Mastering Process Improvement Methodologies: 2025
Process improvement methodologies are structured approaches used to identify, analyze, and optimize business processes with the goal of increasing efficiency, reducing waste, and enhancing overall quality.
These methodologies provide a systematic framework for organizations to continuously evolve and adapt to changing market demands, technological advancements, and customer expectations.
Key Highlights
- Definition and importance of process improvement
- Overview of popular frameworks
- Analysis tools
- Implementation strategies and change management techniques
- Advanced approaches
- Measuring improvements
- Future trends
Introduction to Process Improvement Methodologies
Ever wonder why some companies seem to run like well-oiled machines while others struggle to keep up?
The secret often lies in their approach to process improvement.
At its core, process improvement is all about identifying, analyzing, and refining business processes to boost efficiency, cut costs, and enhance quality.
It’s not just about fixing what’s broken; it’s about constantly seeking ways to do things better.
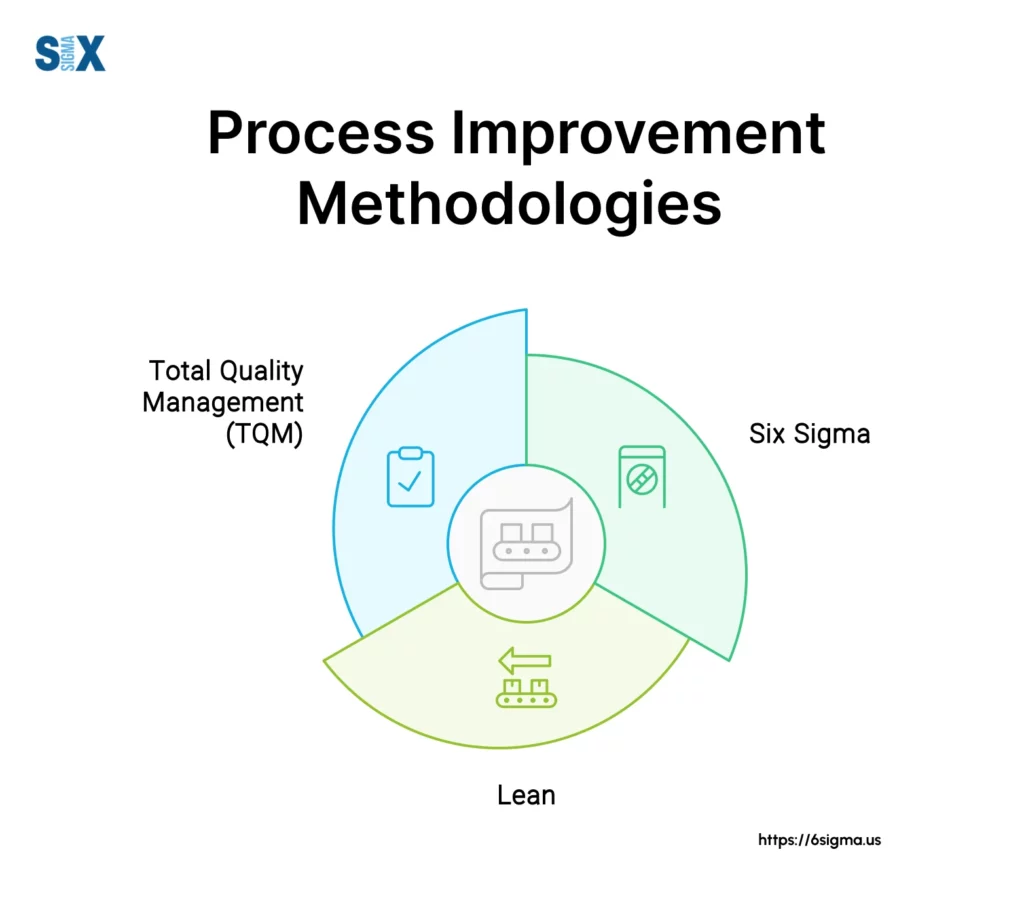
Overview of Continuous Improvement Approaches
Speaking of continuous improvement, these methodologies aren’t just buzzwords; they’re powerful tools that, when applied correctly, can transform your organization.
