DVP&R (Design Verification Plan and Report): A Comprehensive Guide to Quality Assurance
Today product failures can be catastrophic. A 2022 industry report revealed that design flaws discovered late in development cost companies an average of $1.5 million per project and delay market entry by 4-6 months.
For automotive manufacturers, these delays can mean missing critical launch windows and losing market share to competitors.
DVP&R (Design Verification Plan and Report) stands as a crucial quality management tool that helps engineering teams avoid these costly pitfalls.
This systematic approach to testing and validation ensures products meet specifications before they reach production, saving both time and resources while maintaining quality standards.
The DVP&R process bridges the gap between design intent and final product reality.
In this guide, we’ll explore:
- DVP&R fundamentals and core components
- Step-by-step implementation techniques
- Real-world application examples
- Integration with Six Sigma methods
What Is DVP&R?
DVP&R, or Design Verification Plan and Report, serves as a structured document that guides product testing throughout the development cycle.
This critical quality assurance tool outlines the specific tests required to verify that a design meets all functional and performance requirements before mass production begins.
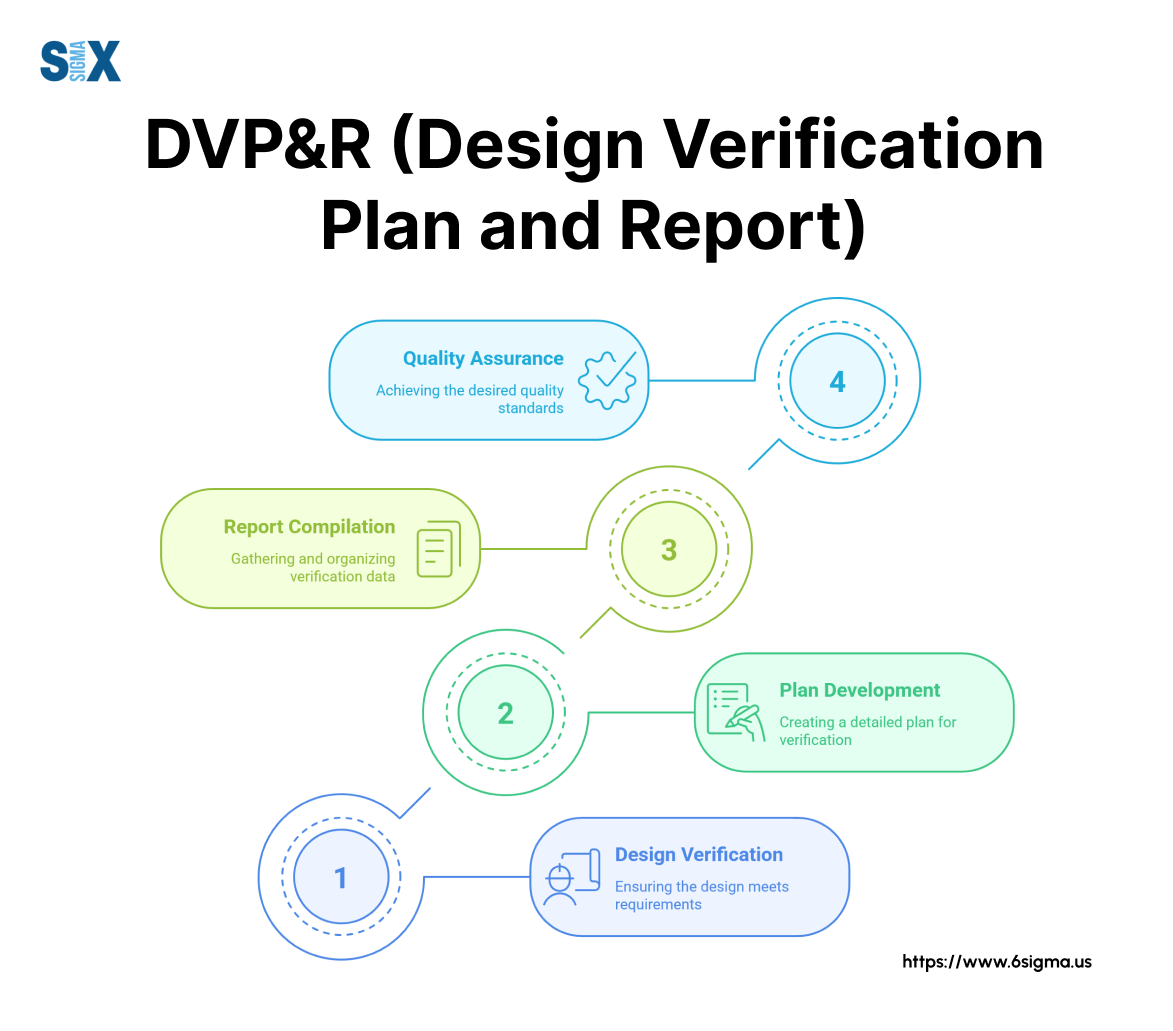
The dvp&r full form breaks down into two essential components that work together to ensure product quality:
The “Plan” portion establishes what tests will be performed, how they’ll be conducted, and what criteria determine success.
Engineers document test methods, sample sizes, acceptance parameters, and scheduling details during the planning phase.
The “Report” section captures actual test results, comparing them against the predetermined acceptance criteria.
This documentation creates a trail of evidence showing whether design requirements have been met. When tests fail, the report helps teams identify necessary design modifications and track retest results until all specifications are satisfied.
DVP&R emerged in the automotive industry during the 1980s as manufacturers sought more rigorous quality control methods.
Ford Motor Company played a significant role in standardizing the approach through their Advanced Product Quality Planning (APQP) framework.
The methodology gained wider adoption when it became part of the QS-9000 quality standard and later evolved within the IATF 16949 automotive quality management system.
Today, what is dvp&r has expanded beyond automotive applications into aerospace, medical device manufacturing, electronics, and other industries where product reliability is paramount.
