Quality Circle: A Guide to Employee-Driven Process Improvement
Quality circle represent organized groups of employees who meet regularly to solve workplace problems and enhance productivity.
These voluntary teams, first developed in Japan during the 1960s, have transformed how organizations approach quality management and process improvement.
Today’s quality circles combine traditional problem-solving methods with modern data analysis techniques.
Team members identify issues, analyze root causes, and implement solutions that directly impact their work areas.
This systematic approach leads to measurable improvements in product quality, operational efficiency, and employee satisfaction.
Key Highlights
- Implementation steps for successful teams
- Modern tools in quality management
- Integration with Six Sigma methods
- Problem-solving techniques and best practices
- Real benefits across different industries
- Team structure and member roles
- Performance measurement and success metrics
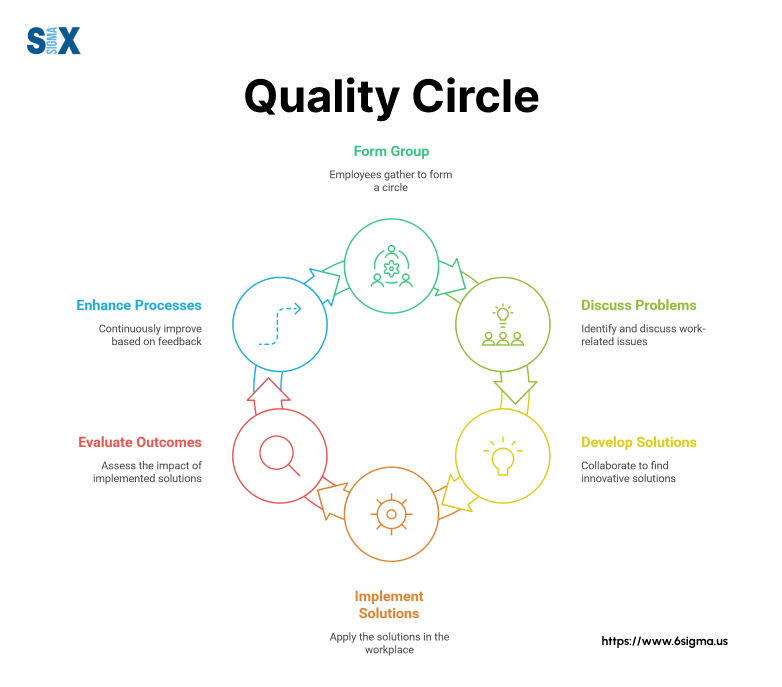
What are Quality Circles?
Quality circles emerged in Japan during the 1960s under the guidance of Kaoru Ishikawa.
The concept gained momentum when Japanese industries needed to rebuild their manufacturing capabilities after World War II.
By 1978, Japan had established over one million quality circles, involving more than ten million workers.
The success in Japan prompted global adoption.
American companies like Lockheed Martin introduced quality circles in the 1970s, while European organizations followed suit in the 1980s.
Today, quality circles operate in various sectors, from manufacturing to healthcare and service industries.
Essential Features Of a Quality Circle
Quality circles function as small teams of employees who share similar work responsibilities.
These groups meet regularly to identify and solve workplace problems. Each circle typically includes 6-12 members who volunteer their participation and receive specialized training in problem-solving techniques.
Team members use analytical tools like Pareto charts, cause-and-effect diagrams, and statistical process control methods.
They collect data, analyze issues, and develop solutions specific to their work areas. Management provides support and resources but allows the circle to maintain autonomy in their problem-solving approach.
Purpose And Strategic Value
The primary objectives of quality circles extend beyond simple problem-solving. These teams aim to enhance product quality, improve workplace efficiency, and boost employee morale.
They serve as platforms for skill development, knowledge sharing, and innovation within organizations.
Quality circles create measurable value through:
- Reduced operational costs
- Enhanced product quality
- Improved employee engagement
- Streamlined work processes
- Innovation in problem-solving
Organizational Framework of a Quality Circle
A typical quality circle consists of four key roles:
- Facilitator: Guides the circle’s activities and ensures proper methodology
- Leader: Coordinates meetings and maintains focus on objectives
- Members: Contribute ideas and implement solutions
- Sponsor: Provides management support and resources
These teams operate within a structured framework that includes regular meetings, documented procedures, and formal presentation of solutions to management.
The circle’s success depends on clear communication channels and strong support from organizational leadership.
