Line Balancing in Six Sigma: Maximizing Production Efficiency
Manufacturing excellence demands precise workflow coordination and resource optimization.
Line balancing stands as a crucial technique within Six Sigma methodology, helping organizations achieve optimal production flow while eliminating waste.
This technique transforms uneven production processes into streamlined operations that match customer demand.
Key Highlights
- Line balancing fundamentals and principles
- Six Sigma integration methods
- Implementation steps and tools
- Real-world applications and results
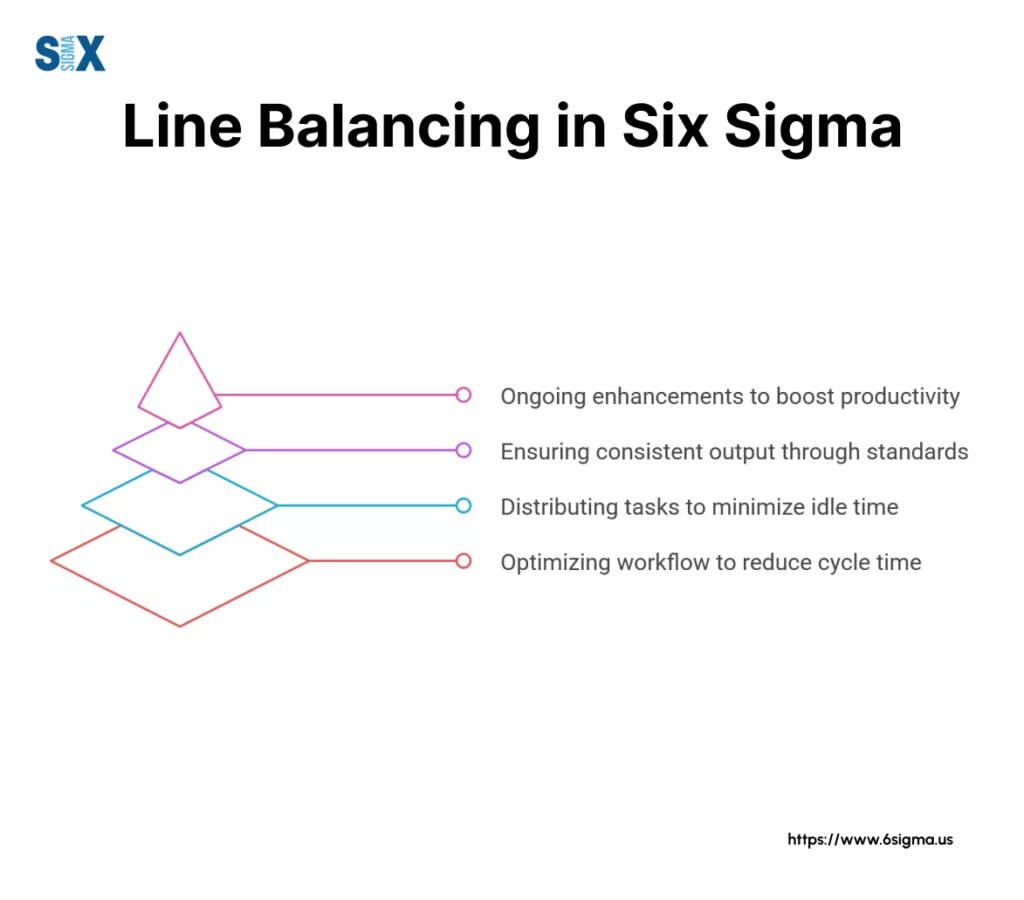
What Is Line Balancing In The Six Sigma Framework?
Line balancing in production represents a methodical approach to distribute work elements across different stations in a manufacturing process.
This technique ensures each station operates within similar time frames, preventing bottlenecks and reducing idle time.
When implemented through Six Sigma principles, line balancing transforms from a simple workload distribution tool into a powerful method for process optimization.