The DVP&R process connects directly to other quality tools, particularly the Design Failure Mode and Effects Analysis (DFMEA).
This systematic approach aligns with broader quality methodologies like Six Sigma certification, which emphasizes data-driven decision making and defect reduction.
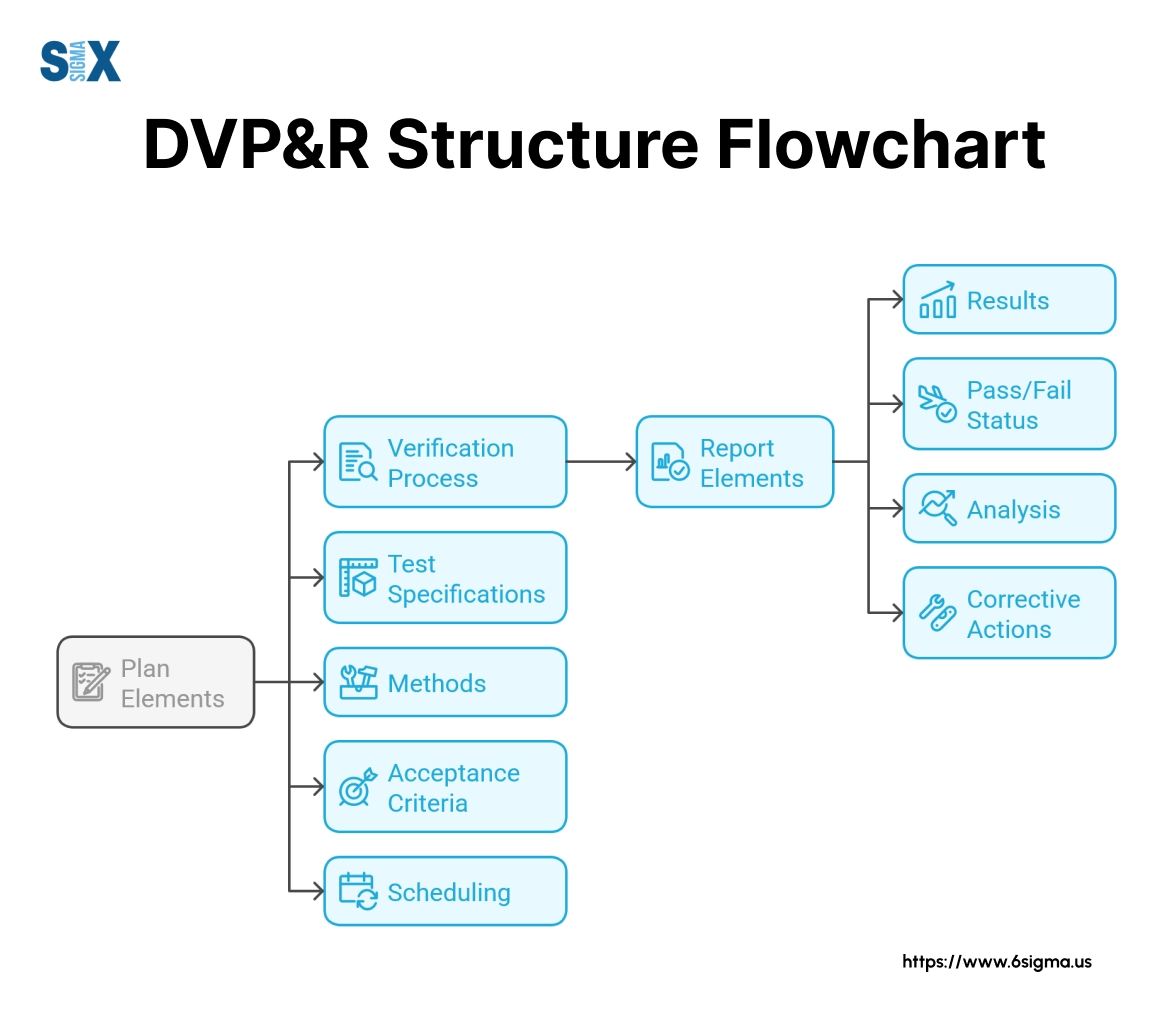
The Role Of DVP&R In Six Sigma
DVP&R plays a crucial role within the Six Sigma quality improvement methodology, particularly during the Measure, Analyze, and Improve phases of the DMAIC framework.
When organizations implement Six Sigma principles to reduce defects and variation, DVP&R provides the structured testing approach needed to verify that improvements actually deliver the intended results.
During the Measure phase, DVP&R helps teams establish baseline performance metrics through initial verification testing.
These measurements become reference points against which future improvements can be evaluated. The detailed test specifications in a DVP&R document ensure consistent measurement methods, reducing the risk of measurement system variation that could compromise data integrity.
In the Analyze phase, DVP&R test results highlight performance gaps between current designs and target specifications.
When a test fails to meet acceptance criteria, Six Sigma practitioners apply statistical analysis tools to identify root causes.
This analytical approach transforms DVP&R from a simple pass/fail checklist into a powerful diagnostic tool that drives targeted design improvements.
The Improve phase relies heavily on DVP&R to validate that proposed solutions effectively address identified problems. Engineers develop verification tests specifically designed to challenge potential failure modes, then document results in the report section.
This evidence-based approach aligns perfectly with Six Sigma’s emphasis on data-driven decision making.
Organizations with robust Six Sigma certification programs often integrate DVP&R training into their curriculum.
Green Belts typically learn basic DVP&R concepts and application, while Black Belt certification dive deeper into statistical test design and analysis methods that enhance verification effectiveness.
Master Black Belts often lead the development of company-specific DVP&R standards and training materials.
The structured nature of DVP&R complements Six Sigma’s statistical approach to quality management.
