What is a Plan for Every Part (PFEP)? A Guide to Achieve Efficient Inventory Management and Lean Manufacturing (2025 Guide)
Inventory management is crucial for operational efficiency. Despite ERPs in place, organizations can struggle with inventory management.
Plan for Every Part (PFEP) contains detailed information about every single part used in the manufacturing process, right from raw materials to finished goods.
Understanding Plan for Every Part (PFEP)
The Plan for Every Part (PFEP) concept is a holistic approach to inventory management. Stemms from Toyota’s lean manufacturing principles.
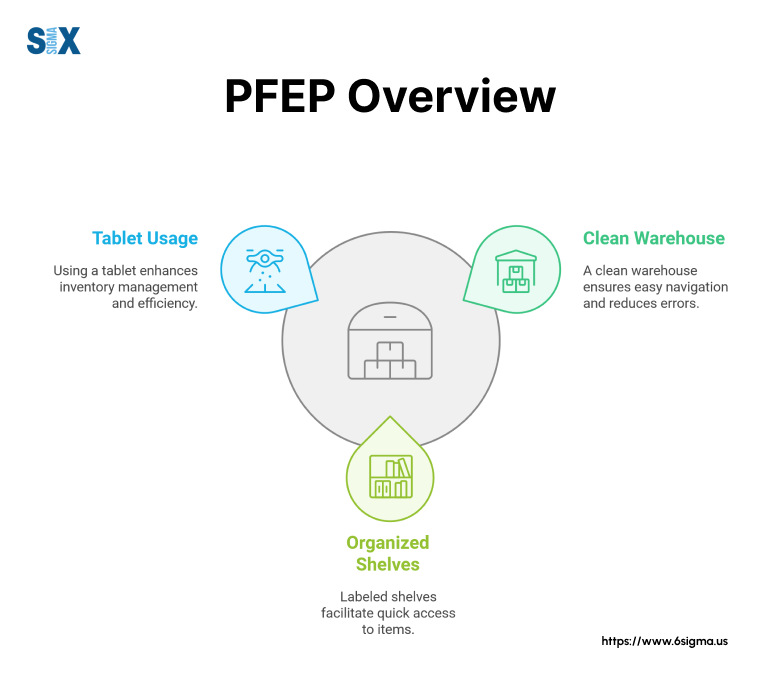
This comprehensive approach transforms chaotic material management into a precise science. The PFEP process goes beyond basic inventory tracking to encompass every aspect of a part’s lifecycle within your facility.
Fundamental components of a PFEP system include;
- Detailed part specifications
- Usage patterns
- Storage locations
- Packaging requirements
- Supplier information
- Delivery schedules
Role in Lean Manufacturing
It supports key lean principles such as just-in-time delivery, kanban systems, and waste reduction. During a project, PFEP data was used to design efficient material handling routes, resulting in a reduction in material movement time. This level of optimization simply isn’t possible with traditional inventory management systems that lack the granular detail provided by a comprehensive PFEP.
Professionals with Six Sigma certification often leverage these methodologies to enhance such initiatives, combining lean principles with data-driven problem-solving techniques.
What truly differentiates PFEP from traditional inventory management is its proactive rather than reactive approach. Instead of responding to stock-outs or excess inventory, PFEP enables organizations to anticipate and prevent these issues before they occur.
Want to Achieve Effective Inventory Management?
Our Lean Introduction course covers essential tools like Value Stream Mapping, Kaizen Events, and Pull Systems – critical components for successful PFEP implementation. Learn how to reduce cycle times and improve productivity while eliminating waste.
For a holistic approach to operational excellence, consider pairing this training with a Six Sigma certification, which equips teams with advanced problem-solving frameworks to sustain PFEP improvements.
Essential Data Elements in a Plan for Every Part (PFEP) System
The success of a PFEP implementation largely depends on the quality and comprehensiveness of its data elements. You can use a structured approach to defining these essential components that consistently deliver results.
