The Definitive Guide to Achieving and Sustaining Process Stability
Ensuring processes are working smoothly is so important for any company that wants satisfied customers and to run well. Understanding and keeping processes steady over time is key to process stability.
Where customer satisfaction and operational efficiency are paramount, understanding and maintaining process stability is crucial for success.
The intricacies of process stability, exploring its definition, significance, and the techniques used to identify, monitor, and improve it.
My expertise in these areas gives me solid insights and solutions to help you establish and preserve process stability.
It’s fundamental to success, especially when quality and performance are paramount. I’ll provide useful perspectives and practical strategies so you can achieve it and maintain it long term.
Key Highlights
- Understand the fundamental concepts of process stability and its relation to common cause and special cause variations.
- Explore the importance of process stability, including its benefits.
- Learn how to identify process stability using powerful tools.
- Discover techniques for improving process stability by reducing common cause variations, eliminating non-value-added steps, and implementing effective root cause analysis.
- Gain insights into industry-specific examples of process stability in manufacturing and service industries.
- See best practices for continuous monitoring, improvement, employee training, and fostering a culture of statistical thinking and process ownership.
- Understand the role of Six Sigma methodologies, such as DMAIC (Define, Measure, Analyze, Improve, Control), and Kaizen.
What is Process Stability?
Any successful manufacturing or service operation lies in the concept of process stability.
It represents the capability of a process to perform consistently and predictably over time, producing outputs that meet specified requirements.
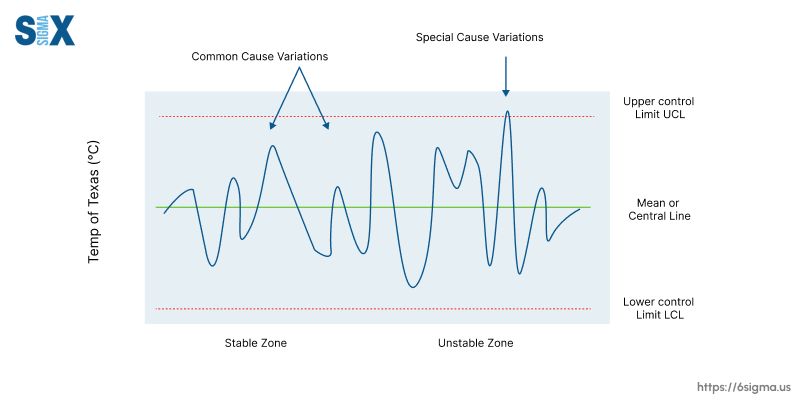
Understanding Process Stability
Process stability refers to the state where a process exhibits only common cause variations, which are inherent and expected fluctuations within the system.
These variations are typically small and occur randomly, resulting in a consistent and predictable output distribution.
When a process is stable, it operates within defined control limits, and its performance remains reliable and consistent over time.
Common Cause Variations vs. Special Cause Variations
To fully grasp the concept of process stability, it is essential to understand the distinction between common cause variations and special cause variations.
Common cause variations are inherent to the process and stem from various factors such as minor fluctuations in raw materials, operator differences, or environmental conditions.
These variations are expected and can only be eliminated with significant process improvements or redesign.
In contrast, special cause variations are unexpected and often result from specific, identifiable events or circumstances that disrupt the normal process behavior.
These variations can be caused by equipment failures, operator errors, or changes in process conditions.
Special cause variations lead to unpredictable and inconsistent process performance, resulting in outputs outside the established control limits.
Statistical Process Control (SPC)
Statistical Process Control (SPC) is a powerful methodology that enables the detection and differentiation of common cause and special cause variations.
By leveraging statistical techniques and control charts, SPC provides a robust framework for monitoring and analyzing process performance over time.
Control Charts
Control charts are essential tools in SPC that visually depict the process performance against statistically derived control limits.
These limits, typically represented as the Upper Control Limit (UCL) and Lower Control Limit (LCL), are calculated based on the process’s historical data and define the acceptable range of common cause variations.
When data points fall outside these control limits, it indicates the presence of special cause variations, prompting further investigation and corrective actions to address the root cause and restore process stability.
Importance of Process Stability
Achieving and maintaining process stability is a critical objective for organizations across industries.
A stable process ensures consistent output quality but also unlocks numerous operational benefits that directly impact customer satisfaction, cost efficiency, and overall competitiveness.
Benefits of a Stable Process
Higher Yields
One of the most significant advantages of a stable process is the ability to consistently produce outputs that meet specifications, resulting in higher yields and reduced waste.
