The Guide to Creating a Quality Assurance Plan with Lean Six Sigma Principles
Do inconsistent results, project delays caused by errors, or rising customer complaints sound familiar?
Many organizations grapple with these issues, often reacting to problems after they occur. A more effective strategy involves proactive quality managementādesigning processes to prevent defects from the start. This is where a quality assurance plan (QAP) becomes essential.
So, what is a quality assurance plan? It’s a documented strategy outlining the activities, standards, and responsibilities needed to achieve predetermined quality levels throughout a project or process.
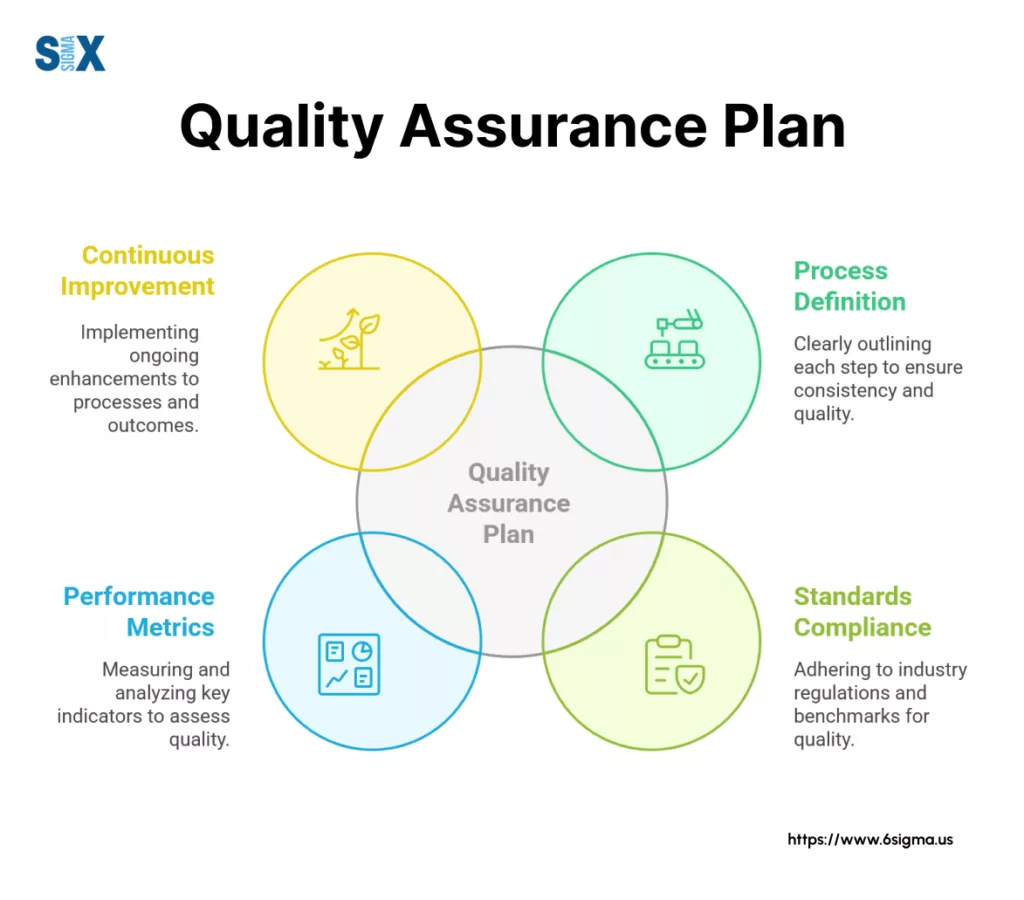
This guide provides a clear path for:
- Planning for quality assurance
- How to construct a robust QAP
- Importance and core components of QAP
- Touching on industry specifics and common pitfalls.
What Is A Quality Assurance Plan (QAP)?
A quality assurance plan (QAP) is far more than just a checklist; it’s a formal, proactive document that meticulously outlines the specific activities, standards, tools, methodologies, and responsibilities required to ensure a product, service, or process consistently meets predefined quality objectives.
Think of it as the strategic blueprint for achieving quality throughout the entire lifecycle.
You might encounter variations in terminology. In some US contexts, it’s called an Advanced Quality Plan (AQP), and within the automotive sector, Advanced Product Quality Planning (APQP) is common.
These terms often reflect industry-specific nuances but share the fundamental goal of structured quality planning.
An effective assurance quality plan focuses deliberately on the process of achieving quality, rather than solely relying on inspecting the final output. Itās about building quality in from the beginning.
Robust quality assurance plans detail how quality will be managed systematically, defining the procedures and controls necessary to prevent defects and ensure consistency, thereby laying the groundwork for reliable performance and customer satisfaction.
Why A quality assurance plan Is Non-Negotiable?
Implementing a quality assurance plan isn’t just good practice; it’s often fundamental to achieving consistent success.
The benefits extend far beyond simply ticking a box. Effective planning for quality assurance directly leads to greater consistency and standardization in processes and outputs, ensuring everyone follows the same playbook.
