What is Continuous Improvement in Manufacturing? Lean Manufacturing Techniques
Manufacturing organizations must consistently better output/quality/value to stay ahead of rivals. This endeavor is called continuous improvement in manufacturing. It’s become pivotal for factories worldwide.
Continuous improvement means using methods like Lean Production, Kaizen, Six Sigma, and Total Quality Management in a structured way. These aid in detecting and executing refinements.
Core aims involve optimizing techniques, truncating defects, wasting less, and boosting overall efficiency. It provides advantages – upgraded quality, lower expenses, swifter output, more delighted clients, and competitive edges.
Key Highlights
- Businesses always look for ways to refine how they make things. This is called “continuous improvement” in factories.
- It uses techniques like Lean Production, Kaizen, Six Sigma, and Total Quality Management. These tools aid in increasing proficiency.
- Main instruments embrace stream mapping, causal investigations, visual governance, mistake-proofedness, and others.
- The aim is to optimize techniques, upgrade quality, trim expenses, and boost client fulfillment.
- Continuous betterment in the long term determines triumph amid competition. It creates an environment of learning, problem-solving, and improvement.
What is Continuous Improvement in Manufacturing
To thrive amid competitive manufacturing, organizations understand perfecting processes forms a necessity.
This undertaken “continuous advancement” signifies techniques’ never-ending process to expel waste, refine quality, and boost efficiency company-wide.
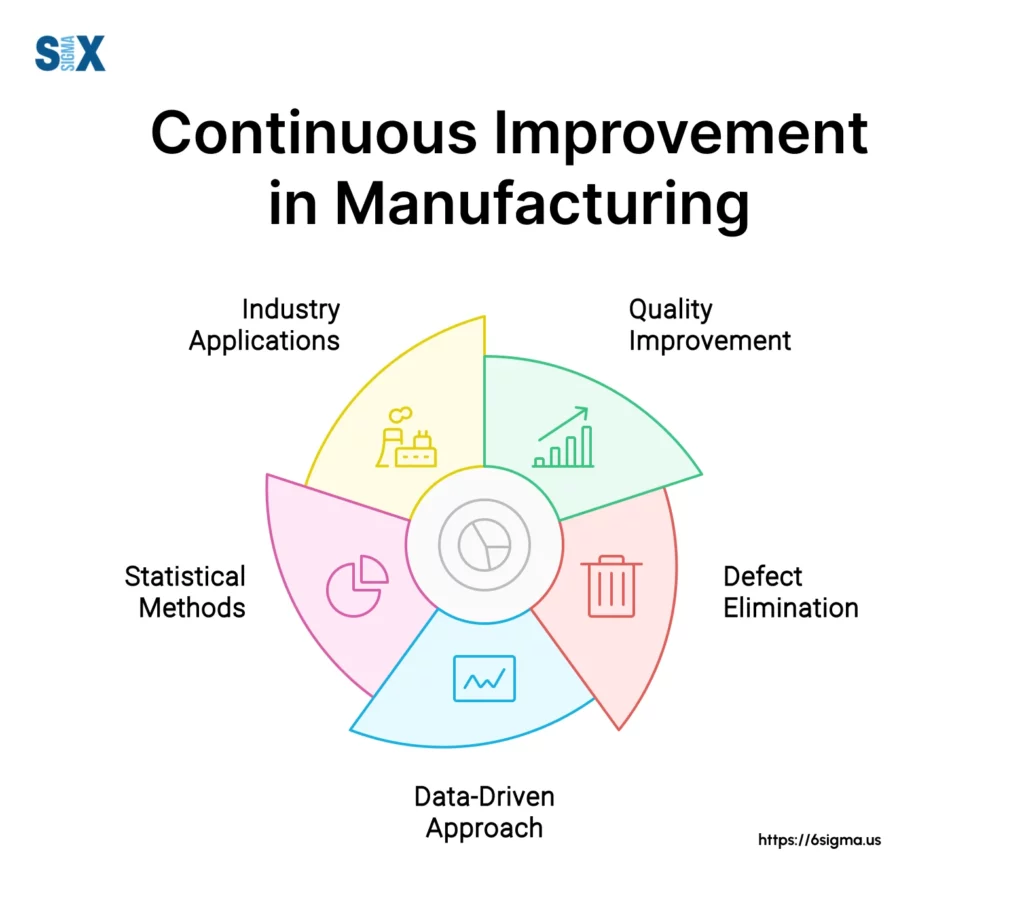
Management guides continual development’s belief encouraging innovations great or minor across operations. This attitude breeds problem-solving and perpetual growth.
Concepts like lean production, Kaizen, and Six Sigma seed continuous advancement philosophy. They synchronize minimizing wasted efforts and safely bolster yields.
By following steady refining models, manufacturers deduct costs, enhance sturdiness, maximize productivity, and satisfy buyers.
Lean Manufacturing and Kaizen Methodology
At the heart of continuous improvement in manufacturing lies the lean manufacturing philosophy and kaizen methodology. Lean manufacturing focuses on maximizing value for the customer while minimizing waste across the entire value stream.
