Lean Techniques – Kanban Pull System. The Only Guide You Need
One handy methodology that has gained steam in recent years: Kanban Pull System.
Coming from the Japanese terms for “visual cue” or “card,” Kanban revolutionized the industry’s grip on workflow direction and crafting processes.
Unlike traditional “pushed” arrangements, Kanban depends on downstream signals to initiate upstream flow. This demand-reactive approach minimizes overproducing, lowers what sits waiting, and ensures resources are deployed precisely as needed.
At the core, Kanban follows the fundamentals of Lean of dumping waste and optimizing methods for maximum efficiency.
By visualizing the whole workflow, containing efforts underway, and targeting constant upgrading, Kanban empowers pinpointing and solving bottlenecks for top-notch, on-schedule results in the most cost-effective way.
Whether synchronizing sprawling operations global or small studio side-projects, Kanban cultivates a fluid, adaptable, and wasteless means of matching movements to genuine market needs.
Key Highlights
- Kanban’s Pull System provides a handy way of directing workflows and optimizing how things get made.
- It builds on just-in-time making, smooth motion, and a demand-reactive supply chain approach.
- The method utilizes visual prompts like Kanban boards and cards to cue ramping work up when manufacturing needs a refill too.
- It contains efforts in progress and targets cutting wasted movements, bottlenecks, and excess inventory sitting idle.
- Adopting Kanban’s Pull System can result in heightened efficiency, faster cycles, better quality oversight, and stronger client loyalty.
- Core to Kanban involves teams regularly reviewing and refining processes for perpetual upgrades too—a permanent work in progress of refinement itself.
What the is Kanban Pull System?
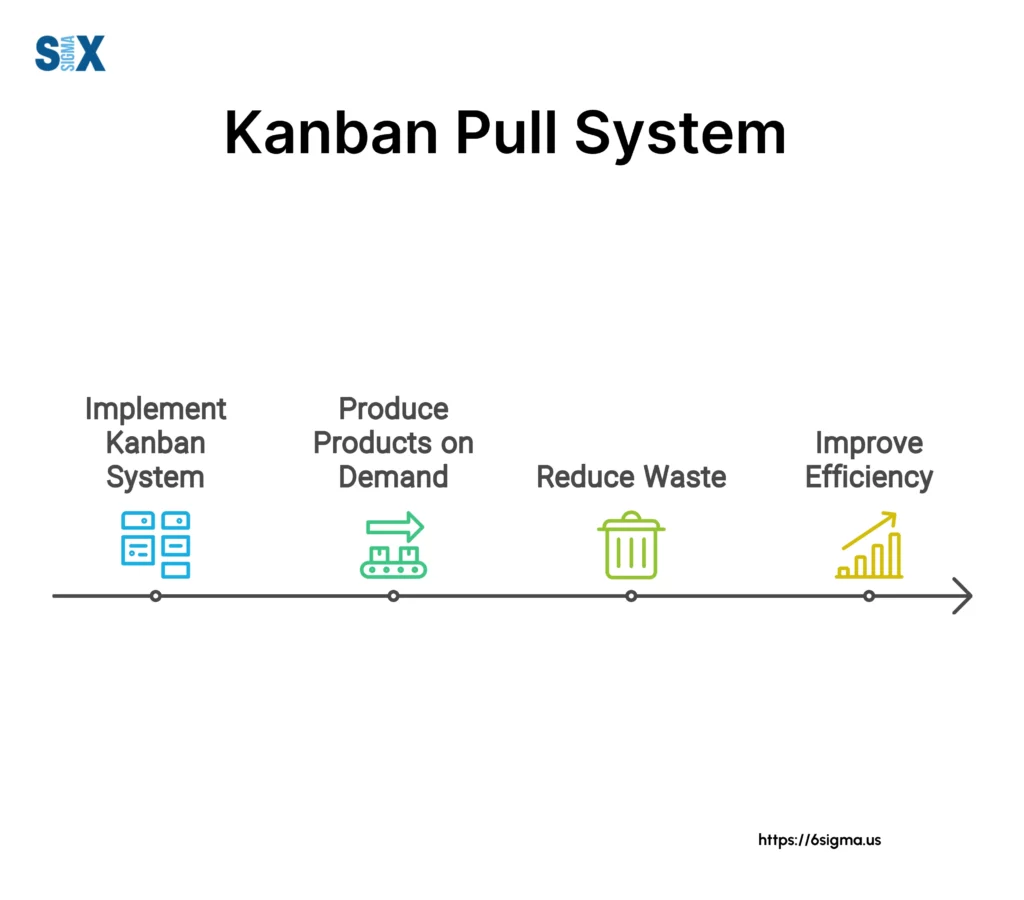
Kanban’s Pull System is a lean manufacturing and workflow direction method using visual cues to optimize grunt flow.
