Failure Mode, Effects, and Criticality Analysis (FMECA): A Comprehensive Guide
FMECA (Failure Mode, Effects, and Criticality Analysis) stands as a vital risk assessment method in modern engineering and maintenance practices.
This systematic approach helps organizations identify potential equipment failures, analyze their effects, and determine critical areas for improvement.
Engineers and maintenance teams rely on FMECA to make data-driven decisions about equipment reliability, maintenance schedules, and resource allocation.
Key Highlights
- FMECA implementation in maintenance programs
- Risk assessment and prioritization methods
- Integration with Six Sigma tools
- Digital transformation applications
- Industry-specific implementation strategies
What is FMECA?
FMECA represents a structured approach to equipment and process analysis that builds upon traditional failure mode assessment methods.
This engineering methodology combines failure analysis with mathematical risk assessment, enabling teams to make informed decisions about maintenance and design improvements.
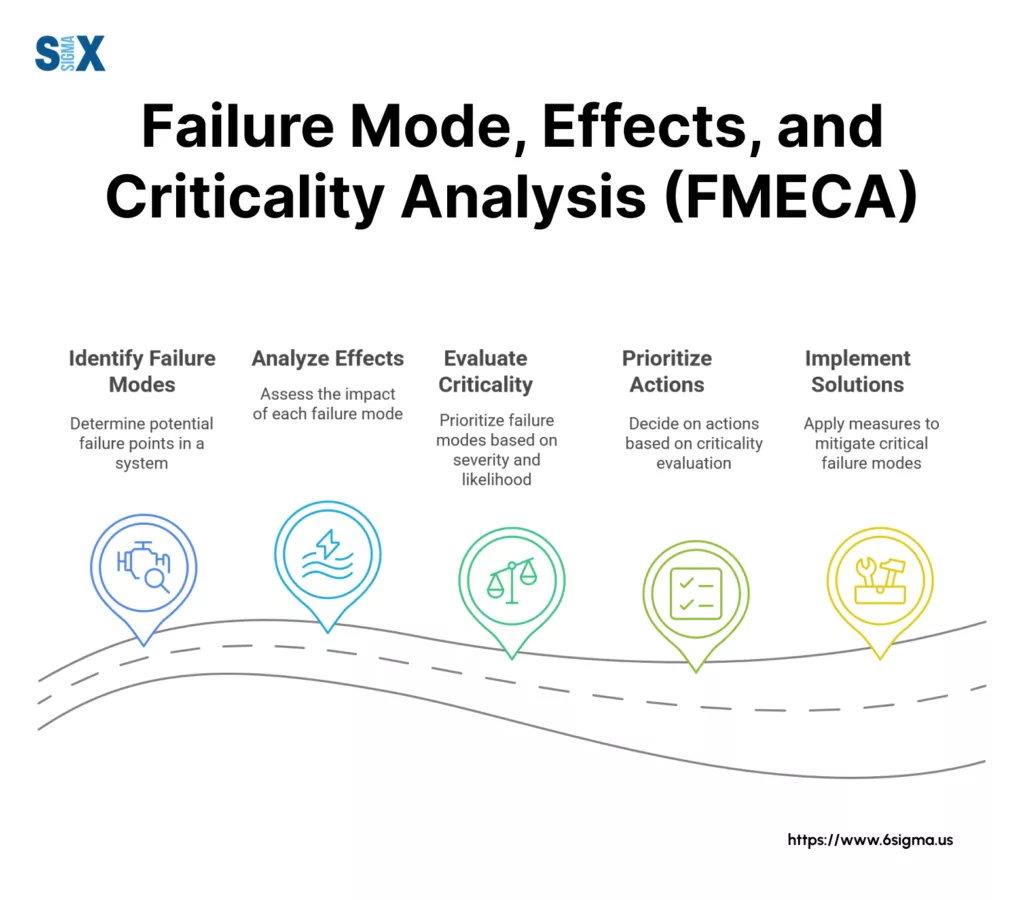
Breaking Down FMECA Components
The FMECA process starts with failure mode identification – pinpointing ways equipment or processes might fail. Engineers then analyze these potential failures to understand their effects on system operation.
The criticality assessment adds a quantitative dimension, measuring both the severity and likelihood of each failure mode.
This systematic evaluation helps maintenance teams and engineers to:
- Predict potential equipment failures
- Calculate failure probabilities
- Measure impact severity
- Rank risks based on criticality
- Plan preventive actions
Purpose and Applications
Manufacturing facilities use FMECA to strengthen their maintenance programs and reduce unexpected downtime.
