Process Failure Mode & Effects Analysis (PFMEA) in Lean Six Sigma
Even the most well-designed processes can be susceptible to failures, which can lead to defects, delays, and costly consequences.
To proactively identify and mitigate potential risks, companies employ a powerful risk assessment tool known as Process Failure Mode and Effects Analysis (PFMEA).
Quick Overview
- PFMEA (Process Failure Mode and Effects Analysis) is a risk assessment methodology used to identify and mitigate potential failures in manufacturing and business processes.
- It is a proactive approach to quality control and process improvement, helping organizations prevent defects and enhance operational efficiency.
- PFMEA involves a structured approach to analyzing processes, identifying potential failure modes, their causes, and effects, and implementing corrective actions.
- The methodology involves forming a multidisciplinary team, process mapping, brainstorming failure modes, assigning severity, occurrence, and detection rankings, and calculating a risk priority number (RPN).
- PFMEA is widely used in various industries, including automotive, aerospace, healthcare, and manufacturing, to ensure product and process quality and safety.
- It is an essential tool in quality management systems, Lean Six Sigma methodologies, and continuous improvement initiatives.
By conducting a PFMEA, companies can enhance their quality control measures, improve process reliability, and ultimately deliver superior products and services to their customers.
What is PFMEA?
Process Failure Mode and Effects Analysis (PFMEA) is a proactive risk assessment methodology used to identify and mitigate potential failures in manufacturing and business processes.
It is a structured approach that helps organizations anticipate and prevent problems before they occur, ultimately improving quality, reducing costs, and enhancing customer satisfaction.
PFMEA is a systematic technique that examines each step of a process, identifies potential failure modes (ways in which the process could fail), analyzes the causes and effects of these failures, and implements preventive actions to reduce the likelihood of occurrence or detect failures before they reach the customer.
Importance of PFMEA in Risk Assessment
Organizations must proactively manage risks to maintain a competitive edge. PFMEA plays a crucial role in risk assessment by providing a comprehensive framework for identifying, evaluating, and mitigating potential process failures.
By conducting a PFMEA, companies can:
- Identify critical process steps and potential failure modes.
- Analyze the severity, occurrence, and detection of failures.
- Prioritize risks based on their potential impact.
- Implement corrective actions and preventive controls.
- Continuously monitor and improve processes.
Benefits of Conducting PFMEA
Implementing PFMEA offers numerous benefits to organizations, including:
- Improved product/service quality: By identifying and addressing potential failures, PFMEA helps organizations deliver higher-quality products and services to customers.
- Cost savings: Preventing failures before they occur can significantly reduce costs associated with rework, scrap, warranty claims, and customer dissatisfaction.
- Enhanced customer satisfaction: By delivering reliable and consistent products/services, PFMEA contributes to increased customer satisfaction and loyalty.
- Risk mitigation: PFMEA provides a structured approach to identifying and mitigating risks, reducing the likelihood of costly failures and disruptions.
- Continuous improvement: The PFMEA process encourages a culture of continuous improvement, as teams regularly review and enhance processes to address potential failures.
- Cross-functional collaboration: PFMEA requires input from a multidisciplinary team, fostering communication and collaboration across different departments and functions.
By conducting a thorough PFMEA, organizations can proactively identify and address potential process failures, minimizing risks, improving quality, and enhancing overall operational excellence.PFMEA vs FMEA
Difference between PFMEA and FMEA
While PFMEA (Process Failure Mode and Effects Analysis) and FMEA (Failure Mode and Effects Analysis) share some similarities, there are distinct differences between the two methodologies.
FMEA is a risk assessment tool used to identify potential failures, their causes, and their effects on a product or system design. It is typically conducted during the design phase and focuses on evaluating the risks associated with the product or system itself.
On the other hand, PFMEA is a risk assessment methodology specifically designed to analyze potential failures in manufacturing or service processes. It aims to identify potential process failures, their causes, and their effects on the process output or customer satisfaction.