Some of the most popular continuous improvement approaches include:
- Six Sigma
- Lean Manufacturing
- Total Quality Management (TQM)
- Agile Methodology
- Kaizen
Each of these has its own unique focus and set of tools, but they all share a common goal: to create a culture of ongoing improvement and optimization.
The key is to find the approach (or combination of approaches) that best fits your organization’s needs and culture.
Popular Process Improvement Frameworks
First up in our process improvement lineup is Six Sigma.
Six Sigma and DMAIC methodology
Born in the manufacturing world but now widely used across industries, Six Sigma is all about reducing variability and defects in processes.
To achieve near-perfection, with no more than 3.4 defects per million opportunities.
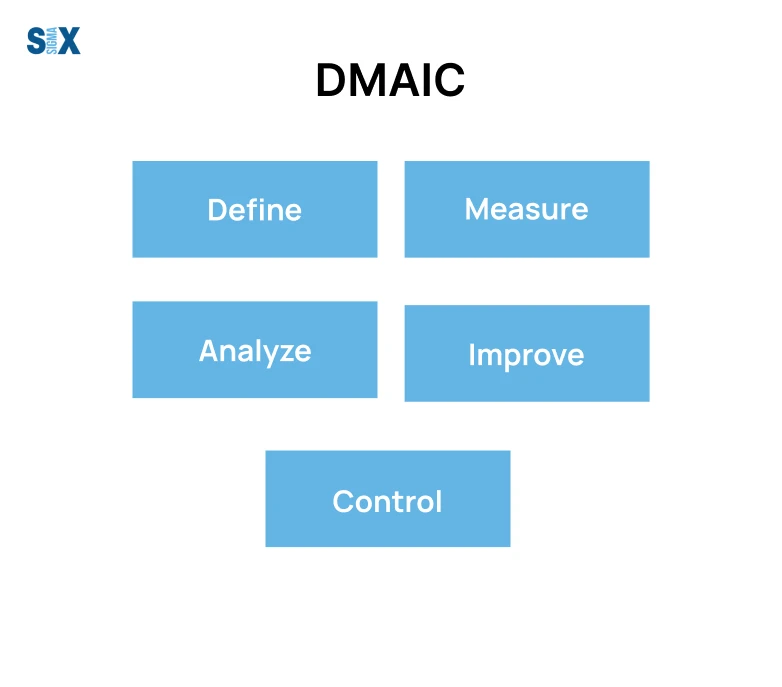
At the heart of Six Sigma is the DMAIC methodology:
- Define the problem
- Measure current performance
- Analyze root causes
- Improve the process
- Control to maintain improvements
This structured approach helps teams tackle complex problems systematically. It’s like having a roadmap for improvement.
Lean manufacturing and waste elimination as Process Improvement Methodologies
If Six Sigma is about precision, Lean is all about trimming the fat.
Originated by Toyota, Lean focuses on eliminating waste in all its forms – overproduction, waiting time, unnecessary transport, excess inventory, and more.
The goal of Lean is to create more value for customers with fewer resources. It’s about doing more with less, which, let’s face it, is music to any manager’s ears.
Total Quality Management (TQM) principles
Total Quality Management, or TQM, takes a holistic approach to improvement.
It’s based on the idea that creating a quality culture throughout an organization leads to long-term success. TQM emphasizes:
- Customer focus
- Total employee involvement
- Process-centered approach
- Integrated system
- Strategic and systematic approach
- Continual improvement
- Fact-based decision making
- Communications
TQM isn’t just about improving processes; it’s about transforming the entire organizational culture.
It’s a big undertaking, but when done right, it can lead to significant improvements in quality, productivity, and customer satisfaction.
Agile methodology for flexible improvements
While Agile is often associated with software development, its principles can be applied to process improvement in any industry.
Agile is all about flexibility, collaboration, and rapid iteration. Instead of spending months or years on a big improvement project, Agile encourages small, frequent changes and constant feedback.
