Process Improvement Methodologies. What is the Continuous Improvement Model
Keeping up with the changing market dynamics and customer needs is key to survival. This calls for a continuous improvement model in business processes, products/services, etc. to gain and maintain an edge over competitors.
The continuous improvement model is a systematic approach to identifying and implementing incremental changes to drive efficiency, reduce waste, improve quality, productivity, and customer satisfaction.
The continuous improvement model is based on the principle – that small changes over time lead to big benefits in the long term. It develops a mindset of continuous learning, experimentation, and adaptation. Effectively leading organizations to deftly deal with changing dynamics, consumer needs, and tech advancements.
If implemented currently, it propels business growth and revenue by streamlining operations, removing non-value-adding activities, and resource optimization.
Key Highlights
- Businesses always pursue better workflows, less waste, and more delighted clients.
- Models like Lean, Six Sigma, and PDCA empower constant upgrading through incremental refinement.
- These programs optimize proficiency, trash scrap, and defective rates, maximizing outputs safely and affordably.
- Common programs involve Kaizen, Total Quality Management, and more.
- Executing ceaseless betterment demands an environment prizing learning, empowering personnel, and choices evidenced empirically.
- Necessary instruments involve stream-mapping, underlying cause discernments, 5S configuration, mistake-proofedness, and managerial walkthroughs.
- Preserving refinement necessitates leadership backing, change management, and unrelenting surveillance adjusting.
What is the Continuous Improvement Model?
Amid fluid commercial landscapes, enterprises must repeatedly refine operations to retain competitors’ edge. This inspires continuous betterment paradigms.
The continuous improvement model denotes a philosophy and methodology enhancing fare through incessant progression. Adopting models boosts proficiency while slashing waste and energizing originality.
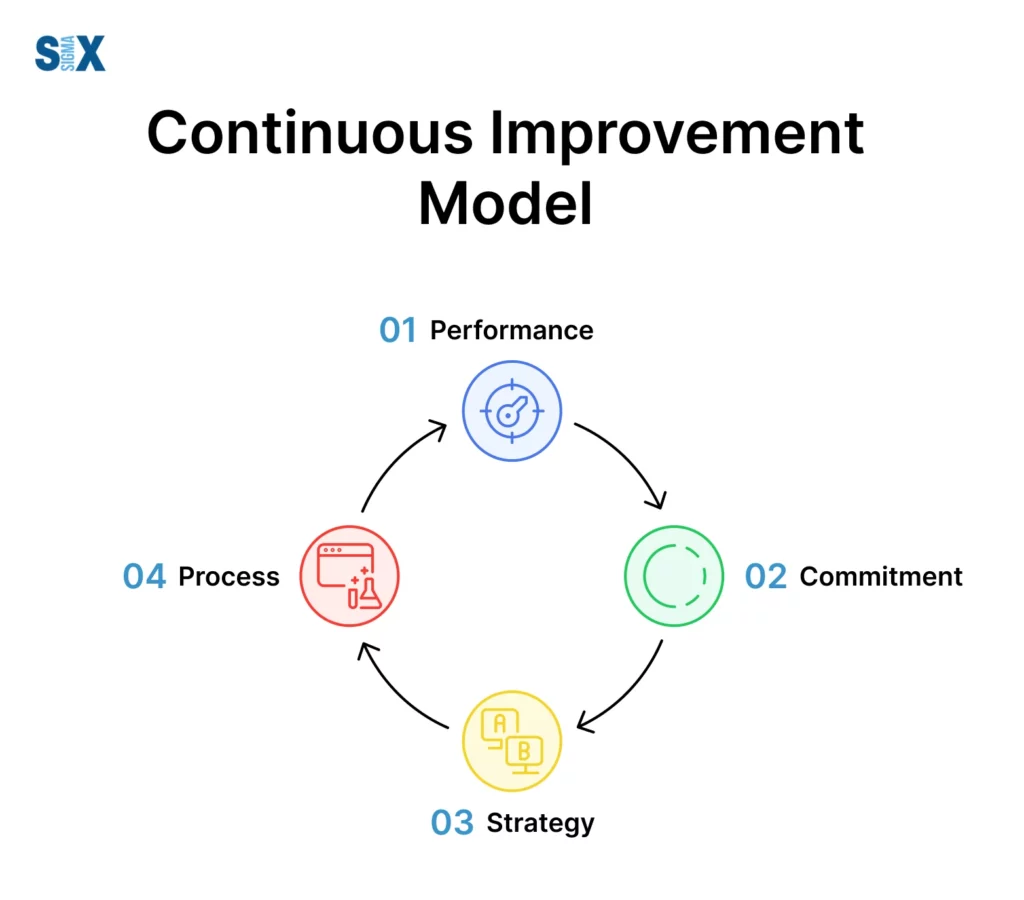
Notions arise from quality-centered ideologies like Lean, Six Sigma, and Toyota—targeting scrap, diversity, and inefficient moves amid operations.
