Project Quality Management. Techniques, Key Concepts, and More
Project quality management is an important process that makes sure projects hit the targeted quality levels, meet all the must-have needs, and live up to what’s expected.
Reliably shipping top-quality products and services is critical for companies to come out on top and stay ahead of the competition.
It involves using a complete set of methods, tools, and techniques throughout a project’s lifecycle to achieve the desired quality goals.
Managing quality in projects isn’t just about fixing defects—it’s a proactive deal focused on preventing issues before they even happen.
By properly deploying quality practices, organizations can boost customer satisfaction, cut back on re-doing work and the associated costs, streamline project workflows, and overall raise the chances of project success in the long run.
Key Highlights
- Project quality management makes sure project results hit the quality targets and criteria needed. It revolves around quality planning, assurance, control, and constant upgrading throughout the project timeline.
- When done right, it boosts customer satisfaction, cuts back on re-doing work and associated costs, and increases the chances of project success in the long haul.
- Key phases involve planning for quality, making sure quality plans are followed, quality control, and quality improvements.
- Quality management leverages various aids and techniques like quality audits, control charts, checklists, and metrics.
- Challenges can include shifting requirements, not enough resources, and pushback to quality processes.
- Never-ending improvement, training everyone involved, and adopting leading quality practices are crucial for sustaining things in the long run.
- The core goal remains delivering to customers on time, on budget, meeting all needs—and doing it with a quality effort from beginning to end.
What is Project Quality Management?
Project quality management is super important for ensuring projects finish as planned while meeting all expectations.
It revolves around proactively planning, monitoring, and controlling quality throughout the project timeline to deliver results that line up with what was defined upfront in terms of specs and standards.
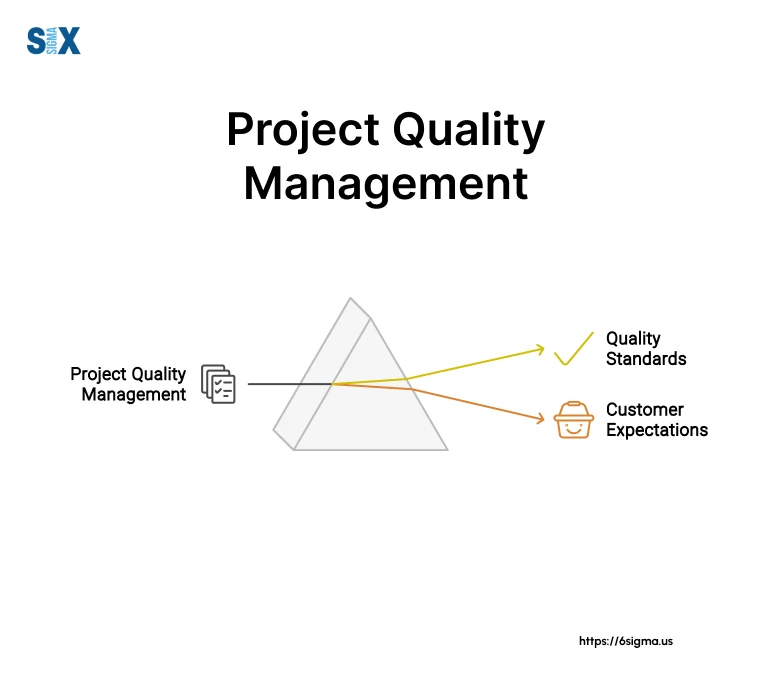
Essentially, it aims to foresee and sidestep defects, errors, or non-compliance rather than just inspecting after the fact to find issues.
With quality management practices in play, teams can reduce re-works, lower costs, streamline processes, and increase customer satisfaction.
For example, teams led by Six Sigma-certified certification often see accelerated improvements in defect prevention and process efficiency due to the methodology’s data-driven focus.
It covers several core aspects like quality planning, assurance, control, and constant upgrading.
Effective project quality demands a methodical approach to engaging the full team, stakeholders, and subject matter experts.
It also means setting clear policies, procedures, and metrics around quality plus nurturing an organization-wide focus on quality and never-ending improvement.
The end goal is reliably providing what was promised, when it was promised, at the expected level of quality—and quality management gets you there.
Project Quality Planning
Project quality planning is a crucial first step in implementing an effective quality management approach for any project.
It involves defining the quality standards, metrics, and processes that will be used to ensure the project deliverables meet the required specifications and stakeholder expectations.
During this phase, the project team should establish a quality management plan that outlines the following key elements:
Quality Metrics and Standards
Identify the specific quality metrics and standards that will be used to measure and evaluate the quality of the project deliverables. This could include industry regulations, client requirements, internal organizational standards, or best practice benchmarks.
Quality Roles and Responsibilities within Project Quality Management
Clearly define the roles, responsibilities, and authorities related to quality management on the project. This includes identifying the quality assurance team or personnel responsible for conducting reviews, inspections, and audits.
Quality Control Processes
Determine the quality control processes that will be implemented, such as peer reviews, testing strategies, checklists, and inspection procedures.