The Agile approach to process improvement might involve:
- Breaking down large improvement initiatives into smaller, manageable chunks
- Implementing changes quickly and getting feedback
- Adapting plans based on what’s learned
- Encouraging cross-functional collaboration
For organizations dealing with rapidly changing environments, Agile can be a powerful tool for staying nimble and responsive.
Kaizen and the PDCA cycle as Process Improvement Methodologies
Last but not least, let’s talk about Kaizen. This Japanese term, which roughly translates to “change for better”, embodies the idea of continuous improvement through small, incremental changes.
It’s not about making big, dramatic changes, but rather fostering a culture where everyone is constantly looking for ways to improve their work.
Central to Kaizen is the PDCA (Plan-Do-Check-Act) cycle:
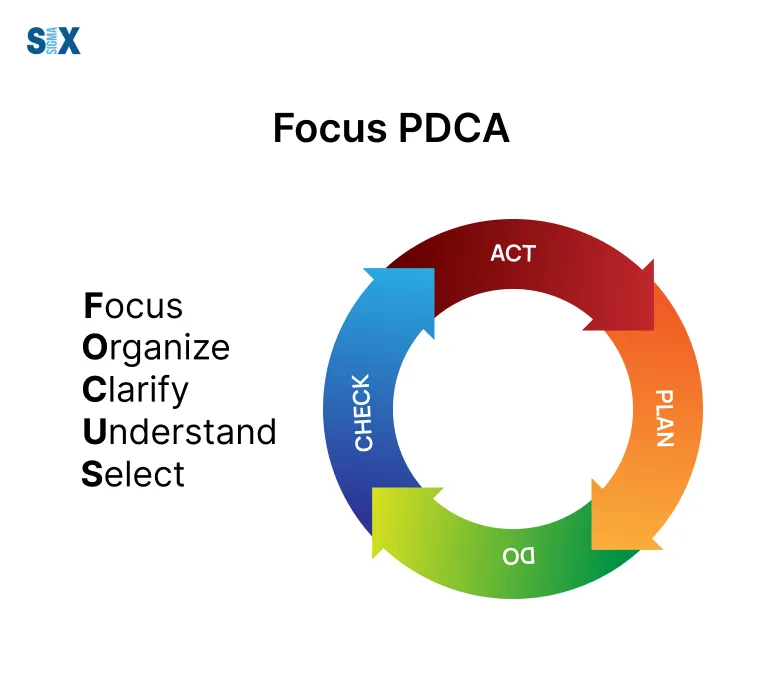
- Plan: Identify an opportunity and plan for change
- Do: Implement the change on a small scale
- Check: Use data to analyze the results of the change
- Act: If the change was successful, implement it on a wider scale and continuously assess your results
The beauty of Kaizen is that it empowers everyone in the organization to contribute to improvement efforts.
It’s not just top-down; it’s a grassroots approach to creating a culture of continuous improvement.
Tools and Techniques for Process Analysis
These are some specific tools and techniques for process analysis.
Value stream mapping and process mapping
Value stream mapping is a lean management technique that helps you visualize the steps involved in taking a product or service from its beginning through to the customer.
Process mapping, on the other hand, is a more general term for any diagram that shows the steps in a process.
This could be a simple flowchart or a more complex diagram showing decision points, inputs, and outputs.
