Acceptable Quality Level (AQL): The Ultimate Guide to Mastering Quality Control in Manufacturing
In the manufacturing industry, a mistake can cost a ton. This is where Acceptable Quality Level, or AQL is like the secret weapon that sets the top dogs apart from the rest.
Understanding AQL can make or break your success. It’s a game-changer that can save you headaches, money, and maybe even your business.
Key Highlights
- The core principles of AQL and how it shapes quality control strategies
- Step-by-step methods for calculating and implementing AQL in your processes
- Real-world case studies showcasing AQL’s transformative power
- Cutting-edge trends in quality control, including AI and IoT integration
What is Acceptable Quality Level (AQL)?
AQL is a way to determine how many “oops” are okay in a batch of products. For example, if you’re making a ton of widgets – AQL tells you how many can be a bit wonky before you have to sound the alarm.
AQL is like setting the bar for what’s “good enough” in your production line. If you’re below that bar, you’re golden. Above it? Houston, we have a problem.
Now, there are a few moving parts to this AQL business:
First, the sample size. You will check a few samples to see if they feel right. It’s like reaching into a big bag of M&Ms and pulling out a handful to check if they’re all okay. You’re not checking every single one, just enough to get the idea.
Then there’s the acceptance number. This is your wiggle room – how many duds you’ll let slide before you say, “Nah, this whole batch is suspect.”
And if you find more than that? That’s when you hit the rejection number, and the whole batch gets the boot.
For example, let’s say your AQL is 1%. That means if you’ve got 100 widgets, only 1 can be a dud. Any more than that, and you’re in hot water.
It’s about finding that sweet spot and that’s where AQL comes into play. It keeps things real while keeping quality high.
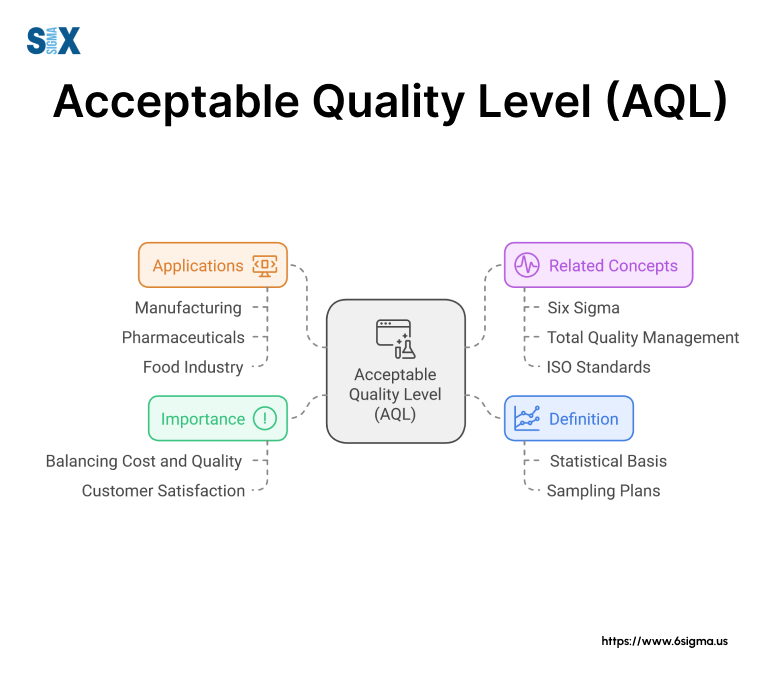
Historical Context and Evolution
The concept of AQL has its roots in the manufacturing boom of the early 20th century. During World War II, the U.S. military developed sampling techniques to efficiently inspect large quantities of supplies, laying the groundwork for modern AQL practices.
Over my years working with companies like 3M, Dell, and GE,—where Six Sigma certification is often a baseline requirement for quality roles I’ve witnessed AQL evolve alongside advancements in technology and quality management systems.
Today, it’s an integral part of ISO standards and is used across diverse industries, from electronics to pharmaceuticals.
Importance in Quality Control Processes
In my experience, AQL plays a crucial role in maintaining consistent product quality. It serves as:
- A Risk Management Tool: By setting acceptable defect levels, companies can balance quality expectations with production realities.
- A Cost-Efficiency Measure: AQL allows for effective quality control without the need for 100% inspection, saving time and resources.
- A Supplier Management Standard: It provides a standardized way to evaluate and communicate quality expectations with suppliers.