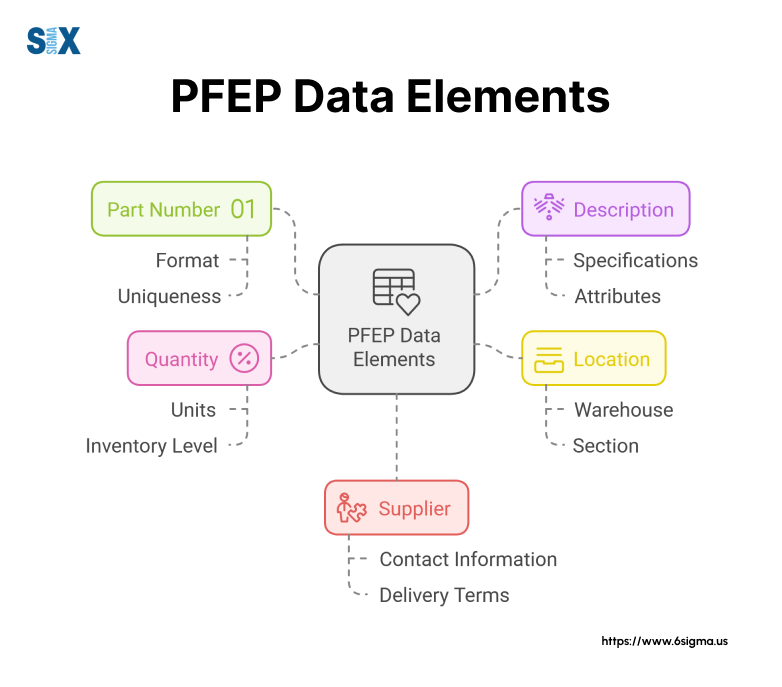
Part Information
It forms the foundation of any PFEP template. Beyond basic details like part numbers and descriptions, I recommend including precise dimensional data, weight specifications, and material composition.
Incorporating detailed part attributes helped reduce packaging waste and optimize storage space utilization. Each part should have a unique identifier that links to all related documentation, including engineering drawings and quality specifications.
Supplier Information
Supplier information is another crucial element that often gets overlooked in traditional inventory systems. Maintaining comprehensive supplier profiles ā including geographical location, lead times, minimum order quantities, and historical performance metrics ā is essential.
Data and Demand Patterns within Plan for Every Part (PFEP)
Usage data and demand patterns represent the dynamic elements of your PFEP system. Tracking both historical consumption and forecasted demand is crucial. This includes daily usage rates, seasonal variations, and production schedule dependencies.
You can use this data to optimize inventory levels, resulting in a reduction in carrying costs while maintaining good service levels.
Storage and Handling Requirements
Storage and handling requirements must be meticulously documented in your PFEP system. This includes specific storage conditions, handling equipment needed, and any special considerations for sensitive components.
Proper documentation of these requirements can reduce material damage and improve warehouse efficiency.
Lead Times and Reorder Points
Lead times and reorder points are critical elements that drive your inventory management strategy. I recommend including not just standard lead times but also variability metrics and safety stock calculations.
This approach can help reduce stockouts while simultaneously decreasing excess inventory.
Packaging Specifications within Plan for Every Part (PFEP)
Packaging specifications might seem straightforward, but they require careful attention. Your PFEP system should detail standard pack quantities, container types, and any special packaging requirements.
Optimizing packaging specifications through PFEP can lead to a reduction in material handling time and an improvement in storage space utilization.
Level of Detail
The level of detail in your PFEP system should be comprehensive enough to support decision-making at all levels of operations, yet practical enough to maintain efficiently.
Successful PFEP implementations typically include 50-75 data fields per part, though this can vary based on industry and operational complexity.
How to Implement Plan for Every Part (PFEP)?
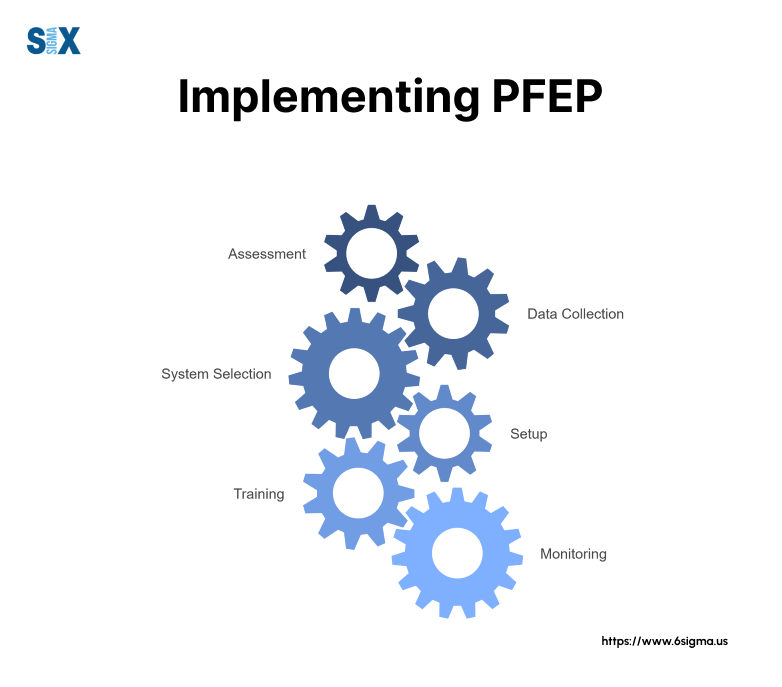
- The journey begins with a thorough assessment of current inventory management practices. Use a diagnostic framework to evaluate existing systems against lean manufacturing principles. This assessment typically reveals significant opportunities for improvement.
