The Ultimate Guide to Manufacturing Compliance: Quality, Safety, and Regulatory Adherence
Compliance is the foundation for building a flexible and scalable manufacturing unit. As the complexities of regulatory landscapes grow, meeting higher demands is becoming more tough.
Manufacturing compliance plays a key role in ensuring all the above happen, most effectively and efficiently.
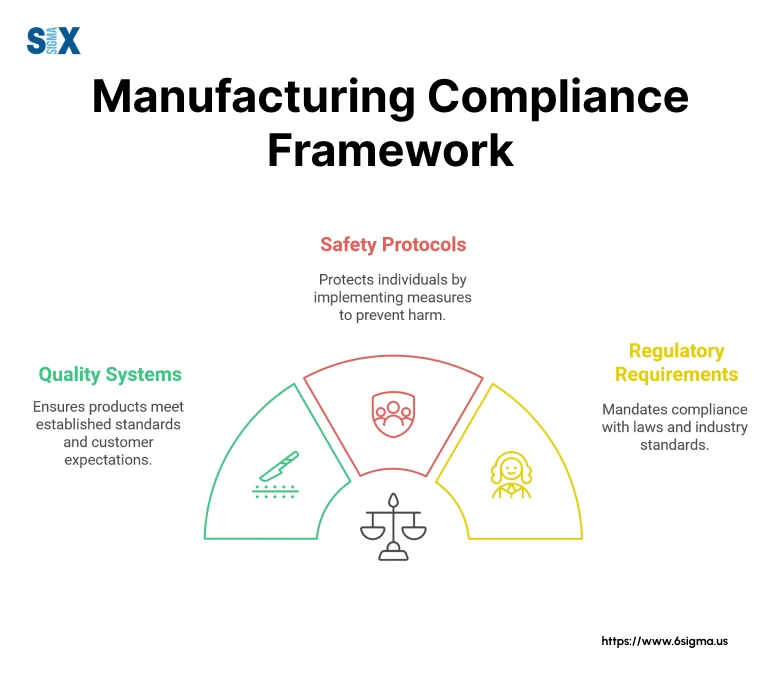
This article will equip you to:
- Building effective compliance frameworks that align with both regulatory requirements and business objectives
- Implementing data-driven approaches to compliance monitoring and improvement
- Leveraging quality management tools to enhance compliance outcomes
- Developing sustainable compliance cultures within manufacturing organizations
Understanding Manufacturing Compliance
Manufacturing compliance consists of many interconnected responsibilities. It represents a systematic approach to meeting regulatory requirements, industry standards, and internal quality controls that govern the production process.
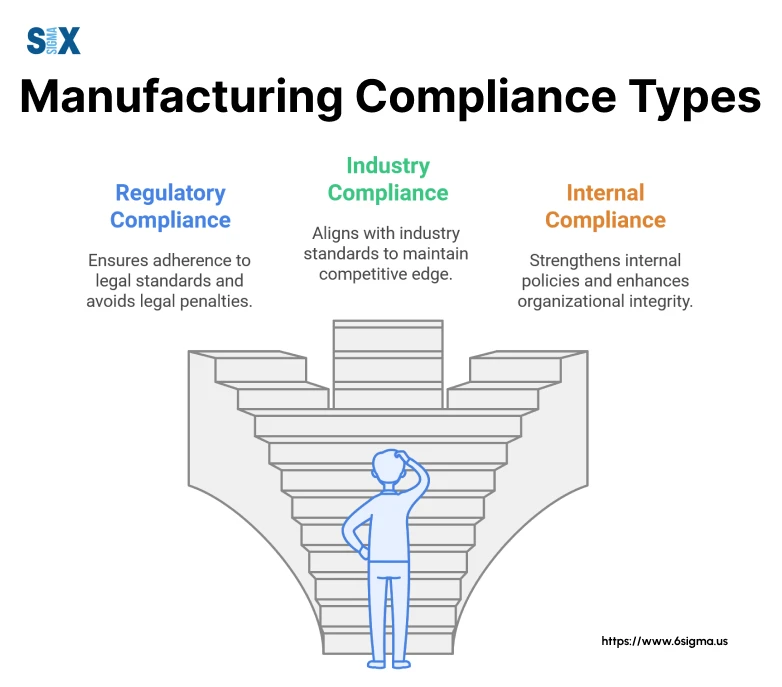
Types of compliance that form the foundation of a robust manufacturing compliance framework:
Regulatory Compliance
This represents the cornerstone of manufacturing compliance, encompassing mandatory requirements set by government agencies. While leading projects at various pharmaceutical manufacturers, FDA regulations shape every aspect of production processes. These requirements are non-negotiable and form the baseline for operational legitimacy.
