The Ultimate Guide to Overall Equipment Effectiveness (OEE): Mastering Calculation, Implementation, and Optimization
Efficiency isn’t just a goal—it’s a necessity for survival and growth.
This is where Overall Equipment Effectiveness (OEE) comes into play, serving as the gold standard for measuring productivity and identifying opportunities for improvement in your operations.
Key Highlights
We’ll dive deep into the world of Overall Equipment Effectiveness (OEE), covering everything from basics to advanced implementation strategies. You’ll learn:
- What Overall Equipment Effectiveness is and why it’s critical for manufacturing success
- How to calculate OEE using a step-by-step approach
- The three key components of OEE (Overall Equipment Effectiveness): Availability, Performance, and Quality
- Real-world examples and case studies showcasing OEE in action
- Strategies for implementing OEE in your organization
- Advanced concepts and future trends in Overall Equipment Effectiveness (OEE)
What is Overall Equipment Effectiveness (OEE)?
At its core, Overall Equipment Effectiveness (OEE) is a powerful metric that measures how effectively a manufacturing operation utilizes its resources. It’s like a report card for your production line, providing a comprehensive view of your manufacturing performance.
The definition of Overall Equipment Effectiveness (OEE) goes beyond just measuring output. It’s a holistic approach considering three critical components: Availability, Performance, and Quality. Let me break these down for you:
- Availability: This measures the amount of time your equipment is running compared to the planned production time. It accounts for both planned and unplanned downtime.
- Performance: This component looks at how fast your equipment is running compared to its ideal speed. Are you operating at peak capacity, or is there room for improvement?
- Quality: This factor considers how many good parts you’re producing compared to the total parts produced. It’s all about minimizing defects and waste.
When we combine these three components, we get a clear picture of our overall equipment effectiveness. The meaning of Overall Equipment Effectiveness (OEE) becomes clear: it’s about maximizing productivity while minimizing waste.
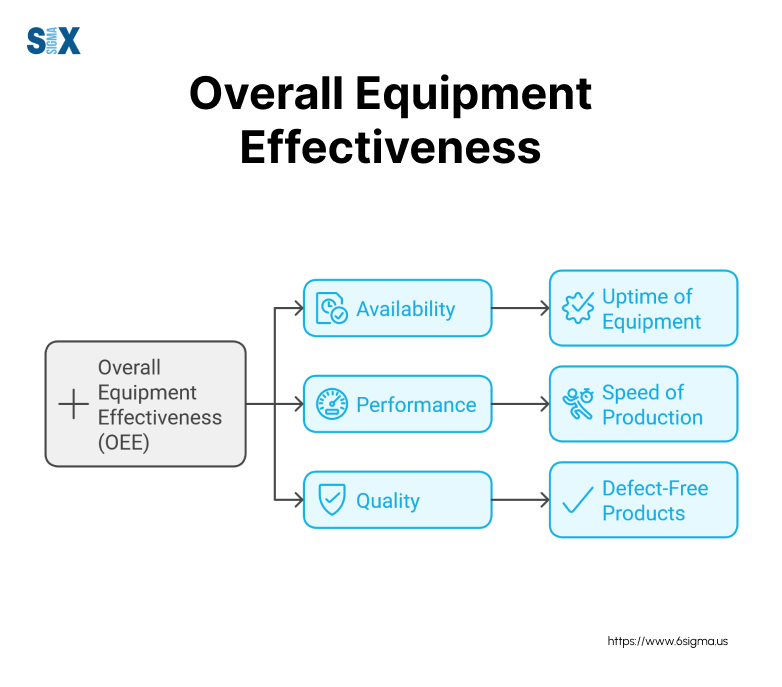
But why is OEE so crucial for manufacturing?
It provides a single, easy-to-understand metric that can highlight inefficiencies in your production process. By identifying these areas of waste, you can focus your improvement efforts where they’ll have the most impact.
OEE fits perfectly into lean manufacturing, which form the basis of Lean Fundamentals, and continuous improvement methodologies. It aligns with the core principles of eliminating waste and constantly striving for better performance. I often use Overall Equipment Effectiveness (OEE) as a starting point when implementing Six Sigma projects in manufacturing environments, leveraging techniques acquired through six sigma certification.
To help visualize this concept, imagine an infographic showing the three components of OEE as gears working together. When all three gears (Availability, Performance, and Quality) are optimized, your OEE score improves, and your manufacturing process runs like a well-oiled machine.
Calculating Overall Equipment Effectiveness (OEE)
I’m going to break down the overall equipment effectiveness formula and guide you through the process step-by-step. By the end of this section, you’ll be able to calculate OEE like a pro.
