A Complete Guide to Poka-Yoke in Six Sigma
Quality management philosophies like Six Sigma and Lean Manufacturing aim to achieve near-perfect processes that have minimal waste, maximum efficiency, and high customer satisfaction.
A key tool for accomplishing these goals is poka-yoke, a concept pioneered by Toyota Production System pioneer Shigeo Shingo in the 1960s.
Want to learn error prevention strategies directly from Toyota’s pioneering methods?
Master Mistake-Proofing Techniques from the Toyota Production System
Poka-yoke, which translates from Japanese as “mistake-proofing”, refers to techniques for preventing defects by designing processes that make errors nearly impossible to commit.
As engineer Shingo realized, rather than blaming workers for inevitable human mistakes, better results come faster from changing systems to guide actions correctly.
Applied as part of continuous improvement initiatives like Six Sigma and Lean, poka-yoke enables identifying root causes of problems and empowers frontline workers to fix issues as they arise.
This mistake-proofing culture increases quality and productivity gains over time across the organization. There are many benefits like a 20% improvement in customer satisfaction with successful implementation.
Origins and History of Poka Yoke
The concept of poka-yoke originated in the manufacturing plants of Toyota in Japan during the 1960s. Industrial engineer Shigeo Shingo, a pioneer of lean production methods at Toyota, first introduced mistake-proofing while observing an assembly process where workers commonly forgot to install a part.
Seeing blame targeted at individuals as an ineffective solution, Shingo developed the countermeasure of using simple mechanisms to guide the process and either prevent errors or make them instantly visible.
This evolved from an earlier term Shingo coined called “baka-yoke” – Japanese for “foolproofing” or “idiot-proofing” – shifting the focus to eliminating defects from the process rather than the person.
As Toyota’s methods attracted global attention, particularly through concepts like Just-In-Time production, Shingo’s approach to error-proofing processes became known as poka-yoke.
Translating as “mistake-proofing” or “avoid inadvertent errors,” poka-yoke formed a key component of the celebrated Toyota Production System (TPS), along with methodologies like 5S workplace organization, quick changeovers, and built-in quality practices.
In addition to TPS, poka-yoke now stands today as a foundational pillar across process excellence frameworks like Lean and Six Sigma.
