All You Need to Know About Process Safety Management. The Only Guide You Need
Process Safety Management (PSM) is a comprehensive preventative approach for inherently risky chemical-handling operations.
The core aim is to involve preventing uncontrolled releases whose consequences endanger lives, property, or environments.
By methodically identifying, weighing, and controlling process risks, PSM safeguards facilities, and surrounding communities.
PSM empowers sustainable progress through opportunity management and hazard governance aligned with surrounding transitions.
Key Highlights
- Process Safety Management (PSM) offers a thorough regulatory framework plus a management system preventing catastrophic chemical releases.
- Established post-tragedy, PSM aims to safeguard facilities from hazardous material’s unbridled emanations through diligent protocols.
- Fourteen interwoven elements address aspects like hazard awareness, functioning guides, personnel training, mechanical soundness plus crisis planning.
- Productive PSM further necessitates strong safety-first mindsets, leadership dedication, engaged staff, and—most importantly—relentless betterment spirit.
- Beyond mishap avoidance, PSM bolsters excellence, cots thrift along accidents, and alignment with regulations. It sparks competitive differentiation too through proactive security structuring.
What is Process Safety Management?
Maintaining security is an overriding concern involving highly hazardous compounds. Process Safety Management (PSM) brings meticulous laws and tested strategies preventing disasters involving these materials.
It offers a methodical technique for evaluating and damping linked risks within techniques employing, holding, crafting, or moving such chemicals.
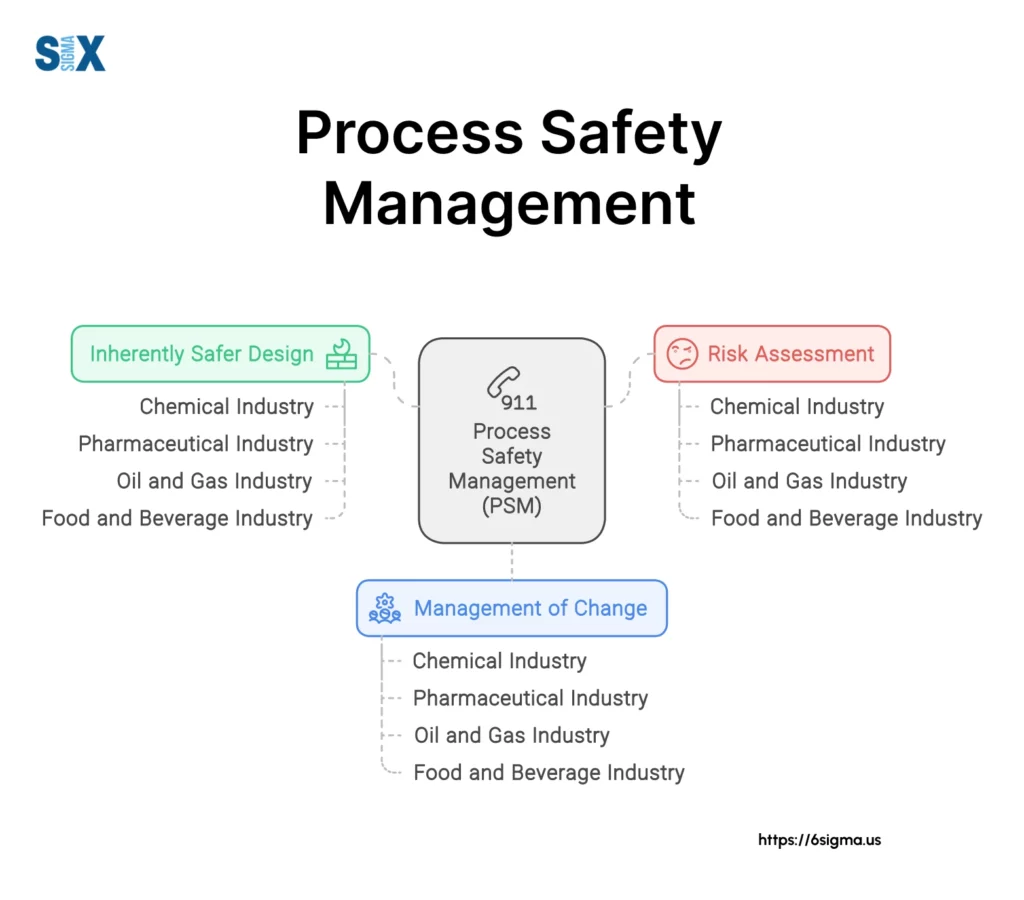
At the nucleus, PSM forms an administrative system interweaving aspects like hazard identification, documented operating guides, personnel training, mechanical upkeep programs, and crisis readiness.