Core Concepts And Definition
The primary goal of line balancing focuses on matching production rates with customer demand.
This alignment requires careful analysis of work elements, cycle times, and resource allocation.
Manufacturing line balancing involves calculating takt time, which sets the pace for production based on customer requirements.
This calculation helps determine the optimal number of workstations and the distribution of tasks.
Integration of Line Balancing With DMAIC Methodology
Six Sigma’s DMAIC framework provides a structured approach to line balancing implementation:
- Define: Identify production targets and current imbalances
- Measure: Calculate cycle times and document current state
- Analyze: Determine root causes of bottlenecks
- Improve: Implement balanced line solutions
- Control: Monitor and maintain the balanced state
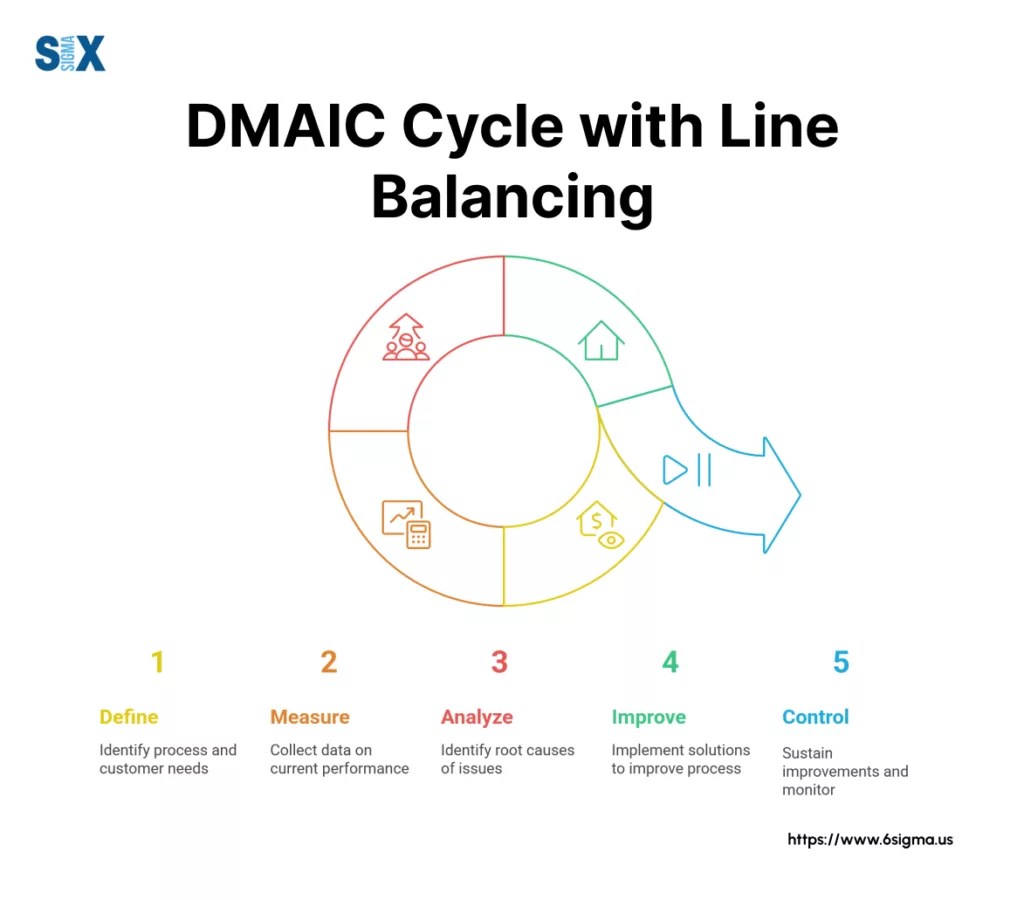
Six Sigma Integration Benefits
Line balancing in Six Sigma delivers measurable improvements across production metrics:
- Production efficiency increases through standardized work distribution
- Worker utilization improves with balanced workloads
- Quality metrics rise due to consistent work patterns
- Lead times decrease through eliminated bottlenecks
Strategic Objectives
Balanced production line implementation aims to achieve several key objectives:
- Minimize station idle time
- Reduce work-in-process inventory
- Optimize resource utilization
- Meet customer demand consistently
- Lower operational costs
The success of line balancing depends on accurate data collection and analysis.