- Data collection and consolidation form the critical foundation of any PFEP implementation. This phase requires meticulous attention to detail. Start by mapping all data sources, including ERP systems, spreadsheets, and even tribal knowledge from experienced staff members. I recommend using a structured data collection template that ensures consistency and completeness.
- Choosing the right PFEP software or platform is crucial for long-term success. Consider several key factors: scalability, integration capabilities, user interface, and reporting functionality.
- Setting up the PFEP database requires a methodical approach. Start with a pilot area or product line to test and refine the system.
- Training staff and stakeholders is perhaps the most critical yet often overlooked aspect of PFEP implementation. Use a comprehensive training program that addresses both technical skills and change management. Foundational training, such as Six Sigma Yellow Belt certification, can equip staff with problem-solving basics to support PFEP data collection and analysis.
- Continuous monitoring and improvement close the implementation loop. Implementing a Plan for Every Part is not a one-time project but an ongoing process. Establish weekly review meetings to address system issues and identify improvement opportunities.
By following this structured approach, organizations can avoid common pitfalls and accelerate their journey to inventory management excellence.
Master the Design Aspects of Efficient Inventory Systems.
Our DFSS Green Belt course covers critical Voice of Customer deployment, design optimization, and more essential skills for implementing a successful PFEP system.
Integration of Plan for Every Part (PFEP) with Existing Systems
Successful integration with existing systems often determines the difference between mediocre and exceptional results.
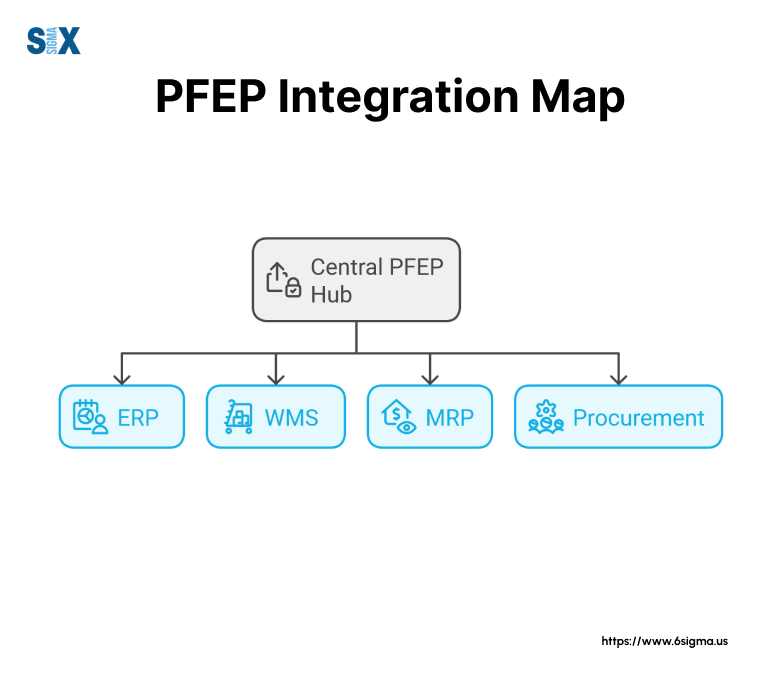
- The integration of PFEP with ERP systems requires careful planning and execution. Use an automated plan for every part that synchronizes with their existing ERP implementation. The key is to establish reliable data bridges that maintain real-time information flow while preserving data integrity across systems.
- When it comes to MRP and production planning integration, many organizations initially struggle with synchronization. Implement a middleware solution that enables PFEP systems to automatically update production schedules based on real-time inventory levels.
- Warehouse management system integration presents unique challenges, but the benefits are substantial. Use a custom interface that connects their PFEP database directly with the WMS. This automated plan for every part implementation reduces picking errors and improves warehouse efficiency.
- Procurement process alignment is perhaps the most critical integration point. Successful PFEP integration with procurement systems requires careful attention to supplier communication protocols and order-triggering mechanisms. Achieve this by creating standardized data exchange formats that allow automated purchase order generation based on PFEP parameters.
Benefits and ROI of Implementing Plan for Every Part (PFEP)
The benefits of PFEP extend far beyond simple inventory management.