The aim of PSM prove early disturbances, calamities/wounds, and environmental harm. It implements care, not reaction, safeguarding individuals and environments proactively.
Importance of Process Safety Management
Implementing an effective PSM program is crucial for several reasons:
- Worker Safety: PSM helps protect employees, contractors, and the surrounding community from the potential risks associated with handling hazardous chemicals.
- Environmental Protection: Incidents involving hazardous chemicals can have severe environmental consequences, such as air and water pollution, soil contamination, and damage to ecosystems. PSM helps mitigate these risks.
- Asset Integrity: Catastrophic incidents can result in significant damage to equipment, facilities, and infrastructure, leading to costly repairs, replacements, and production losses. PSM helps maintain asset integrity and operational continuity.
- Regulatory Compliance: Many industries, such as chemical manufacturing, oil and gas, and pharmaceuticals, are subject to strict regulations and standards related to process safety. Implementing PSM ensures compliance with these regulations and helps avoid penalties and legal liabilities.
- Reputation and Public Confidence: Major incidents can severely damage a company’s reputation and erode public trust. PSM demonstrates a commitment to safety and responsible operations, which can enhance a company’s standing in the community and industry.
History and Background of Process Safety Management (PSM)
The need for a comprehensive process safety management system became evident after several catastrophic incidents in the chemical industry, such as the Union Carbide disaster in Bhopal, India, in 1984, and the Phillips Petroleum Chemical Plant explosion in Pasadena, Texas, in 1989. These events highlighted the importance of proactive measures to prevent such incidents and protect workers, the public, and the environment.
In response, the Occupational Safety and Health Administration (OSHA) in the United States developed the Process Safety Management (PSM) standard in 1992.
This standard, often referred to as the OSHA PSM standard (29 CFR 1910.119), established a systematic approach to managing the risks associated with highly hazardous chemicals.
The PSM standard outlines 14 essential elements that companies must implement to effectively manage process safety risks.
These elements cover various aspects, including process hazard analysis, written operating procedures, employee training, mechanical integrity programs, and emergency planning and response measures.
While the OSHA PSM standard is mandatory for facilities in the United States that handle highly hazardous chemicals above specified threshold quantities, many companies worldwide have adopted PSM principles as industry best practices, recognizing the importance of process safety in preventing incidents and ensuring safe operations.
The 14 Elements of Process Safety Management
Here’s a comprehensive list of the core elements of process safety management:
Process Safety Information
Process safety information is the foundation of an effective process safety management program. It involves gathering and maintaining accurate data on hazardous chemicals, process technology, equipment design, and safe operating limits.
This information is essential for identifying potential hazards, conducting risk assessments, and developing appropriate safeguards.
Key components include material safety data sheets, process flow diagrams, piping and instrumentation diagrams, and equipment design specifications.
Operating Procedures
Operating procedures are detailed, written instructions that outline the steps for safely conducting activities involving hazardous chemicals.
These procedures cover tasks such as startup, normal operations, temporary operations, emergency shutdown, and normal shutdown.
They provide guidance on operating limits, safety systems, and emergency response actions. Clear and up-to-date operating procedures are crucial for ensuring consistent and safe operations, as well as training employees on proper practices.