These processes help detect and prevent defects early in the project lifecycle.
Quality Assurance Activities within Project Quality Management
Outline the quality assurance activities that will validate whether the quality requirements are being met. This could include audits, quality gate reviews, acceptance criteria, and sign-off procedures.
Quality Improvement Methods
Establish continuous improvement methods, such as root cause analysis, corrective/preventive actions, and lessons learned sessions. This enables the team to identify areas for enhancing quality processes iteratively.
Quality Assurance in Projects
Quality assurance is a crucial aspect of project quality management. It refers to the planned and systematic activities implemented to ensure that the project will satisfy the relevant quality standards.
Quality assurance spans the entire project lifecycle from initiation through planning, execution, monitoring, and closure.
The main goals of quality assurance in projects are:
- Prevent defects and errors from occurring in the first place by following proven processes, best practices, and quality standards.
- Provide confidence that quality requirements will be met by adhering to organizational quality policies, principles, and procedures.
- Continuously improve processes, and deliverables and increase efficiency by identifying areas for enhancement.
Some key quality assurance processes used in projects include:
Quality Audits – Periodic formal reviews to evaluate whether project activities comply with organizational and project policies, processes, and procedures.
Process Improvement – Identifying, analyzing, and improving processes to maximize efficiency and minimize errors/defects.
Quality Control – Inspection activities focused on identifying defects in deliverables.
Quality assurance requires an emphasis on continuous process improvement throughout the project.
Processes should be regularly reviewed and optimized based on lessons learned, best practices, and quality metrics/measurements.
Project Quality Management Tools and Techniques
Effective project quality management relies on utilizing the right tools and techniques throughout the process. There are many quality management tools and methodologies that teams can leverage to plan, monitor, control, and improve the quality of their projects.
Cause and Effect Diagrams
Cause and effect diagrams, also called fishbone or Ishikawa diagrams, are visual tools used to identify potential causes of quality issues or defects.
They allow teams to explore all the possible root causes related to materials, methods, measurements, environment, people, and machines that could be contributing to a quality problem.
Control Charts
Control charts are used to monitor and control quality performance over time. They provide a way to study how processes change over time by displaying upper and lower statistical control limits derived from data.
Control charts help identify trends and signals that a process is becoming unstable or going out of control.
Flowcharts
Flowcharts map out and document the logical sequence of steps in a process. Creating a flowchart of a process helps teams visualize the workflow, identify potential failure points or bottlenecks, and look for areas to streamline for quality improvement.
Checklists
Quality checklists provide a structured way to ensure consistency and completeness in carrying out a task or process.
They define the specific quality requirements, components, or steps that should be verified. Checklists are useful tools for inspections, reviews, audits, and testing activities.
Histograms
A histogram is a graphical tool that displays the distribution of data by arranging it into columns or bars.
Quality teams can use histograms to see patterns, spread, and skewness in variables like defects, delays, or process measurements. This helps identify areas that need improvement.
Pareto Charts
The Pareto principle states that 80% of consequences come from 20% of causes. Pareto charts order potential causes from highest contribution to lowest contribution. This allows teams to prioritize and focus on addressing the most critical causes of defects or issues.
Six Sigma
Six Sigma is a data-driven quality management methodology that aims to improve processes by reducing defects and variability. It utilizes statistical tools like control charts, cause and effect diagrams, and process capability analysis to achieve very high-quality performance.
Organizations often prioritize hiring or upskilling employees with a Six Sigma certification, as these professionals are adept at applying statistical tools like process capability analysis to achieve near-perfect quality outputs.
Total Quality Management (TQM)
TQM is a philosophy and set of management practices centered around putting quality at the core of an organization’s culture and activities.
TQM’s focus on waste reduction aligns closely with Lean fundamentals, which complement Six Sigma to create a holistic quality framework
It emphasizes customer satisfaction, continuous improvement, defect prevention over detection, and the involvement of all employees in quality efforts.
Implementing Project Quality Management
Successfully implementing quality management on a project requires careful planning and execution across all phases. Here are some key steps involved:
Define Quality Standards and Metrics
At the outset, it’s critical to establish clear quality standards, goals, and metrics that align with the project objectives and requirements. This could involve adherence to industry regulations, meeting client specifications, or achieving performance benchmarks. Quantifiable metrics allow you to measure and analyze quality performance.
Develop a Project Quality Management Plan
A comprehensive quality management plan outlines the processes, resources, roles, and responsibilities for ensuring quality throughout the project lifecycle. It details quality assurance and control activities, tools/techniques to be used, reporting protocols, and acceptance criteria.
Allocate Necessary Resources
Ensure you have adequate resources – personnel, budget, technology tools, training, etc. – dedicated to quality management efforts. This could involve hiring quality specialists, investing in quality management software, and providing training to the project team.
Implement Quality Assurance Processes
Quality assurance processes like process audits, peer reviews, inspection, and testing need to be built into every phase – planning, execution, monitoring, and control. Preventive actions during development can catch issues early before they become costly defects.