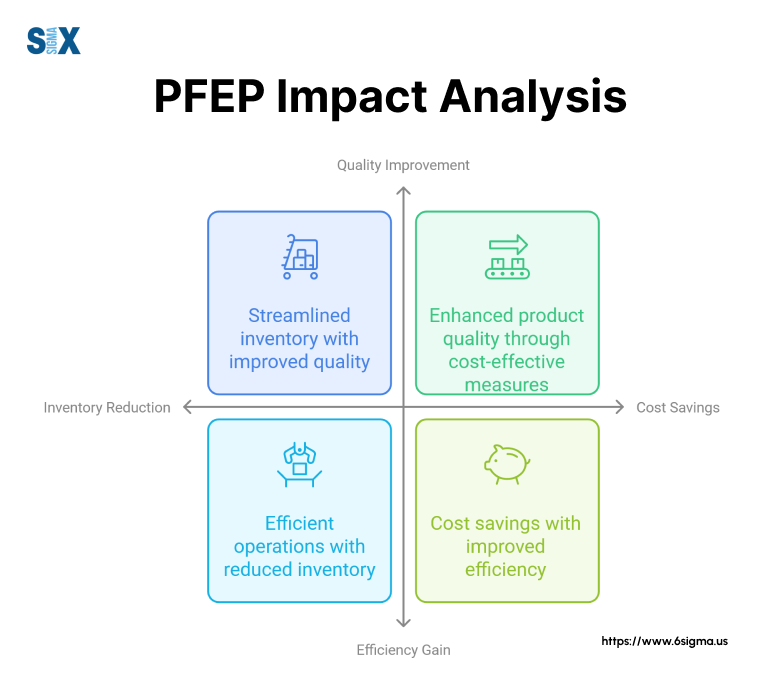
Inventory Accuracy and Control
Let’s start with inventory accuracy and control. Implementing PFEP can lead to a near-perfect inventory accuracy rate.
At a client in the automotive sector, this enhanced accuracy translated into a $2.3 million reduction in safety stock requirements while maintaining service levels.
The plan for every part benefits becomes particularly evident when you consider that most organizations struggle to maintain accuracy rates above 90% using traditional systems.
Carrying Costs and Waste with Plan for Every Part (PFEP)
Reduced carrying costs and waste represent another significant area of return. You can achieve a reduction in inventory carrying costs. This improvement came from better visibility into usage patterns and more precise ordering quantities.
Enhanced Supply Chain Visibility
Enhanced supply chain visibility has become increasingly crucial in today’s volatile market. PFEP implementation can provide real-time visibility across the supply chain, reducing emergency shipments and improving supplier delivery performance. This level of transparency enables proactive decision-making rather than reactive problem-solving.
Streamlined Procurement Process with a Plan for Every Part
Streamlined procurement processes deliver both direct and indirect cost savings. Implement a PFEP system that automates routine purchasing decisions, reduces procurement cycle times, and free-up staff for more strategic activities. The standardized data and processes inherent in PFEP typically reduce procurement-related errors.
Production Efficiency Improvements
Production efficiency improvements are particularly noteworthy. PFEP implementation can result in a reduction in production line stoppages due to parts shortages. The system’s ability to predict and prevent material shortages while optimizing inventory levels can contribute to an increase in overall equipment effectiveness (OEE).
Better Decision-Making with a Plan for Every Part
The data-driven insights provided by PFEP enable better decision-making across all operational levels. Develop metrics that quantify these improvements. For instance, tracking decision-making speed and accuracy, reducing time-to-decision for inventory-related issues, and improvement in forecast accuracy.
ROI of Plan for Every Part (PFEP)
When measuring ROI, focus on both quantitative and qualitative metrics. Typical financial returns include inventory reduction, carrying cost reduction, and productivity improvements.
However, equally important are improvements in customer satisfaction, employee engagement, and supply chain resilience. One aerospace client achieved a 310% ROI within 18 months, primarily through inventory optimization and improved operational efficiency.
Organizations typically achieve full ROI within 12-18 months, with some realizing significant benefits within the first six months of implementation.
Ready to Take Your PFEP Implementation to the Next Level?
Our Lean Master course equips you with advanced tools like Machine Kanban, SMED, and Heijunka to optimize your inventory management. Learn how to guide lean agents and decrease expenses while improving production efficiency.
Challenges and Solutions in Plan for Every Part (PFEP) Implementation
Many challenges can derail even the most promising PFEP initiatives. Letās look at some of the most common obstacles and proven solutions.
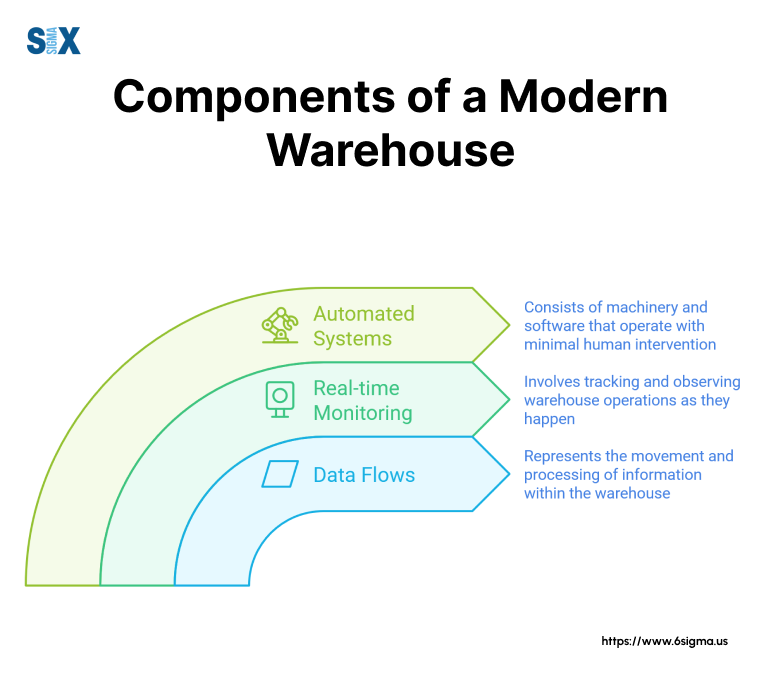
Data Accuracy and Maintenance
Data accuracy and maintenance consistently emerge as primary challenges in the PFEP process. Implement a rigorous data validation protocol and establish clear ownership for each data element.