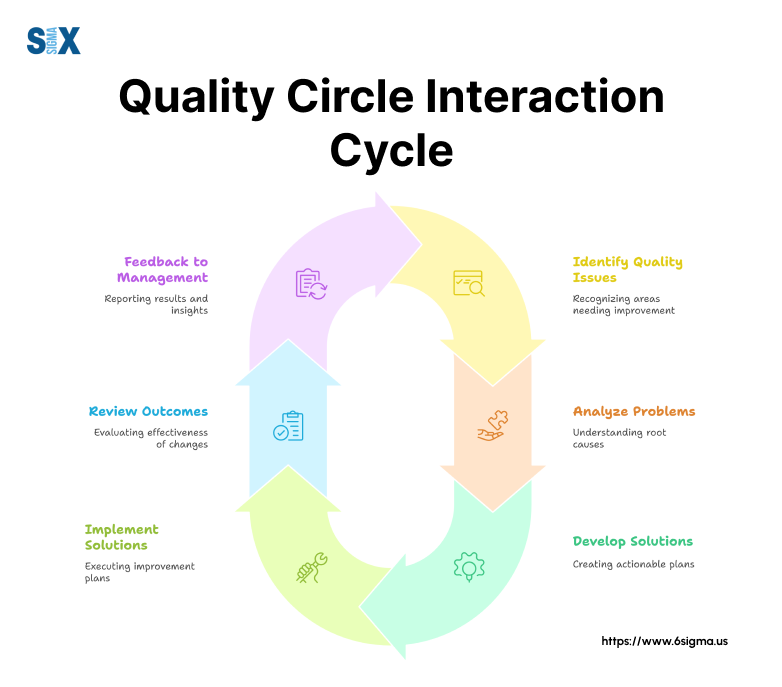
Join our Six Sigma Champion Leadership Program to master the strategic implementation of quality circles and Six Sigma methodologies
Lean Six Sigma Fundamentals
Lean Six Sigma combines two powerful methodologies to eliminate waste and reduce process variation.
This data-driven approach merges Lean’s focus on speed and efficiency with Six Sigma’s emphasis on quality and consistency.
Organizations implement these methods to achieve measurable improvements in their operations and product quality cycles.
The DMAIC Framework
The DMAIC methodology serves as the backbone of Lean Six Sigma projects.
This structured approach includes five phases:
- Define: Teams identify specific problems and project goals
- Measure: Data collection establishes current performance levels
- Analyze: Statistical tools reveal root causes of issues
- Improve: Solutions get developed and implemented
- Control: New processes maintain improved performance
Continuous Improvement Integration
Lean Six Sigma drives ongoing improvement through systematic problem-solving and process optimization.
Teams monitor key metrics, identify improvement opportunities, and implement solutions using statistical tools and proven techniques.
This cycle of improvement helps organizations maintain competitive advantages while delivering consistent product quality.
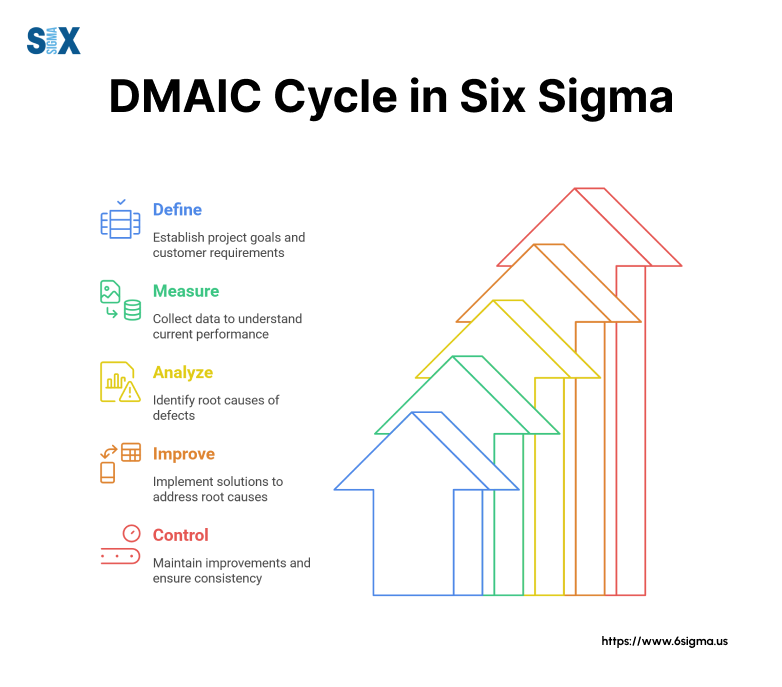
Master the DMAIC process and boost organizational productivity across industries with our Lean Six Sigma Overview course
Quality Circle And Six Sigma: A Powerful Partnership
Quality circles and Six Sigma share common goals while offering distinct advantages to organizations.
Six Sigma provides the statistical tools and structured methodology, while quality circles deliver the grassroots engagement needed for successful implementation.
This partnership creates a robust framework for process improvement and quality enhancement.
The integration of these approaches multiplies their individual benefits.
