Lean Manufacturing – Takt Time vs. Cycle Time vs. Lead Time. A Definitive Guide
Takt time is about production speed to match clients’ consumption rates. It safeguards productions stay in market synch.
Cycle time measures precise moments devoted to finishing manufacturing from commence to endpoint. This finds bottlenecks and boosts throughput.
The lead time contains client requests’ entire tenure spanning submittal, output, and delivery. It surrounds procuring through shipping durations comprehensive.
Monitoring these metrics allows pinpointing inefficiencies, refining techniques, and furnishing client-centered, unraveled solutions equitably and punctually.
Key Highlights
- Three handy timers exist in production needing streamlined workflows: takt time, cycle time, and lead time.
- Takt time signifies necessary crafting speeds tallying consumer rhythms precisely.
- Cycle time quantifies each output’s precise fabrication span.
- Lead time incorporates request reception, production, and shipment—from inquiry through shipping fully.
- Grasping/managing these lean methods empowers to spot sticking points, rework wasteful moments, and optimize techniques thoroughly.
What are Takt Time vs Cycle Time vs Lead Time?
In lean manufacturing, three things let businesses assess techniques and optimize workflows: takt time, cycle time, and lead time.
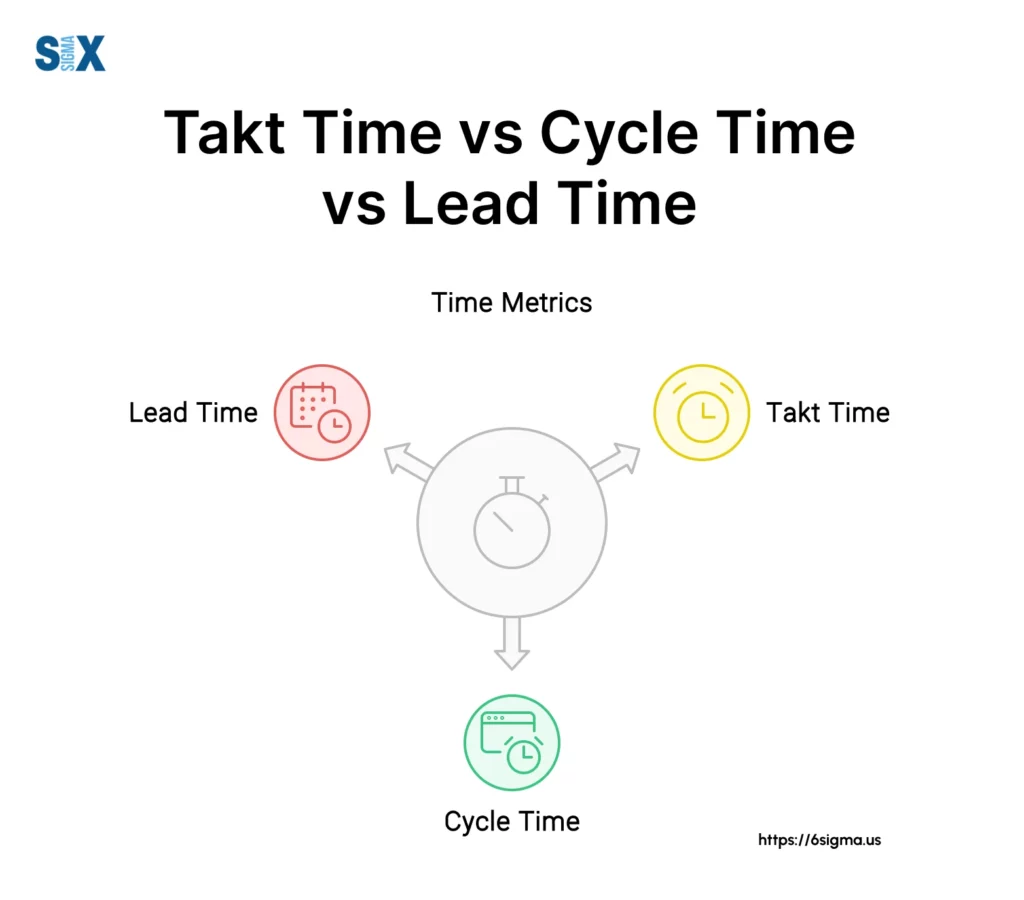
While sounding similar, they mean different things that aid workflow management in different ways.
