Process Flexibility: A Comprehensive Guide to Adaptable Manufacturing and Business Operations
Process flexibility is a system’s ability to effectively respond to changes in product mix, production volume, and operational conditions. The best part, it achieves it without significant modifications to existing facilities and processes.
Process flexibility is now an absolute necessity in modern manufacturing and business operations. It works on building systems that thrive on change, not just adapt to it.
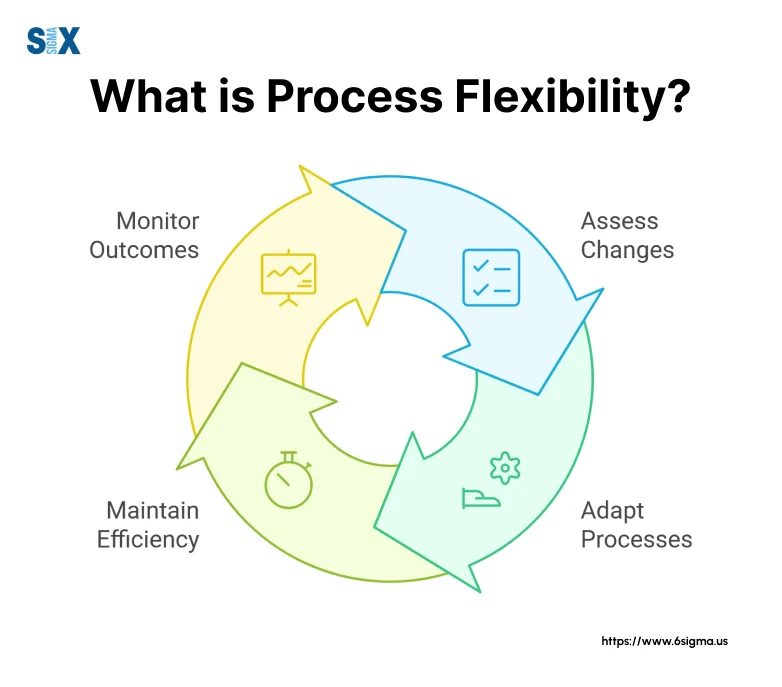
Three critical reasons why organizations must embrace flexible processes:
- Market volatility demands quick adaptation.
- Competitive pressure requires operational agility.
- Resource optimization becomes increasingly critical.
Core Principles of Process Flexibility
Process flexibility fundamentally rests on four core principles.
- The first principle is adaptability in routing. This approach reduces bottlenecks and improves overall throughput. Routing flexibility allows operations to continue smoothly even when certain machines or stations are unavailable.
- The second is volume flexibility. By implementing volume-flexible processes, you can scale production up or down without significant cost implications. This type of process flexibility enables organizations to respond efficiently to market demands while maintaining cost-effectiveness.
- The third is mix flexibility. Implementing this allows production systems to handle various product types simultaneously.
- The fourth type, new product flexibility, allows organizations to introduce new products without major process modifications.
Operations management benefits significantly from process flexibility. Flexible processes contribute to overall operational excellence. Successful process flexibility in operations management typically results in:
- Reduction in changeover times
- Improvement in resource utilization
- Reduction in work-in-progress inventory
Want to Master Process Flexibility and Drive Operational Excellence?
Our Lean Six Sigma Green Belt certification equips you with proven methodologies for process optimization and waste reduction. Transform your organization’s approach to process management!
The Benefits of Manufacturing Process Flexibility: A Data-Driven Analysis
Organizations implementing process flexibility in their manufacturing operations achieve remarkable improvements across multiple performance metrics.
