What is the Theory of Constraints? A Comprehensive Guide
Constraints impose unintended impediments within complex systems. However, through comprehensive viewpoints and impediment prioritizations, unprecedented heights emerge.
Across production facilities and beyond, proven frameworks surface constraints systematically, propelling successes consistently.
Of course, fruitful implementations involve challenges. Resistance overturnings, continuous betterment mindsets cultivation, and refinement technique strategizing hold importance for sustainability and impacts enduringly.
Complementary integrations with other tested methods construct robust, holistic advancement structures leveraging each strength comprehensively.
A beacon emerges, furnishing practical, validated pathways towards unparalleled operations, profits, and maintained differentiations advantageously. Embrace its empowerment confidently, and the organizations’ full gifts are exposed boundlessly.
Key highlights
- Understand the essence of the Theory of Constraints and its systemic approach to problem-solving
- Explore the concept of constraints, including bottlenecks, throughput, and limiting factors
- Master the Five Focusing Steps: a structured approach to identifying, exploiting, and eliminating constraints
- Delve into core TOC principles, such as throughput accounting and global vs. local optimization
- Discover applications of TOC beyond manufacturing, including project management and business processes
- Learn how to integrate TOC with lean and Six Sigma methodologies for a holistic improvement strategy. For teams seeking structured frameworks, enrolling in Six Sigma certification programs (Green Belt, Black Belt) can deepen expertise in constraint resolution and process optimization.
- Gain insights into overcoming resistance and fostering a culture of continuous improvement within your organization
- Explore tactics and best practices for successful TOC implementation, including training, software solutions, and constraints accounting
Understanding the Theory of Constraints
As we embark on our journey to unravel the intricacies of the Theory of Constraints (TOC), it is essential to acknowledge the visionary mind behind this groundbreaking management philosophy – Eliyahu M. Goldratt.
Through his seminal work, “The Goal”, published in 1984, Goldratt introduced a paradigm shift in how organizations approach process improvement and resource optimization.
The Theory of Constraints is a process of ongoing improvement that challenges traditional thinking and encourages a systemic approach to problem-solving.
It recognizes that every system, be it a manufacturing line, a service operation, or a project workflow, is bound by at least one constraint – a bottleneck or limiting factor that impedes progress and hinders the achievement of desired goals.
What is a Constraint?
In the context of TOC, a constraint is anything that restricts a system from achieving its maximum throughput or performance.
It can manifest in various forms, such as a bottleneck in a production line, a policy or procedure that inhibits efficiency, or a lack of critical resources.
Constraints can be physical, such as a piece of equipment with limited capacity, or non-physical, like market demand or organizational culture.
The concept of throughput is central to understanding constraints. Throughput refers to the rate at which a system generates revenue or achieves its desired output.
By identifying and addressing constraints, organizations can maximize their throughput, ultimately leading to increased profitability and operational excellence.
Constraints are often accompanied by variations and waste, which further exacerbate their impact on system performance.
Variations in process inputs, resource availability, or demand patterns can amplify the effects of constraints, while waste, such as excess inventory or unnecessary steps, can drain resources and hinder efficiency.
The Five Focusing Steps of the Theory of Constraints (TOC)
To effectively navigate the constraint-elimination journey, TOC offers a structured, five-step process known as the Five Focusing Steps.
These steps provide a roadmap for organizations to methodically identify, exploit, and ultimately eliminate constraints, fostering a culture of continuous improvement.