Applying poka-yoke enables organizations to prevent defects, reduce waste, lower costs, and improve efficiency – all central aims of continuous improvement programs.
It empowers designing systems and work methods that guide proper performance each time.
Implementing Poka Yoke in Six Sigma
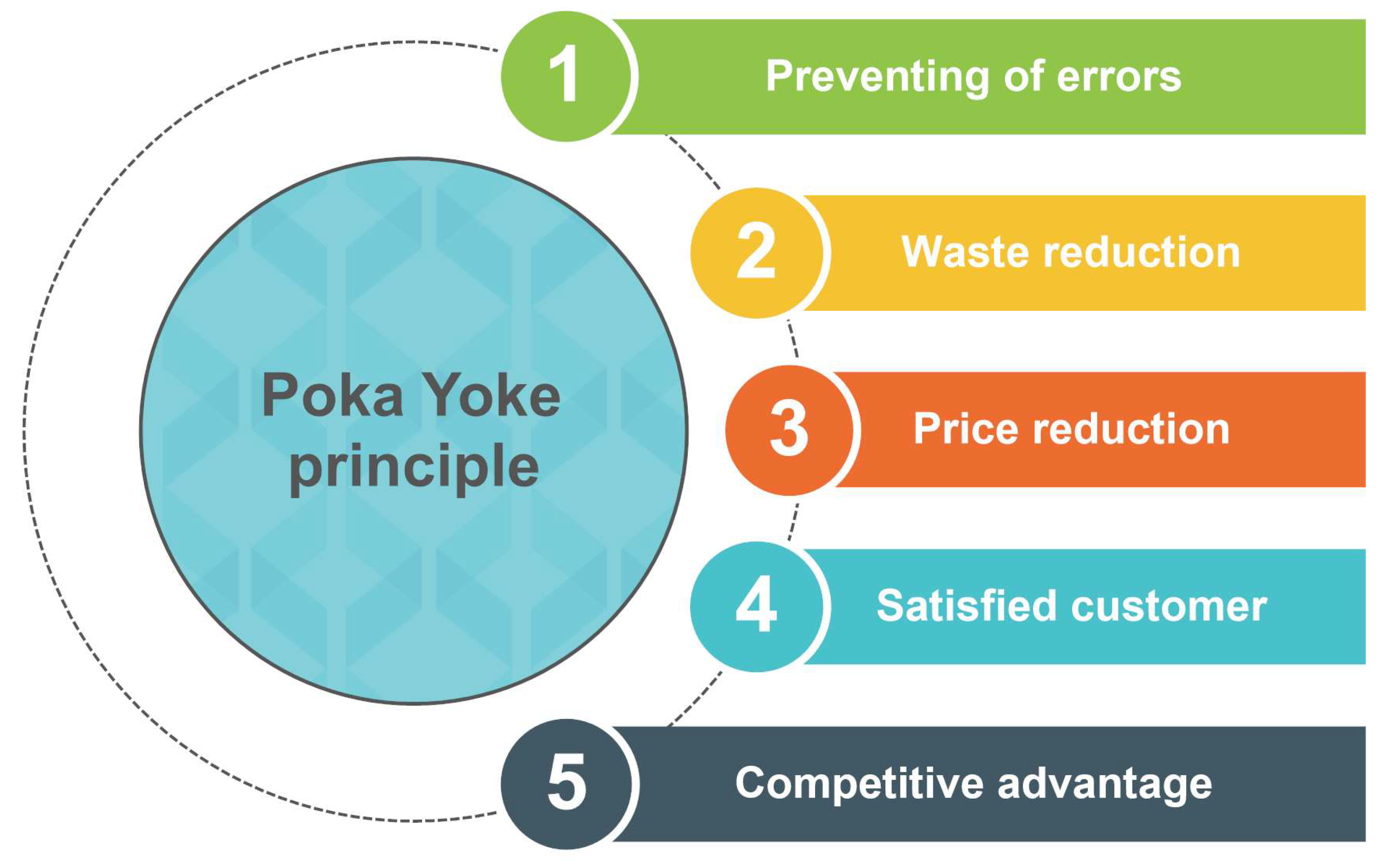
Applying poka-yoke entails redesigning processes to reduce variation from human error and make the desired outcome inevitable.
Shigeo Shingo outlined a five-step methodology for instilling mistake-proofing:
Step 1: Identify Critical Defects and Root Causes
The starting point targets pinpointing high-priority defects to eliminate – ones resulting in costly quality issues, rework, delays, or safety risks.
By asking “why” five times (a Lean tool called 5 Whys analysis), teams uncover root causes and prioritize addressing ones linked to human mistakes. Process mapping provides visualization of each step.
Step 2: Redesign Process to Avoid Identified Errors
In the improvement phase, redesign the process to remove steps where errors originate and introduce mechanisms that cue proper performance.
This guides operators, equipment, and materials to the correct work sequence and outcome. Consider potential failure modes when developing countermeasures.
Step 3: Incorporate Controls and Alerts
Insert visual indicators, alarms, system logic, hardware mechanisms, operational sequences, or structured procedures that either prevent errors or instantly alert that one occurred.
This makes problems visible for quick intervention versus hidden defects detected only later downstream.
Step 4: Validate Proof of Concept
Conduct testing to confirm the integrated mistake-proofing features reliably halt or warn of attempts to vary from set parameters across expected conditions.
Refine limits or operations until attaining robustness.
Step 5: Expand Implementation
With confidence in the effectiveness of critical defects, broaden the mistake-proofing controls across applicable processes to widen the impact.
Continual improvement fosters upgrading standards over generations.
When performed diligently, poka-yoke system redesigns significantly increase productivity, reduce waste, lower costs, and sustain gains.
Embedded error prevention empowers people to achieve high quality reliably.
Types of Poka Yoke in Six Sigma
poka-yoke mechanisms fall into two main categories: control types that automatically stop the process when an error occurs, and warning types that detect the error but rely on the operator to initiate correction.
Within these two branches, several methods apply for preventing mistakes.
