Process Tolerance: Balancing Quality & Cost | A Comprehensive Guide
Ensuring quality while optimizing costs is so important. This delicate balance surfaces through comprehensive knowledge and application of process tolerance – a core concept in quality control and enhancement techniques like Six Sigma.
With over two decades as a Master Black Belt, I’ve seen process tolerancing’s profound impacts firsthand working extensively with major brands.
Insights gained illuminate tolerance examination’s intricate details and role reducing defects, improving consistency and driving cost-efficiency.
Process tolerance defines an acceptable production variation range, establishing standards determining a process’s capability.
It establishes minimum and maximum target value deviations, often shown as +/- or combining average and deviation standards.
Striking this quality-cost balance intricately through effective tolerancing demands deep understanding of approaches, strengths and limitations.
Key Highlights
- Understand the fundamentals of process tolerance and its critical role in balancing quality and cost optimization
- Gain insights into the three primary approaches to tolerancing: worst-case, statistical, and process tolerancing
- Learn how to determine appropriate tolerance levels based on factors like functional limits, usage conditions, process capability studies, and operational windows
- Explore the relationship between process tolerance and Six Sigma quality, including defects per million calculations and tolerance specifications
- Discover practical applications and case studies highlighting the benefits of process tolerancing in addressing challenges like multiple identical components, off-center processes, and industry-specific scenarios
- Master the art of accurate output prediction and achieving quality at lower costs through the effective implementation of process tolerancing principles
Understanding Process Tolerance: Balancing Quality and Cost
At the heart of any manufacturing or production process lies a delicate balance between achieving consistent, high-quality output and minimizing costs.
This balance is largely governed by the concept of process tolerance – a critical factor that sets the standard by which the capability of a process is determined.
What is Process Tolerance?
Process tolerance is a value that defines the acceptable range of variation in the production of goods.
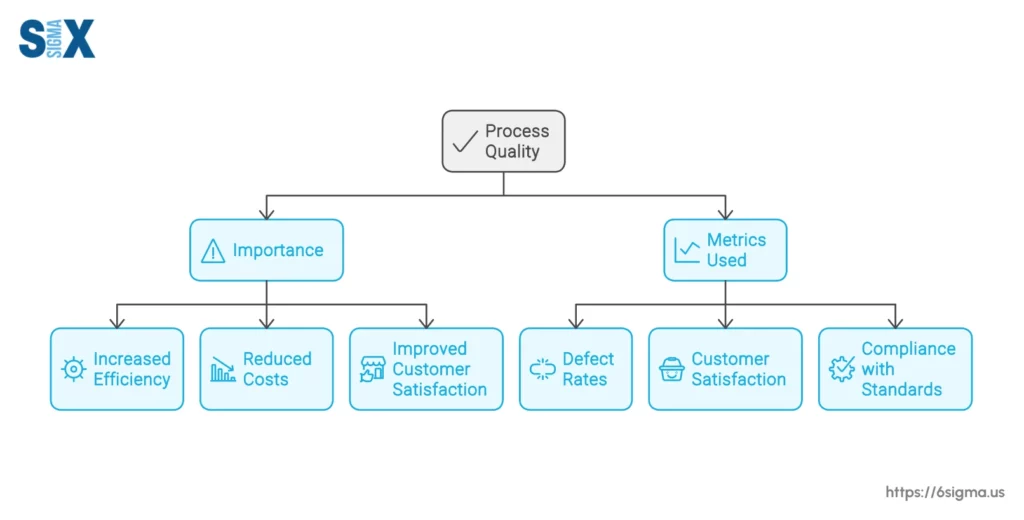
It establishes the minimum and maximum deviations from a target value or specification, often represented by a +/- value or a combination of an average and standard deviation requirement.
For instance, a paint color may require 5 oz (+/- 0.2) of red dye, meaning the end products can have a weight between 4.8 and 5.2 oz and still be considered within tolerance.
Tolerance limits and specification ranges play a crucial role in defining the boundaries of acceptability.
Units falling outside these predetermined limits are considered nonconformances or defects, potentially compromising product quality and functionality.
Importance of Process Tolerance
Implementing appropriate process tolerances is essential for ensuring product consistency, safety, and reliability.
In industries where human safety is paramount, such as aerospace or medical device manufacturing, tolerances are typically set to stricter standards to minimize the risk of defects.
However, excessively tight tolerances can also lead to increased production costs and higher rates of waste, as even minor deviations may result in rejected units.
Finding the right balance between quality requirements and cost optimization is key, and this is where a comprehensive understanding of process tolerance becomes invaluable.
Approaches to Tolerancing
There are three primary approaches to tolerancing: worst-case, statistical, and process tolerancing.
Each method has its strengths, limitations, and applications, and understanding their nuances is crucial for effective tolerance analysis and process control.