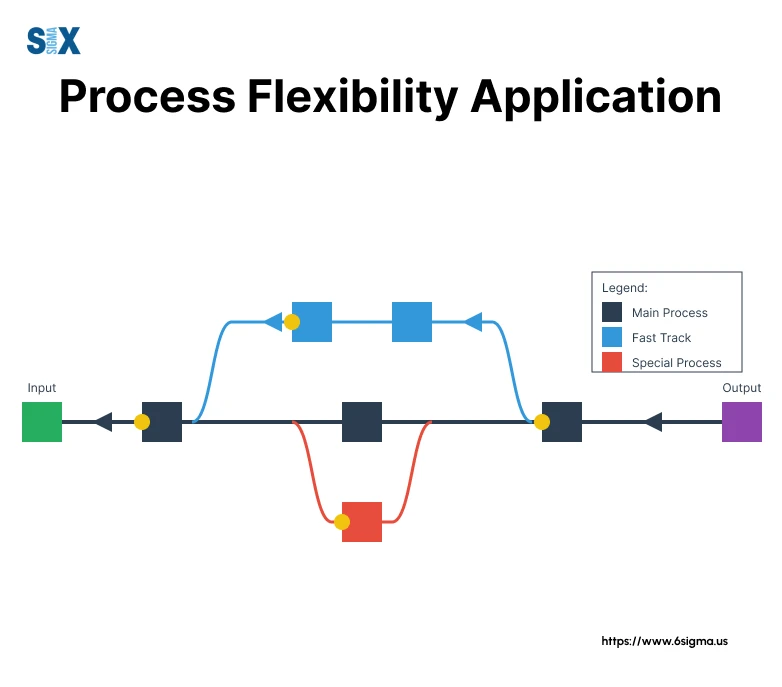
First and foremost, increased efficiency and productivity stand out as primary advantages of manufacturing process flexibility. You can implement flexible manufacturing cells that help increase overall equipment effectiveness (OEE).
Customer satisfaction sees significant enhancement through process flexibility. Implement flexible production systems to reduce lead times. This improvement can lead to an increase in customer satisfaction scores and a reduction in order cancellations. The ability to respond quickly to changing customer demands proved invaluable in maintaining market share and building customer loyalty.
Resource utilization improvements have been particularly noteworthy in my experience. Flexible process implementation can result in a reduction in work-in-progress inventory and an improvement in labor utilization. Itāll also help to identify optimal resource allocation patterns that maximize efficiency while maintaining flexibility.
Market adaptability, perhaps the most crucial benefit, has become increasingly important in today’s volatile business environment. You can implement a “Dynamic Process Architecture”. This approach will allow you to adjust production volumes without significant cost implications, providing crucial adaptability during market fluctuations.
Cost reduction opportunities through process flexibility have been consistently impressive. Cost benefits stem from the “Flexibility Multiplier Effect” ā when processes become more flexible, they naturally eliminate various forms of waste and inefficiency.
Implementing Process Flexibility
Use a systematic approach for process flexibility implementation to consistently deliver results.
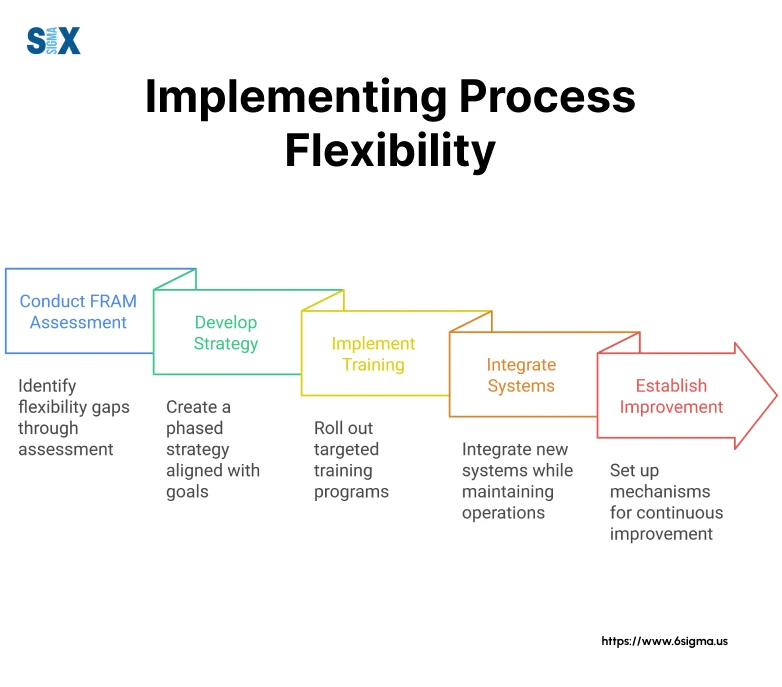
The journey begins with a comprehensive assessment of current processes. Use a “Flexibility Readiness Assessment Matrix” (FRAM). This tool evaluates five critical dimensions: process stability, resource adaptability, technology infrastructure, workforce capabilities, and organizational culture.