The method proves particularly valuable during new equipment installation and process modifications, where early problem identification saves substantial costs.
Process engineers apply FMECA during design phases to spot potential issues before they manifest in production.
Quality teams leverage these insights to develop targeted inspection plans and control measures, ensuring consistent product quality.
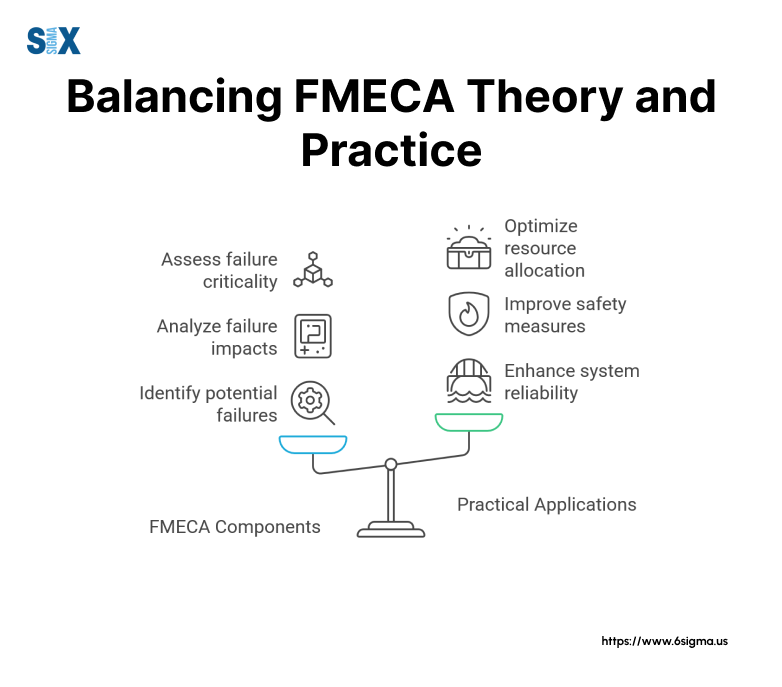
Objectives in Practice
FMECA serves multiple objectives across different industrial settings. In automotive manufacturing, it helps prevent production line failures.
Chemical processing plants use it to maintain safety standards and prevent equipment breakdowns. Electronics manufacturers rely on FMECA to ensure product reliability and reduce warranty claims.
The methodology guides teams through risk evaluation and mitigation planning, supporting both immediate problem-solving and long-term reliability improvements.
This structured approach helps organizations meet regulatory requirements while optimizing their maintenance resources.
FMECA vs Other Methodologies
FMECA and FMEA: Key Distinctions
While FMECA builds upon FMEA principles, it adds crucial quantitative elements to the analysis process. FMEA focuses on identifying potential failures and their effects, whereas FMECA takes this further by incorporating mathematical risk assessment and criticality rankings.
This additional layer helps teams prioritize their improvement efforts based on concrete data rather than qualitative judgments alone.
FMECA Versus 5 Whys Analysis
The 5 Whys technique serves as a reactive problem-solving tool, helping teams uncover root causes after failures occur. FMECA, however, works proactively by identifying potential failures before they happen.
Where 5 Whys excels in simplicity and quick implementation, FMECA provides deeper insights through structured risk assessment and prioritization methods.
FMECA and DFMEA: Design Considerations
Design FMEA (DFMEA) specifically targets product design phases, examining potential failures during product development.
FMECA extends beyond design considerations to include operational and maintenance aspects.
Manufacturing teams often use both methods – DFMEA during product development and FMECA for ongoing process improvement and maintenance planning.
Methodology Comparison Table:
Aspect | FMECA | FMEA | 5 Whys | DFMEA |
---|---|---|---|---|
Primary Focus | Risk quantification and criticality | Failure identification | Root cause analysis | Design improvement |
Timing | Proactive | Proactive | Reactive | Early design phase |
Data Requirements | High | Medium | Low | Medium |
Resource Investment | Significant | Moderate | Minimal | Moderate |
Output Type | Numerical rankings | Qualitative assessment | Root cause identification | Design recommendations |
This comparison highlights FMECA’s unique position in the reliability toolkit.
Its quantitative approach to risk assessment makes it particularly valuable for maintenance planning and resource allocation decisions.
Engineers and maintenance teams often combine these methods, selecting the most appropriate tool based on project requirements and available resources.
