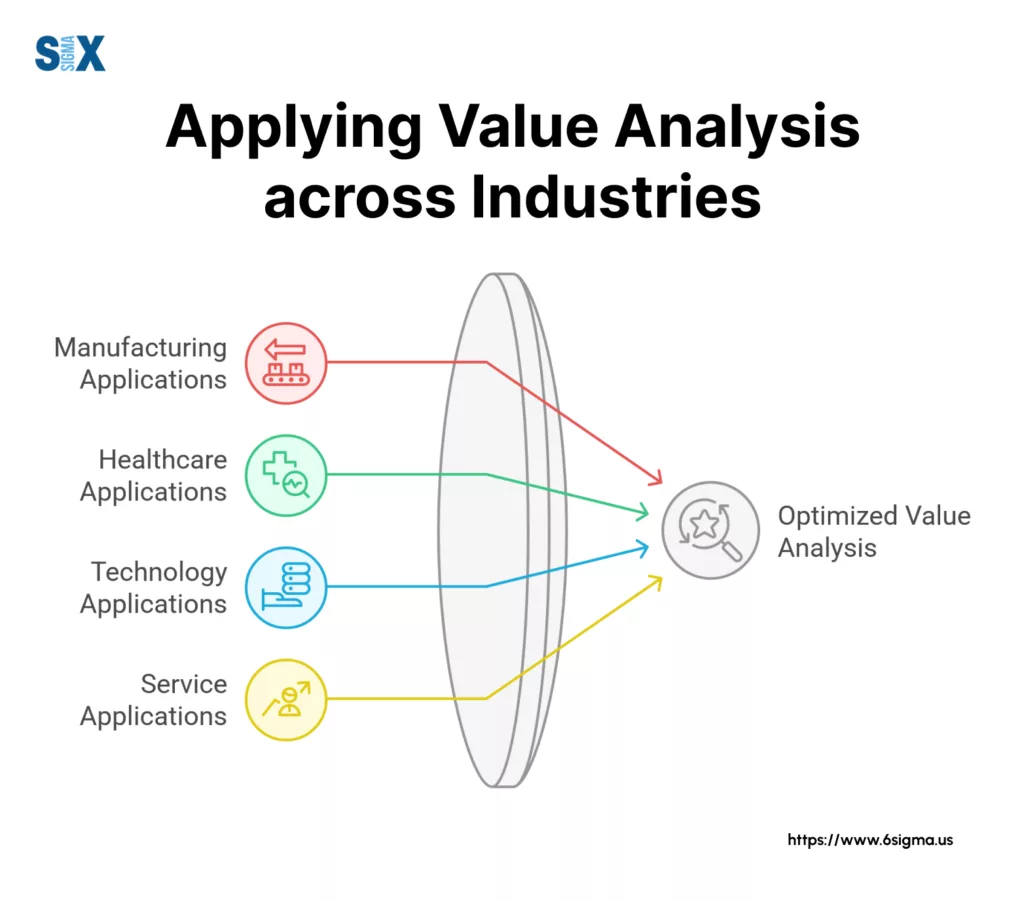
Manufacturing
In the manufacturing sector, Value Analysis has proven particularly effective in optimizing production processes.
During a project with an electronics manufacturer, we applied Value Analysis to their assembly line operations, resulting in a 40% reduction in non-value-added activities and a 25% improvement in throughput.
The key was identifying and eliminating unnecessary movement and waiting times between workstations.
Service
Service industry applications of Value Analysis have yielded equally impressive results.
While working with customer service operations, we used Value Analysis to streamline their support processes. By identifying and eliminating redundant steps in their customer interaction workflow, we reduced average handling time by 35% while improving customer satisfaction scores.
The focus here was on maximizing value-adding customer interaction time.
HealthCare
Healthcare process improvements through Value Analysis have been particularly rewarding. During my consulting work with healthcare providers, we’ve applied Value Analysis to patient flow processes.
One notable project resulted in reducing patient wait times by 45% by identifying and eliminating non-value-adding administrative steps. This not only improved patient satisfaction but also increased the facility’s capacity to serve more patients.
IT and Software Development
In IT and software development, Value Analysis has evolved to address unique challenges in digital processes. While working with software development teams, we adapted Value Analysis principles to agile development workflows.
This resulted in a 30% reduction in development cycle time by identifying and eliminating unnecessary documentation and approval steps while maintaining code quality standards.
Best Practices and Common Pitfalls in Value Analysis
There are several critical success factors and potential pitfalls that can make or break improvement initiatives.