It aims to create more efficient processes by identifying and eliminating non-value-added activities, overburden, and inconsistencies.
Kaizen, which means “change for the better” in Japanese, is the practice of continuous incremental improvement. It involves making small, gradual changes that compound into major process improvements over time.
The kaizen methodology encourages employees at all levels to identify opportunities for positive change and implement solutions, no matter how minor. Even tiny improvements can yield big results when sustained.
Key lean tools and concepts that enable kaizen include:
- Value Stream Mapping: This technique maps out the flow of materials and information required to bring a product to the customer, exposing areas of waste and opportunity.
- 5S Methodology: 5S (Sort, Straighten, Shine, Standardize, Sustain) creates and maintains an organized, clean, efficient workspace.
- Standard Work: Documented procedures capture the most efficient, waste-free way to perform a task so it can be consistently followed.
- Gemba Walks: Observing the actual work environment where value creation happens allows managers to identify areas for improvement.
Manufacturers can foster a culture of continuous process refinement and waste elimination by combining lean thinking with the kaizen philosophy of incremental progress.
Tools and Techniques for Continuous Improvement in Manufacturing
Continuous improvement in manufacturing relies on a variety of lean tools and techniques to identify and eliminate waste, streamline processes, and drive incremental enhancements. Some key tools and methodologies include:
Value Stream Mapping
Value stream mapping is a visual technique used to analyze the flow of materials and information in a manufacturing process.
By mapping out the entire value stream, areas of waste and inefficiency can be identified and targeted for improvement. Value stream maps help organizations visualize bottlenecks, excess inventory, unnecessary transportation, and other forms of waste.
Root Cause Analysis
When problems or defects arise, root cause analysis methods like the 5 Whys and fishbone diagrams help teams systematically identify the underlying sources rather than just addressing symptoms.
Getting to the true root causes allows for effective countermeasures to prevent issues from recurring.
Standard Work for Continuous Improvement in Manufacturing
Documenting precise work procedures and instructions through standard work ensures consistency and eliminates variation in how an operation is performed. Standard work forms the baseline for continuous improvement activities like kaizen events.
Gemba Walks
Gemba (meaning “the real place” in Japanese) walks involve managers and leaders going to the actual workplace to observe processes firsthand. Gemba walks allow issues to be directly witnessed and provide opportunities for process feedback from operators.
Poka-Yoke (Error-Proofing) for Continuous Improvement in Manufacturing
Poka-yoke involves techniques and devices for preventing errors or defects from occurring in a manufacturing process. Simple mechanisms like fixtures, guides, and sensors can “mistake-proof” operations by not allowing defective products to proceed.
5S Methodology
The 5S system (sort, set in order, shine, standardize, sustain) establishes a workplace suitable for visual control and lean production. An organized, clean, and standardized environment is the foundation for many other lean tools to function properly.
Quality Management and Six Sigma
Quality management is a critical aspect of continuous improvement in manufacturing. It involves implementing strategies, processes, and tools to meet or exceed customer expectations for product quality consistently.
Two major quality management methodologies are widely used in manufacturing: Six Sigma and Total Quality Management (TQM).
Six Sigma is a data-driven approach that aims to reduce process variation and defects. It follows the DMAIC (Define, Measure, Analyze, Improve, Control) methodology to identify and eliminate causes of errors or defects in processes.
By applying statistical analysis tools like process capability analysis and measurement systems analysis, Six Sigma drives process optimization and reduces variation to achieve higher-quality outputs with fewer defects.
Some key Six Sigma tools and concepts include:
- Voice of the Customer analysis to understand customer needs
- Critical to Quality (CTQ) metrics definition
- Process mapping to identify potential failure points
- Root cause analysis using techniques like 5 Whys and fishbone diagrams
- Statistical process control (SPC) to monitor processes
- Design of experiments (DOE) to test improvement ideas
Total Quality Management takes a broader approach focused on creating an organization-wide quality culture.
TQM principles emphasize leadership commitment, employee engagement, continuous improvement, customer focus, and an integrated system of tools and techniques. It drives quality through preventive actions rather than just defect detection.
Key aspects of TQM include:
- Top management leadership and quality policy deployment
- Employee training and involvement through quality circles
- Quality tools like process flowcharts, check sheets, histograms
- Emphasis on quality planning in the product/process design stage
- Supplier quality management through audits and ratings
- Customer satisfaction measurement and feedback loops
By integrating quality management philosophies like Six Sigma and TQM, manufacturers can foster a culture of continuous improvement aimed at delivering high-quality products and services that delight customers.
Maintenance and Equipment Reliability for Continuous Improvement in Manufacturing
Achieving continuous improvement in manufacturing requires having reliable, well-maintained equipment and processes.
Breakdowns, defects, and unplanned downtime can severely disrupt operations and hinder improvement efforts. As such, robust maintenance and equipment reliability programs are essential.
Total Productive Maintenance (TPM) is a methodology that engages operators in performing routine maintenance tasks and monitoring equipment health.