Both methodologies share fundamental principles:
- Prevention over detection – identifying and addressing potential issues before they impact customers
- Data-driven decision making – using objective test results rather than opinions
- Process standardization – creating repeatable verification methods
- Continuous improvement – using test results to drive ongoing design refinements
Many automotive and aerospace manufacturers have successfully merged DVP&R practices with Six Sigma initiatives to create integrated quality management systems.
This combined approach leverages the strengths of both methodologies: Six Sigma provides the statistical tools to analyze complex performance data, while DVP&R offers the structured framework to verify that improvements meet requirements.
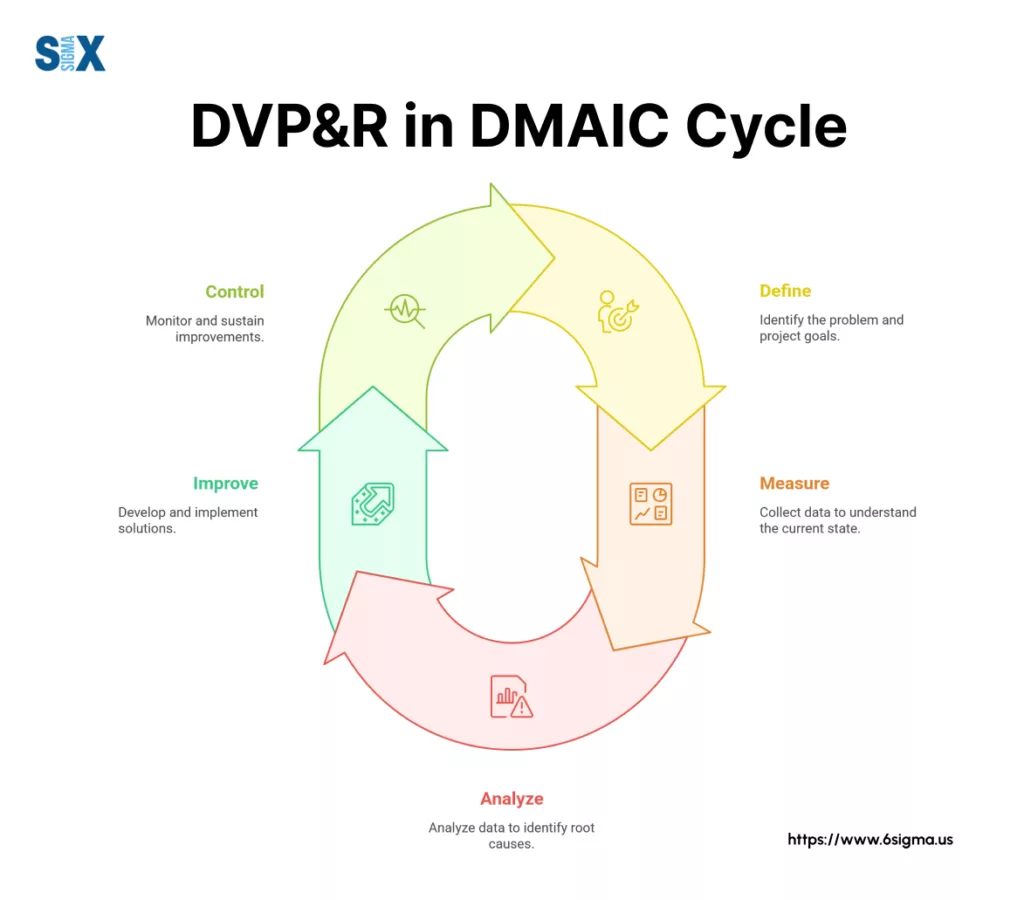
DVP&R Process And Implementation
Creating an effective DVP&R requires a methodical approach that spans the entire product development lifecycle.
The dvp&r process typically unfolds in three distinct phases, each building upon the previous to ensure thorough design verification.
Planning Phase
The planning phase begins immediately after design specifications are finalized. Engineering teams review product requirements and identify critical characteristics that require verification.
This initial step often involves cross-functional collaboration between design, quality, manufacturing, and test engineers.
Teams analyze the Design Failure Mode and Effects Analysis (DFMEA) to prioritize tests based on risk severity, occurrence probability, and detection difficulty.
During planning, engineers must determine appropriate test methods for each requirement. Some tests may leverage existing standard procedures, while others require custom protocols.
The team documents sample sizes, measurement techniques, and equipment needs. They also establish pass/fail criteria based on engineering specifications, customer requirements, and industry standards.
This planning documentation forms the foundation of the verification strategy.
Execution Phase
The execution phase transforms plans into action. Test engineers prepare test equipment, calibrate measurement devices, and procure test samples according to the plan specifications.
They conduct tests following documented procedures, recording raw data and observations throughout the process.
When tests reveal performance issues, engineers must decide whether to modify the test procedure, adjust acceptance criteria, or recommend design changes.
Proper test execution requires meticulous attention to detail.
Reporting Phase
The reporting phase completes the dvp&r tutorial cycle. Engineers analyze test results against acceptance criteria, determining whether each requirement has been satisfied.
They document both conforming and non-conforming results, providing detailed analysis for any failures.
The final report includes recommendations for design improvements, additional testing, or approval for production release.
