Visual Management Techniques for Increasing Efficiency in the Workplace
Visual management, a cornerstone of lean manufacturing and continuous improvement methodologies, is a systematic approach to organizing and presenting information visually within a workplace.
It’s not just about hanging charts on walls; it’s a strategic tool that enhances transparency, facilitates real-time decision-making, and drives operational efficiency.
Key Highlights
- Visual management definition and workplace importance
- Essential components: 5S, KPIs, communication tools
- Kanban, Andon systems, and visual boards
- Lean manufacturing integration and visual factory creation
- Productivity, engagement, and problem-solving benefits
- Best practices for effective visual management
Introduction to Visual Management
Visual management is a powerful methodology that I’ve seen transform countless organizations throughout my career.
At its core, it’s a system of visual tools and cues designed to make the status of operations immediately apparent to all employees.
This transparency is crucial in today’s fast-paced business environment, where quick decision-making can make or break a company’s success.
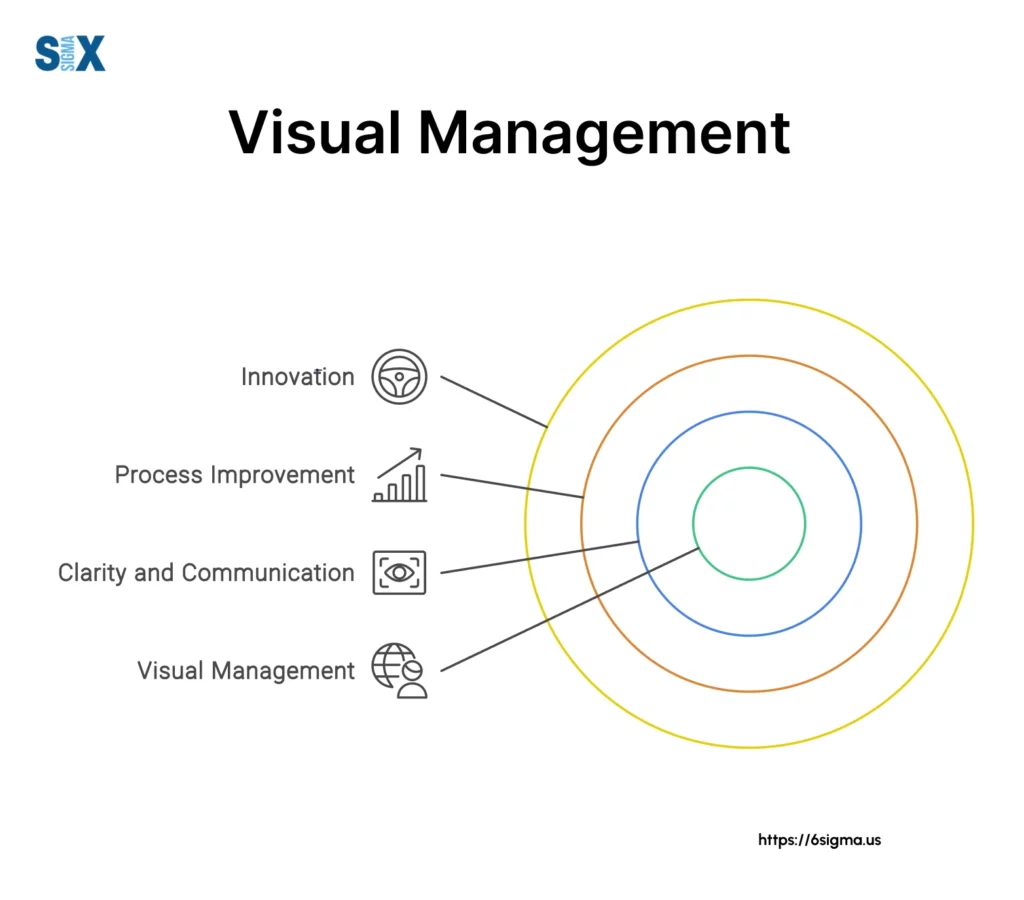
Importance in Modern Workplaces
In today’s complex manufacturing and business landscapes, visual management has become indispensable.
It bridges the gap between data and action, a crucial factor I’ve observed in my years of leading Six Sigma deployments.
By making information visible and accessible, it empowers employees at all levels to contribute to process improvement and problem-solving.
Moreover, in an era where operational efficiency is paramount, this serves as a cornerstone of lean manufacturing principles.
It facilitates continuous improvement by making abnormalities visible, allowing for quick corrective actions.