Control Poka-Yoke
Control poka-yoke automatically interrupts the process when it encounters something wrong, not allowing progress until the defect gets corrected.
This acts as foolproof prevention by making errors impossible within the designed specifications.
Some examples include:
- The assembly line shuts down if a part gets skipped
- Transaction voids if required data fields get omitted
- System locked if test performed out of sequence
The process cannot proceed until fixing the flagged issue, forcing errors to the surface.
Warning Poka-Yoke
Warning poka-yoke detects an error but relies on the operator to initiate correction before allowing the process to continue. Warning signals commonly use visual or audible alerts.
Examples involve:
- The dashboard light indicates a low fluid level
- Alarm sounds for uncovered manhole
- Email notification of order discrepancy
While less foolproof than control methods, warning poka-yoke still exposes errors that may otherwise go unnoticed until creating downstream defects.
Input Checking
Input checking validates that information entered into a system matches predetermined criteria, preventing entry errors upfront. Common applications include:
- Data field validation for date formats, text lengths, and numeric ranges
- Testing user credentials before system access
- Product codes checked against an approved list
- Automatic prompts for missing entries
Successive Checking
Successive checking performs incremental audits between process steps to verify acceptable outcomes before further work gets based on faulty results.
This regulates quality closer to the source by not allowing deviations to propagate. Examples include:
- Inspection of welds before assembly
- Code reviews before software release
- Approving batch records before distribution
Applying input checking and successive checking facilitates early detection at critical control points.
Tools and Techniques
Implementing effective poka-yoke integrates well with common Lean and Six Sigma tools for process analysis and improvement. According to the Aberdeen Group, implementing poka-yoke techniques had a 25% increase in productivity.
In particular, the following methods help uncover where and why mistakes occur to guide mistake-proofing:
Process Mapping
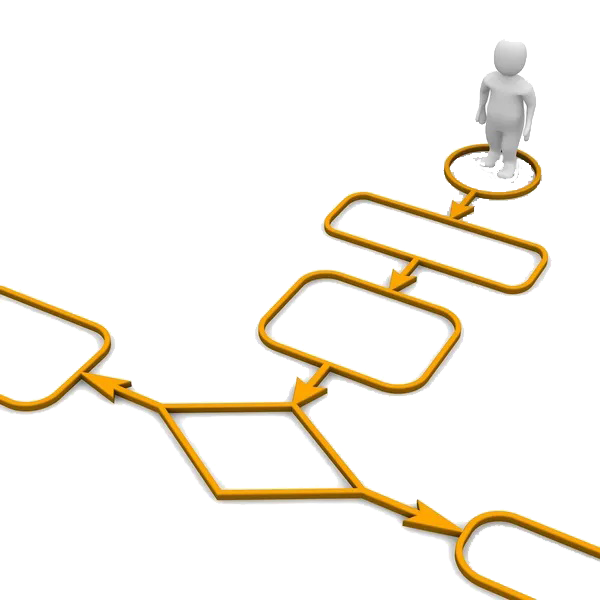
Process mapping provides visualization of all actions in their true sequence, forming the backbone for exploring defects and enhancements.
Tracking cycle times, decision points, inputs, and outputs builds in-depth understanding.
