Business Process Improvement: Why Every Company Should Implement It
Business Process Improvement is a systematic approach to identifying, analyzing, and enhancing existing business processes to achieve greater efficiency, effectiveness, and overall performance.
Business Process Improvement serves as a critical tool in this endeavor, offering a structured methodology to streamline workflows, reduce costs, and ultimately deliver superior value to customers.
Key Highlights
- Defining Business Process Improvement (BPI) and its critical role in organizational success
- Exploring core methodologies
- Essential tools for process optimization and analysis
- Implementing Business Process Improvement (BPI)
- Industry-specific applications of BPI principles
- Future trends
Introduction to Business Process Improvement
Business Process Improvement is a systematic approach to analyzing, redesigning, and optimizing business processes to achieve enhanced efficiency, effectiveness, and overall performance.
It’s not just about making minor tweaks; it’s about fundamentally rethinking how we do business.
The importance of Business Process Improvement (BPI) cannot be overstated.
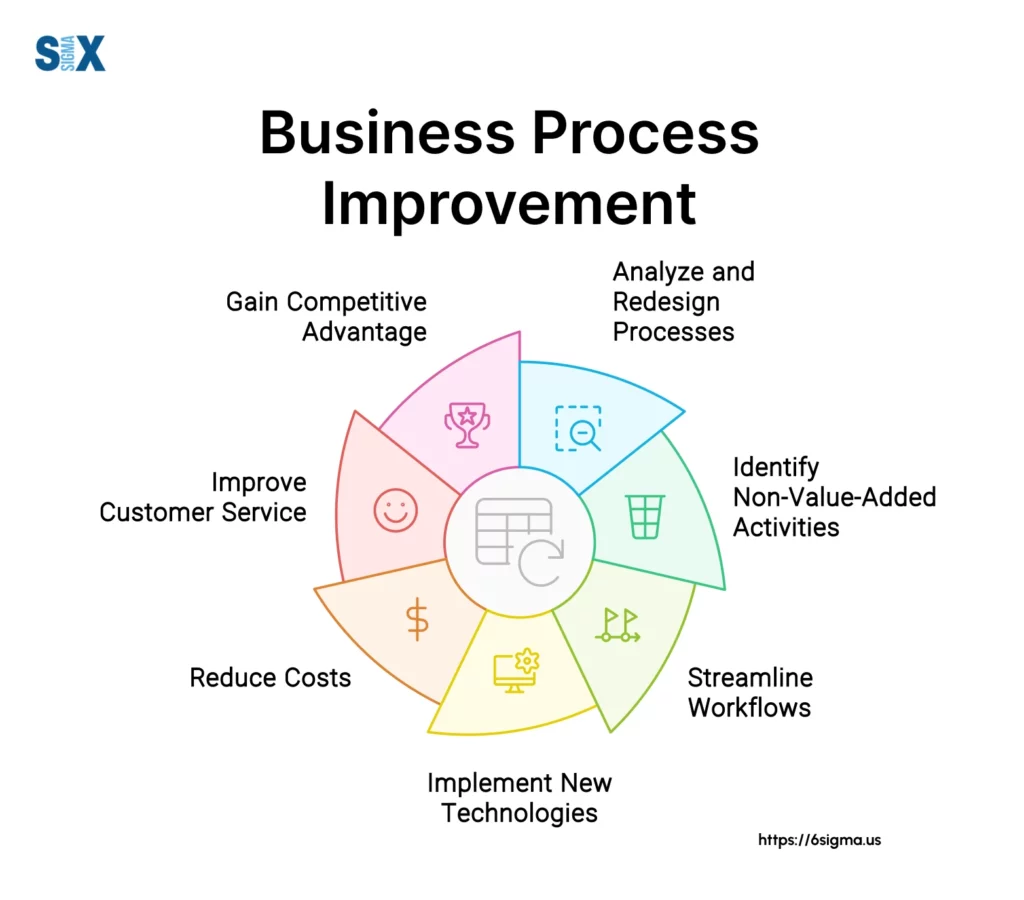
Goals of Process Optimization
The primary goals of process optimization through Business Process Improvement (BPI) are multifaceted.