The primary difference lies in the scope of analysis. FMEA is centered on the product or system design, while PFMEA concentrates on the processes involved in manufacturing or delivering that product or service.
When to use PFMEA vs FMEA
The choice between using PFMEA or FMEA depends on the stage of the product or service lifecycle and the specific objectives of the risk assessment.
FMEA is typically employed during the design phase of a product or system to identify and mitigate potential failures before production or implementation begins.
It helps in identifying design flaws, material incompatibilities, or potential safety hazards early on, allowing for corrective actions to be taken before significant investments are made.
PFMEA, on the other hand, is more relevant during the manufacturing or service delivery phase.
It is used to analyze the processes involved in producing or delivering a product or service, identifying potential failures that could occur during these processes, and implementing preventive or corrective measures to minimize their impact.
Design FMEA and Process FMEA
Within the FMEA methodology, there are two distinct types: Design FMEA and Process FMEA.
Design FMEA, as the name suggests, is focused on analyzing the design of a product or system. It evaluates the potential failures that could occur due to design flaws, material selection, or interactions between components.
Design FMEA is typically conducted early in the product development cycle and helps to identify and mitigate design-related risks before moving to the manufacturing stage.
Process FMEA, on the other hand, is closely related to PFMEA. It analyzes the manufacturing or assembly processes involved in producing a product or delivering a service.
Process FMEA identifies potential failures that could occur during these processes, such as equipment malfunctions, operator errors, or process variations, and helps to implement preventive or corrective actions to minimize their impact on product quality or service delivery.
While PFMEA and Process FMEA share similarities in their focus on process analysis, PFMEA is a more comprehensive methodology that encompasses a broader range of processes, including non-manufacturing processes such as service delivery, logistics, and administrative processes.
PFMEA Methodology
The PFMEA methodology is a structured and systematic approach to identifying and mitigating potential failures in processes.
It involves a series of steps that help organizations proactively address risks and implement preventive measures. Here are the key steps involved in the PFMEA process:
- Forming a multidisciplinary team
The first step in conducting a PFMEA is to assemble a cross-functional team with diverse expertise and perspectives. This team should include representatives from various departments or areas directly or indirectly involved in the process under analysis.
Typical team members may include process engineers, quality experts, operators, maintenance personnel, and subject matter experts. A multidisciplinary team ensures a comprehensive understanding of the process and its potential failure modes. - Process mapping and flowcharting
The team begins by creating a detailed process map or flowchart that outlines the sequence of steps, inputs, outputs, and interactions within the process.
This visual representation helps the team develop a shared understanding of the process and facilitates the identification of potential failure modes. Process mapping also aids in defining the scope and boundaries of the PFMEA analysis. - Identifying potential failure modes
Once the process is mapped, the team brainstorms and identifies potential failure modes associated with each process step. A failure mode is a way in which a process, product, or service could potentially fail to meet its intended function or requirements.
The team leverages their collective knowledge, experience, and techniques like cause-and-effect diagrams or failure mode and effects analysis (FMEA) to identify potential failure modes systematically. - Assigning severity, occurrence, and detection rankings
For each identified failure mode, the team assigns numerical rankings for severity, occurrence, and detection. Severity represents the impact or consequence of the failure mode on the process, product, or customer.
Occurrence measures the likelihood or frequency of the failure mode occurring. Detection refers to the ability to detect the failure mode before it reaches the customer or end-user.
These rankings are typically based on predefined scales or criteria established by the organization or industry standards. - Calculating risk priority number (RPN)
The risk priority number (RPN) is a quantitative measure of risk associated with each potential failure mode. It is calculated by multiplying the severity, occurrence, and detection rankings assigned to the failure mode.
The RPN helps prioritize the failure modes based on their relative risk levels, allowing the team to focus their efforts on the most critical areas.
By following these steps, the PFMEA methodology provides a structured framework for identifying, evaluating, and mitigating potential failures in processes.
It enables organizations to take proactive measures to improve process reliability, reduce risks, and enhance overall quality and performance.
