Lean and Agile Manufacturing: Guide to Modern Production Methodologies
Modern manufacturers face unprecedented challenges, from supply chain disruptions to rapidly changing customer demands.
The integration of lean and agile manufacturing principles helps organizations navigate these challenges effectively.
This combination enables manufacturers to maintain efficient operations while quickly adapting to market shifts and technological advancements.
Key Highlights
- Fundamental principles driving lean and agile methodologies
- Strategic implementation steps for both approaches
- Digital integration techniques and Industry 4.0
- Performance measurement and optimization methods
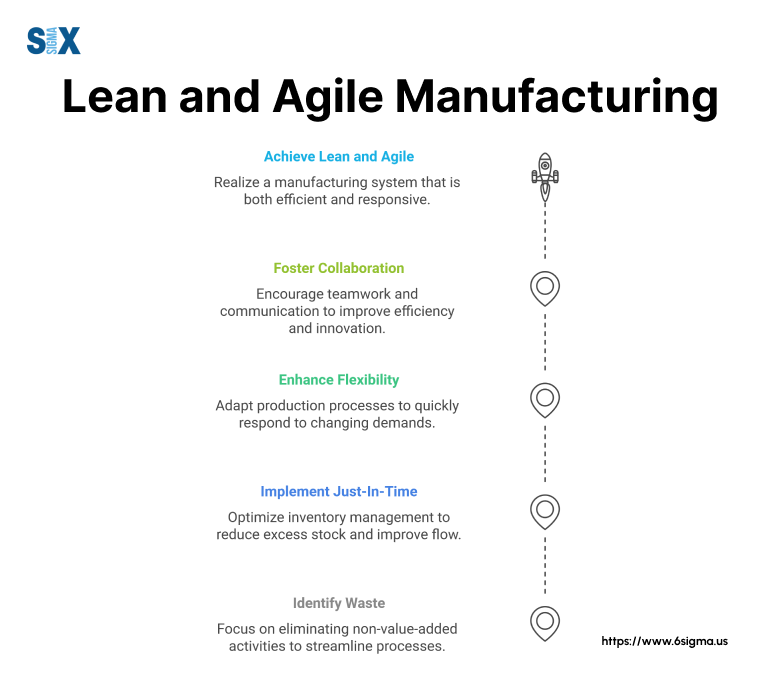
Lean and Agile Manufacturing
The story of lean manufacturing began in post-World War II Japan, specifically within Toyota’s production facilities.
In 1948, Toyota faced significant challenges: limited resources, fierce competition, and the need for efficient production methods. Taiichi Ohno, a Toyota executive, developed the Toyota Production System (TPS), which later became known as lean manufacturing.
This system revolutionized production by focusing on waste elimination and continuous improvement.
Throughout the 1970s and 1980s, Western manufacturers studied Toyota’s success, leading to the widespread adoption of lean production and agile manufacturing principles.
The publication of “The Machine That Changed the World” in 1990 marked a turning point, introducing lean manufacturing concepts to a global audience.
The Rise of Agile Methodology
Agile methodology emerged from a different sector entirely – software development. In 2001, seventeen software developers met in Snowbird, Utah, creating the Agile Manifesto.
While initially focused on software development, the principles quickly spread to manufacturing sectors. The methodology emphasized flexibility, customer collaboration, and rapid response to change.
Manufacturing companies began adopting agile principles in the mid-2000s, recognizing the need for faster response times to market changes and customer demands.
The Merger of Manufacturing Philosophies
The convergence of lean production and agile manufacturing began in the late 2000s.
Organizations realized that combining both methodologies could create more resilient manufacturing systems.
This merger gained momentum during the 2008 financial crisis, as manufacturers sought ways to maintain efficiency while increasing adaptability.
