Operational Excellence with Visual Management Tools. A Complete Guide
It’s important to understand and share information quickly. That’s why visual management tools are so useful. They’re a key part of efficient lean manufacturing.
These tools include many different techniques and systems. They help make the workplace more organized, improve how work is done, and increase productivity.
With these tools, everyone on the team can easily see what’s happening. They can spot problems quickly and work together better. It’s like having a simple way to communicate that everyone understands quickly.
Visual tools make complex information easier to grasp. They help the whole team stay on the same page and make decisions faster. It’s a practical way to keep everything running smoothly.
Key Highlights
- Visual management tools are really important for lean manufacturing systems.
- They’re like the secret sauce that helps things run smoother on the shop floor and keeps everyone focused on always improving.
- Some popular tools you might see are Kanban boards (those visual task trackers), the 5S method (which is all about organizing your workspace), and Andon systems (think of them as a way to quickly signal problems).
- Visual management boards, like dashboards showing key numbers or SQDCP boards (that’s Safety, Quality, Delivery, Cost, and People), help drive excellent operations. They’re like scorecards that everyone can see and understand at a glance.
What are Visual Management Tools?
Visual management tools are helpful in modern manufacturing. They make it easier for everyone to communicate and keep things running smoothly.
These tools use pictures and visuals to share important information quickly. It helps in bringing collaboration and synergy between teams.
These visual aids help with organizing, tracking, and improving the manufacturing process. They’re important in lean manufacturing, which focuses on reducing waste and increasing value.
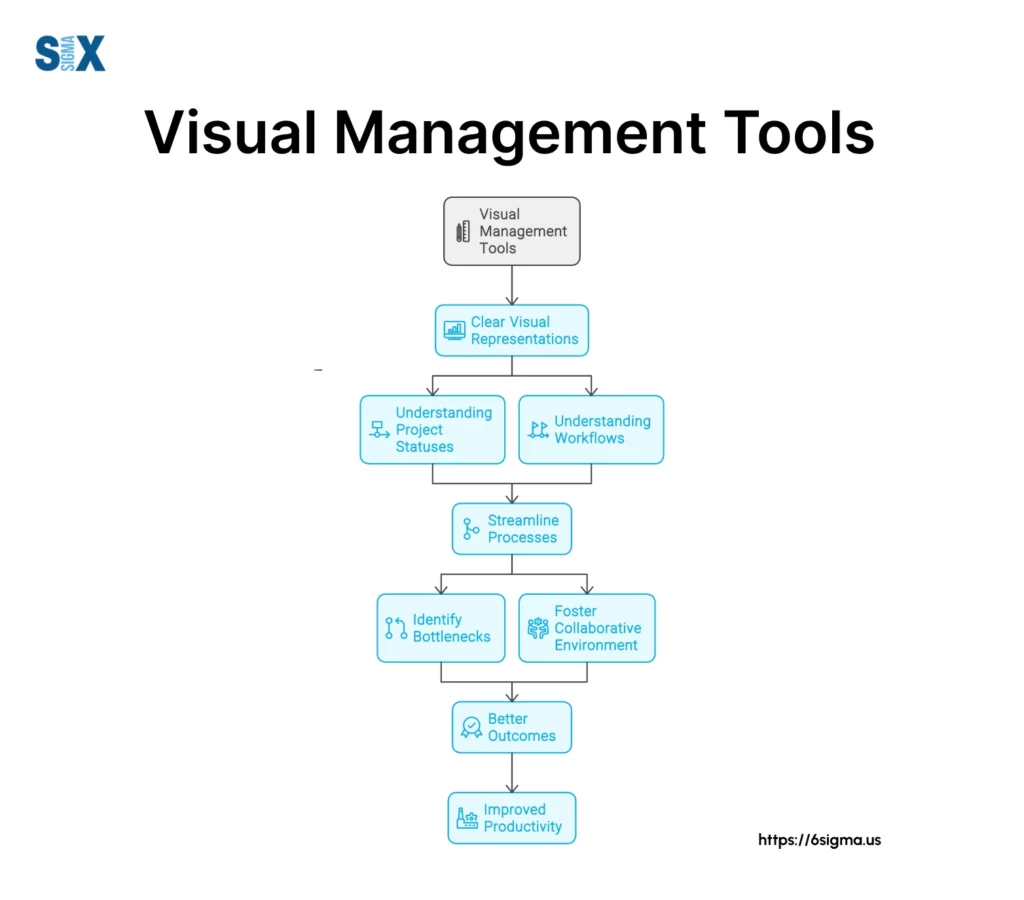
Now, why are these tools so important? Well, they do a bunch of cool things:
- They make complicated info easier to digest. It’s like turning a textbook into a comic book – suddenly, everyone gets it!
