Defining and Optimizing Value-Added vs Non Value-Added Activities
Value Added and Non Value Added concepts are pretty straightforward on the surface, truly understanding the differences can impact efficiency, waste reduction, and customer satisfaction.
For any organization looking to drive continuous improvement, mastering these core concepts is essential.
Key Highlights
- Defining value-added and non-value-added
- Process mapping to visualize workflow and pinpoint improvement areas
- Distinguishing between three categories – value added, necessary non value added, and pure waste
- Eliminating non value added by focusing on 7 common wastes
- Optimizing value added through enhanced quality, functionality, innovation
- Managing essential non value added while minimizing where possible
- Comparing attributes of value-added and non-value-added activities
- Conclusion emphasizes maximizing value added and minimizing non value added for efficiency gains
Value Added vs Non-Value Added
Properly categorizing process elements enables organizations to optimize efficiency, reduce waste, and enhance customer-perceived value.
Understanding value added vs non value added supports organizations in their pursuit of lean operations and continuous improvement.
Properly differentiating between these categories through detailed process mapping and analysis allows for data-driven waste reduction, lead time declines, and quality enhancement.
Mastering these concepts transforms productivity and efficiency.
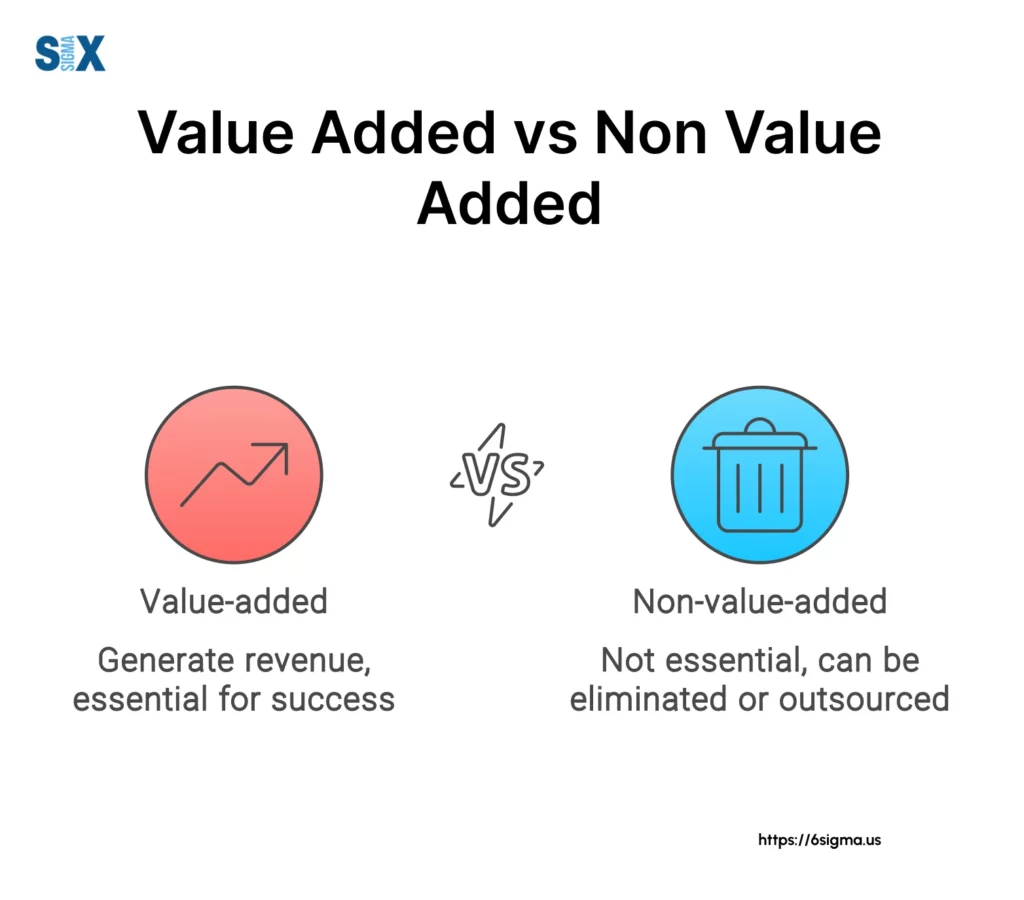
Defining Value Added vs Non Value Added
Value added activities are process steps that directly contribute to transforming inputs into outputs that align with customer needs and preferences.
Essentially, they deliver functionality and features customers are willing to pay for.
In contrast, non value added activities fail to directly enhance the product or service in the customer’s eyes. They represent waste and inefficiency.
Necessary non value added activities do not directly enhance value but are required due to regulations, compliance standards, or other essential functions.
Pure non value added activities provide no value and are unnecessary – these present the biggest opportunities for reduction and elimination.
The seven common wastes we aim to mitigate in lean methodologies are:
Defects
Errors, mistakes, and poor quality result in rework or scrap.
Overproduction
Producing more output than the customer demand requires, resulting in excess inventory.
Transportation
Unnecessary movement and handling of materials that do not add form or function.
Waiting
Idle time created by delays in the process leads to longer lead times.
Inventory
Excess raw materials, work in progress, or finished goods tying up capital.
Motion
Unnecessary movement of people that does not directly contribute to value add.