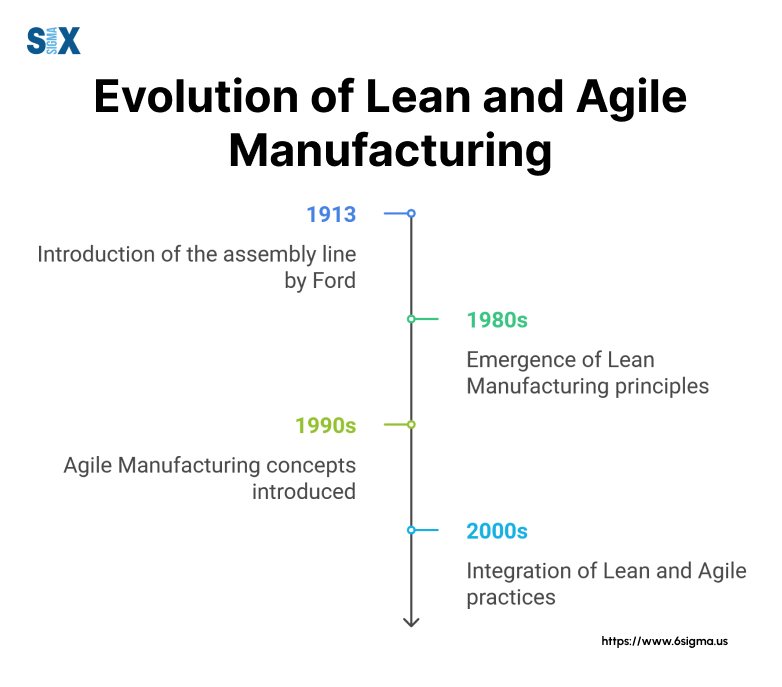
Core Principles That Drive Modern Manufacturing
Lean manufacturing centers on five fundamental principles that guide production processes.
Value definition forms the foundation, requiring manufacturers to identify what customers truly value in their products.
Value stream mapping follows, enabling teams to track each step in the production process and eliminate non-value-adding activities.
The principle of flow optimization ensures smooth production movement without bottlenecks or delays.
Key Agile Manufacturing Principles
Agile manufacturing principles focus on rapid response and adaptability in production systems.
Customer collaboration stands as a primary principle, emphasizing direct engagement throughout the production process.
Cross-functional teams work together, breaking down traditional departmental silos to speed up decision-making and implementation.
Quick iteration cycles enable fast product development and refinement based on real-time feedback.
The principle of flexible production systems allows manufacturers to adjust output quickly based on market demands.
Employee empowerment encourages workers at all levels to contribute ideas and solutions for process improvement.
Implement agile manufacturing principles with Lean Introduction course covering both manufacturing and service-based applications.
Where Lean and Agile Manufacturing Principles Meet
Both lean and agile principles share several common elements in their approach to manufacturing excellence.
Waste reduction remains central to both methodologies, though they define and address it differently. Customer focus drives decision-making in both systems, with an emphasis on delivering maximum value.
Quality management plays a crucial role in both approaches, though lean emphasizes built-in quality while agile focuses on iterative improvement.
Team empowerment and continuous learning represent shared values, promoting employee engagement and organizational growth.
Distinct Approaches to Manufacturing Success
Despite their similarities, these manufacturing methodologies maintain distinct characteristics.
Lean principles prioritize stability and standardization, while agile principles emphasize flexibility and rapid change.
Production planning differs significantly: lean follows strict scheduling while agile adapts more frequently to market changes.
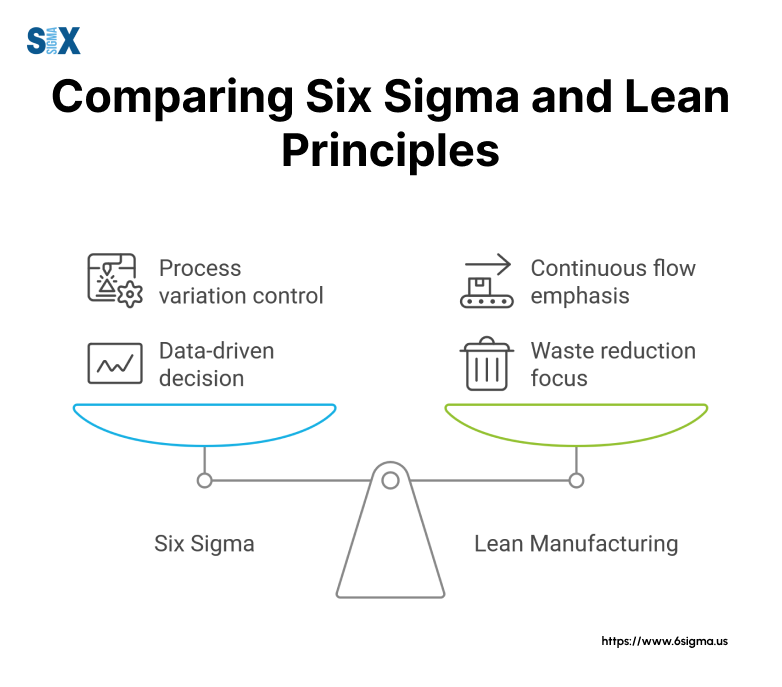
Master the essential principles of Lean Manufacturing with Lean Fundamentals
Analyzing the Differences Between Lean and Agile Manufacturing
The difference between lean and agile manufacturing becomes evident in their primary objectives.
