The Strategic Edge: Continuous Improvement vs Process Improvement
Business excellence requires a clear understanding of different improvement approaches.
Organizations must choose between continuous improvement’s gradual evolution and process improvement’s targeted transformations – or implement both strategically.
The distinction between continuous improvement and process improvement methodologies has become crucial for business leaders seeking to enhance their operational efficiency and drive sustainable growth.
Key Highlights
- Comparing Two Major Business Enhancement Methods
- Systematic vs Goal-Oriented Improvement Approaches
- Short-term Results vs Long-term Cultural Change
- Implementation Strategies for Different Business Sizes
- Measuring Success Through Performance Metrics
- Industry-specific Applications and Case Studies
- Integration Methods for Maximum Business Impact
- Cost-benefit Analysis of Both Approaches
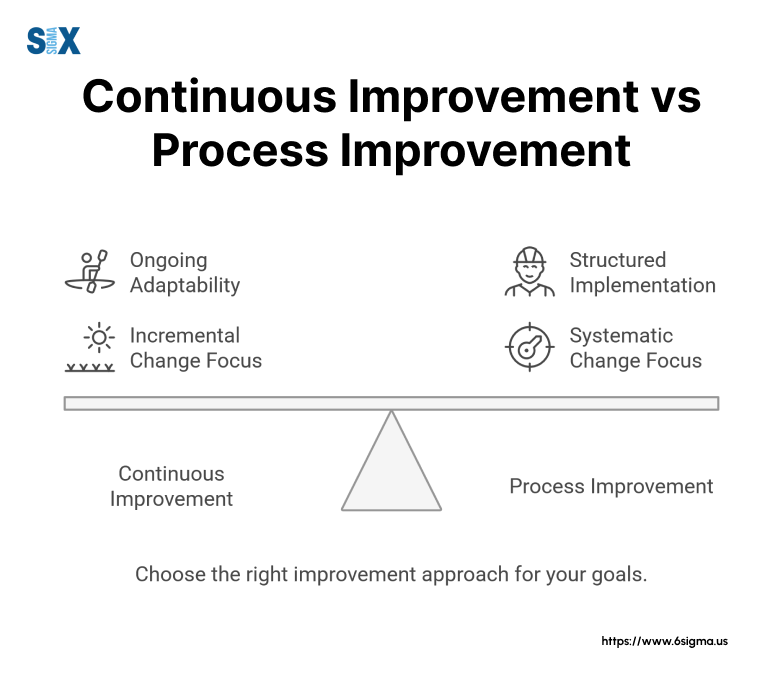
What are Improvement Methodologies?
There are major two methodologies under the six sigma umbrella. Continuous Improvement and Process Improvement.
What Is Continuous Improvement?
Continuous improvement represents a systematic approach to enhancing organizational performance through ongoing, incremental changes.
This methodology, often associated with Japanese business practices like Kaizen, emphasizes steady progress through small, frequent improvements rather than dramatic overhauls.
Organizations implementing continuous improvement focus on engaging every employee in the enhancement process.
From production floor workers to executive leadership, each team member contributes ideas and observations to refine existing processes.
Toyota’s production system stands as a prime example, where daily suggestions from workers have led to significant efficiency gains over time.
The success of continuous improvement relies on creating a culture where change becomes standard practice.
Teams regularly evaluate their work methods, identify potential enhancements, and implement solutions without waiting for major problems to arise.
This proactive stance helps organizations maintain competitive advantages and adapt to market changes efficiently.
Master the fundamentals of Lean Six Sigma and drive continuous improvement
Explore our Green Belt certification course covering Lean Six Sigma Overview and Process Variables Mapping.
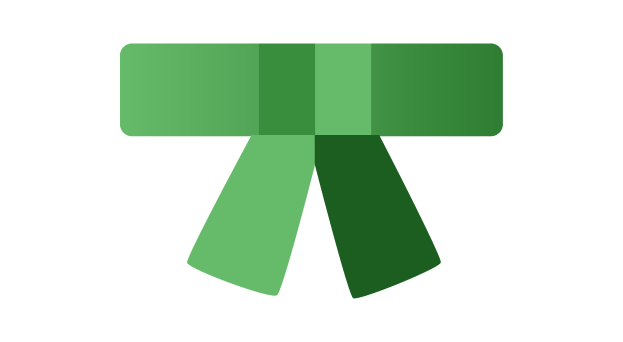
Defining Process Improvement
Process improvement targets specific operational workflows with defined objectives and timelines.