The OEE Formula Explained
Let’s start with the basic OEE formula:
OEE = Availability x Performance x Quality
This formula is the foundation of how OEE is calculated. Each component is expressed as a percentage, and when multiplied together, they give us our OEE score. Now, let’s dive deeper into each component.
Step-by-Step Calculation Guide
- Calculating Availability
Availability = Actual Run Time / Planned Production Time
To calculate this, you need to know
– Planned Production Time
– Downtime (both planned and unplanned) - Calculating Performance
Performance = (Ideal Cycle Time x Total Count) / Actual Run Time
Here, you’ll need
– Ideal Cycle Time (how long it should take to produce one unit)
– Total Count (how many units were produced)
– Actual Run Time (from the Availability calculation) - Calculating Quality
Quality = Good Count / Total Count
This requires
– Total Count (from the Performance calculation)
– Good Count (how many units meet quality standards)
Once you have these three percentages, multiply them together to get your OEE score.
Overall Equipment Effectiveness (OEE) Calculation Example
Let’s walk through an OEE calculation example for a hypothetical manufacturing line:
Planned Production Time: 8 hours (480 minutes)
Downtime: 60 minutes
Ideal Cycle Time: 1 minute per unit
Total Count: 350 units
Good Count: 330 units
- Availability
Actual Run Time = 480 – 60 = 420 minutes
Availability = 420 / 480 = 0.875 or 87.5% - Performance
Performance = (1 x 350) / 420 = 0.833 or 83.3% - Quality
Quality = 330 / 350 = 0.943 or 94.3%
OEE = 0.875 x 0.833 x 0.943 = 0.687 or 68.7%
This OEE calculation example shows us that our hypothetical line is operating at 68.7% effectiveness. There’s room for improvement!
Common Pitfalls in OEE Calculation
- Not accounting for all downtime
- Using theoretical rather than actual cycle times
- Overlooking minor stops or slow cycles in performance calculations
- Not considering rework in quality calculations
To avoid these pitfalls, ensure you’re collecting accurate data and considering all aspects of your production process.
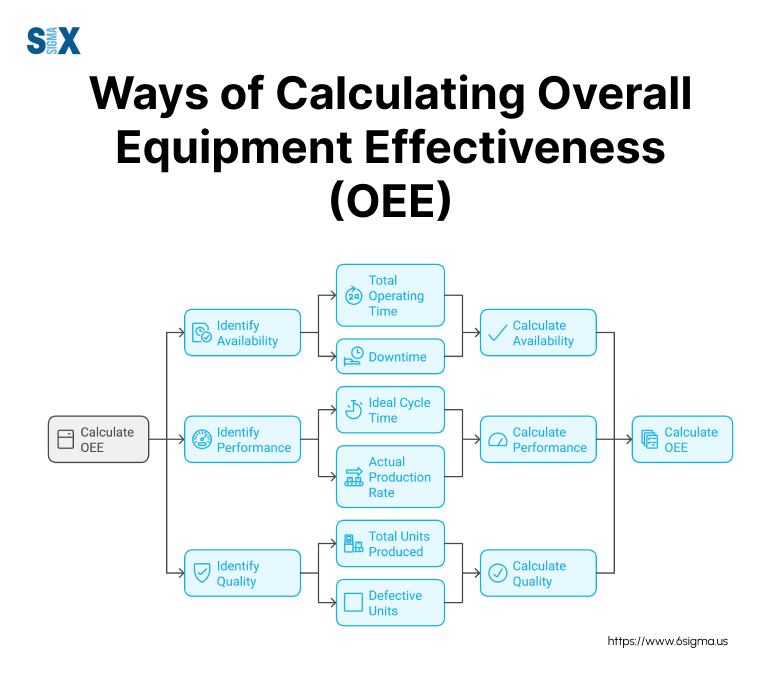
Use our interactive OEE calculator to input your data and calculate your OEE score instantly!
Remember, calculating OEE is just the first step. The real value comes from using this metric to identify areas for improvement and track your progress over time.
Ready to put your Overall Equipment Effectiveness (OEE) knowledge into practice? Our Lean Six Sigma Yellow Belt certification offers hands-on experience with OEE calculation and analysis.
The Six Big Losses and Their Impact on Overall Equipment Effectiveness (OEE)
These losses are the hidden culprits that erode your manufacturing efficiency, and identifying them is crucial for optimizing your OEE.
Overview of the Six Big Losses
The Six Big Losses are categorized into three groups, each impacting a specific component of OEE:
- Availability Losses
- Breakdowns
- Setup and Adjustments
- Performance Losses
- Small Stops
- Reduced Speed
- Quality Losses
- Startup Defects
- Production Defects
How Each Loss Affects Overall Equipment Effectiveness (OEE) Components
- Breakdowns: These unplanned stops significantly impact Availability. For instance, at a paper mill I consulted for, frequent machine breakdowns were reducing their Availability score by 15%.
