Quality Function Deployment: The Customer-Driven Methodology
Customer happiness is the key for any business that wants to succeed and to stay in the long run. One approach that helps companies listen to and please their customers is called Quality Function Deployment, or QFD for short.
QFD gives teams a powerful way to understand exactly what clients want and need when designing products or processes.
It works by translating vague wants into clear objectives right from the beginning. Quality Function Deployment uses special charts and tables to change vague ideas into actual steps that can be measured.
This customer-focused process began in the 1960s in Japan during a big push for higher quality. Companies like Toyota were among the first to use it, and soon other industries saw benefits too by using QFD to create exactly what customers were seeking.
While it started in manufacturing, QFD quickly spread to all sorts of businesses as an easy way to gain an edge through more satisfied repeat customers.
Key Highlights
- Understand the fundamentals of Quality Function Deployment (QFD) and its philosophy
- Explore the rich history and global adoption of QFD as a catalyst for innovation
- Learn the key benefits of Quality Function Deployment
- Master the four phases of Quality Function Deployment: product planning, product design, process design, and quality control
- Dive deep into essential QFD tools
- Gain insights on applications of QFD across diverse industries like automotive, manufacturing, technology, and services
- Learn best practices for implementing Quality Function Deployment in your organization
- Discover how to overcome common challenges and pitfalls when deploying QFD
What is Quality Function Deployment (QFD)?
In Quality Function Deployment lies a fundamental question ā how can organizations truly understand and translate the voice of the customer into tangible product and process designs that consistently exceed expectations?
As a disciplined methodology, QFD provides a robust framework for capturing customer requirements, prioritizing them based on importance, and systematically deploying them throughout the entirety of the development lifecycle.
Voice of the Customer (VOC)
The first step in any QFD initiative is to thoroughly research and document the voice of the customer.
This involves gathering qualitative and quantitative insights into what customers desire, need, and value in a product or service offering.
Common techniques include surveys, interviews, focus groups, analyzing sales data and customer feedback, ethnographic studies, and more.
The goal is to transform these voices into specific, actionable customer requirements or “whats” that can drive the design process.
Customer Requirements
Once the voice of the customer data has been collected and analyzed, the next step is to distill it into a prioritized list of customer requirements.
These requirements articulate the features, functions, performance metrics, and non-functional attributes that customers deem essential or desirable.
House of Quality
The House of Quality matrix is arguably the most powerful and recognizable tool in the QFD toolbox.
This complex diagram maps customer requirements against technical specifications, design characteristics, competitive benchmarks, and more.
Matrix Product Planning
Quality Function Deployment is a matrix-driven planning methodology that cascades requirements and priorities across multiple dimensions of the product realization process.
Subsequent matrices then deploy these outputs into increasing levels of technical detail for product design, manufacturing process design, production planning, and quality assurance.
Customer-driven Engineering
The overarching philosophy of QFD is to embed the voice of the customer into every engineering decision, from early product conceptualization through full-scale production.
Rather than relying on assumptions or historically based requirements, customer-driven engineering ensures that limited resources are directed toward delivering maximum customer value and satisfaction.
History and Origins of Quality Function Deployment (QFD)
Japanese Roots
While Quality Function Deployment has since been embraced globally, its origins trace back to the Japanese quality revolution of the 1960s.
During this pivotal era, pioneers like Dr. Shigeru Mizuno and Dr. Yoji Akao recognized the need for more robust quality practices that started by deeply understanding customer desires.
Their insights laid the theoretical foundations for QFD at a time when Japanese manufacturing was disrupting industries through a laser focus on quality and customer satisfaction.
Yoji Akao and Shigeru Mizuno
Dr. Yoji Akao, a respected quality management consultant, is widely credited as the founder of Quality Function Deployment (QFD).
While assisting the shipbuilding division of Mitsubishi Heavy Industries, Akao developed the foundational matrices and prioritization processes that became QFD.
His colleague Dr. Shigeru Mizuno helped refine and document the methodology based on their experiences working with cross-functional teams in manufacturing environments.
Mitsubishi Shipyard
At Mitsubishi’s Kobe shipyard, QFD was initially conceived and field-tested in the late 1960s.
Facing intense global competition, the shipbuilders desperately needed a way to systematically capture and address customer needs while making intelligent trade-offs during design and construction.
The early successful adoption of Quality Function Deployment at this shipyard demonstrated its potential for bridging the gap between customer expectations and engineering execution.
Toyota and Suppliers
While QFD’s origins were in shipbuilding, it was the automotive industry that rapidly embraced and propagated the methodology across Japan in the 1970s and 80s.
The Toyota Motor Company, already renowned for its Quality Circles and just-in-time production principles, became an early advocate of QFD.Ā
Toyota mandated that its vast supplier network also adopt Quality Function Deployment, catalyzing its widespread adoption as a cornerstone of Japanese quality practices.
