6S Method in Lean Six Sigma for Continuous Improvement
The 6S system – Sort, Set in Order, Shine, Standardize, Sustain, and Safety, is a powerful tool for businesses across industries to streamline operations, reduce waste, and create a safer, more productive work environment.
Whether you’re in manufacturing, the apparel industry, or any other sector, understanding and implementing the 6S methodology can have a transformative impact on your organization.
Key Highlights
- Understand the 6S methodology – what it is, its origins, and the key principles
- Discover the benefits of implementing it in the workplace, including improved efficiency, safety, and cost savings
- Learn how it can be applied in different industries, such as manufacturing, apparel, and more
- Explore best practices and common challenges in 6S implementation, as well as strategies for continuous improvement
What is 6S?
6S is a workplace organization and management methodology that builds upon the well-known 5S system.
It is a comprehensive approach that helps create a clean, organized, and efficient work environment by focusing on six key principles: Sort, Set in Order, Shine, Standardize, Sustain, and Safety.
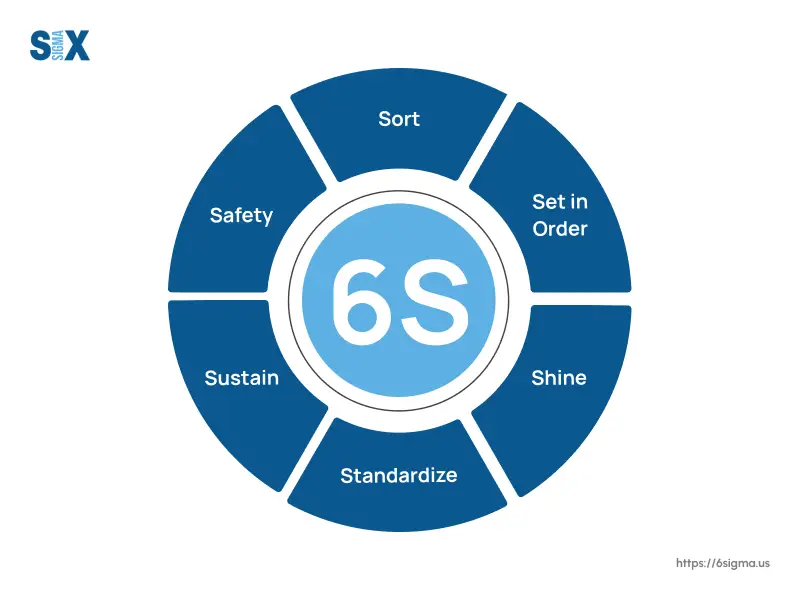
Origins of 5S and Evolution to 6S
The 5S system originated in Japan in the 1950s as a way to improve workplace efficiency and productivity. The five principles of 5S are; Seiri (Sort), Seiton (Set in Order), Seiso (Shine), Seiketsu (Standardize), and Shitsuke (Sustain).
Over time, the 5S methodology has evolved, and many organizations have added a sixth “S” – Safety. This addition recognizes the critical importance of workplace safety and integrates it as a core component of the overall system.
The 6S approach provides a more holistic framework for creating a safe, organized, and efficient work environment.
Explore How 6S fits into the Lean Six Sigma methodology through our FREE short course, Lean Six Sigma Overview
Key Principles of 6S
The six key principles of the 6S methodology are:
- Sort (Seiri): Identifying and removing unnecessary items from the workplace, reducing clutter and potential hazards.
- Set in Order (Seiton): Organizing and labeling necessary items in a logical and accessible manner, ensuring efficient workflows.
- Shine (Seiso): Regular cleaning and maintenance of the workplace, keeping it in pristine condition.
- Standardize (Seiketsu): Establishing consistent work processes, responsibilities, and visual cues to maintain the 6S system.
- Sustain (Shitsuke): Maintaining it over the long term through ongoing training, audits, and continuous improvement.
- Safety (Anzen): Implementing safety measures, providing personal protective equipment (PPE), and promoting a culture of safety awareness.
By following these six principles, organizations can create a well-organized, clean, and safe work environment. External help can make things smoother; employees can take a Six Sigma certification course to increase efficiency, productivity, and overall workplace satisfaction.