- Setup and Adjustments: These planned stops also affect Availability. I once worked with an electronics manufacturer where lengthy changeovers were eating up 20% of their production time.
- Small Stops: These brief interruptions impact Performance. At an automotive parts supplier, I discovered that small, unrecorded stops were reducing their performance score by 10%.
- Reduced Speed: This loss also affects Performance. A food processing plant I advised was running their equipment at 80% of its designed speed due to process variations.
- Startup Defects: These impact the quality score. A pharmaceutical company I worked with was losing 5% of their production to defects during the startup phase.
- Production Defects: These also affect quality. At a consumer electronics factory, 3% of their products were failing final quality checks.
Strategies for Minimizing Losses
- Implement preventive maintenance to reduce breakdowns – Effective root cause analysis training can equip teams to systematically investigate why these breakdowns occur, leading to more robust solutions.
- Use SMED (Single-Minute Exchange of Die) techniques to minimize setup times.
- Train operators to quickly address small stops and record them accurately.
- Optimize processes to run at designed speeds without sacrificing quality.
- Implement Statistical Process Control (SPC) to reduce defects – Pair SPC with root cause analysis training to systematically address recurring defects and downtime triggers uncovered by OEE metrics.
Case Study: Improving OEE by Targeting Specific Losses
Let me share a success story from my work with a leading automotive parts manufacturer. When I first arrived, their OEE was a mere 65%. After analyzing their Six Big Losses, we found that setup times and small stops were their biggest issues.
We implemented an SMED program that reduced their average setup time from 45 minutes to 15 minutes. For small stops, we introduced a quick response team and a system for operators to log these brief interruptions.
The result? Within six months, their Overall Equipment Effectiveness (OEE) jumped to 82%. Their Availability increased from 75% to 85%, and their performance improved from 80% to 90%. This translated to an additional $2 million in annual revenue without any capital investment.
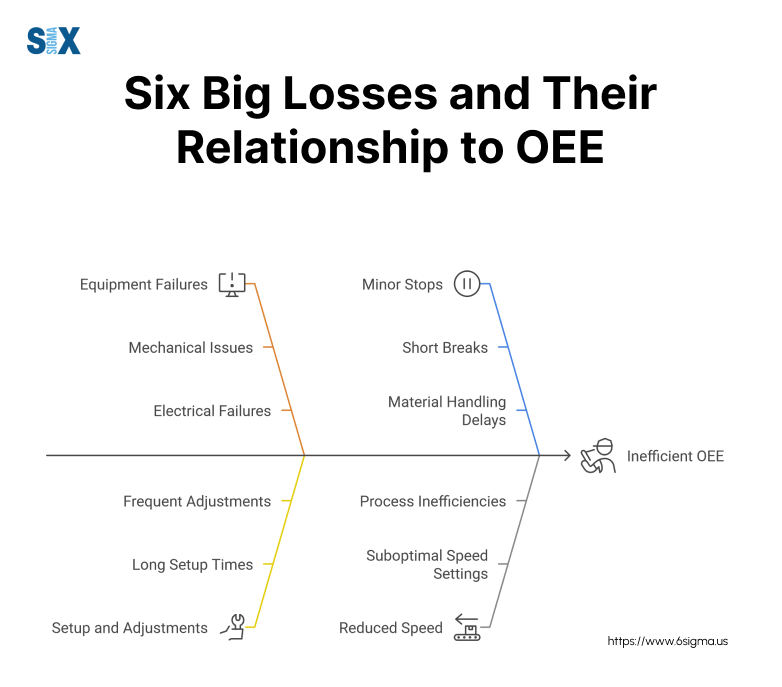
By systematically tackling each loss, you can unlock significant improvements in your production efficiency. Remember, OEE isn’t just about measuring – it’s about identifying opportunities for improvement and taking action.
Ready to tackle the Six Big Losses in your organization? Our Lean Fundamentals course provides practical strategies for identifying and eliminating waste in manufacturing processes.
Industry Benchmarks and Setting Realistic Overall Equipment Effectiveness (OEE) Goals
Understanding industry benchmarks and knowing how to set realistic targets can make the difference between a successful OEE implementation and one that falls short. Let’s dive into the world of OEE benchmarks and goal-setting.
Typical OEE Scores Across Industries
In my experience, OEE scores can vary widely across different manufacturing sectors. Here’s a breakdown of average OEE scores I’ve observed:
- Discrete Manufacturing: 60-75%
- Process Manufacturing: 65-80%
- Pharmaceutical: 70-85%
- Automotive: 65-80%
- Food and Beverage: 55-75%
It’s important to note that these are averages, and individual plants within these industries may perform better or worse.
