Process Operations in Six Sigma, Manufacturing, and Business. All to Know
These days, process operations hold huge importance for manufacturers navigating fast-paced, ultra-competitive landscapes.
They cover the intricate planning, execution, and oversight of diverse processes transforming raw materials into finished goods.
From product design to supply chain governance, operations span a wide range of tasks — all aiming for workflow mastery, lower costs, and maximized productivity.
At the core lies streamlining methods, removing wasted efforts, and constantly upgrading methods to boost efficiency and fulfill what customers want.
This multi-faceted area borrows ideas from domains like Lean manufacturing, Six Sigma, Automation, Supply Chain Management, and beyond.
The focus stays on refining intricate transformations through a mix of structured planning and opportunistic refinements — propelling continual evolution and optimization crucial for sustained excellence in dynamic times.
Process operations stand as the beating heart propelling optimization and maintaining competitiveness through disciplined methodology and data-driven agility.
Key Highlights
- Process operations cover planning, executing, and overseeing varied manufacturing and production methods.
- It considers a mix of tasks from product design to supply chain governance, targeting workflow mastery and lower costs.
- Some major bits involve production scheduling, mapping method flows, quality control, automation, lean manufacturing, and never-ending upgrading.
- The goal centers on streamlining things, wasting less, boosting efficiency, satisfying regulations, and more.
- Cutting-edge tech like Industry 4.0, IoT, and data analytics are reshaping operations for heightened flexibility and competitive spirit.
- Connectivity and information open doors to opportunistic improvements optimizing people and resource allocation in this constantly evolving industry core.
- By streamlining complexity and surgically targeting friction points, process operations orchestrate reliability and flow enhancement vital for competitive advantage.
What is Process Operations?
Process operations refer to the various tasks and activities involved in manufacturing or creating goods/services.
It covers the whole transformation process from raw materials to finished products ready for customers. This area plays a vital role in ensuring smooth, effective production meeting quality benchmarks, and maintaining profits.
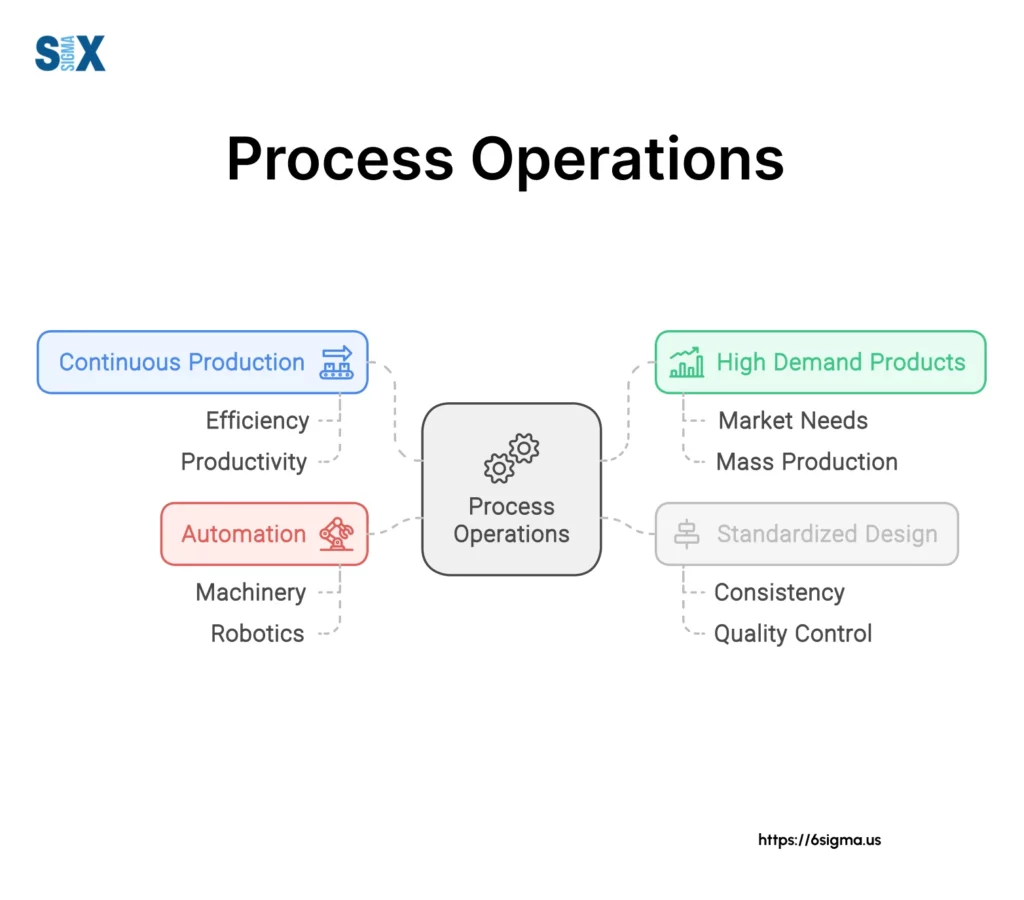
The core focus centers on streamlining and optimizing how materials, info, and resources flow throughout the creation cycle.