Quality circles bring valuable shop-floor insights and daily operational knowledge, while Six Sigma adds data-driven decision-making and systematic problem-solving techniques. Together, they create a more effective quality management system.
Supporting Six Sigma Success
Quality circles strengthen Six Sigma initiatives through several key mechanisms.
Team members from quality circles often become valuable resources for Six Sigma projects, bringing detailed process knowledge and established problem-solving experience.
Their regular interaction with processes provides crucial insights for Six Sigma teams during the Define and Measure phases.
These circles also help sustain Six Sigma improvements through daily monitoring and quick response to process variations.
Their continuous presence on the shop floor enables rapid identification of deviations and immediate corrective actions, supporting the Control phase of DMAIC projects.
DMAIC Integration Framework and Quality Circle
Quality circles fit naturally within the DMAIC structure:
- Define Phase: Circles identify potential project opportunities based on daily observations
- Measure Phase: Circle members assist in data collection and process documentation
- Analyze Phase: Teams provide insights into root causes and process relationships
- Improve Phase: Circles help implement and refine proposed solutions
- Control Phase: Regular circle activities maintain process improvements
This integration creates a feedback loop between strategic Six Sigma projects and daily operational improvements.
Quality circles serve as both implementation teams and early warning systems for process issues, while Six Sigma provides the analytical framework for larger-scale improvements.
Implementation Guide For Quality Circle In Six Sigma
The successful launch of quality circles within a Six Sigma environment requires careful planning and execution.
Organizations should begin with a pilot program in one department before expanding. The implementation process follows these key stages:
Phase 1: Planning and Preparation
- Select pilot areas based on process complexity and team readiness
- Develop training materials aligned with Six Sigma principles
- Establish communication channels between circles and Six Sigma teams
Phase 2: Formation and Training
- Recruit voluntary participants from target work areas
- Conduct initial training on problem-solving tools
- Establish meeting schedules and resource requirements
Phase 3: Operation and Support
- Begin regular circle meetings with defined agendas
- Document progress and challenges
- Provide ongoing coaching and resources
Team Member Roles And Duties
Each quality circle requires specific roles for effective operation. The Circle Leader guides meetings and coordinates activities with Six Sigma teams.
Facilitators provide technical support and ensure alignment with Six Sigma methodologies.
Circle Members contribute ideas and implement solutions, while Management Sponsors remove obstacles and secure resources.
Technical experts from Six Sigma teams often serve as mentors, helping circles apply advanced analytical tools when needed.
This partnership ensures circles maintain their practical focus while leveraging Six Sigma’s statistical rigor.
Essential Tools And Methods of a Quality Circle
Quality circles employ various problem-solving tools that complement Six Sigma techniques. Basic tools include Pareto charts, cause-and-effect diagrams, and check sheets.
More advanced methods incorporate statistical process control charts and capability studies. Circles also use Six Sigma’s data collection and analysis tools when addressing complex issues.
Measuring Circle Performance
Success metrics for quality circles focus on both process improvements and team effectiveness. Key performance indicators include:
Process Metrics:
- Number of implemented solutions
- Cost savings achieved
- Quality improvements measured
- Process cycle time reductions
Team Metrics:
- Meeting attendance rates
- Solution implementation time
- Member participation levels
- Project completion rates
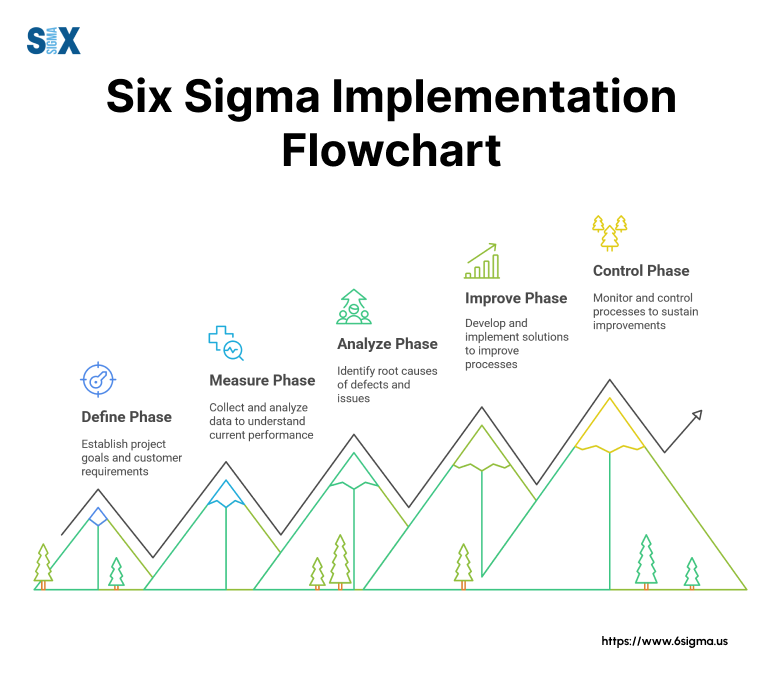
Learn project selection, metrics development, and practical implementation strategies with real-world examples with Six Sigma Champion Course
Benefits And Limitations Of Quality Circle In Six Sigma
The integration of quality circles with Six Sigma methodologies creates significant operational benefits.