This naturally translates into better alignment with customer requirements and boosts overall satisfaction ā you’re actively building processes designed to meet their needs.
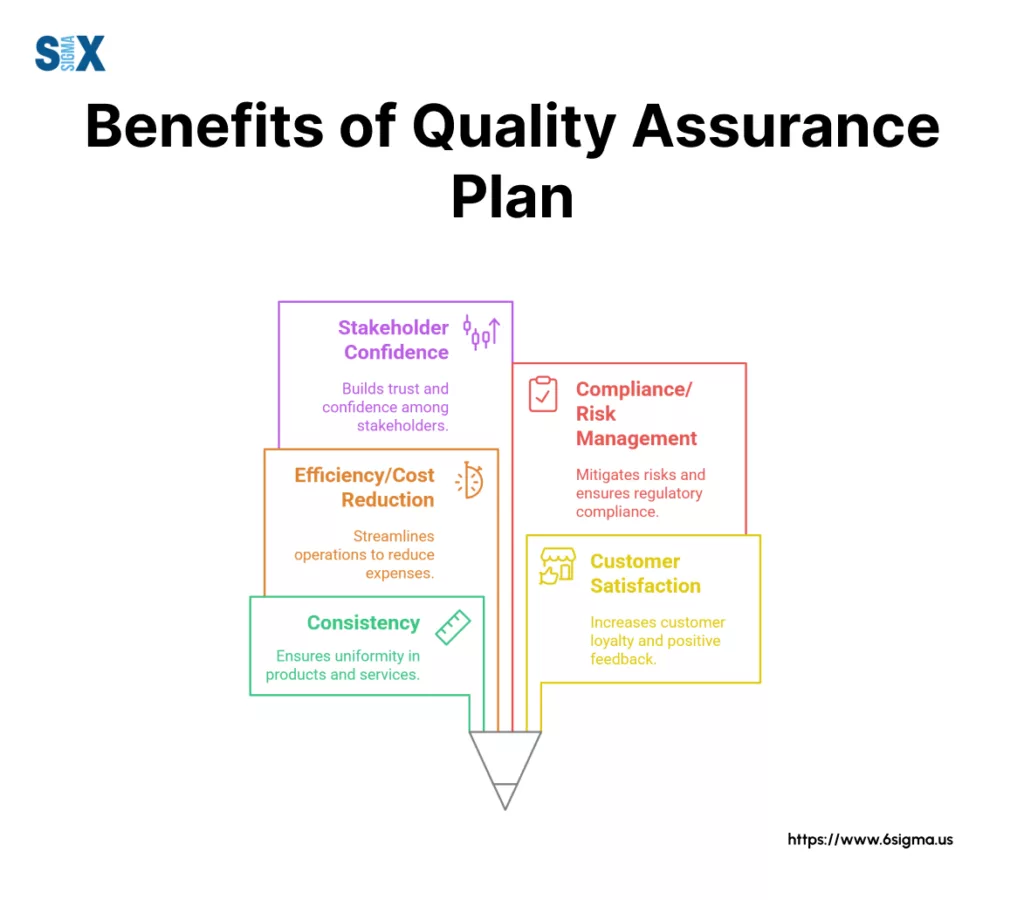
Furthermore, a well-structured quality assurance plan significantly improves operational efficiency. By defining clear procedures and standards upfront, you reduce the likelihood of errors, minimize costly rework, and streamline workflows.
This proactive approach also aids in meeting regulatory requirements and managing risks effectively, providing documented evidence of diligence.
Ultimately, robust quality assurance plans build confidence among stakeholders, demonstrating a clear commitment to quality and reliability.
From a process improvement perspective, the quality assurance plan provides the baseline needed for measurement and analysis, setting the stage for targeted enhancements.
It dictates what quality data needs collection, fostering data-driven decision-making. Importantly, it enforces standard workāa critical concept for predictable performance.
What does a quality assurance plan help minimize?
It directly targets and reduces various forms of waste, such as defects, delays, and the resources spent on fixing problems rather than preventing them.
By defining preventative measures, the quality assurance plan is a powerful tool for defect reduction.
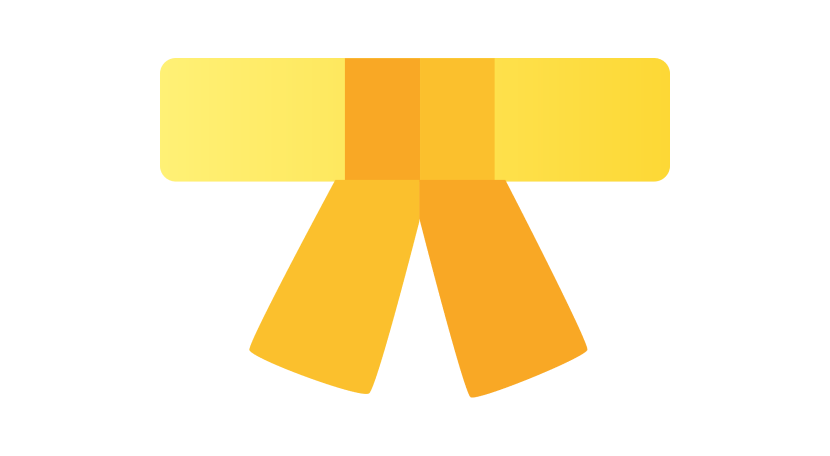
Want to become a valuable contributor to your organization’s quality efforts?
