Mastering Assignable Causes: A Comprehensive Guide for Quality Excellence
Quality exerts greater influence today as companies seek distinction through excellence. A core concept here involves appreciating assignable cause(s) – specific, discernible factors driving fluctuations or divergences in workflow or system outcomes.
Regardless of your role as a quality leader, process engineer, or business manager, the capacity to pinpoint, investigate, and remedy assignable causes proves impactful.
It fosters steady quality standards, optimizes workflows, and propels unrelenting enhancements.
So whether manufacturing, services, or elsewhere, let’s begin leveraging quality intelligence resources within our reach.
Key Highlights
- Understand the fundamental difference between assignable causes and common causes of variation.
- Explore various techniques for detecting and identifying assignable causes.
- Gain insights into the potential sources of assignable causes.
- Discover the numerous benefits of effectively managing assignable causes.
- Learn best practices for data collection and analysis, encompassing both qualitative and quantitative approaches.
- Examine case studies and industry examples that illustrate the successful application of assignable cause management in various sectors.
- Understand the role of assignable causes within the broader context of quality management systems
- Explore the limitations and challenges associated with managing assignable causes, and strategies to overcome them.
- Recognize the importance of promoting a culture of continuous improvement and employee engagement in the pursuit of identifying and addressing assignable causes.
What is an Assignable Cause?
As quality professionals, one of the fundamental concepts we must grasp is the distinction between assignable causes and common causes of variation.
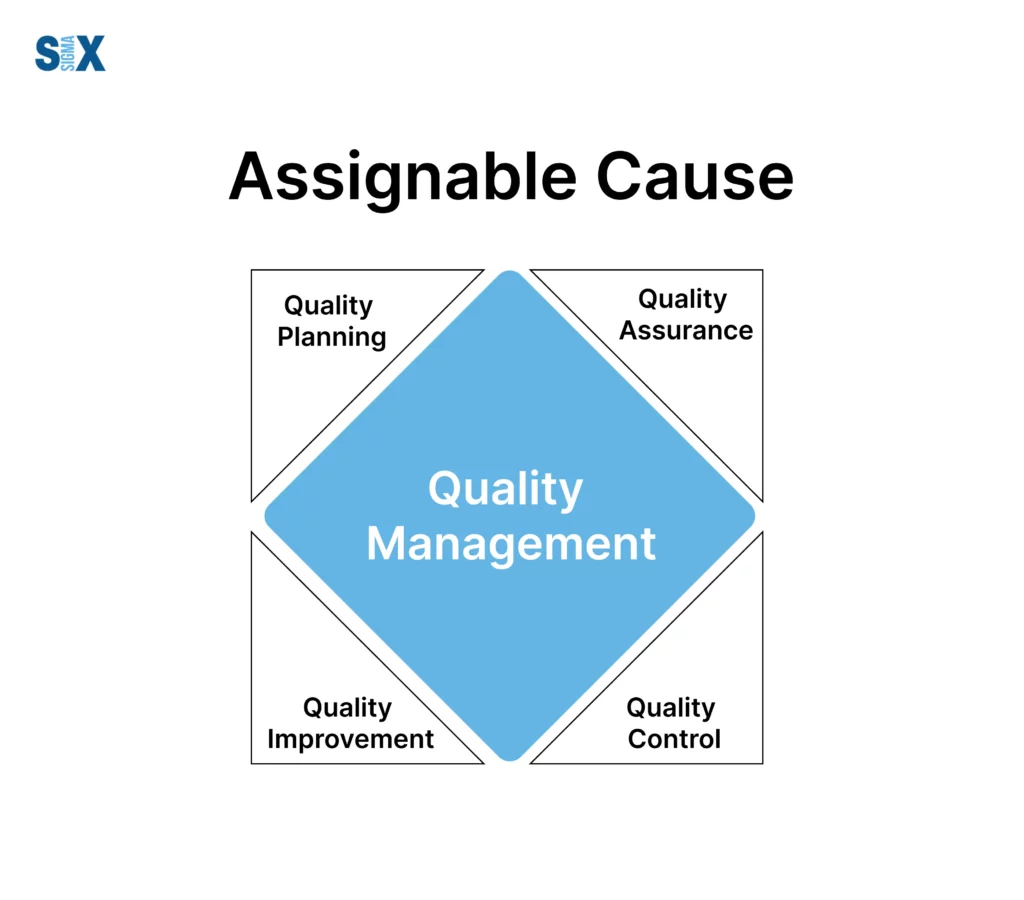
An assignable cause, also known as a special cause, refers to a specific, identifiable factor or event that contributes to a variation or deviation in a process or system’s output.