Unlike the gradual approach of continuous improvement, process improvement involves analyzing current procedures, identifying inefficiencies, and implementing targeted solutions to achieve measurable results.
Business process improvement typically follows structured methodologies such as Six Sigma or Lean Management.
These frameworks provide tools and techniques for measuring performance, analyzing data, and implementing changes.
Organizations often deploy process improvement when facing specific challenges or seeking particular performance targets.
The methodology requires dedicated teams or specialists who focus on individual processes until reaching predetermined goals.
For example, a manufacturing company might use process improvement to reduce production defects by 50% within six months through targeted interventions and systematic changes.
The Role Of Continual Improvement
Continual improvement bridges the gap between continuous and process improvement methodologies.
This approach combines regular enhancement cycles with periodic focused improvements. Organizations using continual improvement maintain ongoing refinement while allowing for occasional larger-scale changes when needed.
The Plan-Do-Check-Act (PDCA) cycle exemplifies continual improvement in action. Teams plan improvements, implement changes, evaluate results, and adjust approaches based on outcomes.
This cyclical process ensures organizations maintain forward momentum while remaining flexible enough to address specific challenges.
Many successful organizations implement continual improvement to balance short-term gains with long-term development.
This balanced approach helps maintain steady progress while allowing for targeted interventions when market conditions or business needs demand more substantial changes.
Each methodology serves distinct organizational needs and can deliver significant value when properly implemented.
Understanding these differences helps leaders select the most appropriate approach for their specific situations and objectives.
Comparing Continuous Improvement vs Process Improvement
Strategic Approach
Continuous improvement operates through incremental changes driven by employee involvement across all organizational levels.
Teams focus on making small, frequent adjustments to existing processes, fostering innovation and adaptability.
This methodology creates a culture of ongoing enhancement, where every team member becomes responsible for identifying and implementing improvements.
Process improvement takes a more structured approach, targeting specific workflows or systems with predetermined objectives.
Teams of specialists analyze current processes, identify bottlenecks, and implement significant changes to achieve measurable goals.
This method often involves larger-scale transformations within defined project timelines.
Operational Scope
The scope of continuous improvement extends throughout the organization, touching every department and function.
This broad reach enables organizations to develop cohesive improvement strategies that break down silos and promote cross-functional collaboration.
Teams work simultaneously on multiple small improvements, creating cumulative positive effects across operations.
Process improvement narrows its focus to specific operational areas or workflows requiring enhancement. Teams concentrate their efforts on resolving particular issues or achieving defined performance targets.
This targeted approach allows organizations to allocate resources efficiently and measure results more precisely.
Project Timeline
Continuous improvement operates without fixed endpoints, creating an ongoing cycle of enhancement and refinement.
Organizations implement this methodology as a permanent feature of their operations, understanding that improvement never truly ends.
This perpetual approach helps businesses stay agile and responsive to market changes.
Process improvement follows defined project timelines with clear start and end dates. Projects typically range from several weeks to months, depending on complexity and scope.
Teams work toward specific milestones and deliverables, measuring success against predetermined metrics.
Implementation Methods
Organizations implement continuous improvement through cultural change and employee empowerment.
Success depends on creating systems that encourage regular feedback, idea generation, and swift implementation of small changes.
Training focuses on problem-solving skills and improvement techniques applicable to daily operations.
Process improvement requires structured project management and specialized expertise. Organizations often deploy dedicated teams or external consultants who use specific methodologies like Six Sigma or Lean.
Implementation involves detailed planning, data analysis, and formal change management procedures.
