The Shingo Model: A Comprehensive Guide to Operational Excellence
Organizations implementing the Shingo Model principles have reported up to 85% improvement in operational efficiency and a 60% increase in employee engagement, according to recent industry studies.
These aren’t just numbers—they represent a fundamental shift in how businesses approach excellence, even for professionals already familiar with six sigma methodologies.
The Shingo Model stands apart from other operational frameworks by focusing on the cultural foundation of excellence rather than just implementing tools or techniques.
Developed by the Shingo Institute at Utah State University, this model has transformed operations across manufacturing, healthcare, government, and service industries worldwide.
Understand the core roadmap and basic tools needed to start making a difference in your team’s performance.
In this guide, you’ll discover:
- Core principles driving sustainable results
- Culture-behavior-systems connection explained
- Implementation steps for your organization
- Real success stories and lessons learned
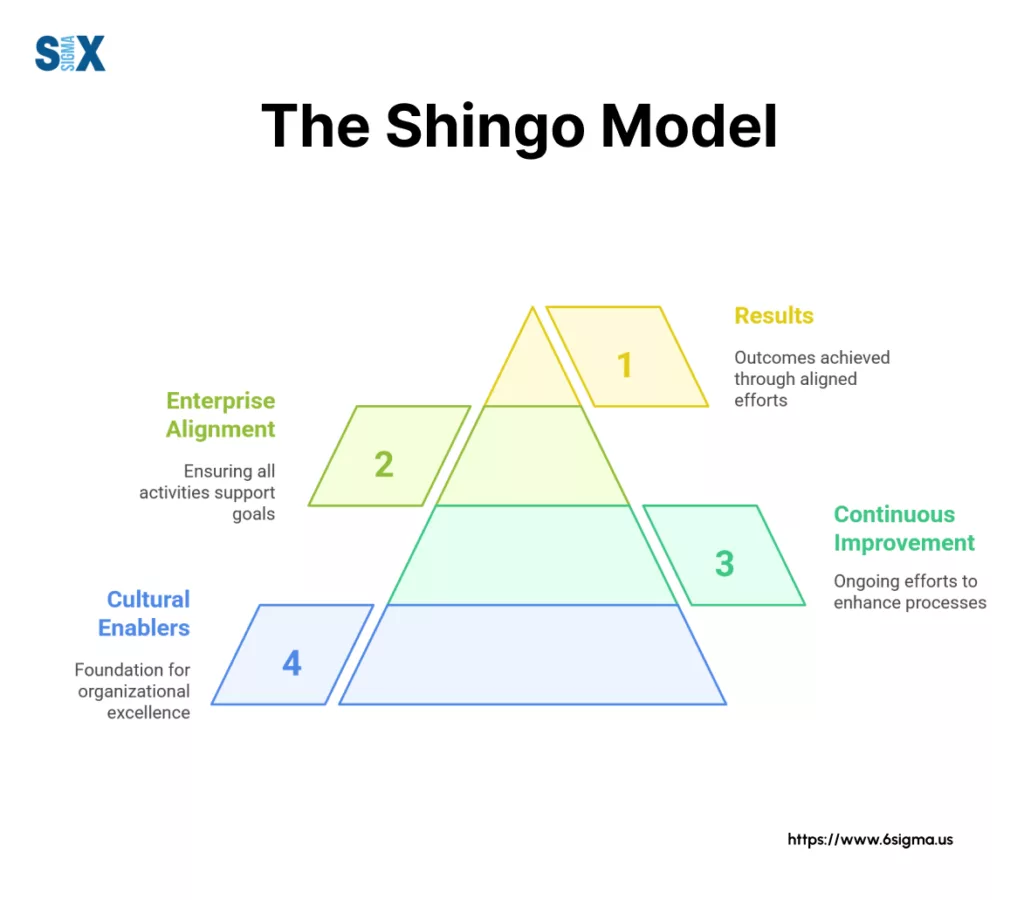
What Is The Shingo Model Foundation?
Dr. Shigeo Shingo revolutionized manufacturing practices long before the Shingo Model took shape.