Models chart a disciplined refinement framework. Cyclical planning/executing/surveilling/modifying amid data and responses characterizes progress.
Demographics incorporate PDCA, Kaizen, Lean Six Sigma, and DMAIC—diverse yet synchronizing fundamental additive refinement.
Correct implementation necessitates cultural reconfiguration motivating employee problem-solving and unending quests for mastery.
Explore how continuous improvement fits into the quality management framework. Lean Six Sigma Overview course introduces you to a comprehensive toolkit to drive efficiency and quality.
By embracing advancement steadfastly, enterprises achieve sustainable growth, more delighted buyers, and leadership amid unpredictability through improvisational skills navigating variability.
Continuous Improvement Tools and Techniques
Successful continuous improvement model requires the right tools and techniques to identify opportunities, analyze problems, implement solutions, and sustain gains. Some powerful continuous improvement tools and methodologies include:
Lean Six Sigma: This data-driven approach combines lean manufacturing/lean enterprise techniques with Six Sigma’s rigorous focus on reducing defects and process variations. Tools like value stream mapping, 5S, and DMAIC are core to Lean Six Sigma.
Kaizen: The Japanese philosophy of kaizen emphasizes ongoing, incremental changes and empowering employees at all levels to identify and act on improvement opportunities. Kaizen techniques include kaizen events/blitzes, Gemba walks, and quality circles.
Root Cause Analysis: Techniques like fishbone (cause-and-effect) diagrams, the 5 Whys, fault tree analysis, and others help teams drill down to the true underlying causes of problems rather than just addressing symptoms.
Statistical Process Control: Tools like control charts, capability analysis, and hypothesis testing provide a statistical framework for monitoring process performance and variation over time.
Poka-Yoke (Mistake-Proofing): These techniques, like using physical devices or mechanisms, aim to prevent errors and defects from occurring in the first place.
Hoshin Kanri (Policy Deployment): This methodology ensures that continuous improvement efforts are aligned with and driven by the organization’s overarching goals and strategic direction.
Voice of the Customer: Surveys, interviews, ethnography, and other techniques capture customer needs, expectations, and dissatisfactions to prioritize improvements.
The key is having a structured way to identify opportunities, get to root causes, develop countermeasures, and follow up to hold the gains.
Master these continuous improvement tools and techniques. Lean Fundamentals course offers practical training in essential CI methodologies.
Implementing a Continuous Improvement Model
Adopting a continuous improvement model requires a systematic approach and commitment from all levels of an organization. The following steps can help effectively implement the continuous improvement model:
Define Goals and Metrics for the Continuous Improvement Model
Before embarking on any improvement initiative, it’s crucial to establish clear goals aligned with the organization’s strategic objectives.
These goals should be specific, measurable, achievable, relevant, and time-bound (SMART). Additionally, define the key performance indicators (KPIs) that will measure progress and success.
Gain Leadership Buy-In
Continuous improvement efforts require strong leadership support and active involvement. Leaders should communicate the vision, allocate necessary resources, and serve as role models, encouraging and recognizing improvement efforts.
Build a Culture of Continuous Improvement
Creating a culture that embraces continuous improvement is essential. This involves training employees on continuous improvement models/methodologies, encouraging idea generation, and recognizing and rewarding improvement efforts. Employee empowerment and engagement are key drivers of success.
Map and Analyze Processes for Continuous Improvement Model
Identify and document the critical processes within the organization. Use techniques like value stream mapping and process flow diagrams to visualize and analyze these processes, identifying areas for improvement, waste elimination, and optimization opportunities.
Prioritize Improvement Projects
Based on the process analysis and alignment with organizational goals, prioritize improvement projects. Consider factors such as potential impact, resource requirements, and project complexity when determining the priority order.
Assemble Cross-Functional Teams
Continuous improvement initiatives often require cross-functional collaboration. Assemble teams with representatives from different departments or functions affected by the targeted process. This diversity of perspectives and expertise fosters more comprehensive solutions.
Use Continuous Improvement Tools and Techniques
Leverage various continuous improvement tools and methodologies, such as Lean Six Sigma, Kaizen, PDCA (Plan-Do-Check-Act) cycle, root cause analysis, and others, to drive improvements systematically.
Implement and Monitor Improvements
Once improvement solutions are identified, develop an implementation plan, allocate resources, and execute the changes. Continuously monitor progress, measure results against the defined KPIs, and make necessary adjustments.