Unlike common causes, which stem from inherent, random fluctuations within the process, assignable causes are distinct, controllable factors that can significantly impact the consistency and predictability of our operations.
Definition of Assignable Cause
Formally, an assignable cause is defined as a specific, identifiable reason that contributes to a variation or deviation in a process or system’s output.
These causes are not part of the regular or expected variation within the system, but rather, they represent external factors or events that disrupt the normal functioning of the process.
Difference Between Assignable Cause and Common Cause
The key distinction between assignable causes and common causes lies in their nature and our ability to control them.
Common causes are inherent to the process and result from the cumulative effect of various small, random variations in factors such as materials, equipment, methods, and personnel.
These causes are inherently present and cannot be easily isolated or eliminated without a fundamental overhaul of the process itself.
When an assignable cause is present, the process is said to be “out of control” or unstable, as the variation it introduces is not within the expected range of common cause variation.
Significance of Assignable Cause in Quality Management
The ability to identify and manage assignable causes is of paramount importance in quality management for several reasons:
- Process Control: Recognizing and addressing assignable causes enables us to bring processes back into a state of statistical control, ensuring consistent and predictable output.
- Root Cause Analysis: Identifying assignable causes is a crucial step in root cause analysis, allowing us to pinpoint the underlying factors contributing to quality issues or deviations.
- Continuous Improvement: By eliminating assignable causes, we can continuously improve processes, reducing variation and enhancing overall performance.
- Cost Reduction: Effectively managing assignable causes helps minimize waste, rework, and associated costs, leading to significant cost savings for the organization.
- Customer Satisfaction: Consistent product or service quality, resulting from the elimination of assignable causes, directly contributes to higher customer satisfaction and loyalty.
In essence, mastering the identification and management of assignable causes is a fundamental prerequisite for achieving robust quality management systems, driving continuous improvement, and delivering superior products or services to our customers.
Identifying Assignable Cause
One of the most powerful tools at our disposal for identifying assignable causes is the control chart.
Control charts are statistical tools designed to distinguish between common cause variation, which is inherent and expected within a process, and special cause (or assignable cause) variation, which represents abnormal or unexpected deviations.
By plotting process data over time and establishing control limits based on the expected range of common cause variation, control charts enable us to visually detect when the process deviates from its normal, stable state.
Points falling outside the control limits or exhibiting non-random patterns are clear signals that an assignable cause is present, prompting us to investigate and identify the specific factor or event responsible for the observed variation.
Western Electric rules for detecting Assignable Cause
While control limits are the most obvious indicators of assignable causes, some additional patterns and rules can help us detect more subtle signals of special cause variation.
The Western Electric rules, developed by the Western Electric Company in the 1920s, are a widely recognized set of guidelines for identifying non-random patterns that may indicate the presence of an assignable cause.
These rules include:
- One or more points beyond the control limits
- A run of seven or more consecutive points on the same side of the center-line
- Six or more consecutive points increasing or decreasing
- Fourteen or more consecutive points alternating up and down
- Two out of three consecutive points beyond the two-sigma warning limits
- Four out of five consecutive points beyond the one-sigma limits
- Fifteen consecutive points within the one-sigma limits
Examples of Assignable Causes
Assignable causes can stem from various sources within a process or system. Some common examples include:
- Human Error: Mistakes, lapses in concentration, or deviations from established procedures by personnel can introduce assignable causes of variation.
- Equipment Malfunction: Wear and tear, mechanical failures, or improper calibration of equipment can lead to assignable causes that impact process output.
- Process Variation: Changes in raw materials, environmental conditions (e.g., temperature, humidity), or deviations from standard operating procedures can result in assignable causes of variation.