Lean manufacturing targets waste elimination and process optimization, measuring success through reduced production costs and improved efficiency.
In contrast, agile manufacturing prioritizes rapid response to market changes and customer demands, gauging success by adaptation speed and customer satisfaction levels.
Process Focus and Implementation
Lean manufacturing emphasizes standardized processes and consistent workflows. Production lines follow carefully mapped value streams, with each step precisely defined and monitored.
Quality checks occur throughout the process, ensuring defects get caught early.
Agile manufacturing takes a more flexible approach to processes. Teams work in shorter production cycles, allowing for quick adjustments based on feedback.
This methodology enables manufacturers to modify production plans rapidly, responding to changing market conditions or customer requirements.
Flexibility Versus Stability b/w Lean and Agile Manufacturing
When comparing lean versus agile manufacturing approaches, their handling of change reveals key distinctions.
Lean systems prefer stability and predictability, implementing changes through structured continuous improvement programs.
These changes typically occur gradually, with careful consideration of their impact on the entire production system.
Agile systems embrace change as a constant factor, building flexibility into every aspect of production. Equipment layouts, worker training, and supply chain relationships all support rapid reconfiguration.
This adaptability allows manufacturers to switch products or adjust production volumes quickly.
Customer Value Creation
Both methodologies prioritize customer value but approach it differently. Lean manufacturing focuses on delivering consistent quality while eliminating costs that customers won’t pay for.
This approach results in streamlined processes that reliably produce high-quality products at competitive prices.
Agile manufacturing emphasizes customization and rapid response to customer needs. The focus stays on quick delivery of exactly what customers want, even if production costs slightly higher.
This approach particularly suits markets where customer preferences change frequently.
Waste Reduction Approaches
Lean manufacturing identifies and eliminates eight specific types of waste: transportation, inventory, motion, waiting, overproduction, over-processing, defects, and unused talent.
Each waste category receives systematic attention through specific tools and techniques.
Agile manufacturing views waste differently, focusing primarily on time waste and missed market opportunities.
This approach considers excess inventory or unused capacity as potential resources for responding to sudden market changes rather than pure waste.
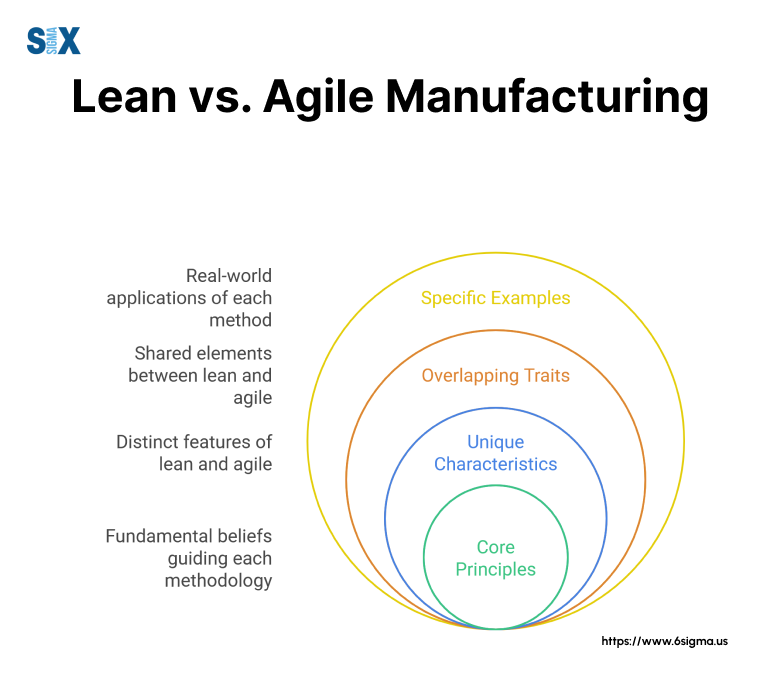
Implementing Lean and Agile Methodologies in Manufacturing
Successful lean and agile methodologies implementation begins with thorough value stream mapping. Organizations must first identify current processes, highlighting areas of waste and inefficiency.