Failure Mode Analysis
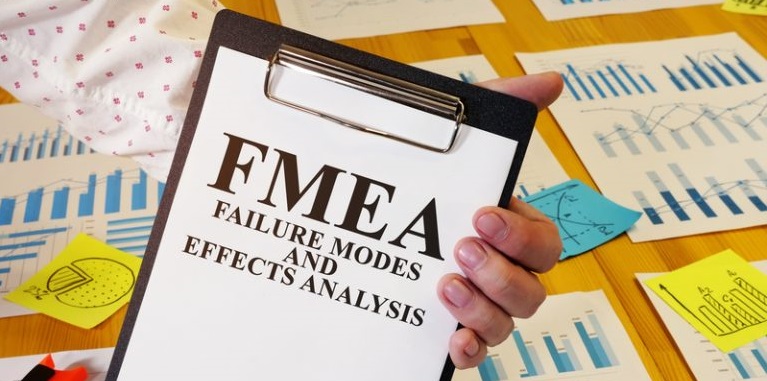
Potential Failure Modes in Processes
Identifying potential failure modes is a crucial step in the PFMEA process. Failure modes refer to how a process or component can fail to perform its intended function.
In manufacturing processes, potential failure modes can include defects, errors, or deviations from specifications. Some common examples of failure modes in processes include:
- Dimensional errors: Deviations from specified dimensions or tolerances, such as incorrect measurements, warping, or shrinkage.
- Material defects: Issues related to the quality or composition of raw materials, such as impurities, contamination, or inconsistencies.
- Process variability: Fluctuations or inconsistencies in process parameters, such as temperature, pressure, or flow rates.
- Equipment failures: Malfunctions or breakdowns in machinery, tools, or equipment used in the process.
- Human errors: Mistakes or oversights made by operators or personnel involved in the process, such as incorrect settings, improper handling, or procedural deviations.
Causes of Failure Modes
Once potential failure modes have been identified, it is essential to determine their underlying causes. Failure causes can be related to various factors, including:
- Design flaws: Inherent weaknesses or limitations in the design of the product, process, or system.
- Material issues: Problems with the quality, composition, or compatibility of raw materials or components.
- Environmental factors: External conditions, such as temperature, humidity, or vibrations, that can impact the process or product.
- Operational errors: Deviations from established procedures or protocols, such as incorrect setup, maintenance, or handling.
- Training deficiencies: Lack of proper training or knowledge among personnel involved in the process.
Effects of Failure Modes
Identifying the potential effects of failure modes is another critical aspect of the PFMEA process. Failure effects can range from minor inconveniences to severe consequences, depending on the nature and severity of the failure mode. Some common effects of failure modes include:
- Product defects: Nonconformities or defects in the final product, affecting its quality, performance, or functionality.
- Process disruptions: Interruptions or delays in the manufacturing or production process, leading to reduced efficiency or output.
- Safety hazards: Potential risks to the health and safety of operators, personnel, or end-users.
- Environmental impact: Negative effects on the environment, such as pollution, waste, or resource depletion.
- Customer dissatisfaction: Failure to meet customer expectations or requirements, leading to complaints, returns, or loss of business.
Brainstorming Techniques for Identifying Failures
To effectively identify potential failure modes, causes, and effects, it is essential to employ structured brainstorming techniques.
These techniques encourage collaboration, creativity, and diverse perspectives among the multidisciplinary team involved in the PFMEA process. Some commonly used brainstorming techniques include:
- Cause-and-effect diagrams (Ishikawa or fishbone diagrams): Visual representations that help identify potential causes of a particular failure mode or effect.
- Failure Mode and Effects Analysis (FMEA): A structured approach to identifying potential failures, their causes, and effects, often used in conjunction with PFMEA.
- Fault tree analysis: A top-down approach that starts with an undesired event and systematically analyzes the potential causes and contributing factors.
- Brainstorming sessions: Open discussions where team members contribute ideas, experiences, and perspectives related to potential failures.
- Process mapping: Visual representations of the process flow, highlighting potential failure points or areas of concern.