Six Sigma tools like process capability studies and statistical process control help maintain the balanced state while identifying opportunities for further improvement.
Regular monitoring and adjustment ensure the line remains balanced despite changes in product mix or demand.
This dynamic approach allows manufacturing teams to respond quickly to variations while maintaining optimal production flow.
The Six Sigma Approach To Line Balancing
Manufacturing line balancing requires a structured methodology to achieve optimal results.
The DMAIC framework provides a systematic approach to identify, implement, and maintain balanced production lines.
Each phase builds upon the previous one, creating a robust foundation for sustainable improvements.
Define Phase
The define phase establishes clear boundaries and expectations for line balancing projects. Project teams must identify specific process requirements that align with business objectives.
Setting measurable goals helps track progress and validate improvements.
Key metrics typically include cycle time reduction targets, throughput expectations, and quality parameters.
Project charters should outline:
- Current state problems and their impact
- Expected financial and operational benefits
- Project scope and timeline
- Resource requirements and constraints
Measure Phase
Accurate data collection forms the backbone of successful balancing production line initiatives. Teams must gather detailed timing data for each process step and analyze variations in cycle times.
Current state mapping reveals inefficiencies and highlights areas requiring immediate attention.
Time study methods include:
- Direct observation and timing
- Video analysis
- Automated data collection systems
- Work sampling techniques
Analyze Phase
During analysis, teams examine collected data to identify bottlenecks and understand root causes of line imbalances.
Value stream mapping helps visualize waste and non-value-added activities. Statistical analysis reveals patterns and relationships between different process variables.
Key analysis tools include:
- Pareto charts of delay causes
- Process capability studies
- Cause-and-effect diagrams
- Time studies analysis
Improve Phase
The improve phase focuses on implementing line balancing solutions. Teams must optimize resource allocation and distribute workload evenly across stations.
Manufacturing line balancing requires careful consideration of operator skills, equipment capabilities, and material flow.
Implementation strategies include:
- Workstation redesign
- Task redistribution
- Equipment modifications
- Standard work development
Control Phase
Maintaining balanced lines requires robust monitoring mechanisms and quick response to deviations.
Teams must establish control plans that include regular audits and performance checks. Visual management systems help operators maintain standardized work practices.
Control measures include:
- Statistical process control charts
- Daily performance metrics
- Regular line audits
- Operator feedback systems
Success in line balancing depends on consistent application of these phases. Regular reviews and adjustments ensure sustained performance improvements.
Teams should document best practices and lessons learned for future reference.
The DMAIC approach provides a proven framework for implementing line balancing in manufacturing environments.
Each phase builds upon previous work, creating a solid foundation for continuous improvement. Regular monitoring and adjustment ensure sustained benefits from balanced production lines.
Essential Components Of Line Balancing In Six Sigma
Successful assembly line balancing requires mastery of several key components that work together to create efficient production systems
These elements form the foundation of effective line balancing strategies and determine the success of implementation efforts.
Takt Time Calculation
Takt time sets the production pace needed to meet customer demand. The calculation uses the following formula:
Takt Time = Available Working Time / Customer Demand
For example, if a facility operates 480 minutes per day and must produce 240 units, the takt time equals 2 minutes per unit.
This calculation guides all subsequent line balancing decisions and resource allocations.