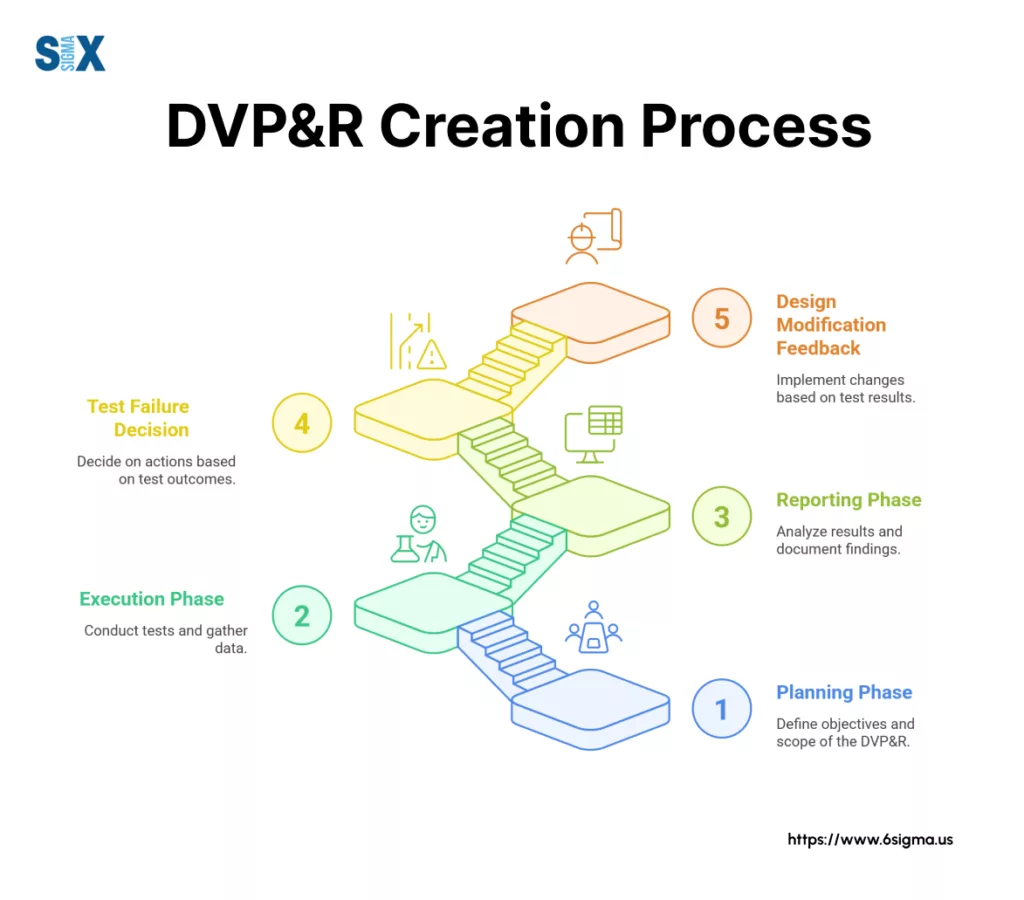
Key Elements Of A DVP&R Form
The dvp&r format includes several standard sections that organize verification information logically. While formats may vary slightly between companies, most include these essential elements:
Header information
Header information captures project identification details including part number, revision level, engineering release date, and team member responsibilities.
The header typically includes approval signatures from engineering, quality, and management stakeholders, formalizing the verification plan.
Test specifications
Test specifications form the core of the document. Each test receives a unique identifier and links directly to a product requirement or specification.
Engineers document the test purpose, applicable specification limits, and reference standards. This section explains what aspect of the design is being verified and why the test matters.
Acceptance criteria
Acceptance criteria define the boundaries between acceptable and unacceptable results. These criteria must be quantifiable whenever possible, with numerical limits rather than subjective assessments.
Engineers specify both the target value and allowable tolerance range. When qualitative evaluation is necessary, the criteria must include clear descriptors of acceptable performance.
The schedule identifies when tests will occur within the product development timeline, often linking to specific prototype builds or development milestones.
Results documentation
Results documentation captures actual test outcomes, including raw data, statistical analysis, and pass/fail determinations. This section transforms the plan into a report by recording verification evidence.
Engineers document any deviations from planned procedures and explain their impact on results validity.
For professionals pursuing Six Sigma certification or Six Sigma Green Belt certification, understanding DVP&R documentation provides valuable skills in measurement system development and test planning. The structured approach to verification aligns perfectly with Six Sigma’s data-driven methodology.
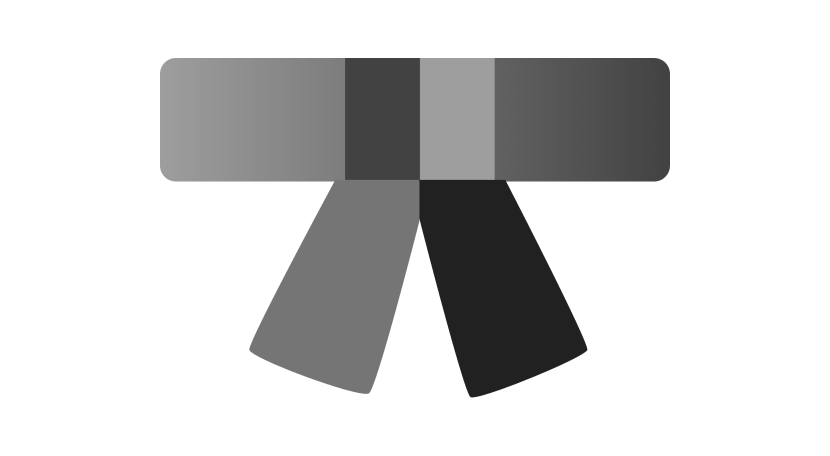
Become a Six Sigma expert, optimize complex verification strategies with Lean Six Sigma Black Belt
Master advanced statistical tools needed for robust DVP&R analysis
DVP&R Vs. Other Quality Tools
Quality professionals often confuse dvp and r with DFMEA (Design Failure Mode and Effects Analysis) since both tools address product quality during development.
However, these methodologies serve distinct yet complementary purposes in the quality management ecosystem. Understanding their relationship helps teams implement both tools effectively.
DFMEA focuses on identifying potential failure modes before they occur. Engineers analyze design elements to predict what might go wrong, why it might happen, and how severe the consequences could be.
This proactive risk assessment happens early in the design process, often before prototypes exist. DFMEA prioritizes risks using Risk Priority Numbers (RPNs) calculated from severity, occurrence, and detection ratings.
In contrast, dvp & r verifies that the final design meets requirements through actual testing. It transforms theoretical concerns into practical validation activities.
While DFMEA predicts problems, DVP&R proves the design works as intended through objective evidence.
