What is COPQ (Cost of Poor Quality)?
Quality issues can significantly impact a company’s profitability and reputation. To quantify the financial impact of poor quality, the concept of cost of poor quality (COPQ) is used.
COPQ refers to all the costs associated with preventing, finding, and correcting defective work. It provides a metric to understand the cost of quality problems and drive improvement initiatives.
Tracking COPQ enables organizations to identify processes that need attention, set quality improvement goals, and allocate resources effectively.
Stop letting poor quality drain your resources
Gain the analytical skills to measure COPQ and lead projects that deliver real financial improvements with Lean Six Sigma Green Belt Certification.
It is an essential metric that highlights the financial benefits of achieving higher quality standards. Analyzing and lowering COPQ can directly increase profitability, along with improving operational efficiency and customer satisfaction.
What is the Cost of Poor Quality (COPQ)?
Cost of poor quality (COPQ) refers to the costs associated with producing defective products or services that fail to meet customer expectations. It highlights the extra costs incurred due to poor processes or systemic issues that allow defects, errors, and quality issues to occur.
COPQ quantifies the costs linked to preventing, finding, and correcting issues to ensure quality. Professionals with a six sigma certification are trained to analyze COPQ data, providing visibility into quality management costs and performance.
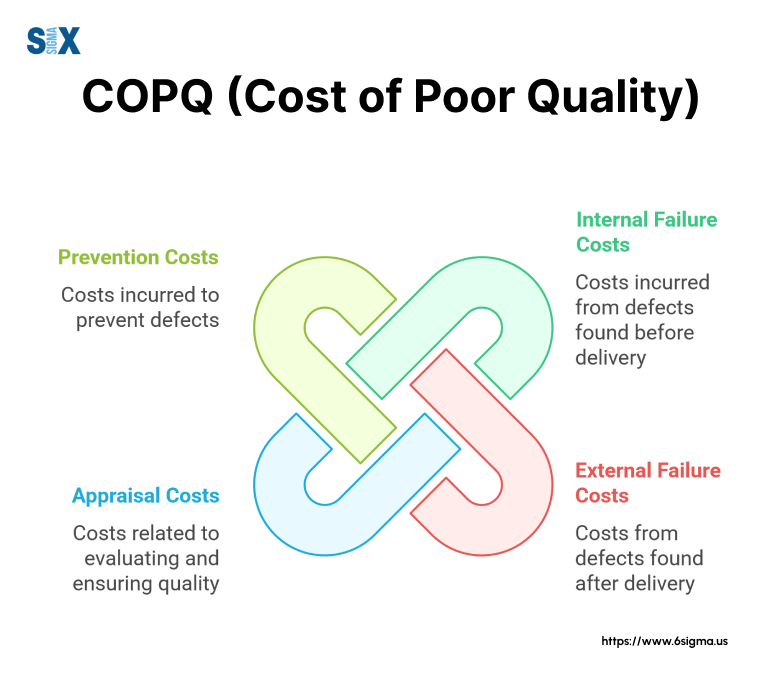
Categories of costs: COPQ is broadly divided into four categories
- Prevention costs: Expenses incurred to prevent defects like training, quality planning, etc.
- Appraisal costs: Inspection, testing, and audits to identify issues.
- Internal failure costs: Expenses from defects found before delivery to the customer.
- External failure costs: Costs occurring after delivery due to returned products, complaints, etc.
Tracking COPQ highlights areas for improvement in processes and systems to reduce overall costs.
It is a key metric for quality control across manufacturing, service, and transactional domains.
Why Measure Cost of Poor Quality
Understanding the cost of poor quality is critical for organizations looking to improve profitability, efficiency, and customer satisfaction. Earning a six sigma certification equips professionals with the tools to measure and reduce COPQ, driving these improvements.
Tracking quality costs allows businesses to identify problem areas, benchmark performance over time, and prioritize quality improvement initiatives.
Impact of COPQ on Profits
The cost of poor quality has a direct impact on an organization’s bottom line. These costs drain profits and can account for a surprising percentage of operating expenses.
