PDSA vs DMAIC: Choosing the Right Process Improvement Model
In process improvement, two titans stand tall: PDSA and DMAIC. But which one is right for your organization?
As businesses strive for operational excellence, the choice between these powerful methodologies can significantly impact your success.
Understanding the nuances between PDSA and DMAIC is crucial for making informed decisions.
Key Highlight
- Overview of both the models
- Origins of PDSA (Plan-Do-Study-Act) and DMAIC (Define-Measure-Analyze-Improve-Control)
- Key differences
- Choosing the right approach
- Understanding of their unique strengths and applications
Understanding PDSA
The Plan-Do-Study-Act (PDSA) cycle, a cornerstone of continuous improvement, has its roots in the work of management guru W. Edwards Deming.
Originally conceived as the Plan-Do-Check-Act (PDCA) cycle, this iterative approach has evolved to become a fundamental tool in quality management and process improvement.
Apply PDSA in your organization! Our Lean Introduction course provides the essential tools and mindset for effective continuous improvement
Deming’s influence on the development of the PDSA cycle cannot be overstated
His philosophy of continuous improvement, which emphasizes learning and adaptation, is perfectly encapsulated in this model. The key principles underlying PDSA include:
- Iterative learning
- Data-driven decision making
- Continuous improvement
- Small-scale testing
When comparing PDSA vs DMAIC, it’s important to note that PDSA’s cyclical nature sets it apart from the more linear DMAIC approach.
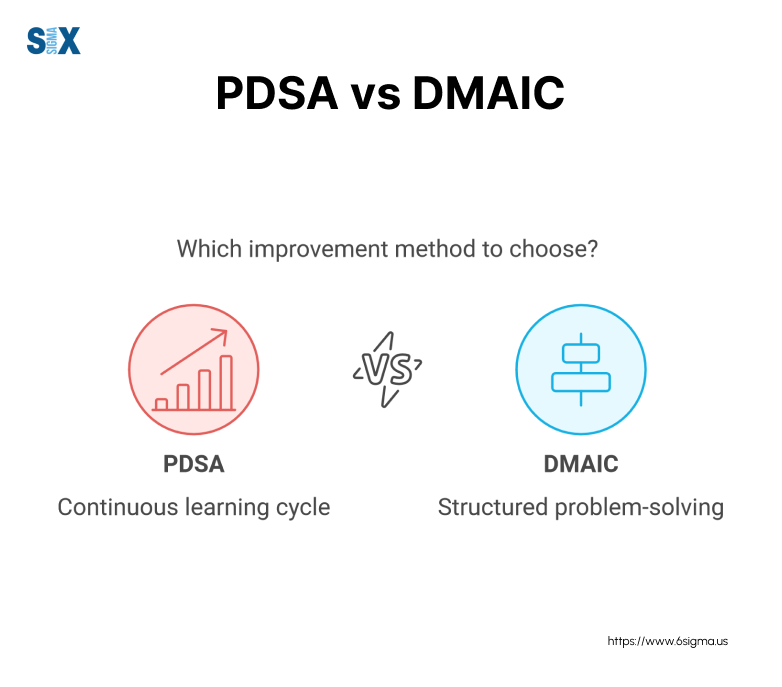
Breaking Down the PDSA Cycle
To truly understand the difference between PDSA and DMAIC, let’s dive into each step of the PDSA cycle:
- Plan: Identify an opportunity and plan for change.
- Do: Implement the change on a small scale.
- Study: Analyze the results and what you’ve learned.
- Act: Refine the change based on what you learned.
For example, a healthcare facility might use PDSA to improve patient wait times:
- Plan: Analyze current wait times and set a goal for reduction.
- Do: Implement a new scheduling system in one department.
- Study: Collect data on wait times after implementation.
- Act: Refine the system based on results and roll out to other departments.
This example illustrates how PDSA in Six Sigma can be applied to real-world scenarios, demonstrating its versatility as both a Lean tool and a project management tool.
Strengths and Limitations of PDSA
When considering PDSA vs DMAIC or DMAIC vs PDSA, it’s crucial to understand the strengths and limitations of each approach. PDSA offers several advantages:
- Flexibility: Easily adaptable to various situations
- Quick implementation: Ideal for rapid improvements
- Continuous learning: Encourages ongoing refinement
However, PDSA also has potential drawbacks:
- Less structured: May not suit complex problems requiring in-depth analysis
- Potential for hasty implementation: Quick cycles might lead to overlooking important details
Understanding these aspects is key to grasping the difference between PDSA vs DMAIC and choosing the right approach for your project.