Key Differences Between Improvement Methodologies
Aspect | Continuous Improvement | Process Improvement |
---|---|---|
Focus | Ongoing small changes | Targeted large changes |
Duration | Perpetual | Time-bound projects |
Scale | Organization-wide | Process-specific |
Resources | All employees involved | Specialist teams |
Results | Gradual gains | Immediate impact |
Leadership | Distributed responsibility | Project-based leadership |
Training | Universal skill development | Specialized expertise |
Metrics | Multiple small improvements | Specific project goals |
Risk Level | Lower risk, smaller changes | Higher risk, larger changes |
Culture Impact | Long-term cultural shift | Short-term process change |
This comparison framework helps organizations evaluate which methodology best suits their current needs and capabilities.
Many successful businesses implement both approaches strategically, using process improvement for specific challenges while maintaining continuous improvement for ongoing operational excellence.
Benefits and Limitations of Improvement Methodologies
Know the in-detail pros and cons of both the methodologies.
Advantages of Continuous Improvement
Continuous improvement delivers significant organizational benefits through sustained, incremental changes.
Toyota’s production system demonstrates these advantages clearly – their employees submit over 1 million improvement suggestions annually, resulting in substantial cost savings and efficiency gains.
Employee engagement rises markedly under continuous improvement programs. Organizations report increased job satisfaction and reduced turnover when teams actively participate in enhancement initiatives.
For example, Motorola documented a 25% increase in employee satisfaction scores after implementing their continuous improvement program.
The methodology also builds organizational resilience. Companies practicing continuous improvement adapt more readily to market changes and competitive pressures.
Boeing’s implementation of continuous improvement principles led to a 50% reduction in production defects over three years while increasing manufacturing flexibility.
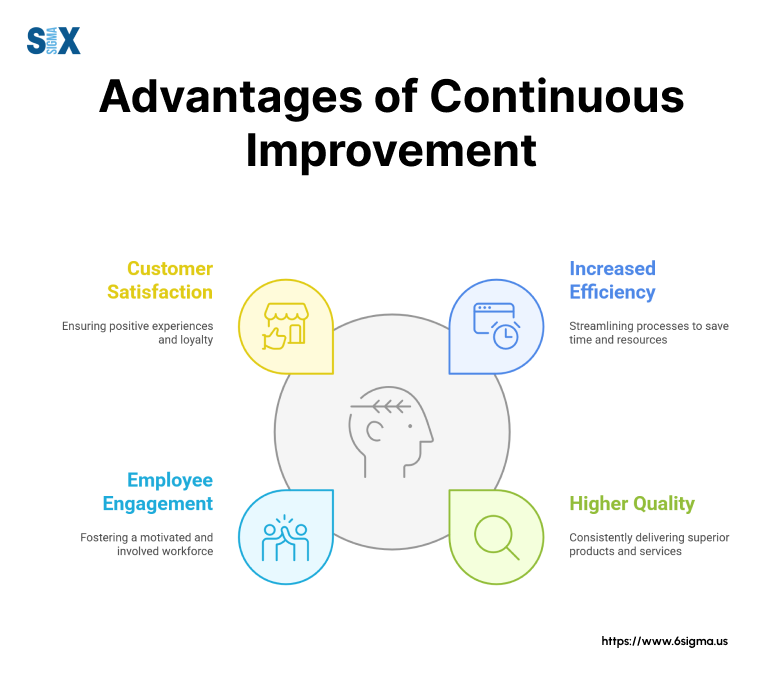
Challenges in Continuous Improvement
Resource demands present significant challenges for continuous improvement initiatives. Organizations must invest consistently in training, tools, and support systems.
Many companies struggle to maintain momentum when facing budget constraints or competing priorities.
Measuring return on investment proves difficult with incremental improvements. Unlike process improvement projects with defined metrics, continuous improvement benefits often appear gradually across multiple areas.
This complexity can make it harder to justify ongoing resource allocation.
Cultural resistance sometimes hampers continuous improvement efforts. Teams comfortable with established routines may resist regular changes, even small ones.
Organizations must actively manage this resistance through effective communication and demonstration of tangible benefits.