This distinction becomes clear when examining how information flows between the two documents.
Aspect | DFMEA | DVP&R |
---|---|---|
Primary Purpose | Identify potential failures | Verify design requirements |
Timing in Development | Early design phase | Throughout development cycle |
Focus | Failure modes and causes | Test methods and results |
Output | Risk assessments and preventive actions | Verification evidence and status |
Key Metrics | Risk Priority Numbers (RPN) | Pass/Fail against specifications |
Team Composition | Cross-functional design team | Test engineers and quality specialists |
Documentation Type | Living risk assessment | Test plan and results record |
Complementary Aspects
The complementary nature of these tools becomes evident when examining their integration points. High-risk items identified in DFMEA directly inform DVP&R test priorities.
When DFMEA reveals a potential failure with severe consequences, engineers develop specific verification tests to ensure the design prevents that failure mode.
This risk-based approach focuses testing resources where they matter most.
Integration Points
DFMEA recommended actions often include verification requirements that appear in the DVP&R. For example, if DFMEA identifies material fatigue as a risk, the DVP&R might include accelerated life testing to verify durability.
This connection ensures that identified risks receive appropriate verification attention.
The relationship works bidirectionally. When DVP&R testing reveals unexpected failures, teams update the DFMEA to reflect the newly discovered failure modes. This feedback loop improves risk assessment accuracy for future projects.
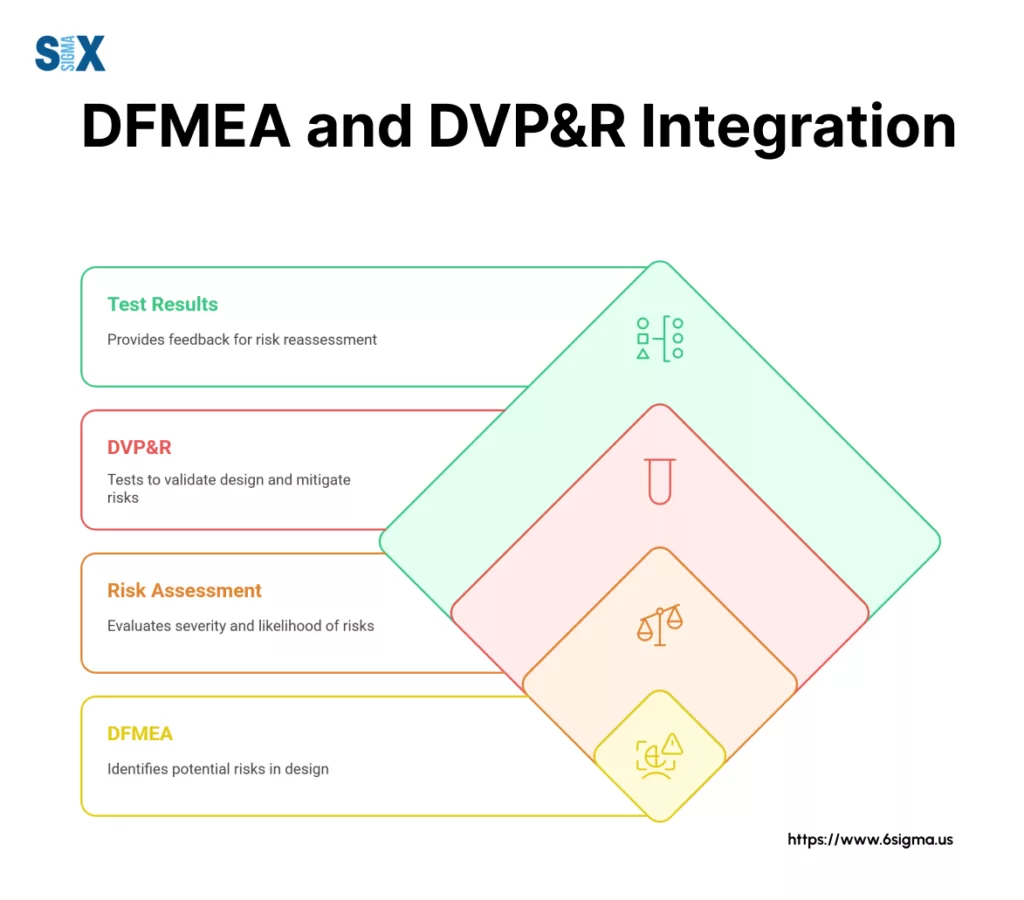
Integration With Root Cause Analysis
When DVP&R testing reveals design deficiencies, integration with root cause analysis techniques becomes essential.
Connection Points
This connection transforms test failures from simple problems into learning opportunities that drive design improvements.
The structured approach of DVP&R provides the perfect foundation for systematic problem-solving.
Test failures documented in DVP&R reports trigger the root cause analysis process. Quality engineers examine failed tests to understand not just what failed, but why it failed.
Engineers can trace exactly which requirement wasn’t met and under what conditions the failure occurred.
Turn DVP&R test failures into permanent solutions with systematic Root Cause Analysis training.
Methodology Alignment
Several root cause analysis methodologies align naturally with DVP&R processes:
The 5-Why technique helps teams drill down from observed test failures to underlying causes. Starting with the failed test result, engineers ask “why” repeatedly until they identify the fundamental issue.
For example, if a component fails a thermal cycling test, the 5-Why process might reveal that a material selection decision made early in design caused the failure.
Fishbone (Ishikawa) diagrams organize potential causes of test failures into categories like materials, methods, machinery, and measurements.
The 8D (Eight Disciplines) problem-solving process incorporates DVP&R in multiple steps. Initial test failures from DVP&R trigger the process.
Implementation of permanent corrective actions requires updated verification protocols to ensure effectiveness.
Process Improvement
Process improvement results from this integration. When root cause analysis identifies systemic issues, teams update both design standards and verification methods.
Future DVP&R documents incorporate these lessons, preventing similar failures on subsequent projects. This continuous improvement cycle gradually raises product quality across the organization.
