A Complete Guide to Gemba Walk. All You Need to Know
As priorities evolve to sustainability and shared prosperity, forward-thinking enterprises appropriately focus on judicious refinement and progress empowering all.
One impactful philosophy gaining adoption involves Gemba walks – where leaders immerse experientially within core functions to uncover strengths, strengthen understanding, and jointly resolve opportunities alongside dedicated teams.
Emerging from Toyota’s heritage-uplifting partnerships, Gemba emphasizes eliminating non-value, respecting roles, and perpetual upliftment. Through participatory walks, leaders gain invaluable insights alongside those navigating realities daily.
This hands-on care fosters deeper listening, as challenges surface to be addressed cooperatively. Solutions emerge organically as strengths flourish where optional restraints dissolve.
Communal walks nurture cultures embracing reflective progress, ownership, and lively problem-solving – guiding optimizations and enhancing the experiences of customers and coworkers alike. All prosper where daily duties are illuminated and partnerships motivate continuous learning.
For any dedicated to the sustainable excellence Gemba exemplifies, these walks prove a pathway towards capable, energized teams and outcomes uplifting communities served through understanding and care for one another.
Key Highlights
- Gemba walks represent a proven learning practice where leaders immerse within core functions to observe and problem-solve cooperatively alongside dedicated teams.
- This firsthand partnership at the actual workplace allows unpacking realities together, as challenges surface to be addressed through equitable understanding.
- Regular walks nurture cultures of continual enhancement, and progress experienced meaningfully by all.
- Benefits incorporate optimized processes, heightened quality and safety, strengthened relationships, and rhythmic adjustments for improved experiences.
- Productive walks necessitate diligent planning, active listening on-site amid respectful exchanges, collaborative solutions, and accountable follow-through together.
- Helpful tools like mapping, checklists, and learning technologies further enrich data analysis, yet progress stems from community, not compliance alone. Potentials synergize as open-minded problem-solving elevates all involved.
- For any committed to the sustainable excellence Gemba cultivates through equitable partnership, these walks prove a proven means of nourishing capable, energized teams where prosperity spreads well beyond enterprise walls through care, honesty, and perpetual advancement joined hand in hand.
What is Gemba Walk?
The term “Gemba” refers to where valuable work actualizes – the experiential domain where potentials emerge. In lean methodologies emphasizing sustained enhancement, Gemba walks represent an impactful learning practice.
These walks cultivate partnerships at core functions to observe and problem-solve equitably alongside dedicated teams. This respectful immersion within daily realities allows unpacking strengths and opportunities together for judicious progress.
Participants actively listen through supportive exchanges, identifying how to cooperatively dissolve obstacles and refine efforts to uplift the experiences of customers and colleagues alike. Progress stems not from targets alone but through the community.
Benefits incorporate optimized processes, safeguarded contributions, and enriched relationships where roles feel valued. Leaders demonstrate commitment to excellence by fostering an environment where all meaningfully contribute through equitable understanding and care.
Challenges surface not as deficiencies, but as tailwinds aiding course corrections. Successes too are recognized to motivate perpetual advancement and ownership across all levels.
Through Gemba walks, capabilities synergize as potentials materialize where optional restraints dissolve and problems resolve collaboratively. All prosper where duties and relationships uplift one another.
Benefits of Conducting Gemba Walks
Conducting regular Gemba walks offers numerous advantages for improving operational efficiency and driving continuous improvement within an organization.
One of the primary benefits is gaining firsthand insights into the actual work processes and conditions on the shop floor or Gemba.
By going to the source and observing operations directly, leaders can identify potential issues, inefficiencies, or opportunities for improvement that may not be apparent from data alone.
Gemba walks foster open communication and employee engagement. When leaders are present on the gemba, it provides an opportunity for front-line workers to voice their concerns, offer suggestions, and feel valued for their contributions.
This direct interaction helps break down organizational silos and cultivates a culture of collaboration and problem-solving.
Another significant benefit of Gemba walks is waste reduction. By observing processes firsthand, leaders can quickly identify sources of waste, whether it’s excess inventory, unnecessary motion, or defects.
Eliminating these wastes can lead to significant cost savings and productivity gains, ultimately improving the organization’s bottom line.
