Corrective Action Report: Comprehensive Guide & Best Practices 2025
Corrective action reports (CARs) are central to Six Sigma’s data-driven methodology for process excellence, with a Six Sigma certification providing the tools to master CAR frameworks and implement sustainable improvements.
Essentially, a corrective action report provides a formal, systematic template for confronting and remedying issues, mistakes, discrepancies, or shortfalls found within operations, offerings, services, or frameworks.
Its purpose illuminates problems’ intrinsic sources, then spurs potent correctives to preclude reoccurrence.
In sharing, we explore CARs’ virtuous design through real applications successfully navigating complexity.
Regardless of field, their gifts in resolving problems prudently while advancing comprehension invite faithful consideration.
Wherever processes could strengthen through structured issue navigation, reflect on CARs’ strategical role in illuminating pathways towards elevated standards sustainably.
Key Highlights
- Understand the definition, purpose, and importance of corrective action reports in quality management and continuous improvement
- Explore the key benefits of implementing CARs, including preventing recurring mistakes, improving overall quality, providing documentation, and facilitating root cause analysis
- Learn the step-by-step process of creating a comprehensive corrective action report, from identifying the issue to verifying the effectiveness of corrective actions
- Gain insights into best practices for conducting thorough root cause analysis, setting measurable corrective actions, and maintaining proper documentation
- Address some questions about corrective action reports, clarifying common misconceptions and providing expert guidance
What is a Corrective Action Report?
Corrective action reports (CARs) are essential tools in Six Sigma and process improvement methodologies, and gaining a Six Sigma certification can deepen your understanding of how to effectively use them to achieve operational excellence and continuous improvement.
A corrective action report is a formal document organizations use to address and rectify issues, errors, non-conformances, or deficiencies identified in processes, products, services, or systems.
It serves as a structured framework for identifying the root cause of a problem, implementing corrective actions to resolve it, and preventing its recurrence in the future.
The primary purpose of a CAR is to facilitate a comprehensive investigation and root cause analysis of an identified issue and to outline specific corrective actions that will be taken to address the root cause effectively.
By doing so, organizations can mitigate the risks associated with the problem and ensure that it does not happen again, thereby enhancing the overall quality and reliability of their operations.
In the context of quality management and continuous improvement initiatives, corrective action reports play a pivotal role.
They are instrumental in maintaining and enhancing the quality of products, services, and processes, fostering a culture of accountability, and driving ongoing process optimization.
CARs are essential tools for organizations striving to meet regulatory compliance requirements, satisfy customer expectations, and achieve operational excellence.
Key components of a well-constructed corrective action report include:
- Description of the issue or non-conformance: A detailed account of the problem, including when, where, and how it was discovered, along with supporting evidence or documentation.
- Root cause analysis: A thorough investigation and analysis to identify the underlying causes or factors contributing to the issue, often employing techniques such as the 5 Whys, Fishbone Diagram, or Failure Mode and Effects Analysis (FMEA).
- Proposed corrective actions: Specific and measurable actions aimed at addressing the root cause of the problem, ensuring that the corrective actions are feasible, realistic, and effective.
- Responsibilities and timelines: Clear assignment of responsibilities for implementing each corrective action, along with realistic deadlines for completion.
- Implementation plan: A detailed strategy outlining how each corrective action will be executed, including steps, resources required, and potential obstacles or challenges.
- Monitoring and verification: A process for monitoring and verifying the effectiveness of the corrective actions, specifying how success will be measured and when the issue will be considered resolved.
- Documentation and communication: Comprehensive records of the issue, root cause analysis, corrective action plans, responsibilities, timelines, and monitoring results, effectively communicated to relevant stakeholders.
