Gemba Board: Driving Operational Excellence with Visual Management Tools
Effective communication and coordination are essential for any business seeking to optimize its processes and maximize efficiency.
One time-tested visual management tool is the Gemba board – a core component of the renowned Toyota Production System.
Originating from the Japanese automaker’s inventory management techniques, Gemba boards have evolved into a versatile communication platform that drives operational excellence across diverse industries.
The name “Gemba” derives from a Japanese business term meaning the actual place where value is created through processes and workflow.
Simply put, Gemba boards provide a real-time overview of key metrics and performance indicators visible to all stakeholders.
They promote transparency while facilitating continuous improvement efforts. In this article, we will explore the concepts and effective implementation of Gemba boards.
Understand these concepts with six sigma certification, as Gemba boards are a key tool in the six sigma methodology.”
We will also learn how leading organizations worldwide are leveraging this lean tool to streamline operations and unlock significant savings.
The same visual management principles apply to manufacturing automotive parts or handling flight check-ins.
Key Highlights
- Definition and purpose of Gemba Boards as powerful visual management tools
- Benefits: Real-time visibility, enhanced communication, continuous improvement
- Core components: KPIs, visual controls, status updates, action items
- Steps for setting up an effective Gemba Board tailored to your workplace
- Leveraging Gemba Boards for continuous improvement through Gemba Walks, team engagement, and data-driven decision-making
- Automating and integrating Gemba Boards with digital tools and systems
- Real-world examples and case studies across manufacturing, quality control, and employee safety
- Insights from an experienced Master Black Belt on optimizing Gemba Board implementation
What is a Gemba Board and Why is it Important?
A Gemba Board is a visual management tool that consolidates real-time information, performance metrics, and action items related to a specific process or work area.
It serves as a centralized hub for communication, problem-solving, and continuous improvement efforts. To fully appreciate the value of Gemba boards, it’s helpful to understand lean fundamentals, which form the foundation of this visual management approach.
The term “Gemba” originates from the Japanese concept of “the actual place” – emphasizing the importance of observing and understanding processes in their real-world context.
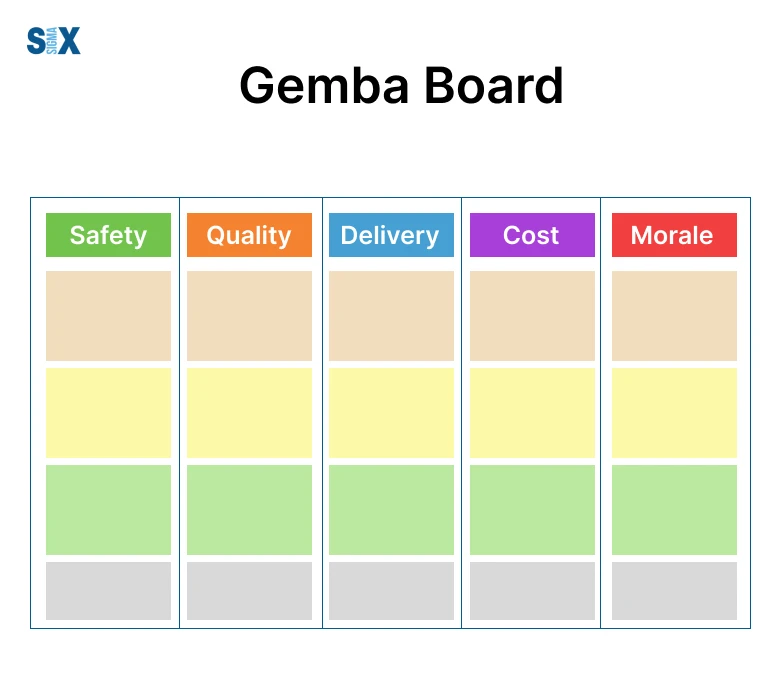
Visual management tools like Gemba Boards are essential for fostering a culture of transparency, accountability, and data-driven decision-making within an organization.