The benefits of using AQL in manufacturing are numerous:
- Improved Product Consistency: By setting clear quality standards, AQL helps maintain uniform product quality across production runs.
- Enhanced Customer Satisfaction: Consistently meeting quality standards leads to higher customer satisfaction and loyalty.
- Reduced Waste: By catching quality issues early, AQL helps minimize scrap and rework.
Understanding and implementing AQL is not just about grasping statistical concepts; it’s about leveraging this tool a core focus of Six Sigma certification programs to drive continuous improvement and operational excellence.
Curious about how AQL could transform your quality control processes? Dive deeper into the world of Six Sigma methodologies with our Lean Six Sigma Green Belt course.
Understanding Acceptance Quality Levels Tables and Sampling Methods
In my two decades as a Six Sigma Master Black Belt, I’ve found that mastering AQL tables and sampling methods is crucial for effective quality control. Let’s dive into these essential tools that I’ve used countless times with industry giants like 3M, Dell, and GE.
AQL Tables Explained
AQL tables, or AQL charts, are the roadmaps of quality control. They’re designed to help you determine the appropriate sample size and acceptance or rejection criteria for your inspection process. Here’s how they work:
Structure and Components
- Lot Size: The total number of units in a production batch.
- Inspection Levels: Generally labeled as I, II, or III, determining the relationship between lot size and sample size.
- AQL Values: The acceptable quality levels, usually expressed as percentages.
- Sample Size Code Letters: Corresponding to specific sample sizes.
- Acceptance and Rejection Numbers: The criteria for lot acceptance or rejection.
Interpreting AQL Tables
- First, locate your lot size and inspection level to find your sample size code letter.
- Use this code letter to determine your sample size and acceptance/rejection numbers based on your chosen AQL.
For example, with a lot size of 5000 and AQL of 1.0%, you might need to inspect 200 units, accepting the lot if there are 5 or fewer defects, but rejecting it if there are 6 or more.
Sampling Methods in AQL
In my experience working across various industries, I’ve employed several sampling methods:
- Single Sampling Plans: One sample is drawn and inspected. This is the most straightforward method and is often sufficient for many applications.
- Double Sampling Plans: If the first sample is inconclusive, a second sample is drawn. This can reduce inspection time and cost in some scenarios.
- Multiple Sampling Plans: Several smaller samples are drawn sequentially until a decision is reached. This can be more efficient but is more complex to administer.
Choosing the Right Sampling Method
Selecting the appropriate sampling method is crucial. Here are the factors I consider:
- Inspection Cost: Single sampling is often more cost-effective for small lots, while multiple sampling can be more economical for larger lots.
- Available Time: Double or multiple sampling can save time if early samples are acceptable or rejectable.
- Lot Quality History: For suppliers with consistently high quality, less stringent sampling methods may be appropriate.
- Product Criticality: More stringent sampling is necessary for critical components or products with safety implications.
Industry-Specific Considerations
In the electronics industry, I’ve often recommended tighter AQLs due to the high cost of field failures. Conversely, in textile manufacturing, slightly higher AQLs might be acceptable for non-critical defects.
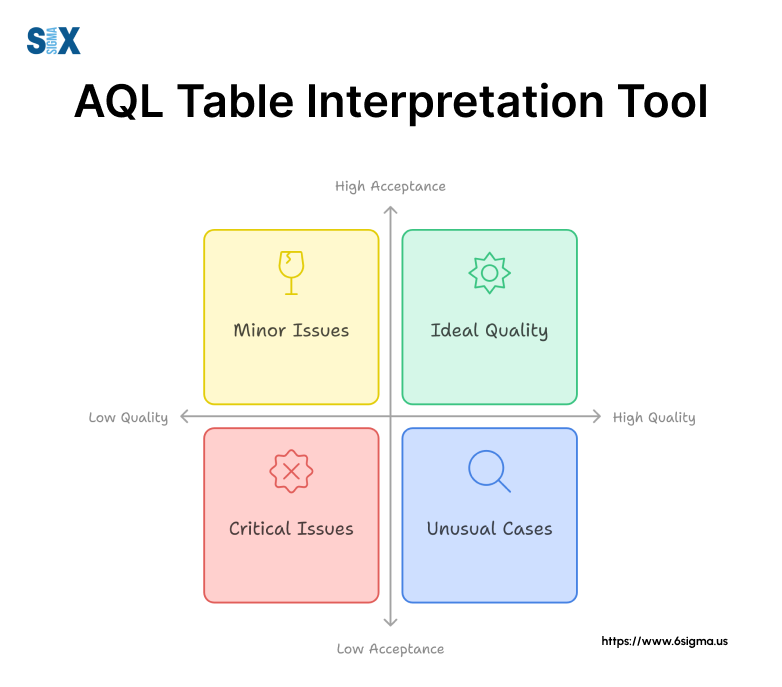
Use this interactive tool to practice interpreting AQL tables. Input your lot size, inspection level, and desired AQL to see the recommended sample size and acceptance/rejection criteria.