World-Class Overall Equipment Effectiveness (OEE) Benchmarks
When we talk about world-class OEE, we’re typically referring to scores of 85% or higher. However, I always caution my clients that this shouldn’t be their immediate goal.
Here’s what world-class OEE typically looks like:
- Availability: 90%
- Performance: 95%
- Quality: 99%
Multiplying these together gives us an OEE of 85.5%. Achieving this level of efficiency requires a relentless focus on continuous improvement and often years of dedicated effort.
How to Set Appropriate OEE Targets for Your Operation
Setting realistic OEE goals is crucial for maintaining momentum and motivation in your improvement efforts. Here’s the approach I’ve used successfully with numerous clients:
- Establish your baseline: Before setting any goals, measure your current Overall Equipment Effectiveness (OEE) over a significant period (at least a month) to get an accurate baseline.
- Identify your biggest losses: Use the Six Big Losses framework we discussed earlier to pinpoint your most significant areas for improvement.
- Set incremental targets: Instead of aiming for world-class OEE immediately, set smaller, achievable goals. For example, if your baseline OEE is 60%, aim for 65% within six months.
- Focus on one component at a time: Often, it’s most effective to focus on improving one OEE component (Availability, Performance, or Quality) rather than trying to improve all three simultaneously.
- Benchmark against similar operations: If possible, compare your OEE with similar operations in your industry to set competitive targets.
- Review and adjust regularly: OEE goals should be dynamic. Review your progress quarterly and adjust your targets as needed.
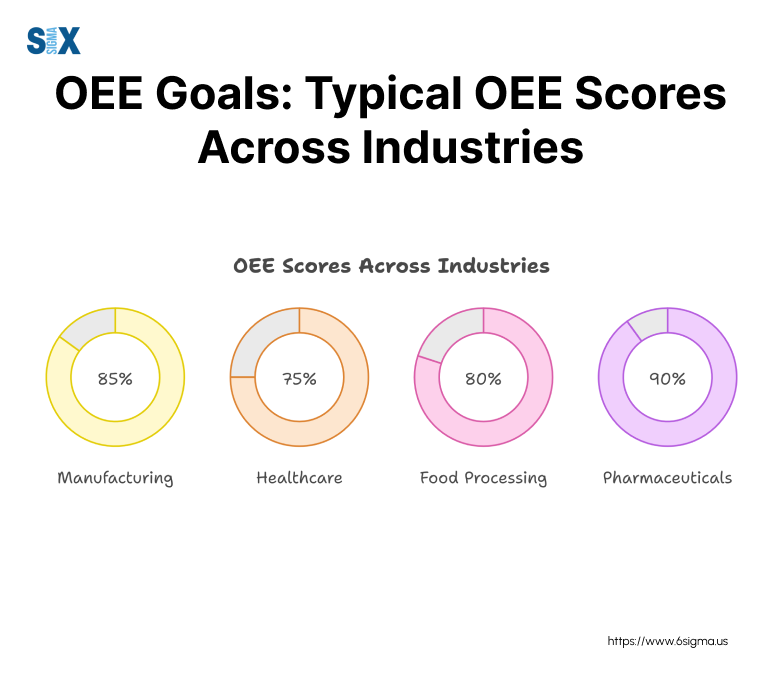
Remember, the goal of Overall Equipment Effectiveness (OEE) isn’t just to hit a number—it’s to drive continuous improvement in your operations. In my work with a major electronics manufacturer, we started with an OEE of 65% and set an initial goal of 70%. By focusing on reducing setup times and minor stops, we hit 72% within four months, which energized the team to push for further improvements.
Setting realistic OEE goals is as much an art as it is a science. It requires a deep understanding of your processes, your team’s capabilities, and the broader context of your industry. But with the right approach, OEE can be a powerful tool for driving substantial improvements in your manufacturing efficiency.
Implementing Overall Equipment Effectiveness (OEE) in Your Organization
With the right approach, it can revolutionize your manufacturing processes. Let me walk you through the steps for a successful OEE implementation, common challenges you might face, and strategies to overcome them.
Steps for Successful OEE Implementation
- Educate and Build Awareness
Start by educating your team about OEE. Everyone from the shop floor to the C-suite should understand what OEE is and why it’s important. - Define Your Metrics
Clearly define how you’ll measure Availability, Performance, and Quality in your specific context. - Establish Baseline Performance
Measure your current OEE to set a starting point for improvement. - Set Realistic Goals
Use the benchmarks we discussed earlier to set achievable targets. - Implement Data Collection Systems
Invest in tools to accurately and consistently collect OEE data. - Analyze and Act on Data
Regularly review OEE data and use it to drive improvement initiatives. - Continuously Improve
Treat OEE implementation as an ongoing process, not a one-time project.