It involves carefully designing, scheduling, and managing the different methods — whether continuous output, batch making, or assembly line setups.
Efficient process operations prove crucial for mass manufacturing, with consistency and profits demanding high volumes of standard products.
It requires aligning varied aspects like production planning, materials handling, process monitoring, and addressing bottlenecks.
Additionally, operations expand beyond physical making. It also considers supporting functions like supply chain governance, inventory oversight, and quality measures satisfying customer/regulatory needs.
Competitive pressure fuels continual upgrading via lean concepts, Six Sigma techniques, and total workflow mastery initiatives. These aim for smoother flows, less wasted efforts, and unceasing upgrades lowering costs and boosting gains over the long haul.
Types of Process Operations
There are several different types of process operations used in manufacturing. The choice depends on factors like the product, production volume, and available resources.
Continuous Production
This type of manufacturing operation runs 24/7 to produce high volumes of the same product continuously. Examples include oil refineries, chemical plants, and some food/beverage production lines. The processes are automated with little human intervention required.
Mass Manufacturing
Mass manufacturing operations produce large quantities of identical products efficiently through highly specialized equipment and division of labor. Famous examples are automotive assembly lines and consumer electronics manufacturing. Consistency and quality control are critical.
Batch Production
In batch production, a quantity of a product is manufactured, completed, and then the process is stopped and restarted for the next batch.
This allows for the production of different product variations without full changeovers. Food processing, pharmaceuticals, and specialty chemicals often use batch operations.
Job Shop Production
This involves manufacturing customized products one at a time or in very small batches. Each job goes through designated work centers based on the specific requirements. Job shops handle low volumes of unique, non-standardized products like machinery, tools, and prototypes.
The type of process selected impacts factors like equipment requirements, material flows, quality procedures, staffing, and overall production strategy. Choosing the right process for the product and demand is crucial for optimizing operations.
Process Flow and Design within Process Operations
At the heart of any process operations is the flow and design of the manufacturing process itself. This involves carefully mapping out and planning each step in the sequence of events to transform raw materials into finished products.
Process flow refers to the specific path and order that materials, components, and information move through during the manufacturing cycle.
An efficient process flow minimizes bottlenecks, delays, and excessive material handling or transportation. Techniques like value stream mapping can help identify and eliminate non-value-added activities.
The process design outlines the specific operations, machinery, tooling, and methods that will be used at each process step.
It specifies parameters like cycle times, temperatures, pressures, and other control variables. Product and component design also gets taken into account to ensure manufacturability.
Some key considerations in process flow and design include:
Production Rate – The required output rate of the process based on takt time and customer demand. This determines bottleneck operations.
Layout – The physical layout and configuration of the production line or cell. Optimizing material and personnel flow is critical.
Automation – The degree of human labor vs automated machinery and material handling equipment integrated into the process.
Flexibility – How well the process can accommodate running different product models, sizes, or variations on the same line.
Product Standardization – Narrowing the number of components and part variations used enables more efficient, repetitive processes.
Whether for continuous, repetitive processes or batch manufacturing of discrete parts and assemblies, the process flow and design lays the foundation for consistent, capable, and optimized operations.
Computer simulation and modeling can help validate processes before physical implementation.
Production Planning and Control within Process Operations
Effective production planning and control are critical for efficient process operations. This involves carefully planning and scheduling the entire production process to ensure smooth flow and optimal utilization of resources.
Production Planning
Production planning determines what products will be produced when they will be produced, and in what quantities.
It involves forecasting demand, determining production capacities, and developing a master production schedule. Proper production planning ensures that materials, labor, and equipment are available when needed to meet customer demand while minimizing inventory costs.
Production Control
Production control manages and monitors the actual production process according to the production plan. This includes:
Production Scheduling – Determining the sequence of operations, start/stop times for each process, and prioritizing production runs to meet due dates.
Material Requirements Planning (MRP) – Calculating raw material needs and scheduling deliveries to ensure adequate inventory when needed for production.
Inventory Management – Tracking and controlling inventory levels of raw materials, work-in-process, and finished goods to prevent shortages or excess.
Capacity Control – Monitoring and adjusting production capacity by scheduling overtime, hiring personnel, or obtaining additional equipment as needed.
Detailed production reporting and data collection allow for monitoring of the process against the plan. Any deviations can then be analyzed and corrective actions taken through adjustments to staffing, inventory, maintenance schedules, etc.