Standardize and Sustain Improvements with the Continuous Improvement Model
After successful implementation, standardize the improved processes and integrate them into the organization’s operations. Develop mechanisms to sustain the improvements, such as regular audits, training programs, and continuous monitoring.
Foster Continuous Learning and Knowledge Sharing
Encourage continuous learning by capturing lessons learned, sharing best practices, and celebrating successes. This helps reinforce the continuous improvement culture and facilitates knowledge transfer across the organization.
Sustaining Continuous Improvement
Creating a culture of continuous improvement is critical for the long-term success of any continuous improvement initiative. Even after implementing new processes and seeing great results, it can be easy to become complacent and revert to old ways of working. To sustain continuous improvement, organizations must ingrain it into their culture and values.
Employee Empowerment and Engagement
Frontline employees are closest to the processes and have valuable insights into areas for improvement. Empowering and engaging employees at all levels is key to identifying continuous improvement opportunities. This can involve training on continuous improvement methodologies, giving employees a voice in process changes, and rewarding those who drive improvements.
Leadership Support for Continuous Improvement Model
Support from top leadership is vital for sustaining a continuous improvement culture. Leaders must exemplify the principles, provide training and resources, celebrate successes, and ensure the continuous improvement model is a strategic priority across the organization.
Continuous Improvement Model as a Core Value
Continuous improvement cannot just be a program or initiative – it must become a core value ingrained in the company’s DNA. It should be part of the onboarding process, regularly discussed in meetings, and tied to performance goals and compensation.
Tracking and Accountability
Implementing tracking mechanisms and creating accountability for continuous improvement model is important. This could involve visual management systems, periodic audits, and benchmarking against best practices. Celebrating wins and sharing results widely helps motivate the organization.
Dedicated Resources
While every employee should be responsible for continuous improvement, having dedicated resources like a continuous improvement team or black belts helps institutionalize it. This team can develop training, drive projects, and ensure efforts don’t get deprioritized.
Case Studies and Success Stories of Continuous Improvement (CI) Model
Seeing continuous improvement models in action can help illustrate their value and potential impact. Here are some notable case studies and success stories of organizations that have successfully implemented continuous improvement models:
Toyota Production System
Toyota is widely regarded as the pioneer of lean manufacturing principles and kaizen (continuous improvement).
The Toyota Production System has been studied and emulated by companies worldwide. Through kaizen, Toyota was able to dramatically reduce waste, improve quality, and increase efficiency across its production lines.
Key principles like just-in-time manufacturing, jidoka (autonomation), and respect for people created a culture of continuous improvement.
Motorola – Six Sigma
Motorola is credited with developing the Six Sigma methodology in the 1980s. By training employees in data-driven process optimization, Motorola was able to save billions of dollars in manufacturing costs.
The continuous improvement model focus allowed Motorola to drastically reduce defects and enhance product quality and customer satisfaction. Six Sigma has since been adopted by companies like GE, Sony, Honda, and many others.
Danaher Corporation
Danaher is an example of a modern company that has built a culture completely centered around the principles of the continuous improvement model and the Danaher Business System.
Through kaizen, Lean, DBS, and other methodologies, Danaher has been able to drive consistent profitable growth across its diverse set of businesses for decades.
Autoliv – Lean Six Sigma
The automotive safety company Autoliv successfully combined Lean and Six Sigma principles to reduce lead times, improve quality, and achieve over $100 million in cost savings over a multi-year period.
Inspired by these success stories? Want to create your own? Lean Six Sigma Green Belt prepares you to lead continuous improvement initiatives and drive significant results in your organization.
What’s Next…
With cultures embracing change, companies surpass peers, please buyers more, and secure prosperity over the long haul.
The key involves selecting enhancement techniques tailored aptly—to fit company needs, industry, and present operations.
Whether PDCA, Lean Six Sigma, or alternate methods, guidance should be customized accordingly.
Leadership’s imperative backing and personnel investment constitute critical components facilitating any refinement campaign’s successful, sustained execution.
Training, resources, and incentives nourish innovative problem-solving-driven teams.
Importantly, betterment persists endlessly. Regularly examining and tweaking strategies, tools, and methodologies readjusts enterprises adapting nimbly to evolutionary commercial seascapes.
Embracing improvement unlocks enterprises’ entirety, inspires ingenuity, and yields growth sustainably amid volatility.
SixSigma.us offers both Live Virtual classes as well as Online Self-Paced training. Most option includes access to the same great Master Black Belt instructors that teach our World Class in-person sessions. Sign-up today!
Virtual Classroom Training Programs Self-Paced Online Training Programs