Debuting in Toyota factories as part of their lean crafting ecosystem, it’s since spread across industries managing cerebral work too.
Essentially, Kanban builds continuity by only “pulling” fresh tasks into motion when there’s space to handle them.
Unlike customary “push” setups dumping work assigned regardless of available Team A support, Kanban maintains flow.
“Kanban” blends Japanese for “visual” and “card/board.” The system employs prompts like cards arranged to guide production pacing.
Tasks appear board-side in real-time—a live workflow visualization.
Setting limits on efforts in progress and only pulling fresh work with open capacity avoids overfilling any segment.
Teams center singularly, decreasing switchbacks for a smoother, more proficient flow. Bottlenecks too become instantly obvious and addressable as issues arise.
Kanban cultivates controlled motion optimized for changing conditions sustainably through its reflexive, constraints-aware structure and cues.
Core Principles of Kanban Pull System
At the heart of the Kanban pull system are a few core principles that drive the methodology. These principles help create a lean, demand-driven workflow that minimizes waste and maximizes efficiency.
Visualize the Workflow
One of the foundational principles is to visualize the entire workflow. This is typically done using a kanban board with vertical columns representing each step of the process.
Work items are represented as cards that flow across the board from left to right as they progress through the workflow. Visualizing the work gives full transparency into the process and reveals bottlenecks.
Limit Work in Progress (WIP)
To avoid overloading the system, WIP limits are set for each workflow step. This prevents the system from taking on more work than it can handle at each stage.
Capping how many items are actively being worked on, reduces bloat, increases flow, and exposes constraints.
Manage Flow with Kanban Pull System
With a visualized workflow and WIP limits in place, the focus shifts to optimizing and managing flow. Work should move through the system at an even, continuous pace from commitment to delivery. This smooth, reliable flow increases throughput and delivery times.
Pull, Don’t Push
Work is “pulled” through the system based on capacity, rather than work being “pushed” in. When existing work is completed, new work is pulled from the backlog into that workflow stage.
This pull system avoids overloading any part of the process and lets workflow based on actual capacity constraints.
Continuous Improvement
A key tenet is the continuous improvement of processes and practices through incremental changes.
For those interested in mastering continuous improvement techniques, consider exploring our six sigma certification programs.
By making the workflow visible and measurable, opportunities for optimization are constantly identified, and teams can leverage root cause analysis to systematically identify and resolve bottlenecks. The Kanban pull system enables small, evolutionary changes that compound into big improvements over time.
Kanban Pull System Implementation
Implementing a Kanban pull system requires careful planning and execution. The key steps include:
Mapping the Value Stream
The first step is to map out the entire value stream for your product or service. This involves identifying all the process steps from the initial concept to delivery to the customer. Having an end-to-end view allows you to see where bottlenecks and constraints exist.
Establishing Pull
With the value stream mapped, you can establish a pull-based flow where work is “pulled” through each step as capacity opens up downstream. This is enabled by limiting work-in-progress (WIP) at each process step using visual kanban cards or signals.
Defining WIP Limits for Kanban Pull System
WIP limits are critical for an effective pull system. Limits should be established for each workflow state based on available capacity. These limits prevent overloading any part of the process and force upstream steps to pause until work can be “pulled” forward.
Visualizing the Workflow
A highly visible kanban board or electronic board is used to visualize the entire workflow. It shows work items flowing through each state in the process with WIP limits enforced. This transparency surfaces bottlenecks and blockers.
Establishing Kanban Policies
Clear policies define how work is pulled through the system. For example, policies around WIP limits, when new work can be started, how work is prioritized, and quality control checkpoints.
Continuous Improvement with Kanban Pull System
The Kanban method enables continuous process improvement through regular retrospectives, metric reviews, and scientific experiments to identify and eliminate waste and optimize flow.
Training the Team
Successfully adopting kanban requires training the entire team on the core principles and practices. This establishes a shared understanding of how to work within a pull system.
Benefits of the Kanban Pull System
One of the primary advantages of implementing a Kanban pull system is improved workflow visualization. By utilizing kanban boards and cards, the entire workflow becomes transparent.
Team members can see the work-in-progress limits, understand bottlenecks, and identify areas for process improvement. This visual management approach makes it easier to spot inefficiencies and opportunities for waste reduction.
The pull production aspect of Kanban systems helps minimize excess inventory and overproduction, a key principle to the fundamentals of Lean. Work only moves forward when there is real demand and capacity available.