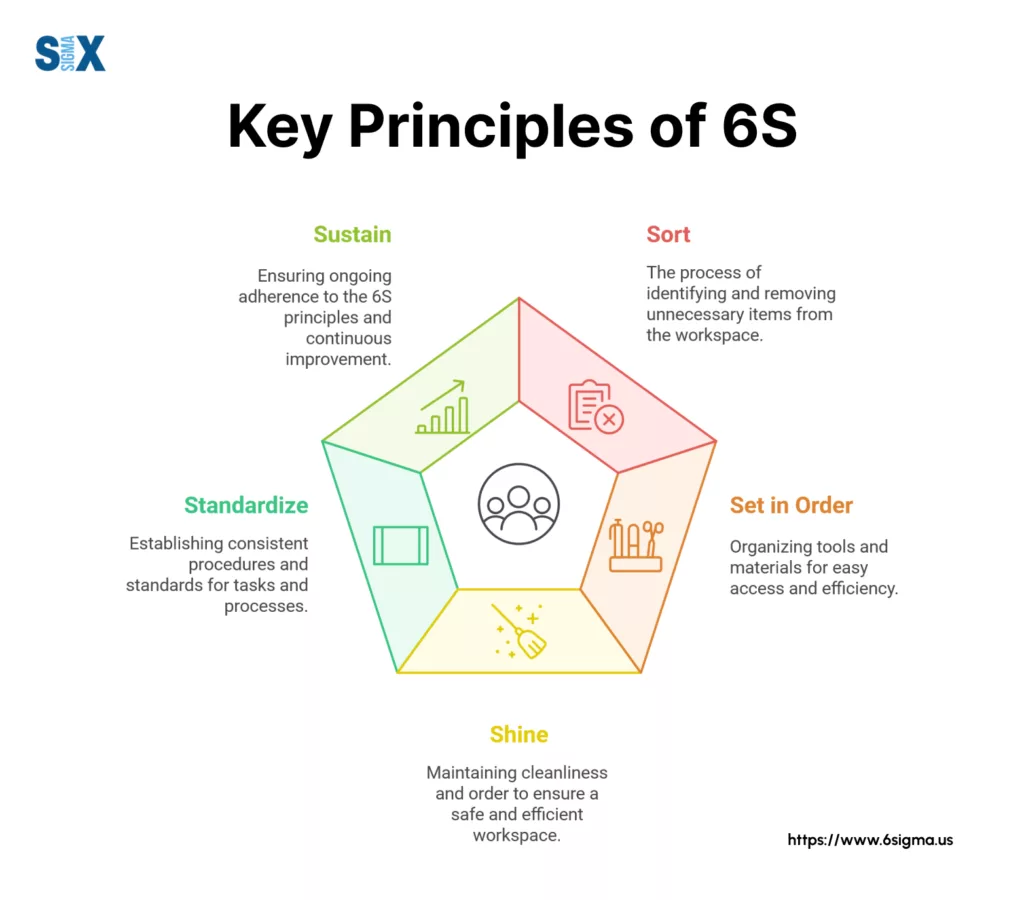
The 6S Steps Explained
Sort
The first step in this methodology is Sort. This involves identifying and removing any unnecessary items from the workplace.
This could include outdated documents, broken equipment, excess inventory, or any other items that are not essential for daily operations.
The goal is to create a clutter-free and organized work environment by getting rid of anything that is not needed. This improves workflow and productivity and reduces the risk of workplace hazards.
Set in Order
Once the unnecessary items have been removed, the next step is Set in Order. This involves organizing and labeling the remaining necessary items logically and efficiently.
This could include storing items in designated areas, using color-coding or labeling systems, and ensuring that everything has a designated and easily accessible place.
The goal is to create a streamlined and intuitive work environment where employees can quickly and easily find what they need.
Shine
The third step in this process is Shine. This involves regular cleaning and maintenance of the workplace.
This includes wiping down surfaces, sweeping and mopping floors, and ensuring that equipment is well-maintained and in good working order.
The goal is to create a clean, well-organized, and visually appealing work environment that promotes a sense of pride and ownership among employees.
