Supplier Quality Management: A Lean Six Sigma Approach for Proactive Collaboration
Modern businesses face increasing pressure to deliver high-quality products while maintaining cost efficiency and meeting sustainability goals.
Supplier Quality Management (SQM) stands as a crucial element in achieving these objectives, particularly when integrated with Lean Six Sigma methodologies.
SQM represents the systematic approach organizations use to evaluate, monitor, and enhance the quality of products and services provided by their suppliers.
This process has transformed from simple quality checks to a sophisticated system that leverages data analytics, automation, and collaborative partnerships.
Key Highlights
- Six Sigma Integration in SQM
- Digital Quality Management Solutions
- Global Supply Chain Excellence
- Risk Mitigation Strategies
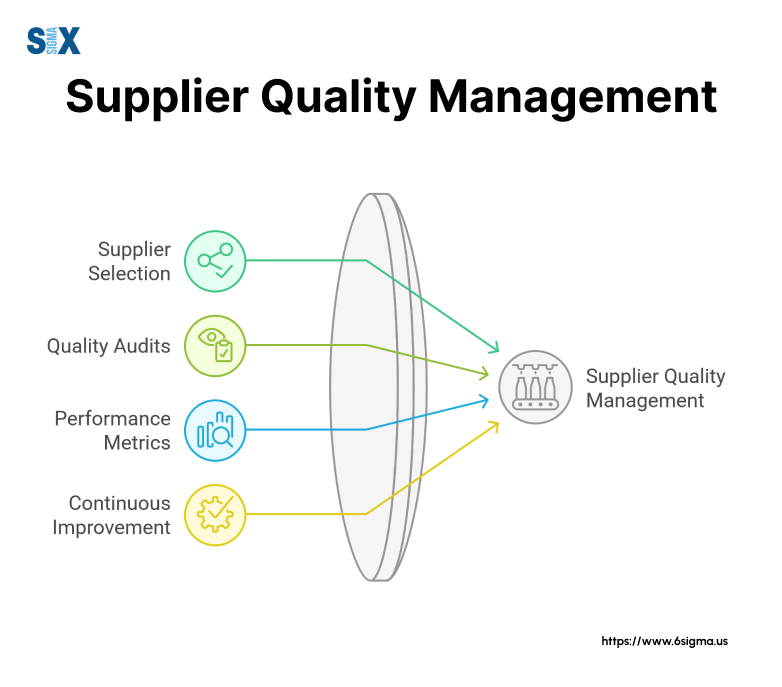
What is Supplier Quality Management?
Supplier Quality Management represents a strategic approach to ensuring product excellence through systematic supplier oversight and collaboration.
This methodology combines quality control measures with performance monitoring to maintain consistent standards across the supply chain.
Organizations implement SQM to reduce defects, minimize risks, and build strong supplier partnerships.
Six Sigma’s Role in Quality Excellence
Six Sigma methodology drives quality improvement in supplier m anagement through data-driven decision making and statistical analysis.
This approach focuses on reducing variations in supplier outputs while maintaining quality standards.
Quality managers use DMAIC (Define, Measure, Analyze, Improve, Control) processes to identify and eliminate defects in supplier deliverables.
The supplier quality system benefits from Six Sigma tools such as:
- Statistical Process Control (SPC) charts
- Failure Mode and Effects Analysis (FMEA)
- Process capability studies
- Root cause analysis techniques
Master the fundamentals of Lean Six Sigma for superior supplier quality management with Lean Six Sigma Overview
Lean Principles in Supplier Quality Management
Lean methodology enhances Supplier Quality Management by eliminating waste and optimizing value streams.
This approach streamlines supplier interactions, reduces lead times, and improves overall efficiency.
Quality engineers focus on creating standardized processes that minimize variability and enhance supplier performance.
Key Lean principles applied to supplier quality include:
- Value stream mapping of supplier processes
- Just-in-time delivery systems
- Standardized work procedures
- Visual management tools
Merging Lean and Six Sigma Approaches
The integration of Lean and Six Sigma creates a powerful framework for Supplier Quality Management.
This combined approach delivers measurable improvements in supplier performance while reducing operational waste.
Supply chain managers utilize both methodologies to achieve optimal results in quality control and process efficiency.
