8D Corrective Action: Mastering Problem-Solving for Continuous Improvement
Businesses constantly refine products, services, and workflows to stay ahead. But issues can still pop up, angering customers and jacking costs while hurting a company’s image. This is where the 8D corrective action problem-solving method earns its stripes.
It was developed by Ford in the 80s and has since spread widely across manufacturing, healthcare, aerospace, and more.
The 8D approach is a methodical process combining pros from different parts of the company, analytical tools, and fact-based decision-making.
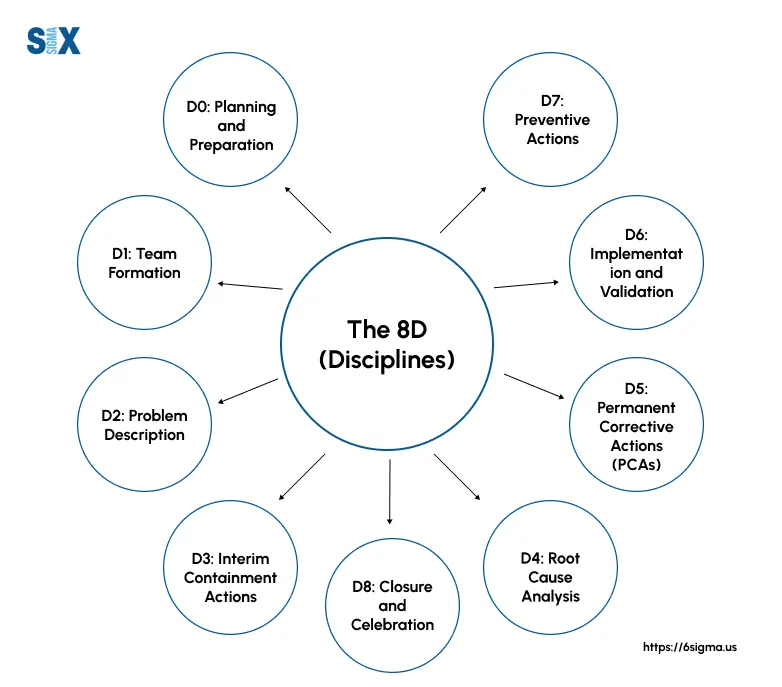
By following its eight systematic steps, organizations can expertly handle thorny problems. They uncover root causes and implement lasting fixes addressing immediate concerns while fueling constant upgrades to prevent repeat issues.
Key Highlights
- Understanding the origins and history of the 8D corrective action methodology, its benefits, and when to apply it for optimal results.
- Exploring the eight disciplined steps of the 8D corrective action process.
- Integrating the 8D methodology with quality management systems, leveraging Enterprise Quality Management Software (EQMS) to streamline workflows.
- Examining case studies and examples from various industries, including manufacturing, service, healthcare, and the automotive sector.
Understanding the 8D Corrective Action Problem-Solving Methodology
The Eight Disciplines (8D) methodology is a structured, team-based approach to problem-solving that aims to identify the root causes of issues and implement effective corrective actions.
It is a comprehensive framework that combines analytical tools, cross-functional collaboration, and a disciplined mindset to tackle complex problems systematically.
The 8D process establishes a step-by-step approach that guides organizations through eight distinct disciplines, each building upon the previous one.
Origins and History of 8D Corrective Action
The origins of the 8D methodology can be traced back to the 1980s when it was developed and pioneered by Ford Motor Company.
Initially referred to as “Team Oriented Problem Solving” (TOPS), this approach was designed to address the recurring quality issues that plagued the automotive industry at the time.
Recognizing the limitations of traditional problem-solving techniques, Ford sought to establish a more robust and effective framework that would not only resolve immediate concerns but also drive continuous improvement and prevent future issues.
The 8D methodology quickly gained traction within Ford and was subsequently adopted as the company’s primary approach for documenting and addressing problem-solving efforts.
