Mastering Process Capability – A Lean Six Sigma Perspective
I’ve seen firsthand how evaluating process capability can transform businesses.
By understanding a process’ natural variability through metrics like Cp, Cpk, and Ppk, operations gain valuable insights. They can identify high-risk areas needing attention and see the true performance capability.
Throughout my career, I’ve led projects involving process capability studies. From manufacturing to business operations, the benefits always amazed me…
Teams realized where to focus resources like reducing defects, cutting costs, and boosting throughput. Customers also noticed the impact as orders were fulfilled right the first time.
I’ll cover the basics of calculating process capability indices using formulas and examples. I’ll also discuss tools available like online calculators. Most importantly, I want to convey how these analyses generated real wins for companies just like yours.
By the end, you’ll understand:
- How process capabilities are measured
- Where to find the data needed
- The value it provides across any industry
- Next steps to apply it within your organization
The Basics – What is Process Capability?
Now that we’ve covered the groundwork, let’s go over some fundamentals – the basic language and math behind process capability.
Process capability indices Cp and Cpk are measures of a process’ natural variability compared to its specification limits.
Cp accounts just for how the spread of data fits within the tolerance range, while Cpk considers centering as well. Both give you an idea of the risk of producing non-conforming units.
Quantitative process analysis is key to breaking through capability barriers. Learn how to spot high-risk areas and maximize process yields. Enroll now in our Green Belt training program for an in-depth look at Process Mapping, Measurement Systems Analysis, and designing experiments to fine-tune processes.
Calculating process indices like the Cpk formula
The actual Cpk formula is fairly straightforward. It’s the smaller value between the distance the process mean is from the lower spec and the distance it is from the upper divided by 3 times the standard deviation. This provides a standardized z-score to benchmark capability.
Example: Ensuring cereal weight tolerances
Let’s look at an example. Say the spec for a cereal box is 4.8 – 5.2 ounces. We collected 50 weight samples and calculated the mean is 5.05 ounces with a standard deviation of 0.1. Plugging this into the Cpk formula gives us a value of 1.5. This robust index tells us high yields are attainable.
Does this help illustrate how the concepts come together in practice? The next section will cover the real-world benefits of my many projects.
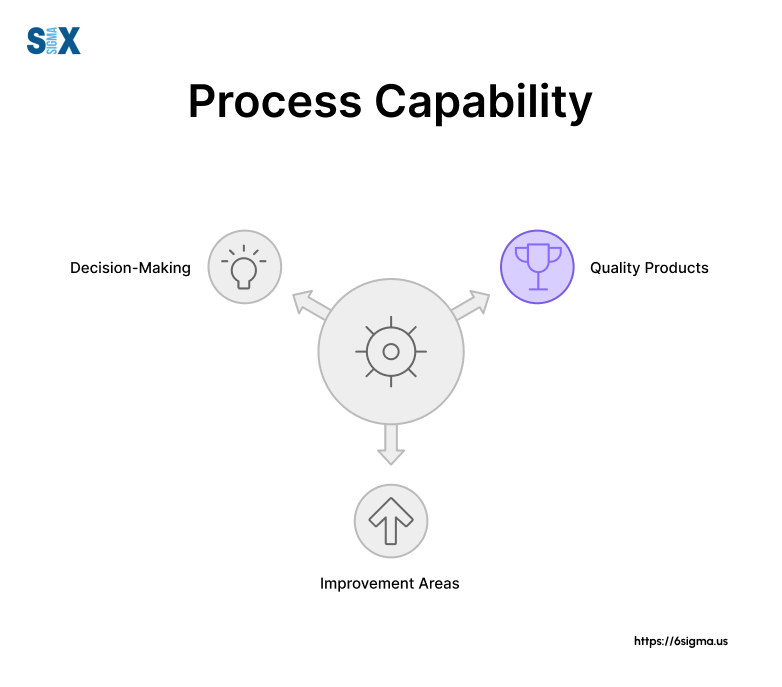
Getting Started with a Process Capability Study
Now that we’ve covered the basics, it’s time to discuss how to launch your first capability project. Based on my decades of experience, here are some suggestions:
Determining the Sample Size Needed
Start by choosing processes that will provide value. Then calculate the appropriate sample size using statistical formulas so your results have meaning. As a rule of thumb, you typically need 25-50 pieces of data minimum.
Curious about how to analyze a process to know whether it will produce significant defects? Take a short course on “Introduction to Capability” to learn the different methods for evaluating a process’s baseline capacity, depending on the type of data being analyzed.
Planning Data Collection Over Time/Equipment for Process Capability
Map out exactly what you’ll measure and from which machines during normal cycles. Be sure to standardize how attributes are defined and collected to get an “apples to apples” comparison later.
Using Control Charts to Identify Stable Processes
Before calculating indices, construct X-bar and R charts from initial samples. This helps verify if any special causes of variation exist that could skew your baseline numbers. Address these first before “freezing the picture” to determine inherent process capabilities.
Analyzing the Results
Once you’ve completed the initial capability analysis, it’s time to review what you’ve found. This stage is hugely important, as proper interpretation will guide important next steps.
Interpreting Cpk values <1, 1-1.33, >1.33
Generally, a Cpk below 1 means the process is not yet capable, and significant process adjustments are necessary. Between 1-1.33 is marginal – changes may still be worth testing. Above 1.33, your process demonstrates a high level of performance stability under natural conditions.