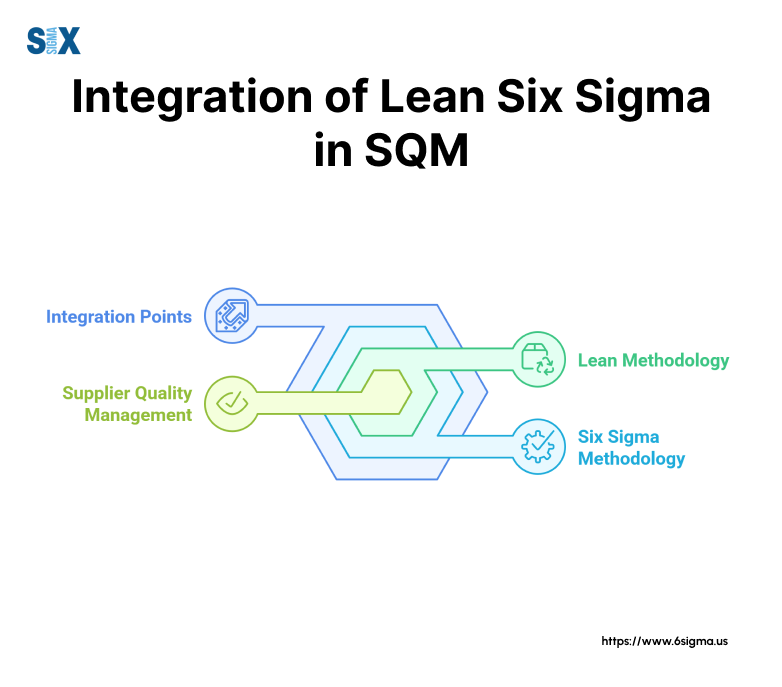
Supply Chain Benefits and Outcomes
Organizations implementing Lean Six Sigma in their supplier quality system experience significant improvements in supply chain performance.
These benefits include reduced defect rates, shorter lead times, and improved supplier collaboration.
Procurement specialists report enhanced supplier reliability and consistent quality outputs through this integrated approach.
Measurable improvements often include:
- Reduced supplier defect rates by 50-70%
- Decreased lead times by 30-40%
- Improved first-pass yield rates
- Enhanced supplier communication efficiency
The combination of Lean and Six Sigma methodologies in Supplier Quality Management creates a robust framework for maintaining high-quality standards while driving continuous improvement throughout the supply chain.
This systematic approach helps organizations build stronger supplier relationships while ensuring consistent product quality.
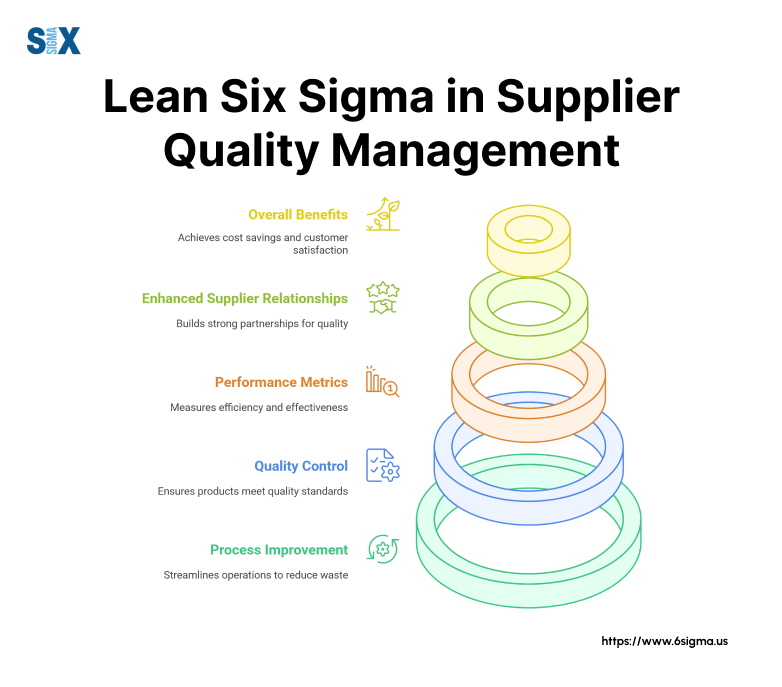
The Role of Lean Six Sigma in Supplier Quality Management
Lean Six Sigma transforms traditional supplier management by introducing data-driven methodologies and process optimization techniques.
This approach strengthens supplier relationships while ensuring consistent quality outputs across the supply chain.
Enhancing Supplier Selection Through Six Sigma
Six Sigma methodologies revolutionize supplier selection by implementing quantifiable criteria and statistical analysis.
