What are Total Quality Management (TQM) Tools? The Only Guide You Need
Driving sustainable results requires client-centered solutions. Total Quality Management (TQM) helps achieve that, with TQM tools, through endless upgrading, purchaser focus, and cross-department error reduction.
These TQM instruments include: charts tracking variations; root-cause investigations; leaner manufacturing; design optimization.
By capably leveraging methods organizations gain valuable transparency, pinpoint areas for improvement, and execute targeted solutions enhancing standard, waste-reduction, and productivity.
Key Highlights
- Total Quality Management envisions customer satisfaction through perpetual tuning feedback by engaged associates.
- Implemented correctly, TQM aids in addressing quality issues, streamlining workflows, slashing waste, and improving seamlessly.
- Integrating these into management optimizes proficiency, reduces hazards, and bolsters client fulfillment.
- Cultivating this quality-centric spirit enhances business performance far into the future through consistently honing and resolving emerging challenges cooperatively.
What are TQM Tools
Boosting prosperity requires consistently enhancing production, revenue, and operational know-how. Embracing Total Quality Management propels exactly this through tireless upgrading via complete collaboration.
TQM depends resourcefully upon an arsenal of instruments and tactics for scrutinizing operations, pinpointing dilemmas, and driving perpetual refinement. These TQM solutions methodically administrate and optimize quality administration and workflows.
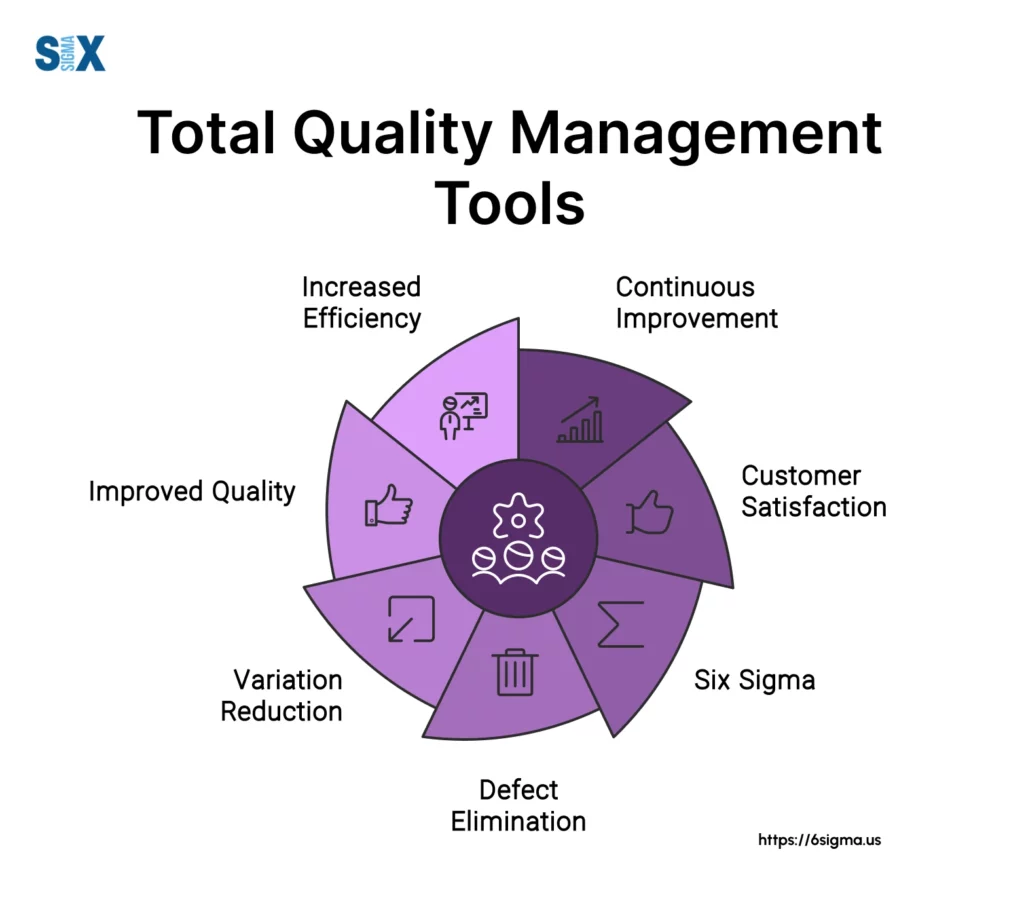
Key dividends involve, efficiency-production gains; redundant variances/expenditures diminishing; more overjoyed clients; worker engagement; and competitive differentiation via uninterrupted quality.