Gain the knowledge to understand process maps, analyze failure modes, and support with our Lean Six Sigma Yellow Belt Training.
QAP vs. Quality Control (QC) Plan: A Crucial Distinction
Understanding the difference between Quality Assurance (QA) and Quality Control (QC) is fundamental when discussing quality management. While often used interchangeably, they represent distinct approaches.
Quality Assurance (QA) is a proactive, process-oriented set of activities focused on preventing defects. It involves designing, implementing, and monitoring processes to ensure quality standards are met consistently. The quality assurance plan is the primary document outlining these QA activities.
Quality Control (QC), conversely, is a reactive, product-oriented set of activities focused on identifying defects in the final product or service. QC typically involves inspection, testing (often guided by a quality assurance test plan or QC test plan), and measurement to verify that outputs meet specified requirements.
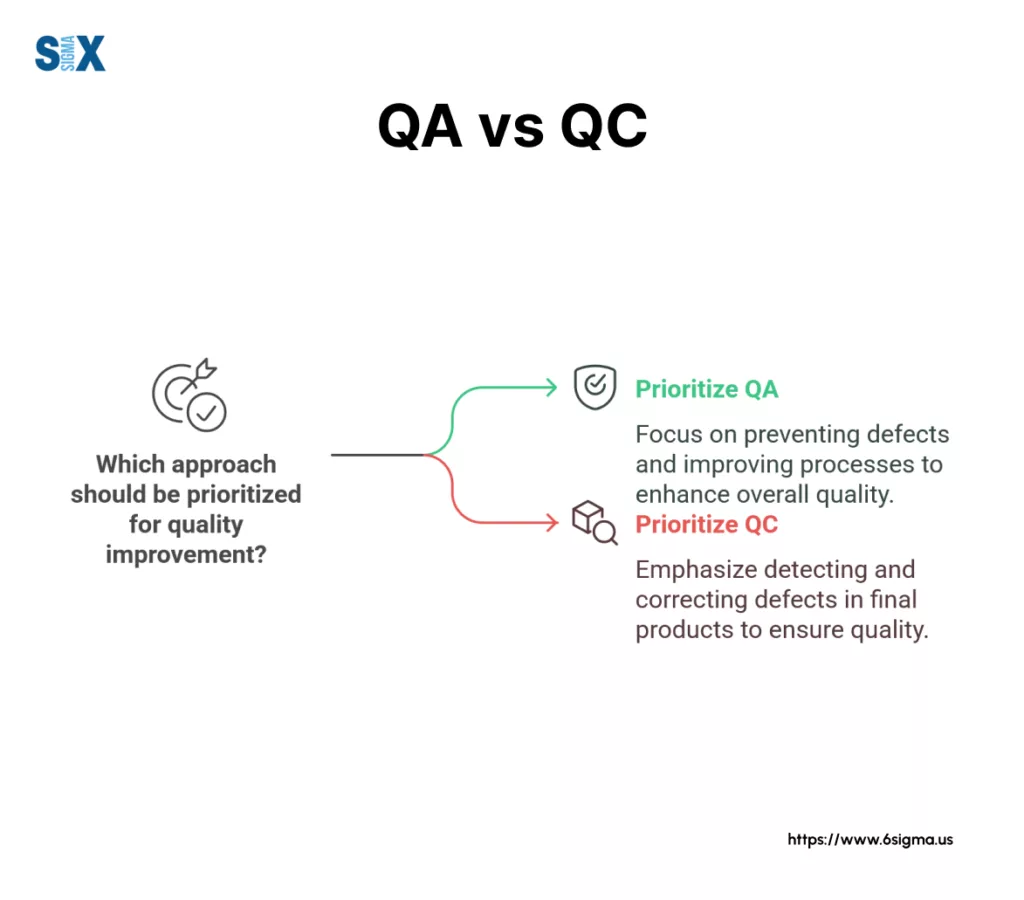
Hereās a breakdown of the key differences:
Feature | Quality Assurance (QA) | Quality Control (QC) |
Focus | Process | Product/Service |
Goal | Prevent defects | Identify/Detect defects |
Timing | Proactive (Throughout the lifecycle) | Reactive (Typically after production/output) |
Orientation | Systemic, Prevention-based | Inspection, Detection-based |
Example | Developing SOPs, Training, Process Audits | Product testing, Code reviews, Inspections |
From a Lean Six Sigma standpoint, the emphasis is heavily on QA. Preventing defects aligns directly with the core Lean Six Sigma goals of eliminating waste (Muda) and improving process capability.