This demand-driven approach aligns with just-in-time production principles and results in better inventory management across the entire supply chain.
Kanban pull systems enable teams to focus on continuous flow by limiting work in progress. Instead of multitasking on too many items, team members concentrate on completing one task before pulling the next into their workflow. This flow increases throughput and reduces cycle and lead times.
Another key benefit is the flexibility kanban provides. The system can adapt quickly to shifting priorities or changes in market demand without dramatically disrupting operations. Teams have a real-time understanding of capacity utilization and can reprioritize work as needed.
Kanban Pull System in Practice
The Kanban pull system is best implemented through a visual Kanban board that displays the workflow and work items moving through the process. This provides the transparency and visualization that is core to Kanban.
Kanban Cards
Work items are represented on kanban cards that flow across the board through the process steps. Cards contain key information about the work item such as description, owner, due date, etc. Physical cards on a wall-mounted board or digital cards in Kanban software can be used.
Columns/Swimlanes
The kanban board is divided into vertical columns or swimlanes that represent each step in the workflow process. Common columns include Requested, Analyzed, Developed, Tested, and Deployed. The team’s definition of “Done” determines the final column.
Work in Progress (WIP) Limits
Each column has an explicit limit on how many cards it can hold at one time. This forces the team to focus on completing work before starting too many new items, preventing overloading. When a column is full, new work cannot be pulled into that step until existing work exits.
Pull System Flow
Work items are “pulled” through the Kanban system based on capacity in the next column/step. As space opens up, the next highest priority work item is pulled forward from the previous step. This pull mechanism helps create a continuous flow of work through the system.
Kanban Meetings
Regular standup or kanban meetings review the board, discuss blockers, replenish the backlog, and make process improvement suggestions. Metrics like lead time and cycle time are reviewed to identify potential bottlenecks.
Software Tools
While Kanban can use manual boards, many teams utilize Kanban software tools like Trello, Jira, or LeanKit. These digital solutions enhance traceability, metrics, automation, and integration with other systems.
Continuous Improvement with the Kanban Pull System
One of the core principles of the kanban pull system is the idea of continuous improvement (kaizen in Japanese). The Kanban system provides a platform for teams to identify opportunities for process improvement and implement incremental changes over time.
The visual nature of the kanban board, with work items represented as cards flowing through the process, makes it easy to spot bottlenecks, delays, and areas of waste or inefficiency.
By monitoring cycle times, lead times, and work-in-progress (WIP) limits, teams can pinpoint where problems exist and develop countermeasures.
The pull-based replenishment mechanism of kanban inherently reduces waste and inventory buildup. However, teams should regularly analyze their workflow and value stream to eliminate any remaining sources of muda (waste) through techniques like value stream mapping.
Kanban encourages short feedback loops and frequent retrospectives where the team reflects on how to optimize their way of working. Improvement opportunities could include updating WIP limits, revising process policies, cross-training personnel, or adopting new tools and automation.
As the team implements changes based on their learnings, the resulting processes become more efficient, with faster flow, shorter lead times, and higher quality over time. Kanban’s emphasis on visualizing the entire workflow highlights the impact of any improvements.
Successful continuous improvement requires a mindset of embracing change rather than preserving the status quo. The Kanban pull system nurtures this mindset by making process problems and constraints highly visible so they can be addressed through iterative kaizen.
To Conclude
Kanban’s Pull System offers a potent lean approach revving productivity, flow and quality for making methods as much as cerebral work.
By visualizing the workflow, limiting simultaneous efforts and pulling according to open capacity, kanban smoothes processes and dumps wasted movements.
Constant upgrading epitomizes Kanban’s prowess. The live Kanban board and cycle/lead time stats furnish priceless insights exposing bottlenecks or refinements streamlining the value chain over the long haul.
Kanban cultivates gradual but compounding betterments with time.
While upgrading demands preliminary training and resources, quicker circles, sharper inventory oversight, higher quality and stronger client faith outweigh costs. Kanban benefits all industries.
Face rising cutthroat pressures, organizations gain competitiveness via philosophies like Kanban.
Resources abound assisting interested parties—books, online tutorials, certification programs like our six sigma certification, advisors and software solutions. Piloting Kanban then expanding eases transitions sustainably with leadership driving lifelong learning of techniques synchronizing operations optimization.
Kanban proves a transformative constant for any enterprise.
SixSigma.us offers both Live Virtual classes as well as Online Self-Paced training. Most option includes access to the same great Master Black Belt instructors that teach our World Class in-person sessions. Sign-up today!
Virtual Classroom Training Programs Self-Paced Online Training Programs