The Importance of Having a Process Improvement Plan for Your Business
A process improvement plan is a strategic roadmap designed to enhance organizational efficiency, reduce waste, and boost overall performance.
It’s a systematic approach that combines data-driven analysis with proven methodologies to identify, implement, and sustain meaningful changes in business processes.
Key Highlights
- Understanding process improvement plan fundamentals
- Step-by-step guide to creating effective plans
- Exploring key methodologies: Lean, Six Sigma, PDCA
- Implementing and managing improvement initiatives
- Best practices for sustainable process enhancement
- Driving operational excellence through continuous improvement
Understanding Process Improvement Plan
Process improvement plan is the backbone of any successful business optimization strategy.
It’s a structured approach to identifying, analyzing, and enhancing existing business processes to meet new goals and objectives.
The importance of such a plan cannot be overstated – it’s the roadmap that guides organizations towards operational excellence and competitive advantage.
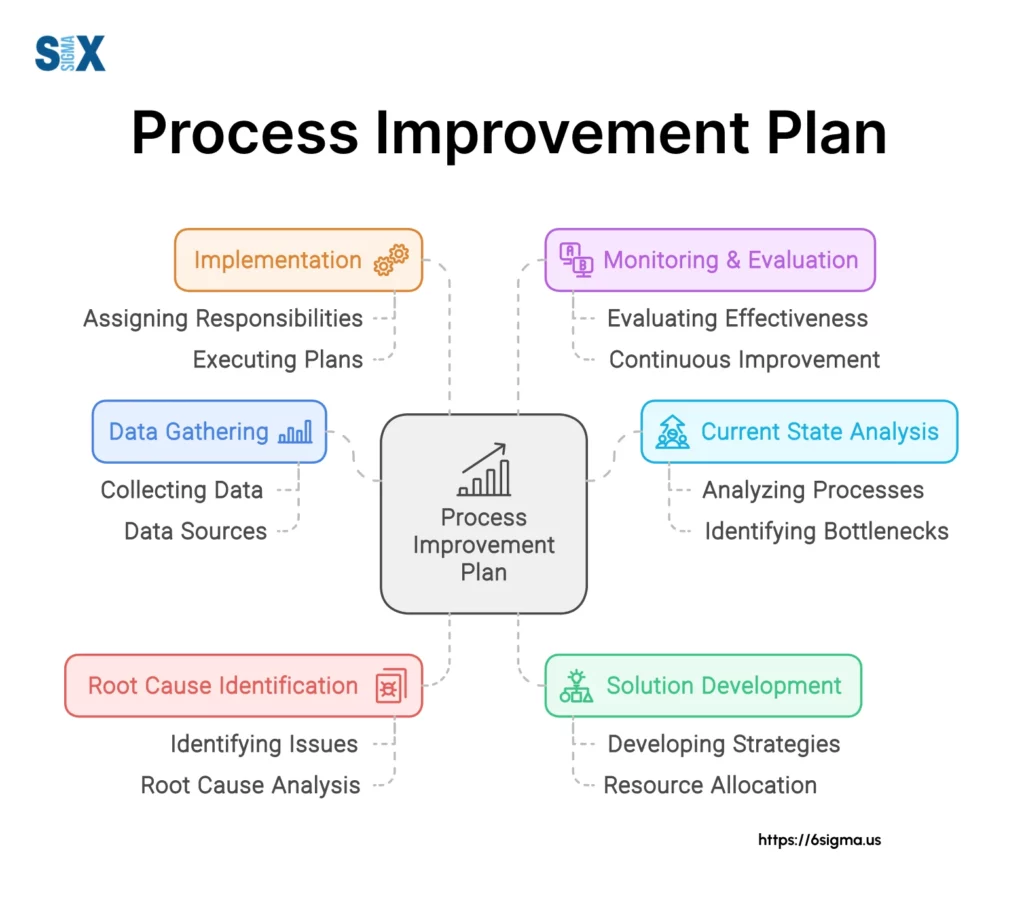
Key Components of a Process Improvement Plan
A robust process improvement plan consists of several critical components:
- Clear objectives: Define what you want to achieve with your improvement efforts.
- Process mapping: A detailed visualization of current workflows.
- Data collection and analysis: Gathering and interpreting relevant metrics.