- They keep everyone on the same page. No more “I thought you meant this” situations.
- They speed up decision-making. You can see what’s happening in real time and make quick calls.
- They help spot problems. It’s like having a bunch of red flags that pop up when something’s not right.
- They break down communication barriers.
When used correctly, they bring great benefits to the overall functioning of an organization:
- Workers get more done because they know exactly what to do.
- Quality goes up because it’s easier to spot and fix mistakes.
- The place gets safer because hazards are marked.
- Inventory becomes a breeze to manage.
- Workflow improves because you can see and fix bottlenecks.
- Employees feel more involved and empowered.
- Problems get solved faster because you can see them coming.
- Training new folks becomes easier and quicker.
Understand the basics of visual management tools to improve workplace efficiency.
Types of Visual Management Tools
Visual management tools are essential components of lean manufacturing systems, designed to enhance shop floor efficiency and promote continuous improvement.
Let’s explore four key types of visual management tools that are widely used in various industries.
Kanban Boards and Workflow Optimization
Kanban boards are one of the most popular visual management tools, originating from the Toyota Production System. These boards provide a clear, visual representation of work in progress, helping teams optimize their workflow and identify bottlenecks.
Key features of Kanban boards include:
- Visual cards representing tasks or work items
- Columns depicting different stages of the process
- Work-in-progress (WIP) limits to prevent overloading
By implementing Kanban boards, organizations can:
- Improve task prioritization
- Enhance team collaboration
- Increase productivity by reducing waste and idle time
- Facilitate continuous improvement through regular process analysis
For example, a manufacturing plant might use a Kanban board to track production orders from initial request to final delivery, allowing managers to quickly identify delays or issues in the production process.
5S Methodology and Workplace Organization
The 5S methodology is a visual management technique focused on organizing the workplace for maximum efficiency and effectiveness. The five S’s stand for Sort, Set in order, Shine, Standardize, and Sustain.
Implementing 5S can lead to:
- Reduced waste and improved productivity
- Enhanced workplace safety
- Better quality control
- Improved employee morale and engagement
Visual aids used in 5S implementation often include:
- Color-coding systems for tool and equipment organization
- Shadow boards for easy tool identification and storage
- Floor markings to designate work areas and traffic flow
For instance, an automotive assembly line might use color-coded shadow boards to ensure that each tool is returned to its proper place after use, reducing time wasted searching for misplaced items.
Andon Systems for Real-Time Data Visualization
Andon systems are visual management tools that provide real-time feedback on the status of production processes. These systems typically use lights, audio signals, or digital displays to alert workers and managers of issues or abnormalities in the production line.
Benefits of Andon systems include:
- Immediate problem identification and resolution
- Reduced downtime and improved overall equipment effectiveness (OEE)
- Enhanced communication between operators and supervisors
- Facilitation of continuous improvement initiatives
An example of an Andon system in action might be a light stack on a production line that changes color to indicate different statuses: green for normal operation, yellow for minor issues, and red for major problems requiring immediate attention.