Resistance to Change with Plan for Every Part
Resistance to change often presents a significant hurdle, particularly among experienced staff members. Use a stakeholder engagement approach that involves key personnel in the planning process and demonstrates immediate wins.
Technology Integration
Technology integration issues frequently complicate the Plan for Every Part process. Create a phased integration approach, starting with critical systems and gradually expanding connectivity.
Scalability with Plan for Every Part (PFEP)
Scalability concerns often arise as organizations grow or expand their PFEP implementation. Design your PFEP system with scalability in mind from the start. During their implementation, build modular components that allow for easy expansion, leading to successful scaling across five additional facilities without significant disruption.
Supplier Collaboration
Supplier collaboration challenges can significantly impact PFEP effectiveness. Use a supplier engagement framework that includes regular communication protocols and shared performance metrics.
Best Practices for Successful Plan for Every Part (PFEP) Management
Best practices that consistently drive successful outcomes are:
- Regular data audits and updates form the foundation of effective PFEP management. Establish a bi-weekly audit protocol that reduces data discrepancies. I recommend implementing a structured audit schedule that includes both automated verification and manual review processes.
- Cross-functional team involvement has proven invaluable in maintaining PFEP effectiveness. Create dedicated PFEP teams that include representatives from operations, procurement, engineering, and quality assurance. The key is ensuring that each team member understands their role in maintaining data integrity and system effectiveness.
- A continuous improvement mindset is essential for long-term PFEP success. Implement regular improvement cycles to achieve a reduction in process variations through systematic evaluation and enhancement of PFEP processes. This approach should include regular performance reviews and adjustment of procedures based on measured outcomes.
- Leveraging automation and AI has become increasingly important in modern PFEP best practices. Implement machine learning algorithms to improve forecast accuracy and reduce manual data entry requirements. However, I always emphasize that automation should complement, not replace, human expertise in PFEP management.
- Supplier relationship management represents a critical best practice often overlooked in PFEP implementations. Use a structured approach to supplier integration that can typically improve delivery performance.
The frequency of PFEP data audits should align with your operational tempo. I recommend daily automated checks for critical data points, weekly operational reviews, and monthly comprehensive audits. This tiered approach has consistently provided the right balance between maintenance effort and system reliability.
Key Performance Indicators for Plan for Every Part (PFEP)
Use a comprehensive framework for measuring PFEP success through specific, actionable KPIs.
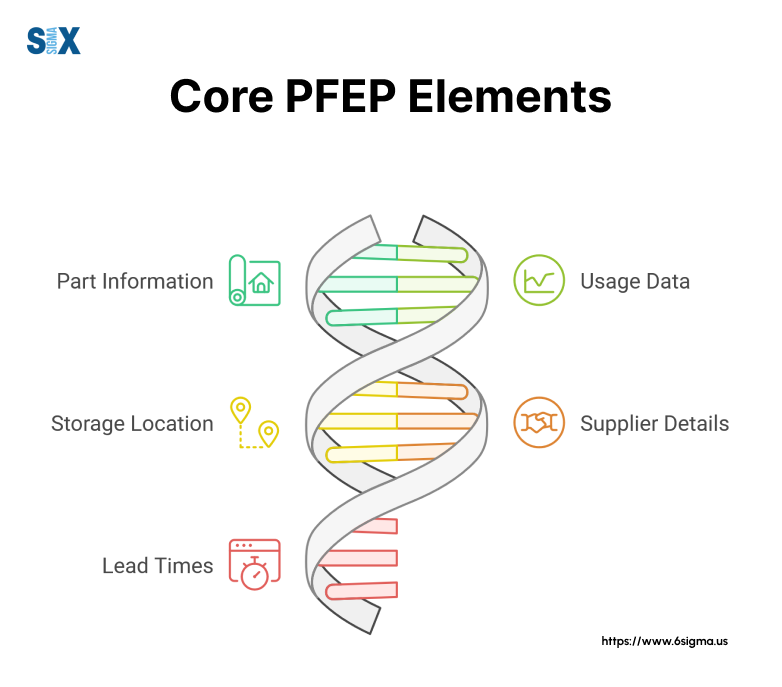
- The inventory turnover ratio stands as a primary PFEP KPI, providing crucial insights into working capital efficiency. Establish precise min-max levels based on usage patterns and lead times, ultimately freeing up resources in working capital.