As the benefits of the 8D corrective action process became evident, it rapidly gained popularity among other manufacturers and industries, transcending its automotive roots.
Today, the 8D methodology is widely employed across various sectors, including manufacturing, healthcare, aerospace, and service industries, among others.
Benefits of Using 8D Corrective Action
Implementing the 8D problem-solving methodology offers numerous benefits to organizations, including:
1. Systematic Approach: The structured nature of the 8D process ensures a consistent and comprehensive approach to problem-solving, reducing the risk of overlooking critical factors or jumping to premature conclusions.
2. Root Cause Identification: By emphasizing root cause analysis, the 8D methodology goes beyond addressing surface-level symptoms and focuses on identifying and eliminating the underlying causes of problems.
3. Cross-Functional Collaboration: The team-based approach fosters cross-functional collaboration, leveraging diverse perspectives and expertise from various departments, leading to more robust and well-rounded solutions.
4. Preventive Measures: The 8D corrective action process incorporates preventive actions to mitigate the recurrence of similar issues, promoting a culture of continuous improvement and proactive problem-solving.
5. Improved Quality and Reliability: By addressing root causes and implementing corrective actions, organizations can enhance the quality and reliability of their products, services, and processes, leading to increased customer satisfaction and cost savings.
6. Knowledge Sharing and Organizational Learning: The documentation and archiving of 8D processes facilitate knowledge sharing and organizational learning, enabling teams to build upon past experiences and lessons learned.
When to Apply 8D Corrective Action
The 8D problem-solving methodology is particularly valuable in situations where:
- Root Cause Analysis is Required: When issues persist despite initial troubleshooting efforts, or when the underlying causes are not immediately apparent, the 8D process can provide a structured approach to root cause analysis.
- Recurring Problems: If an organization experiences recurring problems or quality issues, the 8D methodology can help identify and eliminate the root causes, preventing future occurrences.
- Quality Issues with Significant Impact: When quality issues have a substantial impact on customer satisfaction, safety, regulatory compliance, or financial performance, the rigorous 8D approach can be employed to address the problem comprehensively.
- Complex Problems: For intricate problems involving multiple factors, processes, or departments, the cross-functional nature of the 8D team and the systematic approach can facilitate a thorough investigation and effective solution development.
By understanding the core principles, benefits, and appropriate application scenarios of the 8D problem-solving methodology, organizations can leverage this powerful framework to drive continuous improvement, enhance quality, and maintain a competitive edge in their respective industries.
The Eight Disciplines (8D) Process
At the heart of the 8D corrective action methodology lies a structured, step-by-step approach that guides organizations through eight distinct disciplines.
Each discipline builds upon the previous one, ensuring a thorough investigation, analysis, and resolution of the problem at hand.
The eight disciplines of the 8D process are designed to facilitate a systematic and disciplined approach to problem-solving, leveraging cross-functional collaboration, analytical tools, and data-driven decision-making.
D0: Planning and Preparation
Before embarking on the 8D corrective action journey, proper planning and preparation are crucial. This initial step, often referred to as Discipline Zero (D0), lays the foundation for a successful problem-solving effort.
During D0, the team gathers relevant information about the problem, assesses the need for interim containment actions, and establishes the prerequisites for forming an effective cross-functional team.
This stage involves collecting data on symptoms, identifying potential risks, and ensuring that the necessary resources and support are in place to execute the 8D process effectively.
D1: Team Formation
The first formal discipline of the 8D process focuses on assembling a cross-functional team with the collective knowledge, skills, and expertise required to tackle the problem at hand.
Effective team formation is critical to the success of the 8D corrective action effort, as it ensures diverse perspectives and a comprehensive understanding of the issue.
During D1, team members are carefully selected from various departments or functions, such as product engineering, process engineering, quality assurance, and data analysis.
Best practices in team formation involve considering factors such as technical expertise, problem-solving skills, interpersonal abilities, and the availability and commitment of potential team members.