Master statistical Training with our Lean Six Sigma Overview Training
Standardize
Next is Standardize. This involves establishing consistent work processes and responsibilities throughout the organization.
This could include creating standardized operating procedures, checklists, and job descriptions, as well as ensuring that all employees are trained and held accountable for following these standards.
The goal is to create a consistent and efficient work environment where everyone knows their roles and responsibilities.
Sustain
The fifth step is Sustain. This involves maintaining the 6S system long-term and ensuring that it becomes ingrained in the organization’s culture.
This could include regular audits, ongoing training and education, and rewarding employees for their adherence to the 6S principles.
The goal is to ensure that this system becomes a permanent part of the organization’s operations and is not just a temporary solution.
Safety
The final step in the 6S process is Safety. This involves implementing safety measures and personal protective equipment (PPE) to ensure the well-being of employees.
This could include installing safety guards on equipment, providing appropriate PPE such as hard hats, gloves, and safety glasses, and conducting regular job safety analysis (JSAs) to identify and mitigate potential hazards.
The goal is to create a safe and healthy work environment that protects employees from harm.
Benefits of Implementing 6S
Implementing the 6S methodology in the workplace can provide a wide range of benefits that can significantly improve overall operations and productivity.
Let’s explore some of the key advantages of adopting the 6S system:
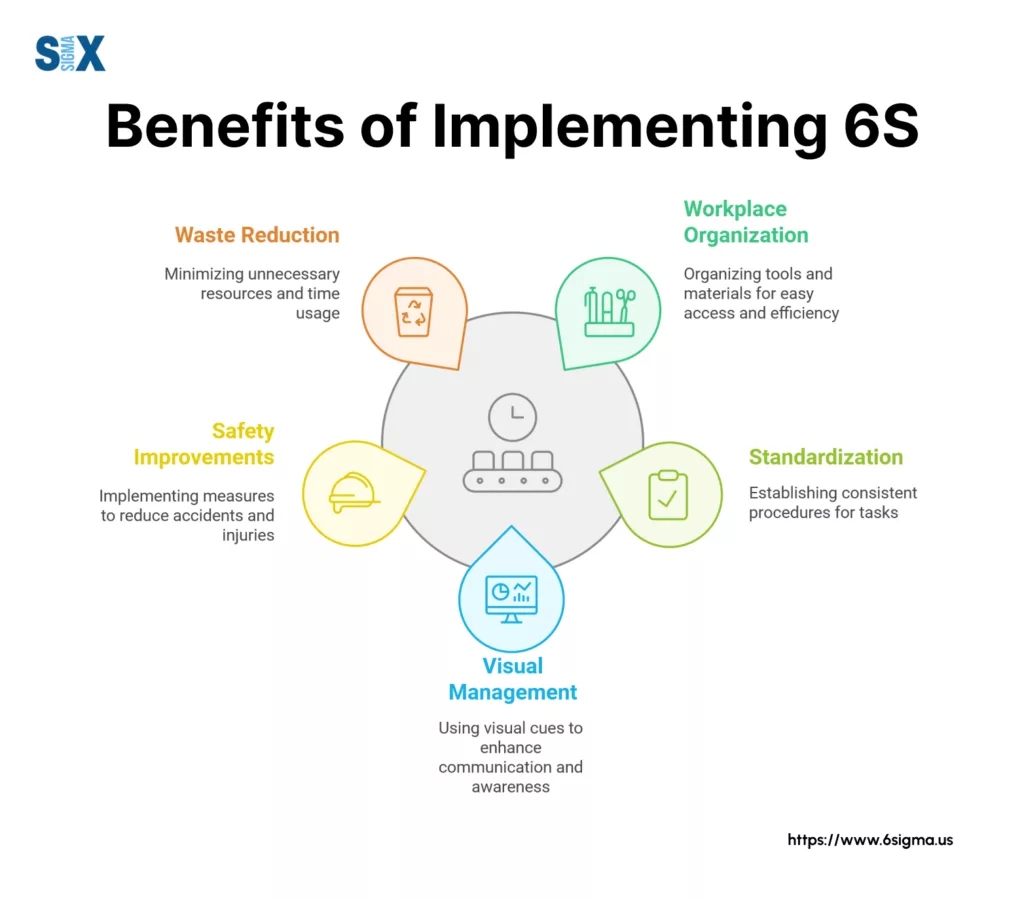
Improved Workplace Efficiency and Productivity
One of the primary goals of 6S is to streamline workflows and eliminate wasteful activities. By sorting through unnecessary items, organizing the necessary ones, and establishing standardized processes, it helps create a more efficient work environment.