Gemba walks also facilitate the standardization of best practices. When leaders observe exemplary processes or innovative solutions on the gemba, they can share and replicate them across the organization, promoting consistency and operational excellence.
Moreover, Gemba walks reinforce the principles of lean manufacturing and continuous improvement.
By regularly going to the gemba, leaders demonstrate their commitment to these philosophies and lead by example, inspiring employees to embrace a mindset of constant learning and improvement.
Conducting gemba walks also allows leaders to assess the effectiveness of standard operating procedures (SOPs) and identify areas where additional training or visual management tools may be required.
Preparing for a Gemba Walk
Proper preparation is key to conducting an effective gemba walk. Before heading out to the gemba (the “real place” where work happens), there are several important steps to take:
Define the Objectives
What specific processes, areas, or issues do you want to observe during the Gemba walk? Having clear objectives will help you stay focused and make the best use of your time.
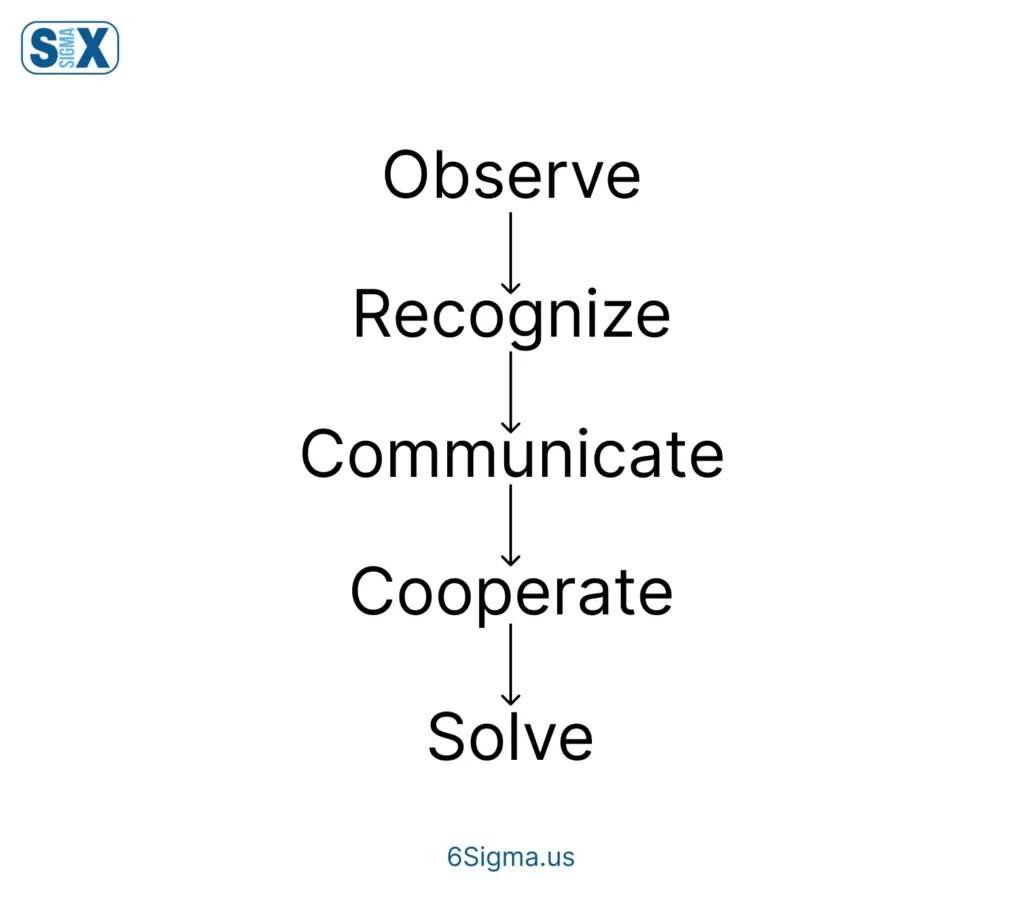
Common goals include identifying opportunities for continuous improvement, observing standard operating procedures in action, or investigating the root causes of a particular problem.
Gather Relevant Data and Information
Review process documentation, metrics, value stream maps, and any other data that can provide context about the area you’ll be observing.
This background information will enable you to better understand what you see during the walk.
Determine the Gemba Walk Route
Based on your objectives, map out which areas, processes, and workstations you plan to observe. Try to follow the flow of the value stream from start to finish if possible.