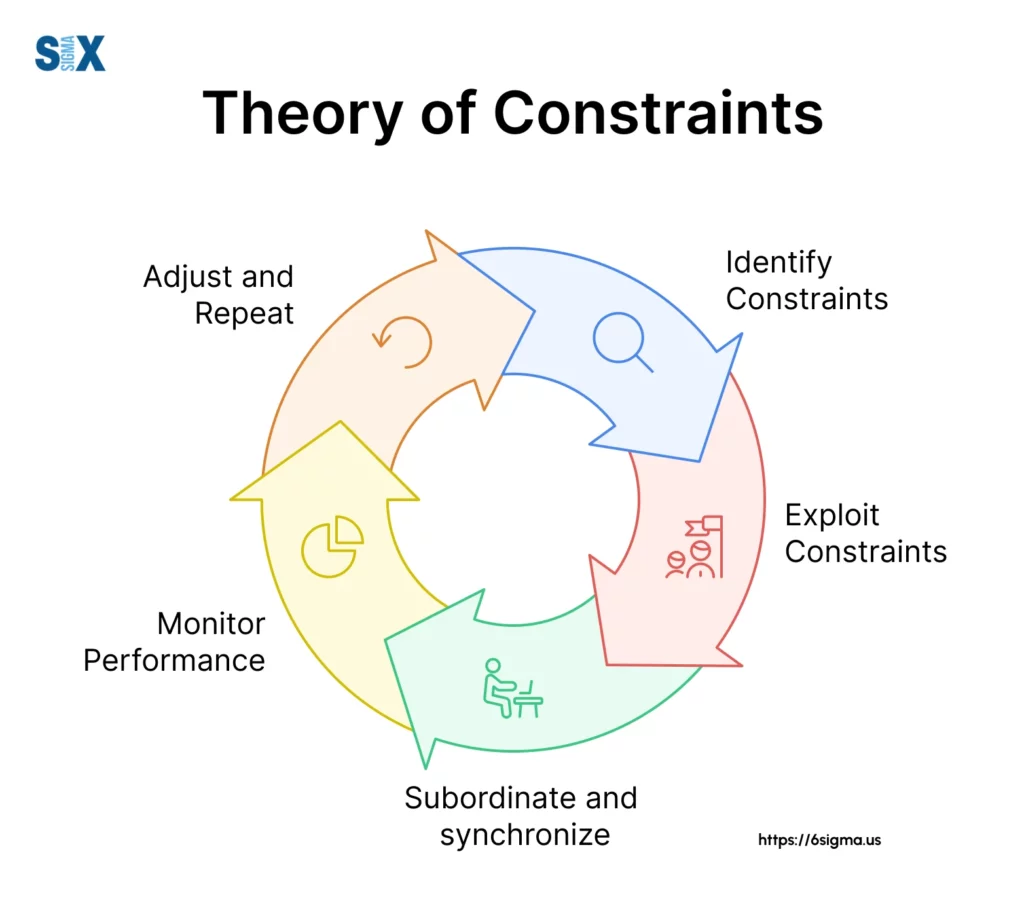
Identify the Constraint
The first step in the TOC process is to identify the current constraint – the bottleneck or limiting factor that is impeding the system’s performance.
This can be achieved through various techniques, such as bottleneck analysis, root cause analysis training, or the use of the Current Reality Tree (CRT), a tool that helps visualize the interconnected causes and effects of a problem.
By pinpointing the constraint, organizations can focus their efforts and resources on the most critical area, maximizing the potential for improvement and avoiding ineffective optimization of non-constraints.
Exploit the Constraint
Once the constraint has been identified, the next step is to exploit it – to maximize its capacity and throughput using existing resources.
This might involve implementing best practices from lean methodologies, such as continuous operation, setup time reduction, or quality improvement initiatives.
The goal is to wring out every ounce of potential from the constraint without incurring significant additional costs or investments.
By exploiting the constraint, organizations can quickly realize performance gains and lay the foundation for further improvements.
Subordinate to the Constraint
In this step, the focus shifts to aligning all non-constraint processes and activities to support and subordinate themselves to the needs of the constraint.
This is where the Drum-Buffer-Rope (DBR) methodology comes into play, a scheduling technique that synchronizes the entire system with the pace set by the constraint, or the “drum”.
By subordinating non-constraints to the constraint, organizations can minimize waste, reduce inventory levels, and ensure a smooth flow of materials or information throughout the system, ultimately improving overall efficiency and throughput.
Elevate the Constraint
If the previous steps have been successful in maximizing the constraint’s performance, but it remains a bottleneck, organizations may need to elevate or eliminate the constraint.
This often involves investing in additional resources, such as upgrading equipment, hiring more personnel, or implementing automation solutions like Jidoka (intelligent automation).
While this step may require capital investment, it is crucial to ensure that the investment is targeted at the true constraint and aligned with the organization’s strategic objectives.