This alignment with lean principles is why I’ve consistently integrated visual management into Six Sigma certification programs and lean manufacturing workshops across the globe
Learn the concepts of visual management and transform your workflow with Lean Six Sigma Yellow Belt
Key Components of Visual Management
Organizing the workplace through the 5S methodology forms the foundation.
Visual Workplace Organization (5S Methodology)
The foundation of effective visual management lies in a well-organized workplace.
This is where the 5S methodology comes into play – a system I’ve successfully implemented in numerous manufacturing environments.
The 5S principles (Sort, Set in Order, Shine, Standardize, and Sustain) create a structured, clean, and efficient workspace that forms its bedrock.
In my experience at companies like GE and HP, implementing 5S has consistently led to reduced waste, improved safety, and increased productivity.
Visual Performance Metrics and KPIs
Key Performance Indicators (KPIs) are the lifeblood of any organization, and visual management brings these metrics to life.
Throughout my career, I’ve stressed the importance of displaying KPIs in a clear, visual format that’s easily understood by all employees.
Whether it’s production targets, quality metrics, or safety indicators, visual KPIs provide real-time feedback on performance.
This immediate visibility allows for quick adjustments and fosters a culture of continuous improvement – a key principle I’ve always emphasized in my Six Sigma training sessions.
Visual Communication Tools
Effective communication is crucial in any organization, and visual tools significantly enhance this process.
These tools break down communication barriers, ensuring that critical information is shared across all levels of the organization.
They promote transparency and alignment, which are essential for driving operational excellence.
Standard Work Procedures
Standardization is a key principle of lean manufacturing, and visual management plays a crucial role in maintaining and communicating standard work procedures.
Throughout my career, I’ve emphasized the importance of visually representing standard operating procedures (SOPs) through charts, diagrams, and instructional visuals.
By making SOPs visual and easily accessible, we ensure consistency in operations, reduce errors, and facilitate training of new employees.
This visual approach to standardization has been a game-changer in many of the international projects I’ve led.
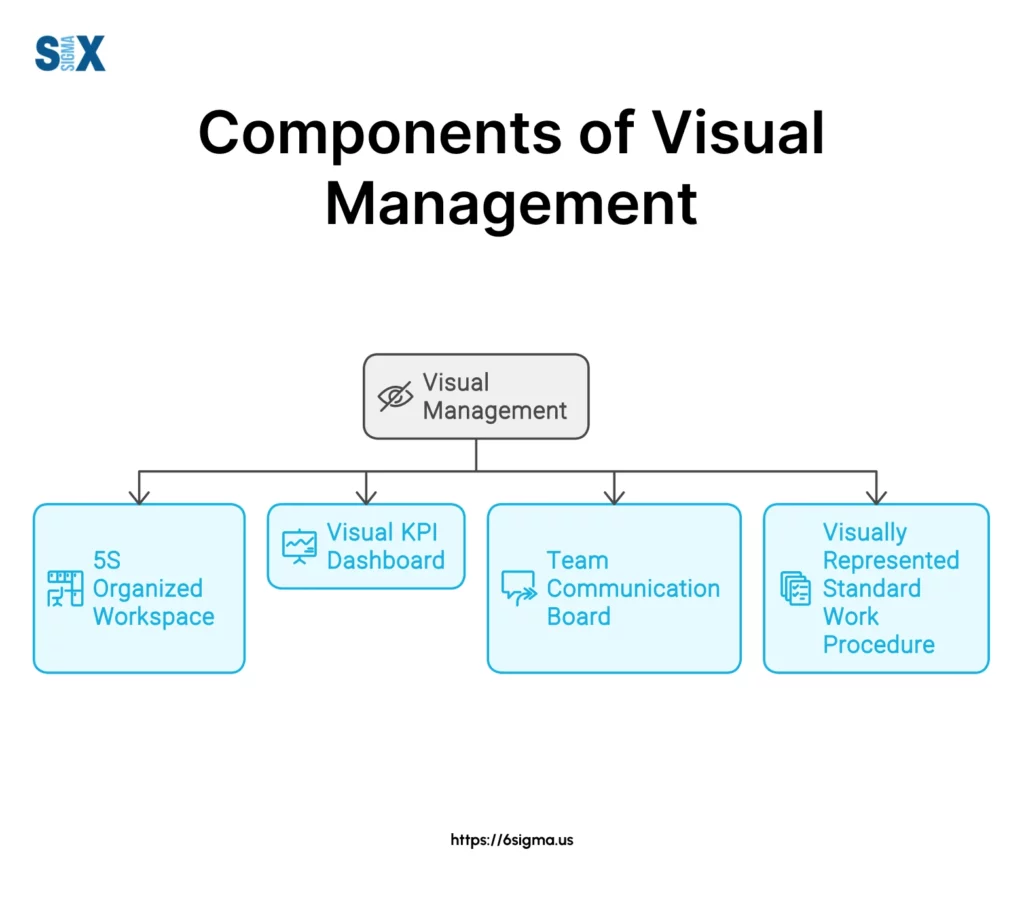
Discover the essentials of visual management components in detail, and enhance your efficiency today with Lean Six Sigma Green Belt
Visual Management Tools and Techniques
A variety of tools and techniques form the backbone of visual management systems.
