Level Loading: Unlocking Efficiency with Lean Production Leveling
For companies constantly seeking to streamline operations and boost efficiency, level loading has become an important principle.
Also known as production leveling or heijunka, this concept revolutionized manufacturing approaches after taking hold in Toyota’s groundbreaking system.
Level loading aims to cut unevenness or variation in output, reducing waste and bettering performance overall.
Generating intermediate goods at an even pace ensures subsequent processing can also occur consistently and predictably.
This contrasts with typical batching where demand swings often induce periods of surplus stock or clogged pipelines.
Applicable across industries from manufacturing to sectors like healthcare and hospitality, level-loading strategies afford meaningful perks when implemented.
These include lower inventory holding costs, smoother cash flow, enhanced flexibility, and happier customers through steadier production flow and lead times.
As a proven approach, it demonstrates how streamlining operations through principles honed by Toyota bolsters performance.
Key Highlights
- Level loading, also known as production leveling or heijunka, is a fundamental principle of lean manufacturing and the Toyota Production System.
- It focuses on reducing variation (mura) in production processes, thereby eliminating waste (muda) and improving overall efficiency.
- Level loading involves producing intermediate goods at a constant rate to enable a smooth and predictable flow of subsequent processing steps.
- There are two primary approaches to level loading: volume leveling and product leveling, each with its strategies and techniques.
- Its implementation can lead to significant benefits, including reduced inventory levels, improved cash flow, enhanced flexibility, and increased customer satisfaction.
- Level loading principles are widely applicable across various industries, from manufacturing to service sectors like healthcare, hospitality, and construction.
- Successful implementation requires overcoming challenges such as cultural resistance, supply chain integration, and potential technical limitations.
- Continuous improvement through methods like setup reduction, continuous flow, and the Kaizen approach is essential for sustaining the benefits of level loading.
- Emerging trends and technologies present opportunities for further optimizing level loading strategies and streamlining operations.
What is Level Loading?
Level loading, also known as production leveling or heijunka in Japanese, is a fundamental concept in lean manufacturing that aims to reduce unevenness or variation (mura) in production processes, thereby eliminating waste (muda).
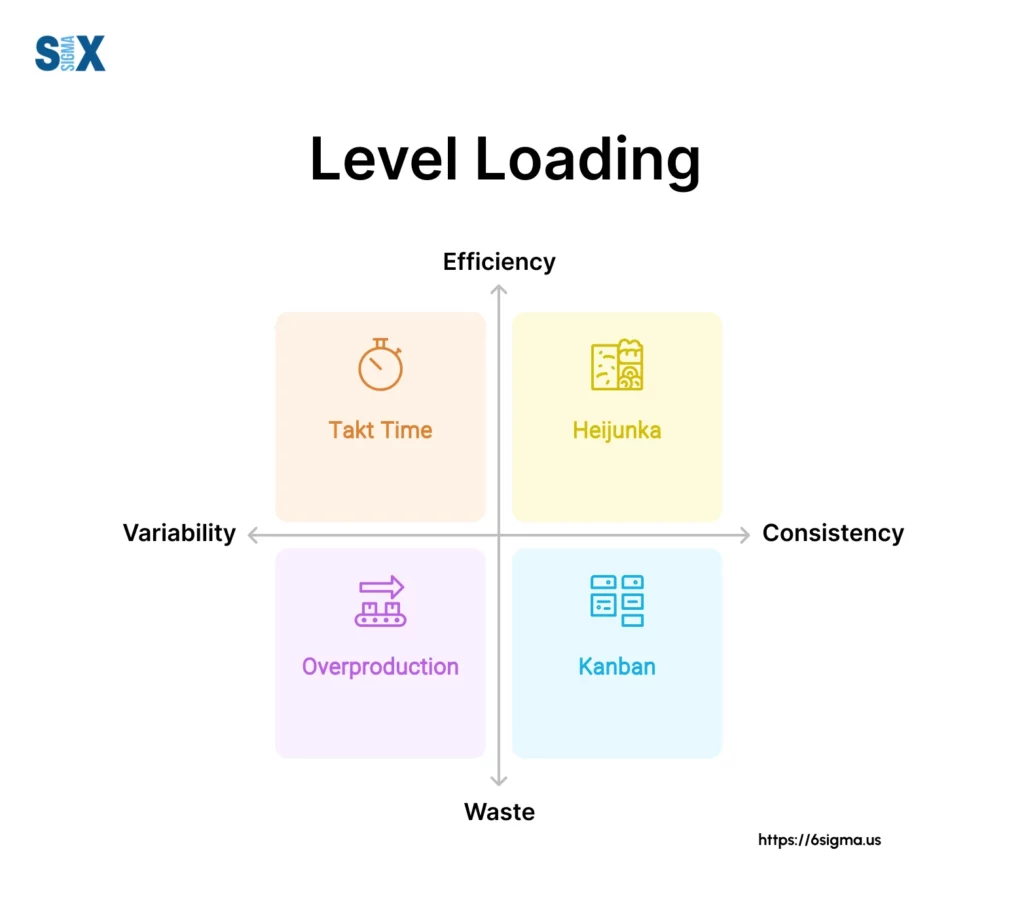
It involves producing intermediate goods at a constant rate, ensuring a smooth and predictable flow of subsequent processing steps.