Common Challenges and How to Overcome Them
- Resistance to Change
Solution: Involve employees in the implementation process and communicate the benefits of Overall Equipment Effectiveness (OEE). - Data Accuracy Issues
Solution: Invest in automated data collection systems and provide thorough training on data entry. - Misalignment of Goals
Solution: Ensure OEE goals align with overall business objectives and communicate this alignment. - Lack of Resources
Solution: Start small with a pilot project to demonstrate ROI before scaling up.
Change Management Strategies for OEE Adoption
- Leadership Buy-In
Secure support from top management. Their commitment is crucial for successful implementation. - Clear Communication
Develop a communication plan to keep all stakeholders informed about the OEE initiative. - Training and Support
Provide comprehensive training on OEE concepts and measurement techniques. - Celebrate Early Wins
Recognize and reward initial improvements to maintain momentum. - Continuous Feedback
Create channels for employees to provide feedback on the Overall Equipment Effectiveness (OEE) process.
Personal Anecdote: OEE Implementation Success Story
Let me share a story from my work with a large automotive parts manufacturer. When I first arrived, their OEE was hovering around 60%, and there was significant skepticism about implementing yet another metric.
We started by forming a cross-functional team and providing extensive education on OEE. We then implemented a user-friendly data collection system and set an initial goal of improving OEE to 65% within six months.
The key to our success was involving operators in the process. We created visual management boards that displayed real-time OEE data, and operators were encouraged to suggest improvements. This level of engagement led to numerous small but impactful changes.
One operator noticed that certain tool changes were taking longer than necessary. By optimizing this process, we reduced changeover times by 20%, significantly improving our Availability score.
Within four months, OEE had improved to 68%, surpassing our initial goal. This early win created a buzz throughout the organization, and soon other departments were clamoring to implement OEE.
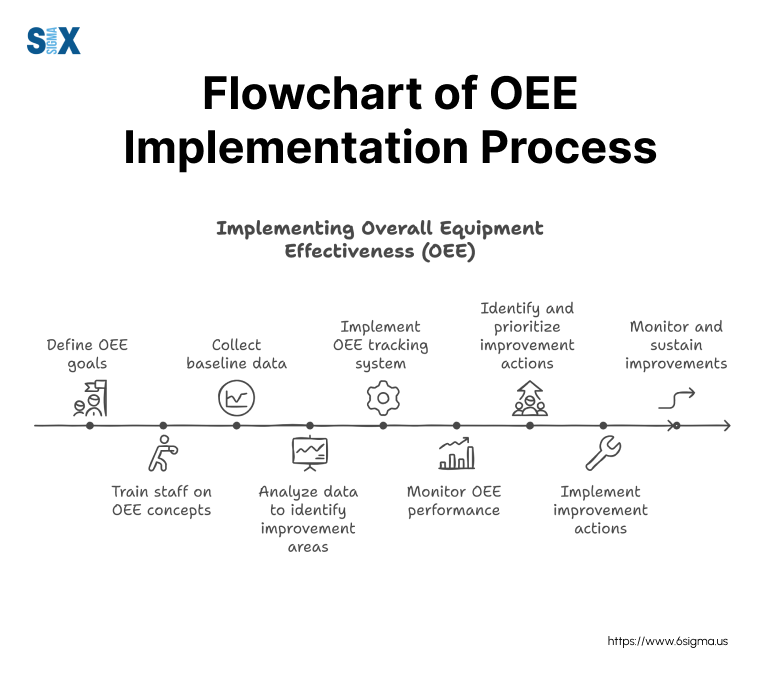
Remember, implementing OEE is not just about measuring – it’s about creating a culture of continuous improvement. It requires patience, persistence, and a willingness to learn from both successes and setbacks. But when done right, OEE can be a powerful tool for driving manufacturing excellence.
Want to lead successful OEE implementations in your organization? Our Lean Six Sigma Green Belt certification provides advanced strategies for process improvement and change management.
More Overall Equipment Effectiveness (OEE) Concepts and Future Trends
Let’s explore some advanced concepts and future trends that are reshaping the landscape of manufacturing efficiency.
Total Effective Equipment Performance (TEEP)
TEEP takes OEE a step further by considering all calendar time, not just planned production time. It answers the question, “How well are we utilizing our assets around the clock?”
TEEP = OEE x Utilization
Where Utilization = Planned Production Time / All Available Time (24/7/365)
I’ve implemented TEEP at a semiconductor plant, which led to a 15% increase in overall asset utilization by identifying opportunities for additional production during previously unused time slots.
Overall Operations Effectiveness (OOE)
OOE broadens the scope beyond individual equipment to encompass entire value streams or production systems. It considers factors like material availability and human resources.