Visual Process Maps and Process Visibility
Visual process maps are graphical representations of workflows or processes, designed to improve process visibility and identify areas for improvement. These maps can take various forms, such as value stream maps, swimlane diagrams, or flowcharts.
Key advantages of visual process maps include:
- Clear visualization of complex processes
- Identification of waste and inefficiencies
- Improved communication and alignment among team members
- Facilitation of process improvement initiatives
For example, a logistics company might use a value stream map to visualize the entire supply chain process, from order placement to final delivery. This visual representation can help identify bottlenecks, unnecessary steps, or opportunities for automation.
By implementing these visual management tools, organizations can significantly enhance their operational excellence, improve employee engagement, and drive continuous improvement efforts.
Each tool serves a unique purpose in creating a more efficient, transparent, and productive workplace environment.
Get a deeper understanding of specific visual management tools to apply them in a workplace setting successfully.
Implementing Visual Management Tools with Boards
Visual management boards are powerful tools in lean manufacturing systems, providing a centralized hub for information and performance tracking. These boards play a crucial role in enhancing shop floor efficiency and promoting operational excellence.
Let’s explore some key types of visual management boards and their applications in detail.
Metrics Dashboards and Performance Indicators
Metrics dashboards are essential visual management tools that display key performance indicators (KPIs) in real time.
These dashboards provide a quick, at-a-glance view of an organization’s performance, allowing managers and employees to track progress toward goals and identify areas for improvement.
When implementing metrics dashboards:
- Choose relevant KPIs that align with your organization’s objectives
- Use clear, easy-to-read visuals such as graphs, charts, and gauges
- Update data frequently to ensure real-time decision-making
- Incorporate color-coding to highlight performance levels (e.g., green for on-target, red for below expectations)
By leveraging metrics dashboards, companies can enhance process visibility and drive continuous improvement efforts across the organization.
SQDCP Boards for Operational Excellence
SQDCP boards, which stand for Safety, Quality, Delivery, Cost, and People, are comprehensive visual management tools that address key aspects of operational excellence.
These boards provide a holistic view of an organization’s performance across multiple dimensions.
Key components of SQDCP boards include:
- Safety metrics: Incident rates, near-misses, and safety improvement initiatives
- Quality indicators: Defect rates, customer complaints, and quality improvement projects
- Delivery performance: On-time delivery rates, lead times, and inventory levels
- Cost efficiency: Production costs, waste reduction efforts, and cost-saving initiatives
- People metrics: Employee engagement, training progress, and productivity measures
By implementing SQDCP boards, organizations can maintain a balanced focus on all critical aspects of their operations, fostering a culture of continuous improvement and operational excellence.
Kamishibai Boards and Continuous Improvement
Kamishibai boards, originating from Japanese manufacturing practices, are versatile visual management tools that support continuous improvement efforts.
These boards use a system of cards to track and audit various processes, ensuring adherence to standards and identifying opportunities for enhancement.
Implementing Kamishibai boards involves:
- Creating cards for each process or area to be audited
- Establishing a regular audit schedule
- Training employees on the audit process and expectations
- Documenting findings and improvement actions
- Rotating responsibilities to engage all team members in the improvement process
Kamishibai boards promote employee engagement, standardization of processes, and a proactive approach to problem-solving, all of which are crucial elements in lean manufacturing systems.
Balanced Scorecard for Comprehensive Performance Tracking
The Balanced Scorecard is a strategic planning and management tool that provides a comprehensive view of an organization’s performance across four key perspectives: financial, customer, internal processes, and learning and growth.
When implemented as a visual management board, the Balanced Scorecard becomes a powerful tool for aligning daily operations with long-term strategic goals.
Key steps in implementing a Balanced Scorecard visual management board include:
- Defining objectives for each of the four perspectives
- Establishing measurable KPIs for each objective
- Setting targets and tracking progress visually
- Identifying initiatives to achieve the objectives
- Regularly reviewing and updating the scorecard to reflect changing priorities
By utilizing the Balanced Scorecard approach, organizations can ensure that their visual management systems capture both short-term operational metrics and long-term strategic goals, providing a holistic view of performance.
