Reduce Changeover Time: Strategies for Manufacturing Efficiency
To reduce changeover time is not just a goal — it’s a necessity for staying ahead.
Changeover time, defined as the period between the last good piece of one production run and the first good piece of the next, is a key factor in overall equipment effectiveness (OEE).
Changeover time can transform production processes, leading to significant improvements in productivity and cost-efficiency.
Key Highlights
- Understanding changeover time
- Measuring and analyzing changeover processes
- Implementing SMED methodology
- Best practices to Reduce Changeover Time
- Lean manufacturing principles
- Continuous improvement strategies
- Long-term benefits and future trends
What is Changeover Time?
Changeover time is the period between the last good part produced in one production run and the first good part produced in the subsequent run.
It’s crucial to note that this includes not just the physical changeover of equipment, but also any quality checks and adjustments needed to ensure the new production meets specifications.
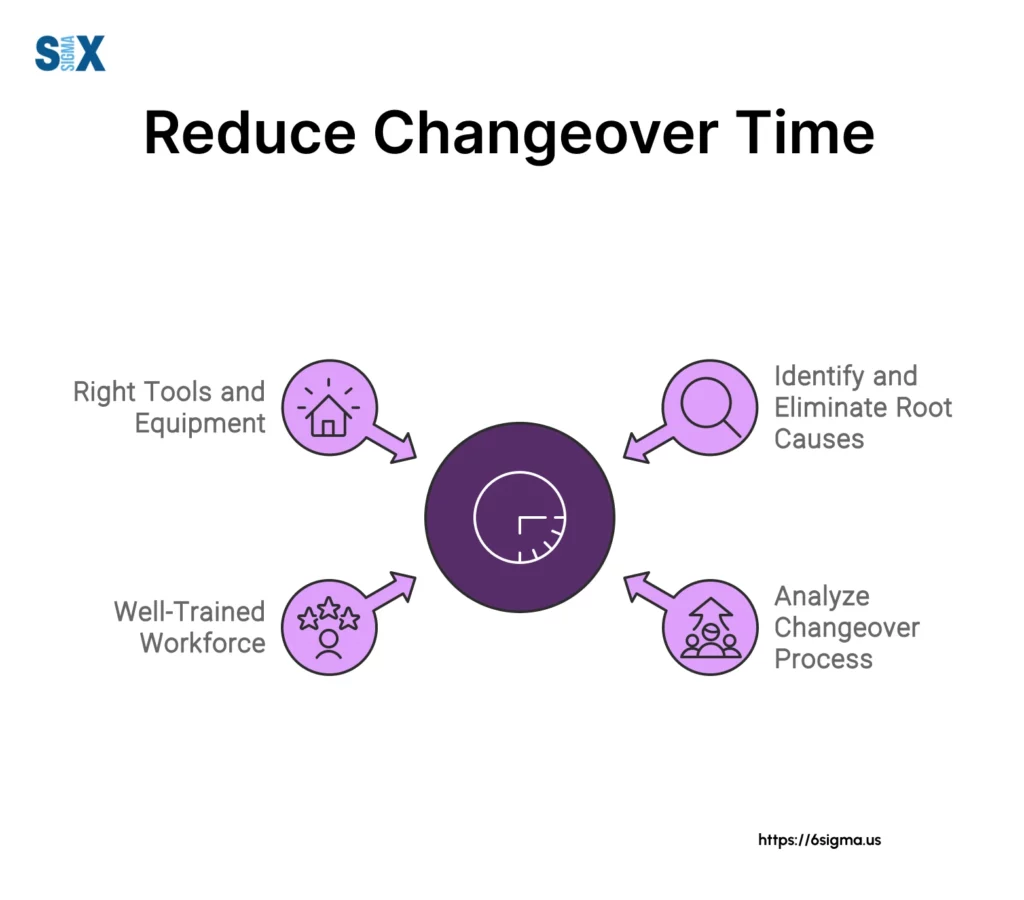
Importance of Reducing Changeover Time
It’s not just about saving a few minutes here and there; it’s about fundamentally improving manufacturing efficiency.
A reduce changeover time leads to increased production flexibility, lower inventory levels, and improved overall equipment effectiveness (OEE).
The ability to quickly switch between products can be a significant competitive advantage.
Changeover time vs. setup time
A common misconception I often encounter is the interchangeable use of changeover time and setup time.
While related, these are distinct concepts. Setup time is a component of changeover time, specifically referring to the time spent preparing a machine or production line for a new run.
Changeover time, on the other hand, encompasses the entire process, including cleanup, setup, and achieving the first good part of the new run.
Understanding this distinction is crucial for effective process optimization.
Measuring and Analyzing Changeover Time
Accurate measurement is the foundation of any improvement initiative.
The most effective method for measuring changeover time involves a combination of direct observation and data collection.
This can include time studies, video analysis, and the use of digital timers.
It’s important to break down the changeover process into discrete steps, allowing for a detailed analysis of each component.