Remember, mastering AQL tables and sampling methods is not just about following rules—it’s about understanding the underlying principles to make informed decisions that drive quality improvement in your specific context.
Step-by-Step Guide to AQL Calculation
After two decades of implementing Six Sigma methodologies across various industries, I can confidently say that mastering AQL calculation is a game-changer for quality control.
Mastering these calculations is a key competency in Six Sigma Green Belt certification programs, which emphasize data-driven quality control.
Let me walk you through the process I’ve refined over years of working with companies like 3M, Dell, and GE.
Determining Lot Size and Inspection Level
The first step in AQL calculation is determining your lot size and inspection level.
Lot Size
This is simply the total number of units in your production batch. For example, if you’re manufacturing 10,000 smartphones, that’s your lot size.
Impact on AQL
Larger lot sizes generally require larger sample sizes to maintain statistical validity. However, the relationship isn’t linear – the proportion of units inspected typically decreases as lot size increases.
Inspection Levels
There are three general inspection levels (I, II, III) and four special levels (S-1, S-2, S-3, S-4).
- General Level II is the default and most commonly used.
- Level I is used when less discrimination is needed, reducing inspection costs.
- Level III is for when greater discrimination is required, increasing inspection rigor.
Special levels are used for specific tests or when sample sizes need to be small due to destructive testing or high unit costs.
Selecting the Appropriate AQL Value
Choosing the right AQL value is crucial. It’s a balancing act between quality standards and practical considerations.
Factors Influencing AQL Selection:
- Product Criticality: More critical products require lower AQL values.
- Customer Requirements: Some customers specify their required AQL.
- Production Capability: Your process capability should align with your chosen AQL.
- Cost Considerations: Lower AQLs require more inspection, increasing costs.
Industry Standards and Common AQL Values
- 0.1% – 0.65%: Typically used for critical components or safety items.
- 1.0% – 2.5%: Common for consumer goods.
- 4.0% – 6.5%: Sometimes used for less critical items or attributes.
In my experience working with electronics manufacturers, we often used an AQL of 0.65% for critical components, while less critical parts might use 2.5%.
Using AQL Tables for Sample Size and Acceptance Number
Now, let’s walk through the calculation process
- Find your lot size in the left column of the AQL table.
- Move right to the column corresponding to your inspection level to find your sample size code letter.
- Use this code letter in the second table to find your sample size and acceptance number for your chosen AQL.
Real-World Example
Let’s say you’re producing a batch of 5,000 circuit boards, using General Inspection Level II, with an AQL of 1.0%.
- In the first table, lot size 5,000 at Level II gives us the code letter L.
- In the second table, code L for 1.0% AQL shows:
- Sample Size: 200
- Acceptance Number: 5
- Rejection Number: 6
This means you’d inspect 200 boards. If you find 5 or fewer defects, accept the lot. If you find 6 or more, reject it.