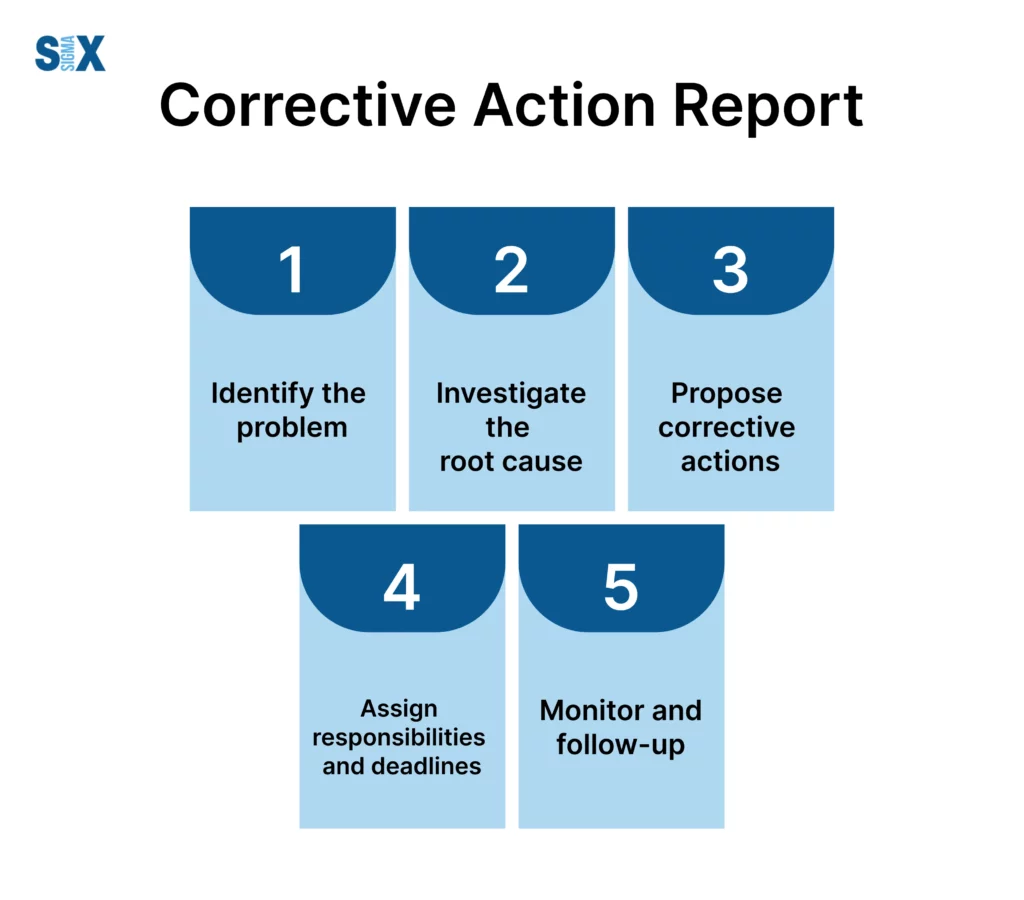
By systematically documenting and addressing problems through corrective action reports, organizations can improve their processes, enhance product and service quality, comply with regulations, satisfy customers, and continuously strive for operational excellence.
Benefits of Corrective Action Reports
Implementing a robust corrective action reporting process can yield numerous benefits for organizations, including:
- Preventing recurring mistakes and defects: By identifying and addressing the root causes of issues, corrective action reports help organizations prevent similar problems from occurring in the future, thereby reducing the likelihood of costly mistakes, defects, and rework.
- Improving overall quality and business health: By continuously identifying and resolving issues through corrective actions, organizations can enhance the quality of their products, services, and processes, leading to improved customer satisfaction, increased efficiency, and better overall business performance.
- Providing documentation and accountability: Corrective action reports serve as formal documentation of issues, root causes, and corrective actions taken, providing a valuable record for accountability, auditing, and reference purposes.
- Facilitating root cause analysis and problem-solving: The process of creating a corrective action report requires a thorough root cause analysis, which fosters a problem-solving mindset and enables organizations to identify and address the underlying causes of issues, rather than merely treating the symptoms.
By leveraging the benefits of corrective action reports, organizations can cultivate a culture of continuous improvement, where problems are viewed as opportunities for learning and growth, and where proactive measures are taken to prevent future occurrences.
Creating a Corrective Action Report
Creating an effective corrective action report is a systematic process that requires careful planning, analysis, and execution. Here are the key steps involved:
- Identifying the issue or non-conformance: The first step is to clearly define the problem or non-conformance that has been identified. This includes gathering relevant details, such as when, where, and how the issue was discovered, as well as collecting supporting evidence or documentation.
- Conducting root cause analysis: Once the issue has been identified, it is crucial to conduct a thorough root cause analysis to determine the underlying factors that contributed to the problem. Various techniques can be employed for this purpose, including:
Root Cause Analysis Techniques
- 5 Whys: This iterative technique involves asking “why” a problem occurred and then asking “why” again for each subsequent answer until the root cause is identified.