Visual Workplace Techniques
Visual workplace techniques are essential components of effective visual management tools in lean manufacturing systems. These techniques enhance communication, improve safety, and boost overall productivity on the shop floor.
Let’s explore some key visual workplace techniques that can significantly impact operational excellence.
Color-coding Systems for Enhanced Visual Communication
Color coding is a powerful visual management tool that simplifies communication and improves process visibility. Organizations can quickly convey information and reduce errors by assigning specific colors to different areas, processes, or equipment. For example:
- Use different colored bins to separate various types of materials or components
- Apply colored tape on floors to designate work zones, walkways, or storage areas
- Implement color-coded labels for inventory management and stock rotation
Color-coding systems help employees quickly identify and understand information, leading to faster decision-making and reduced confusion. This technique is particularly useful in fast-paced manufacturing environments where time is of the essence.
Visual Management Tools for Safety Signage and Floor Markings
Safety is paramount in any manufacturing setting, and visual management tools play a crucial role in maintaining a safe work environment. Safety signage and floor markings are essential visual aids that:
- Communicate potential hazards and safety protocols
- Guide traffic flow and designate safe walkways
- Indicate emergency exits and equipment locations
- Highlight areas that require personal protective equipment (PPE)
By implementing comprehensive safety signage and floor markings, organizations can significantly reduce accidents and injuries while promoting a culture of safety awareness among employees.
Shadow Boards as Visual Management Tool(s) for Tool Organization
Shadow boards are an excellent example of visual management tools that contribute to workplace organization and efficiency.
These boards feature outlines or “shadows” of tools, making it easy to identify missing items and ensure everything is in its proper place. Benefits of shadow boards include:
- Reduced time spent searching for tools
- Improved inventory management of equipment
- Enhanced accountability for tool usage and maintenance
- Streamlined workflow and reduced downtime
Shadow boards are particularly effective when combined with the 5S methodology, supporting the “set in order” and “sustain” pillars of this lean manufacturing approach.
Visual Aids in Manufacturing Processes with Visual Management Tools
Visual aids are crucial for optimizing manufacturing processes and enhancing overall productivity. These aids can take various forms, such as:
- Process flow charts displayed at workstations
- Standard operating procedure (SOP) visual guides
- Quality control checkpoints with visual indicators
- Digital displays showing real-time production metrics
By incorporating visual aids throughout the manufacturing process, organizations can:
- Reduce errors and improve product quality
- Facilitate training and onboarding of new employees
- Enhance process visibility and identify bottlenecks
- Support continuous improvement initiatives
Visual aids in manufacturing processes are essential for maintaining consistency, reducing variability, and promoting operational excellence across the entire production line.
Benefits of Visual Management Tools in Lean Operations
Visual management tools play a crucial role in lean operations, offering numerous benefits that enhance overall productivity, reduce errors, improve communication, and streamline workflows. Let’s explore these advantages in detail:
Productivity Enhancement and Error Reduction
Visual management tools significantly boost productivity by making information readily available and easy to understand.
For instance, Kanban boards provide a clear visual representation of work in progress, helping teams identify bottlenecks and optimize their processes. This increased visibility leads to faster decision-making and more efficient resource allocation.
Moreover, visual cues like color-coding systems and shadow boards reduce the likelihood of errors.
When tools and materials have designated places marked by visual indicators, employees are less likely to misplace items or use the wrong components. This error reduction not only saves time but also improves the quality of output.
Andon systems, another vital visual management tool, allow real-time data visualization. When issues arise on the production floor, these systems immediately alert relevant personnel, enabling quick responses and minimizing downtime.
This rapid problem-solving capability directly contributes to enhanced productivity and reduced errors.