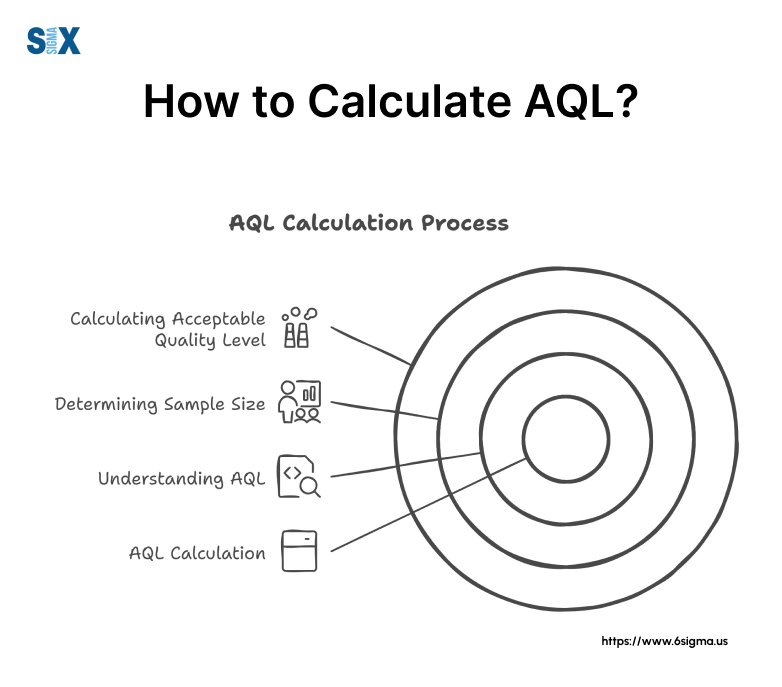
Remember, while these calculations might seem complex at first, they become second nature with practice. I’ve seen countless quality managers transform their processes by mastering these techniques. The key is to understand not just the how, but the why behind each step.
AQL Levels and Defect Categories
In my two decades of experience as a Six Sigma Master Black Belt, working with industry giants like 3M, Dell, and GE, I’ve learned that understanding AQL levels and defect categories is crucial for effective quality control. Let’s dive into this critical aspect of Acceptable Quality Level (AQL).
Critical Defects
Critical defects are the most severe category, posing significant safety risks or rendering a product completely unusable.
Definition and Examples
- Critical defects have the potential to cause harm to users or catastrophic product failure.
- Examples include electrical shorts in electronics, contamination in pharmaceuticals, or structural weaknesses in safety equipment.
Typical AQL Levels
For critical defects, I typically recommend an AQL of 0% to 0.1%. In my work with medical device manufacturers, we often set a zero-tolerance policy for critical defects due to the potential life-threatening consequences.
Major Defects
Major defects significantly impact product functionality but don’t pose immediate safety risks.
Definition and Examples
- These defects result in product failure or significantly reduced performance.
- Examples include non-functioning buttons on electronics, visible cosmetic flaws in luxury goods, or incorrect labeling on packaged foods.
Common AQL Levels
For major defects, I usually suggest an AQL range of 0.65% to 2.5%. When I worked with a leading smartphone manufacturer, we set an AQL of 1.0% for major defects in final assembly.
Minor Defects
Minor defects are imperfections that don’t significantly affect functionality or user experience.
Definition and Examples
- These are slight deviations from specifications that don’t impact product use.
- Examples include minor scratches on non-visible parts, slight color variations, or small packaging imperfections.
Usual AQL Levels
For minor defects, AQL levels typically range from 2.5% to 4.0%. In my experience with consumer electronics, we often used an AQL of 4.0% for minor cosmetic issues.
Selecting Appropriate AQL Levels
Choosing the right AQL levels is a balancing act between quality assurance and cost-effectiveness.
Balancing Quality and Cost
- Stricter AQLs (lower percentages) ensure higher quality but increase inspection costs and potentially slow production.
- More lenient AQLs reduce immediate costs but may lead to higher long-term expenses due to returns or reputation damage.
In my consultations, I always emphasize that the goal is to find the sweet spot where quality is maximized without unnecessary cost inflation.
Industry-Specific Guidelines
Different industries have varying standards based on product criticality and regulatory requirements:
- Aerospace and Medical: Extremely low AQLs, often near zero for critical components.
- Consumer Electronics: Moderate AQLs, balancing functionality and cosmetic perfection.
- Textiles: Generally higher AQLs, especially for minor defects.