- Stock-out frequency serves as another vital indicator of PFEP success. Develop early warning indicators that predict potential shortages before they occur, allowing for proactive rather than reactive inventory management.
- On-time delivery performance provides a customer-focused perspective on PFEP effectiveness. Carefully analyze lead times and safety stock levels, to demonstrate how proper PFEP implementation directly impacts customer satisfaction.
- Carrying cost reduction represents a quantifiable financial benefit of effective PFEP implementation. Have better space utilization, reduce obsolescence, and lower insurance costs.
- Production line efficiency improvements often reveal the operational impact of PFEP implementation. This improvement directly contributes to increased throughput and reduced production delays.
When establishing PFEP KPIs, I always emphasize the importance of creating a balanced scorecard that captures both operational and financial metrics. Successful organizations typically monitor 5-7 core KPIs while maintaining several supporting metrics for detailed analysis.
Struggling with Recurring Inventory Management Issues?
Our Root Cause Analysis course will teach you proven methods to identify and eliminate the underlying causes of inventory problems. Learn how to use facts and evidence to develop sustainable solutions that prevent issues from recurring.
Case Studies: Real-World Plan for Every Part (PFEP) Success Stories
One significant project involved a major automotive manufacturer struggling with inventory accuracy and production delays. Their initial situation mirrors: multiple storage locations for the same parts and frequent line stoppages.
By implementing a comprehensive PFEP system, they achieved a 45% reduction in inventory levels while improving production efficiency by 32%.
This plan for every part example particularly stands out because it demonstrated how proper implementation could transform even the most complex manufacturing environments.
A small electronics company presented a different but equally interesting challenge. With limited resources and over 5,000 SKUs, they needed a scaled approach to PFEP implementation. Started with their highest-volume products, representing about 20% of their inventory but 80% of their throughput.
Within six months, they reduced carrying costs by 38% and improved on-time delivery from 82% to 97%. This case demonstrates that PFEP can be effectively scaled to suit organizations of any size.
Perhaps the most dramatic transformation occurred in the food and beverage sector, where perishability adds another layer of complexity.
Working with a regional beverage distributor, they implemented a PFEP system that reduced waste by 65% and improved inventory turnover by 85%. This example showcases how PFEP principles can be adapted to address industry-specific challenges while maintaining core efficiency benefits.
Plan for Every Part (PFEP) in the Context of Industry 4.0
Modern PFEP implementations leverage advanced technologies to achieve unprecedented levels of efficiency and control.
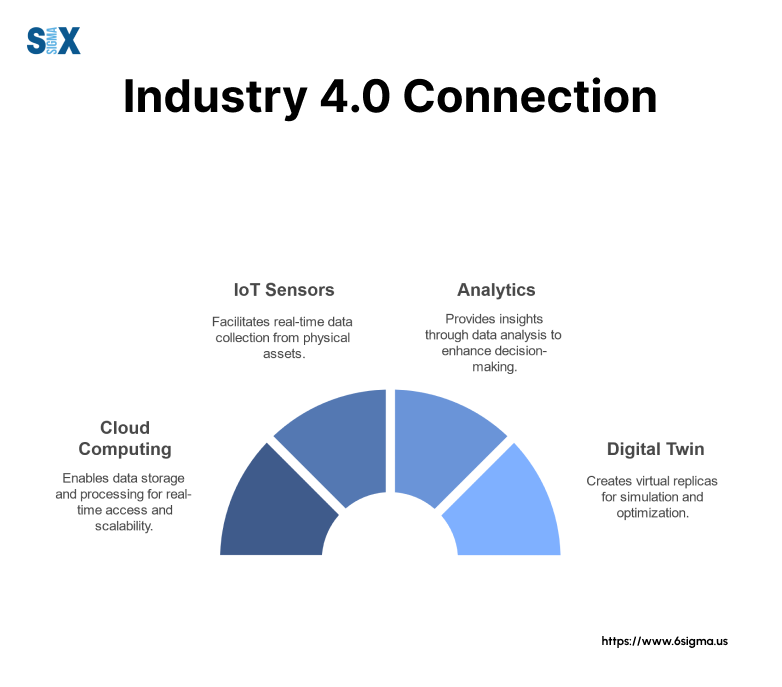
Smart Manufacturing
The integration of PFEP with smart manufacturing systems represents a quantum leap in inventory management capabilities. Implement an Industry 4.0-enabled PFEP system that connected real-time production data with inventory management.
This integration results in a reduction in manual data entry and an improvement in inventory accuracy. The key lies in creating seamless communication between different systems while maintaining data integrity across the entire manufacturing ecosystem.