Born in 1909 in Japan, Shingo worked closely with Toyota during the mid-20th century, where he developed groundbreaking concepts like poka-yoke (mistake-proofing) and SMED (Single-Minute Exchange of Dies).
His innovations helped form the backbone of what we now call the Toyota Production System, which later influenced global lean manufacturing practices.
The transformation from Shingo’s individual contributions to a formal model began in 1988 when Utah State University established the Shingo Prize to recognize excellence in manufacturing.
Initially focused on awarding companies demonstrating lean excellence, the program evolved significantly over the decades.
By the early 2000s, leaders at what became the Shingo Institute realized that sustainable excellence required more than just implementing lean tools—it demanded a principle-centered approach to building culture.
Today, the Shingo Institute serves as the steward of the Shingo Model, offering educational workshops, assessment services, and the prestigious Shingo Prize. The Institute’s research continues to refine the model, making it applicable across diverse industries from healthcare to government services.
This evolution represents a shift from viewing shingo lean techniques as mere tools to understanding them as expressions of deeper principles.
Core Philosophy and Purpose of the Shingo Model
The Shingo Model operates on a simple yet powerful premise: ideal results require ideal behaviors.
Unlike approaches that focus primarily on implementing tools or hitting targets, this model recognizes that sustainable excellence emerges from the daily behaviors of people throughout an organization.
At its foundation, the model defines operational excellence as the consistent delivery of ideal results to all stakeholders.
This achievement depends on systems that drive the right behaviors at every level. Similar to six sigma principles that emphasize data-driven decision making, the Shingo Model provides a structured path to excellence—but with a distinctive focus on cultural transformation.
The model identifies Three Insights of Organizational Excellence that guide implementation:
First, ideal results require ideal behaviors at all levels. Second, purpose and systems drive behavior. Third, principles inform and govern behavior.
These insights form a logical chain: principles inform systems, systems drive behaviors, and behaviors produce results.
What distinguishes shingo operational excellence from other approaches is its emphasis on the “why” behind improvement rather than just the “how.”
Organizations implementing the model learn to move beyond tool-based improvement to build cultures where excellence becomes the natural byproduct of shared beliefs and aligned systems.
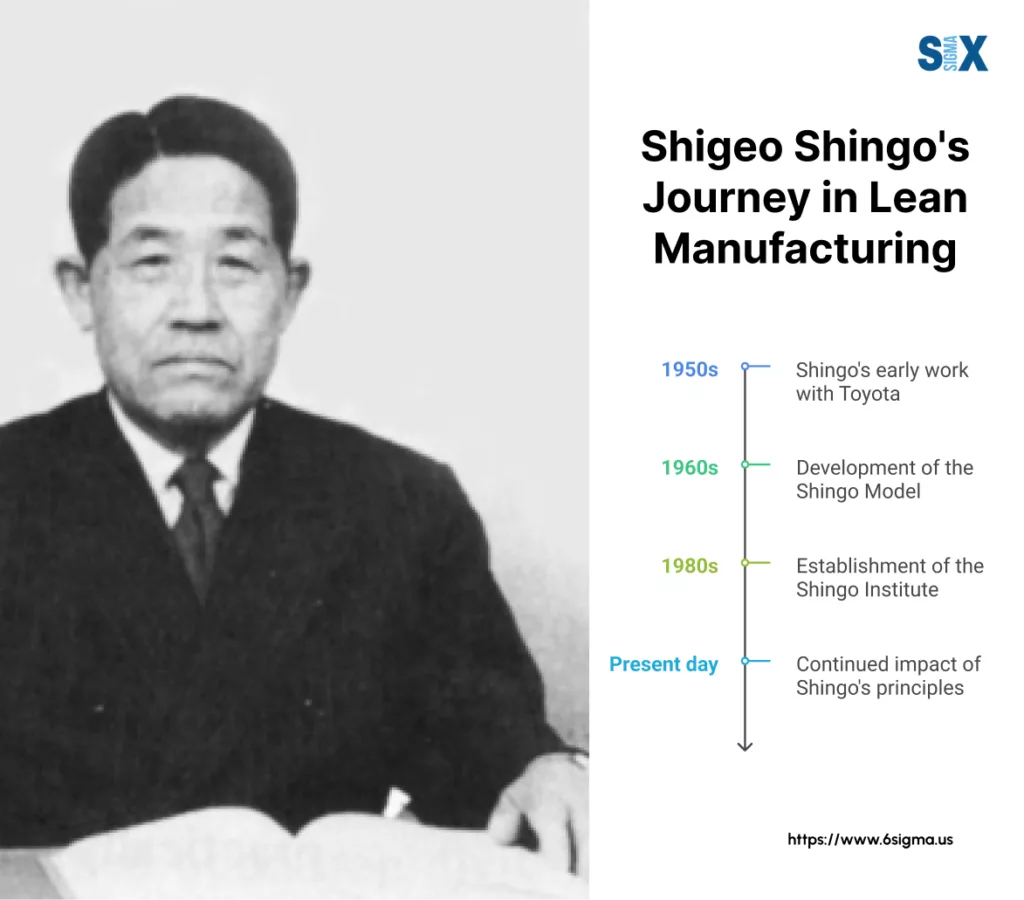
The Shingo Model Framework (The Shingo Diamond)
The Shingo Diamond represents the conceptual heart of the Shingo Model, illustrating how sustainable organizational excellence emerges from the interplay of principles, systems, tools, and results.
Unlike linear improvement frameworks, the diamond shape emphasizes that these elements must remain in balance and alignment.