Some key benefits of implementing Gemba Boards include:
- Real-time visibility: By displaying up-to-date information on performance indicators, bottlenecks, and areas for improvement, Gemba Boards provide teams with a clear, at-a-glance understanding of the current state of operations.
- Enhanced communication: These boards facilitate open and effective communication among team members, fostering collaboration and ensuring that everyone is aligned with organizational goals and objectives.
- Continuous improvement: Gemba Boards are powerful catalysts for driving continuous improvement initiatives. They enable teams to identify opportunities for optimization, implement corrective actions, and track progress over time.
Core Components of an Effective Gemba Board
To maximize the effectiveness of a Gemba Board, it’s essential to include various core components that provide a comprehensive view of the process or work area being monitored.
These components not only ensure transparency but also facilitate data-driven decision-making and targeted improvement efforts.
Key Performance Indicators (KPIs)
One of the most crucial elements of a Gemba Board is the display of Key Performance Indicators (KPIs).
These metrics serve as benchmarks for evaluating the performance and efficiency of the process or work area. KPIs can include:
- Metrics: Quantifiable measures such as cycle times, defect rates, throughput, or lead times, provide a clear picture of the current state of operations.
- Targets: Clearly defined goals or benchmarks that teams strive to achieve, helping to align efforts and track progress towards desired outcomes.
- Productivity trends: Visual representations of performance trends over time, allowing teams to identify patterns, detect anomalies, and make data-driven decisions.
Visual Controls within a Gemba Board
Effective Gemba Boards leverage the power of visual controls to convey information in a clear and easily understandable manner.
These controls can include:
- Color coding: The use of color-coded labels, indicators, or charts to quickly communicate the status of tasks, processes, or performance levels.
- Symbols: Standardized symbols or icons that represent specific actions, conditions, or alert levels, facilitating quick comprehension.
- Workflow visualization: Visual representations of the workflow or process flow, highlighting potential bottlenecks, handoffs, or areas for optimization.
Status Updates
Real-time visibility is a crucial aspect of Gemba Boards, which is achieved by including status updates.
These updates can take various forms, such as:
- Real-time updates: Dynamic displays that reflect the latest information, ensuring that teams are working with accurate and up-to-date data.
- Andon signals: Visual or audible signals that alert teams to issues or deviations from standard procedures, enabling prompt action and resolution.
Action Items
In addition to displaying performance metrics and status updates, Gemba Boards should also incorporate action items to drive continuous improvement efforts.
These can include:
- Task assignments: Clear allocation of responsibilities and deadlines for specific tasks or corrective actions.
- Corrective actions: Documented steps or countermeasures being implemented to address identified issues or areas for improvement.
- Problem areas: Highlighted sections or displays that bring attention to specific processes or work areas requiring focused attention or intervention.
Setting Up a Gemba Board for Your Workplace
Implementing an effective Gemba Board in your workplace requires careful planning and consideration of your organization’s unique needs and objectives.
By following a structured approach, you can ensure that your Gemba Board becomes a powerful tool for driving operational excellence and continuous improvement.
Determining Objectives
The first step in setting up a Gemba Board is to clearly define your objectives. This involves:
- Defining goals: Establish the specific goals or outcomes you aim to achieve through the implementation of the Gemba Board. These goals should align with your organization’s overarching strategic objectives.
- Identifying processes to improve: Pinpoint the critical processes or work areas that will benefit most from the visibility and monitoring provided by the Gemba Board.
Designing the Layout for the Gemba Board
Once your objectives are defined, you can proceed with designing the layout of your Gemba Board. This involves:
- Central location: Choose a highly visible and easily accessible location for your Gemba Board, ensuring that it’s a central point of reference for all team members.
- Simple format: Adopt a clean and organized layout that is easy to understand and interpret at a glance.