Principled instruments descend from assorted quality-field theories—Six Sigma, Lean, Kaizen, and stats administration—spanning development, executing, surveilling, and enhancing phases.
Statistical Process Control Tools
Statistical process control (SPC) tools are an essential part of the TQM toolkit. SPC provides techniques for monitoring process behavior and detecting special cause variation from assignable causes.
This allows processes to be analyzed, improved and brought into a state of statistical control where only common cause variation exists.
Control Charts
Control charts are the primary tool in SPC. They plot data over time and allow you to study how a process varies, as well as analyze patterns of variation from historical data. Some key control charts include:
- X-bar and R Charts: Monitor the mean and range of a process
- Individual and Moving Range Charts: For data from a single source over time
- p Charts: Monitor the proportion of defective items
- c Charts: Monitor defects per unit
Process Capability Analysis as TQM Tools
Process capability studies measure the ability of a process to produce output within specification limits.
Metrics like Cp, Cpk, Pp, and Ppk quantify this capability. Process capability is essential for predicting defect rates and determining if a process can hold tolerances.
Acceptance Sampling
Acceptance sampling uses statistical sampling to determine if a batch or lot of product should be accepted or rejected based on the number of defective units found in a sample.
This avoids 100% inspection while providing quantified protection to the producer and consumer.
Lean and Six Sigma Tools
Lean manufacturing and Six Sigma are two complementary methodologies included in Six Sigma Certification that focus on eliminating waste, reducing variation, and improving efficiency. Several tools are used in these approaches to identify and address process inefficiencies.
5S Methodology: This lean tool promotes a clean, organized, and standardized work environment by following five principles: sort, straighten, shine, standardize, and sustain. Implementing 5S can improve productivity, safety, and quality.
Value Stream Mapping: This lean technique maps the flow of materials and information in a process, helping to visualize value-added and non-value-added activities. It identifies opportunities for waste reduction and process streamlining.
Gemba Walk: Derived from the Japanese term for “the real place“, gemba walks involve managers observing work processes firsthand on the production floor to identify improvement areas.
Kanban System: Kanban is a lean scheduling system that controls the flow of materials through a pull system, preventing overproduction and reducing inventory levels.
Just-in-Time Manufacturing: JIT is a lean approach that aims to produce the right product, at the right time, in the right quantity by minimizing waste from overproduction, waiting times, and excess inventory.
Total Productive Maintenance: TPM is a lean asset management strategy that optimizes equipment effectiveness by involving operators in routine maintenance activities.
DMAIC: This Six Sigma methodology (Define, Measure, Analyze, Improve, Control) central to Six Sigma Green Belt certification provides a structured approach for process improvement by identifying and eliminating causes of defects or errors.
By integrating lean tools focused on reducing waste with Six Sigma’s statistical methods for reducing process variation, organizations can drive significant quality improvements and operational efficiencies.
Root Cause Analysis Tools
Root cause analysis (RCA) is a critical component of any total quality management (TQM) initiative. RCA tools help identify the underlying sources of problems or defects, rather than just addressing the symptoms.
This allows organizations to implement effective, sustainable solutions.
Some powerful RCA tools used in TQM include:
5 Whys Analysis
The 5 Whys is an iterative questioning technique to peel back layers of symptoms to uncover the root cause.
By repeatedly asking “Why?” about the last answer, you can trace the chain of causality. This simple yet effective tool encourages critical thinking to get beyond obvious reasons.
Fishbone (Ishikawa) Diagram as TQM Tools
This diagram visually maps potential causes into categories like personnel, materials, measurement, environment, etc.
Creating the fishbone diagram is a group exercise that combines brainstorming with a logic tree to reveal root causes related to a specific effect or problem.
Failure Mode and Effects Analysis (FMEA)
FMEA is a systematic process for identifying potential failures before they occur. It evaluates risk by examining possible causes and effects for each step of a process or system.
This proactive analysis drives the development of preventive actions to avoid high-risk failures.
Quality Planning and Design Tools
Quality needs to be built into products and processes from the very beginning during the planning and design phases. Several useful tools aid in translating customer requirements into technical specifications and designs.
Quality Function Deployment (QFD)
Quality Function Deployment is a structured method that captures the “voice of the customer” and translates it into specific technical requirements for products and processes.
It helps ensure customer needs drive the entire design by cascading customer requirements down through the various stages of product planning, design, manufacturing, and delivery. QFD uses a series of matrices to map customer requirements to technical characteristics.