Identifying areas for flexibility improvement requires both quantitative and qualitative analysis. Combining process capability indices (Cpk) with value stream mapping provides the most accurate picture of flexibility opportunities.
Developing a flexible strategy is crucial for successful implementation. Use “4D Flexibility Framework”: Define, Design, Deploy, and Develop. This framework can help implement business process flexibility initiatives that improve response times and reduce operational costs. The key is aligning the flexibility strategy with business objectives while considering resource constraints.
Training and change management often determine the success or failure of flexibility initiatives. Resistance to flexible working processes usually stems from insufficient understanding rather than unwillingness to change. To counter this, you can implement a “Flexibility Champions” program where key personnel receive advanced training in process flexibility concepts and become internal advocates for change.
Technology integration plays a vital role in enhancing process flexibility, but it must be approached strategically. Use a technology assessment protocol to ensure new systems support rather than hinder flexibility. This involves evaluating technologies all across, with the “5C criteria”: Connectivity, Configurability, Compatibility, Cost-effectiveness, and Change management capability.
Implementation success requires careful orchestration of these elements. Hereās what I would do when implementing process flexibility:
- Conducted the FRAM assessment, identifying three major flexibility gaps
- Developed a phased implementation strategy aligned with business goals
- Implemented targeted training programs for different organizational levels
- Integrated new flexible manufacturing systems while maintaining operations
- Established continuous improvement mechanisms
Want to Implement Effective Process Flexibility in Your Organization?
Our Process Variables Mapping course shows you how to analyze and optimize your processes for maximum efficiency.
Process Flexibility Case Studies
Letās look at some compelling examples that demonstrate the practical application of flexible manufacturing processes in different industries.
Automotive
In the automotive sector, a tier-one supplier was facing significant challenges with variable demand patterns. Their traditional rigid manufacturing approach resulted in excessive inventory and frequent production disruptions.
By implementing “Dynamic Cell Manufacturing”, they created flexible production cells that could handle multiple product families.
The results were impressive: setup times decreased by 65%, work-in-progress inventory reduced by 40%, and overall equipment effectiveness improved by 35%. This process flexibility example became a benchmark for other automotive suppliers in the region.
Electronics
A major semiconductor manufacturer was managing high-mix, low-volume production efficiently.
They implemented a flexible manufacturing process that incorporated quick-change tooling and modular equipment design.
This approach reduced changeover times from 45 minutes to just 8 minutes, while improving yield by 25%. The key was developing a “Rapid Response Manufacturing Cells” that could switch between different product types with minimal downtime.
MSME
Small businesses often believe process flexibility is beyond their reach, but my experience proves otherwise. A custom furniture manufacturer with just 25 employees implemented scaled-down versions of the same principles used in larger organizations.
By reorganizing their workshop into flexible work cells and training employees in multiple skills, they achieved a 50% reduction in lead times and a 30% increase in customer satisfaction. This demonstrated that process flexibility can be effectively scaled to any business size.
Service
The service industry presents unique opportunities for process flexibility. A healthcare provider applied flexible process principles to their patient care workflows.
By implementing an “Adaptive Service Delivery”, they reduced patient wait times by 45% and improved resource utilization by 35%. The key was creating flexible staff scheduling and standardized yet adaptable treatment protocols that could accommodate varying patient needs.
Measuring Process Flexibility: Metrics To Drive Performance
The key performance indicators (KPIs) for process flexibility must capture both operational agility and business impact. I recommend using the “Flexibility Performance Index” (FPI), which combines multiple metrics into a single, actionable score. This index typically includes changeover time efficiency, volume adaptation rate, and process variation measures.
