Standardized Work in Lean Manufacturing. Everything to Know
Standardized work is a foundational element of lean manufacturing and continuous improvement. Six Sigma certification offers advanced tools to strengthen process optimization alongside these practices.
It refers to the process of documenting the best and most efficient way to perform a task or a series of tasks, and then training employees to follow those standardized procedures.
Ready to transform your organization’s operational efficiency?
Unlock the secrets of lean thinking and drive continuous improvement with Lean Fundamentals.
By establishing standardized work, organizations can ensure consistent, efficient, and high-quality processes, ultimately leading to improved safety, increased productivity, and reduced waste.
The ability to consistently deliver quality products and services is paramount. Standardized work plays a crucial role in achieving this goal by providing a clear and documented framework for how work should be performed.
Key Highlights
- Standardized work is a fundamental lean manufacturing concept that ensures consistent, efficient, and high-quality processes.
- It involves documenting the best way to perform a task or process, creating standard procedures, and training employees to follow them.
- It helps improve safety, increase efficiency, enhance quality, reduce waste, improve communication, and increase visibility and transparency.
- Implementing standardized work involves identifying processes for standardization, developing documentation, training employees, and continuously monitoring and improving the processes.
- It is a crucial foundation for lean manufacturing, as it enables the effective implementation of other lean tools and techniques.
What is Standardized Work?
Standardized work, also known as standardized operating procedures (SOPs), refers to the documented, step-by-step process for performing a specific task or operation.
It establishes the one best way to complete a job, ensuring consistency, quality, and efficiency across an organization.
It defines the sequence of steps, cycle times, inventory levels, and other key metrics required to complete a task effectively.
Importance
Standardized work is a foundational element of lean manufacturing and continuous improvement initiatives. It provides a baseline for how a process should be executed, allowing organizations to identify and eliminate waste, reduce variation, and continuously optimize workflows.
By documenting the standard method, companies can train new employees, onboard more quickly, and ensure all workers follow the same proven process.
It also enables data collection, performance tracking, and root cause analysis when issues arise.
Characteristics of Standardized Work
The key characteristics of standardized work include:
- Documented procedures: Captured in written instructions, visual aids, checklists, and other documentation to ensure consistency.
- Defined sequence of steps: The work is broken down into a specific, repeatable sequence of tasks to be performed in a consistent order.
- Specified cycle time: The expected time to complete each step or the entire process is clearly defined.
- Established work-in-process (WIP) levels: The ideal inventory levels required at each stage are specified to prevent overproduction or delays.
- Identification of key quality touchpoints: Critical quality control checks are built into the process to ensure conformance to standards.
- Continuous improvement mindset: It is not static, but is regularly reviewed and updated to drive ongoing optimization.
With this, organizations can reduce variability, improve quality, and build a culture of continuous improvement – all of which are essential for lean manufacturing success.
Elements of Standardized Work
Standardized work is a critical component of any well-functioning operation, and it encompasses several key elements that work together to create a cohesive and efficient system. Let’s take a closer look at the core elements of standardized work:
Standardized Work Process
At its heart is the standardized work process. This involves defining and documenting the precise steps, sequences, and timing required to complete a specific task or operation.
This process ensures that work is performed in a consistent, repeatable manner, reducing variability and improving overall efficiency.
Documentation
Closely tied to the standardized work process is the documentation that supports it. This includes things like standard operating procedures (SOPs), work instructions, process maps, and visual aids.
These documents provide a clear, detailed record of how work should be carried out, ensuring that everyone involved understands and follows the same procedures.
Standardized Work Procedures
These procedures outline the specific steps and actions required to complete a task. These procedures are typically documented in SOPs or work instructions, and they cover everything from equipment setup and operation to quality checks and problem-solving.
By standardizing these procedures, organizations can minimize errors, improve safety, and ensure consistent outcomes.
Standardized Work Instructions
These instructions provide even more granular, step-by-step guidance for performing a task.
These instructions can include detailed diagrams, photographs, or videos to visually demonstrate the correct way to carry out the work.
These instructions help to eliminate ambiguity and ensure that employees have a clear understanding of how to perform their tasks.
Templates
To further support the standardization of work, many organizations use defined templates for various documents and forms.