Elevating the constraint can unlock significant performance improvements and pave the way for the identification and resolution of new constraints.
Repeat the Process
The Theory of Constraints is a continuous improvement cycle, and organizations must remain vigilant to avoid complacency or inertia.
Once a constraint has been successfully elevated or eliminated, a new constraint will inevitably emerge, and the process must be repeated to identify and address this new bottleneck.
By embracing a mindset of ongoing improvement and consistently applying the Five Focusing Steps, organizations can foster a culture of excellence and sustain their competitive edge in an ever-changing business landscape.
Core Measures and Principles of the Theory of Constraints (TOC)
To support the effective implementation of the Theory of Constraints, Goldratt introduced a set of core measures and principles that serve as a foundation for decision-making and performance evaluation.
Throughput Accounting with the Theory of Constraints
Traditional cost accounting methods often fail to capture the true drivers of profitability and can lead organizations to make suboptimal decisions.
Throughput Accounting, a central tenet of TOC, offers an alternative approach that focuses on three key measures: throughput, operating expense, and investment (inventory).
Throughput represents the rate at which a system generates revenue or achieves its desired output while operating expense refers to the costs associated with turning inventory into throughput. Investment, or inventory, encompasses all the money tied up in physical assets, such as raw materials, work-in-process, and finished goods.
By prioritizing decisions that increase throughput, reduce operating expenses, and minimize investment, organizations can align their actions with the ultimate goal of maximizing profitability and efficiency.
Underlying Theory
Beyond the practical application of the Five Focusing Steps and Throughput Accounting, the Theory of Constraints is underpinned by several fundamental principles that shape its systemic approach to problem-solving.
One key principle is the recognition of interdependencies within a system.
Rather than viewing processes or components in isolation, TOC acknowledges that changes in one part of the system can have ripple effects throughout the entire organization.
Another core concept is the distinction between constraints and non-constraints.
By focusing improvement efforts on constraints, organizations can maximize their impact and avoid wasting resources on optimizing non-constraints, which may yield marginal or negligible benefits.
Additionally, TOC emphasizes the importance of global optimization over local optimization.
While it may be tempting to optimize individual processes or departments, this approach can lead to sub-optimization and potentially conflict with the overall system’s performance.
TOC encourages a holistic, system-wide perspective to ensure alignment and synergy across all operations.
Applications of Theory of Constraints (TOC) Beyond Manufacturing
While the Theory of Constraints was initially developed with a focus on manufacturing environments, its principles and methodologies have proven to be equally applicable and valuable across a wide range of industries and domains.
Project Management
In the realm of project management, TOC principles can be leveraged to identify and mitigate constraints that impede project progress and success.
The Critical Chain Project Management (CCPM) methodology, an extension of TOC, addresses resource constraints, risk management, and project buffer management, enabling project teams to deliver on time and within budget.
By identifying and eliminating constraints related to resource availability, skill gaps, or interdependencies between project tasks, project managers can streamline workflows, minimize delays, and maximize the utilization of critical resources.
Thinking Processes and the Theory of Constraints
In addition to the Five Focusing Steps, the Theory of Constraints offers a set of Thinking Processes – powerful problem-solving tools that aid in the identification and resolution of constraints.
These processes include the Current Reality Tree (CRT), the Future Reality Tree (FRT), the Evaporating Cloud (EC), and the Transition Tree (TT).
The Thinking Processes provide a structured approach to problem analysis, enabling organizations to uncover the root causes of constraints, evaluate potential solutions, and develop actionable strategies for implementation.
By leveraging these tools, organizations can navigate complex challenges with greater clarity and efficacy, fostering a culture of continuous learning and improvement.
Integrating the Theory of Constraints (TOC) with Lean and Six Sigma
While the Theory of Constraints offers a comprehensive framework for process improvement, it can be further enriched by integrating it with other proven methodologies, such as Lean and Six Sigma.
Contrasting Approaches
At first glance, the Theory of Constraints and Lean methodologies may appear to have contrasting approaches.
Lean primarily focuses on waste elimination and the creation of value from the customer’s perspective, while TOC emphasizes the identification and resolution of constraints to maximize throughput.