Team training follows, ensuring all staff members understand lean principles and their roles in the transformation process.
The next phase involves establishing standardized work procedures. These procedures create baseline operations from which improvements can be measured and implemented.
Visual management systems get deployed throughout the facility, making process status and problems immediately visible to all team members.
Agile Implementation Framework
Agile methodology implementation starts with creating cross-functional teams and establishing clear communication channels.
These teams receive authority to make quick decisions, enabling rapid response to changes in production requirements or market demands.
Short production cycles, typically lasting two to four weeks, allow for regular evaluation and adjustment of processes.
Each cycle ends with a review session where teams assess performance and identify areas for improvement.
This iterative approach enables continuous refinement of manufacturing processes while maintaining production flexibility.
Building a Hybrid Manufacturing System with Lean and Agile Manufacturing
Many organizations find success by combining lean and agile manufacturing approaches.
This hybrid system starts with implementing lean principles for stable, repetitive processes while incorporating agile methods for areas requiring greater flexibility.
The integration process requires careful planning and clear guidelines for when to apply each methodology.
Production areas with predictable demand benefit from lean practices, while departments handling custom orders or rapid product changes adopt agile principles.
Technology Integration for Modern Manufacturing
Digital tools play a crucial role in implementing both methodologies.
Manufacturing execution systems track and analyze production data, while real-time monitoring enables quick problem identification and resolution.
These technologies support both the precision of lean manufacturing and the flexibility of agile approaches.
Measuring Implementation Success in Lean and Agile Manufacturing
Regular performance measurement ensures successful implementation of both methodologies.
Key metrics include production efficiency, response time to changes, quality levels, and customer satisfaction scores.
These measurements help teams adjust their approach and maintain continuous improvement cycles.
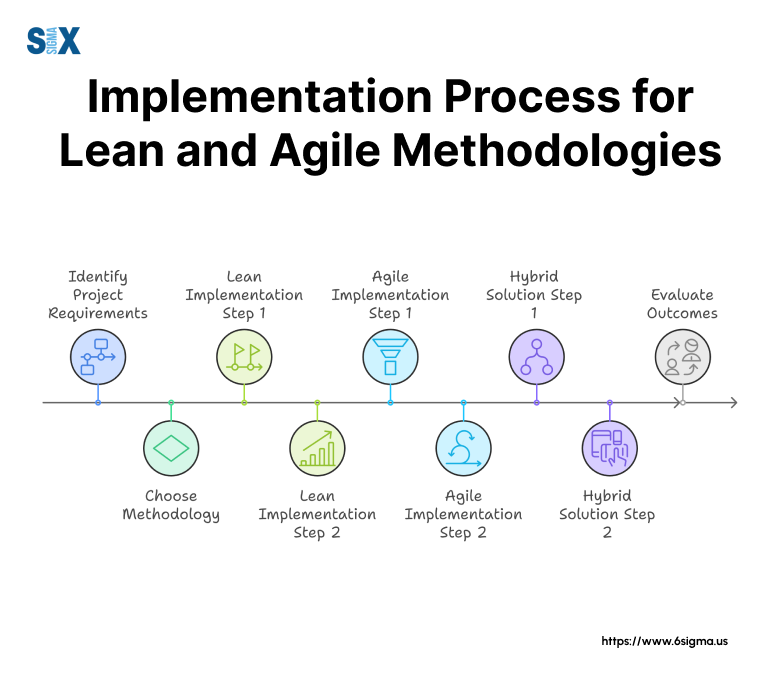
Digital Technologies Reshaping Manufacturing Systems
Digital transformation has revolutionized lean and agile manufacturing systems through advanced technology integration.