FMECA in Process Improvement
FMECA strengthens Lean Six Sigma initiatives by adding structured risk assessment to process improvement efforts.
Organizations implementing Six Sigma methodologies often integrate FMECA into their projects to enhance decision-making and prioritize improvement opportunities.
Role in DMAIC Process
During the Define phase, FMECA guides teams in identifying critical process components where failures could significantly impact quality or productivity.
This early analysis helps scope projects effectively and focus resources on areas with the highest potential return.
The Measure phase benefits from FMECA’s quantitative approach to risk assessment.
Teams gather data on failure frequencies and impacts, creating a baseline for improvement tracking. This numerical foundation supports data-driven decisions throughout the project lifecycle.
In Analysis, FMECA works alongside root cause analysis tools to pinpoint failure sources. The methodology’s structured approach helps teams distinguish between symptoms and underlying causes, leading to more effective solutions.
The Improve phase leverages FMECA’s criticality rankings to prioritize solutions. Teams focus first on addressing high-risk failure modes, ensuring maximum impact from improvement efforts. This targeted approach optimizes resource allocation and accelerates results.
Control phase activities incorporate FMECA findings into monitoring plans.
Teams develop specific metrics and control limits based on critical failure modes, creating sustainable improvements through ongoing measurement and adjustment.
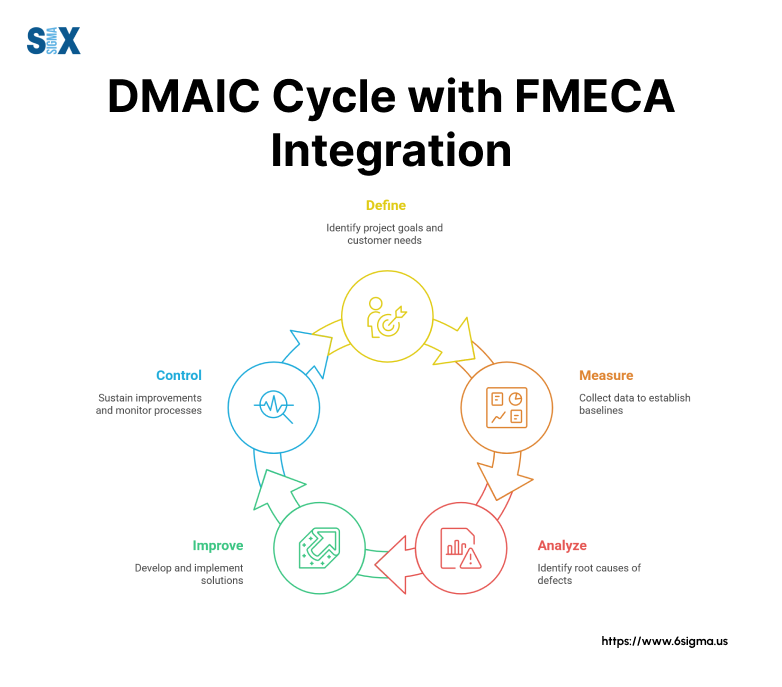
Integration With Six Sigma Tools
Process mapping gains additional depth when combined with FMECA, highlighting potential failure points within workflow steps. This integration helps teams visualize risk areas and design more robust processes.
Cause and effect diagrams become more powerful when informed by FMECA data. Teams can weight different causes based on criticality scores, focusing investigation efforts on the most significant factors.
Control plans developed using FMECA insights target specific failure modes with appropriate monitoring methods. This precision improves detection capabilities and reduces reaction time to potential issues.
Value Stream Enhancement
FMECA supports waste reduction by identifying potential failure points before they impact production. This proactive approach prevents defects, reduces rework, and minimizes unplanned downtime.
Quality improvements stem from better understanding of process vulnerabilities. Teams use FMECA insights to strengthen control methods and establish more effective quality checks at critical points.
Cost optimization occurs through targeted improvement efforts and reduced failure rates. Organizations save resources by addressing high-risk areas first and preventing costly breakdowns.
Process reliability increases as teams implement controls based on FMECA findings. Regular monitoring of critical parameters helps maintain stable operations and consistent output quality.