By measuring quality costs, companies can determine exactly how much money is being lost to rework, scrap, returns, and other quality issues.
Reducing these costs through process improvements and quality control boosts profit margins.
Identify Problem Areas with COPQ
Analyzing quality cost data allows organizations to pinpoint processes, products, or services responsible for the highest defects and failures.
For example, tracking repair and warranty expenses by product line or business unit spotlights which areas incur the greatest quality costs. Companies can use this information to focus quality improvement projects on problem processes first.
Benchmark Performance
Tracking quality costs over time provides an ongoing benchmark to measure performance improvements.
As initiatives like Six Sigma and ISO 9001 reduce errors, organizations can quantify savings in prevention, appraisal, and failure costs. Comparing the current cost of poor quality metrics to past performance illustrates tangible financial gains from quality programs.
Firms can also use industry benchmarks to evaluate how their quality costs stack up against competitors.
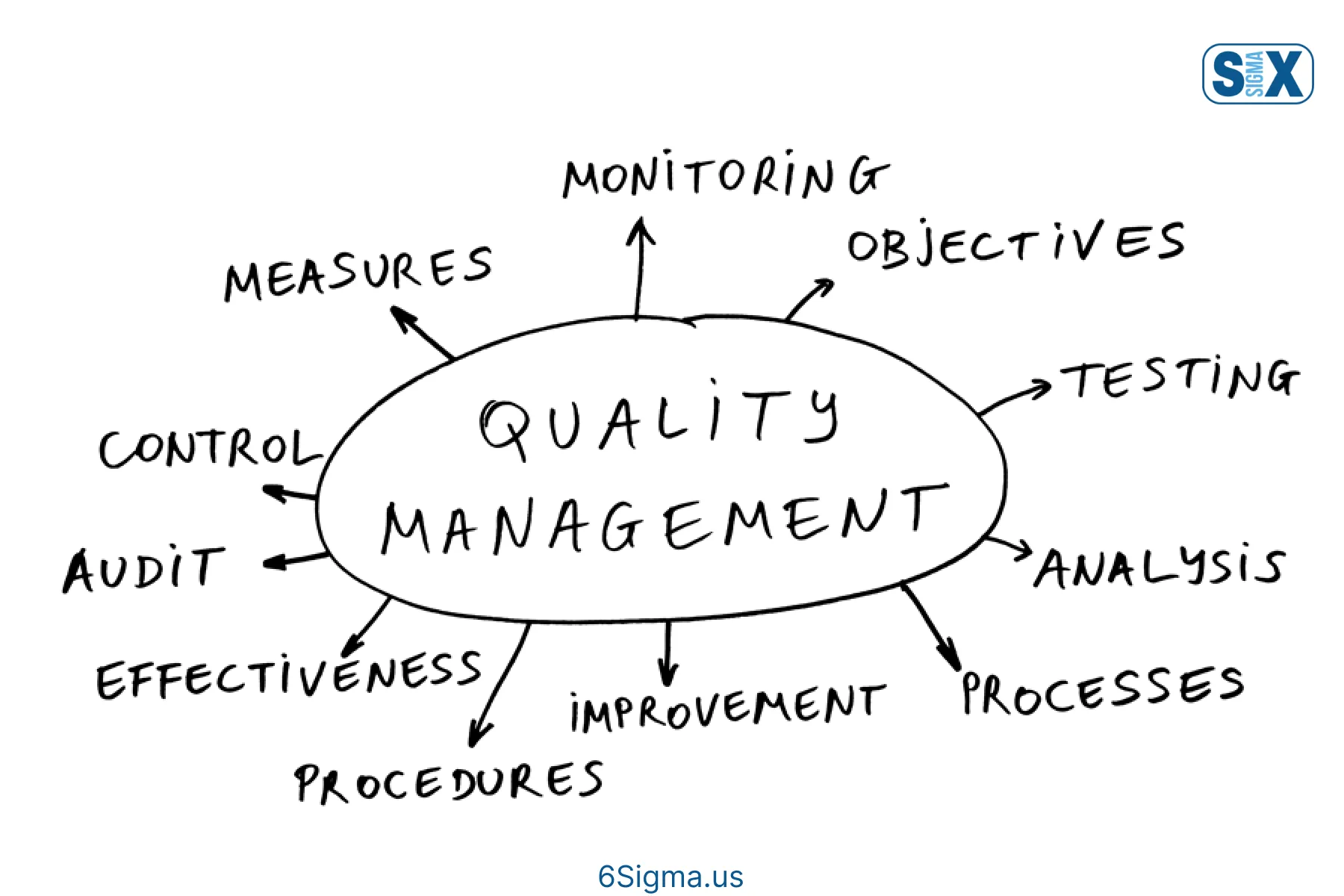
Calculating the Cost of Poor Quality (COPQ)
Understanding the different components of quality costs is essential for calculating the total cost of poor quality. According to quality management principles, quality costs can be divided into four categories:
Prevention Costs
Prevention costs refer to the costs incurred to prevent defects and errors from occurring in products or services. Some examples of prevention costs include:
- Costs of new product review and planning activities
- Process analysis costs
- Quality planning costs
- Supplier quality evaluation costs
- Quality training costs