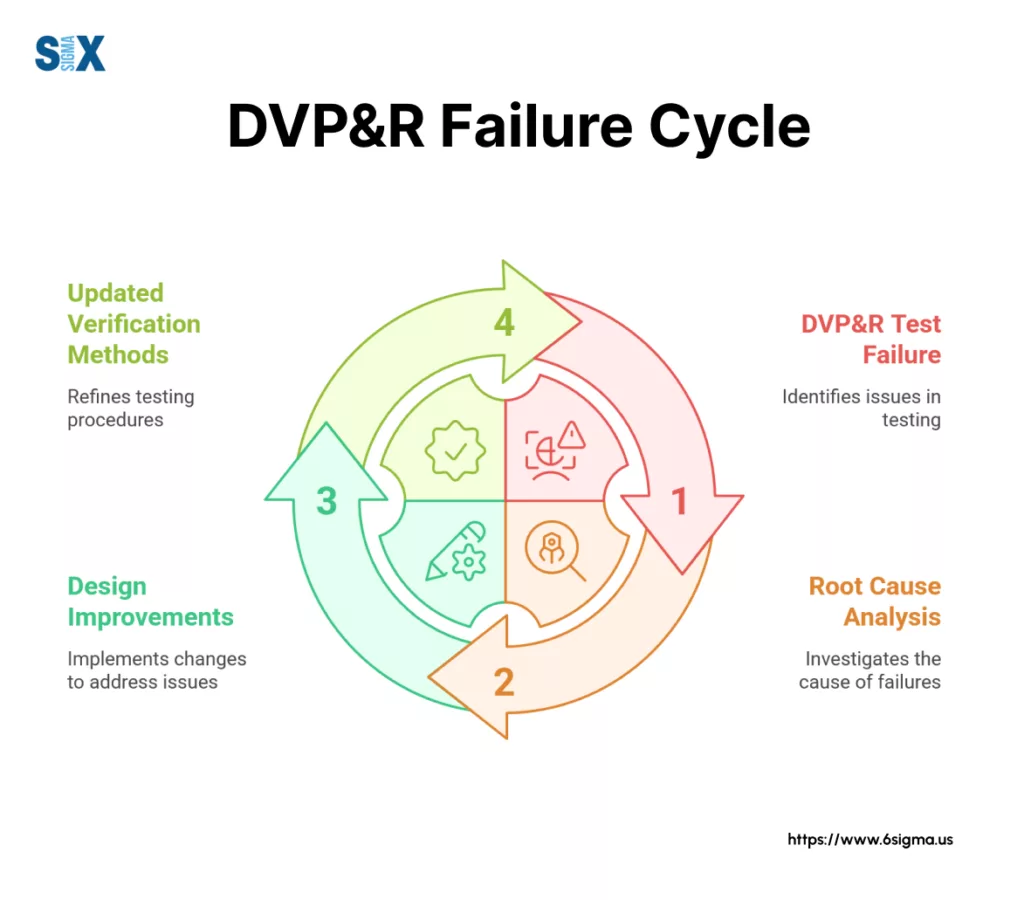
Practical Application And Examples
DVP&R implementation varies significantly across industries, with each sector adapting the framework to address unique product requirements, regulatory demands, and market expectations.
These real-world applications demonstrate how the basic DVP&R structure flexes to accommodate diverse verification needs while maintaining its core purpose.
Automotive
The automotive industry pioneered DVP&R usage and continues to refine its application. Major OEMs like Ford, GM, and Toyota require suppliers to submit standardized DVP&R documentation as part of the Production Part Approval Process (PPAP).
A typical dvp&r example in automotive might focus on a brake component, where verification includes performance testing under extreme temperatures, durability cycling, and noise evaluation. Automotive DVP&Rs typically reference industry standards like SAE, ASTM, and ISO test methods.
For a vehicle door handle assembly, the DVP&R would include mechanical tests like pull strength, cycle durability (50,000+ operations), environmental exposure (salt spray, UV degradation), and temperature extremes (-40°C to +85°C).
Aviation
Aviation manufacturers apply DVP&R within their stringent safety-critical systems. The aviation approach emphasizes traceability between requirements and verification evidence.
A dvp & r example for an aircraft component might include vibration profiles that precisely match expected flight conditions, electromagnetic compatibility testing, and altitude simulation.
Manufacturing
Medical device manufacturers adapt DVP&R to meet FDA and international regulatory requirements. Their approach emphasizes validation of both performance and safety characteristics.
Verification activities often include biocompatibility testing, sterilization validation, and usability studies alongside traditional functional testing.
Medical DVP&Rs maintain careful distinction between verification (does the product meet specifications?) and validation (does the product fulfill intended use?).
Manufacturing equipment builders focus their DVP&R efforts on reliability, maintainability, and performance metrics. Verification typically includes extended run testing, fault injection, and capacity validation.
The acceptance criteria often specify statistical performance measures like Overall Equipment Effectiveness (OEE) and Mean Time Between Failures (MTBF).
Each industry adapts the DVP&R format to address specific needs while maintaining the fundamental plan-and-report structure.
Automotive applications might emphasize Production Part Approval Process (PPAP) alignment, while medical device DVP&Rs focus on regulatory compliance documentation.