Takt time centers production around what consumers grab, fixing necessary production speed.
Cycle timing observes each process’ full period from go to completion, containing all steps.
Lead time covers whole order fulfillment from order placement to delivering completed goods or services.
Takt time speeds up production. Cycle time examines specific processes. Lead time represents total turnaround embracing procurement through shipping.
Monitoring these metrics allows for spotting bottlenecks, streamlining operations, and enhancing consumer satisfaction through continuous modification.
Calculating Takt Time
Takt time is a critical lean manufacturing metric that allows you to match production with customer demand. It represents the maximum amount of time allowed to produce one unit to meet demand.
The takt time calculation is:
Takt Time = Available Working Time / Required Output
Available Working Time is the net time available for production after subtracting breaks, meetings, etc. Required Output is the number of units needed to meet customer demand over that period.
For example, if a factory operates for 480 minutes per shift (8 hours) with 60 minutes of breaks, and they need to produce 200 units to meet demand, the calculation would be:
Available Working Time = 480 minutes – 60 minutes = 420 minutes
Takt Time = 420 minutes / 200 units = 2.1 minutes per unit
This means the process should produce one unit every 2.1 minutes to perfectly align production with demand that shifts.
Takt time provides the critical “pulse” that manufacturing processes should follow. By producing units at this takt rate, inventory will match demand without excess overproduction or underproduction.
Factors like process cycle times, transfer batches, and line balancing must be designed around achieving this takt rate. Calculating and displaying takt times gives teams a cadence to synchronize their efforts.
Measuring and Optimizing Cycle Time
Cycle time refers to the total time required to complete one cycle of an operation or process from start to finish. Accurately measuring and optimizing cycle time is crucial for improving manufacturing efficiency and productivity.
Measuring Cycle Time
There are several methods for measuring cycle time in a manufacturing process:
- Time study: Directly observe and time the process cycle using a stopwatch or video recording. Break it down into individual elements.
- Cycle time data collection: Install sensors or utilize manufacturing execution systems to automatically track and log cycle times.
- Value stream mapping: Map out the entire value stream and analyze cycle times for each process step.
Once cycle times are measured, analyze the data to identify bottlenecks, variability, or non-value-added activities prolonging the cycle. Statistical process control methods can help monitor cycle time performance.
Optimizing Cycle Time
Some strategies to reduce and optimize cycle times include:
- Line balancing: Redistribute workloads across workstations to balance cycle times.
- Automation: Automate lengthy manual tasks to reduce cycle times.
- Lean methods: Implement lean tools like 5S, kanban, and mistake-proofing to eliminate waste.
- Setup reduction: Apply SMED (Single-Minute Exchange of Dies) to reduce changeover times.
- Workforce training: Train operators on cycle time best practices and process standardization.
- Quality improvement: Reduce rework and defects through robust quality systems.
Continuously monitoring cycle time data and applying iterative improvements is key to driving down cycle times. Shorter, more optimized cycle times enable increased manufacturing throughput and productivity.
Understanding Lead Time Components
Lead time refers to the total time it takes to complete a process from start to finish. In a manufacturing context, lead time encompasses the entire duration from when a customer order is received until the finished product is delivered. Lead time consists of several key components:
Processing Time
Processing time, or value-added time, refers to the time spent transforming raw materials into the final product. This includes activities like machining, assembly, testing, and packaging. Processing time directly adds value to the product.
Queue Time
Queue time is the non-value-added time that a product spends waiting to be processed, whether it’s waiting for resources, materials, equipment availability, or other constraints. Minimizing queue time is crucial for improving lead time and throughput.
Move Time
Move time accounts for the time spent transporting materials, work-in-process, or finished goods between processes or locations within the facility. Optimizing material flow can reduce unnecessary move time.
Inspection Time
Inspection time is the duration spent on quality control activities, including receiving inspections, in-process inspections, and final inspections. While necessary, inspection time is typically considered non-value-added.