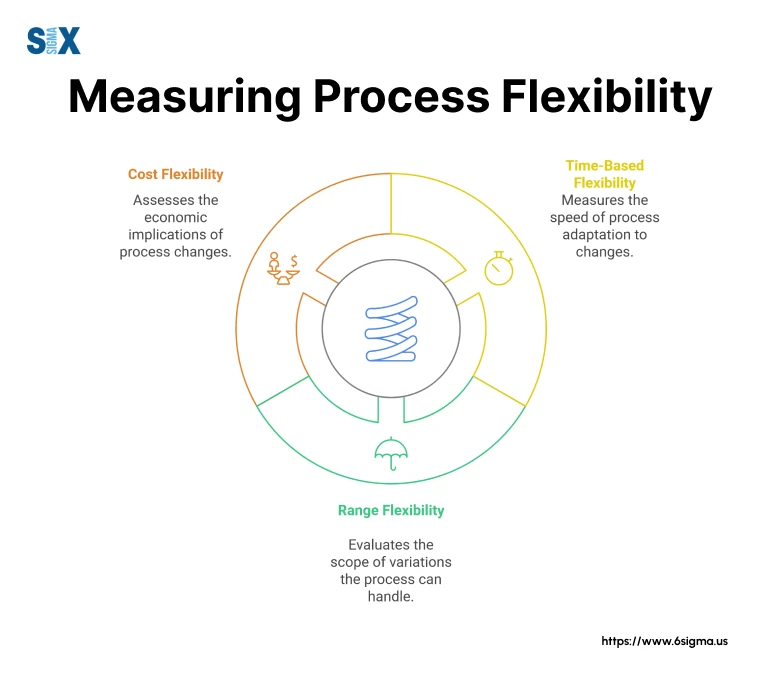
When it comes to benchmarking process flexibility, I advocate for a three-dimensional approach.
- First, we measure time-based flexibility: how quickly can the process adapt to changes?
- Second, we evaluate range flexibility: what is the scope of variations the process can handle?
- Third, we assess cost flexibility: what are the economic implications of process changes?
This framework can help achieve improvement in flexibility metrics while maintaining quality standards.
Continuous improvement in process flexibility requires both leading and lagging indicators. Leading indicators might include operator cross-training levels and equipment modification capabilities while lagging indicators focus on actual performance outcomes like setup time reduction and product mix adaptability.
The measurement system I typically recommend includes what I call the “5C Metrics”:
- Changeover Efficiency: measuring setup time reduction
- Capacity Utilization: tracking resource optimization
- Configuration Adaptability: assessing process modification capability
- Cost Impact: evaluating financial implications of flexibility
- Customer Response: measuring market adaptation speed
Looking to Identify and Address Process Flexibility Challenges?
Learn how to create powerful Cause-and-Effect-Matrices to optimize your processes.
Process Flexibility in the Digital Age: Leveraging Industry 4.0 Technologies
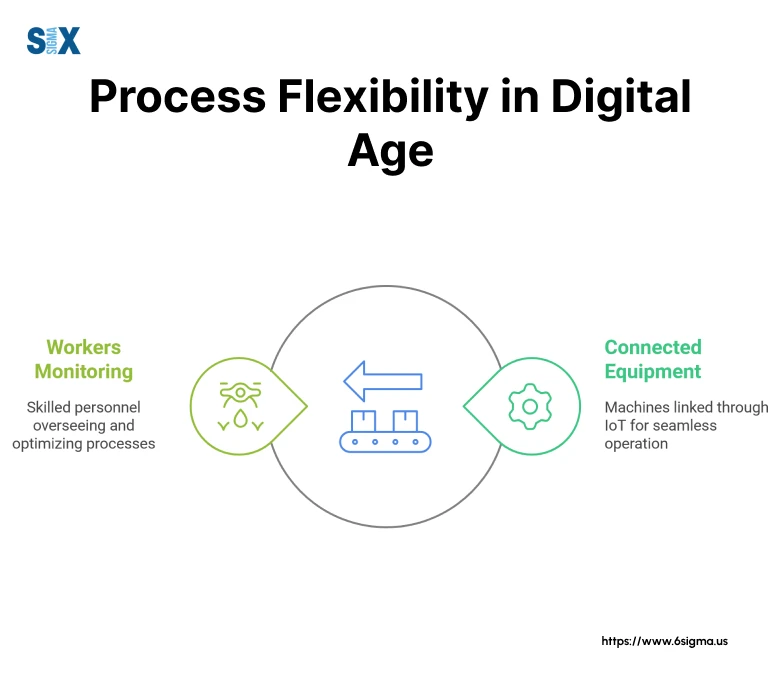
Industry 4.0
Industry 4.0 fundamentally reshapes process flexibility through real-time data integration and adaptive control systems. You can implement “Smart Flexible Manufacturing” ā a system that automatically adjusts process parameters based on real-time production data.