Key objectives include
- Streamlining workflows to eliminate redundancies and bottlenecks
- Reducing operational costs while improving quality
- Enhancing customer satisfaction through improved product or service delivery
- Increasing overall productivity and efficiency
- Fostering a culture of continuous improvement within the organization
These goals align with the broader aim of creating a lean, agile, and responsive organization capable of thriving in an ever-changing business environment.
Benefits of Workflow Efficiency with Business Process Improvement
Improved workflow efficiency is one of the most tangible outcomes of successful BPI initiatives.
Numerous organizations reap substantial benefits from optimized workflows:
- Reduced cycle times: By eliminating non-value-added activities, companies can significantly decrease the time it takes to complete processes.
- Improved resource utilization: Efficient workflows ensure that human and material resources are used optimally.
- Enhanced quality: Streamlined processes lead to fewer errors and defects, resulting in higher quality outputs.
- Increased employee satisfaction: When employees can work more efficiently, it leads to greater job satisfaction and engagement.
- Better decision-making: Efficient workflows often come with improved data collection and analysis, enabling more informed decision-making at all levels of the organization.
These benefits collectively contribute to improved operational performance and a stronger competitive position in the market.
Key Methodologies in Business Process Improvement
Explore the core methodologies driving process improvement, from Six Sigma to Lean Management.
Discover how these powerful approaches can transform your organization’s efficiency and effectiveness.
Six Sigma Methodology and DMAIC Framework
Six Sigma is a data-driven approach that aims to reduce process variation and defects to a level of 3.4 defects per million opportunities.
DMAIC framework – Define, Measure, Analyze, Improve, and Control.
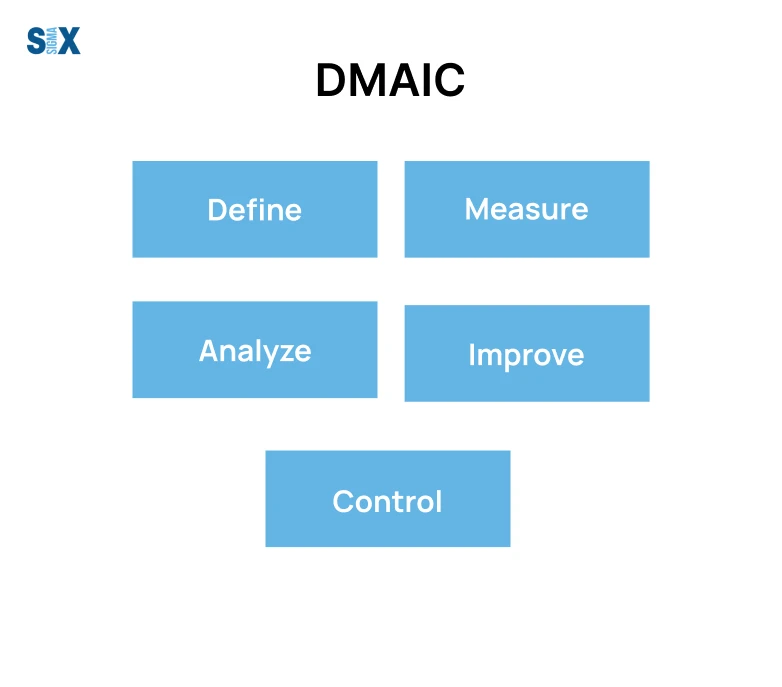
DMAIC framework provides a structured approach to problem-solving and process improvement:
- Define: Clearly articulate the problem and project goals.
- Measure: Collect data to establish baseline performance.
- Analyze: Use statistical tools to identify root causes of problems.
- Improve: Implement and validate solutions to address root causes.
- Control: Establish mechanisms to sustain improvements over time.
This systematic approach ensures that improvements are based on data and facts rather than assumptions or guesswork.
Lean Management and Waste Elimination with Business Process Improvement
Lean management, originating from Toyota’s production system, focuses on maximizing customer value while minimizing waste.
The core of Lean is identifying and eliminating eight types of waste:
- Defects
- Overproduction
- Waiting
- Non-utilized talent
- Transportation
- Inventory
- Motion
- Excess processing
By targeting these wastes, organizations can streamline their processes, reduce costs, and improve overall efficiency.
Kaizen Philosophy and Continuous Improvement
Kaizen, which means “change for the better” in Japanese, is a philosophy of continuous improvement that I’ve found to be incredibly powerful when integrated into an organization’s culture.