Improved Employee Engagement and Communication with Visual Management Tools
Visual management tools foster a culture of transparency and open communication. Metrics dashboards and SQDCP boards (Safety, Quality, Delivery, Cost, and People) display key performance indicators in an easily digestible format.
This visibility into organizational goals and progress helps employees understand their role in the bigger picture, leading to increased engagement and motivation.
Furthermore, visual aids in manufacturing processes, such as process maps and workflow diagrams, facilitate better understanding among team members.
These tools break down complex procedures into simple, visual steps, making it easier for employees to follow standardized processes and communicate effectively about their work.
Kamishibai boards, used for auditing and continuous improvement, encourage regular interaction between management and frontline workers.
This ongoing dialogue not only improves communication but also demonstrates the organization’s commitment to employee input and process improvement.
Streamlined Workflow and Waste Reduction
One of the primary goals of lean operations is to eliminate waste, and visual management tools are instrumental in achieving this objective. Visual process maps help identify non-value-adding activities and inefficiencies in the workflow.
By visualizing the entire process, teams can spot redundancies, unnecessary steps, or potential areas for improvement.
5S methodology, a cornerstone of visual management, focuses on workplace organization and standardization.
By implementing 5S principles (Sort, Set in Order, Shine, Standardize, and Sustain), companies can significantly reduce the time wasted in searching for tools or materials. This organization leads to a more streamlined workflow and increased efficiency.
Floor markings and visual workplace techniques guide the movement of people and materials throughout the facility. These simple yet effective tools minimize unnecessary motion and transportation, two of the eight wastes identified in lean manufacturing.
Improve employee engagement and communication to maximize the benefits of visual management tools.
Best Practices for Implementing Visual Control Systems
Implementing visual control systems is a crucial step in optimizing your lean manufacturing processes and enhancing overall operational excellence. To ensure success, organizations should follow these best practices when adopting visual management tools.
Choosing the Right Visual Management Tool(s) for your Organization
Selecting the appropriate visual management tools is critical for maximizing their effectiveness in your specific work environment. Consider the following factors:
- Assess your needs: Evaluate your current processes and identify areas that could benefit from improved visibility and communication. This will help you determine which visual management tools are most relevant to your organization.
- Start small: Begin with a pilot program using one or two visual management tools in a specific area of your operations. This allows you to test their effectiveness and make adjustments before implementing them across the entire organization.
- Involve stakeholders: Engage employees from various departments in the selection process. Their input can provide valuable insights into which tools will be most useful and easily adopted.
- Consider scalability: Choose visual management tools that can grow and adapt to your organization. Look for solutions that can be easily modified or expanded as your needs change.
- Evaluate compatibility: Ensure that the chosen tools integrate well with your existing systems and processes to avoid disruptions in workflow.
Training Employees on Visual Management Tools and Techniques
Proper training is essential for the successful implementation of visual management tools. Follow these guidelines to ensure your workforce is well-prepared:
- Develop a comprehensive training program: Create a structured curriculum that covers the principles of visual management, the specific tools being implemented, and their role in lean manufacturing systems.
- Provide hands-on experience: Offer practical training sessions where employees can interact with the visual management tools and practice using them in simulated work scenarios.
- Emphasize the benefits: Communicate how visual management techniques can improve productivity, reduce errors, and enhance overall workplace efficiency.
- Tailor training to different roles: Customize training content for various job functions, ensuring that each employee understands how visual management tools apply to their specific responsibilities.
- Encourage peer-to-peer learning: Establish a mentoring system where experienced employees can guide and support their colleagues in adopting visual management practices.
Continuous Evaluation and Improvement of Visual Management Strategies
To maintain the effectiveness of your visual control systems, it’s crucial to regularly assess and refine your visual management strategies:
- Set clear performance indicators: Establish metrics to measure the impact of visual management tools on key areas such as productivity, error rates, and employee engagement.
- Conduct regular audits: Perform periodic evaluations of your visual management systems to ensure they remain relevant and effective.