Quality managers use tools like supplier scorecards and capability studies to evaluate potential partners.
This systematic approach helps organizations identify suppliers who consistently meet quality standards and demonstrate process control capabilities.
The DMAIC framework guides supplier selection through:
- Defining clear supplier requirements
- Measuring historical performance data
- Analyzing capability metrics
- Improving selection criteria
- Controlling ongoing evaluation processes
Performance Metrics and Quality Indicators
Managing supplier quality requires robust performance measurement systems. Six Sigma tools enable organizations to track key metrics such as:
- First-time quality rates
- On-time delivery performance
- Process capability indices
- Cost of poor quality
- Response time to quality issues
Minimizing Supplier Output Variation
Lean Six Sigma techniques reduce variability in supplier deliverables through statistical process control and standardization.
Quality engineers implement control charts and process capability studies to monitor supplier output consistency. This approach helps identify and address quality issues before they impact production.
Key variation reduction strategies include:
- Process standardization
- Statistical process control
- Root cause analysis
- Corrective action programs
Effective Supplier Communication Channels
Six Sigma methodology streamlines supplier communication by establishing structured channels and standardized reporting protocols.
This systematic approach ensures clear transmission of quality requirements and performance feedback. Supply chain managers utilize digital platforms and automated systems to maintain consistent communication flows.
Communication improvements focus on:
- Real-time quality data sharing
- Automated performance reporting
- Standardized quality alerts
- Regular performance reviews
Digital Integration and Automation with Supplier Quality Management
Modern Supplier Quality Management leverages digital tools and automation to enhance Six Sigma implementation.
Quality management professionals utilize advanced analytics platforms and AI-driven systems to monitor supplier performance in real-time.
These technological solutions enable proactive quality management and faster response to potential issues.
The integration of digital technologies delivers:
- Real-time quality monitoring
- Predictive analytics capabilities
- Automated compliance checking
- Enhanced data visualization
This structured approach to managing supplier quality through Lean Six Sigma creates a foundation for sustainable quality improvement and supplier development.
Organizations that implement these methodologies often see significant improvements in supplier performance and overall quality outcomes.
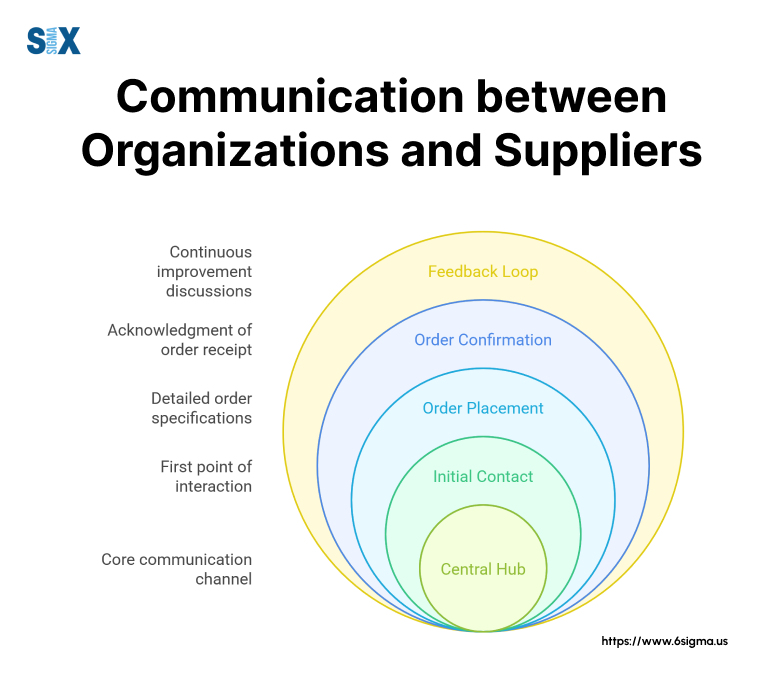
Implementing a Lean Six Sigma-Based Supplier Quality Management System
A successful supplier quality management system requires strategic planning and methodical execution.
Organizations must align their quality objectives with Lean Six Sigma principles to create lasting improvements in supplier performance.