Root Cause Analysis and Fishbone Diagrams as Process Improvement Methodologies
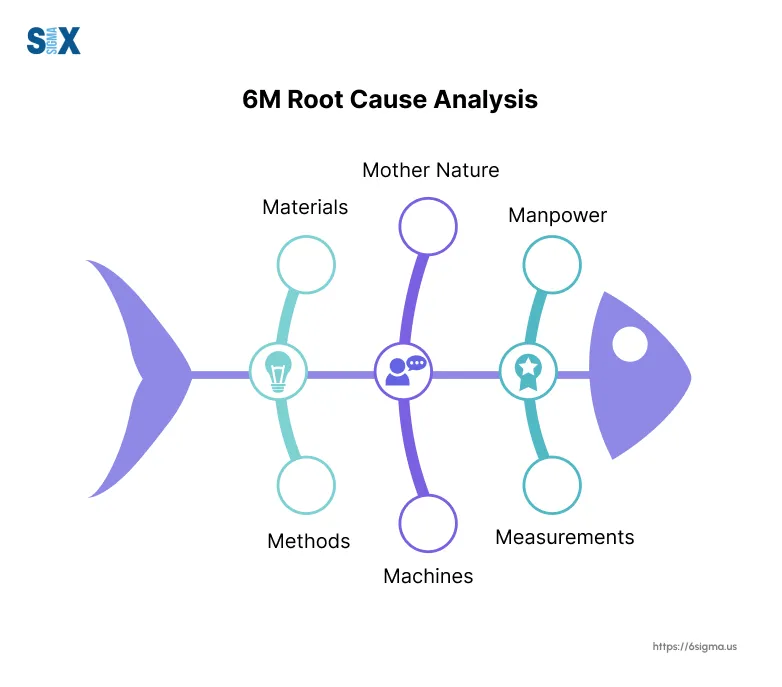
When something goes wrong in a process, it’s tempting to jump straight to solutions. But hold your horses!
Before you can fix a problem, you need to understand its root cause. That’s where root cause analysis comes in.
One popular tool for root cause analysis is the fishbone diagram, also known as the Ishikawa diagram. It looks like a fish skeleton, with the main problem at the “head” and potential causes branching off like bones.
This visual representation helps teams brainstorm and categorize potential causes of a problem.
Remember, the goal isn’t to find someone to blame, but to identify the underlying issues that need to be addressed. It’s about fixing the process, not pointing fingers.
SIPOC analysis for process understanding
SIPOC stands for Suppliers, Inputs, Process, Outputs, and Customers. It’s a tool used to get a high-level view of a process before diving into the details. Here’s how it breaks down:
- Suppliers: Who provides inputs to the process?
- Inputs: What materials, information, or other resources go into the process?
- Process: What are the main steps in the process?
- Outputs: What does the process produce?
- Customers: Who receives the outputs?
SIPOC is great for getting everyone on the same page about the scope and boundaries of a process. It’s often used at the start of an improvement project to ensure everyone understands what’s being analyzed.
Bottleneck analysis and Theory of Constraints
A bottleneck is any point in a process that limits its overall throughput.
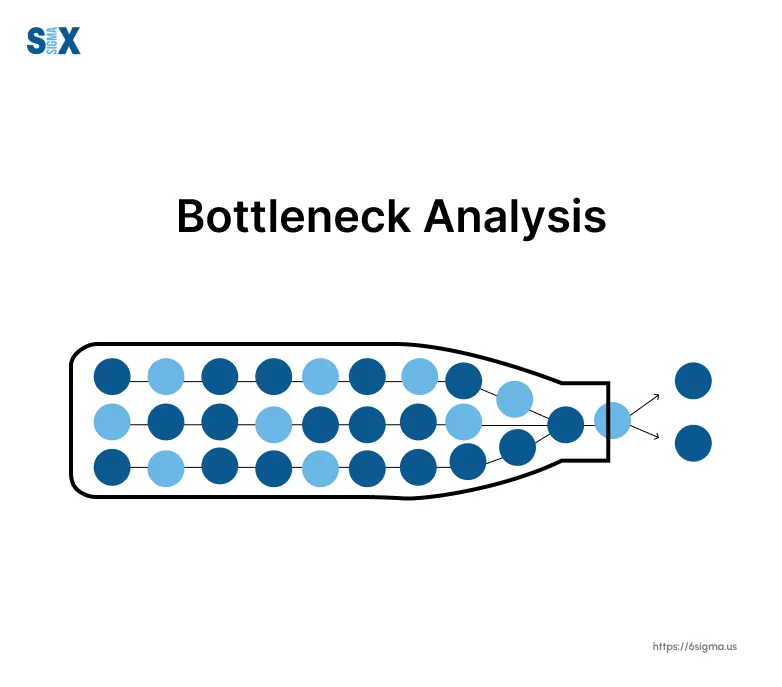
The Theory of Constraints, developed by Dr. Eliyahu Goldratt, suggests that every system has at least one constraint (or bottleneck) that limits its performance.