By employing these brainstorming techniques, the PFMEA team can thoroughly explore and document potential failure modes, their causes, and their effects, laying the foundation for effective risk assessment and mitigation strategies.
Risk Evaluation and Mitigation
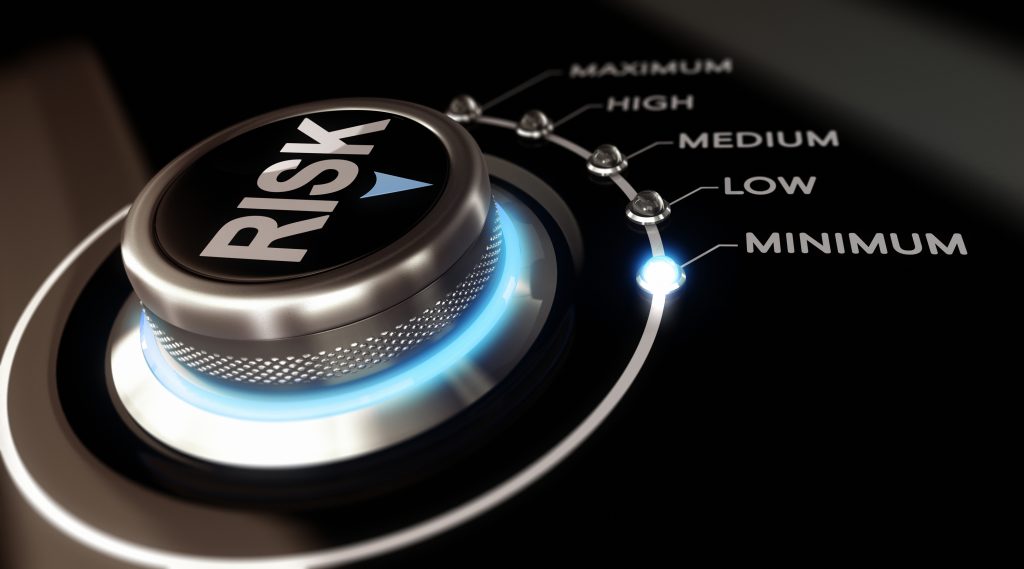
Interpreting RPN Values
After calculating the Risk Priority Number (RPN) for each potential failure mode, the next step is to interpret these values and prioritize the risks.
RPN values range from 1 to 1000, with higher numbers indicating a greater risk. Organizations typically establish their thresholds for determining which RPN values are considered high, medium, or low risk.
For example, a company may categorize RPNs as follows:
- RPN ā„ 100: High risk, immediate corrective action required
- 50 ⤠RPN < 100: Moderate risk, corrective action should be planned
- RPN < 50: Low risk, no immediate action required
It’s important to note that these thresholds can vary across industries and organizations based on their risk tolerance and specific requirements.
Determining Corrective Actions
Once the high-risk failure modes have been identified based on their RPN values, the PFMEA team must determine appropriate corrective actions to mitigate or eliminate these risks.
Corrective actions can include process improvements, design modifications, additional controls, or changes in operating procedures.
The team should consider the following factors when selecting corrective actions:
- Effectiveness: The corrective action should effectively address the root cause of the failure mode and reduce the risk to an acceptable level.
- Feasibility: The corrective action should be practical and achievable within the organization’s resources and constraints.
- Cost: The cost of implementing the corrective action should be weighed against the potential consequences of the failure mode.
- Timeliness: Corrective actions for high-risk failure modes should be implemented promptly to minimize the risk of occurrence.
Risk Mitigation Strategies
In addition to specific corrective actions, organizations can adopt various risk mitigation strategies to proactively manage and reduce risks identified through the PFMEA process. These strategies may include:
- Process improvements: Continuously improving processes through techniques like lean manufacturing, Six Sigma, or process re-engineering can help eliminate potential failure modes and enhance overall process performance.
- Quality control measures: Implementing robust quality control measures, such as statistical process control (SPC), inspection procedures, or automated monitoring systems, can detect and prevent failures before they occur.