Process Hazard Analysis within Process Safety Management
Process hazard analysis (PHA) is a systematic approach to identifying, evaluating, and controlling hazards associated with chemical processes.
It involves a thorough examination of the entire process, including equipment, instrumentation, utilities, human actions, and potential failure scenarios.
Various PHA techniques, such as Hazard and Operability Study (HAZOP), What-If Analysis, and Fault Tree Analysis, can be used to identify and mitigate risks proactively.
Employee Participation
Employee participation is a critical element of process safety management, as workers have firsthand knowledge and experience with the processes and potential hazards.
Employers should establish a system for employees to report potential hazards, suggest improvements, and participate in hazard analyses and incident investigations.
This fosters a culture of safety, empowers employees, and helps identify and address issues before they escalate.
Training
Comprehensive training is essential for ensuring that employees understand the hazards associated with their work and know how to perform their tasks safely.
Training should cover topics such as process safety information, operating procedures, emergency response plans, and safe work practices.
It should be provided initially and refreshed periodically, as well as whenever new processes or equipment are introduced or procedures are updated.
Contractor Safety Management
Contractors often perform specialized tasks or work during turnarounds and maintenance activities, which can introduce new hazards or increase existing risks.
Contractor safety management involves evaluating the safety performance of contractors, providing them with relevant process safety information, and ensuring they follow the facility’s safety policies and procedures.
Clear communication, oversight, and coordination between the facility and contractors are essential for maintaining a safe work environment.
Mechanical Integrity within Process Safety Management
Mechanical integrity refers to the ongoing effort to ensure that process equipment is designed, installed, operated, and maintained safely and reliably.
It involves activities such as equipment inspections, testing, preventive maintenance, quality assurance, and equipment replacement or repair.
Maintaining mechanical integrity helps prevent equipment failures, leaks, and other incidents that could lead to hazardous releases or explosions.
Incident Investigation
Incident investigation is the process of identifying the root causes of incidents, near-misses, or other unplanned events that could have resulted in harm to people, property, or the environment.
Thorough investigations are crucial for understanding what went wrong, implementing corrective actions, and preventing similar incidents from occurring in the future.
Effective incident investigation programs involve trained personnel, systematic methodologies, and a focus on identifying and addressing underlying systemic issues.
Management of Change
Management of change (MOC) is a systematic approach to evaluating and controlling potential hazards associated with changes to processes, equipment, procedures, or personnel.
It ensures that proposed changes are thoroughly reviewed, potential risks are identified and mitigated, and appropriate safeguards are implemented before the change is made.
MOC is critical for maintaining the integrity of the process safety management program and preventing unintended consequences from changes.
Pre-Startup Safety Review
A pre-startup safety review (PSSR) is a systematic evaluation of new or modified processes, equipment, or facilities before they are put into operation. It ensures that all necessary safety measures have been implemented, procedures are in place, and personnel are properly trained.
The PSSR involves a multidisciplinary team that reviews design specifications, safety systems, operating procedures, and other relevant information to identify and address any potential hazards before startup.
Emergency Planning and Response
Emergency planning and response involve developing and implementing procedures for safely handling emergencies that could arise from process-related incidents.
This includes establishing evacuation plans, identifying and training emergency response teams, coordinating with local emergency services, and maintaining appropriate equipment and resources.
Regular drills and exercises help ensure that personnel are prepared to respond effectively in the event of an emergency, minimizing the potential for harm.
Hot Work Permit and Process Safety Management
A hot work permit is a written authorization required before performing any work that involves open flames, sparks, or other sources of ignition in areas where flammable or combustible materials are present.
The permit system ensures that potential fire hazards are identified, appropriate precautions are taken, and the work is monitored and controlled to prevent fires or explosions. It is an essential component of safe work practices in process facilities.