Five Whys Analysis
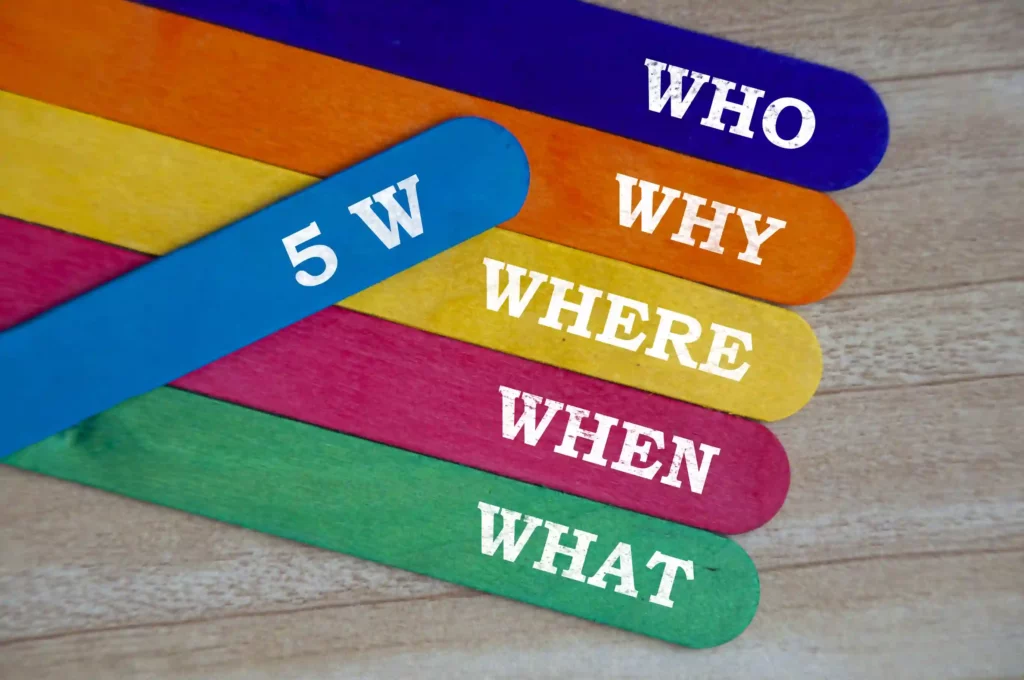
By iteratively asking “why” defects arise, the Five Whys analysis, a technique covered in our root cause analysis training program, penetrates beyond symptoms to reveal root causes.
Posing the question five times unlocks causal relationships obscured by assumptions. The simplicity yet consistency makes it reliable.
Fishbone Diagram
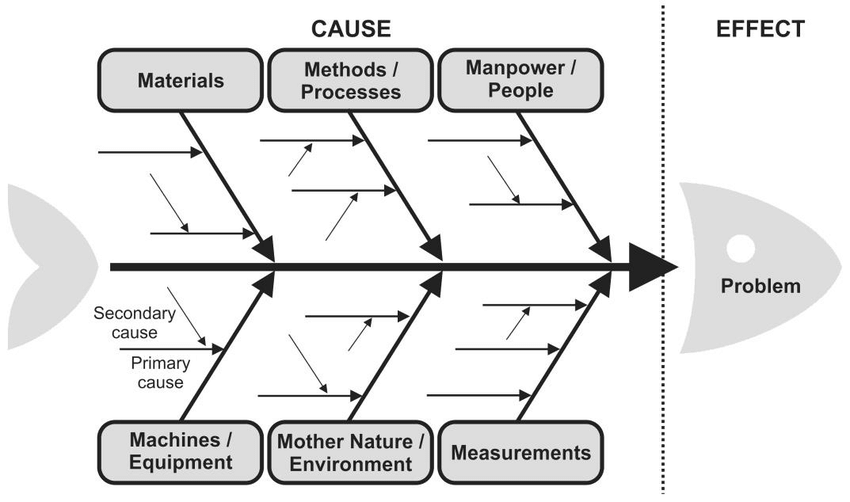
Fishbone diagrams connect multiple contributing factors visually around the core problem. Brainstorming possible categories with teams enables structured evaluation.
The fishbone provides an analytical tool to target solutions.
Failure Mode Analysis
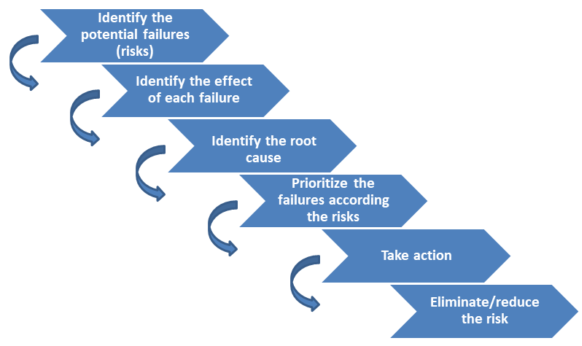
Failure mode analysis systematically identifies ways an asset, process, or system could potentially fail and assesses the effects.
FMEA delivers an inventory of vulnerabilities for mitigating through poka-yoke methods.