While QC activities are necessary checks, an over-reliance on inspection often signals underlying process inefficiencies that Lean Six Sigma aims to address.
An effective QAP defines the robust system intended to build quality in, thereby minimizing the need for extensive, costly QC interventions later.
Anatomy Of A High-Impact Quality Assurance Plan: Core Components
To understand what a detailed quality assurance plan looks like, let’s break down its essential components.
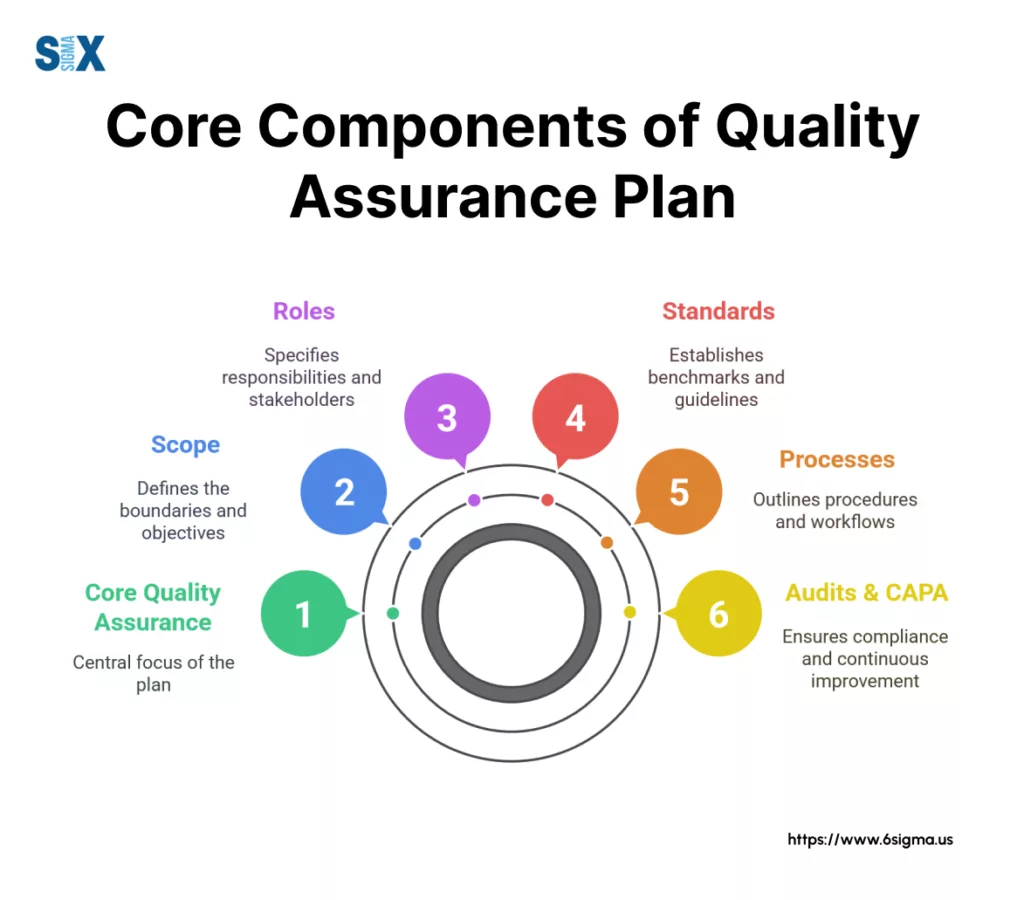
1. Introduction, Purpose, And Scope
This initial section sets the stage. It clearly defines the project, process, or product the QAP covers.
It states the specific quality objectives to be achieved and outlines the boundaries ā what is included and explicitly excluded from the plan’s purview.
2. References
Here, list all relevant documents that inform or are referenced by the QAP. This includes applicable industry standards (like ISO 9001), regulatory requirements, project charters, corporate quality policies, and other key guiding documents for the quality assurance project plan.
3. Management & Organization (Roles & Responsibilities)
Crucially, this section clarifies who is responsible for what regarding quality. It defines roles related to the QAP’s implementation, monitoring, and maintenance.
So, who prepares a quality assurance plan? Often, it’s a collaborative effort led by a QA Manager, Project Manager, or a designated Process Owner.
In Lean Six Sigma environments, a Green Belt or Black Belt might guide its development, ensuring alignment with project goals, while the Process Owner retains ultimate accountability. Specific roles like Project Sponsor or Champion might also be defined concerning quality oversight.
4. Required Documentation
Specify the key documents that the QAP interacts with or governs. This might include Standard Operating Procedures (SOPs), work instructions, specific test plans, design specifications, or data management protocols relevant to the quality assurance project plan.
5. Quality Standards, Methodologies & Metrics
This is where the specific quality targets are detailed. List the standards the project or process must adhere to. Outline the methodologies or techniques that will be employed for assuring quality.
Critically, define the key metrics that will be used to measure quality performance (e.g., defect rates, first-pass yield).