OOE = OEE x Material Availability x Human Performance
In a recent project with an automotive supplier, implementing OOE helped us identify bottlenecks in material flow and staffing, leading to a 20% improvement in overall system performance.
OEE in the Context of Industry 4.0 and Smart Manufacturing
Industry 4.0 is revolutionizing how we collect and analyze OEE data. Internet of Things (IoT) sensors can now provide real-time OEE metrics, allowing for immediate corrective actions.
Key advancements include
- Real-time OEE dashboards
- Automated data collection reduces human error
- Integration with Manufacturing Execution Systems (MES)
During a recent consultation with a major electronics manufacturer, we implemented IoT sensors that provided minute-by-minute OEE data. This allowed operators to make real-time adjustments, resulting in a 10% OEE improvement within just three months.
Predictive OEE using Machine Learning and AI
The future of OEE lies in prediction and prevention. Machine learning algorithms can analyze historical OEE data to predict future performance and potential equipment failures.
Case Study: AI-Driven OEE Optimization
I recently worked with a pharmaceutical company to implement an AI-driven OEE system. The system analyzed patterns in historical OEE data and equipment sensor readings to predict potential failures.
Results
- 30% reduction in unplanned downtime
- 15% improvement in overall OEE
- $2 million annual savings in maintenance costs
The AI system could predict equipment failures up to 72 hours in advance, allowing for scheduled maintenance during planned downtime.
Looking ahead, I see OEE becoming increasingly predictive and prescriptive. Imagine a system that not only tells you when a machine is likely to fail but also recommends the most efficient maintenance schedule and procedures.
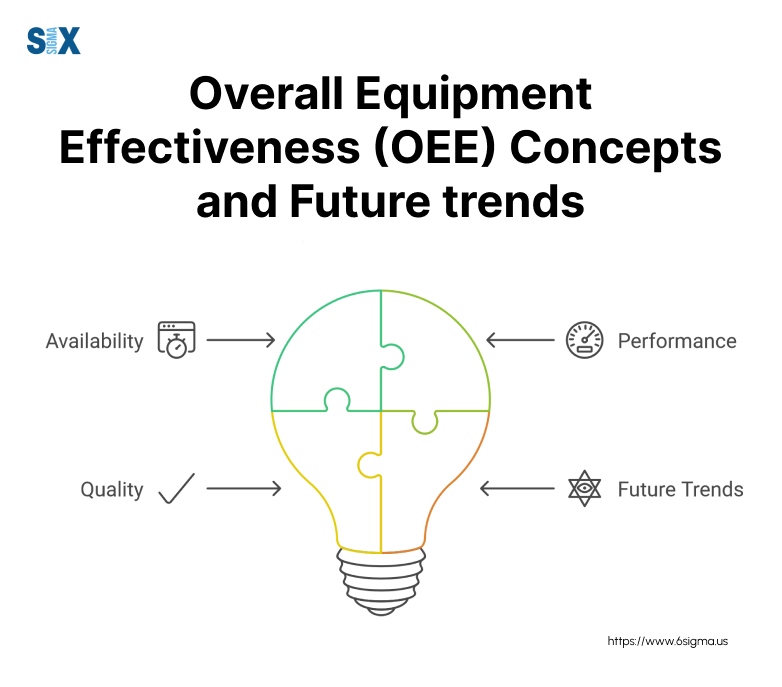
As we move towards autonomous manufacturing systems, OEE will play a crucial role in ensuring these systems operate at peak efficiency. The integration of OEE with technologies like digital twins and augmented reality will provide unprecedented visibility into manufacturing processes.
Overall Equipment Effectiveness (OEE) Software and Tools
I can’t stress enough how crucial the right tools are for success. OEE software and tools have become indispensable for manufacturers looking to optimize their processes. Let me share some insights on choosing and using these powerful resources.
Overview of OEE Software Solutions
OEE software has come a long way since I first started in this field. Modern solutions offer real-time data collection, advanced analytics, and intuitive dashboards. These tools can transform the way you track and improve your manufacturing efficiency.
Key benefits of using OEE software include
- Automated data collection, reducing human error
- Real-time visibility into production performance
- Advanced analytics for identifying improvement opportunities
- Standardized reporting across different production lines or plants
In my work with companies like 3M and Dell, I’ve seen firsthand how the right OEE software can lead to double-digit improvements in productivity within months of implementation.
Key Features to Look for in Overall Equipment Effectiveness (OEE) Tools
When evaluating OEE tools, here are some essential features I always recommend my clients look for:
- Real-time data collection and monitoring
- Customizable dashboards for different user roles
- Automated OEE calculation and reporting
- Root cause analysis capabilities
- Integration with existing manufacturing systems (ERP, MES, etc.)