Cycle Time Optimization
Cycle time represents the actual time required to complete a process. Line balancing example:
A manufacturing line producing automotive parts might have varying cycle times across stations:
- Station 1: 1.8 minutes
- Station 2: 2.3 minutes
- Station 3: 1.5 minutes
The goal involves optimizing these times to match takt time, reducing variations between stations. This optimization often requires task redistribution or process improvements.
Work Element Distribution with Line Balancing
Effective work element distribution ensures balanced workload across all stations.
This process involves:
- Breaking down operations into individual elements
- Measuring time requirements for each element
- Grouping elements into balanced work packages
- Assigning packages to specific stations
Resource Allocation Strategies
Resource allocation in line balancing requires careful consideration of:
Equipment Requirements:
- Machine capacity and capabilities
- Maintenance schedules
- Setup time requirements
Personnel Needs:
- Skill levels required
- Training requirements
- Shift patterns and coverage
Material Flow:
- Storage requirements
- Transportation methods
- Buffer locations
Quality Control Integration of Line Balancing
Quality control measures must be integrated throughout the balanced line.
Key considerations include:
- Inspection points placement
- Error-proofing mechanisms
- Statistical process control implementation
- Feedback loops for continuous improvement
The success of line balancing in Six Sigma depends on proper implementation of these components. Regular monitoring and adjustment ensure sustained performance improvements.
Teams should document best practices and lessons learned for future reference.
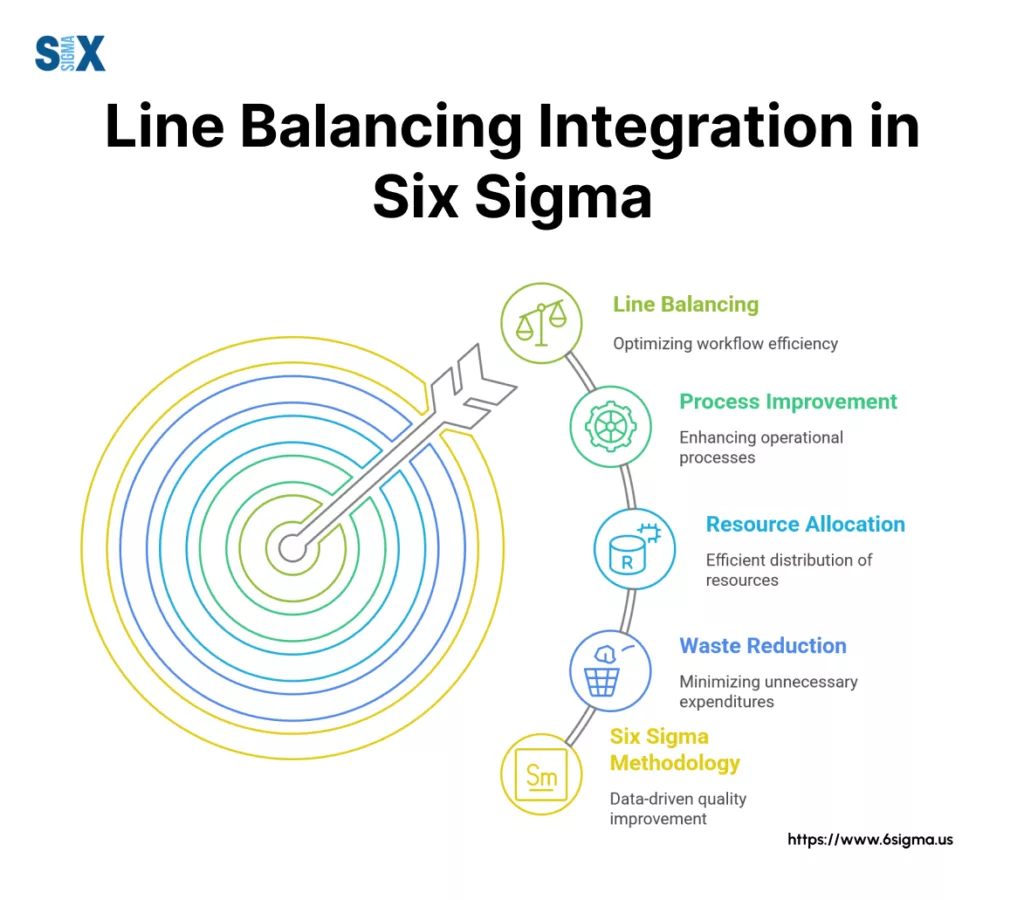
Quality metrics tracking helps maintain balanced operations:
- First-time-through capability
- Defect rates by station
- Rework requirements
- Overall equipment effectiveness
Regular assessment of these components ensures the line remains balanced and efficient. Adjustments should be made based on data-driven decisions and validated through statistical analysis.
