Total Quality Management (TQM) vs Six Sigma. All You Need to Know
Buyer satisfaction takes precedence to establish dominance and ensure survival in today’s fast-moving market. Total Quality Management and Six Sigma arise as notable methodologies to achieve this.
TQM (Total Quality Management) prioritizes never-ending upgradation of the whole operation through employee involvement.
Six Sigma emphasizes data-driven decision-making and variation reduction through meticulously targeting defects’ root cause(s).
Key Highlights
- Total Quality Management and Six Sigma surface as prominent quality-boosting techniques.
- Both paths diminish errors and variations while augmenting client delight and endless progress.
- TQM prioritizes establishing a quality-empowered mindset through dedicated leadership and inclusive personnel involvement.
- Six Sigma concentrates on fact-based problem-solving utilizing analytical instruments surgically targeting scrap.
- Judging likenesses/divergences between these aid enterprises in opting for methods most befitting demands, means, and targets.
What is TQM and Six Sigma?
Businesses use different quality approaches like Total Quality Management (TQM) and Six Sigma.
Both aim to reduce errors and enhance client fulfillment, yet diverge in routines and instruments.
TQM focuses on non-stop upgrading through collaboration-spanning operations. It cultivates quality as a core driver.
Six Sigma utilizes data, statistical tools, and a rigorous improvement cycle seeking near-total quality through variability reduction.
Knowing the contrasts proves pivotal for selecting integration/unique implementation suiting a company’s exact needs, present frameworks, and anticipated objectives.
Similarities between TQM vs Six Sigma
While Total Quality Management (TQM) and Six Sigma have some distinct differences, they share several key similarities in their underlying principles and goals. Both methodologies are focused on continuous improvement, defect reduction, and enhancing customer satisfaction.
Customer Focus: TQM and Six Sigma both place a strong emphasis on understanding and meeting customer needs and expectations. They aim to deliver products and services that consistently meet or exceed customer requirements.
Data-Driven Approach: Both methodologies rely heavily on data collection, analysis, and fact-based decision-making. They use statistical tools and techniques to measure performance, identify root causes of problems, and drive process improvements.
Process Orientation: TQM and Six Sigma view an organization as a collection of interconnected processes. They seek to optimize and improve these processes to reduce variation, eliminate waste, and enhance efficiency.
Employee Involvement: Successful implementation of TQM and Six Sigma requires active engagement and participation from employees at all levels. They promote a culture of continuous learning, problem-solving, and employee empowerment.
Top Management Commitment: Leadership commitment and support are critical for the effective deployment of both TQM and Six Sigma initiatives. Top management must provide resources, set clear goals, and lead by example.
Fact-based Decision Making: Both methodologies discourage decisions based on assumptions or gut feelings. Instead, they emphasize the use of data, statistical analysis, and objective evidence to make informed decisions.
Continuous Improvement: TQM and Six Sigma are ongoing efforts that aim to create a culture of continuous improvement within an organization. They encourage the constant identification and elimination of defects, waste, and inefficiencies.
While TQM and Six Sigma share these fundamental similarities, they differ in their specific approaches, tools, and techniques, which will be explored in the next section.
Key Differences between TQM vs Six Sigma
While they share some similarities in their goals of improving quality and processes, there are several key differences between TQM vs Six Sigma:
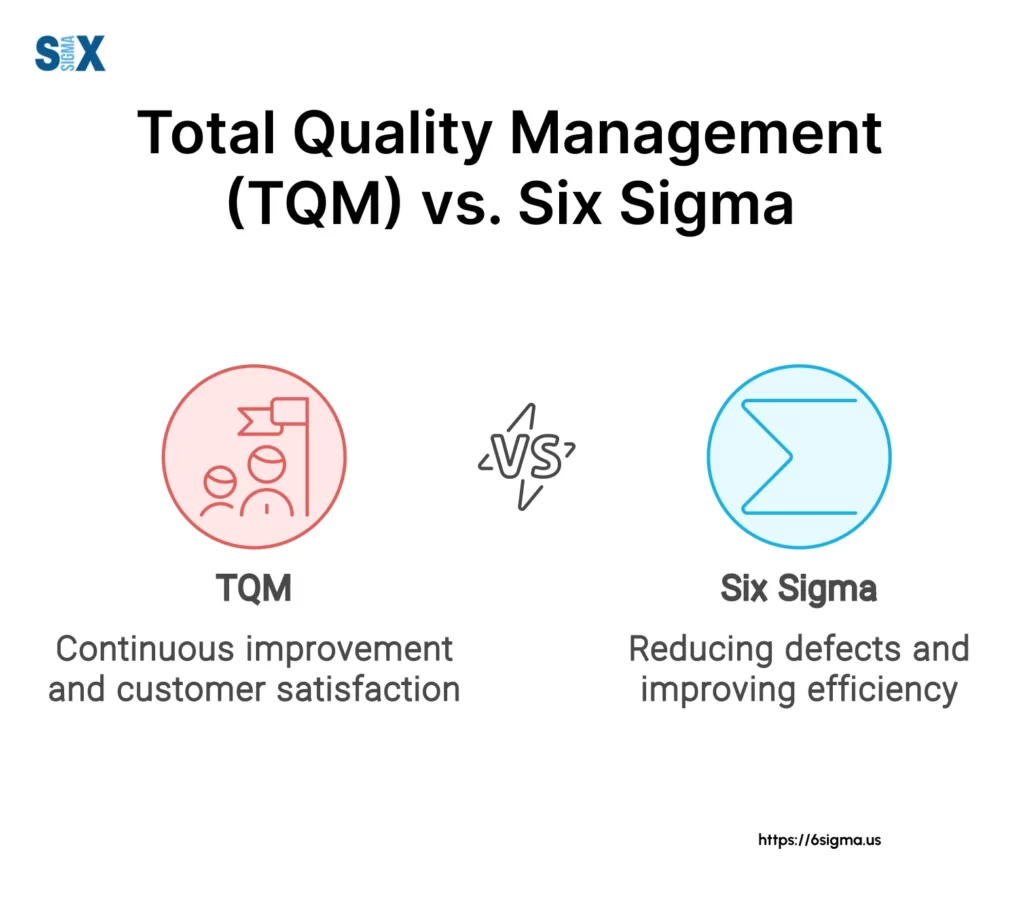