Compliance Audits and Process Safety Management
Compliance audits are periodic evaluations of the process safety management program to ensure that it is being implemented effectively and following regulatory requirements and industry best practices.
Audits involve reviewing documentation, inspecting facilities and equipment, interviewing personnel, and assessing the overall effectiveness of the program elements. They help identify areas for improvement and ensure that the program remains robust and up-to-date.
Trade Secrets
Trade secrets refer to confidential information related to processes, equipment, or operations that provide a competitive advantage to the facility.
The process safety management standard recognizes the need to protect trade secrets while still ensuring that relevant safety information is available to employees, contractors, and regulatory authorities.
Facilities must establish procedures for maintaining the confidentiality of trade secrets while providing necessary process safety information to those who need it for safe operations and emergency response.
Implementing a Successful Process Safety Management (PSM) Program
Implementing an effective process safety management (PSM) program starts with developing a comprehensive PSM plan.
This plan should outline the policies, procedures, and processes necessary to comply with regulatory requirements and establish a robust safety culture within the organization. The PSM plan should be tailored to the specific operations, hazards, and risks associated with the facility.
Key elements of a PSM plan include:
- Defining the scope and applicability of the program
- Identifying the roles and responsibilities of personnel involved
- Establishing procedures for process safety information management
- Outlining the process hazard analysis methodology
- Defining operating procedures and safe work practices
- Establishing employee participation and training requirements
- Addressing contractor safety management
- Outlining mechanical integrity and preventive maintenance programs
- Establishing incident investigation and management of change procedures
- Defining pre-startup safety review processes
- Establishing emergency planning and response procedures
- Implementing a hot work permit system
- Outlining compliance audit processes
- Addressing trade secret protection
Roles and Responsibilities
Clearly defined roles and responsibilities are crucial for the successful implementation and ongoing management of a PSM program. Key roles and responsibilities typically include:
- Process Safety Management Coordinator/Manager: Responsible for overseeing the development, implementation, and continuous improvement of the PSM program.
- Process Safety Information Manager: Responsible for maintaining accurate and up-to-date process safety information, such as process technology, equipment design, and operating limits.
- Process Hazard Analysis Team: Responsible for conducting comprehensive hazard analyses and identifying potential risks and mitigation strategies.
- Operating Procedures Development Team: Responsible for developing and maintaining clear, concise, and up-to-date operating procedures.
- Training Coordinator: Responsible for developing and delivering effective process safety training programs for employees and contractors.
- Mechanical Integrity Coordinator: Responsible for overseeing the mechanical integrity program, including inspections, testing, and preventive maintenance activities.
- Incident Investigation Team: Responsible for thoroughly investigating incidents, identifying root causes, and recommending corrective actions.
- Management of Change Coordinator: Responsible for ensuring that all proposed changes are properly evaluated, approved, and documented.
- Emergency Response Coordinator: Responsible for developing and maintaining emergency response plans and coordinating emergency drills and exercises.
- Compliance Audit Team: Responsible for conducting periodic audits to assess the effectiveness of the PSM program and identify areas for improvement.
Employee Engagement and Training
Employee engagement and training are critical components of a successful PSM program. Employees at all levels of the organization must understand the importance of process safety and their roles and responsibilities in maintaining a safe work environment.
Effective employee engagement strategies may include:
- Establishing a process safety committee or employee participation team
- Encouraging employees to report safety concerns and near-misses
- Involving employees in the development and review of operating procedures
- Providing regular safety meetings and toolbox talks
- Recognizing and rewarding safe behavior and safety improvements
Comprehensive process safety training programs should be developed and implemented to ensure that employees have the knowledge and skills necessary to perform their duties safely. Training topics may include:
Overview of process safety management and regulatory requirements;
- Process hazard analysis techniques
- Safe operating procedures and work practices
- Emergency response and incident reporting
- Mechanical integrity and equipment maintenance
- Management of change procedures
- Contractor safety management
- Incident investigation and root cause analysis
Contractor Management and Process Safety Management
Contractors play a significant role in many process industries, and their activities can have a direct impact on process safety. Effective contractor management is essential to ensure that contractors understand and comply with the facility’s process safety requirements.