Smart sensors now monitor production lines in real-time, enabling immediate detection of process variations and quality issues.
These technological advances support both lean principles of waste reduction and agile requirements for rapid response to changes.
IoT and Analytics Driving Production Excellence
The Internet of Things (IoT) has transformed how manufacturers collect and utilize data.
Connected devices throughout the production floor generate continuous streams of operational data, offering unprecedented insights into manufacturing processes.
This data feeds advanced analytics systems, which identify patterns and predict potential issues before they impact production.
Predictive maintenance programs, powered by machine learning algorithms, analyze equipment performance data to schedule maintenance activities optimally.
This approach reduces unexpected downtime while extending equipment life, supporting both lean efficiency goals and agile flexibility requirements.
Automation and Robotics Evolution with Lean and Agile Manufacturing
Modern robotics systems bring new capabilities to lean and agile manufacturing environments. Collaborative robots work alongside human operators, handling repetitive tasks while allowing workers to focus on more complex activities.
These systems adapt quickly to different production requirements, supporting both standardized lean processes and agile manufacturing needs.
Automated guided vehicles (AGVs) revolutionize material movement within facilities, optimizing logistics flows and reducing transportation waste.
These systems integrate with inventory management software, ensuring materials arrive at workstations exactly when needed, supporting just-in-time production principles.
Measuring Success in Modern Manufacturing Systems
Lean and agile project management success relies heavily on specific performance indicators.
For lean operations, Overall Equipment Effectiveness (OEE) measures equipment productivity by combining availability, performance, and quality metrics.
First-pass yield tracks the percentage of products manufactured correctly without rework, directly indicating process efficiency.
Cycle time reduction serves as another crucial metric, measuring the time from production start to completion.
Inventory turnover rates reveal how effectively materials flow through the manufacturing process, while defect rates provide clear indicators of quality control effectiveness.
Critical Agile Performance Indicators
Agile manufacturing metrics focus on flexibility and response capabilities. Lead time to market measures how quickly new products move from concept to production.
Customer response time tracks the speed of adapting to changing requirements or specifications.
Resource utilization flexibility indicates how efficiently teams reallocate resources to meet shifting demands.
Sprint completion rates show how effectively manufacturing teams meet short-term production goals, while customer satisfaction scores reflect the success of agile responses to market needs.
ROI Calculation Methods b/w Lean and Agile Manufacturing
Return on investment calculations for lean and agile project management require both quantitative and qualitative analysis.
Direct cost savings from waste reduction and efficiency improvements provide immediate financial metrics.
Decreased inventory carrying costs and reduced quality-related expenses contribute to the overall financial impact.
Long-term benefits include increased market share from improved customer satisfaction and faster response to market changes.
Employee retention rates and reduced training costs often improve due to standardized processes and clear performance expectations.
Integrated Performance Management
Modern manufacturing environments benefit from combining lean and agile metrics in unified dashboards.
Real-time monitoring systems track both efficiency metrics and flexibility indicators simultaneously.
This integrated approach enables managers to balance stable operations with rapid response capabilities effectively.
Overcoming Manufacturing Transformation Challenges
The difference between agile and lean manufacturing implementation becomes evident when examining typical challenges.
Resource allocation often presents the first major hurdle, as organizations struggle to balance daily operations with transformation initiatives.
Budget constraints frequently limit the adoption of necessary technologies and training programs.
Technical infrastructure gaps pose significant challenges, particularly when existing systems lack the capability to support new methodologies.
Organizations often find their legacy systems incompatible with modern manufacturing requirements, necessitating substantial upgrades or replacements.
Managing Resistance to Change
Employee resistance typically emerges from concerns about job security and changing role requirements.
Middle management often shows reluctance due to perceived loss of control or authority in more flexible organizational structures.
This resistance can slow implementation progress and reduce the effectiveness of new manufacturing approaches.