Focus
TQM takes a broader approach to quality management across an entire organization. It emphasizes continuous improvement in all aspects of operations.
Six Sigma, on the other hand, is focused specifically on reducing variation and defects in processes and products through data-driven analysis and statistical methods.
Methodology
TQM relies more on qualitative techniques like employee empowerment, customer focus, and management leadership.
Six Sigma follows a defined methodology called DMAIC (Define, Measure, Analyze, Improve, Control) which provides a structured, data-intensive approach to process improvement.
Tools
TQM utilizes a wide range of quality tools like quality circles, benchmarking, quality audits, etc.
Six Sigma relies heavily on statistical tools like process capability analysis, hypothesis testing, design of experiments, and other advanced data analysis techniques.
Metrics
In TQM, metrics are more subjective and customer-focused like customer satisfaction scores.
Six Sigma uses quantitative metrics like defects per million opportunities (DPMO) to measure and track improvement.
Approach to Quality b/w TQM vs Six Sigma
TQM considers quality the responsibility of all employees and aims to build a quality culture.
Six Sigma treats quality improvement as a series of projects driven by experts called Black Belts and Master Black Belts.
Training
TQM training is generally less intensive and more philosophical.
Six Sigma training is very rigorous, involving extensive coursework in statistical analysis and the DMAIC methodology at different belt levels.
By understanding these key differences in focus, approach, tools, and training, organizations can assess which methodology – TQM or Six Sigma – is better suited for their specific quality needs and goals.
TQM Methodology and Tools
Total Quality Management (TQM) is a comprehensive methodology that involves several principles, practices, and tools aimed at achieving continuous improvement in all aspects of an organization.
The core methodology of TQM revolves around customer focus, process improvement, and the involvement of all employees.
Customer Focus: TQM emphasizes understanding and meeting customer needs and expectations. Tools like customer surveys, feedback mechanisms, and voice of the customer analysis help organizations gather insights into customer requirements.
Process Improvement: TQM advocates for continuously improving processes to enhance quality and efficiency. Tools such as process mapping, value stream mapping, and process capability analysis are used to identify opportunities for process optimization.
Employee Involvement: TQM relies on the active participation and empowerment of employees at all levels. Tools like quality circles, suggestion systems, and cross-functional teams foster employee engagement and continuous improvement.
Some other widely used TQM tools include:
- Plan-Do-Check-Act (PDCA) Cycle: This iterative cycle guides the implementation of improvements and ensures continuous monitoring and adjustment.
- Cause-and-Effect Diagrams (Fishbone Diagrams): These diagrams help identify potential root causes of problems or quality issues.
- Statistical Process Control (SPC): SPC involves using statistical techniques to monitor and control processes, ensuring they operate within acceptable limits.
- Failure Mode and Effects Analysis (FMEA): FMEA is a systematic approach to identifying potential failures, their causes, and their effects, allowing for preventive actions.
- Benchmarking: Benchmarking involves studying best practices from other organizations and industries to identify opportunities for improvement.
- Quality Function Deployment (QFD): QFD is a structured method for translating customer requirements into appropriate technical requirements for products or services.
The TQM methodology and its associated tools aim to create a quality culture within the organization, fostering continuous improvement, customer satisfaction, and operational excellence.