Question: How did this insight impact your actions?
In one project, we found a Cpk of 0.8 for a critical welding process. Seeking that >1.33 target, we worked with operators to fine-tune their technique using experimental design. Parameter adjustments like weld temperature and line speed yielded a new Cpk of 1.5 and major quality improvements.
Take time to fully examine what your process capability indices uncovered. Don’t just report results – use them as drivers to boost process understanding, prioritize improvement initiatives, and monitor upgrades over time. That’s where the real value lies!
Improving Process Performance with Process Capability
The journey doesn’t end after the first study. Process capability is meant to be continually reassessed to benchmark enhancements. Let me share an example:
Case Study: Medical Device Calibration Optimization
One client calibrated pH monitors in a facility. Initial Cp/Cpk showed potential to tighten tolerances. We ran a design of experiments test, varying five factors across six levels.
Statistical modeling revealed the main effects and interactions affecting output. Adjusting these based on results significantly boosted process capability.
Leveraging DOE to Find Factor Influences
This case shows how planned experimentation provides a scientific means to identify “levers” within any process.
Simply tweaking parameters blindly is less effective than a structured DOE approach. The insights directly translated into reduced scrap, rework, and more consistent customer calibrations.
Challenge: Identify an Opportunity for Your Process
Take a few minutes to consider your operation. Is there a process ripe for improvement through the design of experiments? Feel free to discuss your thoughts.
Advanced Techniques of Process Capability
For those wanting to delve deeper, I’ll briefly discuss some advanced statistical approaches:
Applying Advanced Stats to Non-normal Data
Real processes don’t always behave perfectly normally. When capability indices fall short, try transforming variables or using non-parametric tests that don’t assume normality like medians/robust z-scores.
Incorporating Dynamic Process Changes with Process Capability
Capabilities can also evolve along with improvements or drift over time. Specialized control charting like CuSum/EWMA helps observe gradual shifts for recalculation, not just step changes.
Process Simulation Software Demo
Beyond basic capabilities, programs now model complex relationships between factors for “what if” scenarios. During a presentation, I demonstrated building a virtual injection molding line and optimizing cycle times/defect rates remotely in real time—a huge time-saver!
Sustaining Gains Over Time with Process Capability
The true test of any improvement effort is maintaining results long-term. This requires relentless focus and an ingrained culture. A few suggestions:
Monitoring Workflows and Risk Management
Build routines to measure top capabilities monthly or quarterly. Use control charts to promptly react if processes shift due to non-special causes. Regular risk assessments also help ensure systems, methods, and responsibilities stay in place.
Refining KPIs that Drive Continuous Improvement with Process Capability
Tie incentives and metrics to hitting capability targets. For instance, one client linked incentive pay for production teams achieving certain Cp levels. This direct motivation boosted a sense of shared ownership over continual progress.
It’s also important that programs evolve with new priorities over time. Re-evaluate which metrics and processes are monitored against changing business needs. Process capability maintains relevance through this flexibility.
Common Questions About Process Capability
Over the years, I’ve noticed common questions about how teams gather and analyze their data to determine these important indices.
Some key highlights include:
Process Mapping is Critical – The first step is understanding your process flow from start to finish. Take the time to diagram each step and identify useful measurement points to collect numbers. This ensures you analyze the entire value-adding process, rather than just one small piece.
Establish a Measurement System – Be sure to use repeatable and accurate monitoring equipment. Your calculated capabilities only provide the truth if your gauges are “capable” themselves. It’s also important data comes from the actual production equipment, not lab tests.
Choose the Right Sample Size – To accurately model a process, you need a large enough sample to smooth out small variations. Usually, 25-50 readings are adequate, though more can give clearer insights over time. Be sure to have an experienced statistician help determine if your quantities are valid.
Consider Stability – Ensure your process is in a state of statistical control before assessment. Use tools like control charts to spot assignable causes of variation. Address these first so your capability numbers represent only common causes of difference innate to the process.
Calculations are Straightforward – Once data meets the above criteria, Cp, Cpk, and Ppk can easily be determined using standard spreadsheet formulae or online calculators.
Still, double-check the math – accuracy is key to credibility!
Conclusion
I’ve conveyed how process capability analysis generates tremendous value for any operation when properly applied and sustained. A few key takeaways to remember:
- Calculating simple indices like Cp and Cpk provides visibility into process performance risks.
- Using tools like control charts and the design of experiments arm you with the scientific understanding needed to optimize processes.
- Continuous re-evaluation supports a culture focused beyond short-term gains to maintaining top performance long-term.
- Shifting from reactive to proactive sets the stage to consistently meet quality and delivery promises to customers large and small.
Most importantly, remember process improvement is a marathon, not a sprint. But with patience and persistence, the rewards grow exponentially, just as they have for all the organizations I’ve been fortunate enough to partner with over the years. I wish you the very best moving forward!
Take a moment to reflect – which process within your organization would most benefit from capability analysis? Jot down one idea in the text box below and optionally share insights.
SixSigma.us offers both Live Virtual classes as well as Online Self-Paced training. Most option includes access to the same great Master Black Belt instructors that teach our World Class in-person sessions. Sign-up today!
Virtual Classroom Training Programs Self-Paced Online Training Programs