Predictive Analytics and Machine Learning
Predictive analytics and machine learning have revolutionized how we approach PFEP implementation. You can use algorithms to analyze historical usage patterns, supplier performance, and market trends to optimize inventory levels automatically.
This advanced application of PFEP principles can lead to a reduction in safety stock requirements while maintaining high service levels. The system’s ability to learn and adapt to changing conditions transforms reactive inventory management into proactive supply chain optimization.
Blockchain
Blockchain technology has emerged as a powerful tool for enhancing traceability within PFEP systems. Implement blockchain-enabled PFEP tracking that provides complete visibility of parts from supplier to final assembly.
This implementation reduced part authentication time and virtually eliminated counterfeit components from entering the supply chain.
Digital Twins
Digital twins have become increasingly crucial in modern PFEP implementations. Create digital representations of their entire inventory ecosystem, enabling real-time simulation and optimization of material flows.
This approach allows you to test various scenarios and optimize storage layouts virtually before implementing physical changes, reducing implementation risks and improving space utilization.
Industry 4.0
The convergence of PFEP and Industry 4.0 technologies has created opportunities for unprecedented operational excellence. Organizations can achieve remarkable results by combining traditional PFEP principles with advanced digital capabilities.
The key is to maintain a balance between technological innovation and practical operational requirements while ensuring that new implementations align with core business objectives.
Sustainability and PFEP
There is a growing emphasis on sustainability in manufacturing operations. You need specific strategies for integrating sustainability principles into PFEP implementations, creating both environmental and economic benefits.
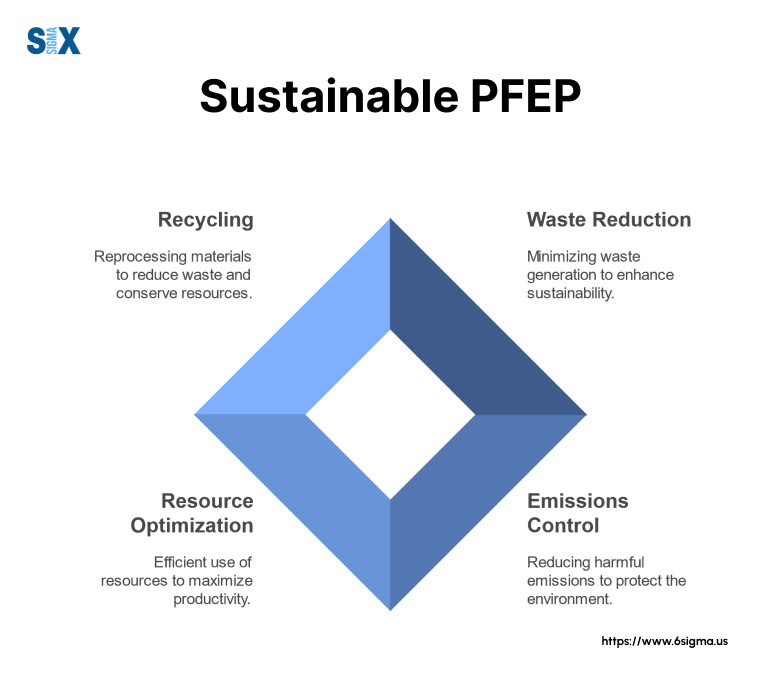
Waste Reduction with Plan for Every Part
Reducing waste through optimized inventory represents one of the most significant sustainability opportunities in PFEP implementation.
Implement a sustainable inventory management system that reduces waste through precise demand forecasting and inventory control. This Plan for Every Part approach can not only minimize excess inventory but can also significantly reduce the environmental impact of obsolete materials.
Transportation Emissions
Transportation emissions reduction has become a crucial focus in modern PFEP implementations. Change material flow patterns using PFEP data, which can result in a reduction in internal transport movements and associated emissions.
The key is to optimize storage locations based on usage frequency and implement efficient delivery routes. This approach not only reduces the company’s carbon footprint but also improves operational efficiency.
Sustainable Packaging
Sustainable packaging considerations have evolved significantly in recent years. This involves analyzing each part’s characteristics to determine optimal packaging solutions that balance protection requirements with environmental impact.
The implementation includes reusable containers, biodegradable materials, and optimized package sizes that reduce both waste and transportation costs.
Circular Economy and Plan for Every Part
Circular economy principles have become increasingly important in PFEP implementation. Use a closed-loop system that tracks materials from receipt through reuse or recycling. This approach improves resource utilization and reduces waste disposal costs.
The PFEP system becomes instrumental in identifying opportunities for material reuse and recycling, supporting a company’s sustainability goals while maintaining operational efficiency.
Sustainable Practices
The integration of sustainability principles into PFEP systems requires careful consideration of environmental impacts throughout the supply chain. Successful implementations typically achieve both environmental and economic benefits.