Establishing ground rules, communication protocols, and team-building exercises can further enhance collaboration and effective teamwork.
D2: Problem Description
In Discipline 2, the team focuses on accurately describing the problem, utilizing quantitative data and evidence-based approaches.
This step is crucial, as it establishes a shared understanding of the issue and guides the subsequent steps of the 8D process.
The problem description involves defining the problem statement in specific, measurable terms, identifying the affected product or process, and quantifying the impact on operations, quality, customer satisfaction, and costs.
Tools such as the “5 Whys” technique, Ishikawa (fishbone) diagrams, and “Is/Is Not” analysis can aid in this process, helping to capture relevant details and categorize information.
D3: Interim Containment Actions
While the team works towards identifying and implementing permanent solutions, Discipline 3 focuses on implementing interim containment actions to mitigate the immediate impact of the problem and protect customers from further exposure.
Interim containment actions are temporary measures designed to isolate the problem and prevent it from causing further harm or spreading to other areas, processes, or products.
These actions may include segregating defective products, implementing additional inspections or checks, or introducing manual oversight until permanent corrective actions are in place.
It is essential to verify the effectiveness of interim containment actions and monitor their implementation to ensure that they are successful in containing the problem and minimizing its impact on operations and customers.
D4: Root Cause Analysis
At the core of the 8D corrective action process lies Discipline 4, which focuses on identifying the root causes of the problem through rigorous analysis and data-driven investigation.
This step is crucial, as it lays the foundation for developing effective and sustainable corrective actions.
During root cause analysis, the team employs various analytical tools and techniques, such as comparative analysis, fault tree analysis, and root cause verification experiments.
These methods help to isolate and verify the underlying causes of the problem, separating symptoms from true root causes.
Thorough documentation and verification of root causes are essential in this discipline, ensuring that the team has a solid foundation for developing effective corrective actions.
D5: Permanent Corrective Actions (PCAs)
Building upon the insights gained from root cause analysis, Discipline 5 focuses on selecting and verifying permanent corrective actions (PCAs) that address the identified root causes and mitigate the risk of future occurrences.
During this stage, the team evaluates potential corrective actions based on their effectiveness in addressing the root causes, as well as their feasibility, cost, and potential impact on other processes or systems.
Risk assessment tools, such as Failure Mode and Effects Analysis (FMEA), can aid in this evaluation process.
Once the most appropriate corrective actions have been selected, the team verifies their effectiveness through pilot testing, simulations, or other validation methods.
This step ensures that the proposed solutions will indeed resolve the problem and prevent its recurrence without introducing unintended consequences.
Detailed planning and documentation of the corrective actions, including acceptance criteria, implementation timelines, and responsibilities, are critical components of Discipline 5.
D6: Implementation and Validation
In Discipline 6, the team focuses on implementing the selected permanent corrective actions and validating their effectiveness in resolving the problem and preventing future occurrences.
This stage involves developing a comprehensive project plan that outlines the steps, timelines, and resources required for successful implementation.
Effective communication and coordination with all relevant stakeholders, including cross-functional teams and management, are essential to ensure a smooth transition and minimize disruptions.
During implementation, the team closely monitors the progress and performance of the corrective actions, gathering data and feedback to validate their effectiveness.
This validation process may involve conducting simulations, inspections, or collecting performance metrics to assess the impact of the implemented solutions.
If the validation process reveals any shortcomings or unintended consequences, the team may need to revisit the corrective actions, make adjustments, or conduct further root cause analysis to address any remaining issues.
D7: Preventive Actions
Discipline 7 of the 8D process focuses on taking preventive measures to ensure that the lessons learned and improvements made during the problem-solving journey are embedded into the organization’s processes, systems, and culture.
In this stage, the team reviews similar products, processes, or areas that could be affected by the same or similar root causes, identifying opportunities to apply preventive actions more broadly.
This proactive approach helps to mitigate the risk of future occurrences and promotes a culture of continuous improvement.