- Costs of maintaining test equipment
Tracking prevention costs helps identify areas for future investment to prevent nonconformities. Generally, higher prevention costs lead to lower failure costs.
Appraisal Costs
Appraisal costs relate to the costs incurred to evaluate processes and products to ensure conformance to quality standards. Some examples of appraisal costs include:
- Inspection costs
- Testing costs
- Equipment calibration and maintenance costs
- Costs of quality audits
- Field testing and evaluation costs
Appraisal costs help verify quality requirements before products reach customers. However, analyzing appraisal costs can identify opportunities to streamline quality control activities.
Internal Failure Costs
Internal failure costs are incurred when products or services fail to meet quality standards before delivery to customers. Some examples are:
- Costs of rework and repairs
- Scrap costs
- Material review costs
- Costs related to reinspection and rescheduling
- Downtime costs due to quality issues
Analyzing internal failure costs identifies problem areas in processes for future corrective action.
External Failure Costs
External failure costs occur when the product or service fails after delivery to the customer. Some examples include:
- Warranty costs
- Liabilities arising from quality issues
- Costs of customer returns and replacements
- Lost sales opportunities
- Costs associated with customer complaints
Monitoring external failure costs is imperative as it directly impacts customer satisfaction levels and brand reputation.
Tracking costs in each of these categories provides critical insights for quality improvement initiatives. The goal is to reduce total quality costs by preventing defects and errors. This requires increasing prevention costs and reducing failure costs over time.
