Continuous Quality Improvement (CQI): Driving Organizational Excellence
Enterprises invariably pursue enhanced routines, refined qualities and operational excellences resolutely. Methodologies distinguishing themselves fruitfully amidst these quests encompass Continuous Quality Improvement (CQI) assuredly.
Over the past two decades, CQI (Continuous Quality Improvement) has demonstrated its transformative power across various industries.
With extensive experience and expertise, CQI has proven its ability to empower organizations and drive meaningful change.
CQIās nucleus comprises systematically identifying betterment amidst organization’s undertakings, productions or servicing.
Embracing perpetual progressionsā notions that evolution potentials persist boundlessly amidst most stabilized modalities, quality cultures nurture workforce’s engagements and empowerments, steering enterprise’s sustained thriving comprehensively.
CQI grounds upon empirical-inquiriesā disciplined approaches, whereby governance-architect’s resolutenesses inform on rigorous analytical evidence-basis.
Countinous self-examinations and enhancements-opportunitiesā identifications along targeted intervention’s conductings propagate routining refinings while eliminating waste or maximized competencies and impactfulness fluidly.
Where intricate scenarios invite prudent navigation, CQI strategical have important role in resolving it.
Progress necessitates optimize relations creatively, resourcefully wherever aspirations surface amid realities.
Key Highlights
- Overview of Continuous Quality Improvement (CQI) and its importance in modern organizations
- Exploration of key CQI methodologies, including Lean Six Sigma, PDSA Cycle, and Baldrige Excellence Framework
- In-depth analysis of CQI applications in the healthcare sector, focusing on patient safety, performance measurement, and staff training
- Practical guidance on implementing CQI within organizations, covering infrastructure establishment, opportunity identification, and sustaining efforts
- case studies and success stories, illustrating the quantitative and qualitative impact of CQI initiatives
- Discussion of emerging trends, challenges, and the role of technology in driving continuous improvement efforts
What is Continuous Quality Improvement (CQI)?
Continuous Quality Improvement (CQI) is a detailed approach that identifies and addresses opportunities for enhancement within an organization’s processes, products, or services.
CQI is rooted in the belief that there is always room for growth and even the most well-established practices can benefit from continuous improvement.
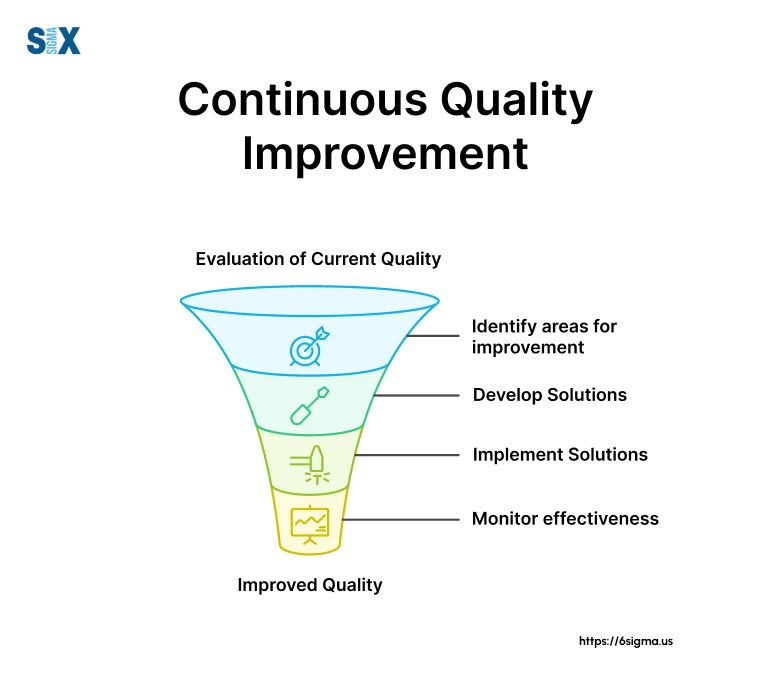
It encourages organizations to adopt a mindset of relentless pursuit of perfection, where complacency is never an option, and the status quo is constantly challenged.