Employees can quickly locate the tools and materials they need, reducing time spent searching and increasing the time spent on value-adding tasks. This leads to improved overall productivity and efficiency.
Enhanced Workplace Organization and Cleanliness
The “sort”, “set in order”, and “shine” principles ensure that the workplace is kept clean, organized, and visually appealing.
This not only creates a more pleasant and comfortable work environment but also makes it easier to identify and address potential issues or problems.
When everything has a designated place and is kept in pristine condition, it becomes simpler to maintain order and prevent clutter from accumulating.
Reduced Workplace Hazards and Increased Safety
Safety is a crucial component of the 6S methodology. By implementing the “safety” principle, organizations can identify and mitigate potential workplace hazards.
This may involve properly storing and labeling hazardous materials, ensuring that walkways and work areas are clear of obstructions, and providing appropriate personal protective equipment (PPE) for employees.
Reducing workplace hazards and promoting a culture of safety can lead to fewer accidents, injuries, and lost-time incidents, ultimately protecting the well-being of the workforce.
Be Successful in your Lean Journey with our Lean Transformation Training
Cost Savings through Waste Reduction and Better Material Handling
The 6S approach encourages the identification and elimination of waste, whether it’s unnecessary inventory, inefficient processes, or underutilized resources.
By optimizing material handling and reducing waste, organizations can achieve significant cost savings.
Additionally, the improved organization and efficiency gained can lead to better inventory management, reduced storage requirements, and more effective use of materials and equipment, all of which contribute to lower operational costs.
Improved Communication and Teamwork Among Employees
The collaborative nature of the 6S implementation process can foster stronger communication and teamwork among employees.
As teams work together to sort, organize, and standardize their work environment, they develop a shared understanding of their roles and responsibilities.
This promotes better coordination, problem-solving, and a sense of collective ownership, ultimately leading to improved morale, job satisfaction, and overall team cohesion.
By leveraging the benefits of this methodology, organizations can create a more efficient, organized, and safer work environment, leading to increased productivity, cost savings, and enhanced employee engagement.
The holistic approach of 6S makes it a powerful tool for driving continuous improvement and optimizing workplace performance.
Dive into Lean principles to boost your workplace optimization efforts.
Our Lean Fundamentals course offers practical training in techniques that complement the 6S methodology.
6S in Different Industries
While the 6S methodology originated in the manufacturing sector, it has since been successfully implemented across a wide range of industries.