- Mobile accessibility for on-the-go monitoring
- Predictive maintenance capabilities
Remember, the goal is not just to calculate OEE, but to use it as a springboard for continuous improvement. Look for tools that support this broader objective.
Comparison of Popular OEE Software Options
While I can’t endorse specific products, I can share some insights on what to consider when comparing OEE software:
- Ease of Use: How intuitive is the interface? Will your operators need extensive training?
- Scalability: Can the software grow with your business?
- Customization: Does it allow for tailoring to your specific processes?
- Support and Updates: How responsive is the vendor’s support team? How often are updates released?
- Cost: Consider both upfront and ongoing costs. Sometimes, a higher initial investment can lead to greater long-term savings.
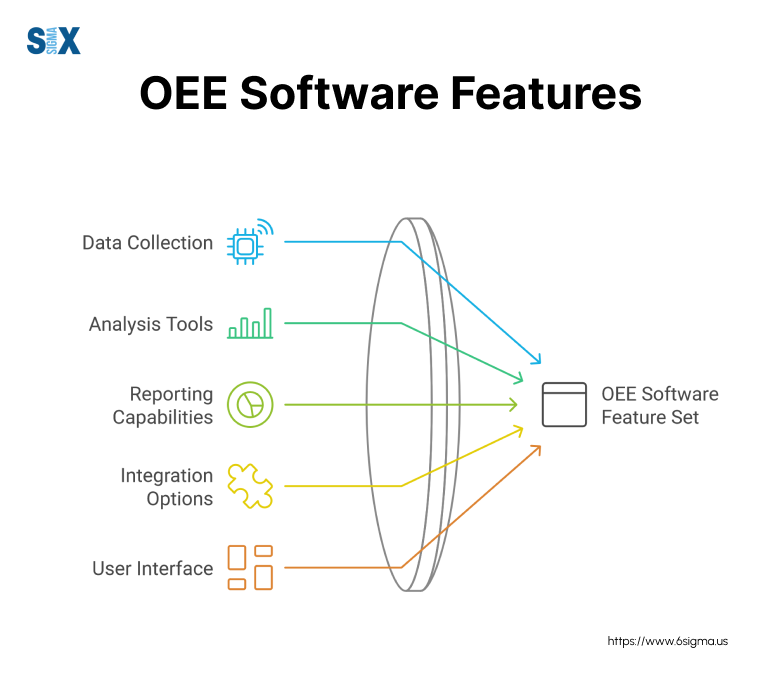
When I helped a major automotive parts manufacturer select their OEE software, we created a similar comparison table. This visual aid was crucial in helping stakeholders understand the trade-offs between different options.
One often overlooked aspect is the OEE calculator functionality. While most software includes this, the flexibility and ease of use can vary significantly. I always recommend testing this feature with your actual data before making a decision.
In my experience, the best OEE software acts as more than just a measurement tool – it becomes a central hub for continuous improvement efforts. For instance, at an electronics manufacturer I worked with, their OEE software not only tracked performance but also integrated with their maintenance scheduling and quality control systems. This holistic approach led to a 25% improvement in OEE within the first year.
Remember, while these tools are powerful, they’re not magic bullets. The real power comes from how you use the insights they provide to drive meaningful improvements in your manufacturing processes.
Case Studies: Overall Equipment Efficiency (OEE) Success Stories
These case studies not only demonstrate the power of OEE but also provide valuable lessons for anyone looking to implement or improve their OEE strategy. Let me share three compelling examples that showcase the versatility and impact of OEE.
Manufacturing Company Case Study: Automotive Parts Manufacturer
One of my most memorable projects was with a leading automotive parts manufacturer struggling with efficiency issues. Their initial OEE score was a mere 62%, well below industry standards.
Challenges
- Frequent unplanned downtime
- Inconsistent product quality
- Lack of standardized processes across shifts
Our Approach
- Implemented real-time OEE tracking system
- Conducted root cause analysis on major downtimes
- Standardized changeover procedures
- Introduced operator-led equipment maintenance
Results
After six months, their OEE improved to 78%, resulting in:
- 25% reduction in unplanned downtime
- 15% increase in production output
- $3.2 million annual cost savings
Key Lesson: Real-time visibility into OEE components can drive rapid improvements when combined with a culture of continuous improvement.
Process Industry Case Study: Chemical Plant
In a chemical plant I consulted for, OEE concepts were applied to continuous production processes, which presented unique challenges.
Challenges
- Difficulty in defining ‘ideal cycle time’ for continuous processes
- Complex interdependencies between process parameters
- Safety concerns limiting experimentation
Our Approach
- Adapted OEE calculation for continuous processes
- Utilized Statistical Process Control (SPC) to identify optimal operating parameters
- Implemented predictive maintenance based on OEE trends
Results
Over a year, we achieved:
- OEE improvement from 72% to 85%
- 30% reduction in quality-related losses
- 20% increase in throughput without additional capital investment
Key Lesson: OEE principles can be adapted to non-discrete manufacturing environments with creative thinking and data-driven approaches.