US Adoption in the 1980s
As Japanese automakers gained significant market share in the US during the 1970s, the Detroit Big Three desperately sought a competitive response.
QFD was identified as a key enabler of the quality renaissance that allowed Japanese manufacturers to meet and exceed customer expectations so consistently.
By the early 1980s, Ford, GM, and Chrysler had all sent teams to study Quality Function Deployment practices in Japan. Their subsequent adoption and customization of QFD for American markets sparked its proliferation across other industries.
The Importance and Benefits of Quality Function Deployment
In my decades of experience deploying Quality Function Deployment across diverse organizations, QFD represents a fundamental shift in mindset – from operating based on internal assumptions and historical requirements, to proactively capturing and responding to the voice of the customer.
When properly implemented, the benefits of QFD are both quantifiable and wide-ranging, impacting everything from customer satisfaction and loyalty to development cost and time-to-market.
Customer Satisfaction
Perhaps the most obvious yet critical benefit of QFD is its ability to improve customer satisfaction levels dramatically.
By systematically deploying specific customer requirements throughout the design process, organizations ensure that products and services more precisely align with what users want and value.
Design Quality
In addition to satisfied customers, Quality Function Deployment also drives higher internal quality levels by reducing defects and rework.
When customer requirements are documented and flowed down to granular engineering specs, there is far less ambiguity and need for assumptions during design and manufacturing.
Competitive Analysis
A core tenet of QFD is performing rigorous competitive benchmarking during the customer requirement capture phase.
By evaluating how effectively competing products and services address customer needs, organizations can pinpoint whitespace opportunities.
The voice of the customer data highlights where incumbents are underdelivering, allowing new offerings to be precisely targeted at those gaps and rapidly gain market share through superior quality.
Key Advantages of Quality Function Deployment
Customer-focused Products
QFD is a customer-focused product development and quality methodology.
By making the customer requirements and prioritized needs the driving input, QFD ensures that limited resources are channeled into delivering maximum customer-perceived value.
Shorter Development Cycles
Another major advantage of Quality Function Deployment implementations that I’ve witnessed is significantly accelerated product development timelines.
Because customer requirements are documented upfront and flow through the design process, there is far less ambiguity and need for rework.
Cross-functional Collaboration
Effective QFD requires input and buy-in from cross-functional teams spanning marketing, engineering, operations, quality, and more.
The process of capturing the voice of the customer, prioritizing needs, and mapping them to technical requirements is inherently collaborative.
QFD breaks down organizational silos and fosters greater cross-pollination of knowledge ā a critical enabler for developing successful products that delight customers.
Structured Documentation
A hallmark of QFD compared to more ad-hoc product development approaches is its structured and documented nature.
Each phase leaves behind a detailed paper trail outlining the key inputs, analysis, trade-offs, and prioritization decisions made.
This documentation creates an invaluable organizational knowledge repository that can be leveraged for future programs and continuous improvement initiatives.
Prioritized Requirements
In the real world of finite resources and complex development constraints, not all customer requirements can be fully addressed.
This is where Quality Function Deployment’s ability to rigorously prioritize requirements based on importance and customer preferences becomes so powerful.
By focusing delivery efforts on the highest impact requirements first, organizations can maximize customer satisfaction while balancing development risks and costs.
The Four Phases of Quality Function Deployment
While the core principles of QFD are powerful, the true strength of this methodology lies in its structured, phased approach to embedding the voice of the customer throughout the entire product realization process.
The QFD workflow is commonly divided into four distinct phases, each building upon the previous one to translate high-level customer needs into increasingly granular engineering requirements, manufacturing processes, and quality controls.
Phase 1 – Product Planning
Voice of the Customer (VOC) research
The product planning phase begins with a concentrated effort to capture the voice of the customer through qualitative and quantitative research techniques like surveys, interviews, focus groups, and analyzing past complaints and desires.
This step is critical for unearthing both obvious requirements that customers articulate, as well as latent, unstated needs.
Customer Needs and Wants
The raw VOC data is then synthesized and distilled into a hierarchical list of customer needs, wants, and preferences ranked by their relative importance.
Effective need statements are precise, measurable, and accurately convey the intent behind the customer’s desired outcome or performance expectation.
Technical Specifications
With prioritized customer needs in hand, cross-functional teams can begin mapping them to specific technical specifications, features, and design characteristics that the product must deliver.
These “hows” form the basis for more detailed engineering requirements in subsequent phases.
Relationship matrix
The iconic House of Quality matrix visualizes the relationships between each customer’s need and the proposed technical specifications.
This allows teams to identify potential conflicts, make informed trade-offs, and prioritize which specs will yield the greatest impact on customer satisfaction based on their importance scores.