Key elements of contractor safety management include:
- Pre-qualification and selection of competent contractors
- Providing contractors with site-specific process safety information
- Ensuring contractors receive appropriate process safety training
- Monitoring contractor activities and performance
- Establishing clear lines of communication and reporting
- Conducting post-job reviews and evaluations
Documentation and Recordkeeping
Accurate and up-to-date documentation is crucial for maintaining an effective PSM program. Documentation and recordkeeping requirements may include:
- Process safety information, such as process technology, equipment design, and operating limits
- Process hazard analysis reports
- Operating procedures and safe work practices
- Employee training records
- Mechanical integrity inspection and maintenance records
- Incident investigation reports
- Management of change documentation
- Pre-startup safety review records
- Emergency response plans and drill records
- Compliance audit reports
Proper documentation and recordkeeping not only help ensure compliance with regulatory requirements but also provide valuable information for continuous improvement and lessons learned.
By developing a comprehensive PSM plan, clearly defining roles and responsibilities, engaging and training employees, managing contractors effectively, and maintaining thorough documentation and recordkeeping, organizations can successfully implement and maintain a robust process safety management program.
Maintaining and Improving Process Safety Management (PSM)
Process Safety Management (PSM) is not a one-time effort; it requires continuous improvement to ensure the effectiveness of the program and to adapt to changing conditions, technologies, and regulations.
Continuous improvement involves regularly reviewing and updating the PSM program, identifying areas for improvement, and implementing corrective and preventive actions.
One approach to continuous improvement is the Plan-Do-Check-Act (PDCA) cycle, which involves:
- Plan: Establish objectives, processes, and procedures for the PSM program.
- Do: Implement the planned processes and procedures.
- Check: Monitor and measure the performance of the PSM program, and identify areas for improvement.
- Act: Take corrective and preventive actions to address identified issues and improve the PSM program.
Continuous improvement also involves learning from incidents, near-misses, and best practices within the organization and across the industry. Sharing lessons learned and implementing corrective actions can help prevent similar incidents from occurring in the future.
Auditing and Corrective Actions
Regular audits are a critical component of maintaining and improving a PSM program. Audits help identify gaps, deficiencies, and areas for improvement within the program. There are two main types of audits:
- Compliance audits: These audits evaluate whether the PSM program meets regulatory requirements, such as the OSHA PSM standard or industry-specific standards.
- Program audits: These audits assess the effectiveness of the PSM program in managing process safety risks and preventing incidents.
Audits should be conducted by qualified personnel, either internal or external to the organization, who have the necessary expertise and objectivity to evaluate the PSM program. The audit process typically involves document reviews, interviews with personnel, and on-site inspections.
When deficiencies or non-conformities are identified during an audit, corrective actions must be taken to address the issues.
Corrective actions may involve revising procedures, providing additional training, or implementing new controls or safeguards. The corrective actions should be documented, and their effectiveness should be monitored and verified.
Management Review and Leadership Support
Management review and leadership support are essential for maintaining and improving the PSM program.
Management should regularly review the performance of the PSM program, including audit results, incident reports, and key performance indicators (KPIs). This review helps ensure that the program remains effective and aligned with the organization’s goals and objectives.
Leadership support is crucial for fostering a strong process safety culture and providing the necessary resources for implementing and maintaining the PSM program. Leaders should demonstrate their commitment to process safety by:
- Communicating the importance of process safety to all employees
- Allocating adequate resources (personnel, budget, training) for the PSM program
- Ensuring that process safety is integrated into decision-making processes
- Promoting employee participation and engagement in process safety initiatives
- Holding personnel accountable for their roles and responsibilities in the PSM program
Effective management review and leadership support can help drive continuous improvement and ensure that the PSM program remains a priority within the organization.