- Fishbone Diagram (also known as Ishikawa Diagram or Cause-and-Effect Diagram): This visual tool allows you to explore and categorize potential causes of a problem into different branches, such as people, processes, materials, and equipment. Organizations often invest in root cause analysis training to ensure teams can systematically apply these tools during CAR investigations.
- Failure Mode and Effects Analysis (FMEA): This systematic approach involves identifying potential failure modes, their causes, and their effects, and then prioritizing them based on risk levels.
- Defining corrective actions: Based on the findings from the root cause analysis, the next step is to define specific and measurable corrective actions that will address the root cause of the problem. These actions should be feasible, realistic, and effective in preventing recurrence.
- Assigning responsibilities and timelines: Once the corrective actions have been identified, it is essential to assign clear responsibilities to individuals or teams for implementing each action.
- Developing an implementation plan: A detailed plan should be developed outlining how each corrective action will be implemented, including specific steps, resources required, and potential obstacles or challenges that may arise during the implementation process.
- Monitoring and verifying effectiveness: After implementing the corrective actions, it is crucial to monitor and verify their effectiveness in addressing the identified issue.
- Documentation and communication: Maintaining comprehensive documentation throughout the corrective action process is essential. This includes records of the issue, root cause analysis, corrective action plans, responsibilities, timelines, and monitoring results.
- Follow-up, review, and continuous improvement: Regular follow-up reviews should be conducted to assess the progress of corrective actions and make adjustments if necessary. Once the issue has been fully resolved, it is important to document the outcomes and lessons learned for future reference.
By following these steps and leveraging best practices, organizations can create comprehensive and effective corrective action reports that drive meaningful improvements and contribute to overall operational excellence.
Corrective Action Report Process
The corrective action report process is a systematic approach to identifying, analyzing, and resolving issues or non-conformances within an organization. It typically involves the following steps:
Step 1: Problem Identification and Reporting
The process begins with the identification and reporting of an issue or non-conformance.
This can be discovered through various means, such as inspections, audits, customer complaints, or internal monitoring processes.
It is crucial to document the problem in detail, including when, where, and how it was discovered, as well as any supporting evidence or documentation.
Step 2: Root Cause Analysis
Once the problem has been reported, a thorough root cause analysis must be conducted to identify the underlying factors that contributed to the issue.
This analysis can be performed using various techniques, such as the 5 Whys, Fishbone Diagram, or Failure Mode and Effects Analysis (FMEA), as discussed earlier.
Step 3: Corrective Action Planning
- SMART goals: The corrective actions should be Specific, Measurable, Attainable, Relevant, and Time-bound, ensuring clarity and achievability.
- Timeframes: Realistic timelines should be established for implementing each corrective action, taking into account the urgency and complexity of the issue.
- Costs: An estimation of the costs associated with implementing the corrective actions, including resources, materials, and personnel requirements.
- Signatories: The corrective action plan should be reviewed and approved by relevant stakeholders, such as process owners, quality managers, or senior leadership, to ensure accountability and buy-in.
Advancing problem-solving skills might involve progressing through Six Sigma tiers such as Six Sigma Green Belt Certification or Six Sigma Black Belt certification, which build expertise in designing and monitoring corrective actions.
Step 4: Implementation and Monitoring
Once the corrective action plan has been developed and approved, the organization must implement the corrective actions according to the established timelines and procedures.
During this phase, it is essential to monitor the progress and effectiveness of the corrective actions, making adjustments as necessary.
Step 5: Verification and Closure
After implementing the corrective actions, the organization must verify their effectiveness in resolving the identified issue.
This may involve conducting follow-up audits, inspections, or performance evaluations to ensure that the problem has been adequately addressed and will not recur.
If the corrective actions are deemed successful, the corrective action report can be formally closed.
Step 6: Continuous Improvement and Lessons Learned
The corrective action report process does not end with the closure of the report.
It is essential to capture and document the lessons learned throughout the process and use them to inform future improvements.
This knowledge can be incorporated into training programs, process updates, or preventive action plans to proactively address potential issues and drive continuous improvement within the organization.
By following this structured process, organizations can effectively identify, analyze, and resolve issues, mitigate risks, and continuously improve their operations, products, and services.