- Tools: Determine the tools you’ll use to create and maintain your Gemba Board, such as whiteboards, software solutions, or a combination of both.
Selecting Visuals
The effectiveness of your Gemba Board heavily relies on the visuals you incorporate. When selecting visuals, consider:
- Charts: Incorporate charts or graphs that effectively convey performance trends, progress toward targets, or other relevant data visualizations.
- Symbols: Utilize standardized symbols or icons that are easily recognizable and understood by all team members.
- Layout for clarity: Arrange the visuals in a logical and intuitive manner, ensuring that the information is presented in a clear and organized way.
Establishing Processes
To ensure the successful implementation and ongoing maintenance of your Gemba Board, it’s crucial to establish clear processes. This includes:
- Update routines: Define the frequency and responsibilities for updating the information on the Gemba Board, ensuring that it remains current and relevant.
- Team responsibilities: Assign specific roles and responsibilities to team members for managing, updating, and monitoring the Gemba Board.
Using the Gemba Board for Continuous Improvement
While setting up an effective Gemba Board is essential, the true value of this visual management tool lies in its ability to drive continuous improvement efforts within your organization.
By leveraging the Gemba Board as a central hub for problem-solving, team engagement, and data-driven decision-making, you can unlock a culture of operational excellence.
Gemba Walks
One of the most powerful applications of the Gemba Board is its integration with Gemba Walks – a practice rooted in the Lean methodology.
During Gemba Walks, teams:
- Observe processes: Physically observe the work area or process being monitored, gaining firsthand insights into potential issues or areas for improvement.
- Root cause analysis: Employ techniques like the “5 Whys” to dig deeper and uncover the root causes of identified problems or inefficiencies.
- 5 Whys: A structured problem-solving approach that involves asking “why” multiple times to identify the root cause of an issue.
- Root cause analysis: Employ techniques like the ‘5 Whys’ to dig deeper and uncover the root causes of identified problems or inefficiencies. These techniques are covered in root cause analysis training, which equips teams to address issues systematically.
Team Engagement with Gemba Board
Effective continuous improvement efforts rely heavily on team engagement and collaboration.
Gemba Boards facilitate this by:
- Open communication: Providing a central platform for team members to openly discuss challenges, share insights, and propose solutions.
- Employee feedback: Encouraging frontline employees to contribute their perspectives and ideas, fostering a sense of ownership and accountability.
- Accountability: Clearly assigning responsibilities and tracking progress, ensuring that everyone is committed to driving improvement initiatives.
Team members with six sigma green belt certification can play a key role in facilitating these efforts, leveraging their training to drive improvement initiatives.”
Data-Driven Decisions
One of the key strengths of Gemba Boards is their ability to facilitate data-driven decision-making. By leveraging the information displayed on the board, teams can:
- Analyze metrics: Closely monitor and analyze performance metrics, identifying trends, patterns, or deviations from desired outcomes.
- Identify bottlenecks: Pinpoint bottlenecks or constraints within processes, enabling targeted interventions and optimization efforts.
Kaizen Events
In addition to ongoing improvement efforts, Gemba Boards can also support focused Kaizen Events – intensive improvement projects that bring together cross-functional teams.
During these events, teams:
- Focused improvement projects: Concentrate on specific processes or areas identified for improvement, leveraging the Gemba Board as a central reference point.
- Cross-functional collaboration: Foster collaboration among diverse teams, benefiting from diverse perspectives and expertise.
Kaizen events are typically facilitated by individuals with six sigma black belt certification, who bring expertise in guiding cross-functional teams through intensive improvement efforts.
Automating and Integrating Gemba Board
As technology continues to evolve, organizations can leverage digital solutions to enhance the effectiveness and efficiency of their Gemba Boards.
By automating and integrating Gemba Boards with existing systems, teams can unlock new levels of real-time visibility, streamlined workflows, and data-driven insights.