Industry Standards Compliance
Industry standards compliance often extends beyond regulatory requirements. Voluntary but crucial standards, such as ISO 9001 and GMP (Good Manufacturing Practice), establish benchmarks for quality and operational excellence. Adherence to these standards not only ensures product quality but also opens doors to new market opportunities.
Internal Policy Compliance
Internal policies often exceed regulatory and industry standards. These company-specific requirements reflect organizational values and strategic objectives, creating a comprehensive framework for operational excellence.
What is a certification of compliance?
A certificate of compliance in manufacturing serves as documented evidence that products meet specified requirements. These certificates play a crucial role in supply chain management and customer relationships. They provide formal verification that products conform to regulatory standards, customer specifications, and quality requirements.
Leading a Compliance Transformation?
Get equipped to drive organizational change with our Six Sigma Champion training. Learn to select, support, and drive successful improvement projects while building a sustainable culture of compliance.
Key Areas of Manufacturing Compliance
There are several critical areas where manufacturing compliance risks intersect with operational excellence. Understanding these key areas is essential for developing comprehensive compliance strategies that align with manufacturing standards while driving continuous improvement.
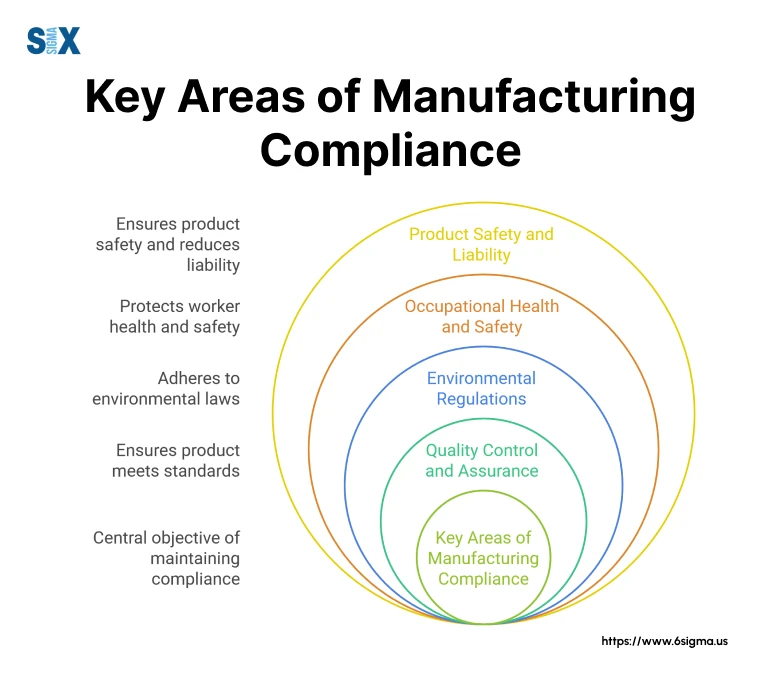
Quality Control and Assurance
Quality control serves as the cornerstone of effective manufacturing compliance. Through implementing statistical process control methods across various production lines, robust quality systems not only ensure compliance but also drive operational efficiency. The key is integrating quality controls seamlessly into production processes rather than treating them as separate compliance checkpoints.
Environmental Regulations with Manufacturing Compliance
Environmental compliance has become increasingly complex in modern manufacturing. Use systematic approaches to managing environmental impacts through precise measurement and control systems. These initiatives not only ensure compliance with EPA regulations but also result in significant cost savings through waste reduction and energy efficiency improvements.
Occupational Health and Safety
Effective health and safety compliance requires a data-driven approach. By applying Six Sigma methodologies to safety processes, you can consistently achieve significant reductions in workplace incidents while maintaining high productivity levels.