Control Charts
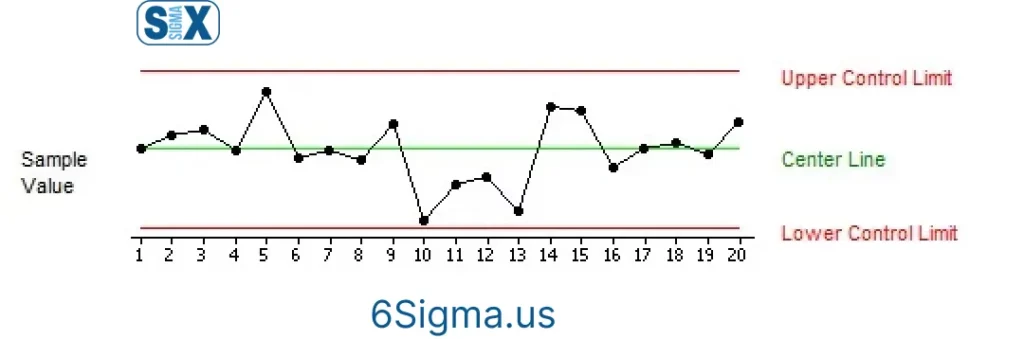
Control charts track process metrics over time to distinguish common cause variation and special cause variation based on statistical probabilities, signaling stability, or instabilities needing correction.
Control limits determine action thresholds.
5S Workplace Organization
5S workplace organization entails sorting, setting in order, systematic cleaning, standardizing, and sustaining production areas for efficiency, visual control, and continuous improvement. The disciplined foundation enables optimal poka-yoke.
Integrating analysis methods with domain experience and stakeholder perspectives arms teams with information to guide optimal poka-yoke mechanisms.
The solutions are tailored to the unique situation.
Take your Process Improvement Skills to the Next Level!
Become a Process Improvement Expert with Lean Six Sigma Green Belt Certification.
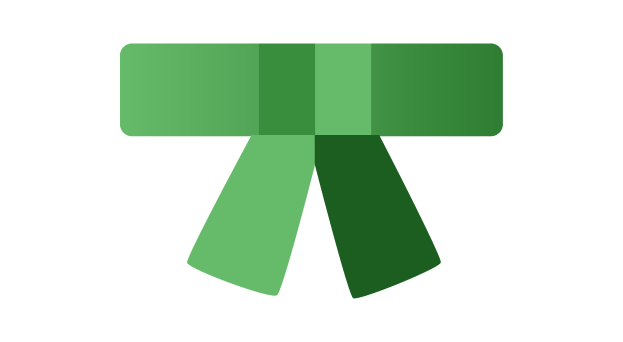
Benefits of Poka-Yoke
Studies by the Aberdeen Group show a 30% reduction in defects by implementing Poka Yoke techniques.
Applying poka-yoke as part of continuous improvement initiatives like Lean Six Sigma and Kaizen events yields powerful benefits for quality, efficiency, costs, and competitiveness, especially when grounded in the fundamentals of Lean:
Reduces Defects and Waste
By preventing errors from occurring in the first place, poka-yoke effectively reduces process defects and associated waste.
Every defect that reaches customers leads to rework, replacements, or lost business. Poka-yoke makes causes visible sooner to minimize impact.
Lowers Costs
In addition to materials wasted through scrapping defective outputs, costs get driven higher by excess process time, capacity overload, administrative burden, and opportunity costs from diverted resources.
Poka-yoke curtails expenses on multiple fronts.
Improves Quality
Preventing defects upfront with poka-yoke means fewer make it downstream to inspectors or customers, directly improving quality. Well-designed mistake-proofing facilitates right-first-time results.
Increases Efficiency
Properly implemented poka-yoke woven as standard work enhances process flow, frees up capacity, and boosts productivity.
Smoother operations with minimal control are needed to maximize asset utilization.
Fosters Continuous Improvement
Poka-yoke inherently takes a continuous view on learning from problems and redesigns systems to steer better outcomes. As processes evolve, so can the application of mistake-proofing mechanisms in a positive feedback loop.