This implementation can result in a reduction in setup times and an improvement in first-pass yield rates. The key is integrating sensors and control systems that can respond to changes in real time.
AI & ML
Artificial Intelligence and Machine Learning have revolutionized how we approach flexible processes in operations management. Organizations are using AI-driven algorithms to predict process variations before they occur, enabling proactive adjustments rather than reactive responses.
This predictive capability reduces unplanned downtime and improves overall equipment effectiveness. The machine learning models implemented continue to refine themselves, making the processes increasingly efficient over time.
Internet of Things (IoT)
The Internet of Things (IoT) has become a cornerstone of modern process flexibility. You can implement an “IoT Flexibility Matrix” ā a network of connected sensors and devices that provide continuous feedback on process performance.
This system enables real-time adjustments to maintain optimal performance despite varying conditions. The results: an improvement in resource utilization and a reduction in quality-related issues.
Digital Twins
Digital twins represent perhaps the most exciting development in recent years. You can create digital replicas of manufacturing processes to allow simulation and optimization flexibility scenarios before implementing them on the factory floor.
This approach can reduce implementation risks and accelerate the deployment of new flexible processes. The ability to test and refine process changes in a virtual environment before physical implementation has transformed how we approach process flexibility.
Successful digital transformation of flexible processes requires a balanced approach. The technology must serve the process, not vice versa. I emphasize the importance of the “Digital Flexibility Framework” ā a structured approach to integrating digital technologies while maintaining focus on core process objectives.
Best Practices for Maintaining Flexible Processes
Several key best practices consistently drive success in maintaining business process flexibility.
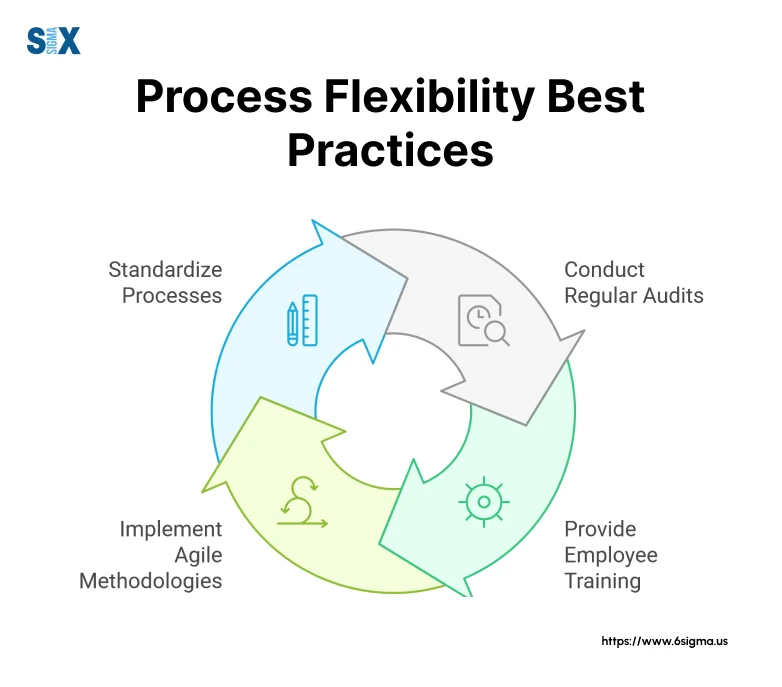
Regular Audits
Regular process audits form the foundation of sustainable process flexibility. You can use the “Flexible Process Audit System” (FPAS), which recommends quarterly comprehensive audits supplemented by monthly focused reviews.