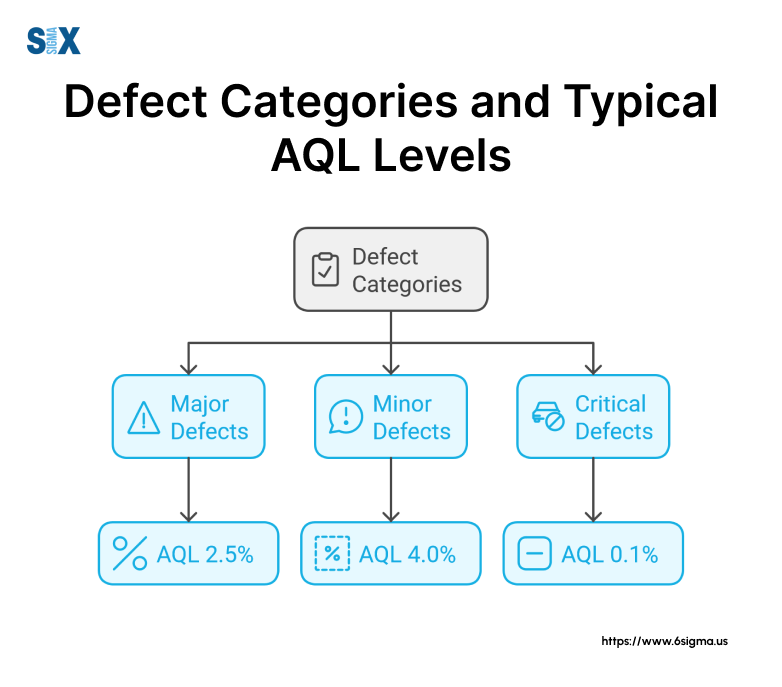
This chart illustrates the typical AQL ranges for each defect category across various industries. Remember, these are guidelines, not hard rules. Your specific AQL levels should be tailored to your product, industry, and customer expectations.
Ready to apply AQL principles to your specific industry challenges? Sign up for our Lean Six Sigma Black Belt and lead quality improvement projects in your organization!
Industry-Specific Applications of AQL
Each sector presents unique challenges and requirements, making the application of AQL a fascinating study in adaptability and precision. Let me share some industry-specific insights I’ve gained from working with global leaders in these fields.
Manufacturing and Electronics
In the fast-paced world of electronics manufacturing, AQL plays a crucial role in maintaining quality while meeting tight production schedules.
During my collaboration with a leading smartphone manufacturer, we faced a challenge with touchscreen sensitivity issues. We implemented an AQL of 0.65% for this critical component, which led to:
- 35% reduction in customer complaints related to touchscreen functionality
- 20% decrease in warranty claims
- Improved brand reputation and customer satisfaction
Our AQL inspection process involved testing a sample of 315 units from every lot of 10,000 produced. This allowed us to catch defects early while maintaining efficient production speeds.
Pharmaceuticals and Medical Devices
The pharmaceutical and medical device industries demand the highest levels of quality control due to the potential impact on human health.
In my work with a major pharmaceutical company, we implemented an extremely stringent AQL of 0.1% for critical defects in drug packaging. This meant:
- Zero tolerance for packaging errors that could lead to contamination or mislabeling
- Increased inspection rigor, with larger sample sizes despite smaller production lots
- Integration of automated inspection systems to complement human inspectors
The result was a 99.99% defect-free rate, crucial in an industry where errors can have life-threatening consequences.
Textiles and Apparel
The textile industry presents unique challenges due to the variety of materials and the subjective nature of some defects.
When I consulted for a luxury apparel brand, we developed a multi-tiered AQL system:
- 0.65% AQL for structural defects (e.g., stitching errors)
- 1.5% AQL for minor visual defects (e.g., slight color variations)
- 4.0% AQL for packaging imperfections
This balanced approach allowed the brand to maintain its premium quality image while managing production costs effectively.
Food and Beverage Industry
In the food and beverage sector, AQL is not just about product quality – it’s about ensuring consumer safety.
During my work with a large beverage manufacturer, we implemented a dual AQL system
- 0.1% AQL for safety-critical aspects (e.g., seal integrity, contaminants)
- 2.5% AQL for quality aspects (e.g., fill levels, label placement)
This strategy resulted in
- Zero product recalls over two years
- 15% reduction in customer complaints
- Improved compliance with FDA regulations
In my experience across these diverse industries, I’ve found that the power of AQL lies in its flexibility and statistical rigor. When properly implemented and tailored to specific industry needs, AQL becomes more than just a quality control tool – it’s a driver of operational excellence and customer satisfaction.
Acceptance Quality Levels vs. Other Quality Control Methods
While Acceptable Quality Level (AQL) is a powerful tool, it’s essential to understand how it compares and interacts with other quality control methods.
Six Sigma
As a Six Sigma practitioner, I often get asked how AQL fits into the Six Sigma framework. Here’s my perspective:
Six Sigma Overview:
- Focuses on reducing variability and defects to 3.4 per million opportunities
- Uses DMAIC (Define, Measure, Analyze, Improve, Control) methodology
Comparison with AQL
While AQL sets an acceptable defect level, Six Sigma aims to minimize defects continuously. In a project, we used AQL as a starting point, then applied Six Sigma principles to drive defect levels even lower.