Let’s take a closer look at how 6S can benefit various industries:
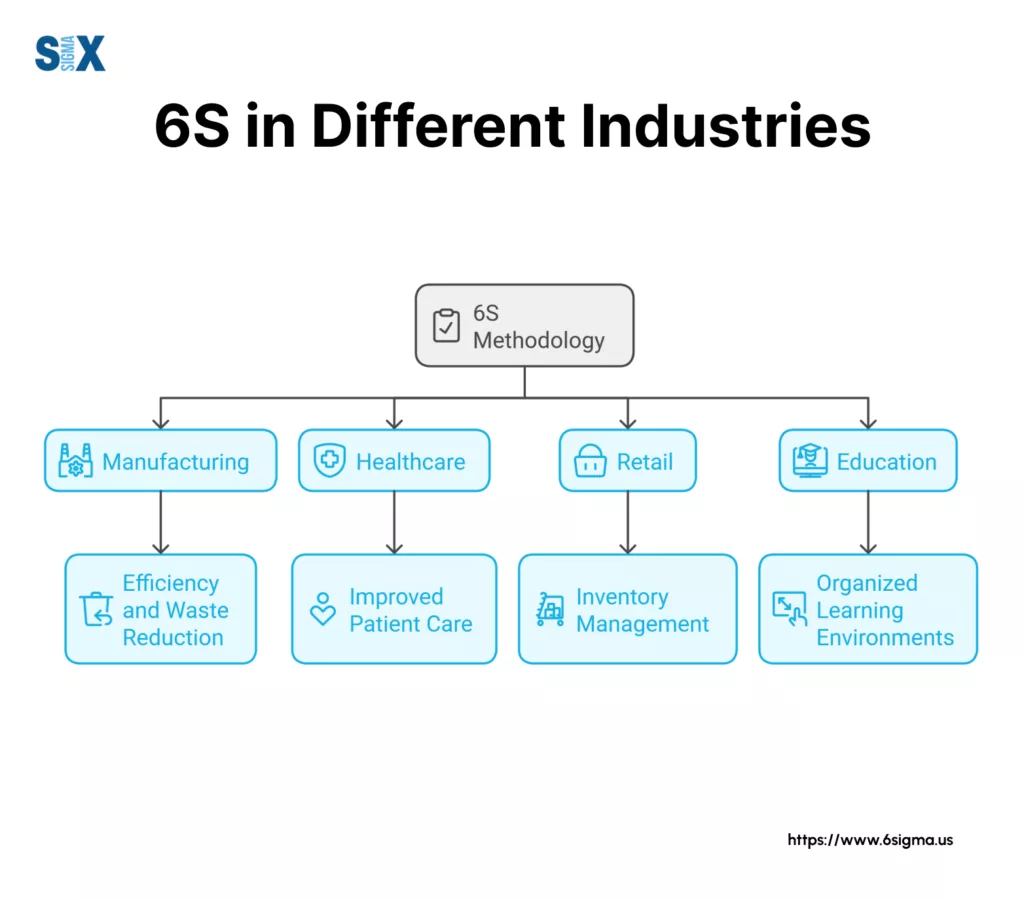
6S in Manufacturing Industries
The 6S system is particularly well-suited for manufacturing environments, where efficiency, organization, and safety are paramount.
In a manufacturing setting, it can help streamline production processes, minimize waste, and create a clean, well-organized workspace.
By implementing these principles, manufacturers can see improvements in areas such as:
- Inventory management and material handling
- Equipment maintenance and upkeep
- Workflow optimization and reduced bottlenecks
- Workplace safety and accident prevention
- Overall equipment effectiveness (OEE) and productivity
Many leading manufacturing companies, from automotive to electronics, have adopted 6S as a core part of their lean manufacturing strategies, reaping the benefits of a more organized, efficient, and safer work environment.
6S in the Apparel Industry
The apparel industry, with its focus on quality, precision, and attention to detail, can also greatly benefit from the 6S methodology. In apparel manufacturing, it can help:
- Optimize fabric and trim storage and organization
- Streamline the cutting, sewing, and finishing processes
- Maintain cleanliness and organization of sewing stations
- Reduce the risk of product defects and quality issues
- Improve workplace safety for apparel workers
By this implementation, apparel manufacturers can enhance their production efficiency, reduce waste, and deliver higher-quality products to their customers.
6S in Other Industries
While the manufacturing and apparel industries are well-known for their 6S implementations, its principles can be applied to a variety of other sectors as well. For example:
- Healthcare facilities can use 6S to organize medical supplies, maintain cleanliness in patient rooms, and improve workflow for healthcare professionals.
- Office environments can leverage it to declutter workspaces, optimize document and file storage, and create a more organized, productive office culture.
- Warehousing and logistics operations can implement it to optimize inventory management, streamline material handling, and enhance workplace safety.
Regardless of the industry, the core principles of 6S – sorting, setting in order, shining, standardizing, sustaining, and ensuring safety – can be adapted to improve efficiency, organization, and overall workplace performance.
Implementing 6S: Best Practices and Challenges
Successful implementation of the 6S methodology requires a strategic and structured approach. These are:
- Gain Management Commitment and Support: Securing buy-in from top-level management is crucial for the success of a 6S initiative. Ensure that leadership understands the benefits and is committed to providing the necessary resources and support.
- Establish a 6S Implementation Team: Assemble a cross-functional team of employees who will be responsible for driving the 6S implementation process. This team should include representatives from different departments and levels of the organization.