Process Safety Culture of Process Safety Management
A strong process safety culture is essential for maintaining and improving PSM. Process safety culture refers to the attitudes, values, and beliefs that an organization and its employees share regarding the importance of process safety. A positive process safety culture promotes a mindset of proactively identifying and managing process safety risks, rather than simply reacting to incidents.
Key elements of a strong process safety culture include:
- Leadership commitment and accountability
- Employee empowerment and participation
- Open communication and reporting of concerns
- Continuous learning and improvement
- Effective training and competency development
- Prioritization of process safety over production pressures
Fostering a positive process safety culture requires ongoing efforts, such as training, communication, and reinforcement of desired behaviors. It also involves recognizing and addressing cultural barriers or weaknesses that may hinder process safety.
Emerging Technologies and Best Practices
Maintaining and improving PSM also involves staying up-to-date with emerging technologies and industry best practices. As new technologies and innovations become available, organizations should evaluate their potential to enhance process safety and consider adopting them when appropriate.
Some emerging technologies that can benefit PSM include:
- Advanced process monitoring and control systems
- Predictive analytics and machine learning for risk assessment
- Augmented reality and virtual reality for training and visualization
- Drones and robotics for inspections and maintenance
- Digital twin technology for process simulation and optimization
In addition to adopting new technologies, organizations should also stay informed about industry best practices and lessons learned from other companies or sectors.
Participating in industry associations, attending conferences, and benchmarking against peers can provide valuable insights and opportunities for continuous improvement.
By embracing emerging technologies and best practices, organizations can enhance their ability to identify and mitigate process safety risks, improve operational efficiency, and stay ahead of regulatory changes and industry trends.
Regulatory Compliance and Industry Standards
Ensuring compliance with relevant regulations and industry standards is a critical aspect of process safety management. Failure to adhere to these requirements can result in severe consequences, including fines, legal liabilities, and potential incidents that can endanger workers, communities, and the environment.
Key Regulatory Frameworks and Industry Standards Related to Process Safety Management:
OSHA Process Safety Management (PSM) Standard
The Occupational Safety and Health Administration’s (OSHA) Process Safety Management (PSM) standard (29 CFR 1910.119) is a comprehensive set of regulations aimed at preventing or minimizing the consequences of catastrophic releases of toxic, reactive, flammable, or explosive chemicals.
The PSM standard applies to facilities that handle highly hazardous chemicals above specified threshold quantities
It outlines the 14 elements of a PSM program, including process safety information, process hazard analysis, operating procedures, employee participation, training, contractor safety management, mechanical integrity, incident investigation, management of change, pre-startup safety review, emergency planning and response, hot work permits, compliance audits, and trade secrets.
EPA Risk Management Plan (RMP)
The Environmental Protection Agency’s (EPA) Risk Management Plan (RMP) rule (40 CFR Part 68) is designed to prevent accidental releases of hazardous substances and minimize the consequences of such releases.
Facilities that use or store certain regulated substances above threshold quantities must develop and implement a risk management program that includes a hazard assessment, prevention program, and emergency response program.
The RMP rule complements the OSHA PSM standard and requires facilities to coordinate their efforts with local emergency response agencies.
Industry-Specific Standards and Guidelines
In addition to government regulations, various industry organizations have developed standards and guidelines specific to their respective sectors.
For example, the American Petroleum Institute (API) has published numerous recommended practices and standards related to process safety management in the oil and gas industry.
The Center for Chemical Process Safety (CCPS) provides guidelines and resources for chemical process safety management.
Other industry-specific standards may be developed by organizations such as the American Chemistry Council (ACC), the International Association of Oil & Gas Producers (IOGP), and the American Society of Mechanical Engineers (ASME).
International Regulations and Standards of Process Safety Management
For companies operating globally, it is essential to comply with international regulations and standards related to process safety management.