By minimizing special cause variations, organizations can optimize resource utilization, increase throughput, and achieve greater operational efficiency.
Ability to Catch and Fix Variations
When a process is stable, any deviations from the expected performance can be easily detected and addressed through established control mechanisms.
This early identification of variations allows organizations to take corrective actions promptly, preventing further deviations and minimizing the impact on output quality and customer satisfaction.
Better Efficiency
Stable processes operate smoothly and predictably, reducing the need for constant adjustments, rework, or unplanned downtime.
This improved efficiency translates into cost savings, increased productivity, and enhanced resource utilization, ultimately driving profitability and competitive advantage.
Consequences of an Unstable Process
Reduced Customer Satisfaction
An unstable process can lead to inconsistent output quality, resulting in customer dissatisfaction and potentially damaging an organization’s reputation.
Customers expect reliable and consistent products or services, and deviations from these expectations can erode trust and loyalty, impacting long-term business success.
Increased Costs
Unstable processes are often accompanied by higher costs due to excessive waste, rework, and inefficient resource utilization.
Special cause variations can disrupt production schedules, lead to unplanned downtime, and require additional inspection or quality control measures, all of which contribute to increased operational costs.
Unpredictable Process Performance
When a process exhibits special cause variations, its performance becomes unpredictable, making it challenging to plan and allocate resources effectively.
This lack of predictability can lead to capacity constraints, missed delivery deadlines, and an overall inability to meet customer demand, ultimately impacting revenue and growth opportunities.
Identifying Process Stability
Identifying whether a process is stable or unstable is a crucial step in the pursuit of operational excellence.
By employing powerful statistical tools and techniques, organizations can accurately assess process behavior, detect deviations, and take appropriate actions to maintain or restore stability.
Run Charts and Scatter Plots
Run charts and scatter plots are valuable tools for visualizing process performance over time.
By plotting key process output variables or quality characteristics, these graphical representations provide insight into the process’s stability or presence of special cause variations.
Run charts display the chronological sequence of data points, enabling the identification of trends, shifts, or patterns that may indicate process instability.
Scatter plots, on the other hand, illustrate the relationship between two variables, helping to identify potential correlations or outliers that could signal disturbances in the process.
Control Chart Analysis
Stable Zones and Unstable Zones
Control charts are among the most widely used and effective tools for assessing process stability. These charts plot process data against statistically derived control limits, allowing for the identification of stable zones and unstable zones.
Stable zones are characterized by data points falling within the control limits, indicating that the process is operating under common cause variations.
Unstable zones, on the other hand, are marked by data points falling outside the control limits, signaling the presence of special cause variations that require further investigation and corrective action.
Special Cause Identification
Control charts not only detect the presence of special cause variations but also provide valuable insights into their potential root causes.
By analyzing the patterns and trends exhibited by the data points, experienced practitioners can identify specific signals or patterns that may indicate the nature of the special cause, such as shifts, trends, cycles, or mixtures of these patterns.
This knowledge empowers organizations to undertake targeted root cause analysis and implement effective corrective and preventive actions, ensuring a swift return to a stable process state.
Improving Process Stability
While achieving process stability is a critical objective, sustaining it over time requires continuous effort and a structured approach.
In my experience working with various organizations, I have found that improving process stability involves a two-pronged strategy: reducing common cause variations and effectively managing special cause variations.
Reducing Common Cause Variations
Common cause variations, although inherent to the process, can be minimized through systematic analysis and implementation of process Improvements.
By reducing these variations, organizations can enhance process stability and achieve more consistent outputs.
Eliminating Non-Value-Added Steps
One effective technique for reducing common cause variations is to eliminate non-value-added steps from the process.
These steps do not contribute directly to the final product or service and often introduce unnecessary complexity and variability.
By streamlining the process and removing redundant or unnecessary activities, organizations can minimize potential sources of variation and improve overall stability.
Reducing Waste
Waste, in various forms such as overproduction, excessive inventory, or inefficient transportation, can contribute to common cause variations and hinder process stability.
Implementing lean principles and techniques, such as value stream mapping and continuous improvement initiatives, can help identify and eliminate waste from the process.
By reducing waste, organizations can simplify operations, enhance efficiency, and promote greater consistency in process performance.
Managing Special Cause Variations
While reducing common cause variations is essential, effectively managing special cause variations is equally crucial for achieving and maintaining process stability.
These variations often stem from unexpected events or circumstances that disrupt the normal process behavior, and they require prompt identification and corrective action.
Root Cause Analysis
When a special cause variation is detected, conducting a thorough root cause analysis is imperative.