Six Sigma Methodology and Tools
The Six Sigma methodology follows a structured and data-driven approach known as DMAIC (Define, Measure, Analyze, Improve, Control). This problem-solving strategy aims to identify and eliminate causes of defects or errors in processes.
Define: Clearly define the problem, goals, and customer requirements for the process improvement project.
Measure: Collect relevant data to establish a baseline and measure the current performance of the process. Statistical tools like process capability analysis help understand the extent of variation.
Analyze: Analyze the data to identify the root causes of defects or variations using techniques such as cause and effect diagrams, regression analysis, and hypothesis testing.
Improve: Develop, test, and implement solutions for the root causes. Tools like the design of experiments help optimize processes.
Control: Implement controls to sustain the improvements through statistical process control, visual management, training, and continuous monitoring.
Key Six Sigma tools include process mapping, cause and effect diagrams, failure mode and effects analysis (FMEA), control charts, design of experiments (DOE), and statistical analysis software. Green Belts and Black Belts are trained professionals who lead Six Sigma projects.
The DMAIC cycle drives process optimization by reducing variation, defects, and cycle times, ultimately improving quality, customer satisfaction, and operational efficiency. Data-driven decisions and rigorous statistical analysis are cornerstones of Six Sigma.
Choosing Between TQM vs Six Sigma
The decision to implement TQM or Six Sigma depends on the specific needs and goals of an organization. Both methodologies aim for continuous improvement and quality enhancement, but they differ in their approaches and areas of focus.
TQM is a broad, company-wide approach that emphasizes creating a quality culture and involving all employees in the continuous improvement process.
It is suitable for organizations that want to improve overall operations, customer satisfaction, and organizational performance. TQM is particularly beneficial for service-oriented industries, where customer interactions and experiences are crucial.
On the other hand, Six Sigma is a more structured, data-driven, and project-based approach that focuses on reducing defects, variations, and waste in specific processes or products.
It is well-suited for manufacturing companies or organizations with complex, repetitive processes that require precise measurements and statistical analysis.
Six Sigma’s DMAIC (Define, Measure, Analyze, Improve, Control) cycle provides a rigorous framework for identifying and eliminating root causes of defects.
Techniques such as root cause analysis are integral to the Analyze phase of DMAIC, and specialized root cause analysis training is available for professionals seeking to master these skills.
Organizations should consider their specific objectives, industry, and existing quality initiatives when choosing between TQM vs Six Sigma.
TQM may be the better choice if the goal is to foster a comprehensive quality culture and improve overall organizational performance.
However, if the primary focus is on reducing defects and variations in specific processes or products, Six Sigma could be more appropriate.
It is also possible to implement both TQM and Six Sigma in a complementary manner, leveraging the strengths of each approach.
For example, an organization can adopt TQM principles to establish a quality-focused culture, while using Six Sigma tools and techniques to tackle specific process improvement projects.
Ultimately, the choice between TQM vs Six Sigma should be based on a thorough assessment of the organization’s needs, resources, and long-term goals, as well as the expertise and commitment of leadership and employees.
Implementing TQM or Six Sigma
Once an organization has decided whether to adopt a TQM vs Six Sigma approach, the next step is proper implementation. Both involve significant changes to processes, company culture, employee training, and management commitment.
For TQM implementation, some key steps include:
- Obtaining complete leadership commitment and driving the quality culture from the top-down
- Developing a strategic quality plan with clear goals, metrics, and accountability
- Providing comprehensive training on TQM philosophies, tools, and continuous improvement techniques
- Empowering employees at all levels to identify and solve quality issues
- Focusing on customer satisfaction by capturing the voice of the customer
- Gradually integrating TQM practices into all business processes and decision-making
Implementing Six Sigma follows a structured approach using the DMAIC (Define, Measure, Analyze, Improve, Control) methodology:
- Define the projects, resources, and customer requirements
- Measure key aspects of the current process and collect data
- Analyze the data to determine the root causes of defects and variability
- Improve the process by eliminating defects and sources of variation
- Control the improved process to ensure continued performance
This is often done by training a specialized workforce of Six Sigma Green Belts and Black Belts to lead projects. Successful deployment requires leadership commitment, data-driven decisions, clear accountability, and a cultural shift toward problem-solving.
Whether implementing TQM or Six Sigma, the transformation requires dedicated resources, employee buy-in, patience, and continuous reinforcement of the quality principles.
Involving all functions and integrating them into the strategic plan helps sustain the quality improvement efforts long-term.
SixSigma.us offers both Live Virtual classes as well as Online Self-Paced training. Most option includes access to the same great Master Black Belt instructors that teach our World Class in-person sessions. Sign-up today!
Virtual Classroom Training Programs Self-Paced Online Training Programs