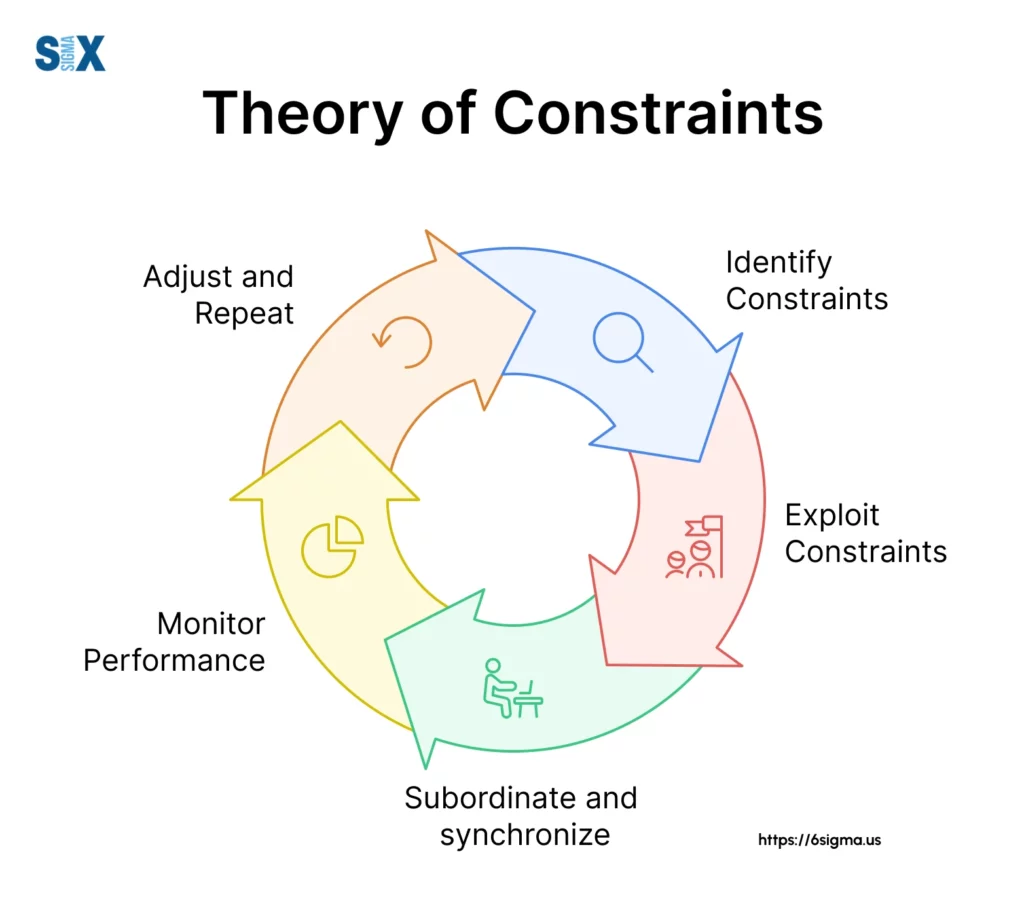
The steps in the Theory of Constraints are:
- Identify the constraint
- Exploit the constraint (get the most out of it)
- Subordinate everything else to the constraint
- Elevate the constraint (if needed)
- Repeat the process
By focusing on identifying and addressing bottlenecks, organizations can often achieve significant improvements in their overall process performance.
It’s about finding that weak link in the chain and strengthening it.
Implementing Process Improvement Methodologies
There’s no one-size-fits-all answer. The right methodology (or combination of methodologies) depends on your organization’s specific needs, culture, and goals.
Here are a few factors to consider:
- The nature of your processes: Are they highly variable or standardized?
- Your organization’s culture: Is it more suited to gradual change or radical transformation?
- Available resources: Do you have the time and budget for extensive training?
- The scale of improvement needed: Are you looking for incremental improvements or a complete overhaul?