Kanban Boards for Workflow Management
Kanban boards have been a staple in my toolkit for visual workflow management.
These simple yet powerful tools provide a visual representation of work in progress, helping teams manage their workload and identify bottlenecks.
In my experience implementing Kanban systems at companies like Dell and Seagate, I’ve seen significant improvements in process flow and team productivity.
The beauty of Kanban lies in its simplicity and flexibility.
Whether it’s a physical board with sticky notes or a digital version, Kanban provides a clear picture of work status, facilitating better resource allocation and workflow optimization.
Andon Systems for Real-time Problem Signaling
Andon systems are another critical components that I’ve frequently implemented in manufacturing environments.
These visual alert systems provide real-time signaling of problems or abnormalities in the production process.
During my tenure at 3M, we implemented Andon lights and boards across several production lines.
The impact was immediate – issues were identified and addressed faster, leading to reduced downtime and improved quality.
Andon systems embody the principle of making problems visible, a cornerstone of lean manufacturing and continuous improvement.
Visual Management Boards
Visual management boards are versatile tools that I’ve used extensively in various contexts, from factory floors to office environments.
These boards serve as central hubs of information, displaying everything from production metrics to improvement initiatives.
In my workshops on Statistical Process Control and Business Process Charting, I always emphasize the power of well-designed boards.
They facilitate daily stand-up meetings, track progress towards goals, and serve as focal points for continuous improvement efforts.
Information Displays and Dashboards
In today’s data-driven world, effective information displays and dashboards are crucial.
These dashboards, whether physical or digital, consolidate critical information into an easy-to-understand format.
They enable quick decision-making and help align the entire organization towards common goals.
In my experience, well-designed dashboards can significantly enhance operational visibility and drive performance improvement.
Implementing Visual Management in Manufacturing
Integrating it into manufacturing environments requires a strategic approach.
Lean Manufacturing Principles and Visual Management
Visual management and lean fundamentals are intrinsically linked, a synergy I’ve leveraged throughout my career in process improvement
Lean principles such as waste reduction, continuous flow, and pull systems are all supported and enhanced by effective visual management.
Creating a Visual Factory
The concept of a visual factory is one that I’ve championed in numerous manufacturing environments.
A visual factory is one where the state of processes, performance metrics, and problems are immediately visible to all.
Creating a visual factory involves strategically implementing visual tools throughout the facility.
This might include color-coding, floor markings, visual work instructions, and prominently displayed performance metrics.
Process Optimization Through Visual Controls
Visual controls are powerful tools for process optimization, a topic I frequently cover in my Six Sigma and lean manufacturing workshops.
These controls can range from simple color-coding systems to more complex boards.
By implementing visual controls, we make process standards clear and deviations immediately apparent. This visibility is crucial for maintaining process stability and driving continuous improvement.
Throughout my career, I’ve seen how effective visual controls can reduce errors, improve quality, and enhance overall process performance.