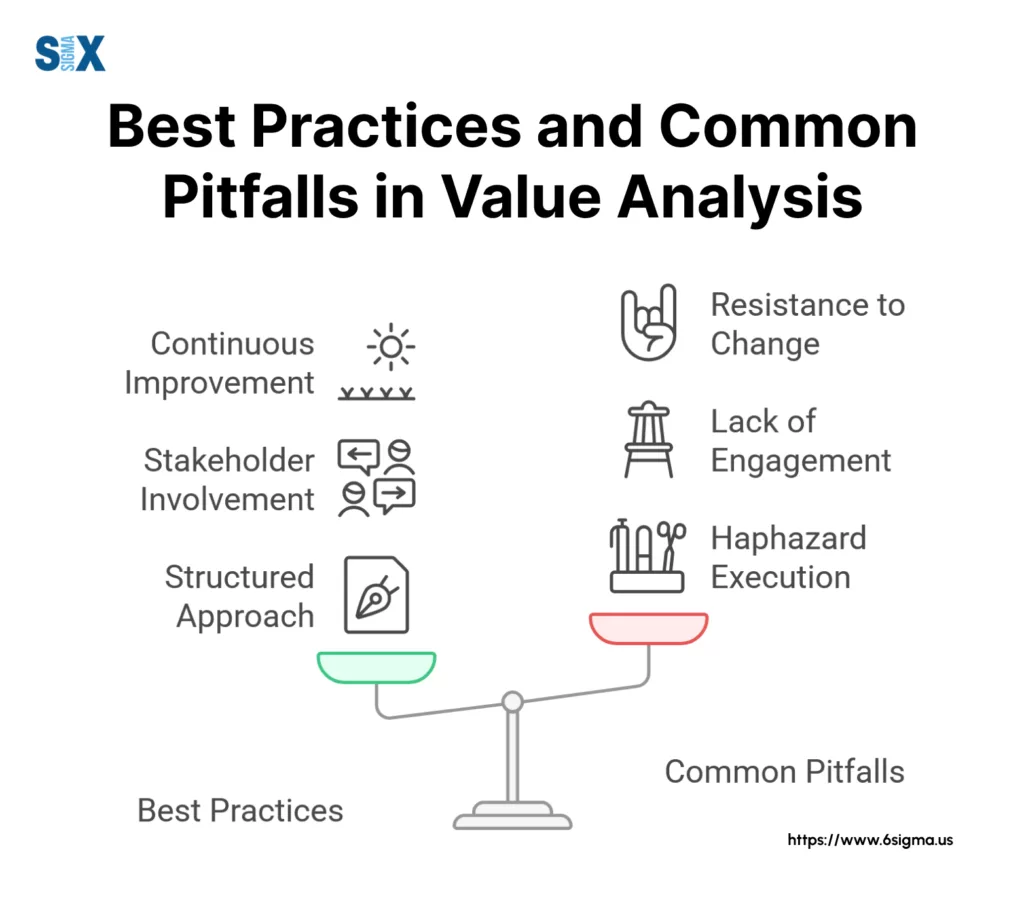
Stakeholder involvement is crucial for successful Value Analysis implementation. Several projects falter despite solid technical analysis simply because key stakeholders weren’t properly engaged. I’ve learned to involve representatives from all affected areas early in the process.
To tackle this, create cross-functional teams that include operators, engineers, and management. This will result in better implementation success rates compared to projects with limited stakeholder involvement.
Maintaining objectivity in assessments can be challenging but is essential for accurate Value Analysis. Use quantitative metrics to minimize subjective bias. Implement a peer review system for value assessments, which helps identify and eliminate personal biases that could have skewed your analysis.
One common pitfall is over-analysis paralysis. Teams spend excessive time analyzing minimal-impact activities while missing larger improvement opportunities. I now advocate for a balanced approach, using Pareto analysis to focus on the vital few rather than the trivial many.
Balancing short-term and long-term improvements requires careful consideration. Organizations focus exclusively on quick wins at the expense of sustainable improvements. The key is maintaining a portfolio approach.
Common mistakes include failing to validate assumptions, inadequate data collection, and rushing to solutions before thoroughly understanding the current state. Successful Value Analysis requires disciplined adherence to the methodology. Use a comprehensive checklist system to ensure teams don’t skip critical steps in their enthusiasm to implement solutions.
The Power of Value Analysis in Six Sigma
Proper implementation of Value Analysis can deliver substantial, sustainable results.
Value Analysis consistently provides the clarity needed to identify and eliminate waste while enhancing customer value.
Fellow Black Belts and aspiring Six Sigma practitioners, I encourage you to embrace Value Analysis as a fundamental tool in your improvement journey. Mastering Value Analysis can accelerate growth and enhance project outcomes!
SixSigma.us offers both Live Virtual classes as well as Online Self-Paced training. Most option includes access to the same great Master Black Belt instructors that teach our World Class in-person sessions. Sign-up today!
Virtual Classroom Training Programs Self-Paced Online Training Programs