- Supplier Issues: Defective or inconsistent materials or components received from suppliers can introduce assignable causes into the process.
- External Factors: Events such as power outages, natural disasters, or regulatory changes can represent assignable causes that disrupt normal operations.
It is essential to remain vigilant and proactively monitor processes for any potential signals of assignable causes, as their timely identification and mitigation are crucial for maintaining quality and process control.
Sources of Assignable Cause
To effectively identify and manage assignable causes, it is crucial to understand their potential sources within a process.
One framework for organizing these sources is the consideration of process components, often referred to as the “6Ms“:
- Manpower (People): Variations in employee skills, training, experience, or procedure adherence can introduce assignable causes.
- Methods: Deviations from established methods, processes, or workflows can lead to assignable causes of variation.
- Materials: Inconsistencies in raw materials, components, or supplies can contribute to assignable causes.
- Machines (Equipment): Malfunctions, improper calibration, or equipment wear and tear can introduce assignable causes.
- Measurements: Inaccurate or imprecise measurement tools or techniques can result in assignable causes of variation.
- Environment: Changes in environmental conditions, such as temperature, humidity, or lighting, can represent assignable causes impacting the process.
By systematically examining each of these process components, we can enhance our ability to identify potential sources of assignable causes and take appropriate corrective actions.
Poorly Designed Processes
In some cases, assignable causes can arise from fundamental flaws or weaknesses in the design of the process itself.
Poorly designed processes may lack robustness, fail to account for potential variations, or introduce unnecessary complexities that increase the likelihood of assignable causes occurring.
Examples of poorly designed processes that can contribute to assignable causes include:
- Inadequate validation or testing during process development
- Insufficient consideration of potential failure modes or risk factors
- Lack of standardization or clearly defined procedures
- Excessive manual interventions or opportunities for human error
- Inadequate control or monitoring mechanisms
- Inefficient layouts or material flows
Addressing assignable causes stemming from poorly designed processes may require a comprehensive review and redesign effort, leveraging principles such as Design for Six Sigma (DFSS) or lean process optimization methodologies.
Changes in External Conditions
While many assignable causes originate from within the process itself, it is essential to recognize that external factors can also contribute to variations and deviations.
Changes in external conditions, such as environmental factors, regulatory requirements, or market dynamics, can introduce assignable causes that disrupt normal operations.
Examples of external conditions that may lead to assignable causes include:
- Fluctuations in temperature, humidity, or other environmental variables
- Power outages or utility disruptions
- Natural disasters or extreme weather events
- Changes in regulatory requirements or industry standards
- Market shifts or fluctuations in customer demand
- Supply chain disruptions or shortages of critical materials
By proactively monitoring and anticipating potential changes in external conditions, organizations can better prepare for and mitigate the impact of assignable causes resulting from these factors.
Benefits of Managing Assignable Cause
One of the primary benefits of effectively managing assignable causes is the ability to achieve superior quality control and product or service consistency.
By identifying and addressing the specific factors that contribute to variations or deviations, organizations can minimize the impact of assignable causes on their processes, resulting in more predictable and consistent outputs.
Consistent quality is a critical competitive advantage in today’s marketplace, as it not only meets customer expectations but also fosters brand loyalty and trust.
Enhanced problem-solving and Root Cause Analysis
The process of identifying and addressing assignable causes is inherently linked to effective problem-solving and root-cause analysis.
When an assignable cause is detected, it prompts an investigation to determine the underlying reason or event responsible for the observed variation.
By thoroughly examining the root cause of an assignable cause, organizations can develop targeted solutions that address the fundamental issue, rather than merely treating the symptoms.
This approach not only resolves the immediate problem but also helps prevent its recurrence, enabling a proactive and sustainable approach to quality management.
Effective root cause analysis facilitated by the identification of assignable causes can lead to process improvements, enhanced efficiency, and cost savings, as organizations can address the underlying issues rather than expending resources on temporary fixes or redundant efforts.
Preventive Action and Continuous Improvement
Managing assignable causes is not merely a reactive endeavor; it also plays a crucial role in proactive preventive action and continuous improvement efforts.
By recognizing and eliminating assignable causes, organizations can implement corrective measures that prevent the recurrence of similar issues in the future.