Effective implementation of preventive actions requires cross-functional collaboration, clear communication, and ongoing monitoring to ensure their sustained effectiveness.
D8: Closure and Celebration
The final discipline of the 8D process, D8, serves as a critical step in recognizing the team’s efforts, sharing lessons learned, and celebrating the successful resolution of the problem.
During this stage, the team conducts a final review of the problem-solving journey, documenting key lessons and insights that can be applied to future projects.
This documentation not only preserves institutional knowledge but also facilitates continuous improvement by enabling the organization to build upon past experiences.
Equally important is the recognition and celebration of the team’s achievements. By acknowledging the collective efforts, dedication, and collaboration of team members, organizations can foster a positive and supportive culture that values problem-solving and continuous improvement.
Formal recognition events, such as team presentations or awards ceremonies, can be organized to showcase the team’s accomplishments and highlight the impact of their work on the organization’s quality, customer satisfaction, and overall performance.
By completing the eight disciplines of the 8D process, organizations can effectively navigate complex problems, identify root causes, implement sustainable solutions, and establish a foundation for continuous improvement and organizational learning.
Integrating 8D Corrective Action with Quality Management Systems
While the 8D problem-solving methodology offers a robust framework for addressing quality issues and driving continuous improvement, its effectiveness can be further amplified by integrating it with an organization’s quality management systems.
Leveraging enterprise-level software solutions can streamline the 8D process, enhance collaboration, and foster a culture of continuous improvement.
The Role of EQMS in 8D Corrective Action
Enterprise Quality Management Software (EQMS) plays a pivotal role in supporting the successful implementation of the 8D corrective action methodology.
By utilizing an EQMS, teams can benefit from features such as:
- Standardized 8D Workflows: Pre-configured 8D workflows and templates ensure consistency and adherence to best practices, guiding teams through each discipline with clearly defined tasks, responsibilities, and timelines.
- Collaboration and Communication: EQMS platforms facilitate cross-functional collaboration by providing secure document sharing, real-time updates, and centralized communication channels, ensuring that all stakeholders remain informed and engaged throughout the 8D process.
- Data Management and Reporting: Comprehensive data management capabilities within an EQMS enable teams to easily capture, analyze, and report on quality data, facilitating data-driven decision-making and root cause analysis during the 8D process.
- Integration with Quality Systems: EQMS solutions often integrate with other quality management systems, such as corrective and preventive action (CAPA) systems, enabling seamless information sharing and ensuring that the insights gained from the 8D process are incorporated into broader quality improvement initiatives.
Automating 8D Corrective Action Workflows
One of the key advantages of leveraging an EQMS is the ability to automate 8D workflows, streamlining the process and reducing the administrative burden on teams.
Automated workflows also facilitate consistent documentation and record-keeping, which is essential for maintaining compliance with industry regulations and standards, as well as enabling knowledge sharing and organizational learning.
Data-Driven Decision-making
The 8D corrective action methodology heavily relies on data-driven decision-making, particularly during the root cause analysis and corrective action selection phases.
An EQMS provides teams with powerful data analysis and reporting capabilities, enabling them to quickly identify trends, patterns, and correlations that can inform their decision-making process.
Continuous Improvement Culture
Ultimately, the integration of the 8D methodology with an EQMS fosters a culture of continuous improvement within an organization.
The insights gained from the 8D process, coupled with the robust reporting and analytics capabilities of an EQMS, provide organizations with a wealth of data and knowledge that can be leveraged to drive ongoing process optimization and quality enhancement initiatives.
Case Studies and Examples of 8D Corrective Action
To illustrate the practical application and impact of the 8D problem-solving methodology, let us explore a few real-world case studies and examples from various industries.
These examples will showcase how organizations have successfully leveraged the 8D approach to address quality issues, resolve complex problems, and drive continuous improvement.
Manufacturing Quality Issues
In the manufacturing sector, where quality and reliability are paramount, the 8D methodology has proven invaluable in addressing a wide range of issues.