At the top of the diamond sits “Results,” representing the organization’s goals and performance metrics. The left point contains “Systems,” which include management systems, operational processes, and improvement methodologies.
The right point holds “Tools and Techniques,” encompassing the practical methods used to solve problems and enhance performance.
The bottom point—and foundation—represents “Cultural Enablers,” the principles that shape organizational behavior.
What makes the shingo model particularly powerful is how it maps the transformation process. The diamond illustrates that while tools might produce short-term results, lasting excellence requires systems aligned with principles that foster the right cultural behaviors.
Many organizations make the mistake of implementing tools without addressing the underlying systems or principles, leading to temporary improvements that fade over time.
The cultural transformation process depicted in the diamond follows a specific sequence: principles inform systems, systems drive behaviors, behaviors produce results.
This insight helps leaders understand why improvement initiatives often fail despite using the right tools—they haven’t addressed the systems and principles that drive sustainable behavior change.
Guiding Principles
The Shingo principles form the bedrock of the model, organized into three dimensions that guide organizational transformation.
These aren’t arbitrary rules but universal concepts that, when applied correctly, naturally lead to excellence.
The first dimension, Cultural Enablers, focuses on principles that build a foundation for excellence:
- Respect Every Individual: Recognizing the inherent worth and potential of each person
- Lead with Humility: Leaders who listen, learn, and coach rather than command
The second dimension addresses Continuous Improvement through four key principles:
- Flow & Pull Value: Organizing work to maximize value delivery with minimal waste
- Seek Perfection: Viewing excellence as a journey of ongoing improvement
- Embrace Scientific Thinking: Using data and experimentation to drive decisions
- Focus on Process: Understanding that process quality determines outcome quality
The third dimension, Enterprise Alignment, ensures cohesion throughout the organization:
- Create Constancy of Purpose: Establishing clear direction that guides all activities
- Think Systemically: Recognizing interdependencies between all parts of the organization
- Create Value for the Customer: Focusing all efforts on delivering customer value
These shingo principles work together, complementing fundamentals of Lean while extending beyond them to address the human and cultural aspects of excellence.
Organizations that successfully embed these principles report not just improved operational metrics but transformed workplace cultures where improvement becomes everyone’s responsibility.
The shingo model guides organizations to move beyond tool-focused improvement to principle-centered excellence.
By aligning systems with principles, organizations create environments where the right behaviors—and therefore the right results—emerge naturally rather than through force or temporary compliance.