This proactive approach aligns with the principles of continuous improvement methodologies, such as Lean and Six Sigma, which emphasize the importance of identifying and addressing root causes to drive sustained process enhancements.
By systematically identifying and addressing assignable causes, organizations can continuously refine their processes, eliminate sources of variation, and optimize performance over time.
Preventive action based on assignable cause management not only reduces the likelihood of future problems but also fosters a culture of continuous learning and improvement within the organization, enabling it to stay ahead of the competition and adapt to changing market dynamics.
Process Optimization and Increased Efficiency
Effectively managing assignable causes is a critical step toward process optimization and increased efficiency.
When assignable causes are identified and addressed, processes can operate within their intended performance parameters, minimizing disruptions, rework, and waste.
By eliminating the sources of variation introduced by assignable causes, organizations can streamline their operations, reduce cycle times, and optimize resource utilization.
This, in turn, leads to increased productivity, lower costs, and improved competitiveness.
Process optimization through assignable cause management also enables organizations to identify and capitalize on potential opportunities for improvement.
Reduced waste, rework, and costs
Uncontrolled variation and deviations resulting from unaddressed assignable causes can lead to significant waste, rework, and associated costs for organizations.
When assignable causes are present, processes may produce defective or non-conforming outputs, necessitating rework, scrap, or even product recalls in severe cases.
The cost savings achieved through effective assignable cause management can be substantial, especially in industries with complex processes or stringent quality requirements.
These savings can be reinvested in process improvements, research and development, or other strategic initiatives, further enhancing the organization’s competitiveness and long-term growth potential.
Best Practices for Managing Assignable Causes
While the identification and management of assignable causes are critical for achieving quality excellence, the effectiveness of these efforts hinges on adhering to best practices.
Here are some essential best practices that organizations should embrace to optimize their approach to managing assignable causes:
Documenting the process of searching for, identifying, and addressing assignable causes is a crucial best practice.
Thorough documentation not only serves as a historical record but also facilitates knowledge sharing and continuous improvement within the organization.
When an assignable cause is identified, it is essential to document the following:
- The specific signals or patterns that initially indicated the presence of an assignable cause (e.g., control chart violations, non-random patterns).
- The methods and techniques employed to investigate and isolate the root cause (e.g., root cause analysis tools, data analysis techniques).
- The specific root cause or assignable cause identified, including a detailed description and any relevant supporting evidence.
- The corrective actions are taken to address the assignable cause, including the rationale behind the chosen approach.
- The results and impact of the corrective actions, including any improvements in process performance or quality metrics.
Comprehensive documentation allows organizations to build a knowledge base of assignable causes and their resolutions, enabling faster response times and more effective problem-solving in the future.
Additionally, it facilitates knowledge transfer and training, ensuring that lessons learned are not lost due to employee turnover or organizational changes.
When an assignable cause is identified, it is crucial to prioritize and act upon it promptly.
Delays in addressing assignable causes can exacerbate their impact, leading to further deviations, increased waste, and potential customer dissatisfaction.
Conclusion & Handling Assignable Cause
Quality leadership demands effectively handling assignable causes, as we’ve discussed at length.
We explored assignable causes’ nature, value, and best practices within continuous improvement frameworks.
By mastering the covered concepts and methods, companies access benefits including enhanced quality control, problem-solving, efficiency, waste/cost reduction, and client satisfaction.
As validated across industries, The principles discussed prove theoretical and actionable.
Ahead, assignable cause management will grow ever more crucial as businesses strive to stay ahead competitively.
Cultivating constant upgrading, insights-led decisions, and empowering employees with knowledge/tools positions enterprises as quality excellence leaders.
Comprehending and practicing assignable cause handling delivers tangible, measurable progress impacting profits and long-term success.
By prioritizing assignable cause administration, companies pave their way to sustained growth, advancing innovations, and a durable competitive edge.
SixSigma.us offers both Live Virtual classes as well as Online Self-Paced training. Most option includes access to the same great Master Black Belt instructors that teach our World Class in-person sessions. Sign-up today!
Virtual Classroom Training Programs Self-Paced Online Training Programs