Product Safety and Liability with Manufacturing Compliance
Product safety compliance requires a comprehensive approach integrating design controls, risk management, and validation processes. This proactive stance on product safety not only ensures regulatory compliance but also significantly reduces liability risks.
Data Protection and Cybersecurity
Cybersecurity has become a critical compliance concern. I suggest using frameworks that ensure both data protection compliance and operational efficiency. This includes establishing secure protocols for handling sensitive manufacturing data while maintaining system accessibility for authorized personnel.
Ethical and Labor Practices with Manufacturing Compliance
Ethical compliance in manufacturing extends beyond basic labor laws. Use comprehensive ethical compliance programs that address cultural differences while maintaining consistent standards across international operations.
Manufacturing Compliance Regulations and Standards
Understanding and effectively managing manufacturing compliance regulations and standards is crucial for operational success.
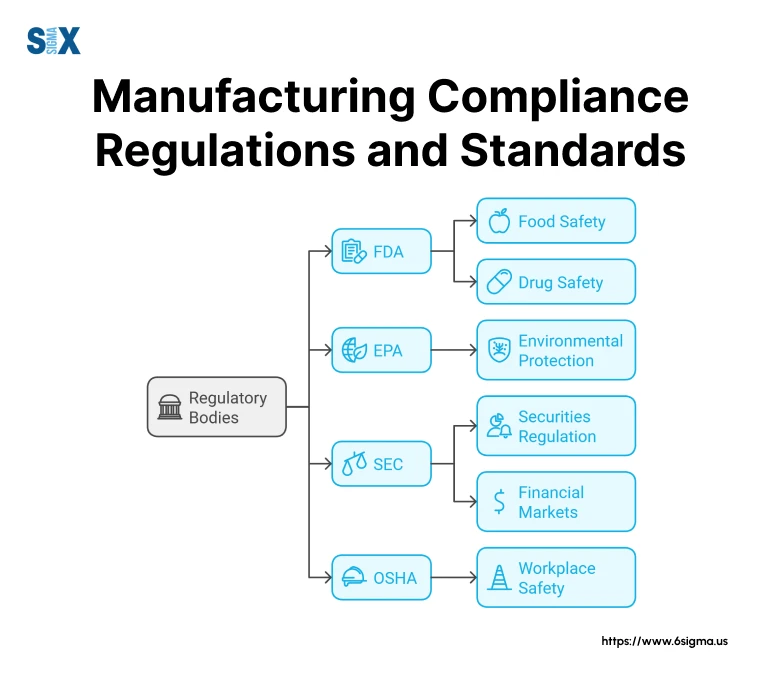
Major Regulatory Bodies
In the United States, three primary agencies oversee manufacturing compliance regulations: the FDA, EPA, and OSHA.
FDA compliance requirements require systems that not only meet regulatory standards but also improve operational efficiency.
The EPA’s environmental regulations have become increasingly stringent, and proactive environmental compliance programs can lead to both regulatory success and cost savings.
OSHA’s workplace safety standards require a systematic approach to risk management and safety protocols.
Key Manufacturing Compliance Standards
ISO 9001 serves as the foundation for quality management systems, and I’ve guided numerous organizations through certification processes. ISO standards provide a common language for quality across borders.
Good Manufacturing Practices (GMP) are particularly critical in regulated industries as they require both technical expertise and cultural transformation.
HACCP principles provide a systematic approach to product safety and quality control.
Industry-Specific Regulations
Each manufacturing sector faces unique regulatory challenges. For example, medical device manufacturers, must address FDA 21 CFR Part 820, while automotive industry clients must address TS 16949 requirements.
International Compliance Considerations
Global manufacturing operations face additional complexity in meeting international standards. Successful international compliance requires understanding both local regulations and global standards. For instance, European manufacturers align US-based quality systems with EU MDR requirements, creating harmonized compliance approaches that work across jurisdictions.
The key to managing these various manufacturing compliance regulations effectively lies in developing integrated management systems that address multiple requirements simultaneously.
Implementing a Manufacturing Compliance Program
Successful manufacturing compliance implementation requires a structured, data-driven approach. Use a comprehensive framework that integrates Six Sigma principles with compliance requirements to create sustainable, effective programs.