Remember, it’s not about picking the “best” methodology, but the one that’s best for you.
And don’t be afraid to mix and match – many organizations find success in combining elements from different approaches.
Change Management and Employee Engagement
The best process improvement methodology in the world won’t do you any good if your employees aren’t on board.
That’s where change management comes in.
Change management is all about guiding your organization through the transition from current processes to improved ones. It involves:
- Communicating the need for change
- Involving employees in the improvement process
- Providing training and support
- Addressing resistance to change
- Celebrating successes along the way
Employee engagement is crucial. After all, your employees are the ones who know your processes inside and out.
They’re often the best source of improvement ideas, and they’re certainly the ones who will be implementing any changes.
Setting up Key Performance Indicators (KPIs) for Process Improvement Methodologies
Setting up the right Key Performance Indicators (KPIs) is crucial.
KPIs are quantifiable measures that help you track progress towards your improvement goals. They might include things like:
- Cycle time
- Defect rate
- Customer satisfaction scores
- Cost per unit
- Employee productivity
The key is to choose KPIs that align with your overall business objectives and the specific goals of your improvement initiative.
Advanced Process Improvement Approaches
These sophisticated techniques offer powerful tools for organizations seeking to push the boundaries of operational excellence.
Lean Six Sigma: Combining methodologies
Lean Six Sigma integrates the waste-elimination focus of Lean with the defect-reduction approach of Six Sigma.
This synergy creates a robust framework for process improvement that addresses both efficiency and quality.
Business Process Management (BPM) systems as Process Improvement Methodologies
Business Process Management (BPM) systems represent a holistic approach to process improvement that encompasses the entire lifecycle of business processes.
These systems provide a framework for designing, executing, monitoring, and optimizing business processes across an organization.
Just-in-Time (JIT) and Kanban Techniques
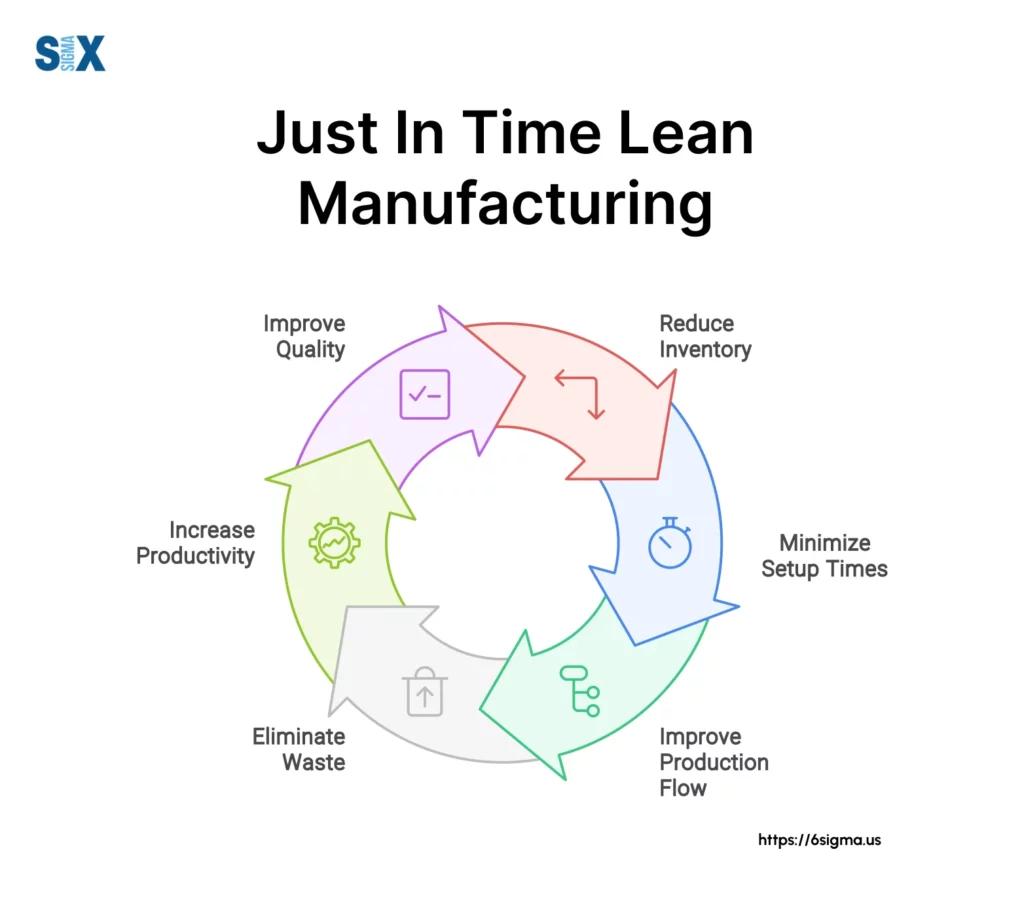
Just-in-Time (JIT) and Kanban are closely related techniques that originated in Japanese manufacturing but have since found applications across various industries.