Key elements and principles that underpin the CQI (Continuous Quality Improvement) philosophy include:
- Customer-centric approach: CQI initiatives are driven by a deep understanding of customer needs and expectations, ensuring that improvements are aligned with delivering exceptional value and satisfaction.
- Data-driven decision-making: Rigorous data collection, analysis, and interpretation form the backbone of CQI efforts, enabling organizations to make informed decisions and measure the impact of their interventions.
- Continuous monitoring and evaluation: CQI is an ongoing cycle of planning, executing, studying, and adjusting, where performance is continuously monitored, and improvements are iteratively implemented based on feedback and learning.
- Employee engagement and empowerment: Successful CQI initiatives rely on the active participation and empowerment of employees at all levels, fostering a culture of ownership, innovation, and continuous learning.
The importance and benefits of embracing CQI within organizations cannot be overstated.
By adopting this methodology, organizations can experience:
- Enhanced quality and consistency of products/services
- Improved operational efficiency and productivity
- Reduced waste and costs
- Increased customer satisfaction and loyalty
- Competitive advantage and market differentiation
- An engaged and motivated workforce
- Continuous learning and adaptation to changing market dynamics
Continuous Quality Improvement Methodologies and Frameworks
While the principles of CQI remain consistent, various methodologies and frameworks have emerged to guide its implementation within organizations.
Three of the most widely adopted approaches are Lean Six Sigma, the Plan-Do-Study-Act (PDSA) Cycle, and the Baldrige Excellence Framework.
Lean Six Sigma
Lean Six Sigma is a powerful methodology that combines the principles of Lean, which focuses on eliminating waste and optimizing flow, with Six Sigma, a data-driven approach to reducing variation and defects.
This integrated approach has proven to be a potent tool for driving continuous improvement within organizations.
The Lean Six Sigma methodology is typically structured around the DMAIC (Define, Measure, Analyze, Improve, Control) cycle:
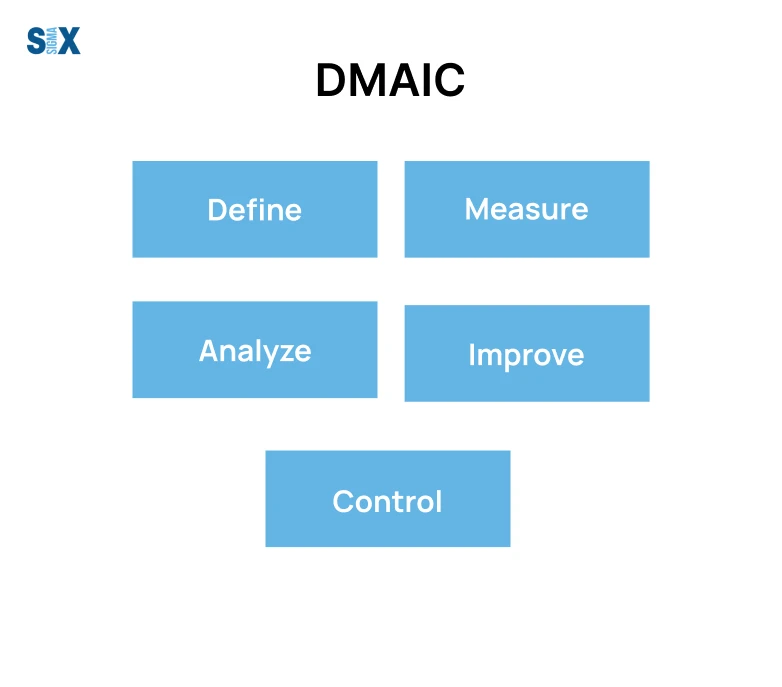
- Define: Clearly define the problem, goals, and scope of the improvement project.
- Measure: Establish baseline performance metrics and collect relevant data.