The importance of level loading lies in its ability to eliminate waste and variation, two key sources of inefficiency in manufacturing operations.
By producing at a consistent pace, level loading helps prevent excessive inventory buildup or production bottlenecks, both of which can lead to increased costs, longer lead times, and decreased customer satisfaction.
Level loading played a vital role in the development of the Toyota Production System, the pioneering approach to lean manufacturing that has since been adopted by companies worldwide.
By implementing level loading principles, Toyota was able to achieve remarkable improvements in production efficiency, quality, and responsiveness to customer demand.
Approaches to Level Loading
There are two primary approaches to level loading: volume leveling and product leveling.
Volume leveling involves producing a family of products that go through the same process steps at a constant rate, based on the long-term average demand.
This approach helps manage fluctuations in demand by carrying a controlled level of inventory, ensuring stability in production processes and timely shipments.
Product leveling, on the other hand, focuses on reducing the time required for changeovers between different product lines or models.
By minimizing changeover times, companies can produce smaller batches more efficiently, enabling them to level the demand for components across the entire value stream and reduce lead times and total inventory levels.
A common tool used in level loading is the heijunka box, a visual scheduling aid that displays the planned production sequence and volumes for a specific period.
This visual representation helps ensure that production remains level-loaded and aligned with customer demand.
Benefits of Level Loading
Waste Reduction
One of the primary benefits of level loading is its ability to reduce waste in various forms:
- Inventory management: By producing at a constant rate based on average demand, level loading helps minimize excessive inventory buildup, reducing carrying costs and freeing up valuable space and resources.
- Reduced changeover times: Product leveling techniques, such as minimizing changeover times, enable more efficient production of smaller batches, reducing the need for large inventory buffers.
- Improved process cycle time: A level-loaded system with a consistent flow of work can significantly reduce process cycle times, leading to faster throughput and improved responsiveness to customer demand.
Improved Efficiency with Level Loading
Level loading contributes to improved efficiency in several ways:
- One-piece flow: By reducing batch sizes and enabling a continuous flow of work, this brings operations closer to the ideal of one-piece flow, where each unit is processed without interruption or waiting time.
- Takt time: Allowing for the establishment of a consistent takt time (the rate at which products must be completed to meet customer demand), enabling better synchronization of production processes.
- Value stream mapping: The principles are essential for effective value stream mapping, which helps identify and eliminate non-value-added activities, further improving efficiency.
Financial Gains
The efficiency gains and waste reduction achieved through level loading translate into significant financial benefits:
- Reduced work in progress (WIP): By minimizing inventory levels and ensuring a smooth flow of work, it reduces the amount of capital tied up in work in progress, improving cash flow.
- Improved cash flow: Lower inventory carrying costs and faster product throughput positively impact cash flow, providing companies with greater financial flexibility.
- Flexibility to meet demand: A level-loaded system can respond more quickly to changes in customer demand, reducing the need for costly expediting or overtime measures.
Implementing Level Loading
Demand Leveling Techniques
While the focus is primarily on the production side, effective demand leveling strategies can further enhance its benefits:
- Sales pipeline management: By carefully managing the sales pipeline and building customer relationships, companies can better predict and level out demand patterns.
- Economic order quantity (EOQ) analysis: Understanding the ordering processes and economic order quantities used by retailers and customers can reveal demand variability caused by these processes, enabling corrective actions.