Using Machine Data Analytics
In recent years, there has been a shift towards the use of advanced machine data analytics in changeover time measurement.
Tools that can automatically track machine states and production data provide real-time insights into changeover performance.
This level of granularity allows for more precise identification of improvement opportunities and can help in setting realistic targets for reduction efforts.
Identifying Bottlenecks and Inefficiencies
Once you have accurate measurements, the next step is to identify bottlenecks and inefficiencies in the changeover process.
Often, the most significant delays are not where you’d expect them to be, which is why a data-driven approach is so crucial.
Implementing SMED (Single-Minute Exchange of Die)
SMED, or Single-Minute Exchange of Die, is a lean manufacturing technique that is incredibly effective to reduce changeover time(s).
Developed by Shigeo Shingo in Japan, SMED aims to reduce changeover time(s) to less than 10 minutes.
Steps to Implement SMED
The SMED process typically involves four main steps:
- Separate internal and external activities
- Convert internal activities to external where possible
- Streamline all aspects of the changeover operation
- Document and standardize the new procedure
The key to successful SMED implementation is a systematic approach and full engagement from the shop floor team.
Internal vs External Setup Activities
A critical aspect of SMED is distinguishing between internal and external setup activities.
Internal activities are those that can only be performed when the machine is stopped, while external activities can be done while the machine is still running.
By converting as many internal activities to external as possible, we can significantly reduce downtime during changeovers.
Best Practices to Reduce Changeover Time
Best practices to reduce changeover time consists of the culmination of decades of industrial experience and innovation.
By implementing these tried-and-true methods, manufacturers can achieve dramatic improvements in their changeover efficiency.
Standardized Work Instructions and SOPs
One of the most effective ways to reduce changeover time is through the use of standardized work instructions and standard operating procedures (SOPs).
These documents should be living, regularly updated based on improvements and feedback from the shop floor.
Quick Changeover Techniques
Quick changeover techniques often involve simple yet effective modifications to equipment and processes.
This might include using quick-release fasteners, color-coding parts, or implementing poka-yoke (error-proofing) devices.
The goal is to make the changeover process as foolproof and efficient as possible.
Visual Management Strategies
Visual management is a powerful tool to reduce changeover time.
This can include shadow boards for tools, clearly marked settings on machines, and visual indicators for machine status.
Optimizing Production Processes
Optimizing production processes is about more than just speed — it’s about creating a harmonious flow.
By aligning every aspect of production, we can achieve significant reductions in changeover time and boost overall efficiency.
Lean Manufacturing Principles
Lean manufacturing principles are at the core to reduce changeover time. Techniques like 5S (Sort, Set in order, Shine, Standardize, Sustain) can create a more organized work environment, facilitating quicker changeovers. Value stream mapping can help identify and eliminate non-value-added activities in the changeover process.
Just-in-Time (JIT) Production
Just-in-Time production, a key component of lean manufacturing, can significantly impact changeover times.
By producing only what is needed when it’s needed, JIT reduces the need for large batch sizes and frequent changeovers. However, this requires highly efficient changeover processes to be effective.
Batch Size Reduction Strategies
Reducing batch sizes can lead to more frequent changeovers, but it also provides more opportunities for improvement.
Smaller batch sizes can actually lead to overall efficiency gains by reducing inventory and improving flow.
Continuous Improvement to Reduce Changeover Time
Continuous improvement is the lifeblood of efficient manufacturing. It’s not just about making changes once, but fostering a culture of ongoing optimization and adaptation.
Kaizen Events and Improvement Initiatives
Kaizen events, or rapid improvement workshops, can be highly effective to reduce changeover time.
These focused events bring together cross-functional teams to analyze and improve specific aspects of the changeover process.
Employee Training and Engagement
Effective changeover time reduction requires full engagement from the shop floor team.
Regular training sessions and clear communication of goals and progress are essential.
The most successful improvement initiatives are those where employees feel ownership of the process and are empowered to suggest and implement improvements.
Monitoring and Adjusting Changeover Processes
Continuous improvement requires ongoing monitoring and adjustment of changeover processes.
Regular audits, performance tracking, and feedback loops should be established to ensure that improvements are sustained and further opportunities are identified.
The Impact of Reduced Changeover Time
Reducing changeover time can lead to significant improvements in manufacturing efficiency.
This includes increased production capacity, reduced inventory levels, improved quality, and greater flexibility to meet customer demands.
Long-term effects
In the long term, companies that effectively reduce changeover time(s) can achieve a significant competitive advantage.
Future Trends
Looking to the future, I anticipate that advanced technologies like artificial intelligence and machine learning will play an increasingly important role to reduce changeover time.
The fundamental principles of lean manufacturing and continuous improvement will remain crucial in achieving and sustaining reduced changeover times.
SixSigma.us offers both Live Virtual classes as well as Online Self-Paced training. Most option includes access to the same great Master Black Belt instructors that teach our World Class in-person sessions. Sign-up today!
Virtual Classroom Training Programs Self-Paced Online Training Programs