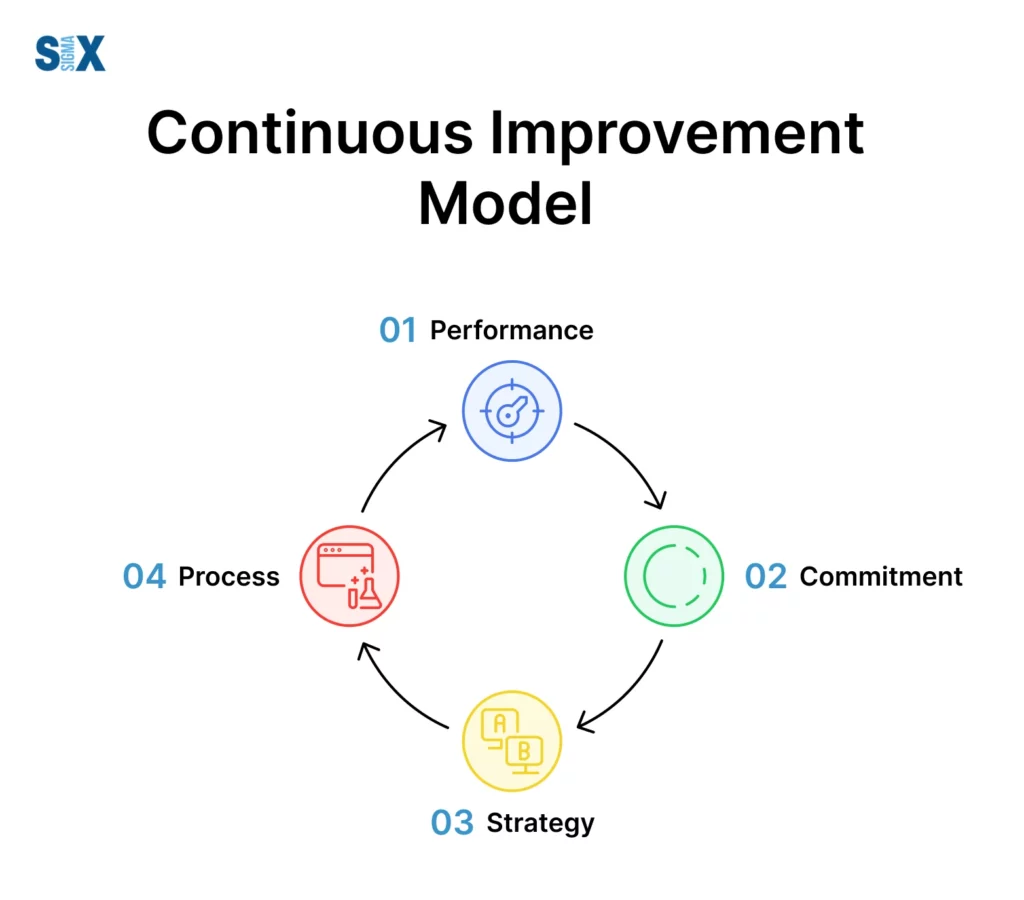
Unlike some methodologies that focus on big, dramatic changes, Kaizen emphasizes small, incremental improvements that add up over time.
This bottom-up approach to improvement can lead to significant cumulative benefits and helps create a culture of continuous learning and innovation.
Total Quality Management (TQM) with Business Process Improvement
Total Quality Management is a comprehensive approach to quality improvement that emphasizes customer satisfaction, employee involvement, and data-driven decision making.
TQM principles successfully applied in various settings, from manufacturing to service industries.
Key elements of TQM include
- Customer focus
- Total employee involvement
- Process-centered approach
- Integrated system
- Strategic and systematic approach
- Continual improvement
- Fact-based decision making
- Communications
When implemented effectively, TQM can lead to improved product quality, increased customer satisfaction, and enhanced organizational performance.
Business Process Re-engineering
Business Process Re-engineering (BPR) is a more radical approach to improvement that involves fundamentally rethinking and redesigning business processes.
BPR can be particularly effective when incremental improvements are no longer sufficient to meet organizational goals.
BPR typically involves
- Identifying core processes
- Analyzing current processes
- Redesigning processes from the ground up
- Implementing new processes
- Continuous monitoring and improvement
While BPR can be more disruptive than other methodologies, it can also lead to dramatic improvements in key performance metrics when executed properly.