Strengths of Process Improvement
Process improvement delivers measurable results within defined time-frames. General Electric’s implementation of Six Sigma generated over $2 billion in savings through targeted process improvements.
These clear outcomes help justify investment and demonstrate value to stakeholders.
The methodology excels at solving specific operational problems. When Ford Motor Company faced quality issues, process improvement initiatives reduced defect rates by 60% in targeted production lines within six months.
Such focused improvements deliver rapid, visible results.
Process improvement also develops specialized expertise within organizations.
Teams gain deep knowledge of improvement methodologies and analytical tools, creating valuable internal capabilities for future projects.
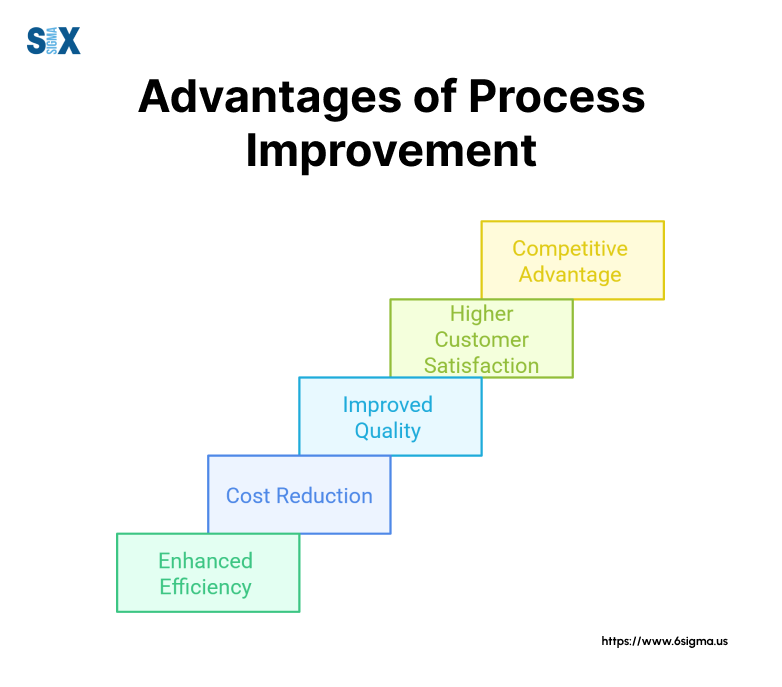
Drawbacks of Process Improvement
High implementation costs often accompany process improvement initiatives. Organizations must invest in specialized training, consultants, and tools.
These expenses can strain budgets, particularly for smaller companies or departments.
The focused nature of process improvement may create silos. Teams concentrate on specific areas while potentially overlooking interconnected processes or broader organizational needs.
This narrow focus can limit the overall impact of improvement efforts.
Sustainability presents another challenge. Once process improvement projects conclude, organizations may struggle to maintain gains without ongoing attention.
Wells Fargo found that 30% of their process improvements showed degradation within one year without proper sustainment plans.
Real-World Applications
Organizations achieve optimal results by selecting the appropriate methodology for specific situations.
Amazon combines both approaches effectively – using process improvement for specific logistics challenges while maintaining continuous improvement programs for ongoing operational excellence.
Healthcare organizations demonstrate similar hybrid approaches. Mayo Clinic employs process improvement for specific patient care protocols while fostering continuous improvement in daily operations. This balanced strategy delivers both immediate results and long-term development.
Manufacturing companies like Siemens leverage both methodologies strategically. Process improvement tackles specific production issues while continuous improvement maintains quality standards and drives innovation across operations.
Learn essential tools like Failure Modes & Effects Analysis and Waste Identification in our comprehensive Green Belt course.
Implementation Guide for Improvement Methodologies
Implementing Continuous Improvement
Successful continuous improvement implementation requires strategic planning and organizational commitment.
The first phase focuses on building foundational elements: leadership support, employee engagement programs, and basic improvement tools.
Organizations should establish clear communication channels and feedback mechanisms to capture improvement suggestions from all levels.
Training plays a crucial role in the second phase. Teams need skills in problem identification, root cause analysis, and solution development.