Together this expands capabilities while controlling costs to do more with existing resources. Embedded poka-yoke drives a prevention mindset making true continuous improvement sustainable.
Examples of Poka-Yoke in Six Sigma
Poka-Yoke mechanisms take many forms spanning simple physical adjustments to complex software integrations. The unifying theme centers on guiding correct performance while preventing or instantly detecting errors.
Automated Data Validation
Input fields can be validated against preset criteria to catch deviations for date formats, text lengths, numeric ranges, or incompatible selections. Logging rejected entries helps improve upstream processes.
Process Step Guides
Color coding, visual indicators, checklists, or control plan integration assists in accurately following defined sequences to meet requirements. Skipping necessary actions gets avoided.
Part Orientation
Designing identical parts asymmetrically or using notches/guides forces proper orientation for foolproof assembly. Errors from misalignment get designed out.
Motion Sensors
Movement sensors ensure openings are clear or parts are in place before allowing hazardous motions that could cause injury or machine damage without the right conditions.
Alert Systems
Dashboards with visual or audible signals notify operators of abnormal readings needing intervention per established protocols before producing defects.
Incorporating principles of mistake-proofing align controls to help personnel complete steps properly as designed. Continual learning about failure modes enables strengthening poka-yoke countermeasures over time. No process reaches perfection but sustained incremental efforts pay dividends.
Integrating Poka-Yoke into Six Sigma
While powerful on its own, the poka-yoke goes further when embedded into structured continuous improvement frameworks like Six Sigma. Mistake-proofing steps align well with the define, measure, analyze, improve, and control (DMAIC) phases, a core framework taught in our Six Sigma certification programs.
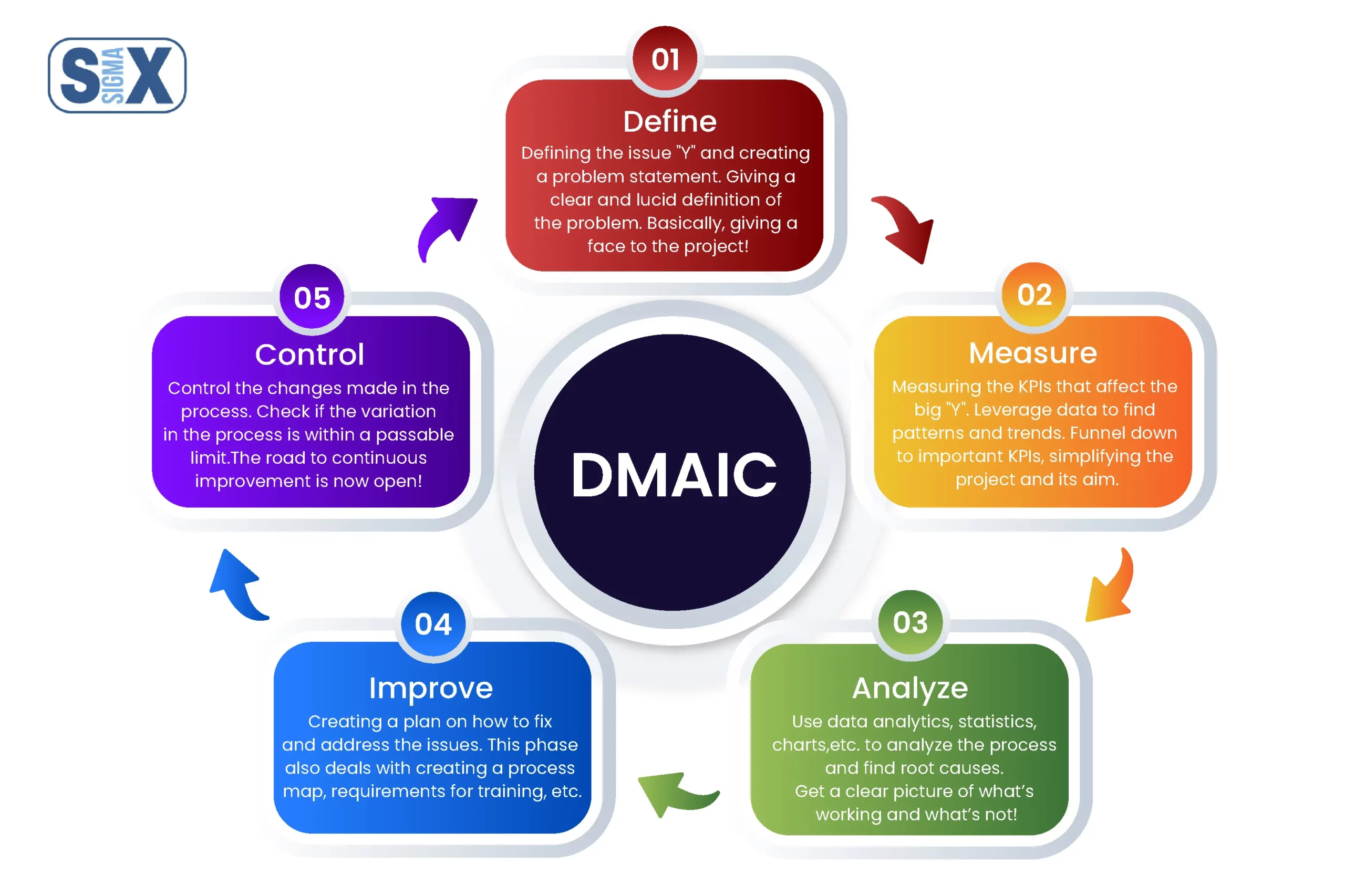
In Define, poka-yoke focuses efforts on critical outputs and defects. Measure gathers metrics on error frequency, impact, and root causes. Analyze evaluates conditions enabling mistakes and potential solutions. Improve and implement preventive redesigns, with Control monitoring performance.
Complementary to Statistical Process Control
Analysts can determine if production varies within expected statistical limits using control charts. By preventing special cause issues originating from human error, poka-yoke sustains stability. Control methods confirm effectiveness.
Enables Shift Left Quality