- Provide Comprehensive Training: Educate all employees on the principles and steps of the 6S methodology. Offer hands-on training sessions to ensure that everyone understands their roles and responsibilities in this system.
- Start with a Pilot Project: Begin the 6S implementation with a small, manageable pilot project. This allows you to test the process, identify any challenges, and refine the approach before scaling it across the entire organization.
- Emphasize Visual Management: Utilize visual cues, signage, and labeling throughout the workplace to make the 6S system intuitive and easy to understand. This helps maintain order and ensure consistency in the implementation.
- Establish Measurable Goals and KPIs: Define clear, measurable goals and key performance indicators (KPIs) to track the progress and success of your 6S implementation. This will help you identify areas for improvement and celebrate your achievements.
- Foster a Culture of Continuous Improvement: Encourage employees to continuously identify opportunities for optimizing and refining the 6S system. Encourage a mindset of ongoing improvement and empowerment among all team members.
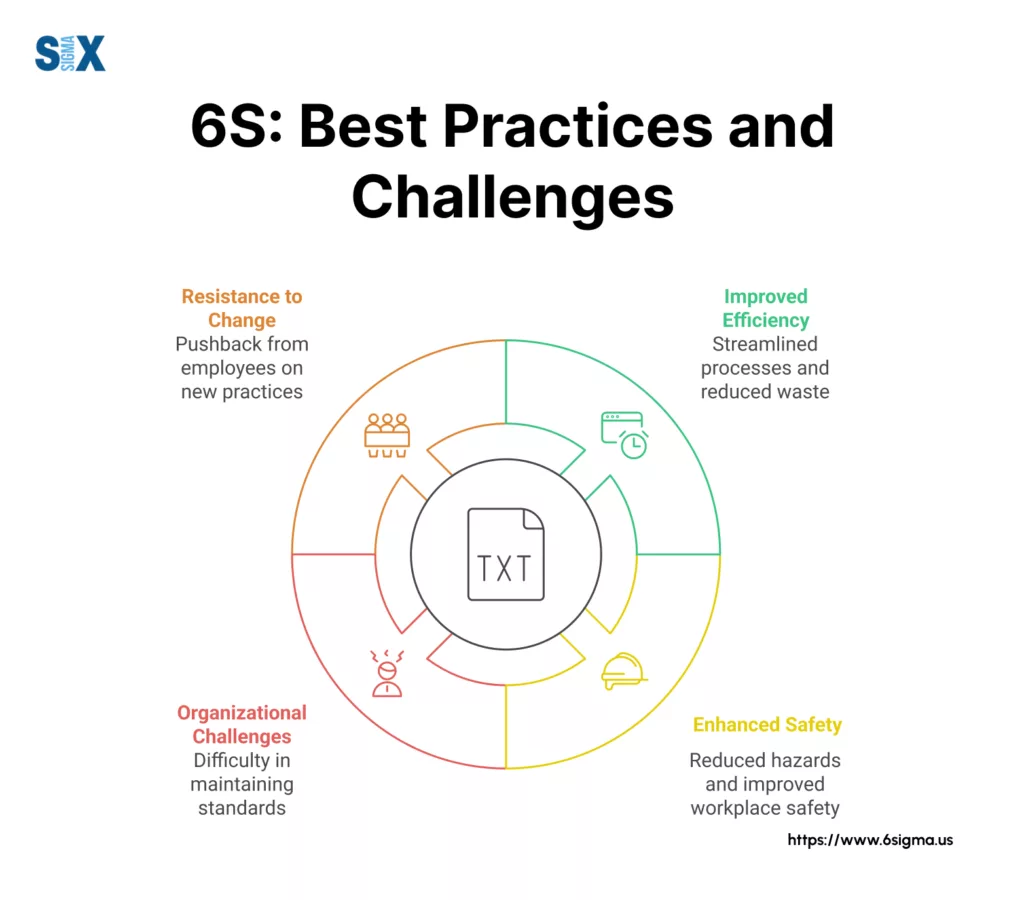
Check our Lean Six Sigma Certification and Training
Common Challenges and Strategies to Overcome Them
While implementing 6S can bring significant benefits, it is not without its challenges. Some common obstacles and strategies to overcome them include:
- Resistance to Change: Employees may be hesitant to adopt new processes and procedures. Overcome this by effective communication, training, and by involving employees in the implementation process.