One notable example is a leading automotive parts manufacturer that faced recurring quality issues with a critical component, resulting in costly rework and customer dissatisfaction.
By implementing the 8D process, a cross-functional team was assembled to investigate the problem. Through root cause analysis, they identified a flaw in the supplier’s raw material handling processes, leading to inconsistencies in the component’s material properties.
The team implemented interim containment actions to segregate and inspect incoming materials, while also working with the supplier to implement permanent corrective actions, such as upgrading their material handling equipment and revising their quality control procedures.
Service Industry Applications of 8D Corrective Action
While the 8D corrective action approach is often associated with manufacturing, it has also proven valuable in the service industry, where quality and process excellence are equally critical.
A prominent financial institution faced challenges with excessive customer complaints related to billing errors and account discrepancies.
By implementing the 8D methodology, a cross-functional team analyzed the problem, identifying root causes such as outdated software systems, inadequate training for customer service representatives, and inefficient data entry processes.
The team implemented interim containment actions, including manual account audits and increased customer communication, while also developing permanent corrective actions, such as upgrading their billing software, revising training programs, and streamlining data entry procedures.
Healthcare and Life Sciences
In the healthcare and life sciences industries, where patient safety and regulatory compliance are paramount, the 8D methodology has proven invaluable in addressing quality issues and mitigating risks.
A prominent pharmaceutical company faced a recurring issue with contamination in one of its drug products, posing potential health risks and regulatory concerns.
By implementing the 8D corrective action process, a cross-functional team investigated the issue, identifying root causes related to inadequate environmental controls in the manufacturing facility and inconsistencies in the cleaning and sterilization procedures.
Interim containment actions included quarantining and recalling affected product batches, while permanent corrective actions focused on upgrading the facility’s HVAC systems, revising cleaning and sterilization protocols, and implementing enhanced environmental monitoring.
Automotive Industry (origin of 8D Corrective Action)
It is fitting to revisit the automotive industry, where the 8D methodology originated. In a recent case study, a major automaker faced recurring issues with engine failures in one of their popular vehicle models, leading to costly warranty claims and customer dissatisfaction.
By implementing the 8D process, a cross-functional team investigated the issue, identifying root causes related to a design flaw in the engine’s cooling system and inadequate testing procedures during the product development phase.
Interim containment actions included issuing technical service bulletins and providing temporary cooling system modifications for affected vehicles.
Permanent corrective actions focused on redesigning the engine’s cooling system, implementing more rigorous testing protocols, and enhancing communication between the engineering and manufacturing teams.
Through the 8D process and integration with their quality management practices, the automaker successfully resolved the engine failure issue, regained customer trust, and enhanced their overall product quality and reliability.
Conclusion
The 8D corrective action problem-solving method has proven extremely useful for handling thorny quality issues, continuously upgrading workflows, and cultivating an excellence culture in businesses.
By pairing its structured team approach with analytical tools and fact-based choices, the 8D process empowers companies to uncover root causes. It also helps implement lasting fixes and prevent repeating mistakes through establishing protective measures.
As the case studies and examples show, it’s been put to great use across many industries from manufacturing to healthcare where it originated in automotive.
Its flexibility and power have made 8D valued for boosting quality, improving customer satisfaction and staying ahead competitively no matter the market.
The Eight Disciplines methodology remains a strong tool for companies serious about excellence, innovation, and customer focus.
By wholeheartedly embracing this robust framework and blending it with modern quality practices, businesses can expertly handle complex problems. They can also unlock fresh opportunities and build the foundation for sustainable success.
In other words, don’t sleep on 8D corrective action problem-solving. Its fact-based, team-centric transformation approach strengthens any organization now and into the future.
SixSigma.us offers both Live Virtual classes as well as Online Self-Paced training. Most option includes access to the same great Master Black Belt instructors that teach our World Class in-person sessions. Sign-up today!
Virtual Classroom Training Programs Self-Paced Online Training Programs