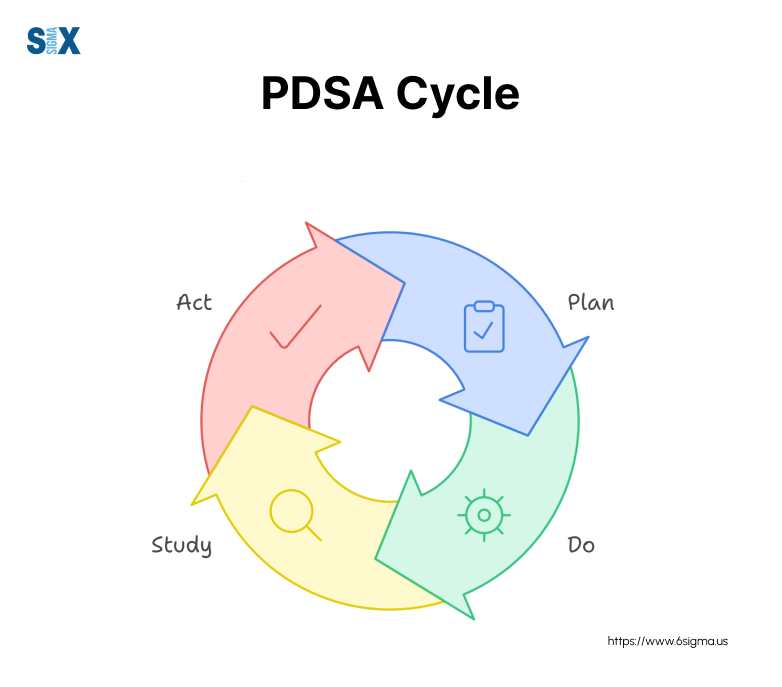
In conclusion, while PDSA and DMAIC share the goal of process improvement, their approaches differ significantly.
PDSA’s iterative nature makes it ideal for quick, ongoing improvements, while DMAIC offers a more structured approach for complex problems.
Understanding DMAIC
While exploring the difference between PDSA and DMAIC, it’s crucial to understand DMAIC’s roots in Six Sigma methodology.
Developed by Motorola in the 1980s, DMAIC (Define, Measure, Analyze, Improve, Control) emerged as a structured approach to problem-solving within the Six Sigma framework.
Transform your approach to problem-solving with our Green Belt course. Learn to apply DMAIC methodology to drive significant, data-driven improvements in your organization.
The core principles of DMAIC include:
- Data-driven decision making
- Process focus
- Customer-centricity
- Structured problem-solving
These principles set DMAIC apart in the PDSA vs DMAIC comparison, offering a more rigorous approach to process improvement.
The Five Phases of DMAIC
To fully grasp the difference between DMAIC and PDSA, let’s break down the five phases of DMAIC:
- Define: Clearly articulate the problem and project goals.
- Measure: Collect data to establish current performance levels.
- Analyze: Use statistical tools to identify root causes of problems.
- Improve: Develop and implement solutions to address root causes.
- Control: Establish procedures to maintain improvements over time.
For example, a manufacturing company might use DMAIC to reduce defects:
- Define: Specify the type of defect and set reduction targets.
- Measure: Collect data on current defect rates and process parameters.
- Analyze: Use statistical analysis to identify factors contributing to defects.
- Improve: Implement process changes based on analysis results.
- Control: Establish monitoring systems to ensure sustained improvement.
This example illustrates how DMAIC in Six Sigma provides a structured approach to problem-solving, contrasting with the more iterative nature of PDSA.
Pros and Cons of the DMAIC Model
When considering PDSA vs DMAIC or DMAIC vs PDSA, it’s important to weigh the advantages and limitations of each approach. DMAIC offers several benefits:
- Rigorous analysis: Ensures thorough understanding of problems
- Data-centric: Decisions based on objective evidence
- Comprehensive: Addresses complex, multifaceted issues
However, DMAIC also has potential drawbacks:
- Time-consuming: May not be suitable for quick fixes
- Resource-intensive: Requires significant data collection and analysis
- Complexity: Can be overwhelming for simpler problems
Understanding these aspects is key to grasping the difference between DMAIC vs PDSA and choosing the right approach for your project.