The International Organization for Standardization (ISO) has developed several relevant standards, including ISO 45001 for occupational health and safety management systems and ISO 31000 for risk management.
The Seveso Directive in the European Union addresses the prevention of major industrial accidents involving dangerous substances. Other international regulations and standards may be applicable depending on the country or region of operation.
Case Studies and Examples
Major Process Safety Incidents
Process safety management is critical to preventing catastrophic incidents in facilities that handle hazardous materials.
- Unfortunately, history has witnessed several major process safety incidents that have resulted in loss of life, environmental damage, and significant financial losses. These incidents serve as stark reminders of the importance of implementing and maintaining robust process safety management systems.
- One of the most infamous process safety incidents is the Bhopal Gas Tragedy in India. In 1984, a leak of methyl isocyanate gas from a pesticide plant owned by Union Carbide Corporation resulted in the exposure of hundreds of thousands of people to the toxic gas. The incident claimed over 15,000 lives and left countless others with lifelong health issues.
It highlighted the devastating consequences of inadequate safety measures and poor emergency response planning. - Another notable incident is the BP Deepwater Horizon oil spill in the Gulf of Mexico in 2010. The explosion on the offshore drilling rig led to the largest marine oil spill in history, causing extensive environmental damage and economic losses.
Investigations revealed multiple process safety failures, including inadequate risk assessment, poor maintenance practices, and a lack of effective oversight. - The Phillips Petroleum Chemical Plant Explosion in Pasadena, Texas, in 1989, is another example of a major process safety incident. The explosion, caused by a runaway reaction during the production of a gasoline additive, resulted in 23 fatalities and numerous injuries.
It highlighted the importance of thorough process hazard analysis, effective operating procedures, and proper employee training.
Successful Process Safety Management (PSM) Implementation Stories
Despite the challenges, many organizations have successfully implemented process safety management systems, demonstrating the benefits of a proactive and comprehensive approach to managing process risks.
One notable success story is the DuPont Company’s journey towards process safety excellence. After a series of incidents in the late 1980s and early 1990s, DuPont embarked on a company-wide effort to improve its process safety performance.
This included implementing robust management systems, fostering a strong safety culture, and investing in employee training and engagement. As a result, DuPont has consistently achieved industry-leading safety performance.
Example
Another example is the Chevron Richmond Refinery in California. Following a major fire in 1999, the refinery underwent a comprehensive process safety management program overhaul.
This involved upgrading equipment, improving operating procedures, and enhancing employee training programs. The refinery has since achieved significant improvements in process safety performance and has been recognized for its commitment to continuous improvement.
Lessons Learned and Best Practices
From these incidents and success stories, several key lessons and best practices emerge for effective process safety management:
- Leadership commitment: Strong leadership commitment and visible support from top management are essential for establishing and maintaining an effective process safety management program.
- Employee engagement: Involving employees at all levels in the development and implementation of process safety management systems is crucial for fostering a strong safety culture and ensuring effective risk management.
- Continuous improvement: Process safety management is an ongoing effort that requires continuous monitoring, evaluation, and improvement. Regular audits, incident investigations, and management reviews are necessary to identify and address gaps or weaknesses in the system.
- Training and competency: Comprehensive training programs and competency assurance processes are vital for ensuring that employees have the knowledge and skills necessary to perform their tasks safely and effectively.
- Effective communication: Clear and transparent communication channels, both within the organization and with external stakeholders, are essential for sharing information, addressing concerns, and promoting a culture of safety.
- Contractor management: Effective management of contractors and third-party service providers is crucial, as their activities can significantly impact process safety.
- Lessons learned: Thoroughly investigating incidents, near-misses, and potential hazards, and sharing lessons learned across the industry, can help prevent similar occurrences and drive continuous improvement.
Recap of Process Safety Management (PSM)
Process Safety Management (PSM) is a comprehensive and systematic approach to identifying, evaluating, and controlling hazards associated with the use of highly hazardous chemicals.