Implementation Roadmap for Quality Excellence
The implementation process follows a structured approach:
Phase 1: Foundation Building
- Assess current supplier quality processes
- Define quality objectives and metrics
- Establish implementation teams
- Create project timelines
Phase 2: System Development
- Design quality control procedures
- Set up data collection methods
- Develop supplier scorecards
- Create communication protocols
Phase 3: Deployment
- Train team members
- Launch pilot programs
- Monitor initial results
- Adjust processes as needed
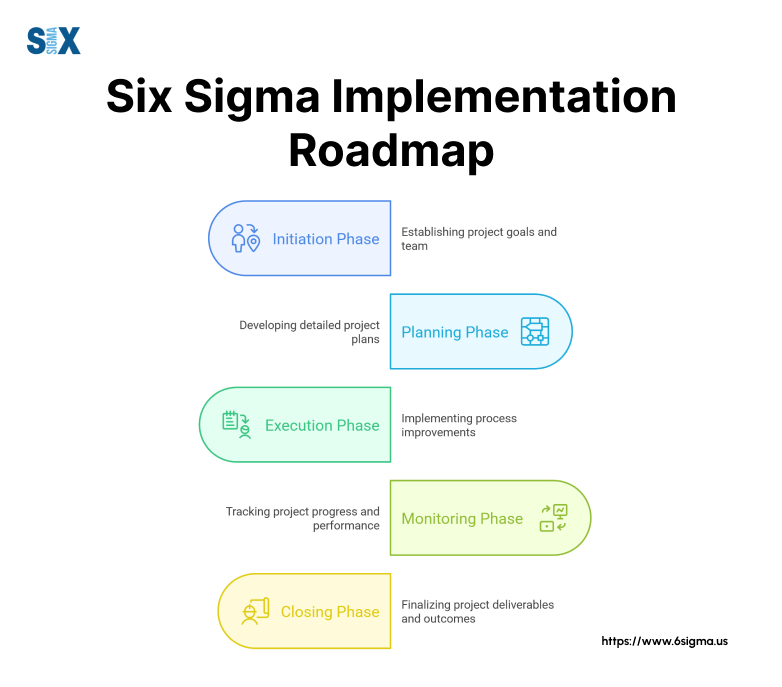
Essential Components of an SQM System
The supplier quality management system consists of several interconnected elements that work together to ensure consistent quality outcomes:
Quality Planning Framework
- Supplier selection criteria
- Performance standards
- Risk assessment protocols
- Quality objectives
Monitoring and Control Systems
- Performance tracking tools
- Statistical process control
- Quality audits
- Corrective action procedures
Communication Infrastructure
- Reporting systems
- Feedback mechanisms
- Documentation requirements
- Collaboration platforms
Lean Six Sigma Tools for Supplier Quality Management
Quality engineers employ specific tools to optimize supplier performance:
DMAIC Tools:
- Process mapping for supplier workflows
- Cause-and-effect analysis
- Statistical process control charts
- Capability studies
Implementation Best Practices for Supplier Quality Management
Successful implementation requires attention to key success factors:
Leadership Engagement
- Executive sponsorship
- Clear communication of objectives
- Resource allocation
- Change management support
Data Management
- Standardized data collection
- Real-time monitoring systems
- Performance analytics
- Reporting automation
Supplier Integration
- Training programs
- Performance feedback
- Continuous improvement initiatives
- Collaborative problem-solving
Digital Transformation Considerations
Modern supplier quality management systems leverage digital technologies:
Quality Management Software
- Automated data collection
- Real-time monitoring
- Performance dashboards
- Document control
Advanced Analytics
- Predictive quality modeling
- Risk assessment tools
- Trend analysis
- Performance forecasting
The implementation of a Lean Six Sigma-based supplier quality management system requires dedication and systematic execution.
Organizations that follow this structured approach while embracing digital transformation create robust quality management systems that deliver sustained improvements in supplier performance.
Remember: Regular system reviews and updates ensure the supplier quality management system remains effective and adapts to changing business needs and technological advances.
Deploy Lean Six Sigma across your supplier network. Learn the strategic framework for organizational success
Proactive Collaboration with Suppliers
Successful supplier quality management demands active partnership between organizations and their suppliers.
This collaborative approach strengthens quality outcomes and drives continuous improvement across the supply chain.
Engaging Suppliers in Six Sigma Programs
Organizations achieve superior results by integrating suppliers into their Six Sigma initiatives.
This integration begins with supplier training programs and extends to joint quality improvement projects.
Quality managers work directly with supplier teams to implement DMAIC methodologies and establish shared quality objectives.