- Root cause analysis: Identifying the underlying issues, not just symptoms.
- Improvement strategies: Developing targeted solutions to address identified problems.
- Implementation plan: A timeline and resource allocation for executing improvements.
- Monitoring and control measures: Systems to track progress and maintain improvements.
Combining Six Sigma certification with specialized root cause analysis training equips teams to tackle complex operational challenges.
Benefits of Business Process Optimization
The benefits of implementing a process improvement plan are far-reaching.
- Increased efficiency and productivity
- Cost reduction through waste elimination
- Enhanced product or service quality
- Improved customer satisfaction
- Better employee morale and engagement
- Increased agility and adaptability to market changes
- Compliance with industry standards and regulations
Steps to Create an Effective Process Improvement Plan
The first step in any process improvement initiative is to gain a clear understanding of your current processes.
Mapping Current Processes and Workflow Analysis
This involves creating detailed process maps or flowcharts.
This technique helps identify value-added and non-value-added activities, providing a foundation for improvement efforts.
Identifying Bottlenecks and Areas for Improvement
Once you have a clear picture of your processes, the next step is to identify bottlenecks and inefficiencies.
This is where data becomes crucial. Using statistical tools and methodologies like Six Sigma, we can pinpoint areas that are under performing or causing delays.
Look for excessive wait times, redundant steps, or processes with high error rates.
Setting Performance Metrics and KPIs for a Process Improvement Plan
To drive improvement, you need to know what success looks like.
This means establishing clear, measurable performance metrics and Key Performance Indicators (KPIs).
The key is to choose metrics that align with your overall business objectives.
Developing Solutions and Process Redesign Strategies
With problems identified and goals set, it’s time to develop solutions.
This is where creativity meets data-driven decision making. Techniques like brainstorming sessions, cause-and-effect diagrams, and design of experiments can help generate and evaluate potential solutions.
The goal is to redesign processes to eliminate waste, reduce variability, and increase value.
Creating an Implementation Timeline for a Process Improvement Plan
The final step in planning is to create a realistic timeline for implementation.
This should include milestones, resource allocation, and contingency plans.
Remember, process improvement is often an iterative process. Be prepared to adjust your timeline as you learn and encounter unexpected challenges.
Methodologies for Process Improvement
Under methodologies we get to see various methods for process improvements including:
Lean Principles and Waste Reduction
Lean methodology, which I’ve successfully implemented in manufacturing and service industries alike, focuses on maximizing customer value while minimizing waste.
The core principle is to create more value for customers with fewer resources. Key concepts include:
- Identifying value from the customer’s perspective
- Mapping the value stream
- Creating flow by eliminating interruptions
- Establishing pull systems
- Continuously seeking perfection
Pairing Lean fundamentals with Six Sigma certification creates a powerful combination for organizations aiming to eliminate waste and variability.
Six Sigma Methodology within the Process Improvement Plan
Six Sigma, a methodology I’ve been passionate about throughout my career, is a data-driven approach to eliminating defects and reducing variability in processes.
It follows the DMAIC framework:
- Define the problem and project goals
- Measure current process performance
- Analyze to determine root causes of problems
- Improve the process by implementing solutions
- Control to sustain the improvements
Six Sigma’s statistical rigor makes it particularly effective for complex problems where the root cause isn’t immediately apparent.
Six Sigma Black Belt-certified experts often achieve faster ROI due to their advanced mastery of statistical analysis and project leadership.
PDCA Cycle for Continuous Improvement
The Plan-Do-Check-Act (PDCA) cycle, also known as the Deming Cycle, is a four-step model for carrying out change.