Master Line Balancing with Our Green Belt Intensive Training!
Learn from Master Black Belt instructors
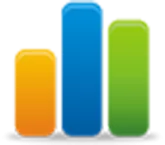
Implementation Framework
Successful production line balance requires careful planning and systematic execution.
This framework provides a structured approach to implementing line balancing initiatives within Six Sigma projects.
Prerequisites For Implementation of Line Balancing
Team formation marks the first critical step in balancing the line.
The implementation team should include:
- Process Engineers: Lead technical aspects
- Operators: Provide hands-on insights
- Quality Specialists: Ensure quality standards
- Project Manager: Coordinate activities
- Six Sigma Expert: Guide methodology
Resource assessment determines project feasibility and requirements. Teams must evaluate:
Financial Resources:
- Budget allocation
- Expected ROI
- Investment requirements
Technical Resources:
- Equipment availability
- Software tools
- Measurement systems
Baseline measurements establish current performance levels.
Key metrics include:
- Current cycle times
- Production rates
- Quality levels
- Resource utilization
- Throughput times
Step-By-Step Implementation Guide
Process Mapping
Creating detailed process maps reveals workflow patterns and dependencies. Teams should document:
- Material flow
- Information flow
- Decision points
- Quality checkpoints
Data Collection Methods
Accurate data collection supports effective production line balance decisions. Required data includes:
- Time studies
- Quality metrics
- Equipment performance
- Resource utilization
- Operator feedback
Analysis Techniques
Statistical analysis reveals improvement opportunities. Common techniques include:
- Capability studies
- Variation analysis
- Root cause investigation
- Bottleneck identification
Implementation Strategies
Executing line balancing changes requires careful coordination:
Phase 1: Pilot Implementation
- Select test area
- Train operators
- Monitor results
- Gather feedback
Phase 2: Full Implementation
- Roll out changes
- Monitor performance
- Address issues
- Document results
Monitoring and Control
Sustained success requires ongoing monitoring:
Daily Monitoring:
- Production metrics
- Quality data
- Resource utilization
Weekly Reviews:
- Performance trends
- Issue resolution
- Improvement opportunities
Monthly Assessments:
- Strategic alignment
- Resource allocation
- Long-term sustainability
The implementation framework ensures systematic execution of line balancing initiatives. Regular review points allow teams to adjust strategies based on actual results.
Documentation of lessons learned supports continuous improvement efforts.
Create Meaningful Charts and Graphs for Data Analysis and Line Balancing with Minitab Essential Training
Advanced Applications And Modern Trends
Modern manufacturing environments demand sophisticated line balancing solutions that leverage digital technologies.
These advancements transform traditional line balancing approaches into data-driven, automated systems that deliver superior results.
Industry 4.0 Integration
Smart manufacturing principles revolutionize line balancing through connected systems and real-time data analysis.
Digital sensors monitor production flow, automatically adjusting work distribution based on current conditions.