Key integration steps include:
- Supplier Six Sigma training programs
- Joint project team formation
- Shared quality metrics development
- Regular progress reviews
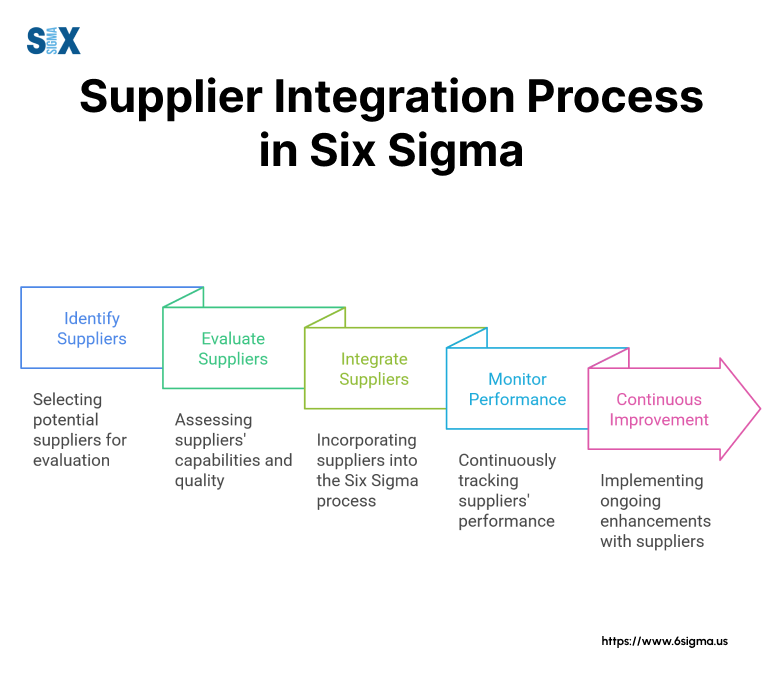
Building Collaborative Problem-Solving Networks
Best practices in supplier quality management emphasize collaborative problem-solving approaches.
This strategy creates a shared responsibility for quality improvements and encourages innovative solutions.
Supply chain managers establish structured frameworks for joint problem identification and resolution.
The collaborative framework includes:
- Cross-functional team formation
- Regular quality review meetings
- Shared data analysis sessions
- Joint root cause investigations
Driving Joint Improvement Initiatives with Supplier Quality Management
Continuous improvement projects benefit from combined organizational expertise and resources.
These joint initiatives focus on specific quality challenges and process improvements. Quality engineers from both organizations work together to:
- Identify improvement opportunities
- Develop action plans
- Implement solutions
- Monitor results
- Document best practices
Knowledge Sharing and Best Practices Exchange
Effective supplier quality management relies on systematic knowledge sharing between organizations.
This exchange creates a learning environment that benefits all parties. Procurement specialists facilitate regular knowledge transfer through:
Best Practice Forums
- Regular workshops
- Success story sharing
- Lesson learned sessions
- Innovation exchanges
Digital Knowledge Platforms
- Online collaboration tools
- Shared documentation systems
- Virtual training programs
- Performance dashboards
Measuring Collaborative Success with Supplier Quality Management
Organizations track the effectiveness of supplier collaboration through specific metrics:
Performance Indicators:
- Joint project completion rates
- Quality improvement outcomes
- Innovation implementation success
- Knowledge sharing participation
- Supplier engagement levels
This proactive approach to supplier collaboration strengthens quality management systems and creates sustainable improvements.
The implementation of these collaborative practices helps organizations build stronger supplier relationships while maintaining high quality standards across the supply chain.
Global Considerations and Challenges in Supplier Quality Management
Modern suppliers quality management faces unique challenges in the global marketplace.
Managing Quality Across Global Supply Networks
Global supply chain quality requires sophisticated management approaches that account for geographical distances and time zones.
Quality managers implement standardized processes while allowing flexibility for local conditions. This balance ensures consistent quality outputs across different regions.
Key global management strategies include:
- Standardized quality protocols
- Local quality team deployment
- Cross-border communication systems
- Cultural adaptation programs
Navigating Regional Compliance Requirements with Supplier Quality Management
Different regions maintain unique regulatory frameworks and compliance standards.
Regional Variations:
- Quality certification requirements
- Documentation standards
- Testing protocols
- Reporting mechanisms
Environmental and Sustainability Integration
Modern supplier quality management emphasizes environmental responsibility and sustainable practices.