- Analyze: Identify root causes and factors contributing to the problem or inefficiency.
- Improve: Develop, implement, and validate solutions to address the identified issues.
- Control: Establish control measures to sustain the improvements and monitor ongoing performance.
Lean Six Sigma also emphasizes the concept of Kaizen, which promotes continuous incremental improvements through the elimination of waste (muda) in processes.
Statistical tools and analysis play a crucial role in identifying and quantifying areas for improvement, enabling data-driven decision-making.
Plan-Do-Study-Act (PDSA) Cycle
The PDSA Cycle, also known as the Deming Cycle or the Shewhart Cycle, is a fundamental model for continuous improvement.
Developed by Walter A. Shewhart and popularized by W. Edwards Deming, this iterative approach provides a structured framework for implementing and refining improvements.
The PDSA Cycle consists of four stages:
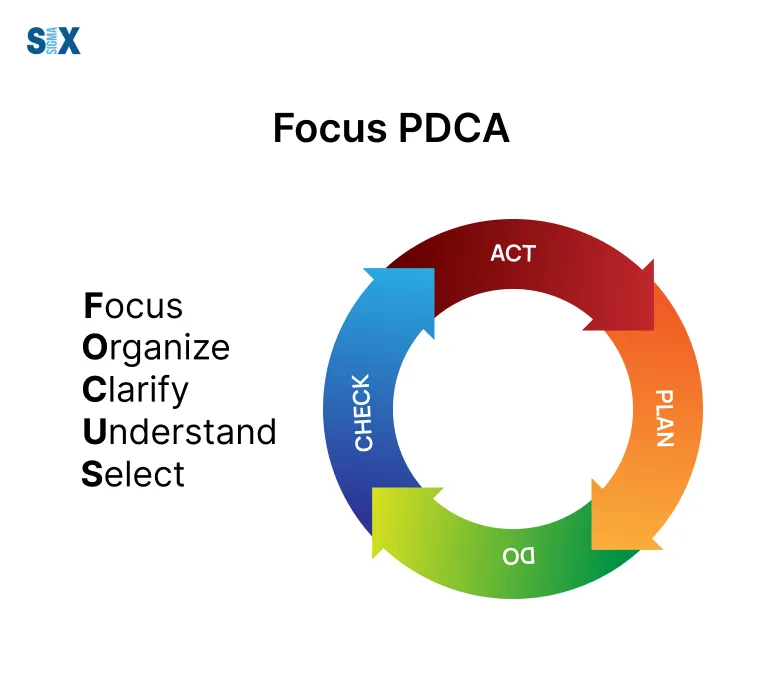
- Plan: Identify the problem, gather relevant data, and develop an improvement plan.
- Do: Implement the planned improvement on a small scale or pilot basis.
- Study: Analyze the results of the implementation, gather data, and evaluate the effectiveness of the improvement.
- Act: Based on the study phase, decide whether to adopt, modify, or abandon the improvement. If successful, standardize and implement the improvement on a broader scale.
The beauty of the PDSA Cycle lies in its simplicity and versatility. It can be applied to a wide range of improvement initiatives, from small-scale process tweaks to large-scale organizational transformations.
By embracing this iterative approach, organizations can continuously refine and optimize their processes, leveraging learnings from each cycle.
Baldrige Excellence Framework and Continuous Quality Improvement
The Baldrige Excellence Framework is a comprehensive management approach that promotes organizational performance excellence and continuous improvement.
Developed by the Baldrige Performance Excellence Program, this framework provides a systems perspective for understanding and managing organizational performance.
The Baldrige Excellence Framework is structured around seven interconnected categories:
- Leadership: Examining how senior leaders guide and sustain the organization’s commitment to excellence.
- Strategic Planning: Evaluating how the organization establishes and deploys its strategic direction.
- Customer Focus: Assessing how the organization builds lasting relationships with customers and determines their requirements and expectations.
- Measurement, Analysis, and Knowledge Management: Examining how the organization selects, gathers, analyzes, manages, and improves its data, information, and knowledge assets.