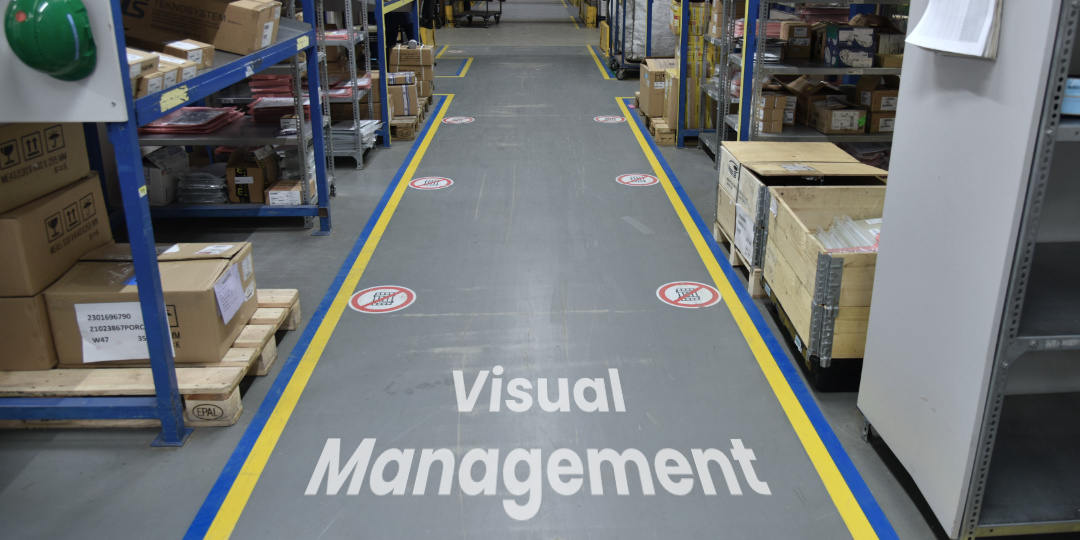
Benefits of Visual Management
Visual management offers numerous advantages, from increased productivity to enhanced employee engagement.
Improved Productivity and Waste Reduction
One of the most significant benefits of visual management is its impact on productivity and waste reduction.
By providing clear, real-time information about work status, performance, and issues, it enables quicker decision-making and problem-solving.
This leads to improved efficiency and reduced waste – key outcomes that I’ve helped numerous organizations achieve through its implementation.
Enhanced Employee Engagement and Empowerment
Visual management is a powerful tool for fostering employee engagement and empowerment.
By making information accessible to all, it creates a sense of ownership and involvement among employees at all levels.
When employees can see the impact of their work and understand how it fits into the bigger picture, they become more engaged and proactive in driving improvements.
Faster Problem Identification and Resolution
Perhaps one of the most valuable benefits is its ability to facilitate rapid problem identification and resolution.
By making abnormalities immediately visible, this enables teams to address issues quickly before they escalate.
This aligns closely with the principles of Statistical Process Control that I’ve taught in numerous workshops where root cause analysis training is often paired with visual management strategies.
Visual management provides the tools to detect process variations early, allowing for prompt corrective actions and continuous improvement.
Best Practices in Visual Management
Effective visual management requires careful design, consistent maintenance, and ongoing evaluation.
Designing Effective Visual Aids
Designing effective visual aids is crucial for the success of any visual management system.
Throughout my career, I’ve emphasized the importance of creating visual tools that are clear, concise, and relevant to the specific needs of the organization.
Key considerations include using consistent color coding, ensuring information is up-to-date and accurate, and making sure visual aids are placed where they’re most needed.
The goal is to create visual tools that communicate critical information at a glance, facilitating quick understanding and decision-making.
Maintaining Up-to-date Visual Information
One of the biggest challenges in this is keeping information current.
Outdated information can lead to confusion and erode trust in this system.
In my Six Sigma deployments and lean manufacturing initiatives, I’ve always stressed the importance of establishing clear processes for updating visual information.
This might involve assigning responsibility for updates, setting regular review schedules, and leveraging technology to automate data updates where possible.
The key is to ensure that visual management tools always reflect the current state of operations.
Continuous Evaluation and Improvement of Visual Management Systems
Like any business process, visual management systems should be subject to continuous evaluation and improvement.
This aligns with the Plan-Do-Check-Act cycle that I’ve applied in numerous process improvement projects throughout my career.
Regular audits, soliciting feedback from users, and staying abreast of new technologies are all crucial for maintaining a robust system.
As business needs evolve, so too should this system to ensure it continues to deliver value.
Conclusion
As we’ve explored throughout this article, visual management is a powerful methodology that can transform how organizations operate.
From improving productivity and reducing waste to enhancing employee engagement and facilitating faster problem-solving, the benefits are far-reaching.
Future Trends in Visual Management
Looking ahead, I see exciting developments on the horizon.
The integration of digital technologies, such as IoT sensors and augmented reality, promises to take it to new heights.
Professionals seeking to stay ahead in this evolving landscape should consider advanced Six Sigma certifications that integrate these emerging technologies
SixSigma.us offers both Live Virtual classes as well as Online Self-Paced training. Most option includes access to the same great Master Black Belt instructors that teach our World Class in-person sessions. Sign-up today!
Virtual Classroom Training Programs Self-Paced Online Training Programs