Toyota’s successful implementation model demonstrates the importance of starting with simple tools and gradually introducing more sophisticated techniques as capabilities mature.
The third phase involves creating sustainable systems. Organizations must develop metrics to track improvements, recognition programs to reward participation, and documentation processes to share successful practices.
Regular review meetings help maintain momentum and ensure alignment with organizational goals.
Process Improvement Implementation Steps
Process improvement implementation follows a more structured pathway. The initial stage requires careful selection of improvement targets based on business impact and resource availability.
Organizations should prioritize projects that align with strategic objectives and offer clear return on investment.
Project planning forms the second crucial stage. Teams must define scope, objectives, timelines, and success metrics.
GE’s successful implementation of Six Sigma demonstrates the importance of detailed project charters and well-defined roles for team members.
Execution represents the third critical stage. Teams collect data, analyze current processes, develop solutions, and implement changes according to project timelines. Regular status reviews and adjustment periods ensure projects stay on track and deliver expected results.
Creating A Hybrid Implementation Model
Many organizations benefit from combining both methodologies through a hybrid implementation approach.
This model starts with establishing continuous improvement as the organizational foundation while deploying process improvement for specific challenges.
The hybrid model requires careful coordination. Organizations should create central improvement teams that oversee both continuous and process improvement initiatives.
These teams coordinate resources, prevent duplication of efforts, and ensure methodologies complement rather than compete with each other.
Success in hybrid implementation depends on clear governance structures. Organizations need defined criteria for selecting improvement approaches, resource allocation procedures, and integrated measurement systems. IBM’s successful hybrid model demonstrates how organizations can balance both methodologies effectively.
Key Implementation Considerations
Resource allocation demands careful attention in any implementation model. Organizations must balance immediate project needs with long-term capability development.
Successful implementations typically start with pilot programs before expanding across the organization.
Technology support plays an increasingly important role. Organizations should invest in appropriate tools for tracking improvements, managing projects, and sharing knowledge.
Digital platforms can significantly enhance implementation effectiveness and sustainability.
Change management remains critical throughout implementation. Organizations must actively manage resistance, communicate benefits, and celebrate successes. Regular assessment of implementation progress helps identify and address challenges early.
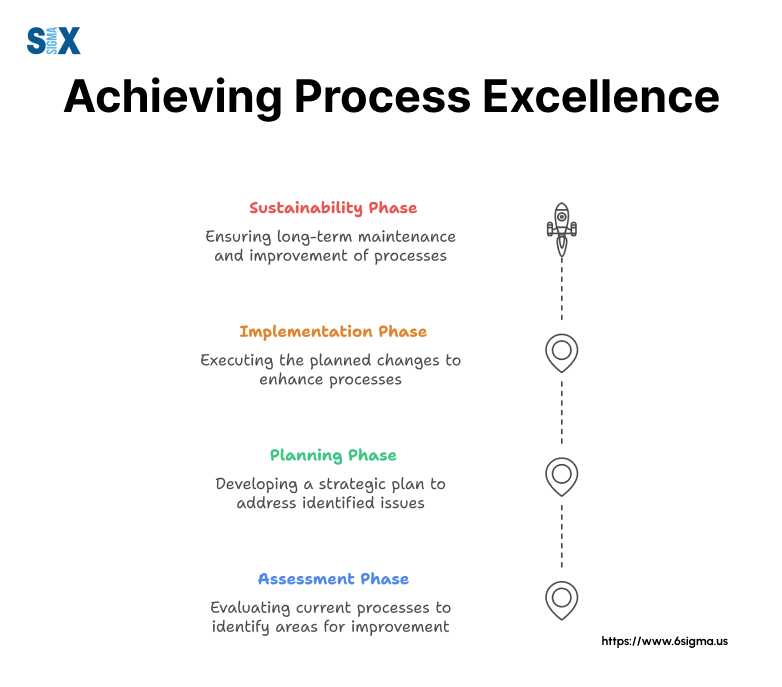
This implementation guide provides organizations with structured approaches for deploying improvement methodologies.