Prepare Questions and Checklist
Develop a list of open-ended questions to ask operators, supervisors, and other personnel you encounter.
Having a Gemba walk checklist of things to look for during observations can also be helpful, such as looking for examples of the 8 wastes of lean manufacturing.
Inform Those Involved for Gemba Walk
Let managers, supervisors, and employees in the areas you’ll be walking know the purpose, timing, and who will be part of the Gemba walk.
This promotes transparency and ensures they aren’t caught off guard.
Assemble the Right Team for Gemba Walk
Determine who should participate based on the objectives. This could include process owners, subject matter experts, lean champions, and frontline employees familiar with the processes being observed.
Conducting an Effective Gemba Walk
The true value of a gemba walk lies in how it is executed. Simply walking around the facility is not enough – there needs to be a structured approach to observing processes, engaging employees, and identifying opportunities for improvement.
Key steps to conduct an effective gemba walk:
Go to the Actual Process Area
The Gemba is where work happens, so you need to go to the manufacturing floor, service area, office space, or wherever the core processes occur.
Avoid conference rooms or removed areas where you can’t fully witness the process in action.
Observe Current Conditions Closely
With an open perspective, watch how the work unfolds. Look for deviations from standard operating procedures, wasted motion, inefficient layouts, quality issues, and other opportunities.
Take notes and ask questions to understand the root causes behind what you see.
Engage with Employees for Gemba Walk
Don’t just observe silently. Talk to the employees doing the job and get their perspectives. They are the experts on that process and can provide invaluable insights.
Ask open-ended questions about challenges they face and potential improvements.
Avoid Judgement or Criticism
A Gemba walk should be a collaborative learning experience, not an opportunity to criticize or assign blame.
Approach it with humility, empathy, and a desire to understand before seeking to improve.
Collect Data for Gemba Walk
Along with qualitative observations, gather quantitative data like cycle times, defect rates, inventory levels, etc.
Empirical evidence strengthens the case for making changes.
Identify Kaizen Opportunities for Gemba Walk
As you go, make note of quick kaizen (continuous improvement) opportunities that can be implemented immediately, as well as larger projects for further analysis.
Categorize them based on complexity, cost, and impact.
Follow-Up and Follow-Through
A Gemba walk is just the start – you must diligently follow up on the areas identified for improvement.
Develop action plans, allocate resources, and ensure the organization learns from the experience.
Analyzing and Acting on Gemba Walk Findings
The Gemba walk is just the first step in the continuous improvement process. After observing the manufacturing processes and gathering data, it’s crucial to analyze the findings and develop an action plan to address any issues or opportunities identified.
Data Analysis
During the gemba walk, you likely collected various types of data, such as:
- Process cycle times
- Defect rates
- Inventory levels
- Downtime occurrences
- Employee feedback
Thoroughly analyze this data to identify patterns, trends, and root causes of problems. Use tools like value stream mapping, cause-and-effect diagrams, and statistical process control to gain insights from the data.
Root Cause Analysis
One of the key objectives of a Gemba walk is to uncover the root causes of problems or inefficiencies in the manufacturing processes.
Apply root cause analysis techniques like the 5 Whys or fishbone diagrams to dig deeper and identify the underlying factors contributing to the issues observed.
Develop Action Plans for Gemba Walk
Based on your analysis, develop specific action plans to address the identified problems and implement improvements.
These plans should outline the steps to be taken, assign responsibilities, and set timelines for completion.
Involve Team Members
Engage the team members who work in the areas observed during the Gemba walk. They have first-hand knowledge and can provide valuable insights into the problems and potential solutions.
Encourage their participation in developing and implementing the action plans.
Prioritize and Implement Solutions
Prioritize the action items based on their impact, urgency, and available resources. Start with the low-hanging fruit ā solutions that can be implemented quickly and yield immediate results.
This will build momentum and demonstrate the value of the Gemba walk process.
Continuous Monitoring with Gemba Walk
Implementing solutions is not the end of the process. Continuously monitor the performance of the improved processes to ensure that the desired results are achieved and sustained.
Regularly review the key metrics and make adjustments as needed.
Standardize Improvements with Gemba Walk
If the implemented solutions prove successful, standardize them by updating standard operating procedures (SOPs), visual controls, and training materials.