Leadership misalignment creates additional complications when different departments maintain varying levels of commitment to transformation initiatives.
This misalignment often results in inconsistent implementation and reduced overall effectiveness of both lean and agile manufacturing practices.
Strategic Solutions for Success
Successful implementation requires clear communication strategies that address stakeholder concerns directly.
Regular training sessions help employees understand the benefits of new methodologies while developing necessary skills.
Pilot programs demonstrate success on a smaller scale, building confidence in the transformation process.
Change management programs should focus on creating visible wins early in the implementation process.
These early successes help build momentum and reduce resistance to further changes. Regular feedback sessions enable teams to voice concerns and contribute improvement suggestions.
Building Sustainable Change
Long-term success depends on establishing robust support systems and maintaining consistent leadership commitment.
Regular assessment and adjustment of implementation strategies ensure continued progress toward manufacturing goals. Documentation of successful practices helps standardize approaches across different departments and facilities.
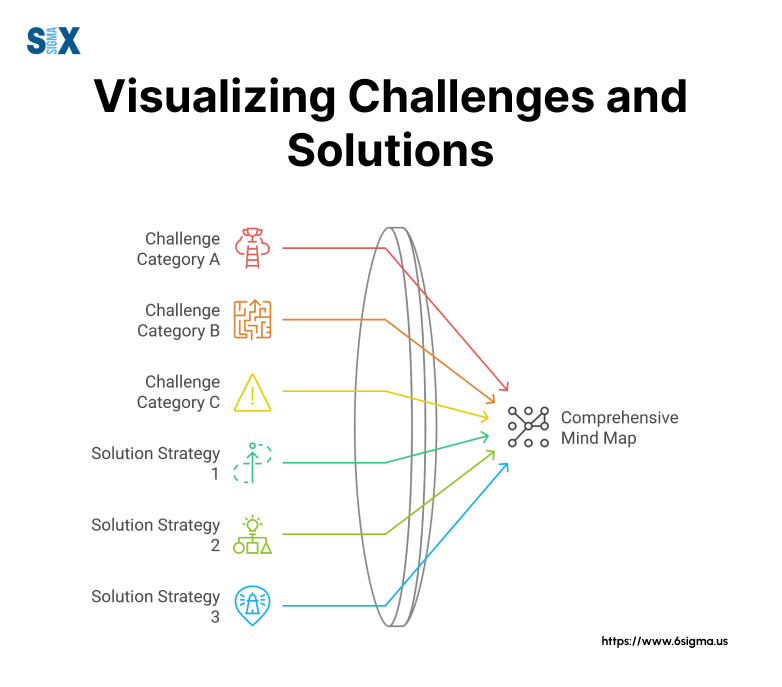
Build a Robust Foundation in both Lean and Agile Methodologies with Lean Fundamentals
Moving Forward
Lean and agile manufacturing methodologies have proven their value in today’s dynamic manufacturing environment.
The integration of these approaches enables organizations to maintain efficient operations while responding quickly to market changes.
Digital transformation continues to enhance both methodologies, providing new tools for implementation and measurement.
The Manufacturing Horizon
Manufacturing excellence now demands a balanced approach combining lean efficiency with agile responsiveness.
Industry 4.0 technologies will further enhance these methodologies through advanced analytics, artificial intelligence, and connected systems.
Sustainability requirements will shape future implementations, driving innovations in waste reduction and resource optimization.
Taking Action Today
Organizations must evaluate their current manufacturing processes against modern best practices.
This assessment should consider both immediate efficiency needs and long-term flexibility requirements.
Success requires commitment from leadership, engagement from employees, and investment in supporting technologies.
Manufacturing leaders should begin by identifying specific areas where lean and agile principles can deliver immediate value.
Starting with pilot projects allows organizations to build expertise while demonstrating concrete benefits.
These initial successes create momentum for broader transformation efforts, leading to sustained manufacturing excellence.
SixSigma.us offers both Live Virtual classes as well as Online Self-Paced training. Most option includes access to the same great Master Black Belt instructors that teach our World Class in-person sessions. Sign-up today!
Virtual Classroom Training Programs Self-Paced Online Training Programs