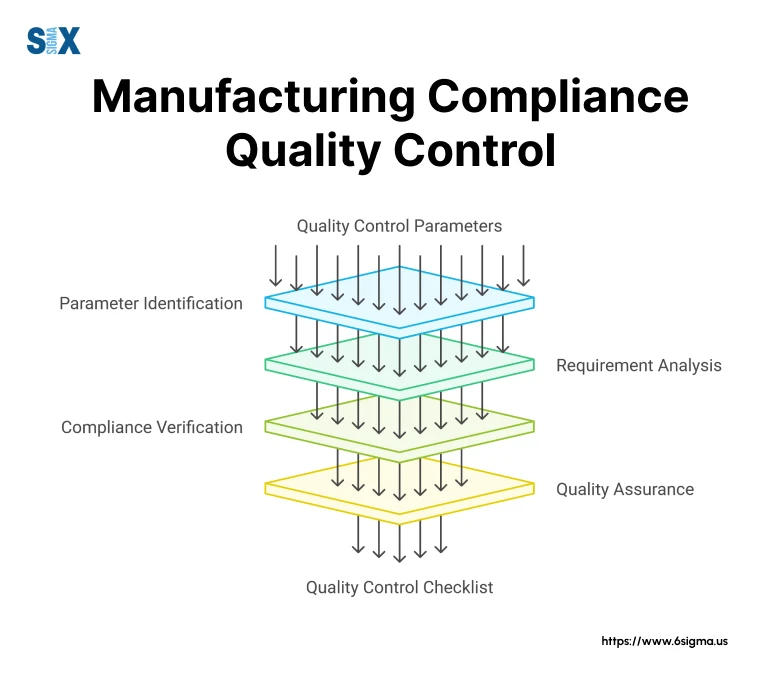
Conducting a Compliance Risk Assessment
The foundation of any effective compliance program begins with a thorough risk assessment. You can use an approach like FMEA (Failure Mode and Effects Analysis) to identify and prioritize compliance risks. This method helps organizations allocate resources effectively while ensuring comprehensive coverage of critical compliance areas.
Developing a Compliance Strategy
Strategy development must align with both regulatory requirements and business objectives. Use a strategic framework that integrates compliance goals with operational excellence initiatives, creating a unified approach that enhances both compliance and productivity.
Creating and Implementing Policies and Procedures
Effective policies must be both comprehensive and practical. Successful implementation requires clear documentation combined with process controls. Using Six Sigma tools, you can develop standard operating procedures that ensure consistency while maintaining operational efficiency.
Manufacturing Compliance Training Programs
Training represents a critical component of any compliance program. Effective programs must be role-specific and performance-based. I typically suggest implementing a tiered training approach, starting with basic compliance awareness and progressing to detailed procedural training for specific job functions.
Monitoring and Auditing Processes
Regular monitoring is essential for maintaining compliance effectiveness. I suggest developing metrics-based monitoring systems that provide real-time visibility into compliance performance. These systems should include both leading and lagging indicators to enable proactive management of compliance risks.
Continuous Improvement and Adaptation of the Manufacturing Compliance
Compliance programs must evolve to remain effective. Use adaptive compliance systems that respond to changing regulatory requirements while maintaining operational efficiency. This includes regular reviews of program effectiveness and systematic approaches to implementing improvements.
The key to successful implementation lies in creating a culture of compliance that becomes part of the organization’s DNA.
Tired of Recurring Compliance Issues?
Master structured problem-solving with our Root Cause Analysis training. Learn to identify and eliminate the root causes of compliance problems. Perfect for teams handling quality and regulatory challenges.
Manufacturing Compliance Checklist: Essential Elements for Success
Here’s a comprehensive manufacturing compliance checklist that has proven invaluable for organizations striving to achieve and maintain regulatory compliance. This systematic approach will ensure comprehensive coverage of critical compliance elements while maintaining operational efficiency.