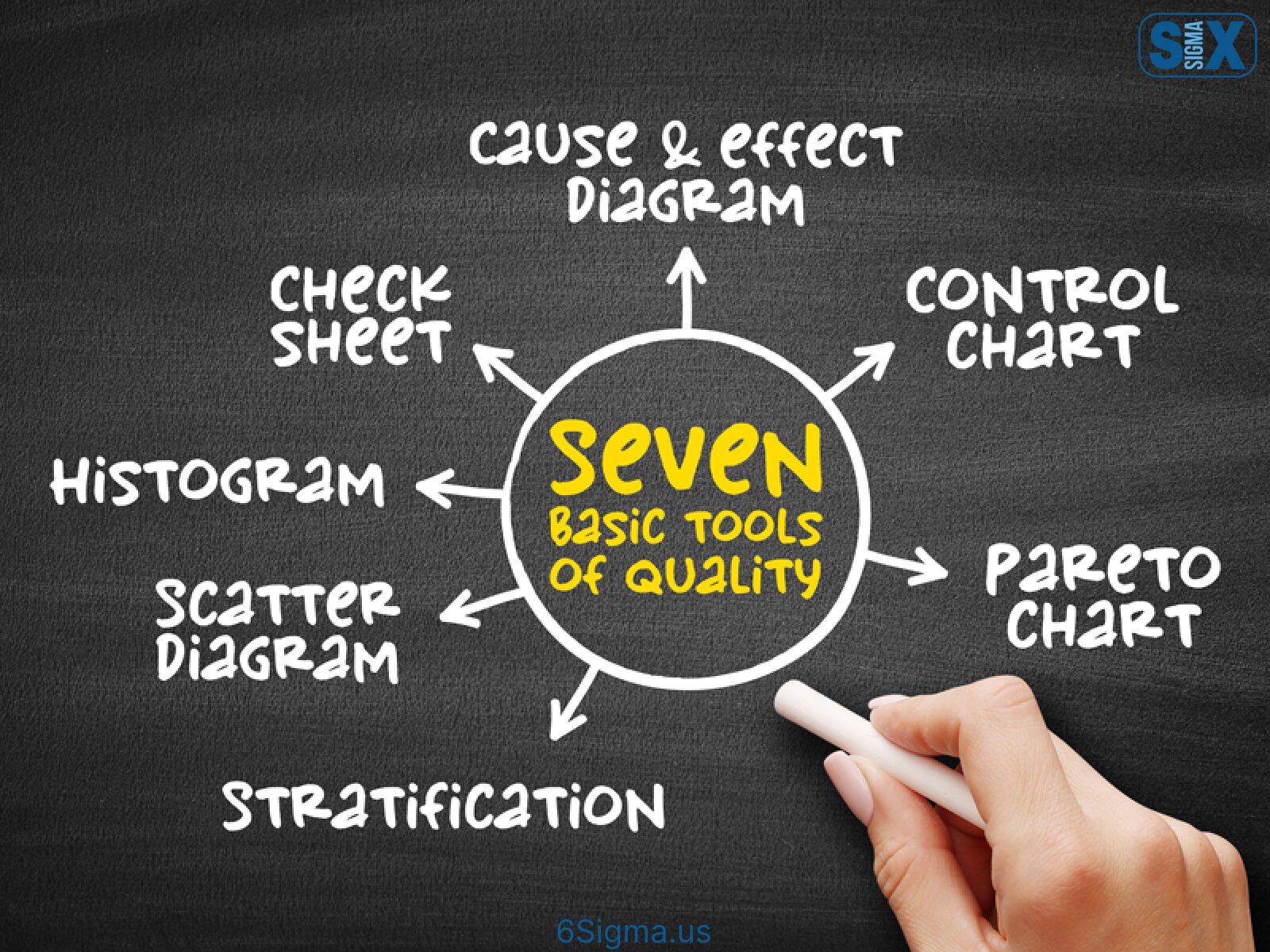
Cost of Poor Quality in Lean Six Sigma
COPQ is inherently linked to Lean Six Sigma as it quantifies the costs associated with defects and inefficiencies in processes.
Lean Six Sigma focuses on reducing waste (Lean) and minimizing variation (Six Sigma), both of which directly reduce COPQ by optimizing processes and improving quality. Our six sigma green belt certification provides hands-on training in these methodologies, enabling professionals to lead COPQ reduction projects.
Categorization of COPQ
The four categories of COPQ (prevention, appraisal, internal failure, and external failure costs) align well with Lean Six Sigma principles.
Prevention costs emphasize proactive measures—central to Lean Six Sigma’s focus on defect prevention through methodologies such as Define, Measure, Analyze, Improve, Control (DMAIC).
Integration of Concepts into Lean Six Sigma Practices
Focus on Prevention
Organizations can adopt a proactive stance by investing in prevention costs, aligning with Lean Six Sigma’s view of quality management as an upfront engineering task. By utilizing tools such as Failure Mode and Effects Analysis (FMEA), companies can anticipate potential quality issues before they occur.
Establishing a Quality Culture
Building a strong quality culture is endorsed by Lean Six Sigma, as it fosters commitment to quality at all organizational levels. Training programs focused on quality awareness can be integrated into Lean Six Sigma methodologies to empower employees, driving sustainable improvements.
Automation in Quality Control
Lean Six Sigma encourages using advanced data collection tools (like Statistical Process Control) to monitor quality metrics, allowing for a quicker response to quality issues.