Best Practices for Corrective Action Reports
To maximize the effectiveness of corrective action reports, it is crucial to adhere to best practices throughout the process. Here are some key best practices to consider:
- Conducting thorough root cause analysis: A comprehensive root cause analysis is essential for identifying the underlying factors contributing to the issue. Failing to uncover the true root cause can lead to ineffective corrective actions and a higher likelihood of the problem recurring.
- Including specific details and evidence: Corrective action reports should provide detailed descriptions of the issue, including specific details, supporting evidence, and documentation. This level of detail is necessary for a thorough analysis and effective corrective action planning.
- Involving relevant stakeholders: Engaging stakeholders from various departments or functional areas can provide diverse perspectives and valuable insights during the corrective action process. This can lead to a more comprehensive understanding of the issue and more effective corrective actions.
Integrating Lean fundamentals into CAR processes can further streamline problem-solving and reduce waste. - Setting realistic and measurable corrective actions: Corrective actions should be specific, measurable, attainable, relevant, and time-bound (SMART). This ensures that the actions are clear, achievable, and can be effectively monitored and evaluated for their impact.
- Maintaining proper documentation and records: Comprehensive documentation and record-keeping are essential throughout the corrective action process. This includes documenting the issue, root cause analysis, corrective action plans, responsibilities, timelines, monitoring results, and lessons learned.
- Ensuring accountability and follow-up: Assigning clear responsibilities and deadlines for corrective actions is crucial for maintaining accountability and ensuring timely implementation. Regular follow-up and monitoring are also necessary to verify the effectiveness of the corrective actions and make adjustments if needed.
By adhering to these best practices, organizations can create robust and effective corrective action reports that drive meaningful improvements, mitigate risks, and foster a culture of continuous improvement.
Frequently Asked Questions (FAQs) about Corrective Action Reports
Corrective Action Reports (CARs) are formal documents organizations use to address and rectify issues, errors, non-conformances, or deficiencies identified in processes, products, services, or systems.
They provide a structured approach to identifying the root cause of a problem, implementing corrective actions to resolve it, and preventing its recurrence in the future.
CARs are essential tools for quality management and continuous improvement initiatives, as they help organizations maintain and enhance the quality of their offerings, comply with regulations, satisfy customer expectations, and achieve operational excellence.
Preparing a comprehensive Corrective Action Report involves several key steps:
– Identify and document the issue or non-conformance in detail, including when, where, and how it was discovered, along with supporting evidence.
– Conduct a thorough root cause analysis using techniques like the 5 Whys, Fishbone Diagram, or Failure Mode and Effects Analysis (FMEA) to identify the underlying causes of the problem.
– Define specific and measurable corrective actions that directly address the root cause of the issue.
– Assign responsibilities and realistic timelines for implementing each corrective action.
– Develop a detailed implementation plan outlining the steps, resources required, and potential challenges for executing the corrective actions.
– Establish a monitoring and verification process to evaluate the effectiveness of the corrective actions and ensure the problem has been resolved.
– Maintain comprehensive documentation throughout the process, including records of the issue, root cause analysis, corrective action plans, responsibilities, timelines, and monitoring results.
– Communicate the Corrective Action Report to relevant stakeholders and ensure accountability for implementing the corrective actions.
– Conduct regular follow-up reviews to assess progress, make adjustments if necessary, and document lessons learned for future reference.
– Formally close the Corrective Action Report once the issue has been successfully resolved and the effectiveness of the corrective actions has been verified.
No, not every Corrective Action Report is the same.
The specific details and format of a CAR may vary depending on industry standards, organizational requirements, and the nature and severity of the issue being addressed.
For example, CARs in highly regulated industries such as healthcare or aviation may have more stringent requirements and additional components compared to those in less regulated sectors.
Similarly, a CAR addressing a critical non-conformance that could lead to significant consequences (e.g., product recalls or safety hazards) would likely be more comprehensive and require more rigorous root cause analysis and corrective actions than a CAR addressing a minor process deviation.
Regardless of the specific format or industry, the fundamental principles of identifying the root cause, implementing effective corrective actions, and preventing recurrence remain consistent across all Corrective Action Reports.
SixSigma.us offers both Live Virtual classes as well as Online Self-Paced training. Most option includes access to the same great Master Black Belt instructors that teach our World Class in-person sessions. Sign-up today!
Virtual Classroom Training Programs Self-Paced Online Training Programs