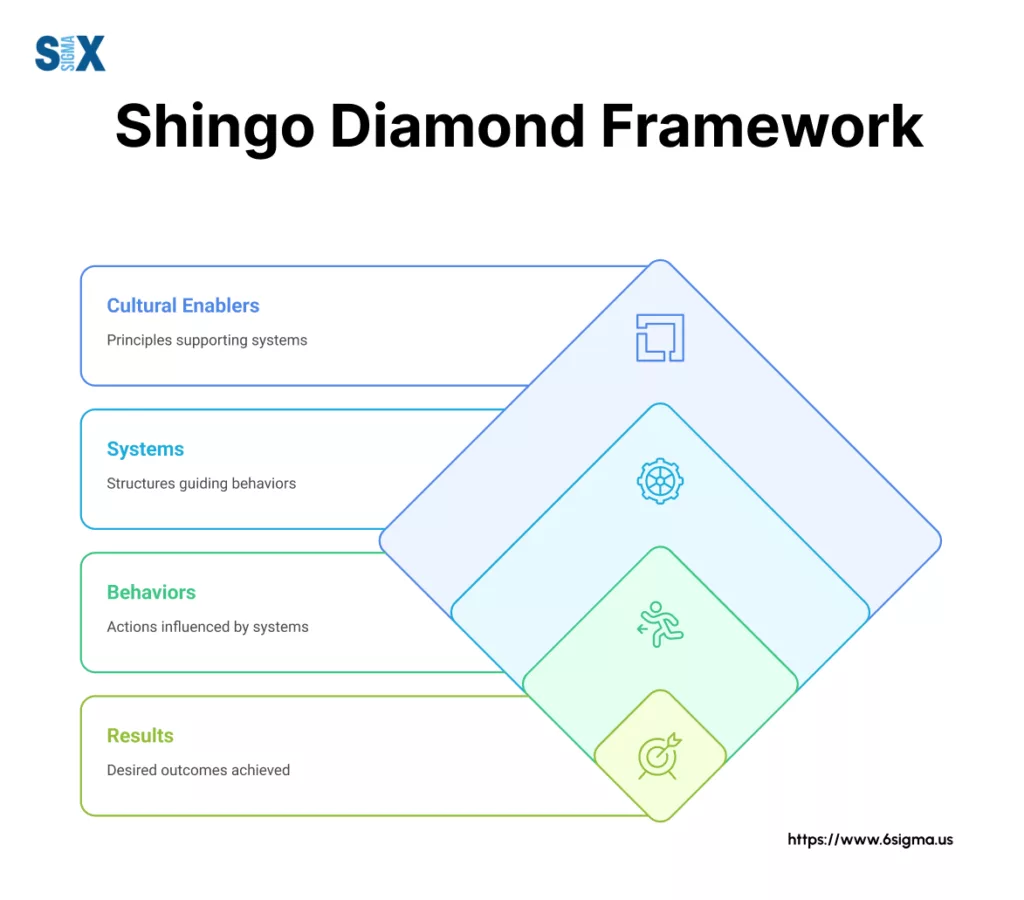
Lead projects that deliver real results with a proven framework
Gain a working knowledge of the Lean Six Sigma roadmap and the analytical methods with Lean Six Sigma Green Belt Certification
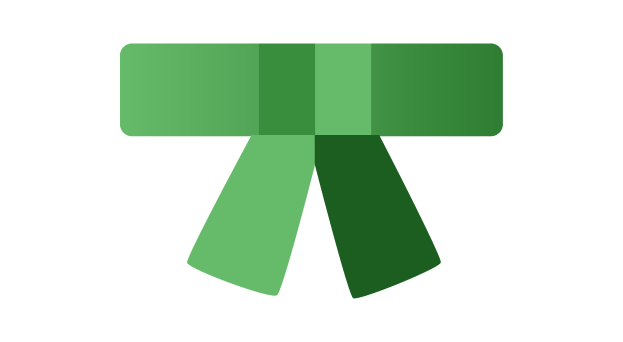
Implementation and Practice
Implementing the Shingo Model requires a structured approach that moves beyond superficial changes to reshape organizational DNA.