Despite these differences, successful implementations share common elements:
- Clear traceability between requirements and verification methods
- Objective acceptance criteria based on measurable parameters
- Documented test results with pass/fail determinations
- Formal approval processes for both plan and report phases
DVP&R ROI Calculator
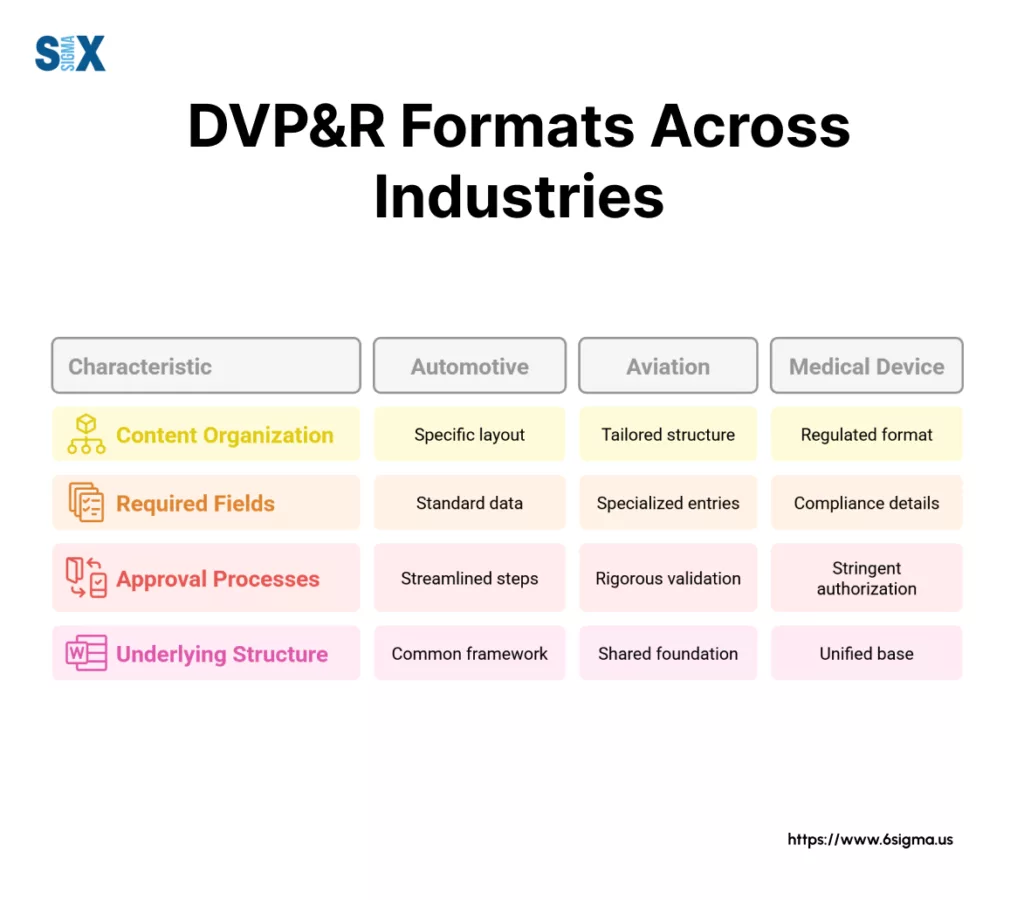
Training And Implementation
Effective DVP&R implementation requires specific skills that organizations must develop through structured training programs.
Companies that invest in dvp & r training see higher quality outcomes, reduced development cycles, and fewer field failures.
Skill Development
Engineering staff need technical training focused on test method selection, sample size determination, and statistical analysis of results.
Engineers must understand how to translate design requirements into verifiable test parameters and how to establish appropriate acceptance criteria.
This technical foundation ensures DVP&R documents contain meaningful verification activities rather than superficial checks.
Quality professionals require training on document control, approval workflows, and integration with other quality system elements.
Their role often includes ensuring DVP&R compliance with customer and regulatory requirements.
Quality staff typically become the internal experts on DVP&R format standards and documentation requirements.
Certification Paths
Project managers benefit from training that emphasizes resource planning, schedule integration, and risk management aspects of the verification process.
Their understanding of DVP&R helps them allocate appropriate time and resources for testing activities throughout the development cycle.
Most organizations structure dvp&r training in progressive levels:
Basic awareness training introduces the DVP&R concept, terminology, and purpose.
This level targets all product development staff and typically takes 2-4 hours. Participants learn to read and interpret DVP&R documents even if they don’t create them.
Practitioner training develops skills for creating and executing verification plans. This intermediate level requires 1-2 days and includes hands-on exercises developing test plans for sample products.
Engineers learn to select appropriate test methods, define acceptance criteria, and document results properly.
Advanced training focuses on statistical aspects of verification, test method development, and integration with design controls. This level typically spans 3-5 days and targets lead engineers and quality specialists who will become internal experts.
Integration with Six Sigma training
Many organizations integrate DVP&R training with their Six Sigma Green Belt certification programs. The statistical tools taught in Six Sigma courses directly apply to verification planning and results analysis.
Green Belts learn to design experiments that efficiently verify multiple requirements while minimizing testing resources.
For more advanced practitioners, Six Sigma Master Black Belt certification programs often include specialized modules on verification strategy and test system development.
These experts typically lead the development of company-specific DVP&R standards and training materials.
Industry-specific training supplements these general approaches. Automotive sector training emphasizes PPAP requirements and IATF 16949 compliance.
Best Practices And Common Pitfalls
Organizations that successfully implement DVP&R follow several best practices that maximize its effectiveness while avoiding common implementation pitfalls.
These practices transform DVP&R from a documentation exercise into a powerful quality assurance tool.
Start verification planning early in the design process. Waiting until design completion often results in rushed testing and missed opportunities to influence design decisions.
Leading companies begin drafting DVP&R documents during concept development, refining the verification approach as design details emerge.
This early planning identifies potential verification challenges before designs are finalized.
Link verification activities directly to customer requirements and design specifications. Each test should have clear traceability to specific requirements.
This linkage ensures complete verification coverage and prevents unnecessary testing. When requirements change, the verification plan must be reviewed and updated accordingly.
Common pitfalls include:
Vague acceptance criteria that allow subjective pass/fail determinations. Criteria like “shall function properly” or “acceptable appearance” create inconsistent evaluations.
Insufficient sample sizes that fail to account for production variation. Testing one or two prototypes may not reveal issues that will emerge in mass production.
Incomplete test methods that lack procedural details. Instructions like “test for durability” without specifying conditions, cycles, or evaluation points lead to inconsistent verification.