- Finished goods inventory management: Maintaining a strategic level of finished goods inventory can help buffer against demand fluctuations, allowing for a more level-loaded production system.
Production Leveling Strategies
On the production side, several strategies can be employed to achieve level loading:
- Fixed repeating schedule: This approach involves producing a mix of products in small batches according to a fixed, repeating schedule, ensuring a consistent flow of work.
- Volume leveling: As discussed earlier, volume leveling involves producing at the long-term average demand rate and carrying a controlled level of inventory to manage demand variability.
- Product leveling: By reducing changeover times and enabling smaller batch sizes, product leveling allows for a more flexible production mix and better alignment with customer demand.
Continuous Improvement with Level Loading
Successful implementation requires a continuous improvement mindset:
- Setup reduction: Ongoing efforts to reduce changeover times can further enhance the benefits of product leveling and enable even smaller batch sizes.
- Continuous flow: Continuously striving for a true one-piece flow, where each unit is processed without interruption, is a key goal of level loading.
- Kaizen approach: Embracing the Kaizen philosophy of continuous improvement, involving all employees in identifying and eliminating waste and inefficiencies, is essential for sustaining the benefits.
Level Loading in Service Industries
While level loading originated in manufacturing, its principles have proven valuable in various service industries as well.
Healthcare
- Patient flow management: These techniques can be applied to optimize patient flow in healthcare facilities, ensuring a consistent and efficient delivery of care.
- Appointment scheduling: By leveling the scheduling of appointments, healthcare providers can better manage resource allocation and reduce wait times for patients.
Hospitality
- Restaurant order management: It can help restaurants streamline their order processing and food preparation, improving efficiency and reducing customer wait times.
- Hotel room availability: By level-loading room availability and reservations, hotels can better manage their inventory and provide a more consistent level of service.
Construction
- Project scheduling: These principles can be applied to construction project scheduling, ensuring a consistent flow of work and optimizing resource allocation.
- Resource allocation: By leveling the demand for various resources (materials, equipment, labor), construction companies can improve efficiency and reduce downtime.
Challenges and Considerations of Level Loading
Cultural Resistance
The implementing often requires a significant cultural shift within an organization:
- Transitioning from traditional batch production: Moving away from the mindset of producing large batches to meet demand can be challenging, as it requires a different approach to planning and execution.
- Mindset shift towards continuous flow: Embracing the concept of continuous flow and minimizing interruptions in production can be a cultural hurdle, especially in industries accustomed to batch processing.
Supply Chain Integration
Effective level loading requires close integration and collaboration with suppliers and customers:
- Aligning with suppliers and customers: The efforts must be coordinated with suppliers to ensure a smooth flow of materials and components, as well as with customers to align production with demand.
- Information sharing and collaboration: Transparent communication and data sharing across the supply chain are essential for successful implementation and demand leveling.
Technical Limitations
In some cases, technical limitations may hinder the full implementation of these strategies:
- Equipment constraints: Certain production equipment or processes may not be easily adaptable, requiring careful evaluation and potential modifications or replacements.
- Process complexity: Highly complex or customized production processes can make it more challenging, necessitating creative solutions or compromises.
Conclusion
Level loading, or production leveling, is fundamental to lean manufacturing and transformed process enhancement approaches.
By generating stable output and minimizing variations, it facilitates smooth workflow, higher efficiency, lower stockpiles, and more flexibility financially.
Its benefits extend far beyond manufacturing too – it applies to sectors like healthcare, hospitality, and construction.
Still, proper implementation means overcoming cultural inertia, integrating supply chains thoughtfully, and addressing technical capability barriers.
As lean principles spread worldwide, it adoption will likely spread across industries too.
Emerging technologies present exciting optimization options – analytics, IoT, and Industry 4.0 solutions could streamline operations further.
Companies embracing this in their lean journey will be best poised to elevate competitiveness and customer satisfaction.
They can catalyze long-term success, even amid ever-changing demands. By reducing waste in an innovative yet proven manner, level loading demonstrates lean thinking’s power for performance progress.
SixSigma.us offers both Live Virtual classes as well as Online Self-Paced training. Most option includes access to the same great Master Black Belt instructors that teach our World Class in-person sessions. Sign-up today!
Virtual Classroom Training Programs Self-Paced Online Training Programs