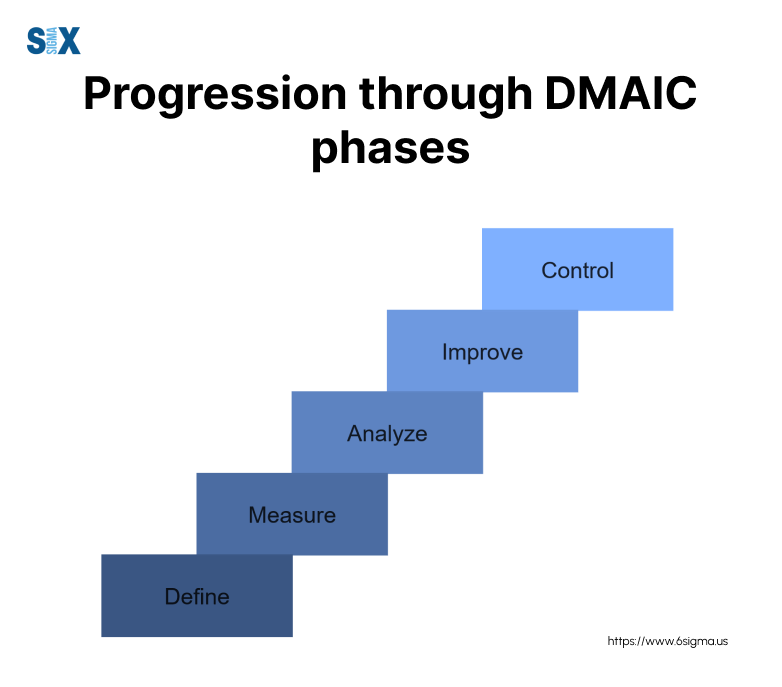
While PDSA and DMAIC both aim at process improvement, their approaches differ significantly.
DMAIC’s structured, data-driven methodology makes it ideal for complex problems requiring in-depth analysis, while PDSA offers a more flexible, iterative approach.
PDSA vs DMAIC: A Comprehensive Comparison
When it comes to process improvement methodologies, understanding the difference between PDSA and DMAIC is crucial for selecting the right approach for your organization.
Structural Differences
One of the key differences between PDSA vs DMAIC lies in their structural approaches:
PDSA (Plan-Do-Study-Act):
- Iterative and cyclical
- Emphasis on continuous improvement
- Flexible and adaptable to changing circumstances
DMAIC (Define-Measure-Analyze-Improve-Control):
- Linear and sequential
- Focus on solving specific problems
- More structured and rigid approach
The PDSA cycle allows for rapid iterations and quick adjustments, making it ideal for dynamic environments.
In contrast, DMAIC provides a systematic approach that’s well-suited for complex problems requiring in-depth analysis.
Data and Analysis Requirements
When comparing DMAIC vs PDSA, data requirements and analytical depth are significant differentiators:
PDSA:
- Less data-intensive
- Relies on quick, actionable insights
- Uses basic statistical tools
DMAIC:
- Requires extensive data collection
- Employs advanced statistical analysis
- Utilizes sophisticated quality management tools
While PDSA can be implemented with minimal data, DMAIC demands a more comprehensive dataset to drive decision-making. This difference between DMAIC and PDSA can impact the choice of methodology based on data availability and analytical capabilities.
Time and Resource Commitments
The difference between PDSA vs DMAIC is also evident in their resource requirements:
PDSA:
- Shorter project durations (days to weeks)
- Smaller team sizes
- Less intensive training required
DMAIC:
- Longer project timelines (weeks to months)
- Larger, cross-functional teams
- Requires specialized training (e.g., Six Sigma certification)
Organizations with limited resources or time constraints may find PDSA more accessible, while those seeking comprehensive solutions might opt for the more resource-intensive DMAIC approach.
Outcome Focus and Long-term Impact
The long-term effects and focus areas differ when comparing PDSA and DMAIC:
PDSA:
- Targets incremental improvements
- Encourages a culture of continuous improvement
- Results may be less dramatic but more frequent
DMAIC:
- Aims for significant, breakthrough improvements
- Focuses on eliminating root causes of problems
- Results are typically more substantial but less frequent
While both PDSA and DMAIC aim to improve processes, their approaches to achieving and sustaining results vary considerably.