Order Handling Time
Order handling time encompasses administrative tasks like processing customer orders, scheduling production, generating documentation, and coordinating logistics. Streamlining these processes can positively impact lead time.
By understanding the various components that make up lead time, manufacturers can identify opportunities for improvement and implement strategies to reduce non-value-added time, thereby shortening overall lead times and enhancing operational efficiency.
Lean Manufacturing and Process Optimization
Takt time, cycle time, and lead time are all critical metrics in lean manufacturing principles and process optimization efforts.
Lean focuses on maximizing value and minimizing waste across the entire value stream. Understanding and improving these time metrics is key to achieving leaner, more efficient production flows.
Value stream mapping is an essential lean tool for analyzing and designing a future state with improved material and information flows.
By mapping out value-adding and non-value-adding activities, manufacturers can identify bottlenecks, sources of variability, and opportunities for lead time reduction. Cycle time analysis and monitoring process cycle time variability enable targeted improvements.
Just-in-time (JIT) manufacturing aims to produce the right part at the right time in the right amount. Properly calculated takt times ensure production matches customer demand rates, avoiding excess inventory or underproduction.
JIT also requires extremely low variability in cycle times across processes to maintain production flow synchronization.
Production line balancing is another lean technique focused on aligning the cycle times of each process step or workstation with the takt time.
Lines must be balanced to the bottleneck operation’s cycle time. Unbalanced lines result in waiting time waste, increasing overall lead times.
Implementing lean methods like continuous flow, pull systems, setup time reduction, total productive maintenance, and mistake-proofing improves manufacturing cycle efficiency.
These reduce the non-value-adding time from processes and enable tighter synchronization to takt times.
Best Practices for Improving Takt Time, Cycle Time, and Lead Time
Optimizing takt time, cycle time, and lead time is crucial for achieving lean manufacturing principles and maximizing production efficiency. Here are some best practices to consider:
Value Stream Mapping
Value stream mapping is a lean technique that helps visualize the entire production flow and identify areas of waste or inefficiency. By mapping out the value stream, you can pinpoint bottlenecks, excess inventory, and unnecessary steps that contribute to longer cycle times and lead times.
Production Line Balancing
Unbalanced workloads across workstations can lead to bottlenecks and increased cycle times. Production line balancing aims to distribute tasks evenly among workstations, ensuring a smooth production flow and minimizing idle time.
Just-in-Time (JIT) Manufacturing
JIT manufacturing is a lean philosophy that focuses on producing only what is needed when it is needed, and in the required quantities. By implementing JIT principles, you can reduce excess inventory, minimize lead times, and improve overall process cycle time.
Continuous Improvement (Kaizen)
Embracing a culture of continuous improvement is essential for sustaining takt time, cycle time, and lead time optimization efforts. Encourage employees to identify and eliminate waste, streamline processes, and implement incremental improvements on an ongoing basis.
Standardized Work Instructions
Clearly defined and standardized work instructions help reduce variability in cycle times and ensure consistent quality. Provide comprehensive training and regularly review and update work instructions to reflect process improvements.
Preventive Maintenance
Unplanned equipment downtime can significantly disrupt production flow and increase cycle times. Implement a preventive maintenance program to minimize breakdowns and ensure equipment reliability, reducing the risk of production delays.
Data-Driven Decision Making
Collect and analyze data related to takt time, cycle time, and lead time to identify trends, bottlenecks, and areas for improvement. Use this data to make informed decisions and measure the impact of process changes.
Cross-Training and Flexibility
Cross-training employees and promoting workforce flexibility can help mitigate the impact of absenteeism, skill gaps, or workload fluctuations on cycle times. Encourage cross-functional collaboration and knowledge sharing.
Supplier Integration and Collaboration
Collaborate with suppliers to optimize lead times for raw materials and components. Establish clear communication channels, share production schedules, and work together to streamline the supply chain and reduce lead times.
SixSigma.us offers both Live Virtual classes as well as Online Self-Paced training. Most option includes access to the same great Master Black Belt instructors that teach our World Class in-person sessions. Sign-up today!
Virtual Classroom Training Programs Self-Paced Online Training Programs