Plan for Every Part (PFEP) and Post-Pandemic Supply Chain Resilience
The global pandemic has fundamentally changed how we approach supply chain management, and PFEP has become crucial for building resilient supply chains.
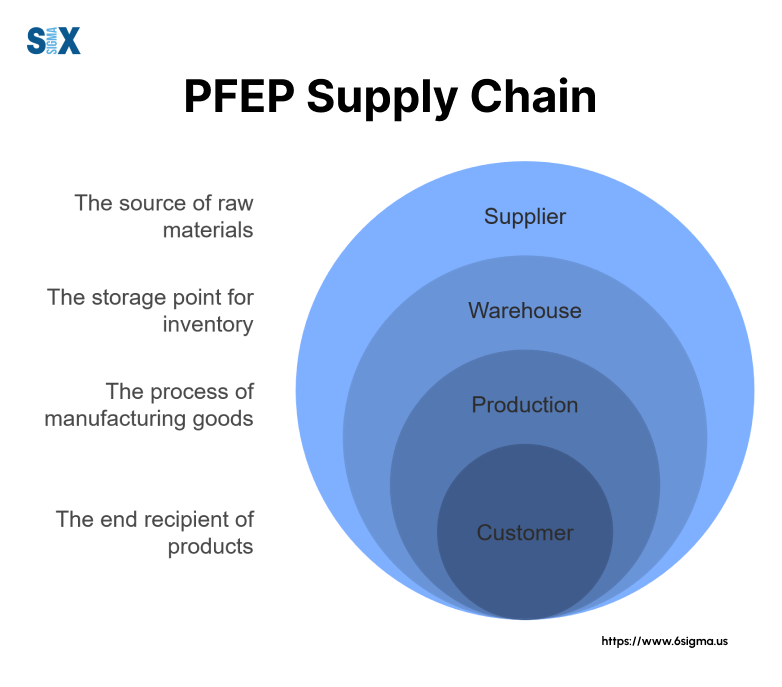
- Addressing supply chain disruptions requires a comprehensive understanding of your entire parts ecosystem. Utilize PFEP data to identify critical components and supply chain vulnerabilities.
This analysis will enable you to reduce supply disruption impacts through strategic inventory positioning and supplier diversification. The key lies in using detailed PFEP records to map supply chain dependencies and develop robust contingency plans.
- Risk mitigation strategies have evolved significantly in the post-pandemic era. Implement a multi-tiered risk assessment framework within the PFEP system to evaluate suppliers based on geographical location, capacity constraints, and historical performance.
This approach can help reduce supply chain disruptions and improve overall supply chain resilience. The Plan for Every Part system becomes instrumental in identifying and addressing potential risks before they impact operations.
- Building flexibility and adaptability into supply chains has become paramount. Restructure your PFEP implementation to include alternative suppliers and routing options for critical components.
This enhanced flexibility will allow you to maintain high service levels despite significant market disruptions. The key is to maintain detailed data about alternative sources and transportation routes within the PFEP system.
- Scenario planning with PFEP data has emerged as a crucial tool for supply chain resilience. You can use PFEP data to model different disruption scenarios and plan appropriate responses.
This approach enables you to reduce response time to supply chain disruptions while maintaining optimal inventory levels.
The post-pandemic environment demands a more sophisticated approach to supply chain management, and PFEP provides the foundation for building this resilience.
Through careful analysis of component data, supplier relationships, and logistics networks, organizations can develop robust strategies for managing future disruptions.
Going Ahead
The benefits of PFEP implementation extend far beyond basic inventory management. I’ve seen organizations achieve remarkable results: inventory reductions, productivity improvements, and exceed customer service levels.
For businesses considering PFEP implementation, the message is clear: in today’s dynamic manufacturing environment, traditional inventory management approaches are no longer sufficient.
PFEP provides the framework needed to optimize operations, reduce costs, and build resilient supply chains. It also successfully adapts to organizations of all sizes and complexities.
The key takeaways for effective PFEP management center on commitment, consistency, and continuous improvement. Success requires more than just implementing software or creating databases ā it demands a cultural shift toward data-driven decision-making and operational excellence.
The integration of advanced technologies, sustainability requirements, and increasing supply chain complexity will make PFEP even more crucial for operational success. Organizations that embrace these changes while maintaining core PFEP principles will be best positioned for future success.
Take the first step toward PFEP implementation by assessing your current inventory management practices and identifying opportunities for improvement.
The future belongs to organizations that can effectively manage their parts ecosystem while maintaining flexibility and efficiency ā and PFEP provides the foundation for achieving these goals.
SixSigma.us offers both Live Virtual classes as well as Online Self-Paced training. Most option includes access to the same great Master Black Belt instructors that teach our World Class in-person sessions. Sign-up today!
Virtual Classroom Training Programs Self-Paced Online Training Programs