Organizations evaluate suppliers based on:
Environmental Criteria:
- Carbon footprint metrics
- Waste reduction programs
- Resource conservation efforts
- Environmental compliance records
Sustainability Measures:
- Renewable energy adoption
- Circular economy practices
- Ethical sourcing policies
- Social responsibility programs
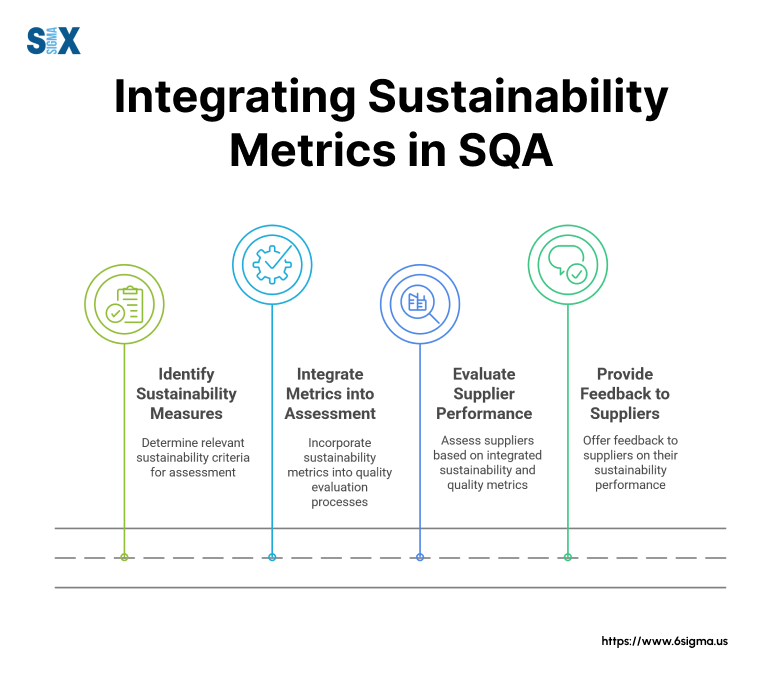
Post-Pandemic Quality Strategies
The global pandemic transformed supplier quality management practices. Organizations now implement enhanced resilience measures:
Risk Mitigation Strategies
- Supply chain diversification
- Local supplier development
- Digital quality monitoring
- Remote audit capabilities
Operational Adaptations
- Virtual quality assessments
- Remote collaboration tools
- Digital documentation systems
- Real-time monitoring platforms
Technology Integration for Global Management
Digital solutions enable effective global supplier quality management through:
Advanced Technologies:
- Cloud-based quality platforms
- AI-powered monitoring systems
- Blockchain traceability
- IoT quality sensors
These global considerations require organizations to maintain flexible yet robust supplier quality management systems.
Success in international markets demands attention to regional variations while maintaining consistent quality standards across the supply chain.
The evolution of global supplier quality management continues as organizations adapt to new challenges and opportunities.
This dynamic environment requires ongoing assessment and adjustment of quality management strategies to ensure sustained success in international markets.
Moving Forward with Supplier Quality Management
The evolution of supplier quality management continues to reshape supply chain operations and quality control practices.
Key Insights for Quality Excellence
Successful supplier quality management programs demonstrate several critical elements. The integration of Lean Six Sigma methodologies provides a structured approach to quality improvement.
Quality managers must focus on:
- Data-driven decision making
- Continuous process improvement
- Supplier relationship development
- Technology integration
- Risk management strategies
Taking Action: Implementation Steps
Organizations ready to enhance their supplier quality management should:
First Quarter:
- Assess current quality processes
- Identify improvement opportunities
- Select appropriate digital tools
- Develop implementation roadmap
Second Quarter:
- Train quality teams
- Deploy pilot programs
- Monitor initial results
- Adjust strategies as needed
Building Long-Term Success
The path to excellence in supplier quality management requires commitment to:
Continuous Learning
- Regular team training
- Best practice updates
- Technology skill development
- Industry standard monitoring
Process Innovation
- Digital transformation initiatives
- Quality tool advancement
- Automation implementation
- Performance optimization
The future of supplier quality management offers exciting opportunities for organizations willing to invest in advanced technologies and innovative practices.
By implementing these strategies, organizations can build robust quality management systems that deliver sustained value and competitive advantage.
SixSigma.us offers both Live Virtual classes as well as Online Self-Paced training. Most option includes access to the same great Master Black Belt instructors that teach our World Class in-person sessions. Sign-up today!
Virtual Classroom Training Programs Self-Paced Online Training Programs