- Preventive maintenance: Establishing a comprehensive preventive maintenance program can reduce the likelihood of equipment failures and ensure consistent process performance.
- Training and education: Providing regular training and education to employees on PFMEA methodology, quality management, and risk mitigation techniques can foster a culture of continuous improvement and risk awareness.
Fault Tree Analysis for High-Risk Failures
In cases where the PFMEA identifies high-risk failure modes with severe consequences, organizations may choose to conduct a more in-depth analysis using fault tree analysis (FTA).
FTA is a top-down, deductive technique that graphically models the logical relationships between potential causes and the undesired event (failure mode).
The fault tree analysis process involves the following steps:
- Define the top event: Identify the specific failure mode or undesired event to be analyzed.
- Construct the fault tree: Using logic gates (AND, OR) and event symbols, create a visual representation of the potential causes that could lead to the top event.
- Analyze the fault tree: Evaluate the fault tree to identify the most critical paths and combinations of events that contribute to the top event.
- Quantify the risk: If sufficient data is available, calculate the probability of occurrence for the top event and its contributing causes.
- Identify risk mitigation strategies: Based on the fault tree analysis, develop and implement appropriate risk mitigation strategies to address the identified causes and reduce the likelihood of the top event occurring.
Fault tree analysis provides a structured and systematic approach to understanding the root causes of high-risk failures and can complement the PFMEA process by offering deeper insights into risk mitigation strategies.
PFMEA Implementation and Best Practices
Successful implementation of PFMEA requires integrating it into an organization’s overall quality management system. This ensures that the risk assessment process is aligned with the company’s quality objectives and policies.
By embedding PFMEA into the quality management framework, organizations can establish a systematic approach to identifying, evaluating, and mitigating potential process failures.
To effectively integrate PFMEA, companies should:
- Define clear roles and responsibilities for the PFMEA team members.
- Establish triggers or criteria for when to conduct a PFMEA (e.g., new process introduction, process changes, recurring quality issues).
- Develop standardized procedures and templates for conducting PFMEAs consistently across different processes or departments.
- Align PFMEA activities with other quality tools and methodologies, such as control plans, process capability studies, and measurement system analysis.
- Implement a system for tracking and monitoring PFMEA recommendations and corrective actions.
Continuous Improvement and Process Monitoring
PFMEA is not a one-time activity but rather a continuous process improvement tool. Organizations should regularly review and update their PFMEAs to ensure that they remain relevant and effective in mitigating potential failures. This involves:
- Monitoring key process indicators and quality metrics to identify any new or emerging failure modes.
- Conducting periodic PFMEA reviews, especially after process changes or when new data becomes available.
- Reassessing risk priority numbers (RPNs) and revising corrective actions as needed.
- Incorporating lessons learned from previous PFMEA cycles and applying them to future analyses.
- Encouraging a culture of continuous improvement, where employees are empowered to identify and report potential process failures.
Documentation and Record-keeping
Proper documentation and record-keeping are essential for the successful implementation and long-term effectiveness of PFMEA. Organizations should maintain detailed records of their PFMEA activities, including:
- PFMEA reports, documents the identified failure modes, effects, causes, and recommended corrective actions.
- Meeting minutes and attendance records for PFMEA team sessions.
- Supporting documents, such as process flow diagrams, control plans, and fault tree analysis.
- Records of corrective actions taken, including implementation dates and responsible parties.
- Evidence of PFMEA review and update cycles, including revision histories.
Comprehensive documentation not only provides a historical record but also serves as a valuable reference for future PFMEA activities and knowledge transfer within the organization.
Training and Education for PFMEA Teams
Effective PFMEA implementation relies on having a well-trained and knowledgeable team.
Organizations should invest in training and education programs to ensure that PFMEA team members have the necessary skills and expertise to conduct thorough and accurate analyses. Training topics may include:
- PFMEA methodology and techniques, such as process mapping, brainstorming, and risk evaluation.
- Understanding of severity, occurrence, and detection rankings, and how to assign them consistently.