The journey typically begins with a thorough assessment of current systems and behaviors against the model’s principles and ideal state.
Most organizations start with the Shingo Model handbook as their guide, which outlines a multi-phase implementation process.
The initial discovery phase involves educating leadership teams about the model’s principles and conducting baseline assessments.
These assessments evaluate how well existing systems align with guiding principles and identify gaps between current and ideal behaviors.
The design phase follows, where cross-functional teams develop system improvements that better align with Shingo principles. This might include redesigning performance metrics, communication channels, leadership practices, and improvement methodologies.
The key difference from traditional improvement efforts is the explicit focus on how these systems will drive ideal behaviors rather than just process outputs.
Implementation occurs in waves, typically starting with pilot areas where leadership commitment is strong. Each area follows a similar pattern: education, assessment, design, implementation, and evaluation.
The Shingo Model handbook emphasizes that this isn’t a program with a finish line but rather a journey of ongoing learning and refinement.
Throughout implementation, different roles carry specific responsibilities:
- Executives establish vision, remove barriers, and model ideal behaviors
- Middle managers align systems and coach teams on principle application
- Frontline leaders facilitate daily improvement and reinforce behaviors
- Associates engage in improvement and provide feedback on systems
Behavioral Benchmarks of the Shingo Model
The Shingo Model distinguishes itself by defining clear behavioral benchmarks that indicate principle adoption.
These benchmarks provide tangible evidence that principles are truly embedded rather than just posted on walls or mentioned in meetings.
For leaders, ideal behaviors include regularly going to the gemba (workplace), asking questions rather than giving answers, celebrating failures as learning opportunities, and demonstrating respect through actions.
Middle managers demonstrate principle adoption when they develop people’s capabilities, make decisions based on principles rather than expedience, and align systems to support ideal behaviors.
Frontline associates exhibit ideal behaviors when they identify and solve problems without waiting for direction, speak openly about issues, take ownership of quality, and actively participate in improvement activities.
The Shingo Model provides detailed behavioral examples for each principle across different organizational roles.
Cultural indicators serve as measurable proxies for these behaviors. These might include the number of employee-generated improvements, response times to quality issues, cross-functional collaboration metrics, or how decisions are documented against principles.
Many organizations utilizing root cause analysis techniques find that behavioral patterns often reveal deeper system issues that require adjustment.
Measurement methods combine quantitative metrics with qualitative assessment. The Shingo Institute’s assessment methodology includes structured observations, interviews across organizational levels, system reviews, and result analysis.
Organizations often develop custom assessment tools based on the Shingo Model handbook that fit their specific context while maintaining alignment with the model’s principles.
The most successful implementations create feedback loops where behavioral observations inform system adjustments, creating a virtuous cycle of improvement that drives the organization toward ideal performance.