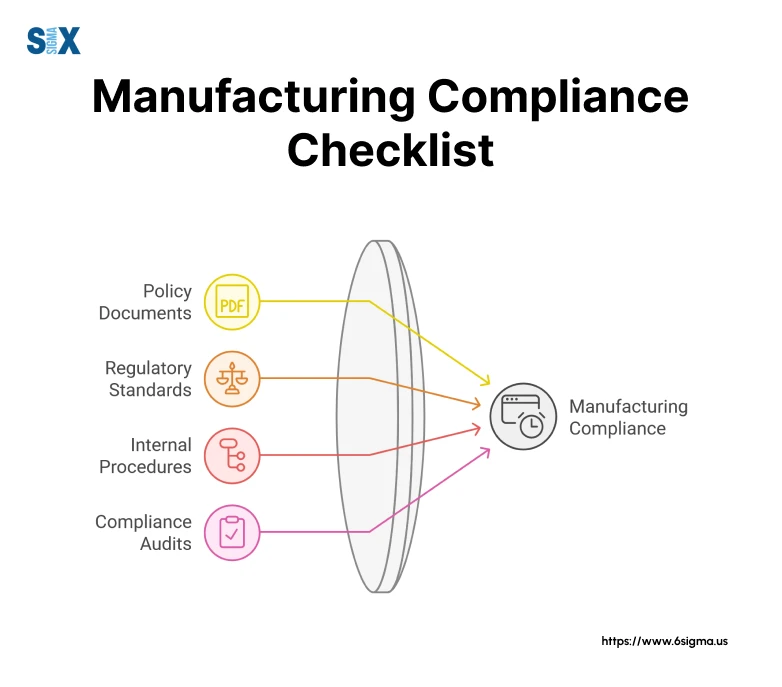
Essential Elements of a Compliance Program
Every successful program must address four fundamental areas.
- Documented policies and procedures that clearly define compliance requirements and responsibilities.
- Robust training programs that ensure all personnel understand their roles in maintaining compliance.
- Monitoring and measurement systems that provide real-time visibility into compliance performance.
- Corrective action protocols that address any deviations promptly and effectively.
Overcoming Manufacturing Compliance Challenges
I’ve encountered numerous manufacturing compliance risks and challenges. Drawing from my experience, here are effective strategies for addressing these obstacles while maintaining operational excellence.
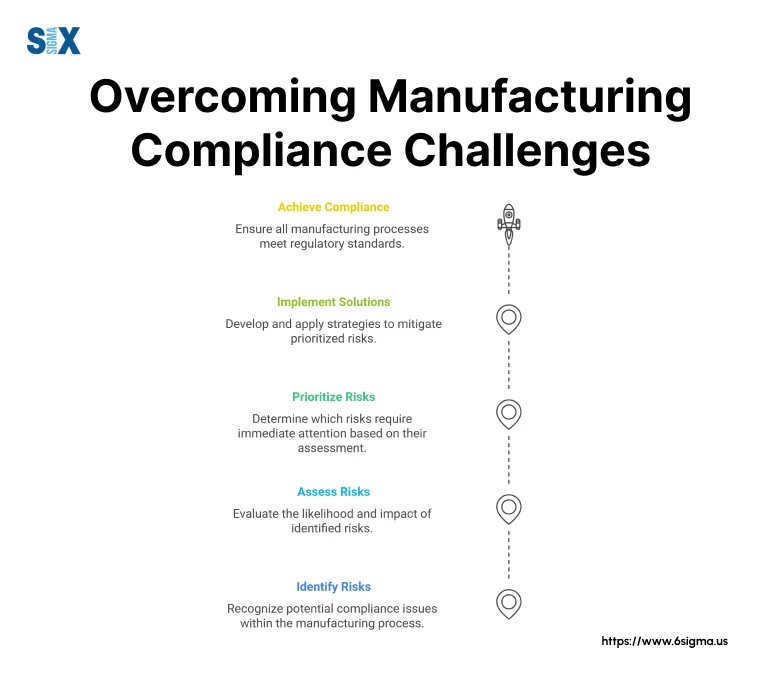
Common Obstacles in Achieving Compliance
One of the most persistent challenges I’ve observed is the resistance to change within established manufacturing processes. You can overcome this by implementing data-driven approaches that demonstrate the value of compliance initiatives.
Another significant obstacle is the complexity of managing multiple compliance requirements simultaneously. Integrated management systems can effectively address this challenge while reducing redundancy.