Quality Control and Improvement within Process Operations
Quality is paramount in process operations to ensure products meet specifications and customer requirements. Effective quality control and continuous improvement practices are essential for operational excellence.
Quality Control
Quality control involves monitoring and inspecting processes, inputs, and outputs to detect defects or deviations from standards. Common quality control techniques include:
– Statistical process control (SPC) using control charts to identify variations
– Sampling plans to inspect representative products or materials
– Automated inspection using sensors and machine vision systems
– First piece and last piece inspection of production runs
Having rigorous quality control allows you to identify issues early, contain them, and prevent defects from reaching customers. It provides data to analyze root causes.
Continuous Improvement
No process is perfect, so there are always opportunities to improve operational efficiency, reduce costs, and enhance quality. Continuous improvement is an ongoing effort to incrementally improve processes over time. Proven methodologies include:
- Six Sigma – Data-driven approach to eliminate defects and reduce variability
- Lean manufacturing – Systematic approach to minimize waste and optimize flow
- Kaizen – Philosophy of making small, incremental changes regularly
- Plan-Do-Check-Act cycle – Iterative process to test changes and standardize improvements
Applying these techniques, manufacturers analyze process data, identify opportunities, implement changes, and measure results. Engaging employees is critical for sustainable continuous improvement.
Supply Chain and Logistics with Process Operations
Effective process operations require seamless integration with supply chain and logistics functions.
Supply chain management encompasses all the activities involved in planning, implementing, and controlling the flow of goods, services, and information from the point of origin to the point of consumption.
Material Handling and Logistics
Material handling is a crucial aspect of process operations that deals with the movement, protection, storage, and control of materials throughout the manufacturing process.
Efficient material handling systems ensure that raw materials, work-in-process goods, and finished products are transported smoothly within the facility. Proper logistics planning is essential to coordinate materials and products’ inbound and outbound transportation.
Inventory Management with Process Operations
Inventory management is the practice of ordering, storing, and using a company’s inventory, including raw materials, components, and finished products.
Maintaining optimal inventory levels is critical for process operations to avoid stockouts that can disrupt production while minimizing excess inventory that ties up working capital.
Techniques like just-in-time (JIT) inventory, vendor-managed inventory (VMI), and inventory optimization software help synchronize inventory with production requirements.
Distribution and Warehousing
The distribution process involves receiving finished goods from manufacturing, storing them in warehouses, picking and packing orders, and delivering products to customers.
Warehouses play a pivotal role in buffering the manufacturing process from fluctuations in supply and demand. Efficient warehouse management, layout design, and distribution logistics are essential for the timely delivery of products to customers.
Operational Excellence and Optimization with Process Operations
Achieving operational excellence and continuous optimization is crucial for any manufacturing or production operation. The ultimate goals are to maximize efficiency, reduce costs, improve quality, and drive sustainable growth.
Lean Manufacturing
Lean manufacturing principles focus on minimizing waste and maximizing value for the customer. This involves techniques like just-in-time production, continuous flow, pull systems, and eliminating non-value-added activities. Implementing lean practices streamlines processes, reduces inventory levels, and improves cycle times.
Six Sigma
Six Sigma is a data-driven methodology that aims to virtually eliminate defects and variability in processes. It follows the DMAIC (Define, Measure, Analyze, Improve, Control) roadmap to identify the root causes of issues and make improvements. Applying Six Sigma leads to tighter process control and fewer quality problems.
Kaizen (Continuous Improvement) and Process Operations
Kaizen is the philosophy of continuously making small, incremental improvements. It empowers employees at all levels to identify opportunities and implement changes. This creates a culture of ongoing process optimization and operational discipline.
Overall Equipment Effectiveness (OEE)
OEE measures how effectively manufacturing operations are utilized compared to their full potential. It accounts for availability, performance, and quality. Maximizing OEE involves addressing equipment downtime, inefficient performance, and quality defects.
Production Bottlenecks and Constraints with Process Operations
Identifying and addressing bottlenecks or constraints in the production process is vital. Techniques like value stream mapping, theory of constraints, and simulation modeling can pinpoint the limiting factors. Alleviating these allows the entire system to operate more efficiently.
Technology and Automation
Leveraging new technologies like industrial IoT, big data, AI/machine learning, robotics, and automation enables smarter, more optimized operations. Automated process monitoring, predictive maintenance, and real-time production adjustments drive improvements.
Change Management
Effectively managing organizational change is key when optimizing processes. Having a structured approach that addresses people, processes, and technology aspects maximizes improvement initiative success.
SixSigma.us offers both Live Virtual classes as well as Online Self-Paced training. Most option includes access to the same great Master Black Belt instructors that teach our World Class in-person sessions. Sign-up today!
Virtual Classroom Training Programs Self-Paced Online Training Programs