- Gather employee feedback: Encourage open communication with your workforce to identify areas for improvement and gather suggestions for enhancing visual management practices.
- Stay informed about industry trends: Keep abreast of new developments in visual management tools and techniques to ensure your organization remains competitive.
- Implement continuous improvement cycles: Use methodologies like PDCA (Plan-Do-Check-Act) to systematically refine and optimize your visual management strategies.
- Celebrate successes: Recognize and reward teams and individuals who effectively utilize visual management tools to drive improvements in their work areas.
Emerging Trends in Visual Management Tools
Augmented Reality (AR) Integration
Integrating AR technology with traditional visual management tools is set to revolutionize shop floor operations.
AR-enabled devices can overlay real-time data, instructions, and visual cues directly onto the physical workspace, enhancing process visibility and worker guidance.
For instance, AR glasses could display step-by-step assembly instructions or highlight areas requiring maintenance, significantly reducing errors and improving productivity.
Internet of Things (IoT) Enhanced Visual Controls
The proliferation of IoT devices is enabling more sophisticated and responsive visual management systems.
Smart sensors and connected devices can automatically update visual displays in real time, providing instant feedback on production metrics, equipment status, and environmental conditions.
This level of connectivity allows for more dynamic and accurate visual management, supporting faster decision-making and proactive problem-solving.
AI-Powered Visual Analytics
Artificial Intelligence is transforming how visual data is interpreted and presented. AI algorithms can analyze vast amounts of operational data to identify patterns, predict issues, and suggest optimizations.
These insights can be translated into clear, actionable visual cues on management boards or digital displays, helping teams to focus on the most critical areas for improvement and supporting continuous improvement initiatives.
Personalized Visual Dashboards
As manufacturing processes become more complex, there’s a growing trend towards personalized visual management tools. Customizable digital dashboards allow each worker or team to focus on the metrics and information most relevant to their specific roles, enhancing engagement and efficiency. These personalized views can be accessed across various devices, ensuring that critical information is always at hand.
Role of Technology in Advancing Visual Management Practices
1. Digital Transformation of Traditional Tools
Many traditional visual management tools are being digitized, offering greater flexibility and real-time updates. Digital Kanban boards, for example, can be instantly updated across multiple locations, ensuring all team members have access to the latest workflow information.
Similarly, digital SQDCP boards can provide live updates on safety, quality, delivery, cost, and people metrics, facilitating quicker responses to deviations.
2. Cloud-Based Collaboration
Cloud technology is enabling seamless collaboration and information sharing across different departments and even multiple manufacturing sites.
Visual management tools hosted in the cloud allow for centralized data management and distributed access, supporting consistent practices across the organization and facilitating benchmarking and best practice sharing.
3. Mobile Integration:
The increasing use of mobile devices in manufacturing environments is making visual management more accessible and interactive.
Mobile apps can provide on-the-go access to visual management tools, allowing workers to input data, receive alerts, and view performance metrics from anywhere on the shop floor. This mobility enhances responsiveness and keeps everyone informed in real time.
4. Advanced Data Visualization:
Emerging data visualization technologies are making it easier to represent complex data in intuitive, visual formats. 3D modeling, interactive charts, and heat maps can provide more engaging and informative visual representations of manufacturing processes and performance data.
These advanced visualizations can help in identifying trends, bottlenecks, and improvement opportunities more effectively.
5. Integration with Broader Management Systems:
Visual management tools are increasingly being integrated with broader enterprise management systems, such as ERP (Enterprise Resource Planning) and MES (Manufacturing Execution Systems).
This integration allows for a more holistic view of operations, connecting shop floor activities with broader business objectives and facilitating more aligned decision-making across the organization.
SixSigma.us offers both Live Virtual classes as well as Online Self-Paced training. Most option includes access to the same great Master Black Belt instructors that teach our World Class in-person sessions. Sign-up today!
Virtual Classroom Training Programs Self-Paced Online Training Programs