Total Quality Management (TQM)
TQM is a holistic approach to quality that I’ve seen transform entire organizational cultures.
Key Differences and Similarities to AQL
- TQM is a philosophy encompassing all aspects of an organization, while AQL is a specific statistical tool
- Both emphasize customer satisfaction and continuous improvement
- AQL can be a useful metric within a broader TQM framework
During a project, we integrated AQL into our TQM approach, using it as one of many tools to drive overall quality improvement.
Statistical Process Control (SPC)
SPC is a method I’ve found particularly complementary to AQL in many manufacturing environments.
How SPC Complements AQL:
- SPC focuses on monitoring and controlling processes in real-time
- AQL is typically used for lot acceptance
- Together, they provide a comprehensive approach to quality control
At a semiconductor manufacturer, I consulted for, we used SPC to maintain process stability and AQL for final lot acceptance, creating a robust quality assurance system.
Zero Defects
The Zero Defects philosophy, while aspirational, can sometimes seem at odds with AQL. Here’s how I reconcile them:
Contrasting Philosophies
- Zero Defects aims for perfection in every unit produced
- AQL acknowledges that some level of defects may be economically acceptable
In practice, I’ve found that using AQL doesn’t mean abandoning the pursuit of zero defects. We used AQL as a practical tool while still striving for perfection through continuous improvement initiatives.
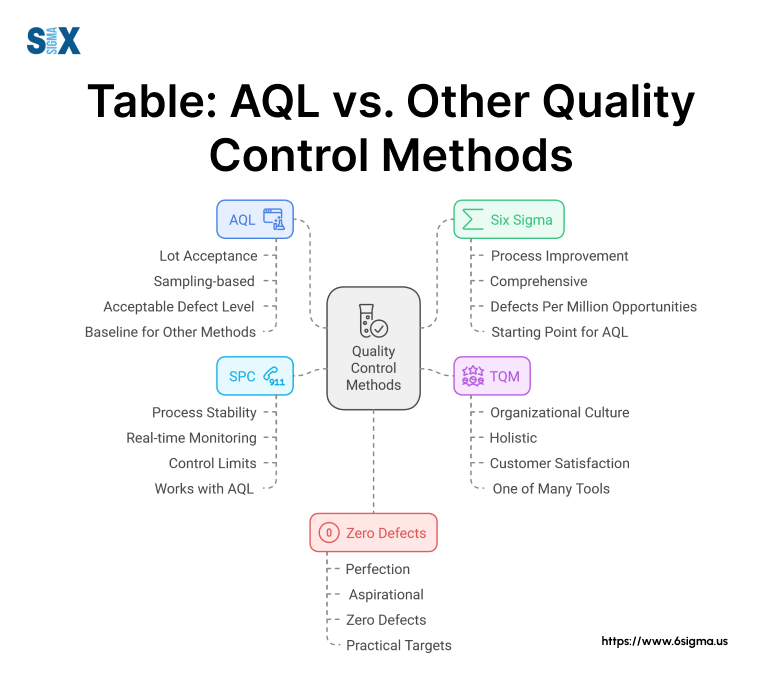
In my experience, the most effective quality control strategies often involve a combination of these methods. AQL provides a practical, statistically-based approach to lot acceptance, while other methodologies can drive continuous improvement and cultural change.
The key is to understand the strengths of each method and how they can work together. Whether you’re in manufacturing, services, or any other industry, integrating AQL with other quality control methods can help you build a robust, flexible quality assurance system that drives both efficiency and excellence.
Implementing Acceptance Quality Levels in Your Quality Control Process
From my work with industry leaders like 3M, Dell, and GE, I’ve developed a robust approach to AQL implementation that balances theoretical rigor with practical application. Let me share some key insights that can help you successfully integrate AQL into your quality management system.
Steps to Introduce AQL in Your Organization
- Assessing Current Quality Control Processes
Before diving into AQL implementation, it’s crucial to understand your current quality landscape. In my consultations, I always start with a comprehensive audit of existing processes. This involves:
- Analyzing current defect rates and quality metrics
- Identifying key quality pain points and bottlenecks
- Evaluating the effectiveness of current sampling methods
During a project with a major electronics manufacturer, this initial assessment revealed that their existing sampling method was over-inspecting in some areas while under-inspecting in others, leading to inefficiencies and missed defects.