6. Key Processes & Procedures
Outline the core operational or project processes that fall under the scope of the QAP. This section details how critical tasks related to quality will be performed, referencing standardized work instructions or detailed procedures where applicable.
7. Data Collection & Analysis Plan
Quality improvement requires data. This component describes how quality-related data will be collected, where it will be stored, and the methods used for its analysis. Specify tools or techniques like check sheets, control charts, or Pareto analysis that will support data-driven decisions within the planning for quality assurance.
8. Reviews, Audits & Testing Strategy
Define the schedule and procedures for formal reviews, process audits, and specific testing activities required to verify quality.
This includes specifying the types of tests, frequency, and responsibilities for execution and reporting.
9. Problem Reporting & Corrective Actions (CAPA)
Establish a clear process for identifying, documenting, tracking, and resolving quality issues or non-conformances.
This Corrective and Preventive Action (CAPA) process is vital for addressing root causes and preventing recurrence, a cornerstone of effective QAP.
10. Tools, Environments & Resources
List any specific tools (software, hardware, measurement devices), specialized environments, or critical resources needed to execute the quality assurance plan effectively.
11. Supplier Quality Management (If Applicable)
If external suppliers impact the final quality, outline how their performance will be managed and assured. This might include supplier selection criteria, incoming material inspection procedures, or supplier audits as part of the overall QAP.
12. Training Requirements
Identify the necessary training for personnel involved in executing or overseeing quality-related tasks defined in the QAP. This ensures staff have the required competencies.
13. Risk Management (Quality Focus)
Describe how risks specifically related to achieving quality objectives will be identified, assessed, and mitigated. Tools like Failure Modes and Effects Analysis (FMEA) might be referenced here to proactively address potential failure points.
14. Reporting & Communication
Define how quality performance, audit results, and issue status will be documented, reported, and communicated to relevant stakeholders. Specify the frequency, format, and recipients of quality reports generated under the quality assurance project plan.
How To Write Your Quality Assurance Plan: A Practical Approach
Knowing the components is one thing, but actually constructing the document requires a structured process.
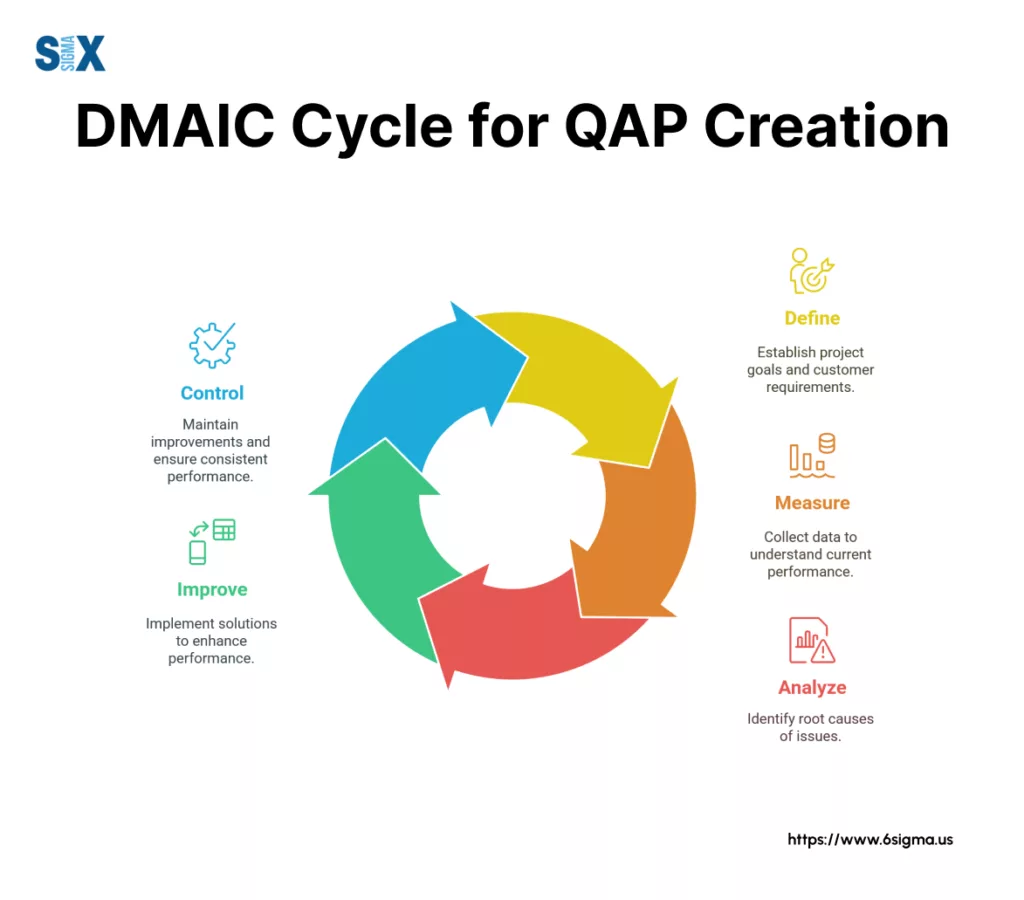
Step 1: Define (The Foundation)
Begin by clearly defining the scope of your QAP. What specific project, product, or process will it cover? Identify your customers (both internal and external) and understand their needs and expectations ā often referred to as the Voice of the Customer (VoC).