Overprocessing.
The value-added test analyzes if a process meets three criteria: directly contributes value, customer willing to pay, and done right the first time.
Identifying Value Added vs Non-Value Added
Process mapping provides a visual representation of the workflow, enabling deeper analysis of each step to categorize it as value-added, necessary non-value-added, or pure waste.
We must clearly define value based on the voice of the customer – what they need and are willing to pay for.
As we analyze process elements, we identify direct value-adding activities, necessary non-value added, and non-value added activities failing to enhance value.
Applying the value-added test provides further clarity. Leveraging metrics, data, and customer perspectives gives quantifiable insight. For example, correlating cycle times with value contributed.
Comparison b/w Value Added vs Non-Value Added
Element | Value Added | Non-Value Added |
Customer willing to pay | Yes | No |
Contributes to product/service | Directly | Indirectly or not at all |
Impact on process | Positive | Negative or neutral |
Example activities | Assembly, joining | Rework, searching, delays |
Eliminating Non-Value Added
The priority is eliminating pure non value added activities completely.
This allows for streamlining the workflow, reducing cycle times, enhancing standardized work procedures, and focusing resources on value generation.
Removing non value added steps enhances quality, throughput, and customer satisfaction.
Optimizing Value Added
For value-added activities, our emphasis shifts to optimization. We boost product quality, functionality, and overall efficiency of these processes.
Embedding innovation into value creation further provides a competitive advantage.
Fostering a culture and mindset of continuous incremental improvement ensures value-added activities remain optimized over lengthy time horizons.
Several key strategies can be employed:
Enhance Product Quality
There are always opportunities to incrementally improve output quality by reducing defects, improving consistency, and preventing errors in value-added steps.
We leverage statistical process control, test methods, and other quality tools for this enhancement.
Improve Functionality
Incorporating more features, personalization, and overall functionality improvements into value-added activities results in outputs better-serving customer needs.
The voice of the customer data guides these efforts.
Increase Efficiency
We frequently can accomplish the same value-added transformation with less resource expenditure through setup time reductions, improved changeovers, balanced workflows, and method optimization.
Embrace Innovation
Emerging technologies around automation, advanced analytics, and smart connected machines provide innovation opportunities to get far more output from value-added process elements.
Foster Continuous Improvement
Applying Kaizen, we sustain a focus on constantly optimizing value-added activities.
Small daily and weekly improvements compound over the long run. Structured problem-solving workshops also unveil improvement insights.
Getting the highest ratio of value-added output compared to resource investment input drives productivity, quality, and profitability – the central tenets of optimizing overall equipment effectiveness.
This journey centers on never being complacent with value-added performance.
Managing Necessary Non-Value Added
Necessary non-value-added tasks do not directly contribute to product or service enhancements but remain essential due to regulatory compliance, quality control activities, or other imperative functions.
As these tasks do not directly boost customer-perceived value, our emphasis is balancing and minimizing them so they do not hinder value-added pursuits.
Several key strategies can effectively manage necessary non value added activities:
Meet Standards While Reducing Footprint: We integrate necessary rules, checks, and validations seamlessly into workflows to avoid workflow interruptions. Visual controls, poka-yoke devices, and real-time alerts enable seamless compliance.
Digitization and Automation: Transitioning manual data collection, reporting, inspection documentation, changeover verification, and other necessary non-value-added tasks to electronic platforms & databases streamlines administration while still meeting standards. Smart-connected machines also automate real-time equipment monitoring.
Shared Resources and Dual-Purpose Assets: Leveraging crossover training and dual-skilled workers enables one employee to handle value-added operations while managing necessary non-value-added tasks in their small windows of downtime. Machines like printers can also serve dual uses.
Balance Against Value Added: Scheduling production runs to maximize value-added runtimes provides buffers to execute short necessary non value added activities like equipment calibration, safety checks, or regulatory reporting in equipment downtimes without extending overall cycle times.
Continuous Incremental Reduction: Small periodic changes and micro-improvements cumulatively shrink the time, labor, and space necessary for non-value-added activities.
We also constantly evaluate if each necessary non-value-added task remains essential or if the requirements driving it have changed to enable elimination.
Achieving highly efficient operations hinges on both maximizing value added and effectively managing necessary non value added.
Though essential, necessary non-value added presents resource tradeoffs we systematically minimize through combinations of simplification, digitization, balance in scheduling, and continuous incremental reductions.
Key Benefits
Proper value added vs non value added differentiation and management yields measurable business results:
- Cost savings from waste reduction
- Shorter lead times from leaner workflow
- Improved quality from fewer defects
- Increased customer value from heightened product performance
- Greater productivity from focusing on value-adding activities
- Higher profitability from efficiency gains and waste reduction
Conclusion
Mastering the identification and management of value-added vs non value added elements paves the path toward lean operations and continuous improvement.
Assessing process maps and each activity to categorize them arms organizations with data-driven insight on improvement opportunities.
The journey centers on eliminating pure waste, optimizing value added, and balancing necessary non value added tasks.
SixSigma.us offers both Live Virtual classes as well as Online Self-Paced training. Most option includes access to the same great Master Black Belt instructors that teach our World Class in-person sessions. Sign-up today!
Virtual Classroom Training Programs Self-Paced Online Training Programs