Resource constraints often present another major hurdle. Use cost-effective compliance strategies that leverage existing resources while maintaining regulatory adherence. Documentation requirements can also become overwhelming without proper systems in place.
Based on my experience implementing quality management systems, establishing streamlined documentation processes is crucial for sustainable compliance.
Strategies for Addressing Manufacturing Compliance Risks
To effectively manage manufacturing compliance risks, I recommend implementing a systematic approach based on Six Sigma principles. Use risk assessment matrices that help prioritize compliance initiatives based on both regulatory requirements and operational impact.
This approach ensures resources are allocated effectively while maintaining comprehensive compliance coverage.
Training and communication represent critical elements in risk mitigation. Regular training sessions combined with clear communication channels significantly reduce compliance-related incidents.
Additionally, establishing metrics-based monitoring systems provides early warning of potential compliance issues, allowing for proactive intervention.
Balancing Compliance with Operational Efficiency
One of the most challenging aspects of manufacturing compliance is maintaining operational efficiency while ensuring regulatory adherence. You can use methodologies that integrate compliance requirements into standard operating procedures, minimizing their impact on productivity.
The key lies in viewing compliance not as a burden but as an opportunity for process improvement.
Ready to Drive Data-driven Compliance Improvements?
Our Green Belt certification covers essential tools to transform your approach to quality management and compliance with comprehensive training in Lean Six Sigma methodologies.
Leverage Technology for Manufacturing Compliance
You can leverage advanced software solutions and data analytics to transform compliance processes from reactive to proactive systems.
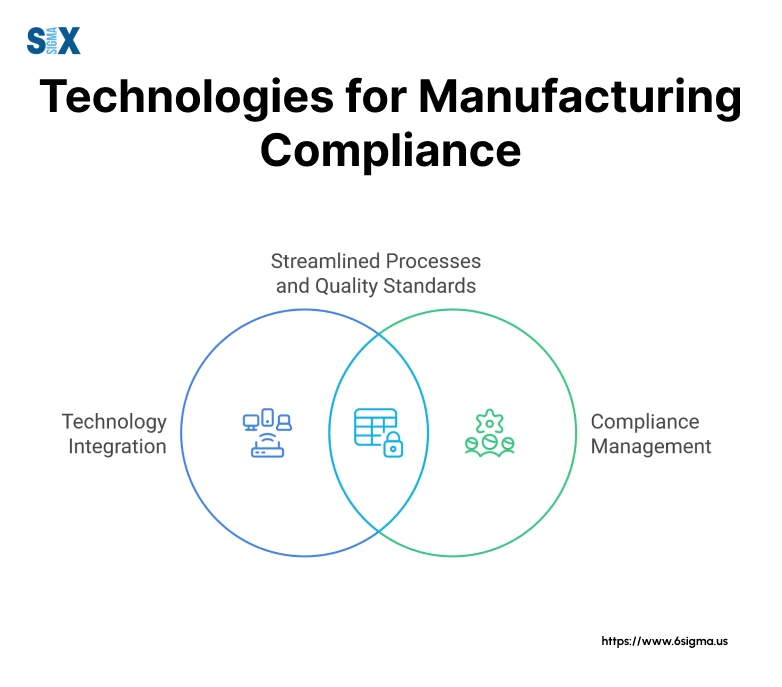
Software Solutions for Compliance Management
Modern software for manufacturing compliance has evolved significantly from simple documentation tools to comprehensive management systems. Implement integrated compliance management platforms that unified quality control, regulatory reporting, and audit management.
These systems provided real-time visibility into compliance status while significantly reducing manual documentation efforts. Based on my experience working with various manufacturers, I recommend selecting solutions that offer modular functionality, allowing organizations to scale their compliance management capabilities as needs evolve.
Data Analytics and Compliance Monitoring
Leverage advanced analytics to identify compliance trends and predict potential issues before they occur. Implement predictive analytics systems that reduce compliance-related incidents. These systems analyze patterns in-process data to identify potential compliance risks, enabling proactive intervention.
Automation in Manufacturing Compliance Processes
Automation has transformed how we approach manufacturing compliance. Implement automated compliance workflows that not only ensure consistent adherence to procedures but also significantly reduce human error. These systems should automatically track and document compliance activities, generating required reports and maintaining audit trails with minimal manual intervention.