Translate these needs into specific, measurable Critical to Quality characteristics (CTQs). Assemble the team responsible for developing and implementing the plan, clarifying roles.
Set clear, specific, measurable, achievable, relevant, and time-bound (SMART) quality objectives that the quality assurance plan aims to achieve.
Step 2: Measure (The Baseline & Plan)
Once objectives and CTQs are defined, identify the key metrics you will use to track performance against them.
Crucially, detail how data related to quality processes will be collected ā this involves specifying methods, frequency, and responsibilities, drawing directly from the QAP components discussed earlier (like Data Collection Plan).
If possible, establish a baseline measurement of current performance before implementing changes outlined in the quality assurance plan. This baseline provides a starting point for measuring improvement.
Step 3: Analyze (Identifying Opportunities)
While deep process analysis often follows initial implementation, effective planning for quality assurance involves anticipating this stage.
Define how the collected quality data will be reviewed and analyzed. Specify the techniques (e.g., control charts, Pareto analysis, root cause analysis) that will be used to identify trends, process gaps, variations, or areas needing improvement.
The insights gained from this planned analysis will inform future refinements of the quality assurance plans and associated processes.
Step 4: Improve (Developing the Processes)
This is where you document the ‘how-to’ within the quality assurance plan itself.
Based on best practices, requirements, and any initial analysis, detail the standardized processes, procedures, controls, and methodologies that will be used to achieve the quality objectives.
Define the corrective and preventive action (CAPA) process for addressing deviations. Essentially, you are documenting the improved state or the target process within the quality assurance plan.
Step 5: Control (Sustaining the Gains)
Finally, finalize the sections of the quality assurance plan that ensure sustainability.
Detail the ongoing monitoring activities, reporting requirements, audit schedules, and training plans necessary to maintain the desired quality level.
Ensure the quality assurance plan is integrated into the regular management system and becomes part of the ongoing process control strategy.
Critically, define a regular review cycle for the QAP itself ā it should be a living document, updated as processes evolve or new insights are gained. This step solidifies how to create a quality assurance plan that endures.
Master the DMAIC methodology and the statistical tools.
Create, implement, and manage effective Quality Assurance Plans with Lean Six Sigma Green Belt
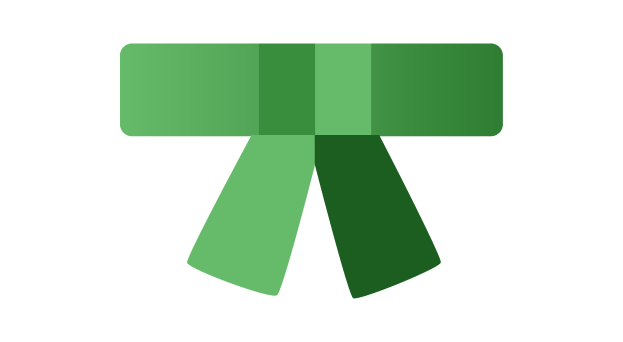
Tailoring Your QAP: Industry Applications
A generic plan rarely suffices; tailoring is key for effective implementation. Consider how a quality assurance project plan might differ across various sectors:
Software Development
In software, the quality assurance plan heavily emphasizes defect prevention throughout the development lifecycle.
Key areas include integrating automated testing, defining clear release criteria, ensuring code quality standards are met, and embedding quality checks within Agile sprints or DevOps CI/CD pipelines.
Manufacturing
Manufacturing QAPs typically concentrate on process control and consistency. This involves Statistical Process Control (SPC), rigorous supplier quality management, adherence to standards like ISO 9001, strict equipment calibration schedules, and ensuring material traceability.
Healthcare
Patient safety and regulatory compliance are paramount in healthcare QAPs.
Focus areas include adherence to regulations (like HIPAA or FDA guidelines), validation of processes and equipment, defining and monitoring clinical pathways, and ensuring data integrity.
Construction
For construction projects, the quality assurance project plan emphasizes compliance with building codes and safety regulations.
It details materials testing protocols, critical inspection points throughout the build process, subcontractor quality management, and adherence to safety protocols.
Integrating QAPs
A quality assurance plan isn’t a static document; its application and integration must adapt to the project management or development methodology being used.