Success depends on selecting and adapting these approaches based on organizational context, resources, and objectives.
Turn theory into practice with structured improvement methodologies with our Green Belt program covering everything from project selection to control plans.
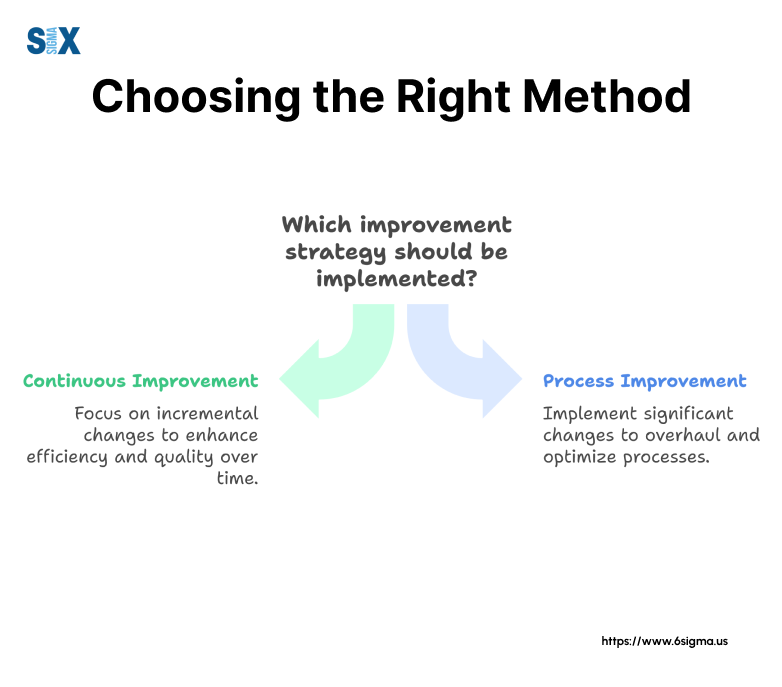
Integration Strategies for Improvement Methodologies
Organizations achieve superior results by strategically combining continuous and process improvement methodologies.
This integrated approach leverages the strengths of both systems while minimizing their individual limitations.
Major corporations like Siemens demonstrate the power of integration through their unified improvement program, which delivered 30% efficiency gains across operations.
Strategic integration requires careful planning and coordination. Organizations must establish clear guidelines for when to apply each methodology.
For example, continuous improvement drives daily operational excellence, while process improvement tackles specific performance challenges. This balanced approach ensures resources deploy effectively across improvement initiatives.
The integration process demands strong governance structures. Organizations should create central improvement teams that coordinate activities, allocate resources, and maintain alignment between different improvement initiatives.
These teams serve as bridges between continuous improvement activities and targeted process improvement projects.
Organizational Alignment Strategies
Successful integration depends on aligning improvement efforts with organizational goals. Companies must establish clear connections between strategic objectives and improvement initiatives.
Microsoft’s integrated improvement program demonstrates this alignment, linking each initiative directly to corporate strategic pillars.
Leadership plays a crucial role in maintaining strategic alignment. Executive teams must actively support both improvement methodologies while ensuring they work together cohesively.
Regular strategy reviews help maintain focus and adjust improvement priorities based on organizational needs.
Performance measurement systems require adaptation to support integrated improvement efforts. Organizations should develop metrics that capture both incremental gains from continuous improvement and larger impacts from process improvement projects.
This balanced measurement approach provides accurate assessment of overall improvement effectiveness.
Building Sustainable Integration
Sustainability demands careful attention to organizational culture. Teams must understand how both methodologies contribute to organizational success.
Regular communication and training help maintain awareness and engagement across improvement initiatives.
Resource management becomes more sophisticated under integrated approaches. Organizations must balance investments between ongoing continuous improvement activities and targeted process improvement projects.
Successful companies typically allocate resources based on strategic priorities while maintaining minimum support levels for both methodologies.
Knowledge management systems play vital roles in sustainable integration.
Organizations should establish mechanisms for sharing insights and best practices between continuous and process improvement teams.
These systems help maximize learning and prevent duplicate efforts across improvement initiatives.