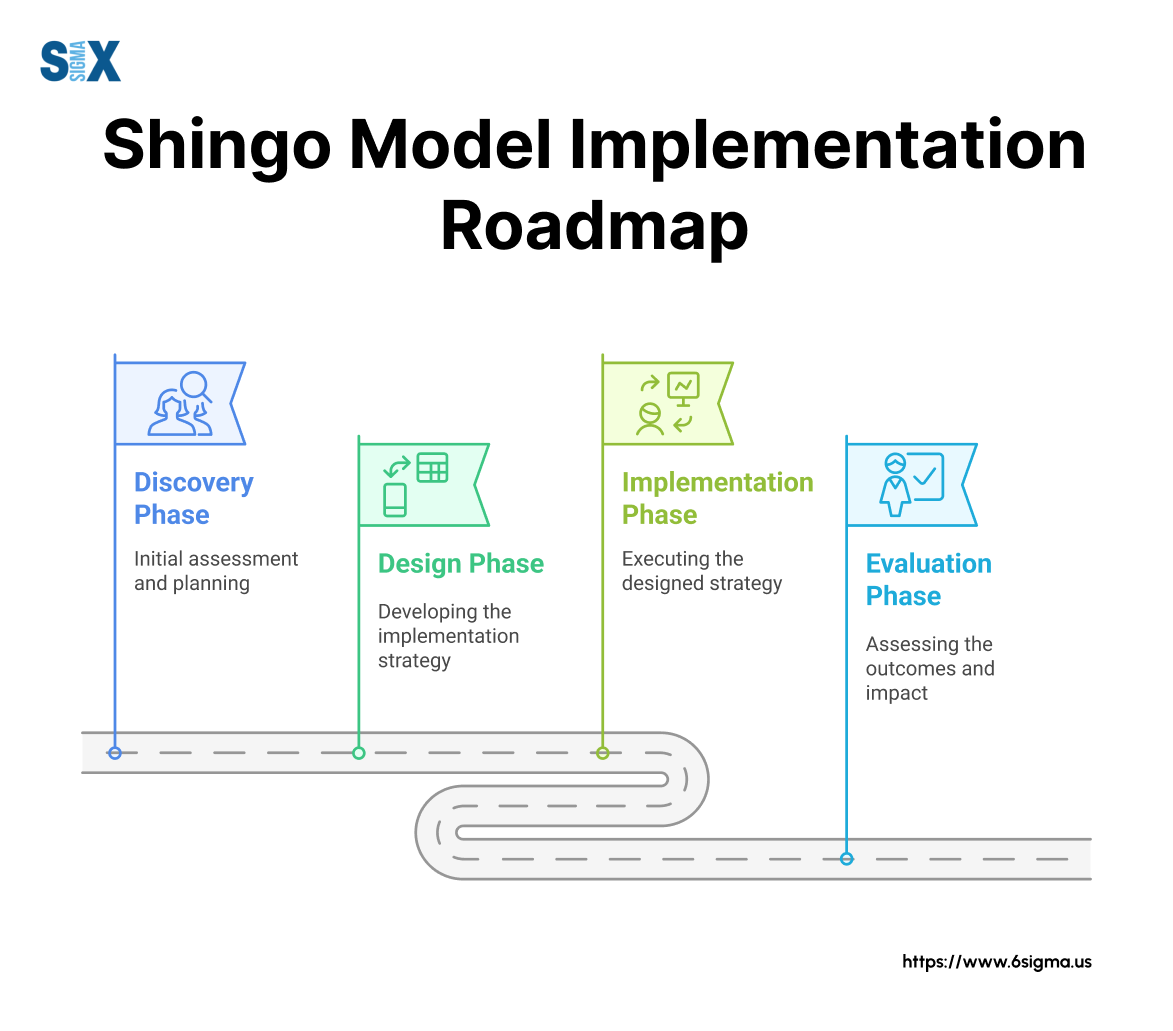
Master advanced techniques for complex process optimization
Enhance your analytical skills to lead top-quality projects and with Six Sigma Black Belt Certification.
Integration of the Shingo Model with Other Methodologies
Organizations often wonder how the Shingo Model fits with their existing improvement methodologies, particularly with Lean Six Sigma.
Rather than competing approaches, the Shingo Model provides the cultural foundation that maximizes the effectiveness of technical improvement methods.
Lean Shingo integration creates a powerful combination where Lean tools find fertile ground in a principle-centered culture. While Lean focuses on eliminating waste and improving flow, the Shingo
Model addresses why these improvements often fail to stick—the missing cultural elements. Organizations with mature Lean programs frequently discover that the Shingo Model fills critical gaps in their transformation efforts.
The complementary nature becomes clear when examining specific elements. Lean provides concrete tools like value stream mapping, standard work, and visual management.
The Shingo Model explains the principles behind these tools and how to create systems that encourage their proper use.
For example, the Lean concept of “go see” aligns perfectly with the Shingo principle of “respect every individual”—both emphasize direct observation and engagement with frontline work.
Integration strategies typically follow three patterns. Some organizations begin with the Shingo Model to establish cultural foundations before implementing technical tools.
Others introduce Shingo principles to enhance existing Lean Six Sigma programs.