Analyzing the Cost of Poor Quality Data
Once the cost of poor-quality data has been collected, it needs to be analyzed to identify opportunities for improvement.
Thorough analysis provides insights into the largest contributors to quality costs and helps determine the most impactful areas to focus process improvement efforts.
There are a few key ways to analyze quality cost data:
Failure vs Prevention Costs
A useful analysis is to compare failure costs (costs incurred from defects) to prevention costs (costs of activities to prevent defects).
The goal is for prevention costs to exceed failure costs, as this shows that proactive efforts are being invested in quality. A higher percentage of failure costs indicates reactive quality efforts and room for improvement.
Direct vs Indirect Costs
Costs can also be categorized as direct or indirect. Direct costs are easily traceable to a quality failure like material scrap.
Indirect costs are harder to connect and estimate like lost sales or customer dissatisfaction. Evaluating the magnitude of indirect vs direct costs highlights the greater business impact of quality beyond operations.
Trend Analysis with COPQ
Analyzing quality costs over time instead of a single snapshot better indicates progress. Quality cost data can be tracked periodically to identify trends and correlate quality initiatives to their financial impact.
Comparing the cost trends to process metrics like defects per unit or first pass yield provides further context into what is driving changes in quality costs.
Significant reductions in the cost of poor quality and increases in prevention costs signal the maturity of the quality system.
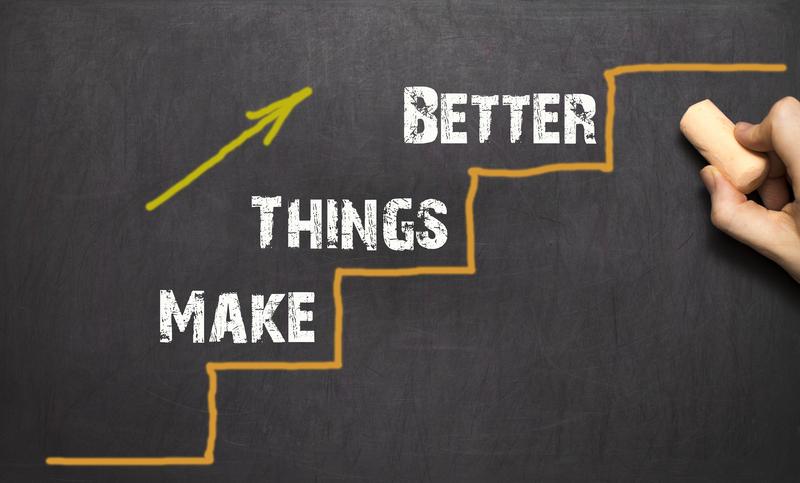
Strategies to Reduce Cost of Poor Quality
Reducing quality costs should be a strategic priority for organizations looking to improve profitability. There are several effective strategies to lower quality costs:
Process Improvement Methodologies
Implementing process improvement methodologies like Six Sigma and Lean helps reduce variations and defects.
Root cause analysis training complements these methodologies by teaching professionals how to identify and address the underlying causes of quality issues.
These provide a data-driven approach to analyze processes, identify root causes of problems, and implement solutions. Key techniques include:
- Define, Measure, Analyze, Improve, Control (DMAIC) – The core Six Sigma approach, often covered in Six Sigma Green Belt certification and Six Sigma Black Belt certification programs, to optimize processes
- Value stream mapping – Documents process flows to identify waste
- 5S – Workplace organization for efficiency
- Error proofing – Design processes to prevent defects
Quality Management Systems with COPQ
A quality management system like ISO 9001 provides a framework to implement quality best practices across the organization.
This includes quality planning, control of documents and records, handling non-conformances, audits, corrective actions, and continual improvement.
Training and Culture
Training employees on quality awareness and building a culture of quality is essential. This includes leadership commitment, employee empowerment, and recognition programs.
A strong quality culture enables long-term gains over short-term workarounds.
Automation
Automating certain process steps reduces variability induced by human errors.
This includes automated inspection systems, testing equipment, machine monitoring, etc. that provide objective data. However, over-automation should be avoided.