These systems enable:
- Automated workload distribution
- Predictive maintenance scheduling
- Dynamic resource allocation
- Real-time performance optimization
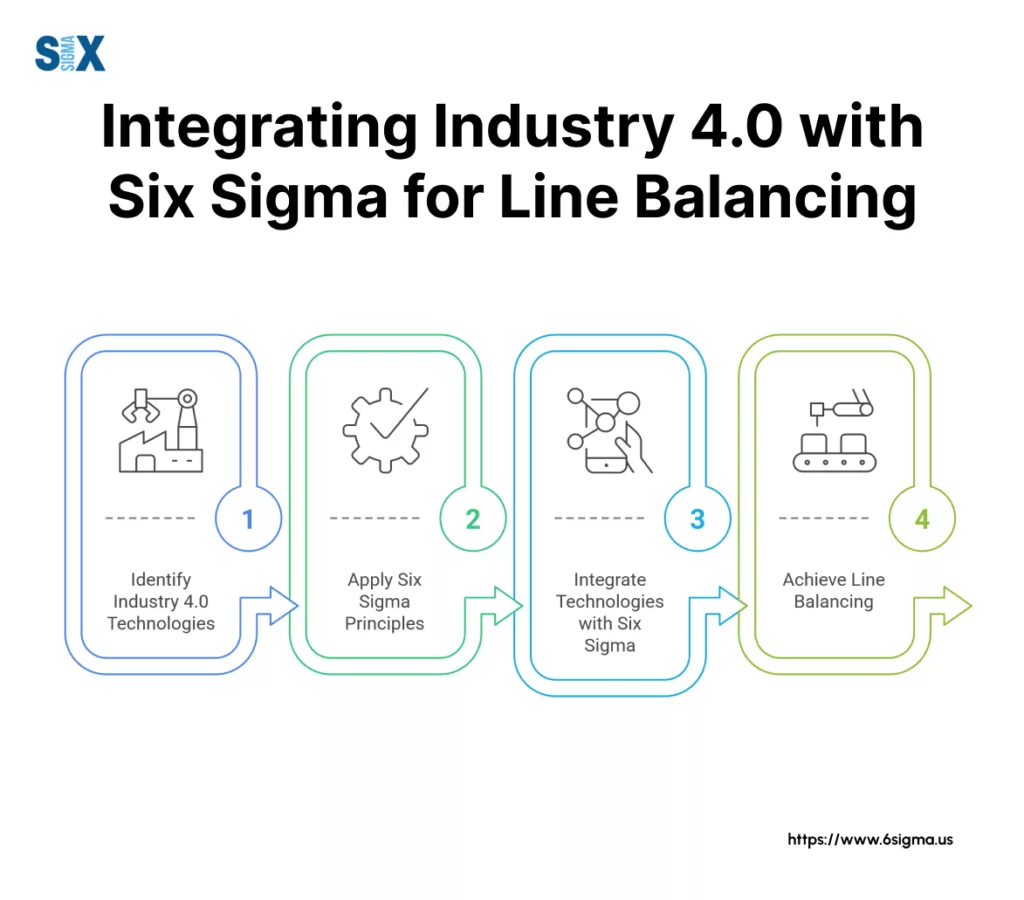
Digital Transformation In Line Balancing
Digital tools enhance traditional line balancing methods through improved accuracy and response times. Modern software solutions provide:
Production Simulation:
- Virtual line testing
- Scenario modeling
- Impact analysis
- Risk assessment
Digital Twin Technology:
The creation of virtual production lines allows teams to test changes without disrupting actual operations. These models provide valuable insights for optimization efforts.
AI And Machine Learning Applications
Artificial intelligence transforms line balancing through pattern recognition and predictive analytics.
Machine learning algorithms analyze historical data to:
- Predict bottlenecks before they occur
- Optimize work distribution patterns
- Identify improvement opportunities
- Suggest resource allocation adjustments
Real-Time Monitoring Systems and Line Balancing
Advanced monitoring solutions provide immediate feedback on line performance. Digital dashboards display:
Performance Metrics:
- Current cycle times
- Station utilization rates
- Quality indicators
- Production targets
Alert Systems:
- Deviation notifications
- Maintenance requirements
- Resource shortages
- Quality issues
IoT Integration Benefits of Line Balancing
Internet of Things technology enables seamless communication between machines, operators, and management systems.