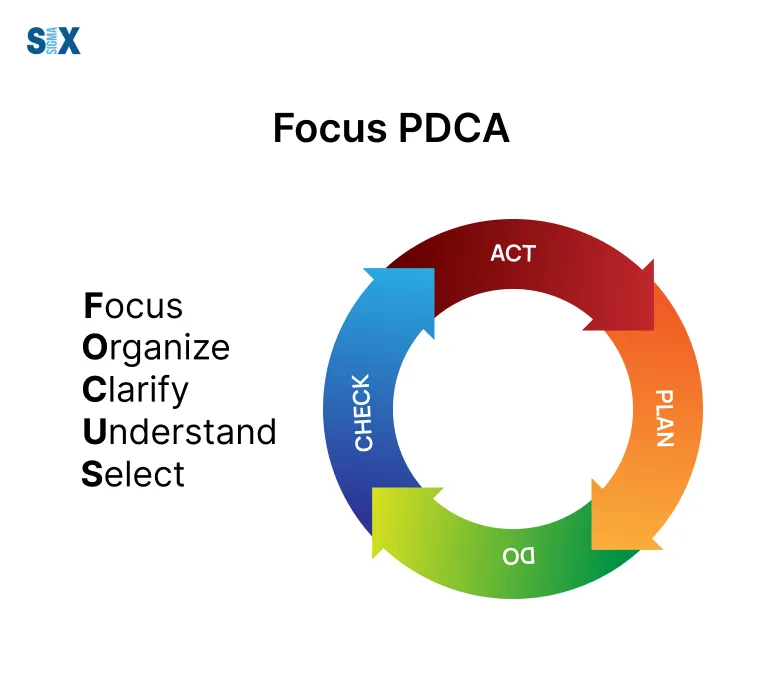
It’s a simple yet powerful tool for continuous improvement:
- Plan: Identify and analyze the problem
- Do: Develop and implement a solution
- Check: Evaluate the results
- Act: Standardize the solution if successful, or begin the cycle again
I’ve found PDCA particularly useful for quick improvements and for fostering a culture of continuous improvement across all levels of an organization.
Implementing Your Process Improvement Plan
Change Management Strategies
Implementing process improvements often requires significant organizational change.
Effective change management strategies include:
- Clear communication of the reasons for change
- Involvement of stakeholders at all levels
- Addressing resistance proactively
- Providing necessary resources and support
- Celebrating early wins to build momentum
Employee Engagement and Training for Process Improvement Plan
Engaged employees are crucial for successful process improvement.
Training is a key component of this.
This not only built necessary skills but also fostered buy-in and enthusiasm for the improvement initiatives.
Standardized Work Procedures
Standardization is crucial for sustaining improvements.
This involves documenting best practices, creating clear work instructions, and ensuring consistency across operations.
Monitoring Progress and Measuring ROI of your Process Improvement Plan
Continuous monitoring is essential to ensure that improvements are sustained and to quantify the Return on Investment (ROI) of your efforts.
Use the KPIs established earlier to track progress. Regular reviews and audits can help identify any slippage back to old practices.
Remember, the goal is not just short-term gains, but long-term, sustainable improvement.
Best Practices for Successful Process Improvement
Some of the best techniques and practice for a succesful process improvement in your organization.
Fostering a Culture of Continuous Improvement
A culture of continuous improvement is the bedrock of sustained success.
This means encouraging all employees to look for ways to improve their work processes constantly.
- Leadership commitment and visible support
- Empowering employees to make improvements
- Recognizing and rewarding improvement efforts
- Making continuous improvement part of performance evaluations
Data-driven decision making for Process Improvement Plan
There’s no excuse for gut-feel decision making. Use statistical tools to analyze data and drive decisions.
This could involve simple trend analysis or more advanced techniques like Design of Experiments.
Stakeholder feedback and communication
Regular communication with all stakeholders – employees, customers, suppliers – is crucial.
Their feedback can provide valuable insights into areas for improvement that might not be apparent from internal data alone. Establish formal feedback mechanisms and act on the input received.
Regular process documentation and updates
As processes evolve, it’s important to keep documentation up-to-date. This ensures that improvements are sustained and that best practices are shared across the organization.
Driving Operational Excellence Through Process Improvement
From understanding the fundamentals and methodologies to implementation strategies and best practices, the key is to approach improvement systematically and continuously.
Long-term benefits of process improvement plans
The long-term benefits of commitment to process improvement are substantial.
Organizations that excel at this create a sustainable competitive advantage, are more adaptable to change, and are better positioned to meet future challenges.
Next steps for organizations
Organizations looking to grow and improve their process improvement journey, starting with a honest assessment of current capabilities.
Identify areas of greatest opportunity or need, invest in training and tools, and remember that improvement is a journey, not a destination.
SixSigma.us offers both Live Virtual classes as well as Online Self-Paced training. Most option includes access to the same great Master Black Belt instructors that teach our World Class in-person sessions. Sign-up today!
Virtual Classroom Training Programs Self-Paced Online Training Programs