JIT focuses on producing goods exactly when they’re needed, reducing inventory costs and improving efficiency.
Kanban, which means “signboard” in Japanese, is a visual system for managing work-in-progress and ensuring a smooth flow of production.
5S method for workplace organization
The 5S method is a systematic approach to workplace organization that originated in Japan.
The five S’s stand for Sort (Seiri), Set in Order (Seiton), Shine (Seiso), Standardize (Seiketsu), and Sustain (Shitsuke).
While it might seem simple, I’ve found that implementing 5S can have a profound impact on productivity and quality.
Measuring and Sustaining Process Improvements
Implementing process improvements is only half the battle.
To truly drive lasting change and continuous improvement, organizations must have robust systems for measuring performance and sustaining gains over time.
Statistical process control and Benchmarking
Statistical Process Control (SPC) is a method of quality control that uses statistical methods to monitor and control a process.
Benchmarking, on the other hand, involves comparing your processes against industry best practices or competitors.
This can provide valuable insights into areas for improvement and help set realistic performance targets.
Continuous process improvement strategies
Continuous process improvement is not a one-time event but an ongoing journey.
Strategies for sustaining improvement efforts include:
- Regular process audits and reviews
- Employee suggestion systems
- Continuous training and skill development
- Cross-functional improvement teams
- Regular communication of improvement results
One effective approach I’ve used is to establish a formal continuous improvement program with dedicated resources and clear governance structures.
This ensures that improvement efforts remain a priority even as the organization faces day-to-day operational challenges.
Operational excellence and long-term benefits of Process Improvement Methodologies
When process improvement methodologies are successfully implemented and sustained, they can lead to operational excellence.
The long-term benefits of achieving operational excellence include:
- Increased profitability and market share
- Improved customer satisfaction and loyalty
- Enhanced employee engagement and job satisfaction
- Greater agility and adaptability to market changes
- Sustainable competitive advantage
Future Trends in Process Improvement Methodologies
As we look to the future, several emerging trends are shaping the evolution of process improvement methodologies.
Digital Transformation and Process Automation
Digital technologies are revolutionizing process improvement.
Advanced analytics, artificial intelligence, and robotic process automation (RPA) are enabling organizations to identify improvement opportunities and implement changes at an unprecedented scale and speed.
Data-driven decision making in process improvement
The proliferation of data and advanced analytics tools is enabling more sophisticated, data-driven approaches to process improvement.
The shift towards remote and hybrid work models is necessitating adaptations to traditional process improvement methodologies.
Virtual process mapping sessions, remote data collection techniques, and digital collaboration tools are becoming essential components of the process improvement toolkit.
The fundamental principles of process improvement – systematic analysis, data-driven decision making, and a focus on continuous improvement – remain as relevant as ever.
The key to success will be in adapting these principles to the new realities of the digital age and the evolving nature of work.
SixSigma.us offers both Live Virtual classes as well as Online Self-Paced training. Most option includes access to the same great Master Black Belt instructors that teach our World Class in-person sessions. Sign-up today!
Virtual Classroom Training Programs Self-Paced Online Training Programs