Integration Success Factors
Clear governance structures significantly impact integration success. Organizations need defined decision-making processes for selecting improvement approaches and allocating resources.
These structures ensure efficient coordination between different improvement activities while maintaining strategic alignment.
Technology support enhances integration effectiveness. Modern improvement management platforms help organizations track activities, measure results, and share knowledge across both methodologies. These tools provide valuable data for decision-making and resource allocation.
Employee engagement remains critical for successful integration. Organizations must create opportunities for staff to participate in both continuous and process improvement activities.
This involvement helps build understanding and support for integrated improvement approaches while developing organizational capabilities.
The integration of continuous and process improvement methodologies creates powerful synergies for organizational development.
Through careful planning, strong governance, and sustained commitment, organizations can leverage these combined approaches to drive superior performance and competitive advantage.
Measuring Success in Improvement Initiatives
Effective measurement of continuous improvement requires both leading and lagging indicators.
Leading indicators track employee participation rates, number of improvement suggestions submitted, and implementation rates of proposed changes.
These metrics help predict future success and identify areas needing attention.
Quality metrics play a central role in continuous improvement measurement. Organizations should monitor defect rates, customer satisfaction scores, and process capability indices.
Toyota’s measurement system demonstrates this approach, tracking daily quality metrics across all production areas to maintain excellence.
Operational efficiency indicators provide crucial insights into continuous improvement effectiveness. Key metrics include cycle time reductions, productivity improvements, and waste elimination measurements. These indicators help organizations quantify the cumulative impact of small, ongoing improvements.
Process Improvement Performance Metrics
Process improvement projects demand specific, measurable outcomes. Organizations typically track project completion rates, achievement of targeted improvements, and financial benefits realized.
GE’s Six Sigma program exemplifies this approach, requiring clear financial targets for each improvement project.
Time-based metrics help evaluate process improvement effectiveness. Organizations monitor project duration, implementation speed, and time to benefit realization.
These measurements ensure projects deliver results within expected timeframes while maintaining momentum.
Resource utilization metrics provide important context for process improvement initiatives. Teams track labor hours invested, consultant costs, and technology investments. These measurements help organizations evaluate the efficiency of improvement efforts and optimize resource allocation.
ROI Analysis Framework
Financial impact assessment requires structured evaluation methods.
Organizations should establish clear frameworks for calculating return on investment from both continuous and process improvement initiatives. This analysis includes direct cost savings, productivity gains, and revenue improvements.
Indirect benefits demand careful consideration in ROI calculations. Organizations must account for improved employee engagement, enhanced customer satisfaction, and strengthened competitive position.
While these benefits prove harder to quantify, they significantly impact overall ROI.
Long-term value creation deserves special attention in ROI analysis.
Organizations should evaluate sustained performance improvements, capability development, and cultural transformation. These enduring benefits often exceed immediate financial returns from improvement initiatives.
Measurement Best Practices
Regular reporting cycles maintain focus on improvement outcomes. Organizations should establish monthly reviews of continuous improvement metrics while monitoring process improvement projects weekly.
This cadence ensures timely identification of issues and opportunities.
Data visualization enhances measurement effectiveness. Organizations benefit from clear, accessible dashboards that display key metrics and trends.
These visual tools help stakeholders quickly understand performance and make informed decisions.
Measurement systems require periodic review and adjustment. Organizations should evaluate metric relevance, update targets, and refine calculation methods based on changing business needs.
This dynamic approach ensures measurement systems continue supporting organizational objectives effectively.
Making The Right Choice: Continuous Improvement vs Process Improvement
The distinction between continuous improvement and process improvement methodologies shapes organizational success in today’s competitive business environment.
These approaches offer unique advantages and serve different organizational needs, making the selection process crucial for achieving desired outcomes.
Key Distinctions Reviewed
Continuous improvement drives organizational excellence through steady, incremental changes across operations. This methodology builds strong improvement cultures, engages employees at all levels, and creates sustainable performance gains.
Organizations like Toyota demonstrate how continuous improvement transforms operations through persistent focus on small enhancements.