Connected devices provide:
Data Collection:
- Automated timing data
- Quality measurements
- Equipment status
- Material flow tracking
Process Control:
- Automated adjustments
- Remote monitoring
- Predictive maintenance
- Resource optimization
These technological advances create smarter, more responsive production lines. Real-time data analysis enables quick adjustments to maintain optimal balance.
Integration of these technologies with Six Sigma methodologies strengthens process control and improvement efforts.
Implementation Considerations:
- Infrastructure requirements
- Data security measures
- Training needs
- Integration planning
- ROI assessment
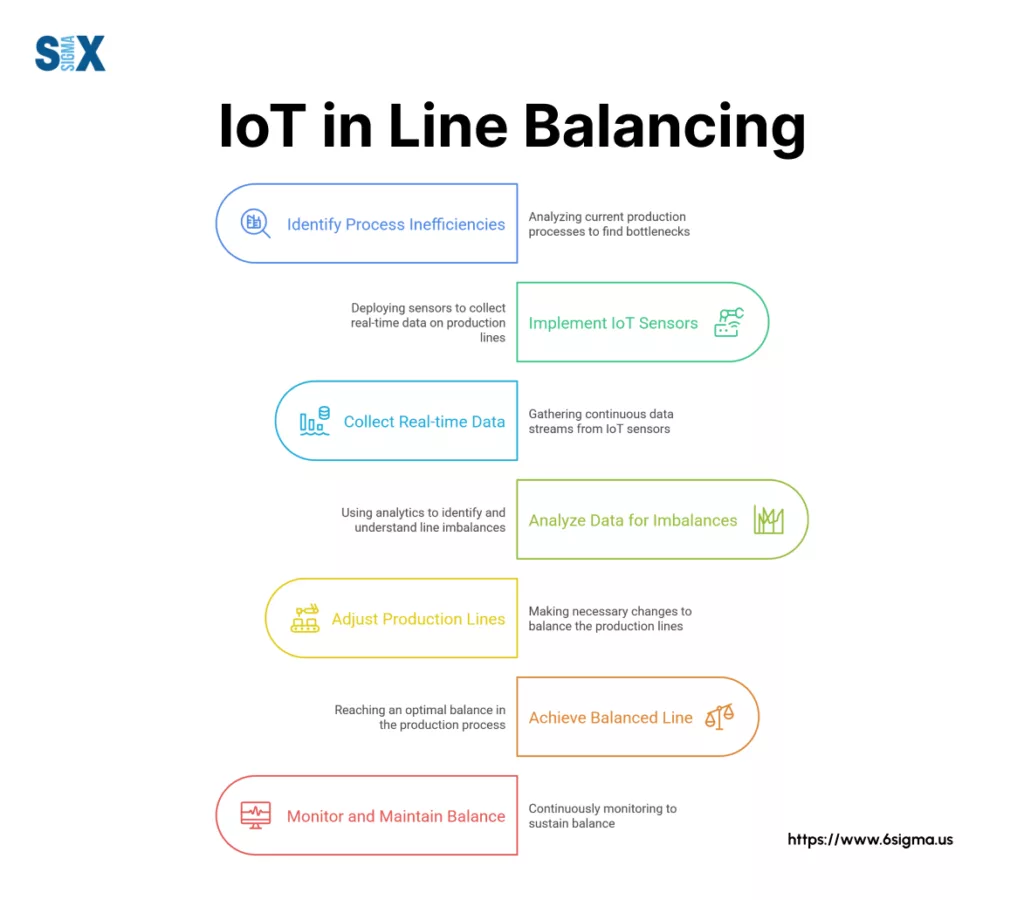
The future of line balancing lies in these advanced applications. Organizations must carefully evaluate and implement these technologies to maintain competitive advantage.