A third approach implements both simultaneously, using improvement projects as vehicles to teach principles while solving problems.
Organizations that successfully integrate these approaches report enhanced outcomes beyond what either methodology achieves alone.
Technical improvements implement faster and sustain longer. Employee engagement increases as people understand the “why” behind improvement activities.
Problem-solving becomes more effective as teams apply both technical tools and principle-based thinking.
The integration also creates development pathways for improvement professionals with various six sigma certification levels to enhance their effectiveness by adding cultural transformation skills to their technical expertise.
Black Belts who understand Shingo principles often become more effective change agents because they address both technical and social dimensions of improvement.
The Shingo Model doesn’t replace Lean Six Sigma—it elevates it. By providing the cultural context and principle foundation, the model helps organizations realize the full potential of their improvement methodologies rather than experiencing the all-too-common pattern of initial gains followed by regression to previous performance levels.
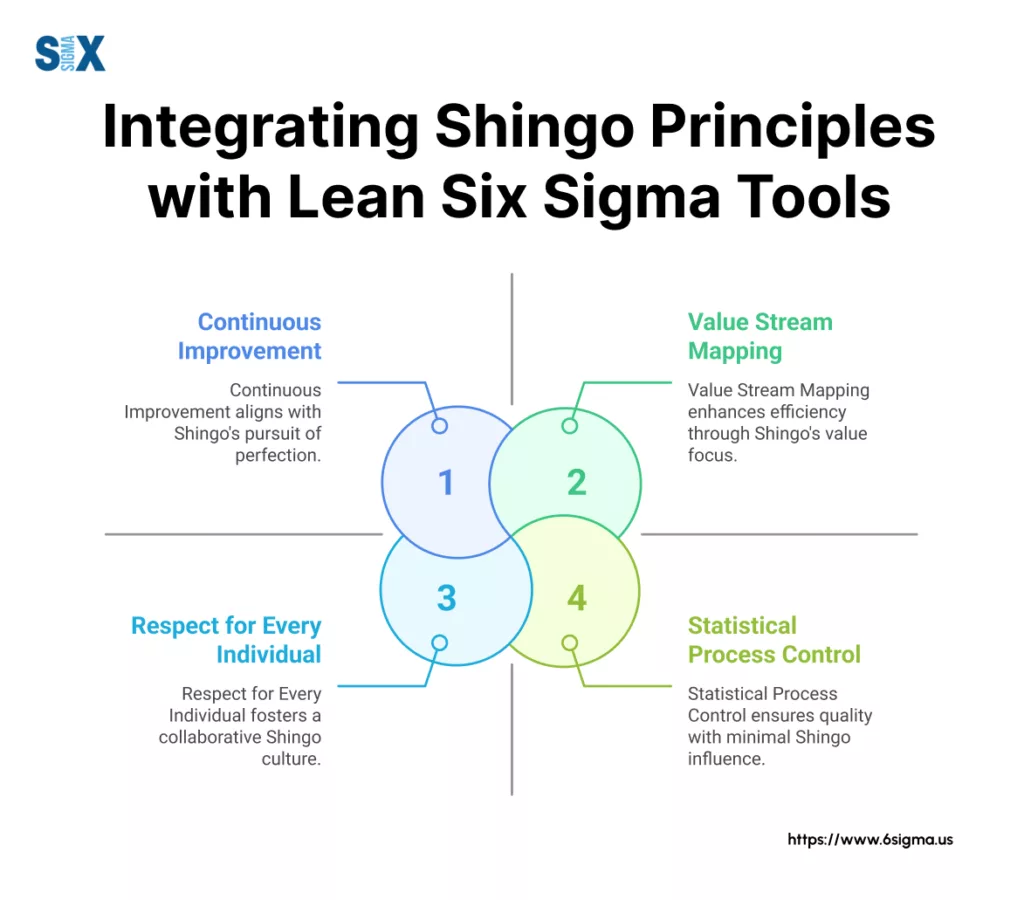
Common Challenges and Solutions of the Shingo Model
Organizations implementing the Shingo Model typically encounter several predictable hurdles. Understanding these challenges and proven mitigation strategies significantly increases success rates.