This will help sustain the improvements and prevent regression to old ways of working.
Foster a Culture of Continuous Improvement
Use the Gemba walk as a catalyst for fostering a culture of continuous improvement within the organization.
Celebrate successes, share learnings, and encourage employees to actively participate in identifying and solving problems through regular Gemba walks and kaizen events.
By effectively analyzing the findings from Gemba walks and taking appropriate actions, organizations can drive significant improvements in their manufacturing processes, reduce waste, increase efficiency, and enhance overall operational performance.
Gemba Walk Tools and Technologies
To conduct an effective Gemba walk and capture valuable insights, several tools and technologies can be leveraged.
These tools aid in data collection, documentation, and analysis, ultimately enhancing the overall process improvement efforts.
Gemba Walk Checklists and Templates
Checklists and templates are essential tools for a structured Gemba walk. They help ensure that all critical areas are covered and that observations are consistently recorded.
These templates often include sections for noting process steps, identifying potential wastes or inefficiencies, recording metrics, and documenting action items.
Customizable templates allow organizations to tailor the checklists to their specific needs and processes.
Visual Management Boards for Gemba Walk
Visual management boards, such as whiteboards or digital displays, are powerful tools for Gemba walks.
They visually represent the process flow, key performance indicators (KPIs), and improvement opportunities.
During the Gemba walk, these boards can capture observations, document issues, and communicate action plans with the team members on the shop floor.
Digital Cameras and Video Recorders
Capturing visual evidence during a Gemba walk is invaluable for later analysis and communication.
Digital cameras and video recorders allow teams to document processes, identify potential areas for improvement, and share findings with stakeholders who may not have been present during the walk.
Data Collection Apps and Software
Specialized Gemba walk apps and software solutions have emerged to streamline the data collection and analysis process.
These tools often integrate with existing systems, such as enterprise resource planning (ERP) or manufacturing execution systems (MES), enabling real-time data capture and analysis.
They can also facilitate collaboration, task assignment, and progress tracking for identified improvement opportunities.
Virtual Gemba Walk Technologies
In today’s digital age, virtual Gemba walk technologies have gained traction, particularly when physical presence on the shop floor is challenging or restricted.
These technologies leverage video conferencing, augmented reality (AR), or virtual reality (VR) to provide a remote, immersive experience of the Gemba.
Virtual Gemba walks can be especially beneficial for organizations with multiple sites or when travel is limited.
Root Cause Analysis Tools and Gemba Walk
During a Gemba walk, identifying the root causes of issues is crucial for implementing effective solutions.
Root cause analysis tools, such as fishbone diagrams, 5 Whys, and cause-and-effect diagrams, can systematically analyze and understand the underlying reasons behind observed problems or inefficiencies.
Best Practices and Challenges for Gemba Walk
- Make gemba walks a regular habit, not just a one-time event. Consistency is key to driving continuous improvement.
- Involve employees and get their perspective. The Gemba walk is a collaborative process.
- Avoid being judgmental or critical. Approach with an open mind to learn.
- Ask open-ended questions to encourage deeper discussion.
- Follow up on action items identified during the walk. Closing the loop is crucial.
- Share learnings from the Gemba walk across the organization. Spread knowledge.
- Use a Gemba walk checklist or template to stay structured and focused.
- Implement visual management tools like kanban boards based on observations.
Common Challenges of Gemba Walks
- Getting bogged down in day-to-day activities and not making time for Gemba walks.
- Employees feel intimidated or anxious about being observed.
- Identifying the real root causes behind process issues.
- Lack of follow-through on action items and recommendations.
- Difficulty convincing leadership of the value of gemba walks.
- Engaging employees who are resistant to change.
- Translating observations into meaningful process improvements.
- Scaling Gemba walks across a large, distributed organization.
Parting Notes
By understanding and applying best practices while being aware of potential challenges, organizations can maximize the value and impact of their Gemba walk initiatives.
Consistent practice, employee involvement, and a culture of continuous improvement are vital for successful Gemba walks.
SixSigma.us offers both Live Virtual classes as well as Online Self-Paced training. Most option includes access to the same great Master Black Belt instructors that teach our World Class in-person sessions. Sign-up today!
Virtual Classroom Training Programs Self-Paced Online Training Programs