Implementing a combination of these strategies in a planned manner will significantly cut down poor quality costs and boost profits.
The key is to promote quality within the organizational culture.
Gain hands-on skills to drive immediate quality improvements in your organization with Lean Six Sigma Green Belt BootCamp Classroom Training
Benefits of Reducing the Cost of Poor Quality
Reducing the cost of poor quality can have significant benefits for an organization. Here are some of the major advantages:
Measuring and analyzing the cost of poor quality allows companies to identify areas for improvement. By implementing changes to reduce defects, rework, and waste, organizations can see several positive effects.
Increased profitability with COPQ
Lowering quality costs directly improves profits, as less money is spent on scrap, repairs, returns, etc. Companies can then allocate these savings to growth initiatives.
Reducing errors also minimizes lost sales opportunities from dissatisfied customers.
COPQ Contributing Towards Improved Efficiency
With fewer defects occurring, less time is spent reworking products to meet specifications. Smooth processes waste fewer materials and require less human effort per output.
This allows capacity to be directed at revenue-generating activities.
Better customer satisfaction
High-quality products that meet requirements consistently lead to improved customer satisfaction. With fewer complaints and returns to process, customers have a better brand experience. This builds loyalty and can support higher sales volumes and pricing power.
By benchmarking quality costs, pursuing targeted improvements, and creating a culture of quality, companies stand to gain financially while also strengthening market positioning through enhanced customer satisfaction.
- Tracking the cost of poor-quality metrics provides the business intelligence to guide these beneficial changes.
- Cost of poor quality refers to the costs associated with defects and failures in products or services. It includes prevention costs, appraisal costs, internal failure costs, and external failure costs.
- Measuring the cost of poor quality is important to understand its impact on profits, identify problem areas for improvement, and benchmark performance.
- Prevention costs relate to activities that prevent defects, appraisal costs involve inspecting for defects, internal failure costs arise from defects found before delivery, and external failure costs occur after delivery.
- Analyzing the cost of poor-quality data involves comparing failure versus prevention costs, direct versus indirect costs, and conducting trend analysis.
- Strategies to reduce costs include process improvement methodologies like Six Sigma and Lean, implementing quality management systems, training, culture building, and automation.
- The benefits of reducing the cost of poor quality include increased profitability, improved efficiency, better product quality, and enhanced customer satisfaction.
Quantifying and analyzing the cost of poor quality provides visibility that drives strategic quality initiatives.
This ultimately translates to substantial savings and competitive advantage for businesses. Adopting a culture of continuous improvement is key to minimizing quality costs on an ongoing basis.
Frequently Asked Question on COPQ
A. The four elements of COPQ are:
1. Prevention costs (e.g., training, quality planning)
2. Appraisal costs (e.g., inspection, testing, audits)
3. Internal failure costs (defects found before delivery)
4. External failure costs (costs occurring after delivery)
A. COPQ measurement refers to quantifying all costs associated with preventing, finding, and correcting defective work. It provides a metric to understand quality problems’ financial impact and helps drive improvement initiatives.
A. COPQ is calculated by summing up costs in four categories:
– Prevention costs (quality planning, training, equipment maintenance)
– Appraisal costs (inspection, testing, calibration)
– Internal failure costs (rework, repairs, scrap)
– External failure costs (warranty, returns, complaints)
A. In the context of Six Sigma, COPQ refers to the costs associated with producing defective products or services that fail to meet customer expectations. It highlights extra costs incurred due to poor processes or systemic issues that allow defects, errors, and quality issues to occur.
A. The COPQ process involves:
1. Identifying and categorizing quality-related costs
2. Tracking these costs across the four categories
3. Analyzing the data to identify problem areas
4. Implementing improvement strategies
5. Monitoring trends and bench-marking performance
SixSigma.us offers both Live Virtual classes as well as Online Self-Paced training. Most option includes access to the same great Master Black Belt instructors that teach our World Class in-person sessions. Sign-up today!
Virtual Classroom Training Programs Self-Paced Online Training Programs