Failure Mode and Effects Analysis (FMEA) as TQM Tools
Failure Mode and Effects Analysis is a risk analysis technique used to identify potential failures in products or processes. For each potential failure mode, it evaluates the severity, likelihood of occurrence, and likelihood of detection.
This allows prioritization of the highest-risk failure modes for prevention and mitigation efforts during design. FMEA is commonly used in industries like automotive, aerospace, and medical devices.
Design of Experiments (DOE) as TQM Tools
Design of Experiments refers to statistical techniques for strategically planning and conducting tests to determine the individual and combined influences of various factors (input variables) on a process output or product characteristic.
DOE provides an efficient method for simultaneously studying multiple factors instead of changing one factor at a time. Common goals are screening factors, optimizing processes, achieving robust designs, and elucidating cause-and-effect relationships.
Process Mapping Tools
Visualizing processes through tools like process flow diagrams, value stream maps, and swim lane diagrams is essential for understanding, analyzing, and improving processes.
These mapping tools identify unnecessary complexity, non-value-added activities, bottlenecks, and opportunities for improvement that should be addressed in new process designs.
By utilizing quality planning and design tools like these, organizations can enhance their ability to meet customer expectations and requirements right from the start. Proactive use of these methods helps prevent issues rather than having to reactively fix problems later on.
Continuous Improvement Tools
At the core of TQM is the concept of continuous improvement (kaizen). This involves constantly looking for ways to improve processes, products, and services. A variety of tools and methodologies are utilized to drive ongoing improvement efforts:
Kaizen Tools
Kaizen is the Japanese term for “improvement” or “change for the better” often integrated with Lean Fundamentals It focuses on making small, incremental changes that accumulate over time. Some common kaizen tools include:
- 5S Methodology – This workplace organization method uses a systematic approach (Sort, Straighten, Shine, Standardize, Sustain) to create a clean, organized, and efficient environment.
- Gemba Walk – Gemba is the “real place” where work happens. Gemba walks involve managers and leaders observing processes firsthand to identify improvement opportunities.
- Kanban System – Kanban is a lean manufacturing scheduling system that visualizes workflow and limits work-in-process to improve efficiency.
Quality Circle Tools
Quality circles are groups of workers who meet regularly to discuss and solve quality issues. Common quality circle tools include:
- Brainstorming – Generating many ideas in a short timeframe to explore solutions.
- Affinity Diagrams – Organizing ideas into related groups/themes for further analysis.
- Process Mapping – Creating visual representations of workflows to identify redundancies or waste.
By empowering employees and promoting continuous learning, these tools help ingrain the philosophy of incremental improvement into an organization’s culture.
Implementation and Integration of TQM Tools
Implementing TQM tools across an organization requires a structured approach and integration with existing processes.
Successful implementation hinges on gaining buy-in from all levels, providing comprehensive training, and making quality a core part of the organizational culture.
Training Programs
Rolling out new TQM tools necessitates developing robust training programs for employees, including comprehensive Six Sigma certification programs to build advanced problem-solving skills.
Training can take various forms like classroom sessions, online courses, workshops, and on-the-job coaching. It’s important to make training an ongoing process to reinforce concepts and share best practices.
Change Management within TQM Tools
Introducing new quality tools inevitably leads to changes in processes, roles, and responsibilities. Managing this change is crucial for smooth implementation.
Leaders must communicate the rationale, expected benefits and provide support to navigate the transition. Celebrating small wins and recognizing champions can help build momentum.
Integration with Existing Systems
For maximum effectiveness, TQM tools need to be integrated with the organization’s existing quality management systems, IT infrastructure, and business processes.
This could involve modifying enterprise software, redefining workflows, updating documentation, and more. Cross-functional collaboration is key to identifying and resolving integration issues.
Performance Tracking with TQM Tools
Implementing new tools is just the first step – tracking their performance is equally vital. Organizations should establish metrics to measure the tools’ impact on quality, productivity, cost savings, and customer satisfaction.
Regular reviews allow for course correction and continuous improvement of the implementation approach.
Cultural Transformation
At its core, TQM implementation requires a cultural shift that prioritizes quality in every process and decision.
Leaders must relentlessly reinforce this through policies, incentives, and leading by example. Creating an environment of trust, empowerment, and collaboration enables employees to fully embrace TQM principles.
SixSigma.us offers both Live Virtual classes as well as Online Self-Paced training. Most option includes access to the same great Master Black Belt instructors that teach our World Class in-person sessions. Sign-up today!
Virtual Classroom Training Programs Self-Paced Online Training Programs