However, these two philosophies share a common goal: improving organizational performance and profitability.
Lean achieves this by minimizing non-value-added activities and optimizing process flow, while TOC zeroes in on the most significant bottlenecks impeding system performance.
Advanced practitioners, such as those with Six Sigma Black Belt certification, can design hybrid strategies that align TOC buffers with statistical process control for maximum efficiency.”
Additionally, Lean and TOC differ in their approach to inventory management.
Lean advocates for minimizing inventory levels through just-in-time (JIT) and pull systems, while TOC recognizes the need for strategic buffer inventories to protect constraints and ensure a smooth flow of materials or information.
Synergies and Tools
Despite these differences, Lean and TOC can be seamlessly integrated, leveraging the strengths of each methodology to create a holistic and robust improvement strategy.
Value stream mapping, a core Lean tool, can be used to visualize and analyze process flows, helping to identify potential constraints that TOC can then address.
Moreover, Lean principles and tools, such as 5S (Sort, Set in Order, Shine, Standardize, and Sustain) and visual management, can be applied to the constraint itself, further enhancing its performance and reducing waste.
By combining the constraint-focused approach of TOC with Lean’s emphasis on waste elimination and process optimization, organizations can achieve a synergistic effect, maximizing throughput while minimizing non-value-added activities and maintaining a relentless pursuit of perfection.
Making Theory of Constraints (TOC) Work in Your Organization
Implementing the Theory of Constraints is not merely a technical endeavor; it requires a fundamental shift in mindset and a sustained commitment to change throughout the organization.
Overcoming Resistance
One of the greatest challenges in adopting TOC lies in overcoming resistance and breaking free from entrenched paradigms and organizational inertia.
Paradigm constraints, deeply ingrained beliefs or practices that limit an organization’s ability to embrace change, can be formidable obstacles.
Effective change management and employee engagement are crucial in overcoming these barriers.
Leaders must communicate the value and benefits of TOC, foster a culture of continuous improvement, and provide comprehensive training and coaching to equip employees with the necessary knowledge and skills.
By actively involving frontline employees in the improvement process and celebrating successes, organizations can build momentum and create a shared sense of ownership, paving the way for sustained commitment to the Theory of Constraints.
Choosing Tactics
When it comes to implementing TOC, organizations have a range of tactics and strategies at their disposal.
Training and coaching programs, such as Six Sigma Green Belt certification or Lean Introduction workshops, can equip employees with the necessary skills to exploit constraints and reduce waste systematically
Additionally, embracing constraints accounting, a methodology that aligns financial accounting practices with TOC principles, can reinforce the organization’s commitment to maximizing throughput and minimizing inventory and operating expenses.
By carefully selecting and tailoring the appropriate tactics to their unique circumstances, organizations can create a roadmap for successful TOC implementation, fostering a culture of continuous improvement and driving sustained profitability and growth.
Conclusion
Theory of Constraints represents monumental perspective recalibrations for enterprises approaching refinement and resource optimization.
By embracing system-wide viewpoints and prioritizing impediments’ removals, organizations unlock hitherto unattained excellence heights.
Across producing facilities, services, and project administration environments alike, TOC principles and methodologies prove efficacy time and again.
However, achieving fruitful TOC implementations presents challenges undoubtedly.
Overturning resistance, cultivating continual betterment mindsets, and strategically selecting refined techniques hold prime import ensuring sustainabilities and impacts enduringly.
By integrating TOC complementarily with methodologies like Lean and Six Sigma, enterprises construct robust, holistic refinement frameworks leveraging each philosophy’s strengths in driving waste eliminations, optimized processes, and constraint resolutions comprehensively.
Theory of Constraints emerges as a beacon, furnishing practical, proven paths towards operational excellence, profitability, and maintained competitive differentiations. Embrace TOC’s empowerment, then grasp enterprises’ full gifts boundlessly.
SixSigma.us offers both Live Virtual classes as well as Online Self-Paced training. Most option includes access to the same great Master Black Belt instructors that teach our World Class in-person sessions. Sign-up today!
Virtual Classroom Training Programs Self-Paced Online Training Programs