This approach helps manufacturers identify and address flexibility gaps before they impact performance, resulting in a reduction in process-related disruptions. The key is not just conducting audits but ensuring they drive meaningful improvements in flexible processes.
Employee Training
Employee empowerment and cross-training have proven crucial for maintaining process flexibility. Implement “Flexibility Skills Matrix” ā a systematic approach to cross-training to ensure each process has at least three qualified operators. This redundancy helps increase process uptime and improve employee engagement scores.
Agile Methodologies
Agile methodologies in process management represent a paradigm shift. You can adapt traditional agile principles to create “Flexible Process Sprints” ā two-week cycles of process improvement focused on enhancing flexibility. This approach can lead to a reduction in change implementation time and improvement in process adaptation capabilities.
Standardization
Balancing standardization with flexibility remains one of the most challenging aspects of process management. Use a “Standardized Flexibility Framework” that helps maintain consistency while preserving adaptability. This framework can help achieve improvement in process efficiency while maintaining strict quality standards.
The success of these best practices relies heavily on the “Three Pillars of Sustainable Flexibility”:
- Systematic monitoring through regular audits
- Continuous capability building through cross-training
- Balanced approach to standardization and adaptation
Conclusion: Embracing Process Flexibility for Future Success
The importance of process flexibility will only increase. Market volatility, technological advancement, and evolving customer expectations are creating an environment where rigid processes simply cannot survive.
The path forward requires a commitment to continuous improvement in flexible processes. I recommend organizations take the following actions:
- First, assess your current process flexibility using structured evaluation tools.
- Second, invest in your people. The most successful flexible processes have one thing in common: well-trained, empowered employees who understand and embrace process flexibility principles.
- Third, leverage technology strategically. I’ve seen how digital tools can dramatically enhance process flexibility ā but only when aligned with clear operational objectives and supported by capable teams.
- Process flexibility isn’t just about adapting to change ā it’s about creating organizational capabilities that turn change into opportunity.
Start with small, focused improvements and gradually build toward comprehensive flexibility across your operations!
Frequently Asked Questions About Process Flexibility
The article provides several examples, but a notable one is from the automotive sector where a tier-one supplier implemented “Dynamic Cell Manufacturing” with flexible production cells that could handle multiple product families.
This resulted in a 65% decrease in setup times, a 40% reduction in work-in-progress inventory, and a 35% improvement in overall equipment effectiveness.
Business process flexibility is a system’s ability to effectively respond to changes in product mix, production volume, and operational conditions without requiring significant modifications to existing facilities and processes. It’s considered an absolute necessity in modern manufacturing and business operations.
Flexibility in the decision process is the ability to adapt and modify decisions based on changing circumstances and new information. It involves maintaining multiple options, being able to revise decisions quickly, and having contingency plans in place to respond to changing conditions effectively.
While the article doesn’t explicitly define “functional or work process flexibility,” it describes related concepts through four core principles: routing flexibility, volume flexibility, mix flexibility, and new product flexibility. These allow for adaptable operations and efficient resource utilization.
The key features of process flexibility include:
1. Adaptability in routing – reduces bottlenecks and improves throughput
2. Volume flexibility – the ability to scale production up or down cost-effectively
3. Mix flexibility – handling various product types simultaneously
4. New product flexibility – introducing new products without major modifications
5. Reduction in changeover times
6. Improved resource utilization
7. Reduced work-in-progress inventory
The primary advantage of process flexibility is increased efficiency and productivity, which stands out as the foremost benefit in manufacturing operations. This leads to improved overall equipment effectiveness (OEE) through flexible manufacturing cells.
The article doesn’t provide a multiple-choice selection to answer this specific question. However, based on the article, the “Dynamic Cell Manufacturing” example from the automotive case study would be a strong demonstration of built-in process flexibility, as it created flexible production cells capable of handling multiple product families with significant measurable improvements.
SixSigma.us offers both Live Virtual classes as well as Online Self-Paced training. Most option includes access to the same great Master Black Belt instructors that teach our World Class in-person sessions. Sign-up today!
Virtual Classroom Training Programs Self-Paced Online Training Programs