Organizations report increased employee engagement when quality circles support Six Sigma projects.
Teams identify problems faster and implement solutions more effectively due to their daily process involvement.
Quality circles enhance Six Sigma initiatives through improved data collection and real-time process monitoring.
Their constant presence on the shop floor enables quick detection of deviations and rapid response to quality issues. This combination leads to sustained process improvements and reduced implementation costs.
Key Implementation Challenges
Despite their benefits, quality circles face several limitations when operating within Six Sigma frameworks.
Resource constraints often impact circle effectiveness, particularly when competing with larger Six Sigma projects for attention and funding. Some organizations struggle with maintaining consistent participation and momentum over time.
Technical knowledge gaps can hinder quality circles when dealing with complex Six Sigma tools.
Teams might feel overwhelmed by statistical requirements or struggle to align their practical approaches with Six Sigma’s rigorous methodology.
Cultural resistance sometimes emerges when traditional quality circle methods clash with Six Sigma protocols.
Overcoming Implementation Barriers
Organizations can address these challenges through structured support systems.
Regular training sessions help bridge knowledge gaps, while dedicated mentoring programs connect quality circles with Six Sigma experts.
Clear communication channels between circles and Six Sigma teams prevent duplicate efforts and resource conflicts.
Success requires balanced resource allocation and management support. Organizations should establish clear boundaries between quality circle activities and Six Sigma projects.
Creating standardized procedures for escalating complex issues helps circles maintain their effectiveness while leveraging Six Sigma expertise when needed.
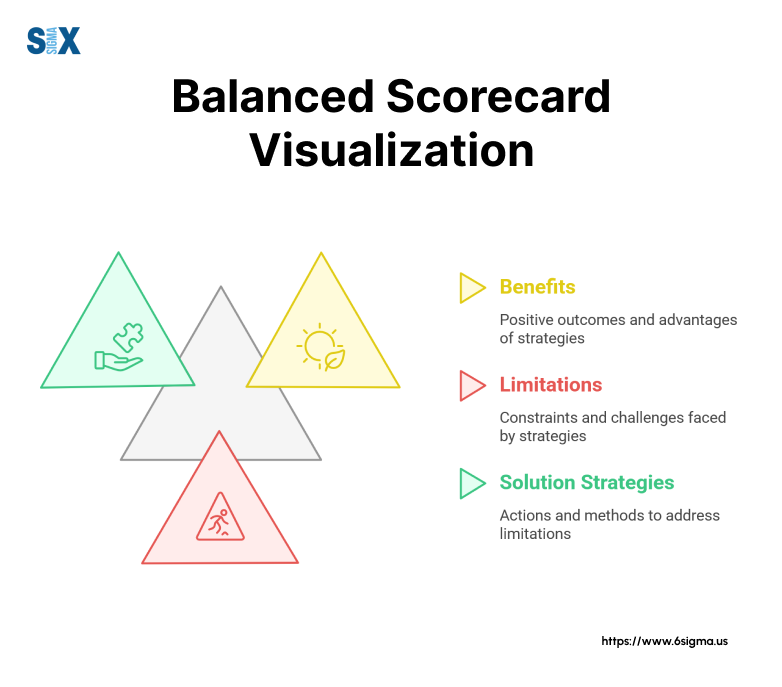
Looking Ahead: Quality Circle In Modern Quality Management
Quality circles remain vital tools in today’s quality management systems, particularly when integrated with Six Sigma methodologies.
Their ability to engage frontline workers while supporting data-driven improvements makes them valuable assets for organizations seeking operational excellence.
The future of quality circles points toward increased digitalization and remote collaboration capabilities.
Modern quality circles will likely incorporate artificial intelligence tools for data analysis while maintaining their fundamental focus on employee-driven improvements. This evolution ensures their relevance in Industry 4.0 environments.
Organizations that successfully blend quality circles with Six Sigma create robust improvement systems. This combination delivers both strategic process improvements and daily operational excellence.
As businesses face increasing quality demands and competitive pressures, this integrated approach becomes more crucial for sustainable success.
SixSigma.us offers both Live Virtual classes as well as Online Self-Paced training. Most option includes access to the same great Master Black Belt instructors that teach our World Class in-person sessions. Sign-up today!
Virtual Classroom Training Programs Self-Paced Online Training Programs