Poka-yoke principles integrated early in design shift quality left on the value stream. Building in mistake-proofing during new product development or process creation prevents defects from arising at the outset.
Reduces Control Plan Complexity
The more prevention through poka-yoke eliminates upstream errors, the fewer downstream inspection and reactionary controls remain necessary. Simplified control plans lower administrative costs.
Jointly applying poka-yoke with Six Sigma tools ushers enhanced benchmarking, analysis of variability, process redesign, and monitoring of gains. Mixing managerial and technical tactics produces optimal solutions. Workers gain autonomy in upholding standards through embedded mistake-proofing.
Sustaining a Poka-Yoke Culture
While many organizations rightfully pursue poka-yoke for discrete issues, the real power unfolds across entire systems over long time horizons by fundamentally changing culture.
Sustaining mistake-proofing necessitates commitment across managerial levels and frontline teams.
Elevate Your Quality Management to World-Class Standards with a Six Sigma Black Belt Certification
Empowering Workers to Fix Issues
Enabling workers to take ownership of deficits through embedded poka-yoke provokes deeper process knowledge and engagement.
Responsibility for originating solutions creates change agents at all levels.
Leaders should encourage surfacing errors without repercussion, recognizing each as an improvement opportunity. This no-blame culture opens pathways for preventing future occurrences.
Regular Audits
Even world-class poka-yoke controls require regular revalidation to confirm effectiveness, identify any degradation, and spark new ideas.
Scheduling different groups to audit areas outside their purview brings fresh perspectives.
Management demonstrates commitment by participating personally in routine Gemba walks.
Updating with New Technology
As process technology and control automation continue improving, new options become available to reduce manual involvement and take prevention mechanisms to heightened precision.
But upgrading the poka-yoke also demands ensuring personnel possess capabilities to sustain enhancements.
When Poka-Yoke gets woven into operational DNA, it no longer seems an added chore but rather feels integral to daily work. This fusion unlocks the method’s ultimate usefulness.
Leaders must champion the journey toward reliable systems.
SixSigma.us offers both Live Virtual classes as well as Online Self-Paced training. Most option includes access to the same great Master Black Belt instructors that teach our World Class in-person sessions. Sign-up today!
Virtual Classroom Training Programs Self-Paced Online Training Programs