Throughout this article, we have explored the 14 essential elements of PSM, as outlined by the Occupational Safety and Health Administration (OSHA), and the steps involved in implementing and maintaining an effective PSM program.
The key points covered include:
- Understanding the importance of Process Safety Information, Operating Procedures, Process Hazard Analysis, and Employee Participation in identifying and mitigating risks.
- Implementing robust Training programs, Contractor Safety Management, and Mechanical Integrity practices to ensure safe operations.
- Conducting thorough Incident Investigations, Managing Changes effectively, and performing Pre-Startup Safety Reviews to prevent accidents.
- Establishing comprehensive Emergency Planning and Response, Hot Work Permit, and Compliance Audit systems.
- Protecting Trade Secrets while maintaining transparency and accountability.
- Developing a PSM Plan, defining roles and responsibilities, and engaging employees and contractors.
- Maintaining documentation and records, conducting audits, and implementing corrective actions for continuous improvement.
- Fostering a strong Process Safety Culture and leveraging emerging technologies and best practices.
- Complying with OSHA PSM Standard, EPA Risk Management Plan (RMP), industry-specific standards, and international regulations.
By implementing these key elements, organizations can effectively manage the risks associated with highly hazardous chemicals and protect their employees, communities, and the environment.
Importance of Process Safety Management
Process Safety Management is crucial for organizations that handle highly hazardous chemicals, as it helps prevent catastrophic accidents, injuries, and environmental disasters.
Effective PSM programs not only protect human life and the environment but also safeguard businesses from financial losses, legal liabilities, and reputational damage.
PSM is essential for maintaining safe and reliable operations, promoting a positive safety culture, and fostering trust among employees, stakeholders, and the community.
By proactively identifying and mitigating risks, organizations can avoid costly incidents, production disruptions, and regulatory fines.
Furthermore, PSM plays a vital role in ensuring regulatory compliance and maintaining a social license to operate.
By adhering to OSHA’s PSM Standard, EPA’s Risk Management Plan, and other industry-specific regulations, organizations demonstrate their commitment to safety and responsible operations.
Future Trends and Challenges
As the chemical industry continues to evolve, Process Safety Management will face new challenges and trends. Some of the future trends and challenges include:
- Emerging Technologies: The integration of advanced technologies such as Industrial Internet of Things (IIoT), data analytics, and artificial intelligence will reshape PSM practices.
These technologies can enhance risk assessment, predictive maintenance, and real-time monitoring, but they also introduce new cybersecurity risks and skill requirements.
- Aging Infrastructure: Many chemical facilities and infrastructure are aging, increasing the need for effective mechanical integrity programs, risk assessments, and proactive maintenance strategies.
- Regulatory Changes: Evolving regulations, such as the EPA’s Risk Management Plan Reconsideration Rule and the OSHA’s proposed updates to the PSM Standard, will require organizations to adapt their PSM programs and comply with new requirements.
- Workforce Challenges: The industry faces a shortage of skilled and experienced process safety professionals, necessitating robust training programs, knowledge transfer initiatives, and attracting and retaining talent.
- Climate Change and Sustainability: As the industry focuses on reducing its environmental footprint and addressing climate change, PSM programs will need to incorporate sustainable practices, energy efficiency measures, and resilience planning.
- Contractor Management: With the increasing use of contractors and third-party service providers, effective contractor safety management and oversight will become even more critical.
- Organizational Culture: Fostering a strong process safety culture, promoting leadership commitment, and encouraging employee engagement will remain a crucial challenge for many organizations.
By embracing a culture of safety excellence and adapting to changing circumstances, the chemical industry can maintain its commitment to Process Safety Management and ensure the protection of people, assets, and the environment.
SixSigma.us offers both Live Virtual classes as well as Online Self-Paced training. Most option includes access to the same great Master Black Belt instructors that teach our World Class in-person sessions. Sign-up today!
Virtual Classroom Training Programs Self-Paced Online Training Programs