Regular assessment of new technologies ensures continued optimization of line balancing efforts.
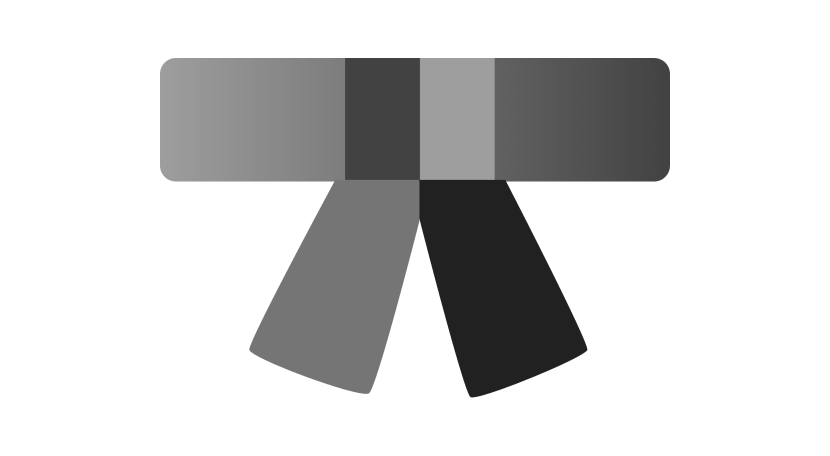
Become a Line Balancing Expert with Black Belt Certification
Dive deep into advanced analytics and process optimization
Common Challenges And Solutions
Organizations implementing line balancing in Six Sigma projects frequently encounter specific obstacles.
Understanding these challenges and their solutions helps teams prepare effective mitigation strategies.
Implementation Obstacles
Resistance to Change:
Teams often face push-back from operators accustomed to existing processes. Solution: Implement change management protocols and involve operators in planning phases.
Resource Constraints:
Limited budgets and personnel can hamper implementation efforts. Solution: Develop phased implementation plans prioritizing high-impact areas first.
Data Accuracy Issues:
Unreliable or incomplete data leads to poor decision-making. Solution: Establish robust data collection systems and validation procedures.
Troubleshooting Guide for Line Balancing
Uneven Work Distribution:
- Task allocation methods
- Operator skill levels
- Equipment capabilities
- Material flow patterns
Quality Issues:
- Review inspection points
- Assess operator training
- Evaluate process controls
- Check equipment settings
Best Practices For Success
Documentation Requirements:
- Process changes
- Performance metrics
- Training programs
- Quality data
Communication Protocols:
- Daily updates
- Issue reporting
- Performance feedback
- Improvement suggestions
Risk Mitigation Strategies with Line Balancing
Preventive Measures:
Create contingency plans for:
- Equipment failures
- Personnel absences
- Material shortages
- Quality issues
Monitoring Systems:
Implement checks for:
- Process deviation
- Resource utilization
- Quality metrics
- Timeline adherence
Moving Forward With Line Balancing In Six Sigma
Line balancing in Six Sigma represents a crucial tool for manufacturing excellence. The integration of traditional methods with modern technologies creates powerful opportunities for process improvement.
Organizations must carefully balance technical requirements with practical implementation considerations.
Success requires:
- Systematic implementation approaches
- Regular monitoring and adjustment
- Strong team engagement
- Continuous improvement focus
The future of line balancing lies in digital integration and real-time optimization. Organizations that master these techniques position themselves for sustained competitive advantage.
Teams should focus on building strong foundations while remaining flexible to adopt new technologies and methods.
SixSigma.us offers both Live Virtual classes as well as Online Self-Paced training. Most option includes access to the same great Master Black Belt instructors that teach our World Class in-person sessions. Sign-up today!
Virtual Classroom Training Programs Self-Paced Online Training Programs