Failure to update DVP&R documents when designs change. Verification plans must evolve alongside the product design. Organizations need change management processes that trigger DVP&R reviews when specifications change.
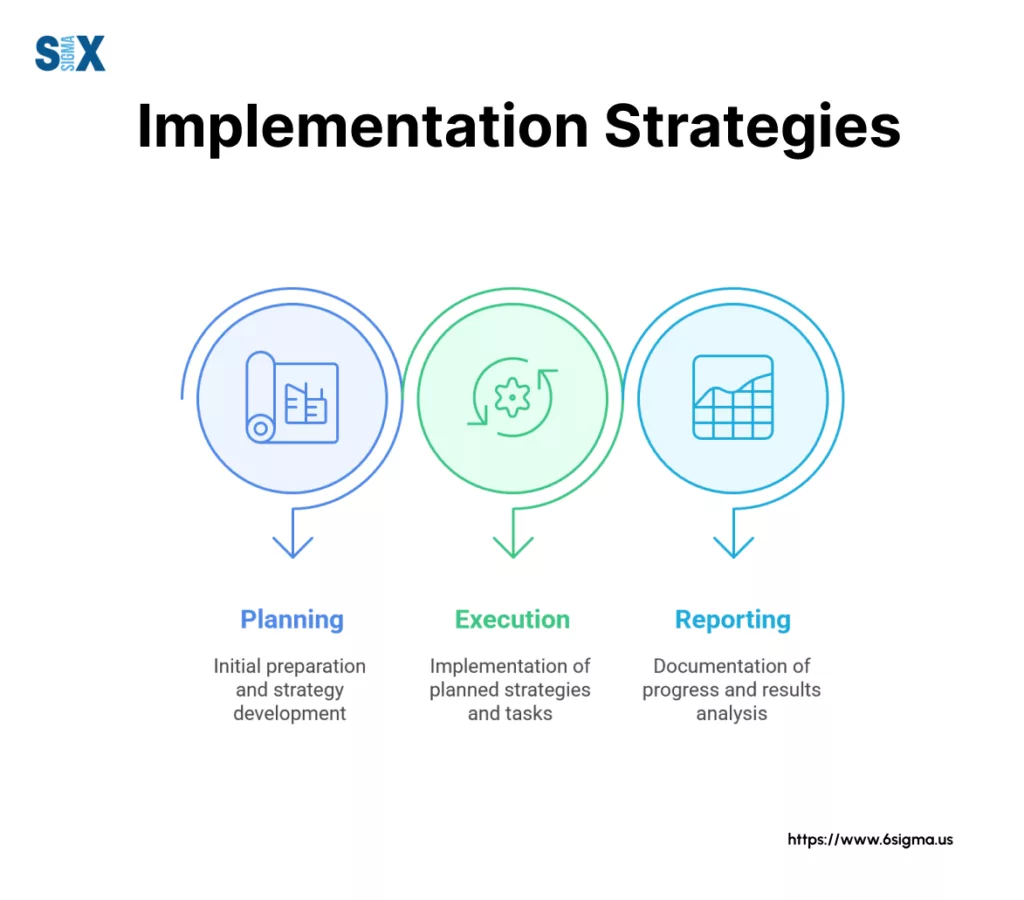
Lead Impactful Quality Improvements
Master verification tools like DVP&R with our Six Sigma Green Belt Certification
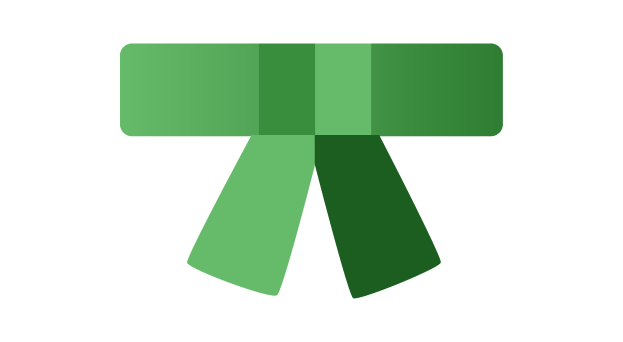
Conclusion And Resources
DVP&R stands as an essential quality management tool that bridges the gap between design intent and production reality.
The key takeaways for successful DVP&R implementation include:
- DVP&R serves both planning and documentation purposes, guiding verification activities while creating an evidence trail of design adequacy.
- Effective verification requires clear traceability between customer requirements, design specifications, and test methods.
- Integration with other quality tools like DFMEA and root cause analysis maximizes DVP&R effectiveness.
- Industry-specific adaptations maintain core DVP&R principles while addressing unique sector requirements.
- Proper training across multiple organizational roles ensures consistent application and maximum benefit.
Organizations seeking to improve their verification processes can leverage several resources:
Industry standards like AIAG’s Advanced Product Quality Planning (APQP) manual provide foundational guidance on DVP&R implementation within automotive quality systems.
Similar resources exist for medical, aerospace, and other regulated industries.
Software tools range from simple dvp&r template spreadsheets to sophisticated test management systems integrated with PLM (Product Lifecycle Management) platforms. These tools streamline documentation, improve traceability, and enhance collaboration across development teams.
Consulting organizations specializing in quality management can provide implementation assistance, training programs, and customized templates tailored to specific industry needs. Their experience across multiple companies offers valuable implementation insights.
For organizations beginning their DVP&R journey, starting with a standardized template provides immediate structure while allowing customization as needs evolve.
The ultimate measure of DVP&R effectiveness isn’t documentation completeness but product performance. This outcome justifies the investment in developing robust verification processes and training teams in their effective implementation.
SixSigma.us offers both Live Virtual classes as well as Online Self-Paced training. Most option includes access to the same great Master Black Belt instructors that teach our World Class in-person sessions. Sign-up today!
Virtual Classroom Training Programs Self-Paced Online Training Programs