Key Differences Between PDSA vs DMAIC
To summarize the main differences between DMAIC vs PDSA, consider this comparison table:
Aspect | PDSA | DMAIC |
---|---|---|
Approach | Iterative, cyclical | Linear, sequential |
Data Requirements | Minimal | Extensive |
Project Duration | Short-term | Long-term |
Team Size | Small | Large, cross-functional |
Training Needs | Basic | Advanced (Six Sigma) |
Improvement Focus | Incremental | Breakthrough |
Flexibility | High | Low |
Best For | Quick improvements, dynamic environments | Complex problems, stable processes |
While both PDSA and DMAIC are valuable process improvement tools, their differences make them suitable for different scenarios. PDSA excels in quick, iterative improvements, while DMAIC shines in tackling complex, data-heavy problems.
Understanding these distinctions is key to choosing the right methodology for your specific needs.
Remember, the choice between PDSA and DMAIC isn’t always an either-or decision.
Many organizations successfully use both methodologies, applying PDSA for rapid improvements and DMAIC for more complex challenges.
Lead transformative change with our Black Belt course which equips you with the expertise to navigate complex improvement projects using both PDSA and DMAIC methodologies
When to Use PDSA vs DMAIC: Decision-Making Framework
Choosing between PDSA and DMAIC can significantly impact your project’s success. This decision-making framework will help you navigate the difference between PDSA and DMAIC, ensuring you select the most appropriate methodology for your specific situation.
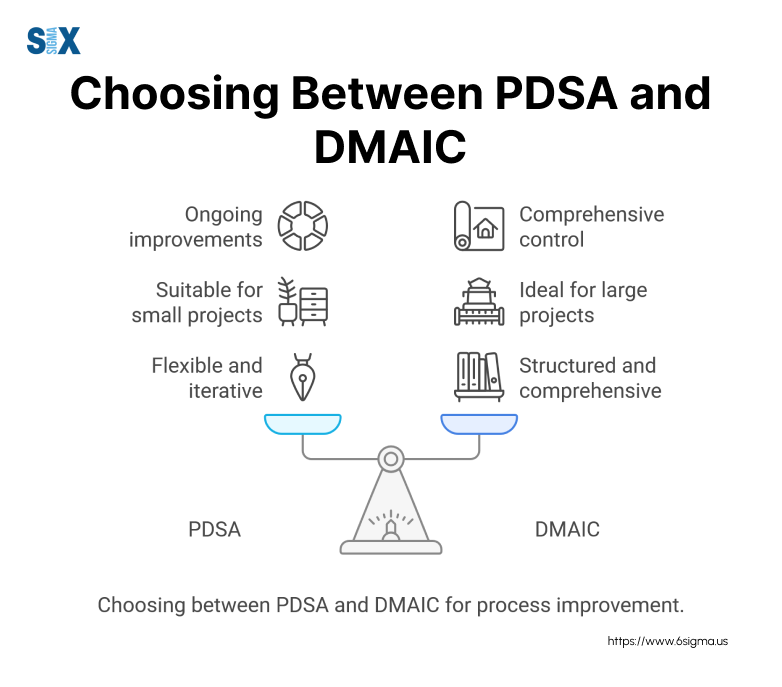
Project Scope and Complexity Considerations
When comparing PDSA vs DMAIC, consider your project’s scope and complexity:
- PDSA: Ideal for smaller, less complex projects or quick improvements
- DMAIC: Better suited for large-scale, complex problems requiring in-depth analysis
For instance, a small retail store might use PDSA to improve customer greeting procedures, while a large manufacturing plant might employ DMAIC to overhaul its entire production line.
Organizational Culture and Resources
The difference between DMAIC and PDSA becomes evident when considering organizational factors:
- PDSA:
- Suits agile, fast-paced environments
- Requires fewer resources and less specialized training
- Promotes a culture of continuous, incremental improvement
- DMAIC:
- Thrives in structured, data-driven organizations
- Demands more resources and specialized expertise (e.g., Six Sigma training)
- Fosters a culture of rigorous problem-solving and process optimization
Problem Type and Data Availability
The nature of the problem and available data play crucial roles in the PDSA vs DMAIC decision:
PDSA:
- Effective for problems with limited or quickly changing data
- Suitable for exploratory improvements where the solution isn’t clear
- Useful when quick action is needed, even with incomplete information
DMAIC:
- Excels with data-rich problems requiring statistical analysis
- Ideal for addressing root causes of persistent, complex issues
- Best when comprehensive data collection and analysis are feasible
Industry-Specific Considerations
Different industries may favor one approach over the other:
- Healthcare: Often uses PDSA for rapid improvements in patient care processes
- Manufacturing: Frequently employs DMAIC for defect reduction and quality control
- Software Development: May lean towards PDSA for iterative product improvements
- Finance: Might prefer DMAIC for risk management and compliance projects
Understanding these industry trends can guide your choice between PDSA and DMAIC.