- Lack of Sustained Commitment: Maintaining the 6S system over the long term can take time and effort. Regularly review and reinforce the principles, and recognize and reward employees for their contributions.
- Inadequate Resources: Ensure that you have sufficient resources, such as budget, time, and personnel, to support the 6S implementation. Prioritize and allocate resources effectively to address the most critical needs.
- Insufficient Employee Engagement: Engage employees at all levels and encourage their active participation in this process. Provide opportunities for feedback and recognition to foster a sense of ownership.
- Difficulty in Sustaining the 6S System: Develop a comprehensive plan for maintaining the 6S system, including regular audits, continuous improvement initiatives, and ongoing training and communication.
Continuous Improvement and Sustaining the 6S System
Implementing 6S is not a one-time event but rather a continuous journey of improvement.
Embrace a mindset of ongoing optimization and refinement to ensure the long-term success of your 6S system.
Regularly review and assess the effectiveness of your practices, and make adjustments as needed. Encourage employees to identify opportunities for improvement and empower them to implement changes.
By fostering a culture of continuous improvement, you can ensure that this system remains effective and sustainable over time.
The Importance of 6S for Workplace Optimization
By implementing the six key principles – Sort, Set in Order, Shine, Standardize, Sustain, and Safety – organizations can unlock significant benefits, including improved efficiency, enhanced safety, reduced waste, and better communication among employees.
The 6S system helps create a more organized, clean, and well-maintained work environment, which in turn boosts productivity and reduces the risk of workplace accidents and injuries.
Through the implementation of safety measures and the use of personal protective equipment (PPE), it also helps safeguard the well-being of workers, which is of paramount importance.
Beyond the immediate gains in efficiency and safety, the long-term, sustainable nature of 6S also enables continuous improvement.
By establishing standardized processes and fostering a culture of accountability and ownership, organizations can ensure that the 6S principles become ingrained in the daily operations and workflows of the workplace.
We encourage all our readers to explore the transformative potential of 6S and consider implementing this proven methodology in their workplaces.
Whether you’re in the manufacturing sector, the apparel industry, or any other field, the benefits are clear – a more organized, efficient, and safer work environment that ultimately drives greater success and profitability for your business.
Remember, the journey to workplace optimization is an ongoing one, and 6S provides a comprehensive framework to guide you every step of the way.
Embrace the 6S principles, empower your team, and unlock the full potential of your workplace. The rewards will be well worth the effort.
Most Asked Questions (FAQs) about 6S Lean
6S stands for Sort, Set in order, Shine, Standardize, Sustain, and Safety. These principles are designed to create an organized and efficient workplace.
The function of 6S is to enhance workplace organization and efficiency by systematically improving processes, reducing waste, and ensuring a safe working environment.
The rule of 6S emphasizes maintaining a clean, organized, and safe workspace. It encourages continuous improvement and adherence to the established standards to ensure sustainability.
In healthcare, 6S focuses on improving patient safety and care quality by organizing workspaces, streamlining processes, and minimizing errors through effective management practices.
The role of 6S is to foster a culture of continuous improvement and operational excellence, ensuring that all employees are engaged in maintaining a clean and efficient work environment.
6S is important because it leads to increased productivity, reduced waste, improved safety, and enhanced employee morale, ultimately contributing to better organizational performance.
5S stands for Sort, Set in order, Shine, Standardize, and Sustain. It is a methodology aimed at organizing and managing the workspace effectively.
6S builds upon the principles of 5S by adding Safety as an essential component, emphasizing the importance of a safe working environment alongside organization and efficiency.
5S tools include various techniques and resources used to implement the 5S methodology, such as checklists, visual management tools, and training materials to promote organization and efficiency in the workplace.
SixSigma.us offers both Live Virtual classes as well as Online Self-Paced training. Most option includes access to the same great Master Black Belt instructors that teach our World Class in-person sessions. Sign-up today!
Virtual Classroom Training Programs Self-Paced Online Training Programs