- Facilitation skills for leading PFMEA team sessions and encouraging participation.
- Root cause analysis techniques for identifying failure causes.
- Best practices for documenting and communicating PFMEA findings and recommendations.
Ongoing training and knowledge-sharing sessions can help maintain a high level of PFMEA competency within the organization and ensure consistent application of the methodology across different processes and teams.
By following these best practices for PFMEA implementation, organizations can effectively integrate the risk assessment tool into their quality management systems, foster a culture of continuous improvement, maintain comprehensive documentation, and develop a skilled workforce capable of conducting thorough and valuable PFMEA analyses.
Case Studies and Examples
Successful PFMEA implementations have been reported across a wide range of industries, demonstrating the versatility and effectiveness of this risk assessment methodology (process analysis technique).
In the automotive industry, PFMEA has been extensively used during the design and manufacturing phases to identify and mitigate potential failures in-vehicle components and production processes.
One notable example is Ford Motor Company’s implementation of PFMEA, which led to significant improvements in product quality and customer satisfaction.
The aerospace industry, with its stringent safety requirements, has also embraced PFMEA as a crucial risk assessment tool.
Boeing, for instance, has utilized PFMEA to analyze and address potential failure modes in aircraft design, manufacturing, and maintenance processes, enhancing overall reliability and reducing the risk of catastrophic failures.
In the healthcare sector, PFMEA has proven invaluable in identifying and mitigating risks associated with medical devices, pharmaceuticals, and clinical procedures.
By conducting thorough PFMEA (failure mode effects analysis), healthcare organizations can prioritize corrective actions and implement preventive measures to ensure patient safety and improve healthcare outcomes.
Key Takeaways from PFMEA Projects
While PFMEA implementations have yielded significant benefits, several lessons have emerged from real-world projects that can help organizations optimize their PFMEA efforts:
- Multidisciplinary team collaboration: Assembling a diverse team with expertise from various functional areas (design, manufacturing, quality control, etc.) is crucial for identifying comprehensive failure modes and effective corrective actions.
- Continuous improvement: PFMEA should be treated as an ongoing process rather than a one-time exercise. Regular reviews and updates are necessary to address changes in processes, materials, or operating conditions.
- Data-driven decision-making: Relying on historical data, such as field reports, warranty claims, and customer feedback, can provide valuable insights into potential failure modes and their effects, enhancing the accuracy of the PFMEA.
- Integration with other quality tools: Combining PFMEA with complementary tools like fault tree analysis, design of experiments (DoE), and statistical process control (SPC) can strengthen the overall risk assessment and mitigation efforts.
PFMEA Software Tools and Resources
To streamline the PFMEA process and facilitate collaboration, various software tools and resources are available:
- PFMEA software: Dedicated PFMEA software solutions, such as Relyence, Minitab, and aPriori, offer features like team collaboration, data management, and automated RPN calculations, simplifying the PFMEA workflow.
- Quality management platforms: Many quality management systems (QMS) and product lifecycle management (PLM) platforms, like Greenlight Guru and Propel, integrate PFMEA functionality, allowing seamless integration with other quality processes.
- Industry guidelines and standards: Organizations like the Automotive Industry Action Group (AIAG), the International Electrotechnical Commission (IEC), and the International Organization for Standardization (ISO) provide guidelines, templates, and best practices for conducting effective PFMEAs.
- Online resources and communities: Various online forums, blogs, and professional communities offer valuable insights, case studies, and knowledge-sharing opportunities related to PFMEA implementation and best practices.
By leveraging these tools and resources, organizations can streamline their PFMEA efforts, facilitate cross-functional collaboration, and stay up-to-date with industry best practices, ultimately enhancing their risk assessment and mitigation capabilities.
SixSigma.us offers both Live Virtual classes as well as Online Self-Paced training. Most option includes access to the same great Master Black Belt instructors that teach our World Class in-person sessions. Sign-up today!
Virtual Classroom Training Programs Self-Paced Online Training Programs