Competitive Analysis
An integral part of the House of Quality is a competitive assessment section that scores how effectively competing products address each customer’s need.
This benchmarking highlights potential gaps and market opportunities to be exploited in the new design.
Phase 2 – Product Development
Critical Parts and Assemblies
With high-level technical specifications defined, the product development phase dives deeper to identify the critical product sub-systems, components, and assemblies required to deliver on those specs.
Each one is systematically mapped and traced back to its impact on specific customer needs.
Key characteristics
For each critical part or assembly, key characteristics that contribute to fulfilling technical requirements are documented.
These may include form, fit, function, performance metrics, and more. Detailed engineering targets, tolerances, and acceptance criteria are established.
Product Design Requirements
The aggregated key characteristics from all components flow down to become the product design requirements and a DFMEA is conducted to identify and mitigate potential failures in delivering on customer needs.
Design FMEA Inputs
The relationship matrices and prioritized customer needs from the previous phase feed directly into the Design Failure Mode and Effects Analysis (DFMEA) process.
This allows the most critical customer requirements to drive risk identification and mitigation strategies during design.
Phase 3 – Process Planning
Manufacturing Processes
With the product design defined, teams can now determine the specific manufacturing processes required to produce components and assemble the final product according to specs.
Process maps, flow diagrams, workstations, and procedures are documented.
Process Flow
Each step in the manufacturing process flow is analyzed to understand potential impacts on key product characteristics.
This evaluation highlights critical process parameters that must be carefully monitored and controlled.
Critical Process Characteristics
Through mapping, the team identifies the vital few process characteristics that contribute most significantly to producing conforming components and assemblies.
These critical inputs become the focal points for statistical process control and real-time monitoring.
Quality Controls
With critical process parameters identified, quality teams can establish rigorous control plans, sampling strategies, and acceptance criteria.
Tools like SPC, mistake-proofing, and FMEA ensure these characteristics remain stable and in statistical control.
Phase 4 – Process Quality Control
Process Capability
Before full-scale production launch, the manufacturing processes undergo thorough capability studies and statistical validation.
This data-driven approach provides quantitative evidence that processes can reliably produce conforming products within specification limits.
Inspection and Testing
Complementing the established quality controls, comprehensive product inspection, and testing protocols are defined based on critical characteristics.
These may include incoming inspections, in-process checks, final product acceptance tests, accelerated life tests, and more.
Continuous Improvement
Quality Function Deployment is an iterative methodology anchored in the principle of continuous improvement.
As production ramps up, processes are closely monitored using statistical tools, and any deviations from expected quality targets are treated as opportunities to further optimize.
The Customer Feedback Loop
Perhaps most importantly, the QFD workflow establishes closed-loop mechanisms to constantly solicit and incorporate new customer feedback.
This voice of the customer is analyzed and prioritized, with findings deployed back through the appropriate QFD phases to drive ongoing product and process enhancements.
Quality Function Deployment Tools and Matrices
Quality Function Deployment methodology lies in a detailed set of interlinked matrices and prioritization tools.
While the House of Quality is arguably the most recognizable, the true power of QFD emanates from the structured way these matrices cascade and deploy requirements across the entire product realization cycle.
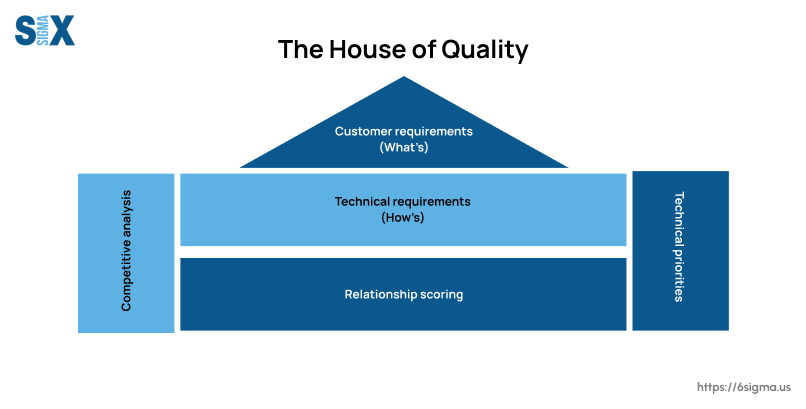
The House of Quality Matrix
Customer Requirements (“Whats”)
The left side of the iconic House of Quality matrix captures the voice of the customer in the form of specific “what” requirements and needs.
These precise statements convey both obvious demands customers articulate as well as latent needs uncovered through research.
Critically, each “what” is weighted based on its relative importance to customer satisfaction and business impacts.
Technical Requirements (“Hows”)
Across the top of the matrix, the team documents the key technical requirements, specifications, and design characteristics that potentially address the customerās “whats”.