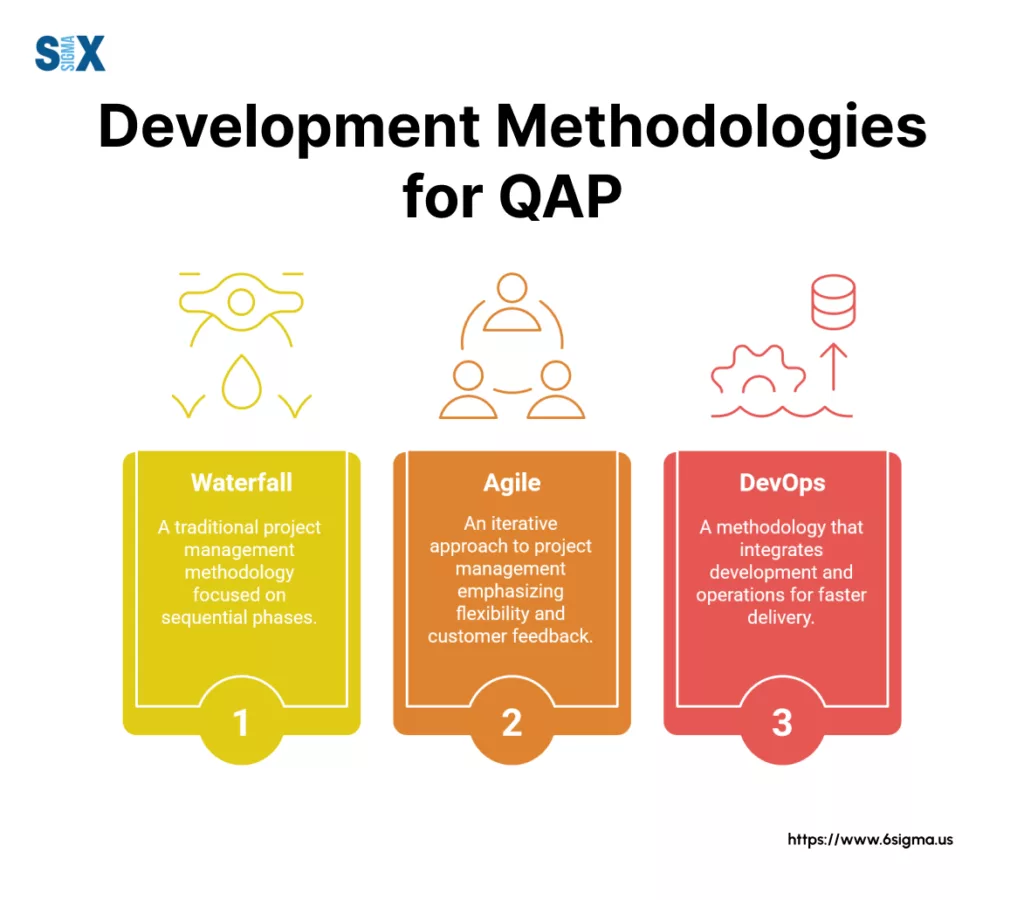
How quality assurance is planned and executed varies significantly across different operational styles.
Waterfall
In traditional Waterfall projects, the quality assurance plan tends to be more formal and is typically developed comprehensively upfront.
It often defines strict quality gates between distinct project phases (e.g., design, development, testing). The focus is on ensuring stability and meeting requirements before proceeding to the next stage.
Agile
Agile environments require a more dynamic approach. Here, the quality assurance plan principles are integrated directly into sprints or iterations.
Quality activities focus on defining a clear “Definition of Done” for user stories, incorporating continuous testing throughout the sprint, and utilizing rapid feedback loops.
DevOps
Within a DevOps culture, the quality assurance plan informs the automation strategy, particularly for quality checks embedded within Continuous Integration and Continuous Deployment (CI/CD) pipelines.
The emphasis is on continuous monitoring, automated testing at various stages, rapid feedback from production, and building quality inherently into the development and operations flow to maintain speed and reliability.
Tools & Software For Streamlining Your QAP
While a quality assurance plan can certainly be managed manually, various software tools can significantly streamline its creation, execution, and monitoring.