- Workforce Focus: Evaluating how the organization engages, manages, and develops its workforce to utilize its full potential.
- Operations Focus: Assessing how the organization designs, manages and improves its key products and work processes.
- Results: Examining the organization’s performance and improvement in key areas, including product and process outcomes, customer satisfaction, workforce engagement, and operational effectiveness.
The Baldrige Excellence Framework encourages organizations to conduct self-assessments, identify strengths and opportunities for improvement, and implement targeted initiatives to drive continuous improvement across all aspects of their operations.
By leveraging these methodologies and frameworks, organizations can establish a robust and structured approach to Continuous Quality Improvement, ensuring that their pursuit of excellence is guided by proven principles, data-driven insights, and a commitment to ongoing refinement.
Continuous Quality Improvement (CQI) in Healthcare
The healthcare industry has been at the forefront of adopting Continuous Quality Improvement methodologies, driven by the critical need to enhance patient safety, improve clinical outcomes, and optimize operational efficiency.
CQI initiatives in healthcare have become instrumental in addressing challenges, reducing costs, and delivering high-quality care.
Patient Safety and Quality Improvement
Patient safety is a paramount concern in the healthcare sector, and CQI plays a crucial role in identifying and mitigating potential risks, reducing medical errors, and improving patient outcomes.
By continuously monitoring and analyzing processes, organizations can pinpoint vulnerabilities, implement preventive measures, and foster a culture of safety and accountability.
One notable example of a successful CQI initiative in healthcare is the implementation of surgical checklists.
By standardizing pre-operative procedures and ensuring all critical steps are followed, organizations have reported significant reductions in surgical complications, infections, and mortality rates.
Performance and Outcomes Measurement using Continuous Quality Improvement
In the healthcare domain, accurately defining and measuring key performance indicators (KPIs) and patient outcomes is essential for driving continuous improvement.
CQI frameworks emphasize the importance of establishing clear metrics, collecting reliable data, and analyzing this information to identify areas for enhancement.
Performance metrics can encompass various aspects, such as patient satisfaction scores, readmission rates, length of stay, infection rates, and treatment effectiveness.
By regularly monitoring and reporting on these metrics, healthcare organizations can make data-driven decisions, allocate resources effectively, and implement targeted interventions to improve outcomes.
Data collection and analysis also enable organizations to benchmark their performance against industry standards, identify best practices, and learn from high-performing peers, further fueling their continuous improvement efforts.
Staff Training and Support
Successful CQI initiatives in healthcare require the active engagement and participation of healthcare professionals at all levels, from physicians and nurses to administrative staff and support personnel.
Building a culture of continuous improvement necessitates investing in staff training and support, empowering individuals to contribute to improvement efforts, and fostering a collaborative, interprofessional team approach.
Organizations can implement structured training programs to equip staff with the knowledge and skills required to understand and apply CQI methodologies, such as root cause analysis, process mapping, and data analysis techniques.
By cultivating a workforce that is well-versed in CQI concepts and committed to continuous learning, healthcare organizations can drive sustainable improvements, enhance patient experiences, and maintain a competitive edge in an ever-evolving industry.
Implementing Continuous Quality Improvement (CQI) in Organizations
Embarking on a Continuous Quality Improvement journey requires a strategic and comprehensive approach to ensure successful implementation and long-term sustainability.
Establishing a Continuous Quality Improvement Infrastructure
The first step in implementing CQI within an organization is to establish a robust infrastructure that supports and enables continuous improvement efforts.
This involves:
- Leadership endorsement and commitment: Gaining buy-in and active support from top leadership is crucial for driving organizational change and allocating the necessary resources for CQI initiatives.
- Stakeholder engagement and support: Engaging stakeholders, including employees, customers, suppliers, and partners, in the CQI process is essential for identifying improvement opportunities, gathering diverse perspectives, and fostering a sense of ownership and accountability.