Worst-Case Tolerancing
Worst-case tolerancing is a conservative approach that aims to account for the most extreme scenarios.
It assumes that all inputs will simultaneously be at their respective tolerance limits, representing a highly unlikely, if not impossible, situation in most real-world processes.
While this method ensures that the output will remain within its tolerance range as long as the inputs are within their specified limits, it often leads to an overestimation of variation.
This can result in unnecessarily tight tolerances for inputs, driving up costs and potentially increasing waste.
Statistical Tolerancing
Statistical tolerancing, on the other hand, takes a more realistic approach by assuming that processes are centered and that inputs vary independently according to a statistical distribution.
This method relies on techniques like propagation of error and variation transmission analysis to predict the average and standard deviation of the output based on the statistical tolerances of the inputs.
While statistical tolerancing can provide narrower tolerance ranges for outputs, potentially reducing costs, it can also underestimate variation if the assumption of centered processes is violated.
Off-center or unstable processes may result in defective products, even when inputs meet their statistical tolerance requirements.
Process Tolerancing: A Unified Approach
Process tolerancing represents a unified approach that combines the strengths of worst-case and statistical tolerancing while addressing their limitations.
It allows for the specification of both worst-case tolerances (for averages) and statistical tolerances (for variation around the average) within the same analysis.
This flexibility enables accurate representation of input behaviors, whether they are best described by worst-case scenarios, centered processes, or off-center conditions.
By providing a middle ground between the two extremes, process tolerancing offers a powerful tool for predicting output behavior accurately while balancing quality and cost considerations.
Determining Process Tolerance
Selecting the appropriate process tolerance for each input variable is a critical step in ensuring accurate tolerance analysis and effective process control.
The choice depends on various factors, including functional limits, usage conditions, process capability studies, and operational windows.
Worst-Case Tolerance Considerations
Worst-case tolerances are often the most appropriate choice for inputs representing usage or environmental conditions, such as temperature or humidity, where individual units may be continuously exposed to extreme conditions.
These tolerances are also suitable for inputs that are outside the direct control of the designer or manufacturer.
Statistical Tolerance Considerations
Statistical tolerances are well-suited for inputs with automatic controls that keep them centered on the target value, such as die temperature in a heat-sealing process.
Stable processes and in statistical control, as determined by capability studies or control charts, can also be represented by statistical tolerances, provided the assumption of independence between inputs is met.
Process Tolerance Considerations
Process tolerances are particularly useful for manually controlled processes, where an operating window can be maintained around the target value using control charts or other monitoring techniques.
They can also account for deterioration or drift over time, combining the effects of manufacturing variation and long-term changes in a single tolerance specification.
In cases where multiple identical components are used, process tolerances can capture the correlated behavior arising from lot-to-lot variation, providing a more accurate representation than independent statistical tolerances.
Process Tolerance and Six Sigma Quality
The pursuit of process excellence and defect reduction is a central tenet of the Six Sigma methodology, and process tolerance plays a pivotal role in achieving these goals.
Six Sigma Requirements
Six Sigma quality is defined as a measurable characteristic, such as flow rate or seal strength, having no more than 3.4 defects per million units produced.
This stringent requirement translates into specific process tolerance specifications, where the average must be within a certain range, and the standard deviation must not exceed a predetermined value.
Implementing Six Sigma Quality
To meet Six Sigma standards, organizations must implement rigorous process monitoring and control measures.
Control charts are invaluable tools for tracking process performance and ensuring that averages and variations remain within the specified tolerance limits.
Continuous improvement efforts, guided by process tolerancing principles, can help identify opportunities for tightening tolerances, reducing variation, and driving defect rates towards the Six Sigma goal of 3.4 defects per million or fewer.
Conclusion
Process tolerancing emerges crucial for quality and cost optimization pursuits. Its unified approach combining worst-case and statistical methodology strengths offers unparalleled flexibility and accuracy in envisioning output behavior.
The power to tailor specifications to each variable’s unique characteristics – be it functional boundaries, usage situations, process capabilities or operational parameters – equips organizations achieving the ideal balance of high quality, low costs.
Through effectively applying process tolerancing principles, companies unlock perks of reliable planning, defect declines and ultimately, building quality products while keeping costs down.
By embracing this potent methodology, businesses can stay ahead of rivals and pave the road to enduring success in challenging global market environments, where demands constantly evolve.
Process tolerancing demonstrates the payoffs awaiting those committed to performance and efficiency progress through an analytical mindset.
SixSigma.us offers both Live Virtual classes as well as Online Self-Paced training. Most option includes access to the same great Master Black Belt instructors that teach our World Class in-person sessions. Sign-up today!
Virtual Classroom Training Programs Self-Paced Online Training Programs