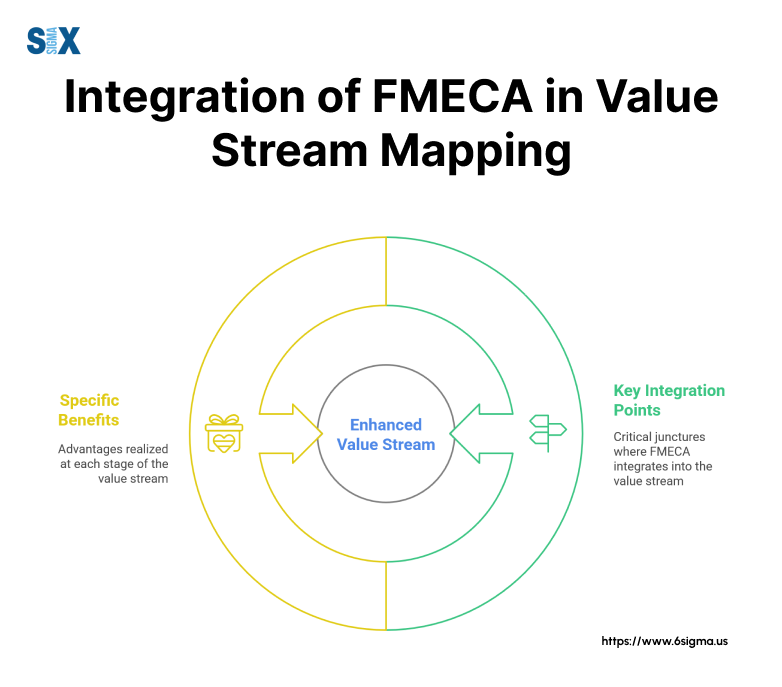
Take the First Step Towards Operational Excellence
Turn risk analysis into strategic advantage with our Lean Six Sigma Green Belt course
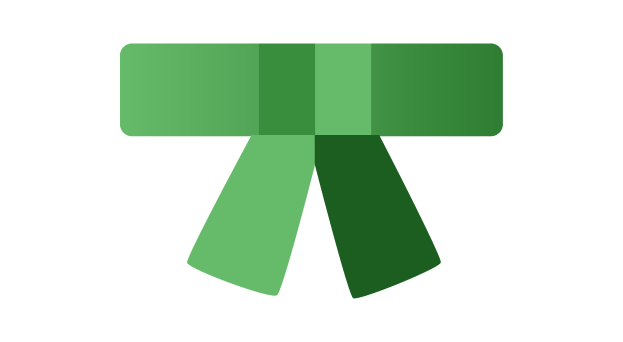
The FMECA Process: Step-by-Step Guide
The FMECA process begins with clear system boundaries and operational requirements.
Engineering teams document equipment functions, performance parameters, and operating conditions. This foundation ensures all subsequent analysis focuses on relevant failure modes and their impacts.
Manufacturing facilities often start by breaking down complex systems into manageable subsystems. Each component’s role, interactions, and performance requirements must be clearly defined.
This detailed mapping helps teams understand potential failure points and their relationships within the larger system.
Failure Mode Identification
Teams examine each system component to identify potential failure modes.
This step requires input from operators, maintenance personnel, and engineers who understand equipment behavior under various conditions. Historical maintenance records provide valuable insights into common failure patterns.
Documentation during this phase should include specific descriptions of how each component might fail. Rather than general statements, teams note exact failure mechanisms.
For example, instead of “pump failure” the analysis might specify “pump bearing seizure due to inadequate lubrication”.
Effects Analysis
Once failure modes are identified, teams analyze their effects on system operation. This analysis considers both immediate and downstream impacts.
Engineers evaluate how each failure affects system performance, safety, and production quality.
The effects analysis must account for different operating conditions and potential cascading failures.
Teams document both local effects on specific components and the broader impact on system functionality.
Criticality Assessment
During criticality assessment, teams assign numerical values to each failure mode based on:
- Severity of consequences
- Probability of occurrence
- Likelihood of detection
- Time to failure
This quantitative evaluation transforms qualitative insights into measurable risk factors. Teams use standardized scoring criteria to ensure consistent assessment across different system components.
Risk Prioritization
The final step ranks failure modes based on their criticality scores. This prioritization guides maintenance planning and resource allocation.
Teams focus first on addressing high-risk failures that could significantly impact operations or safety.
Risk prioritization helps maintenance managers develop targeted improvement plans.