Leadership misalignment often derails implementation efforts when executives verbally support the Shingo Model while continuing behaviors that contradict its principles.
This disconnect quickly undermines credibility throughout the organization. Successful organizations address this by starting with intensive leadership development focused on personal application of principles before broader rollout.
Regular leadership behavior assessments and peer coaching help maintain alignment as the transformation progresses.
Middle management resistance emerges frequently. These key players may feel caught between executive expectations and frontline realities.
Organizations overcome this by involving middle managers in system design, providing them with specific tools to apply principles in their areas, and recognizing their critical role in translating principles into daily practices.
Cultural assessment difficulties arise when organizations struggle to measure the intangible aspects of their transformation.
Rather than abandoning measurement, successful organizations develop balanced scorecards that include both traditional performance metrics and cultural indicators like leadership behaviors, employee feedback, and principle application in decision-making.
Sustainability challenges emerge after initial enthusiasm wanes. Organizations maintain momentum by integrating principles into hiring practices, promotion criteria, and on-boarding processes.
Facing recurring problems or implementation roadblocks with unclear origins?
Equip yourself with a structured process to effectively determine the root cause of issues and implement sustainable solutions.
Getting Started with the Shingo Model
Before diving into implementation, organizations should evaluate their readiness for the Shingo operational excellence model. This assessment examines several critical dimensions that predict success.
Leadership commitment represents the most crucial readiness factor. Executives must demonstrate willingness to change their own behaviors first and invest in long-term cultural transformation rather than quick fixes.
Organizations should honestly evaluate whether leaders will remain committed when faced with competing priorities or short-term performance pressures.
Current improvement maturity also influences readiness. Organizations with some experience in structured improvement methodologies typically adapt to the Shingo Model more readily than those starting from scratch.
However, organizations with deeply entrenched tool-focused improvement programs may need to overcome fixed mindsets about what drives excellence.
Resource Requirements for the Shingo Model
Implementing the Shingo Model requires thoughtful resource allocation across several categories. Time represents the most significant investment, with typical transformations requiring 3-5 years to fully mature.
Organizations should plan for leadership development time, assessment activities, system redesign efforts, and ongoing coaching.
Financial resources include workshop costs, possible consulting support, assessment tools, and internal resource allocation.
While the Shingo operational excellence model doesn’t require expensive technology, organizations typically budget for training materials, visual management tools, and possible facility modifications to support principle application.
Shingo Model Implementation Progress Tracker
Cultural Enablers
Continuous Improvement
Enterprise Alignment
Results
Leadership Alignment
Principle Understanding
System Design
Behavioral Indicators
Implementation Progress Summary
Next Steps
Organizations ready to begin their Shingo journey should follow a structured approach to maximize success. Initial education typically starts with executive teams attending the Shingo Institute’s “Discover Excellence” workshop to build shared understanding of the model’s principles and assessment approach.
Following education, many organizations conduct a baseline assessment using the Shingo assessment methodology or a simplified version adapted for internal use.
This assessment identifies principle-to-system gaps that become improvement priorities.
Developing an implementation roadmap comes next, typically starting with one or two focus areas rather than organization-wide deployment. Successful organizations begin with areas where leadership support is strongest and potential for visible results exists.
Building internal capability follows, with selected staff receiving deeper training in the Shingo Model and assessment methods. These individuals then lead implementation efforts and coach others throughout the organization.
Regular reassessment and adjustment complete the cycle, with organizations measuring both performance results and cultural indicators to evaluate progress and refine their approach.
The Shingo operational excellence model emphasizes that transformation is a journey rather than a destination, with ongoing learning and refinement as organizational conditions evolve.
SixSigma.us offers both Live Virtual classes as well as Online Self-Paced training. Most option includes access to the same great Master Black Belt instructors that teach our World Class in-person sessions. Sign-up today!
Virtual Classroom Training Programs Self-Paced Online Training Programs