These templates can include things like checklists, inspection forms, data collection sheets, and more.
By using consistent templates, organizations can ensure that information is captured and organized in a standardized way, making it easier to analyze and compare data over time.
Standardized Work Checklists
Checklists are a powerful tool for ensuring that all necessary steps are followed.
These checklists can be used to guide employees through complex procedures, verify that critical tasks have been completed, and provide a visual record of the work that was performed.
They help to reduce the risk of errors or omissions and promote consistency across the organization.
By implementing these core elements, organizations can achieve greater efficiency, improved quality, and enhanced safety in their operations.
The consistent, documented processes and procedures that it provides serve as a foundation for continuous improvement and sustainable success.
Benefits of Implementing Standardized Work
Implementing standardized work in the workplace can provide a wide range of benefits that improve overall business operations and performance. Some of the key advantages of standardized work include:
Improved Safety
It helps create a safer work environment by establishing clear, consistent procedures that minimize the risk of errors or accidents.
When processes are well-documented and followed consistently, it reduces the chances of unsafe shortcuts or oversights that could lead to injuries or incidents.
It also enables better training and onboarding of new employees to ensure they understand proper safety protocols.
Increased Efficiency
By defining the optimal sequence of steps and elements for a given process, standardized work helps eliminate waste and redundancy.
Employees can complete tasks more quickly and with less effort, boosting overall productivity and throughput. It also facilitates the identification of improvement opportunities to streamline processes even further.
Enhanced Quality
It provides a framework for consistent, high-quality output. When work is performed the same way every time, according to documented procedures, it reduces variability and defects.
This helps ensure products or services meet the required specifications and customer expectations. Standardized work also enables better quality control monitoring and continuous improvement.
Reduced Waste
Eliminating unnecessary motion, transportation, inventory, and other forms of waste is a key benefit.
By optimizing process flows and eliminating non-value-added steps, organizations can significantly reduce waste and improve resource utilization a core principle taught in lean fundamentals. This leads to cost savings and a leaner, more efficient operation.
Improved Communication
Standardized work documentation, such as work instructions and visual controls, provides a common language and understanding across the organization.
This facilitates clearer communication, reduces ambiguity, and makes it easier to train new employees or transfer knowledge. It also enhances transparency, allowing everyone to see and understand the correct way to perform a task.
Increased Visibility and Transparency
The detailed documentation and visual management aspects create greater visibility into operational processes.
This allows managers and team members to easily observe, monitor, and measure performance. It also increases transparency, making it easier to identify problems, bottlenecks, or opportunities for improvement.
By its implementation, organizations can achieve significant benefits across safety, efficiency, quality, waste reduction, communication, and overall operational visibility.
This creates a more stable, predictable, and continuously improving work environment.
Applying Standardized Work in the Workplace
Identifying Processes for Standardization
The first step in applying standardized work in the workplace is to identify the processes that are suitable for standardization. Look for repetitive, high-volume tasks or workflows that are prone to variability and errors. These are prime candidates for standardization.
Analyze the current state of these processes, documenting the steps, identifying pain points, and understanding the root causes of any issues – a practice central to Six Sigma methodologies. This will help you determine the areas that would benefit the most from a standardized approach.
Developing Standardized Work Documentation
Once the processes have been identified, the next step is to develop the necessary documentation. This includes creating standard operating procedures (SOPs), work instructions, checklists, templates, and other visual aids.
The documentation should provide clear, step-by-step guidance on how the work is to be performed, including the sequence of steps, the tools and materials required, and any quality or safety checks.
It’s important to involve the frontline workers in the development of this documentation to ensure it accurately reflects the actual work being done and is easy to understand and follow.
Implementing Standardized Work Practices
With the documentation in place, the next step is to implement these practices across the organization. This involves training employees on the new procedures, providing the necessary resources and support, and ensuring adherence to the standards.
Standardized work should be embedded into the daily routines and workflows of the organization, becoming the expected way of doing things.
Managers and supervisors play a crucial role in reinforcing its importance and modeling the desired behaviors.
Monitoring and Continuously Improving
Standardized work is not a one-time implementation; it requires ongoing monitoring and continuous improvement. Establish a system to regularly review these practices, gather feedback from employees, and identify opportunities for improvement.