Process improvement delivers targeted solutions for specific operational challenges. This structured approach enables organizations to achieve significant improvements within defined time-frames.
Companies like GE showcase how process improvement methodologies solve complex operational issues through focused initiatives and specialized expertise.
Strategic Implementation Considerations
Organizations must evaluate several factors when selecting improvement approaches. Resource availability, organizational culture, and business objectives play crucial roles in determining the most effective methodology.
Many successful organizations implement hybrid approaches, combining continuous and process improvement strategies to maximize benefits.
The implementation journey requires careful planning and sustained commitment. Organizations should establish clear governance structures, develop appropriate metrics, and create supporting systems for their chosen methodology.
These foundations ensure improvement initiatives deliver expected results while building organizational capabilities.
Future Success Factors
Digital transformation continues reshaping improvement methodologies. Organizations must adapt their approaches to leverage new technologies and data analytics capabilities.
This evolution enables more precise measurement of improvement impacts while supporting faster implementation of changes.
Organizational agility becomes increasingly important in methodology selection. The ability to switch between or combine improvement approaches helps organizations respond effectively to changing market conditions.
This flexibility, supported by strong improvement capabilities, creates sustainable competitive advantages.
Success in improvement initiatives ultimately depends on matching methodologies to organizational needs and capabilities.
Whether choosing continuous improvement, process improvement, or a hybrid approach, organizations must maintain clear alignment with strategic objectives while building robust implementation systems.
The journey toward operational excellence continues evolving, but the fundamental choice between continuous improvement and process improvement remains central to organizational success.
Through careful evaluation and strategic implementation, organizations can leverage these methodologies to drive superior performance and sustainable growth.
Frequently Asked Questions about Improvement Methodologies
A. Process improvement focuses on specific operational changes within defined time-frames, while continuous improvement involves ongoing, incremental enhancements across all organizational areas. Process improvement typically delivers larger, targeted changes, whereas continuous improvement creates sustained progress through smaller, frequent adjustments.
A. Process engineering involves redesigning entire workflows or systems from the ground up, often requiring significant technical expertise. Continuous improvement builds upon existing processes through gradual refinements. While process engineering creates new operational frameworks, continuous improvement enhances established procedures incrementally.
A. Process re-engineering fundamentally restructures operations, often resulting in dramatic organizational changes. Continuous improvement maintains existing structural frameworks while making steady enhancements. Process re-engineering typically requires larger investments and carries higher risks, whereas continuous improvement presents lower risks through gradual evolution.
A. Transformation involves fundamental changes to organizational structure, culture, and operations. Continuous improvement focuses on steady enhancement of current practices. While transformation creates significant organizational shifts, continuous improvement delivers sustained progress through systematic refinement of existing processes.
A. Kaizen represents one methodology within continuous improvement philosophy. While all Kaizen practices qualify as continuous improvement, not all continuous improvement initiatives follow Kaizen principles. Kaizen emphasizes specific Japanese management practices, whereas continuous improvement encompasses various methodological approaches.
A. Six Sigma provides a structured approach to process improvement using statistical analysis and data-driven decision-making. This methodology aims to reduce defects and variations in processes through defined project phases: Define, Measure, Analyze, Improve, and Control (DMAIC). Organizations like Motorola and GE have achieved significant results using Six Sigma methods.
A. Process improvement typically divides into incremental improvement and breakthrough improvement. Incremental improvement focuses on steady enhancements to existing processes, while breakthrough improvement creates significant operational changes. Both types serve important roles in organizational development, depending on specific needs and objectives.
A. While Agile incorporates continuous improvement principles, it represents a specific project management methodology primarily used in software development. Continuous improvement applies broadly across all organizational functions. Agile emphasizes iterative development and customer feedback, while continuous improvement focuses on systematic process enhancement across operations.
SixSigma.us offers both Live Virtual classes as well as Online Self-Paced training. Most option includes access to the same great Master Black Belt instructors that teach our World Class in-person sessions. Sign-up today!
Virtual Classroom Training Programs Self-Paced Online Training Programs