To help you make an informed decision, consider this comparison table of scenarios for PDSA vs DMAIC usage:
Scenario | PDSA | DMAIC |
---|---|---|
Quick process tweaks | ✓ | |
Complex quality issues | ✓ | |
Limited data available | ✓ | |
Need for in-depth analysis | ✓ | |
Agile environment | ✓ | |
Structured organization | ✓ | |
Continuous small improvements | ✓ | |
Large-scale transformations | ✓ |
Remember, the choice between PDSA and DMAIC isn’t always clear-cut. Some organizations successfully blend elements of both approaches, creating hybrid methodologies tailored to their specific needs.
The key is to understand the difference between PDSA vs DMAIC and apply the most suitable aspects of each to your unique situation.
As you navigate the decision between DMAIC vs PDSA, keep in mind that both methodologies aim to drive improvement.
Your choice should align with your organization’s culture, resources, and the nature of the problem at hand.
By carefully considering these factors, you’ll be well-equipped to select the most effective approach for your process improvement initiatives.
The Future of Process Improvement: Evolving PDSA and DMAIC
As we look ahead, the landscape of process improvement continues to evolve, impacting how we approach PDSA vs DMAIC methodologies. Understanding these changes is crucial for staying ahead in the field of continuous improvement.
Technological Advancements and Their Impact
The rapid pace of technological innovation is reshaping how we apply PDSA and DMAIC:
- AI and Machine Learning: Enhancing data analysis capabilities in both PDSA and DMAIC processes
- IoT and Big Data: Providing real-time insights, allowing for more dynamic applications of PDSA
- Automation: Streamlining DMAIC processes, particularly in the Measure and Analyze phases
These advancements are blurring the lines between PDSA and DMAIC, creating opportunities for more integrated approaches.
Emerging Trends in Process Improvement Methodologies
The difference between PDSA and DMAIC is evolving with new trends:
- Agile DMAIC: Incorporating iterative elements of PDSA into the DMAIC framework
- Data-Driven PDSA: Enhancing PDSA with more robust data analysis techniques
- Hybrid Models: Combining elements of PDSA and DMAIC for tailored solutions
- Lean Six Sigma Digital: Adapting both methodologies for digital transformation projects
These trends are reshaping how we perceive the difference between DMAIC and PDSA, leading to more flexible and adaptable approaches.
Adapting PDSA and DMAIC for the Digital Age
As organizations become more digital, PDSA and DMAIC are adapting:
- PDSA in Digital Environments:
- Faster iteration cycles
- Integration with agile methodologies
- Focus on user experience metrics
- DMAIC in the Digital Realm:
- Emphasis on data security and privacy
- Incorporation of digital process mining techniques
- Application to software development and cloud infrastructure optimization
The future of PDSA vs DMAIC lies in their ability to adapt to these digital challenges while maintaining their core principles.
- AI and Machine Learning integration
- Hybrid PDSA-DMAIC models
- Adaptation for digital transformation projects
- Integration with emerging technologies (e.g., blockchain, VR)
As we navigate the evolving landscape of process improvement, the key is to remain flexible and open to new approaches that blend the best of PDSA and DMAIC.\
Supercharge your process improvement efforts with data-driven insights. Our Statistical Process Control course provides the tools to make more informed decisions in your PDSA or DMAIC projects
Conclusion
Throughout this exploration of PDSA vs DMAIC, we’ve uncovered the unique strengths and applications of each methodology.
The key differences between PDSA and DMAIC lie in their structure, data requirements, and project scope:
- PDSA excels in rapid, iterative improvements
- DMAIC shines in complex, data-heavy problem-solving
Understanding the difference between DMAIC and PDSA is crucial for selecting the right approach for your specific needs.
As we’ve seen, the choice between PDSA and DMAIC isn’t always binary – many organizations benefit from a nuanced approach that draws from both methodologies.
As process improvement evolves, so too will the applications of PDSA and DMAIC. Staying informed about emerging trends and adaptations will be key to leveraging these powerful tools effectively in the future.
Remember, the journey of process improvement is ongoing. Whether you choose PDSA, DMAIC, or a combination of both, the most important step is to begin.
SixSigma.us offers both Live Virtual classes as well as Online Self-Paced training. Most option includes access to the same great Master Black Belt instructors that teach our World Class in-person sessions. Sign-up today!
Virtual Classroom Training Programs Self-Paced Online Training Programs