Essential Tools and Techniques for Process Optimization
These are the crucial tools and techniques that form the backbone of successful process optimization.
Learn how to leverage process mapping, root cause analysis, and KPIs to drive meaningful improvements.
Process Mapping and Value Stream Analysis
Process mapping and value stream analysis are fundamental tools in the BPI toolkit.
Process mapping involves creating a visual representation of a business process, showing each step, decision point, and flow of information or materials.
It provides a clear picture of how work is currently done and can reveal inefficiencies, redundancies, and bottlenecks.
Value stream analysis takes this a step further by focusing on the flow of value through the process.
It helps identify which activities add value from the customer’s perspective and which ones are wasteful.
Root Cause Analysis and Problem-solving
Root cause analysis is a critical skill in process improvement.
It involves digging deeper to identify the underlying causes of problems rather than just addressing symptoms.
Techniques like the “5 Whys” and Ishikawa (fishbone) diagrams are invaluable tools in this process.
What may initially appear to be a simple problem often has complex underlying causes that span multiple areas of the organization.
Problem-solving in BPI is a structured process that involves
- Defining the problem
- Gathering and analyzing data
- Generating potential solutions
- Selecting and implementing the best solution
- Monitoring results and making adjustments as needed
This systematic approach ensures that solutions are based on facts and data rather than hunches or assumptions.
Performance Metrics and Key Performance Indicators (KPIs)
You can’t improve what you don’t measure.
That’s why establishing appropriate performance metrics and Key Performance Indicators (KPIs) is crucial in any Business Process Improvement (BPI) initiative.
Good KPIs should be
- Relevant to the organization’s goals
- Measurable and quantifiable
- Actionable
- Timely
- Easy to understand and communicate
Examples of KPIs might include cycle time, defect rate, customer satisfaction scores, or cost per unit.
The specific KPIs will depend on the nature of the process and the organization’s strategic objectives.
Benchmarking and Best Practices of Business Process Improvement
Benchmarking involves comparing your organization’s processes and performance against industry leaders or best-in-class organizations.
It’s a powerful tool for identifying improvement opportunities and setting performance targets.
When done correctly, benchmarking can provide valuable insights into:
- How top performers achieve their results
- What “good” looks like in your industry
- Innovative practices that you might adapt to your organization
Process Automation and Innovation
Process automation is increasingly becoming a key driver of process improvement.
Process automation can involve
- Implementing workflow management systems
- Using robotic process automation (RPA) for repetitive tasks
- Leveraging artificial intelligence
Innovation in process improvement goes beyond automation. It involves continuously looking for new and better ways to do things.
Implementing Business Process Improvement
From identifying opportunities to managing change, this is a roadmap for turning improvement plans into reality.
Identifying Improvement Opportunities and Bottlenecks
The first step in any BPI initiative is identifying where improvements can be made.
This often involves a combination of data analysis, process observation, and stakeholder input.
- Processes with high error rates or quality issues
- Processes with long cycle times or frequent delays
- Activities that consume a disproportionate amount of resources
- Areas with frequent customer complaints
- Processes that haven’t been reviewed or updated in a long time
Bottlenecks are points in a process where work gets held up, slowing down the entire process.
Identifying and addressing these bottlenecks can often lead to significant improvements in overall process performance.
Developing an Improvement Strategy with Business Process Improvement
Once improvement opportunities have been identified, the next step is developing a comprehensive improvement strategy.
- Align with organizational goals and priorities
- Define clear, measurable objectives
- Identify key stakeholders and their roles
- Outline the methodologies and tools to be used
- Set realistic timelines and resource requirements
- Include a plan for measuring and sustaining improvements
It’s crucial to get buy-in from leadership and key stakeholders at this stage.
Change Management and Employee Engagement
Successful Business Process Improvement often requires significant changes in how people work, which can be met with resistance. Effective change management is therefore crucial.
This involves
- Clearly communicating the reasons for change
- Involving employees in the improvement process
- Providing necessary training and support
- Addressing concerns and resistance proactively
- Celebrating quick wins to build momentum
Employee engagement is particularly important in BPI. In my experience leading workshops for managers and business analysts.
Data-driven decision making with Business Process Improvement
One of the core principles of Business Process Improvement is making decisions based on data rather than intuition or assumptions.