Perform Continuous Quality Control in Project Quality Management
Quality control involves monitoring outputs, conducting inspections, testing deliverables against requirements, and recording quality data. Control charts, cause analysis, and other QC techniques identify areas requiring corrective actions.
Establish Clear Roles and Accountability
Delineate quality roles like quality manager, assurance auditors, and control inspectors across different levels. Make quality everyone’s responsibility by building it into processes, standards, and the overall culture.
Leverage Quality Management Tools
A variety of tools support quality management – QMS software, process modeling, statistical analysis, defect tracking, requirements traceability matrices, and more. The right tools enhance visibility and control.
Conduct Quality Reviews and Audits within Project Quality Management
Schedule regular quality reviews, audits, and inspections at strategic points. These verify adherence to processes/standards and identify areas for improvement. Management quality audits assess the overall effectiveness of the QM system.
Implement Corrective/Preventive Actions
Based on quality data, reviews, and audits, promptly execute corrective actions to address non-conformances and preventive actions to preclude potential issues. Continuous improvement is key.
Capture Lessons Learned
At project closure, thoroughly document quality management successes, challenges, and lessons learned to improve future efforts. An experienced quality team is an asset.
Benefits and Challenges of Project Quality Management
Implementing an effective project quality management process provides many important benefits, but also comes with some challenges that must be addressed.
Benefits
Improved Customer Satisfaction – By focusing on quality throughout the project lifecycle, you deliver a final product/service that meets or exceeds customer requirements and expectations. This leads to higher customer satisfaction.
Cost Savings – Catching and fixing defects early through quality assurance activities is much less costly than addressing issues later. Quality management helps avoid expensive rework and delays.
Increased Efficiency – Having standardized quality processes, templates, and tools in place streamlines activities and reduces wasted effort. Team members understand what is expected.
Competitive Advantage – Delivering a consistently high-quality product/service helps differentiate your organization and build a reputation for excellence.
Risk Mitigation – Quality risk management identifies potential threats to quality upfront so preventive actions can be taken to avoid or mitigate those risks.
Continuous Improvement – Quality management promotes an environment of continuous process improvement by capturing lessons learned and best practices.
Challenges
Culture Shift – Implementing quality management may require a shift in the project team and organizational culture to emphasize quality over just delivery speed.
Initial Investment – There are upfront costs for developing quality processes, training team members, acquiring tools, and getting certified.
Maintaining Processes – Quality processes must be continuously updated and refined based on feedback. This requires an ongoing investment of time and resources.
Integration Across Teams – Getting all project teams aligned and following the defined quality management processes can be difficult, especially in large organizations.
Resistance to Change – Some team members may be resistant to new quality processes they perceive as bureaucratic overhead.
Quality Data Challenges – Collecting, analyzing, and consistently reporting on quality metrics across projects can be complex.
Continuous Improvement in Project Quality Management
Project quality management is not a one-time effort, but rather an ongoing process of continuous improvement. Even after implementing quality management practices, it’s essential to regularly review and enhance the processes to drive better results consistently.
The core principle of continuous improvement is to identify areas for optimization, implement changes, monitor the impact, and make further adjustments as needed.
This cyclical approach ensures that quality management practices remain relevant, efficient, and aligned with evolving project requirements, industry standards, and best practices.
Some key aspects of continuous improvement in quality management include:
Quality Audits and Reviews
Conducting regular quality audits and retrospective reviews allows teams to assess the effectiveness of current processes, identify pain points or bottlenecks, and gather feedback from stakeholders. These insights inform areas for process refinement or the adoption of new quality management techniques.
Metrics and Data Analysis within Project Quality Management
Consistently measuring and analyzing quality metrics, such as defect rates, rework efforts, customer satisfaction scores, etc., provides quantifiable data to track progress, identify trends or patterns, and make data-driven decisions for improvement.
Employee Training and Skill Development
Investing in ongoing training and professional development for project teams ensures they stay up-to-date with the latest quality management methodologies, tools, and best practices. This empowers them to continuously enhance their quality management capabilities.
Encouraging a Quality-Focused Culture for Project Quality Management
Creating a culture that values quality and continuous improvement is crucial. This involves fostering an environment where team members feel empowered to identify opportunities for optimization, suggest improvements, and embrace change for better quality outcomes.
Adopting New Tools and Technologies
Staying abreast of new quality management tools, software, and technologies can streamline processes, automate repetitive tasks, and provide better visibility and control over quality efforts. Regularly evaluating and integrating suitable innovations supports continuous improvement.
Collaboration and Knowledge Sharing
Facilitating cross-functional collaboration and knowledge sharing within the organization allows teams to learn from each other’s experiences, leverage proven quality management practices, and collectively drive improvement initiatives.
SixSigma.us offers both Live Virtual classes as well as Online Self-Paced training. Most option includes access to the same great Master Black Belt instructors that teach our World Class in-person sessions. Sign-up today!
Virtual Classroom Training Programs Self-Paced Online Training Programs