- Dedicated resources: Allocating dedicated resources, such as a CQI team or department, budget, and specialized tools and technologies, demonstrates the organization’s commitment to continuous improvement and ensures sustained efforts.
- Communication and training: Implementing effective communication strategies and providing comprehensive training programs to educate employees on CQI principles, methodologies, and tools is crucial for ensuring widespread adoption and understanding.
By establishing a robust CQI infrastructure, organizations lay the foundation for a culture of continuous improvement, where every aspect of the organization is subject to ongoing evaluation and refinement.
Identifying Improvement Opportunities
Once the infrastructure is in place, the next step is to identify areas within the organization that present opportunities for improvement.
This can be achieved through:
- Benchmarking and gap analysis: Comparing the organization’s performance against industry best practices, standards, or high-performing peers can help identify areas where improvements are needed.
- Process mapping and analysis: Documenting and analyzing existing processes can reveal inefficiencies, bottlenecks, or opportunities for streamlining and optimization.
- Voice of the customer (VOC) analysis: Gathering and analyzing customer feedback, complaints, and preferences can provide valuable insights into areas that require improvement to enhance customer satisfaction and loyalty.
- Employee input and suggestions: Encouraging and actively soliciting input from employees, who have firsthand experience with processes and operations, can uncover valuable improvement opportunities.
- Setting measurable goals and targets: Establishing specific, measurable, achievable, relevant, and time-bound (SMART) goals and targets for improvement initiatives can help focus efforts and track progress effectively.
By leveraging these techniques, organizations can prioritize improvement opportunities, allocate resources effectively, and align their CQI efforts with strategic objectives and customer needs.
Sustaining Continuous Quality Improvement Efforts
Implementing CQI is an ongoing journey, not a one-time event. Sustaining continuous improvement efforts requires a long-term commitment and dedicated effort.
Key strategies for sustaining CQI within an organization include:
- Continuous monitoring and evaluation: Regularly monitoring and evaluating the progress and impact of improvement initiatives is essential for identifying areas that require further attention or adjustments.
- Celebrating successes and sharing best practices: Recognizing and celebrating successful improvement initiatives can help reinforce the culture of continuous improvement and motivate employees to actively participate.
- Embedding CQI into organizational processes: Integrating CQI principles and methodologies into core organizational processes, such as strategic planning, new product development, and operational management, ensuring that continuous improvement becomes ingrained in the organizational DNA.
- Fostering a culture of learning and innovation: Encouraging a mindset of continuous learning, experimentation, and innovation can help organizations stay agile and adapt to changing market dynamics, embracing new improvement opportunities as they arise.
By sustaining CQI efforts, organizations can continually refine their processes, enhance their offerings, and maintain a competitive edge in an ever-changing business landscape.
Future Trends and Challenges
As we look towards the future, it is clear that Continuous Quality Improvement will continue evolving before us.
New technologies and data insights will change the landscape of how organizations approach excellence.
Exciting tools like artificial intelligence, machine learning, and smart sensors connected by the internet offer great potential for enhancing existing CQI efforts.
Data and insights in real-time could provide a window into processes, customer behaviors and metrics like never before.
Predictive analysis may help foresee issues and bottlenecks to act beforehand. Continuous monitoring of operations could pinpoint inefficiencies or places for optimization.
However, taking advantage of these technologies is no simple task. Employees will need to learn new skills to work seamlessly with advanced tools.
Companies must develop strong frameworks to ensure data is handled properly. And new technologies must integrate smoothly into time-tested CQI methods already in place.
By facing challenges head-on and open-mindedly embracing emerging possibilities, organizations can stay at the forefront of driving growth, innovation and competitive edge through Constant Quality Improvement.
Positioning themselves for both today and tomorrow, they can continue their journey toward operational excellence.
SixSigma.us offers both Live Virtual classes as well as Online Self-Paced training. Most option includes access to the same great Master Black Belt instructors that teach our World Class in-person sessions. Sign-up today!
Virtual Classroom Training Programs Self-Paced Online Training Programs