This involves
- Collecting relevant data on process performance
- Using statistical tools to analyze the data
- Drawing evidence-based conclusions
- Using data to validate improvement ideas
It not only helps identify the root causes of problems but also provides a basis for measuring the impact of improvements.
Measuring and monitoring progress
Once improvements are implemented, it’s crucial to measure and monitor their impact.
This involves
- Tracking relevant KPIs
- Comparing performance to baseline measurements
- Conducting regular reviews to ensure improvements are sustained
- Making adjustments as needed based on ongoing data
Achieving Operational Excellence through Business Process Improvement
Business Process Improvement (BPI) can propel your organization towards operational excellence. with these strategies for enhancing productivity, reducing costs, and fostering a culture of continuous improvement.
Enhancing Productivity and Efficiency
One of the primary goals of BPI is to enhance productivity and efficiency.
This often involves
- Streamlining workflows to eliminate unnecessary steps
- Automating repetitive tasks
- Improving resource allocation
- Enhancing communication and collaboration
Driving Cost Reduction and Resource Optimization with Business Process Improvement
Cost reduction is often a key driver of Business Process Improvement (BPI) initiatives.
This can be achieved through
- Eliminating waste in processes
- Reducing errors and rework
- Optimizing inventory levels
- Improving asset utilization
However, it’s important to approach cost reduction strategically.
Improving quality management and customer satisfaction
Quality improvement is at the heart of methodologies like Six Sigma and TQM. Improved quality leads to:
- Reduced defects and errors
- Increased customer satisfaction
- Lower costs due to reduced waste and rework
- Enhanced brand reputation
Fostering a Culture of Continuous Improvement
Perhaps the most important outcome of BPI is fostering a culture of continuous improvement. This involves:
- Encouraging all employees to look for improvement opportunities
- Providing mechanisms for employees to suggest and implement improvements
- Recognizing and rewarding improvement efforts
- Making continuous improvement a part of everyday work, not just special projects
Business Process Improvement Across Industries
Business Process Improvement (BPI) principles adapt to different sectors, from manufacturing to healthcare.
Manufacturing and Lean principles
The manufacturing sector was where many Business Process Improvement (BPI) methodologies, particularly Lean, originated.
- Reduce production lead times
- Minimize inventory
- Improve product quality
- Enhance flexibility and responsiveness to customer demands
While these principles were developed in manufacturing, they can be adapted to other industries as well.
Service industries and process standardization
In service industries, BPI often focuses on standardizing processes to ensure consistent service delivery. This might involve:
- Creating standard operating procedures
- Implementing customer relationship management systems
- Standardizing customer interaction scripts
- Using metrics to track and improve service quality
Healthcare and patient-centric improvements with Business Process Improvement
In healthcare, BPI often focuses on improving patient outcomes and experiences. This might involve:
- Reducing wait times
- Improving care coordination
- Enhancing patient safety
- Optimizing resource utilization
Financial services and regulatory compliance
In financial services, Business Process Improvement (BPI) often needs to balance efficiency improvements with regulatory compliance.
This involves
- Automating compliance checks
- Streamlining reporting processes
- Improving risk management procedures
- Enhancing data security and privacy
Future Trends in Business Process Improvement (BPI)
Digital transformation is reshaping Business Process Improvement (BPI).
This involves
- Leveraging cloud computing for process management
- Using Internet of Things (IoT) devices for real-time process monitoring
- Implementing advanced analytics for process optimization
These digital technologies can enable new levels of process efficiency and innovation.
I’ve found that this approach can be particularly effective in fast-changing business environments.
While still in early stages, I believe these technologies will play an increasingly important role in BPI in the coming years.
Finally, there’s a growing focus on making process improvements sustainable, both in terms of maintaining improvements over time and in terms of environmental sustainability.
This involves
- Designing processes with long-term sustainability in mind
- Considering environmental impact in process improvements
- Aligning process improvement with broader business transformation initiatives
This holistic approach to Business Process Improvement (BPI) is crucial for organizations looking to achieve lasting success in today’s complex business environment.
SixSigma.us offers both Live Virtual classes as well as Online Self-Paced training. Most option includes access to the same great Master Black Belt instructors that teach our World Class in-person sessions. Sign-up today!
Virtual Classroom Training Programs Self-Paced Online Training Programs