This may involve conducting audits, analyzing performance metrics, and implementing corrective actions. Encourage a culture of continuous improvement, where employees are empowered to suggest and implement changes to these processes.
By continuously refining and optimization, organizations can ensure that it remains effective and relevant in the face of changing business requirements and evolving best practices.
Want to master process optimization and drive organizational excellence?
Learn the powerful methodologies that turn complex challenges into strategic opportunities with Lean Six Sigma Green Belt Certification.
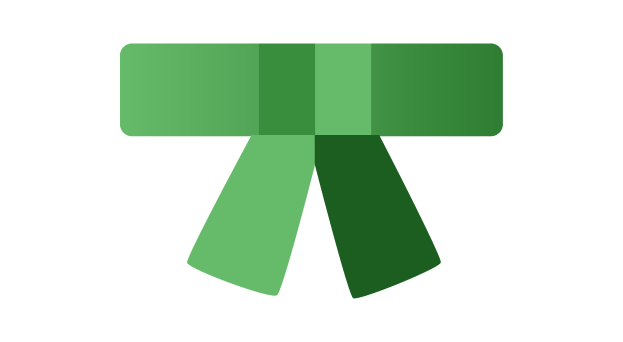
Standardized Work and Lean Manufacturing
Standardized work serves as a core element of lean manufacturing, frequently combined with Six Sigma methodologies for holistic process improvement. Also, Six Sigma certification equips individuals with expertise to integrate these approaches effectively.
It establishes consistent, repeatable processes that eliminate variability and waste, allowing for continuous improvement efforts to take hold.
In a lean environment, it ensures that every task is performed the same way each time, using the most efficient methods and materials.
This consistency allows for the identification of abnormalities or problems, which can then be addressed through kaizen (continuous improvement) activities.
Without standardized work, it becomes challenging to distinguish between normal and abnormal conditions, making it difficult to identify opportunities for improvement.
Tired of fighting fires instead of solving real problems?
Discover the techniques to uncover and eliminate root causes systematically.
Integrating with Lean Tools and Techniques
Standardized work seamlessly integrates with other lean manufacturing tools and techniques, such as 5S, poka-yoke (mistake-proofing), total productive maintenance (TPM), and just-in-time (JIT) production.
For example, 5S (sort, set in order, shine, standardize, sustain) helps maintain the organization and cleanliness of the work environment.
Poka-yoke features are often incorporated into these instructions to prevent errors and ensure quality. TPM helps maintain the equipment and machinery used in these processes, ensuring their reliable operation.
JIT production relies on the predictability and stability provided by standardized work to synchronize the flow of materials and information.
By aligning standardized work with these lean tools, organizations can achieve greater synergy and maximize the benefits of their lean transformation efforts.
Continuous Improvement through Standardized Work
Standardized work is not a static concept; it is a dynamic process that evolves through continuous improvement. As organizations implement it, they should regularly review and refine the processes to identify opportunities for further optimization.
Its foundation, standardized work instruction (SWI), serves as a starting point for continuous improvement.
As team members follow the SWI and encounter challenges or inefficiencies, they can suggest improvements, which can then be tested, implemented, and incorporated into the updated SWI.
This cycle of Plan-Do-Check-Act (PDCA) allows for the gradual refinement of standardized work, leading to increased efficiency, quality, and safety.
Furthermore, it provides the necessary stability and consistency to support other continuous improvement methodologies, such as kaizen.
By eliminating variability and establishing a baseline, standardized work enables teams to focus on identifying and addressing the root causes of problems, rather than constantly firefighting issues caused by inconsistent processes.
Standardized work is a critical foundation for lean manufacturing, as it provides the stability and consistency necessary for the successful implementation of other lean tools and techniques.
By integrating standardized work with lean practices and continuously improving processes, organizations can drive sustainable and impactful improvements in their operations.
SixSigma.us offers both Live Virtual classes as well as Online Self-Paced training. Most option includes access to the same great Master Black Belt instructors that teach our World Class in-person sessions. Sign-up today!
Virtual Classroom Training Programs Self-Paced Online Training Programs