This analysis involves systematically investigating the underlying factors that contributed to the variation, rather than addressing only the surface-level symptoms.
By identifying the true root cause(s), organizations can implement targeted and effective solutions that prevent the recurrence of similar issues and restore process stability.
Corrective and Preventive Actions
Once the root cause(s) of a special cause variation has been identified, it is essential to implement corrective actions to address the immediate issue and prevent its recurrence.
Additionally, preventive actions should be taken to proactively mitigate the risk of similar variations arising in the future.
These actions may involve process improvements, equipment maintenance or upgrades, operator training, or the implementation of control mechanisms to monitor and respond to potential deviations promptly.
Process Stability in Practice
The importance of process stability transcends industries and sectors. Whether in manufacturing or service environments, achieving and maintaining stable processes is paramount for delivering consistent quality, meeting customer expectations, and driving operational excellence.
Manufacturing Process Stability
In the manufacturing realm, process stability is critical for ensuring consistent product quality, minimizing defects, and optimizing production yields.
For example, in the automotive industry, a stable manufacturing process is essential for producing vehicles that meet stringent safety and performance standards. Even minor variations in processes such as welding, painting, or assembly can lead to significant quality issues and potential recalls.
Similarly, in the pharmaceutical industry, process stability is a regulatory requirement for ensuring the consistent potency, purity, and safety of drug products.
Deviations from established control limits can result in batch failures, regulatory non-compliance, and potential health risks for patients.
Service Industry Process Stability
Process stability is equally vital in the service industry, where consistency and reliability are key drivers of customer experience and satisfaction.
In sectors such as healthcare, finance, or hospitality, stable processes are essential for delivering consistent service quality and meeting customer expectations.
For instance, in the healthcare industry, stable processes ensure that patients receive timely and accurate diagnoses, treatments, and follow-up care.
Variations in processes such as patient intake, laboratory testing, or medication administration can have severe consequences and compromise patient safety.
In the logistics and transportation sectors, process stability is crucial for maintaining delivery times and ensuring efficient supply chain operations. Unstable processes can lead to delays, lost or damaged goods, and ultimately, dissatisfied customers and financial losses.
Best Practices for Process Stability
Achieving and sustaining process stability requires a comprehensive approach that encompasses continuous monitoring, improvement, and a culture that fosters employee engagement and statistical thinking.
Continuous Monitoring and Improvement
Process stability is not a one-time achievement; it requires ongoing vigilance and a commitment to continuous improvement.
Regularly monitoring process performance through tools like control charts and statistical process control techniques is essential to detect deviations and take corrective actions promptly.
Six Sigma DMAIC
The Six Sigma DMAIC (Define, Measure, Analyze, Improve, Control) methodology provides a structured approach to improving process stability.
By systematically defining the problem, measuring key process characteristics, analyzing root causes, implementing improvements, and establishing control mechanisms, organizations can effectively address both common and special cause variations, ensuring sustained process stability.
Kaizen
Complementing the Six Sigma approach, the Kaizen philosophy of continuous improvement empowers employees at all levels to identify and eliminate waste, streamline processes, and drive incremental improvements.
By fostering a culture of continuous learning and improvement, organizations can proactively address potential sources of variation and maintain process stability over the long term.
Employee Training and Engagement
Achieving and maintaining process stability requires a workforce that understands and embraces the principles of statistical thinking.
Providing comprehensive training in statistical methods, process monitoring techniques, and problem-solving approaches is crucial for equipping employees with the necessary skills and mindset.
Furthermore, nurturing a sense of process ownership among employees is essential.
When employees feel accountable for the processes they operate, they are more likely to actively monitor and take ownership of process stability initiatives, contributing to sustained operational excellence.
Parting Notes
Keeping processes steady is so important for any company that wants to do consistent, high-quality work and be efficient.
Following the helpful tips in this guide can start you on a path of constant betterment, where process stability is built deep into how your business operates as a real advantage over competitors.
It’s worth remembering, maintaining process stability takes dedication to always look for issues, big and small, and fix them.
Statistical analysis, team involvement and tried-and-true techniques like Six Sigma and Kaizen can unlock your processes’ full ability. That way you deliver top value to customers.
By using data to understand processes inside and out, and involving everyone to keep improving, companies can establish process stability and the smooth operations necessary to succeed long term in today’s competitive marketplace.
SixSigma.us offers both Live Virtual classes as well as Online Self-Paced training. Most option includes access to the same great Master Black Belt instructors that teach our World Class in-person sessions. Sign-up today!
Virtual Classroom Training Programs Self-Paced Online Training Programs