Digital Gemba Board
The advent of specialized software solutions has opened up new possibilities for Gemba Board implementation.
Some key advantages of digital Gemba Boards include:
- Software options: A range of software platforms designed specifically for visual management and Gemba Board implementation, offering customizable dashboards and features.
- Real-time syncing: Seamless integration with data sources, ensuring that the information displayed on the Gemba Board is always up-to-date and accurate.
- Accessibility: The ability to access and update Gemba Boards remotely, enabling collaboration and visibility across geographically dispersed teams.
Integration with Systems
To maximize the potential of digital Gemba Boards, organizations can integrate them with existing systems and data sources. This integration can involve:
- Linking to ERP: Connecting the Gemba Board to Enterprise Resource Planning (ERP) systems, ensuring that production data, inventory levels, and other critical information are seamlessly incorporated.
- Manufacturing data sources: Integrating with manufacturing execution systems (MES), quality management systems, or other data sources specific to the organization’s operations.
Reporting and Analytics
Digital Gemba Boards also offer advanced reporting and analytics capabilities, such as:
- Automated reports: Generating regular reports and summaries, streamlining the reporting process, and providing stakeholders with timely insights.
- Visualizing trends: Powerful data visualization tools that enable teams to identify patterns, trends, and correlations within their performance data.
Examples and Case Studies
To truly appreciate the impact of Gemba Boards, it’s essential to explore some examples and case studies from various industries.
These success stories highlight the versatility and effectiveness of Gemba Boards in driving operational excellence across different domains.
Manufacturing Productivity
In the manufacturing sector, Gemba Boards have proven instrumental in optimizing workflows and reducing cycle times.
Case studies have demonstrated their effectiveness in:
- Reducing cycle times: By identifying bottlenecks and implementing targeted improvements, organizations have achieved significant reductions in cycle times, leading to increased throughput and productivity.
- Optimizing workflows: Through visual representation of processes and real-time monitoring, teams have been able to streamline workflows, eliminate non-value-added activities, and optimize resource allocation.
Quality Control with Gemba Board
Gemba Boards have also proven invaluable in the realm of quality control, enabling organizations to enhance product quality and ensure process standardization.
Examples include:
- Defect tracking: Monitoring and tracking defect rates, root cause analysis, and implementing corrective actions to reduce defects and improve overall quality.
- Process standardization: Establishing and reinforcing standard operating procedures (SOPs) through visual cues and reminders, fostering consistency and reducing variability.
Employee Safety
Beyond productivity and quality, Gemba Boards have also played a crucial role in promoting employee safety and fostering a culture of prevention.
Applications in this domain include:
- Hazard monitoring: Identifying and addressing potential hazards or safety concerns through visual indicators and alerts.
- Preventive measures: Implementing and reinforcing safety protocols, and providing visual reminders and guidelines to minimize the risk of incidents or injuries.
Conclusion
In this discussion, we have examined how Gemba boards empower organizations through affordances such as real-time visibility, collaboration, and continuous improvement.
By leveraging core elements including key performance indicators, visual signals, status updates and action items, teams gain a holistic view of processes to make evidence-based decisions.
Additionally, integrating Gemba boards with practices such as Gemba walks, team engagement and Kaizen events generates productive synergies fueling an atmosphere of steady refinement.
As technology advances, automation and integration of Gemba boards with digital solutions presents novel opportunities.
Real-time data synchronization, sophisticated reporting, and seamless integration with existing systems unlock unprecedented levels of efficiency and insight.
The proven success of visual management strategies suggests Gemba boards deserve a prominent role in any enterprise striving for excellence.
When the right information is clearly accessible to relevant stakeholders, transformative results are well within reach.
SixSigma.us offers both Live Virtual classes as well as Online Self-Paced training. Most option includes access to the same great Master Black Belt instructors that teach our World Class in-person sessions. Sign-up today!
Virtual Classroom Training Programs Self-Paced Online Training Programs