Emerging Technologies in Compliance
Implementing IoT sensor networks that provide continuous compliance monitoring of critical parameters. AI algorithms analyze this data in real time, automatically adjusting processes to maintain compliance while optimizing efficiency. These emerging technologies are particularly effective in complex manufacturing environments where traditional monitoring methods may be insufficient.
Remember that technology should enable, not replace, sound compliance practices.
Manufacturing Compliance Case Studies
These case studies demonstrate how different manufacturers have successfully adapted compliance programs to their unique circumstances while achieving operational excellence.
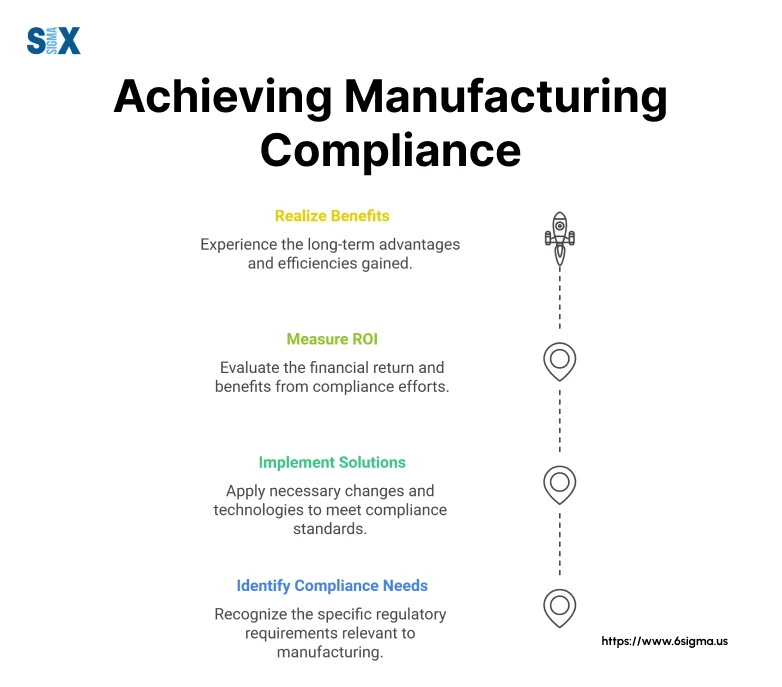
Small Manufacturer Success
During my consulting work with a small precision manufacturing company, we faced the challenge of implementing FDA compliance requirements with limited resources. By applying Six Sigma methodologies, we developed a streamlined approach that focused on critical control points.
The company implemented targeted manufacturing compliance services that prioritized essential requirements while maintaining operational efficiency. Within six months, they achieved full regulatory compliance while reducing quality-related costs by 30%.
Large Corporation Achievement
While working with a major electronics manufacturer operating across twelve countries, we tackled the complex challenge of harmonizing compliance processes globally. We designed an integrated compliance framework that standardized procedures while accommodating local regulatory requirements.
The implementation of centralized manufacturing compliance services resulted in a 45% reduction in compliance-related incidents and significant cost savings through eliminated redundancies.
Mid-Sized Company Innovation: Medical Device Solutions
A mid-sized medical device manufacturer demonstrated how technology could transform compliance management. We implemented a digital compliance platform that automated documentation and monitoring processes.
This strategic use of manufacturing compliance services enabled the company to achieve ISO 13485 certification three months ahead of schedule while reducing compliance-related administrative time by 60%.
Key Lessons Learned
These success stories share common elements:
- Successful compliance implementation requires a systematic approach tailored to organizational size and resources. Starting with core requirements and gradually expanding the program proves most effective.
- Technology adoption should align with organizational capabilities. Successful digital transformation depends on the careful matching of technological solutions with organizational readiness and needs.
- Employee engagement proves crucial for sustainable compliance. Organizations that invest in comprehensive training and clear communication achieve better long-term compliance outcomes.
SixSigma.us offers both Live Virtual classes as well as Online Self-Paced training. Most option includes access to the same great Master Black Belt instructors that teach our World Class in-person sessions. Sign-up today!
Virtual Classroom Training Programs Self-Paced Online Training Programs