Non-Traditional OEE Application: Healthcare Services
One of my most innovative projects involved applying OEE concepts to improve operating room efficiency in a large hospital.
Challenges
- Adapting manufacturing metrics to healthcare setting
- Resistance from medical staff to ‘production line’ thinking
- Variability in procedure times and emergency cases
Our Approach
- Redefined OEE components for healthcare:
- Availability: Room utilization during scheduled hours
- Performance: Actual vs. expected procedure times
- Quality: Post-operative complications and readmissions
- Implemented a visual management system for room turnover
- Standardized pre-operative processes
Results
After nine months:
- ‘OEE’ improved from 65% to 82%
- 22% increase in surgical procedures performed
- $4.5 million additional revenue generated
- Reduced patient wait times by 35%
Key Lesson: OEE principles can be creatively applied beyond traditional manufacturing to drive efficiency in service industries.
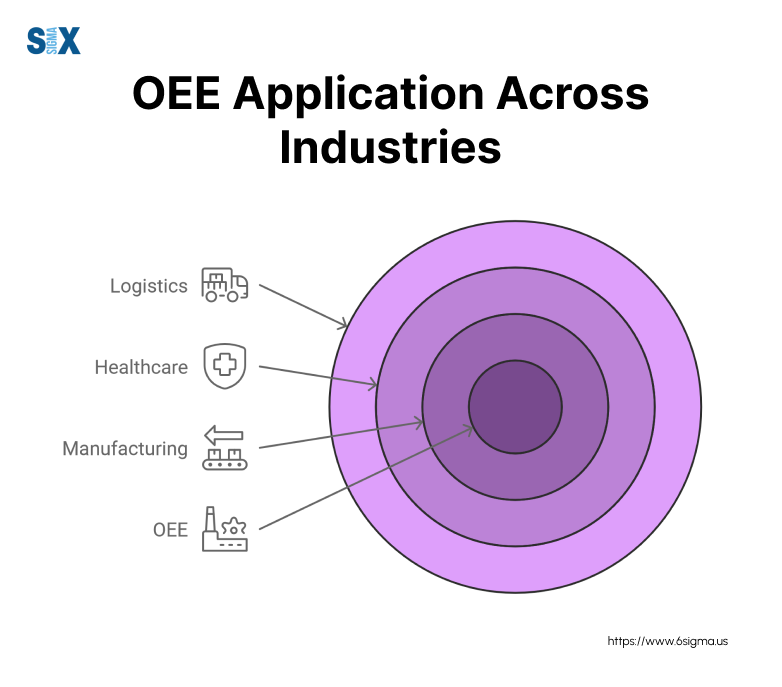
These case studies demonstrate that regardless of the industry or process type, OEE can be a powerful tool for driving efficiency and productivity. Driving such significant transformations often requires advanced process improvement leadership, which are covered in our Six Sigma Black Belt certification program.
The key lies in adapting the OEE concept to your specific context, engaging your team in the process, and maintaining a relentless focus on continuous improvement.
Ready to become an OEE expert and drive significant improvements in your organization? Our comprehensive Lean Six Sigma Black Belt course covers advanced OEE techniques and more.
Conclusion
The key takeaway is this: OEE is not just a metric, it’s a mindset. It’s a way of looking at your manufacturing processes holistically, identifying hidden inefficiencies, and driving continuous improvement.
In today’s competitive global marketplace, the importance of OEE cannot be overstated. It’s the difference between surviving and thriving, between good and world-class performance. As we’ve seen, even small improvements in OEE can lead to significant gains in output and profitability.
So, what’s your next step? If you haven’t already, I encourage you to start measuring OEE in your operations today. Begin with a single production line or process. Calculate your baseline, set realistic improvement targets, and engage your team in the journey of continuous improvement.
Remember, the goal isn’t perfection from day one, but rather consistent, incremental progress over time.
For those of you already using OEE, challenge yourself to take it to the next level. Can you implement real-time OEE tracking? Can you leverage predictive analytics to anticipate and prevent losses before they occur? The possibilities are endless.
Remember, in the world of manufacturing, what you don’t measure, you can’t improve. So start measuring, start improving, and let OEE be your guide on the journey to manufacturing excellence.
SixSigma.us offers both Live Virtual classes as well as Online Self-Paced training. Most option includes access to the same great Master Black Belt instructors that teach our World Class in-person sessions. Sign-up today!
Virtual Classroom Training Programs Self-Paced Online Training Programs