These include:
- Enhanced preventive maintenance schedules
- Additional monitoring equipment
- Design modifications
- Updated operating procedures
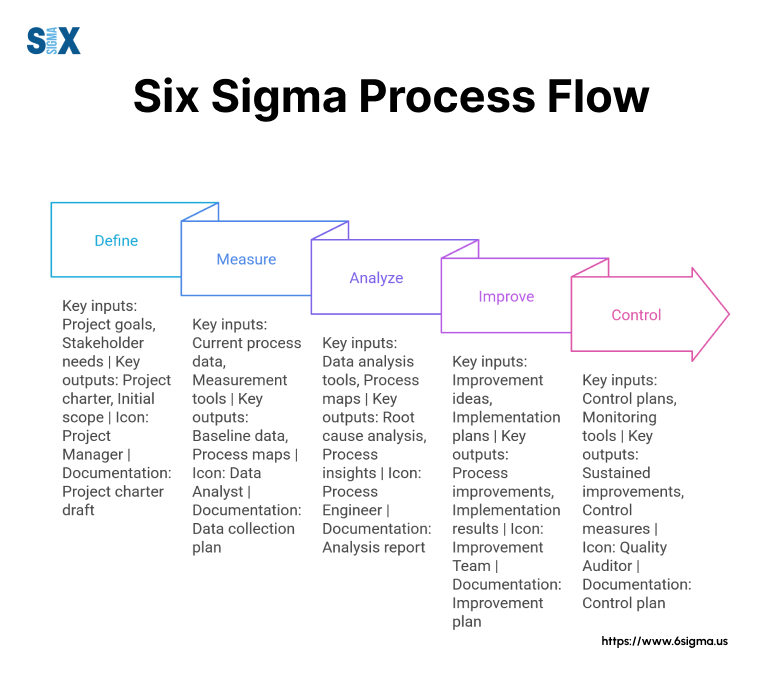
This structured approach ensures thorough analysis of potential failures while maintaining focus on practical risk reduction.
Each step builds upon previous findings, creating a robust foundation for maintenance and reliability improvements.
FMECA Criticality Analysis
FMECA criticality analysis transforms qualitative failure assessments into measurable risk values.
This numerical approach helps maintenance teams and engineers make informed decisions about resource allocation and intervention timing.
The analysis considers both the probability of failure occurrence and the severity of potential consequences.
Manufacturing facilities use criticality scores to develop maintenance schedules and spare parts strategies.
These scores reflect the relative importance of different system components and their potential impact on operations.
Higher criticality ratings indicate areas requiring more frequent monitoring and faster response times to potential issues.
Ranking System Structure
The FMECA ranking system typically uses a scale from 1 to 10 for each evaluation factor. Severity rankings consider safety impacts, production losses, and repair costs.
Occurrence rankings reflect failure frequency based on historical data or engineering estimates. Detection rankings measure how easily teams can identify potential failures before they occur.
Teams multiply these individual rankings to calculate the Risk Priority Number (RPN):
Severity (1-10) x Occurrence (1-10) x Detection (1-10) = RPN (1-1000)
This calculation provides a standardized method for comparing different failure modes across systems and equipment types.
Higher RPN values indicate priorities for maintenance attention and improvement efforts.
Assessment Methods
Quantitative assessment relies on actual failure data, maintenance records, and equipment history.
Teams analyze mean time between failures, repair costs, and downtime duration to establish accurate rankings. This data-driven approach provides the most reliable basis for criticality decisions.
Qualitative assessment becomes necessary when historical data proves limited or unavailable. Engineering teams use expert judgment and industry standards to estimate potential impacts and failure frequencies.
While less precise than quantitative methods, this approach still provides valuable guidance for risk management.
Mixed-method assessment combines both approaches, using available data while incorporating expert knowledge to fill gaps.
This pragmatic strategy proves particularly useful when implementing FMECA in new facilities or with recently installed equipment.
The matrix helps visualize risk levels and prioritize actions:
- Red Zone (High RPN): Immediate action required
- Yellow Zone (Medium RPN): Scheduled improvement needed
- Green Zone (Low RPN): Monitor through routine maintenance
Regular review and updates of criticality assessments ensure rankings remain relevant as operating conditions change.
Teams should reassess rankings after significant equipment modifications, process changes, or when new failure modes emerge.
Benefits and Strengths of FMECA
FMECA delivers significant value through systematic risk assessment and failure prevention.
Manufacturing facilities report reduced downtime, lower maintenance costs, and improved equipment reliability after implementing FMECA programs.
The methodology’s structured approach helps teams identify and address potential issues before they impact production.
Quality improvements stem from better understanding of failure modes and their effects. Teams can implement targeted controls and monitoring systems, reducing defect rates and warranty claims.