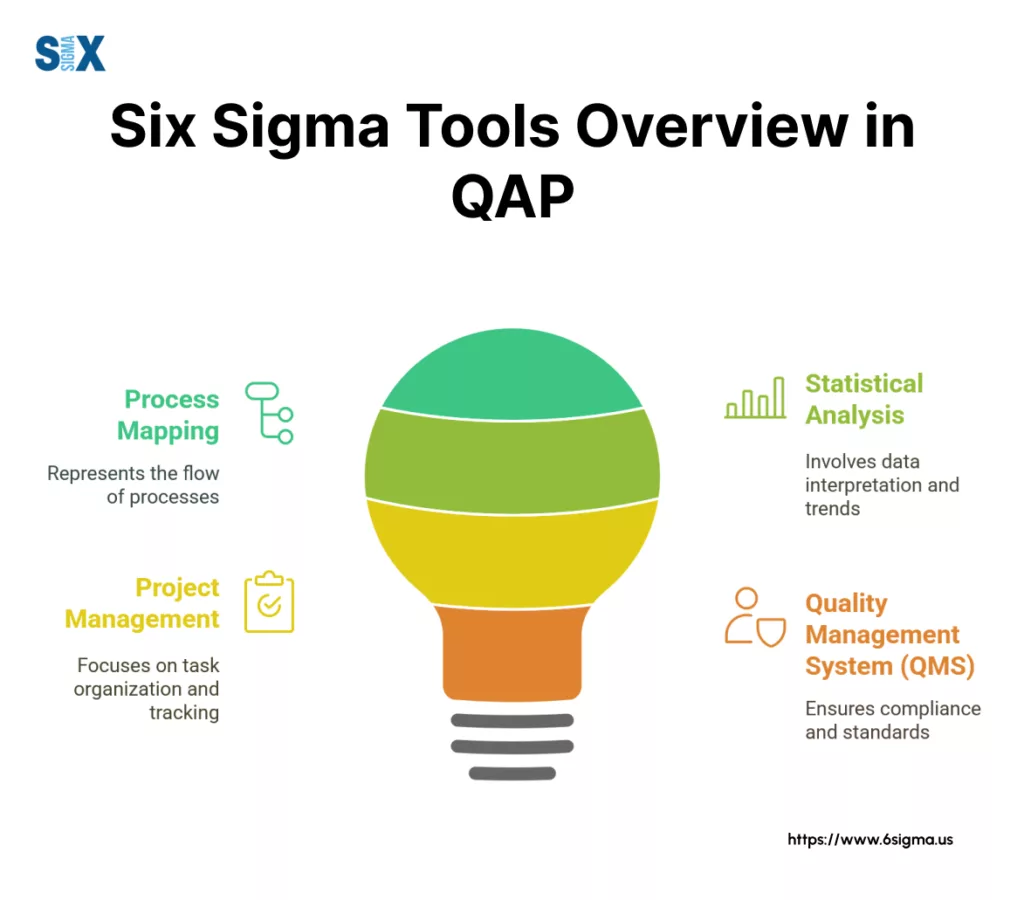
Consider these categories:
- Process Mapping Tools: Software like Visio or Lucidchart helps visualize and document the processes outlined in your QAP, ensuring clarity and common understanding.
- Statistical Analysis Software: For data-driven quality initiatives, tools such as Minitab or JMP are invaluable for analyzing quality metrics, identifying trends, and supporting process improvement efforts mentioned in the quality assurance plan.
- Project Management Platforms: Tools like Jira or Asana can track quality-related tasks, manage corrective actions (CAPA), and monitor progress against the QAP’s schedule and objectives.
- Quality Management Systems (QMS): Dedicated QMS software offers integrated solutions for document control, audit management, training records, and CAPA processes, centralizing many aspects of quality assurance plan execution.
Measuring Success: Quantifying QAP Effectiveness & ROI
How do you know if your quality assurance plan is truly effective? Measuring success goes beyond simply checking if tasks were completed.
It requires quantifying the impact on performance and linking quality efforts to tangible business results.
Focus on metrics that reflect real improvement, such as a reduction in Defects Per Million Opportunities (DPMO) or an improvement in process capability indices like Cpk and Ppk.
Track the reduction in the Cost of Poor Quality (COPQ), which includes expenses from scrap, rework, and warranty claims.
Need to effectively analyze quality data and demonstrate the impact of your QAP?
Learn to utilize essential statistical software to create meaningful charts and perform the data analysis with Minitab Essentials Training
Frequently Asked Questions (FAQ) About Quality Assurance Plans
A. Writing a quality assurance plan typically involves a systematic process: Define the scope, objectives, and quality requirements; Measure key metrics and plan data collection; Analyze potential process gaps and plan for data review; Improve by documenting standardized processes and controls; and Control by outlining monitoring, reporting, and review cycles to sustain quality.
A. The responsibility often falls to a QA Lead, Project Manager, or the designated Process Owner. It’s frequently a collaborative effort involving subject matter experts and stakeholders. In organizations using Lean Six Sigma, a Green or Black Belt might facilitate or guide its development.
A. A typical quality assurance plan is a structured document containing sections like an introduction (purpose, scope), references, roles and responsibilities, quality standards and metrics, key processes, data collection plans, review/audit procedures, corrective action processes, and reporting requirements, as detailed in the ‘Anatomy of a High-Impact QAP’ section.
A.Creating an effective quality assurance plan requires following a structured approach, like the Define-Measure-Analyze-Improve-Control steps outlined earlier. This ensures all critical aspects of quality management are considered and documented systematically.
A. A quality assurance plan template (or template quality assurance plan) is a pre-structured document or outline that serves as a starting point and guide for creating your own specific QAP. It helps ensure consistency and includes prompts for essential components.
A. A well-implemented quality assurance plan helps minimize defects, errors, inconsistencies, project risks, rework, wasted resources, and delays associated with poor quality. It proactively addresses potential issues to reduce their occurrence and impact.
SixSigma.us offers both Live Virtual classes as well as Online Self-Paced training. Most option includes access to the same great Master Black Belt instructors that teach our World Class in-person sessions. Sign-up today!
Virtual Classroom Training Programs Self-Paced Online Training Programs