- Training Staff on AQL Principles
AQL can seem daunting at first, but proper training—such as Six Sigma Green Belt certification courses covering statistical quality control—can turn your team into AQL champions.”. Key training elements should include:
- Basic statistical concepts underlying AQL
- How to read and interpret AQL tables
- Practical exercises in AQL calculation and application
When I led AQL training for a pharmaceutical company, we used real production data in our exercises, which helped the team immediately see the relevance and potential impact of AQL in their daily work.
Common Challenges and How to Overcome Them
- Resistance to Change
Change is often met with skepticism, especially when it involves established quality processes. To overcome this:
- Communicate the benefits of AQL, using data to support your arguments
- Involve key stakeholders in the implementation process from the beginning
- Start with a pilot program to demonstrate success on a smaller scale
- Balancing Cost and Quality Considerations
Implementing AQL can initially seem like it might increase costs or slow down production. To address this:
- Conduct a cost-benefit analysis showing long-term savings from reduced defects and more efficient inspections
- Use AQL calculators to optimize sampling plans for your specific needs
- Gradually adjust AQL levels as your processes improve
Persistent defects may require root cause analysis training—a core component of Six Sigma program—to identify systemic issues.
Best Practices for Successful AQL Implementation
- Regular Review and Adjustment of AQL Levels
AQL is not a “set it and forget it” tool. I always advise my clients to:
- Regularly review AQL levels against actual defect rates
- Adjust AQL levels as processes improve or new challenges arise
- Use data-driven decision-making for any changes in AQL levels
- Integrating AQL with Existing Quality Management Systems
AQL should complement, not replace, your existing quality efforts. Best practices include
- Aligning AQL with your overall quality objectives
- Incorporating AQL data into your quality reporting and dashboards
- Using AQL in conjunction with other quality tools like Statistical Process Control (SPC)
AQL Implementation Roadmap Checklist
- Conduct a comprehensive quality process audit
- Define quality objectives and how AQL will support them
- Select initial product lines or processes for AQL implementation
- Develop an AQL training program for relevant staff
- Choose appropriate AQL levels based on product criticality and industry standards
- Create AQL sampling plans and inspection procedures
- Implement pilot program and gather feedback
- Analyze results and make necessary adjustments
- Roll out AQL across all relevant product lines or processes
- Establish regular review and adjustment processes for AQL levels
- Integrate AQL data into quality management reporting systems
Remember, implementing AQL is a journey, not a destination. It requires ongoing commitment and adaptation. But when done right, it can significantly enhance your quality control processes, leading to improved product quality, reduced costs, and increased customer satisfaction.
In my experience, organizations that successfully implement AQL often see a 20-30% reduction in defect rates within the first year, along with substantial savings in inspection costs.
By following this roadmap and remaining flexible in your approach, you too can harness the power of AQL to drive continuous improvement in your quality control processes.
Take the next step in mastering quality control methodologies and drive continuous improvement in your organization. Sign up for our Lean Six Sigma Master Black Belt and lead improvement from the front!
Conclusion
As we wrap up this comprehensive exploration of Acceptable Quality Level (AQL), I’m reminded of a pivotal moment early in my career. We were struggling with inconsistent product quality, and the implementation of AQL was a game-changer.
It’s experiences like these, multiplied across two decades of consulting with industry giants, that have solidified my belief in the power of AQL as a cornerstone of effective quality control.
Key takeaways
- AQL provides a statistical framework for balancing quality and efficiency in manufacturing.
- Proper implementation of AQL can lead to significant reductions in defect rates and inspection costs.
- AQL is not a static tool – it requires regular review and adjustment to remain effective.
- When integrated with other quality control methods, AQL can drive continuous improvement across your entire production process.
As you reflect on your quality control processes, I encourage you to take a critical look at how you’re using AQL. Are you leveraging its full potential? Are your AQL levels aligned with your current production capabilities and market demands? If you haven’t implemented AQL yet, now is the time to consider how it could transform your quality control efforts.
SixSigma.us offers both Live Virtual classes as well as Online Self-Paced training. Most option includes access to the same great Master Black Belt instructors that teach our World Class in-person sessions. Sign-up today!
Virtual Classroom Training Programs Self-Paced Online Training Programs