This proactive stance particularly benefits industries with high quality requirements, such as automotive and aerospace manufacturing.
Safety enhancements result from early identification of potential hazards. Organizations use FMECA findings to strengthen safety protocols and emergency response procedures.
These improvements protect both personnel and equipment while ensuring regulatory compliance.
FMECA Implementation Strategy
Successful FMECA implementation requires careful planning and resource allocation. Organizations should start with pilot projects on critical equipment or processes.
This focused approach allows teams to refine their methodology before expanding to other areas.
Resource requirements include dedicated team members, analysis tools, and data collection systems. Engineering and maintenance personnel need training in FMECA methodology and documentation procedures.
Management support proves essential for securing necessary resources and maintaining program momentum.
Teams should establish clear success metrics and review procedures.
Regular assessment of FMECA effectiveness helps justify continued investment and identifies areas for improvement.
Documentation standards ensure consistent analysis across different departments and facilities.
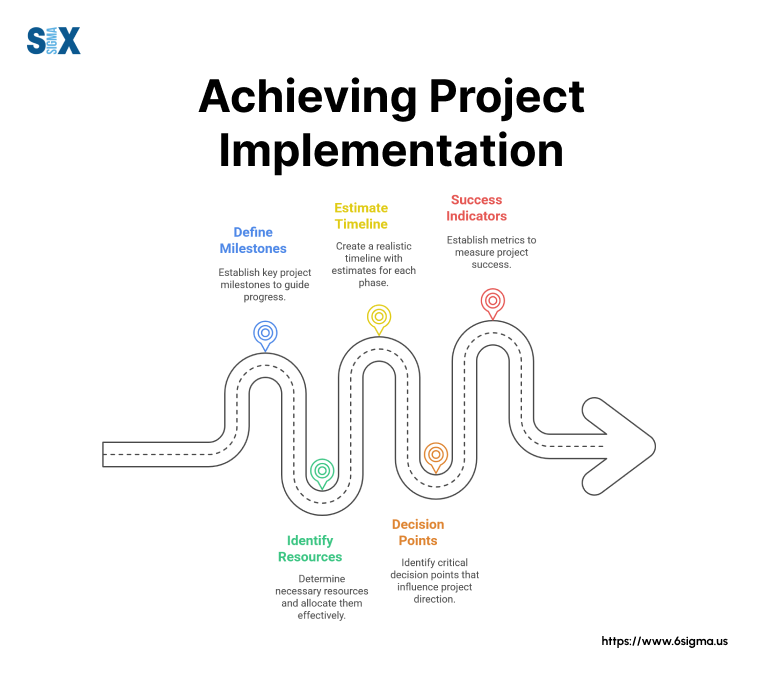
Lead with Data-Driven Reliability Strategies with Leadership Champion Training and Change Your Organization’s Maintenance Approach
FMECA in Maintenance
Modern maintenance strategies integrate FMECA with predictive technologies. Sensors and monitoring systems provide real-time data on equipment condition, enabling more accurate failure predictions.
This integration helps maintenance teams optimize inspection schedules and repair timing.
Digital platforms streamline FMECA documentation and analysis. Software tools help teams track failure modes, calculate risk priorities, and manage improvement projects.
These systems also facilitate data sharing across departments and locations, improving coordination and decision-making.
Maintenance planning benefits from FMECA’s systematic approach to risk assessment. Teams develop more effective preventive maintenance schedules based on criticality rankings.
This targeted strategy optimizes resource utilization while maintaining equipment reliability.
The Road Ahead
FMECA provides a robust framework for risk assessment and reliability improvement.
Organizations across industries benefit from its structured approach to failure prevention and maintenance optimization.
The methodology continues evolving with new technologies and applications, maintaining its relevance in manufacturing.
Success requires commitment to proper implementation and ongoing program support. Teams must balance analytical rigor with practical constraints while maintaining focus on key objectives.
Regular review and adjustment ensure FMECA programs deliver sustained value through improved reliability and reduced maintenance costs.
The future of FMECA lies in greater integration with digital technologies and predictive maintenance systems.
These advances will enhance analysis capabilities while streamlining implementation.
Organizations that embrace these developments position themselves for continued improvement in equipment reliability and maintenance effectiveness.
SixSigma.us offers both Live Virtual classes as well as Online Self-Paced training. Most option includes access to the same great Master Black Belt instructors that teach our World Class in-person sessions. Sign-up today!
Virtual Classroom Training Programs Self-Paced Online Training Programs