These “hows” define what the product or service must deliver to fulfill the associated customer needs.
Relationship Scoring
The body of the House of Quality is a relationship matrix that scores the correlation between each “what” and “how”.
This criticality scoring allows the team to pinpoint the vital few technical requirements that will yield the greatest impact on achieving prioritized customer needs.
Competitive Analysis
An integral component is a competitive assessment that scores how effectively competing products and services address each “what”.
This benchmarking exposes gaps and market opportunities for the new design to exploit in exceeding customer expectations.
Technical priorities
Through roll-up calculations, each “how” receives an overall importance rating based on its cumulative impact across all customer requirements.
This prioritization ensures development resources are focused on the most critical technical characteristics driving customer satisfaction.
Other QFD Matrices
Part Deployment
As the QFD process advances into product design, additional matrices map the prioritized technical requirements from the House of Quality against critical components, assemblies, and their key characteristics.
This part deployment ensures customer needs precisely flow down into specific engineering specifications.
Process Deployment
Once component designs are established, QFD process matrices link their key characteristics to critical manufacturing process parameters that must be controlled.
This deployment drives the development of robust control plans targeting the vital few inputs influencing product quality.
Production Planning
In the final phases, QFD planning matrices integrate production requirements like yield, volume, maintenance, and other operational considerations.
These outputs feed into quality assurance protocols, statistical process controls, and other production launch readiness activities.
Implementing Quality Function Deployment in Your Organization
While the benefits of QFD are numerous, successfully institutionalizing this customer-driven methodology within an organization requires careful planning and execution.
Drawing from my experiences guiding deployments at industry leaders, I’ve distilled several critical success factors that maximize the impact of QFD initiatives.
Cross-functional Teams
QFD is inherently a cross-functional exercise that requires committed participation from voices across the organization.
From marketing professionals capturing the voice of the customer, to design engineers defining technical specs, to manufacturing experts advising on process capabilities ā broad stakeholder involvement is critical.
Customer Data Collection
Robustly capturing the true voice of the customer through quantifiable data is foundational to an effective QFD program.
Proven market research techniques like surveys, interviews, ethnography studies, and competitive benchmarking ensure customer inputs accurately reflect real needs and priorities.
Matrix Facilitation
Properly facilitating the construction and population of QFD matrices is an often underappreciated skill.
Integration with the Design Process
Rather than operating as a silo, Quality Function Deployment must be systematically integrated into the organization’s existing product design and NPD processes.
This prevents it from becoming an academic exercise disconnected from execution and ensures customer needs seamlessly deploy into implementation.
Overcoming Challenges
Significant organizational change invariably faces resistance. When deploying QFD, being prepared to address common hurdles is key.
These may include skepticism over new techniques, disagreements on customer priority scoring, and general inertia against shifting established ways of working.
Quality Function Deployment Examples and Case Studies
While QFD originated in manufacturing environments, its applicability in translating customer needs into high-quality product and service designs has been validated across virtually every industry.
To bring these concepts to life, let’s explore a few diverse examples that highlight the unique ways Quality Function Deployment can be leveraged.
Automotive Industry
As an early pioneer and adopter of QFD, the automotive industry provides some of the most compelling case studies.
From Ford using QFD to redesign its truck chassis around prioritized customer needs like ride quality and hauling capability, to Nissan deploying QFD to optimize vehicle ergonomics based on differently sized driver populations ā QFD has been instrumental in Detroit’s quality renaissance.
Manufacturing Examples
World-class manufacturers like Sony have employed QFD to guide product designs optimized for customer-centric measures like ease of use, repairability, and environmental impacts.
In another example, Philips deployed QFD to integrate often-overlooked customer “whats” like aesthetics and intangible brand perceptions into the design of its personal care product lines.
Service Industry Use Cases
While originally conceived for physical products, QFD has proven equally powerful in the service sector at innovating improved customer experiences. For example,
Continental Airlines applied QFD to overhaul its passenger check-in and boarding procedures by first capturing and prioritizing what customers value most in those interactions, like efficiency and hospitality.
Software and Technology
Even in software-centric environments, QFD provides structures for aligning development initiatives with customer needs.
Microsoft employed QFD to gather requirements for new releases of its Windows operating system, while biotech pioneers like Amgen have used it to design better interfaces for their genomics research platforms based on voice-of-the-scientist inputs.
Across every application, following Quality Function Deployment’s rigorous methodology to truly understand what matters most to customers, and precisely executing those needs, has yielded innovative, market-leading products, services, and experiences that consistently deliver superior satisfaction.
SixSigma.us offers both Live Virtual classes as well as Online Self-Paced training. Most option includes access to the same great Master Black Belt instructors that teach our World Class in-person sessions. Sign-up today!
Virtual Classroom Training Programs Self-Paced Online Training Programs