The goal is to maximize overall equipment effectiveness (OEE) by reducing six big losses: breakdowns, setup/adjustments, idling, reduced speed, process defects, and startup rejects.
TPM focuses on improving equipment design for easier maintenance, autonomous maintenance by operators, and maintenance prevention.
Visual management techniques like shadow boards and labeling make it easy to identify missing tools and keep workstations organized. Poka-yoke (error-proofing) devices detect abnormalities and prevent defects from being passed on.
Single Minute Exchange of Dies (SMED) reduces changeover times through streamlining and conversion to external setups.
Root cause analysis methods like the 5 Whys and fishbone diagrams help investigate the underlying sources of equipment failures and process problems.
This prevents simply treating symptoms and allows the implementation of robust countermeasures. Overall equipment effectiveness (OEE) is a key performance indicator that measures productivity losses from availability, performance, and quality issues.
By implementing rigorous maintenance processes, error-proofing, quick changeovers, and root-cause problem-solving, manufacturers can improve equipment reliability and uptime. This provides a stable base for driving continuous improvement in quality, productivity, and flow.
Lean Production Systems and Flow
Lean production systems and flow are critical components of continuous improvement in manufacturing. These systems aim to create a smooth, efficient flow of materials and information through the production process, minimizing waste and maximizing value for the customer.
Just-in-Time Manufacturing (JIT)
Just-in-Time (JIT) manufacturing is a lean production strategy that focuses on producing the right parts at the right time in the right quantities.
It involves synchronizing the flow of materials and information throughout the supply chain to minimize inventory levels and associated costs.
JIT relies on pull production, where downstream processes signal their demand to upstream processes, enabling a continuous flow of materials.
Continuous Flow for Continuous Improvement in Manufacturing
Continuous flow is the concept of arranging production processes in a smooth, uninterrupted sequence. It involves eliminating bottlenecks, reducing lead times, and minimizing work-in-process inventory.
Cellular manufacturing, where machines and workstations are arranged in a sequence that supports a smooth flow of materials, is a common approach to achieving continuous flow.
Takt Time
Takt time is the rate at which a product must be manufactured to meet customer demand. It synchronizes the pace of production with the rate of customer demand, ensuring that products are produced quickly (leading to excess inventory) and slowly (causing shortages).
Kanban System for Continuous Improvement in Manufacturing
The Kanban system is a lean production control mechanism that regulates the flow of materials and information through visual signals or cards.
It helps to maintain optimal inventory levels, prevent overproduction, and ensure that the right parts are produced at the right time and in the right quantities.
Single Minute Exchange of Dies (SMED)
SMED is a lean technique that focuses on reducing the time required to changeover or set up equipment for different product runs.
By minimizing changeover times, manufacturers can achieve smaller batch sizes, reduce inventory levels, and respond more quickly to changes in customer demand.
Value Stream Mapping (VSM)
Value stream mapping is a lean tool used to visualize and analyze the flow of materials and information throughout the entire production process.
It helps identify and eliminate non-value-adding activities, bottlenecks, and sources of waste, enabling a smoother and more efficient flow of materials.
Sustaining a Continuous Improvement Culture
While implementing lean tools and methodologies is crucial, sustaining a culture of continuous improvement is equally important for long-term success.
A continuous improvement culture empowers employees at all levels to identify opportunities for improvement, experiment with solutions, and drive positive change.
Leadership Commitment and Alignment
Executive leadership must be fully committed to continuous improvement and align the organization’s goals, strategies, and incentives to support it.
Leaders should visibly participate in improvement activities, such as Gemba walks, and provide the necessary resources and training.
Employee Engagement and Empowerment for Continuous Improvement in Manufacturing
Engage employees in the continuous improvement journey by providing training, encouraging idea submission, and recognizing contributions.
Empower employees to identify and resolve issues within their scope of influence. Create a blame-free environment that fosters open communication and learning from failures.
Structured Improvement Process
Establish a structured process for identifying, prioritizing, and implementing improvement opportunities.
This could involve regular kaizen events, value stream mapping exercises, or a formal suggestion system. Ensure improvements are data-driven and align with organizational goals.
Continuous Learning and Knowledge Sharing
Foster a culture of continuous learning by providing ongoing training, sharing best practices, and encouraging knowledge transfer across the organization. Capture lessons learned and success stories to reinforce the benefits of continuous improvement.
Performance Management and Recognition for Continuous Improvement in Manufacturing
Align performance management systems to incentivize and recognize continuous improvement efforts and results. Celebrate large and small successes to reinforce the desired behaviors and sustain momentum.
Continuous Monitoring and Adaptation
Regularly review and adapt the continuous improvement approach based on changing business needs, emerging technologies, and lessons learned.
Solicit feedback from employees and stakeholders to identify areas for improvement in the continuous improvement process itself.
SixSigma.us offers both Live Virtual classes as well as Online Self-Paced training. Most option includes access to the same great Master Black Belt instructors that teach our World Class in-person sessions. Sign-up today!
Virtual Classroom Training Programs Self-Paced Online Training Programs